Chapitre 1 Quelques notions d’air comprimé Pour l’air comprimé comme pour bien
Chapitre 1 Quelques notions d’air comprimé Pour l’air comprimé comme pour bien d’autres choses dans la vie, le diable se cache dans les détails et de petites causes produisent souvent de grands effets, en bien ou en mal. Examinées de près, les choses sont souvent différentes de ce qu’elles paraissent au premier abord. L’air comprimé, par exemple, peut coûter très cher s’il est produit et utilisé dans des conditions défavorables, ou au contraire être très économique dans des conditions générales bien adaptées. Dans le premier chapitre, nous nous penchons sur quatre notions de la technique d’air comprimé accompagnées de quelques remarques importantes. 1. Débit Le débit d’un compresseur est le volume d’air, ramené à la pression atmosphérique, que le compresseur injecte à l’état comprimé dans le réseau. Pour mesurer le débit, on procède comme indiqué à la fi g. 1 : relever tout d’abord la température, la pression atmosphérique et l’humidité de l’air à l’entrée de la machine complète. La pression de service maximale, la température de l’air comprimé et le volume d’air débité sont ensuite mesurés en sortie de compresseur. Enfin, on ramène le volume V2 mesuré à la sortie d’air comprimé aux conditions d’aspiration, à l’aide de l’équation des gaz parfaits (cf. formule ci-dessus). Ce calcul donne le débit du compresseur, à ne pas confondre avec le débit du bloc compresseur. Equation Temperature d’aspiration T1 Volume de sortie V2 Température de sortie T2 Humidité de l’air aspiré Frel Pression de vapeur pp 2. Puissance utile La puissance utile est la puissance transmise mécaniquement à l’arbre par le moteur du compresseur. Elle est à son point optimal lorsque le rendement électrique et le facteur de puissance cos φ sont exploités au maximum sans surcharge du moteur. La puissance utile optimale se situe dans la plage de puissance nominale qui figure sur la plaque constructeur du moteur électrique. Attention : Si la puissance utile s’écarte trop de la puissance nominale du moteur, le compresseur gaspille de l’énergie et/ou subit une usure accrue. 3. Puissance absorbée La puissance absorbée est la puissance électrique consommée par le moteur du compresseur pour une sollicitation mécanique donnée de l’arbre moteur (puissance utile). Elle est égale à la puissance utile plus les pertes de puissance du moteur, comme les pertes électriques et mécaniques dues aux roulements et à la ventilation du moteur. La puissance absorbée au point nominal se calcule avec la formule ci-dessous : Un, ln, et cos ϕn fi gurent sur la plaque constructeur du moteur électrique. P = Un x ln x √3 x cos ϕn 4. Puissance spécifique La puissance spécifique désigne le rapport entre la puissance électrique absorbée et le débit d’air fourni à une pression de service donnée (fi g. 2). La puissance électrique absorbée par un compresseur est la somme des puissances absorbées de tous les moteurs du compresseur, à savoir le moteur principal, le moto ventilateur, le moteur de la pompe à huile, le kit hors-gel etc. Si la puissance spécifique est utilisée pour calculer des coûts d’exploitation, elle doit se rapporter aux bornes de la centrale complète à la pression de service maximale. Pour cela, il faut diviser la puissance absorbée totale à la pression maximale par le débit du compresseur à cette même pression Puissance absorbée/ débit= P spéc. Puissance absorbée Ventilateur Pertes de rendement internes, comprises dans le rendement moteur Sortie d’air comprimé (débit) Aspiration d’air 5. IE – la nouvelle formule des moteurs économes en énergie La première classification du rendement des moteurs triphasés asynchrones est apparue aux États-Unis en 1997 avec la loi EPACT (Energy Policy Act). L’Europe a ensuite mis en place sa propre classification. Depuis 2010, les moteurs électriques sont soumis à la norme internationale IEC. Les classifications et le renforcement des législations ont conduit à une nette amélioration du rendement énergétique des moteurs électriques des catégories supérieures. Les moteurs à grand rendement offrent de gros avantages : a) De basses températures de service Sur les petits moteurs, les pertes de rendement internes (frottement, échauffement) peuvent représenter jusqu’à 20 % de la puissance absorbée, et 4 à 5 % sur les moteurs de plus de 160 kW. Les moteurs IE3/IE4 limitent l’échauffement et donc les pertes (fig. 3). Dans un moteur conventionnel en charge normale l’augmentation de la température de service est d’environ 80 K avec une réserve de température de 20 K par rapport à la classe d’isolation F, alors que dans les mêmes conditions, l’élévation de température d’un moteur IE ne dépassera pas 65 K environ, avec une réserve de température de 40 K. b) Une plus grande longévité Les basses températures de service réduisent la sollicitation thermique du moteur, des roulements et du bornier, d’où une plus grande longévité du moteur. c) 6 % d’air comprimé en plus avec moins d’énergie Une moindre déperdition de chaleur se traduit par une augmentation du rendement. En étudiant soigneusement ses compresseurs par rapport aux moteurs à grand rendement, KAESER a pu augmenter le débit des machines de 6 % et leur puissance spécifi que de 5 %. Résultat : des débits plus importants, des temps en marche plus courts et une réduction de la consommation d’énergie par mètre cube d’air comprimé Fig 3 Quel est le compresseur le mieux adapté pour produire de l’air comprimé exempt d’huile ? Indépendamment de ce que peut affirmer tel ou tel constructeur, la réponse à cette question est claire : il est possible d’obtenir de l’air comprimé de grande qualité, exempt huile, aussi bien avec un compresseur à vis sèches ou à pistons secs qu’avec un compresseur refroidi par huile ou par fl uide. Le choix du système doit être guidé par des critères de rendement. 1. Qu’entend-on « air comprimé exempt d’huile » ? Selon la norme ISO 8573-1, l’air comprimé est considéré comme exempt d’huile si sa teneur en huile (vapeur d’huile comprise) est inférieure à 0,01 mg/m³. Cela représente environ 4 % de ce qui est contenu dans l’air atmosphérique. Cette quantité est si faible qu’elle est pratiquement impossible à détecter. Mais qu’en est-il de la qualité de l’air aspiré par le compresseur ? Elle dépend fortement de l’environnement : la teneur en hydrocarbures due aux émissions industrielles et à la circulation automobile peut se situer entre 4 et 14 mg/m³ d’air dans les zones moyennement polluées. Dans les zones industrielles où des huiles sont utilisées pour le 2. Pourquoi traiter l’air comprimé ? Le compresseur fonctionne comme un gros aspirateur qui absorbe les polluants, les concentre du fait de la compression puis les rejette dans le réseau en l’absence de traitement. a) Les compresseurs « sans injection d’huile » Le fonctionnement décrit ci-dessus se vérifie surtout pour les compresseurs à vis sèches ou à pistons secs : du fait des polluants , un compresseur simplement équipé d’un préfiltre de 3 microns ne peut pas produire de l’air comprimé exempt d’huile. En dehors de ces préfi ltres, les compresseurs à vis sèches ou à pistons secs ne disposent pas de composants de traitement. b) Les compresseurs refroidis par fluide ou par huile Dans ce type de compresseurs, le fluide (ou l’huile) de refroidissement neutralise les polluants agressifs et évacue une partie des particules contenues dans l’air comprimé. 3. Traiter l’air comprimé pour maîtriser sa qualité Même si l’air comprimé produit est relativement pur, son traitement est indispensable. Dans les conditions ordinaires d’aspiration d’air atmosphérique plus ou moins pollué, la compression, avec ou sans injection d’huile, ne permet pas d’obtenir une qualité d’air déshuilé définie, conforme à ISO 8573-1. La production d’air comprimé est plus ou moins économique suivant la plage de pression et de débit envisagée qui, à son tour, détermine le type de compresseur requis. Le séchage est le traitement fondamental pour toute utilisation de l’air comprimé. Généralement, le procédé le plus économique est le séchage frigorifique économe en énergie . 4. Le système de purification d’air KAESER Le rendement des compresseurs à vis modernes, refroidis par fluide ou par huile est supérieur d’environ 10 % à celui des compresseurs à vis Chapitre 3 Pourquoi sécher l’air comprimé ? Le problème tient à l’hygrométrie de l’air : lorsque l’air atmosphérique se refroidit, comme c’est le cas après avoir été comprimé dans le compresseur, la vapeur d’eau qu’il contient se condense. Un compresseur de 5 m³/min (débit rapporté à une température ambiante de +20 °C, 70 % d’humidité relative et 1 barabs) « produit » environ 30 litres d’eau sur huit heures. Il faut éliminer cette quantité d’eau du système d’air comprimé pour éviter des dysfonctionnements et des dommages aux équipements. Par conséquent, le séchage économique et non polluant est une partie importante du traitement pour parvenir à de l’air comprimé adapté aux besoins. 1. Un exemple concret Un compresseur refroidi par fluide aspire 10 m³ d’air à la minute. Ce volume d’air à la pression ambiante, à 20 °C et avec une humidité relative de 60 % contient environ 100 g de vapeur d’eau. La compression de l’air à un taux de 1:10 fournit un mètre cube d’air industriel à uploads/s1/ guide-air-comprime.pdf
Documents similaires
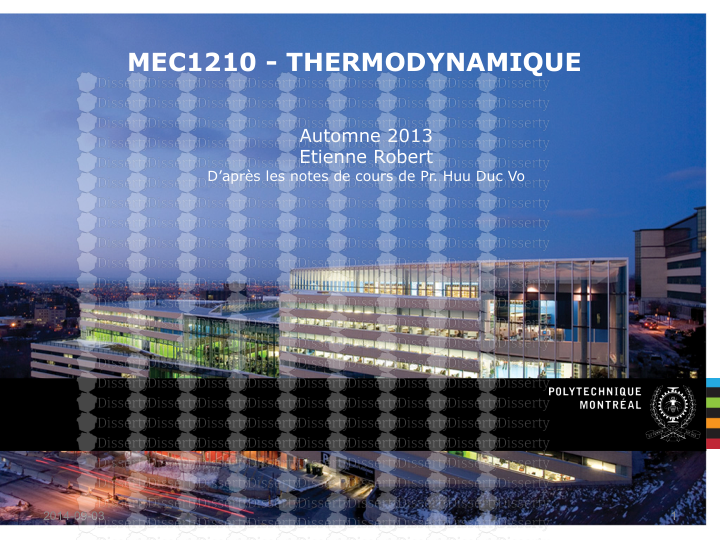
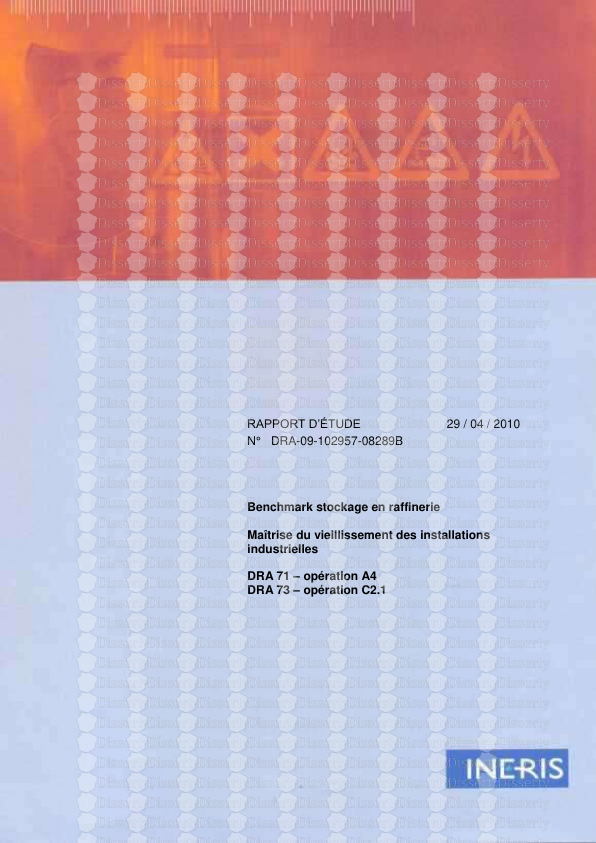
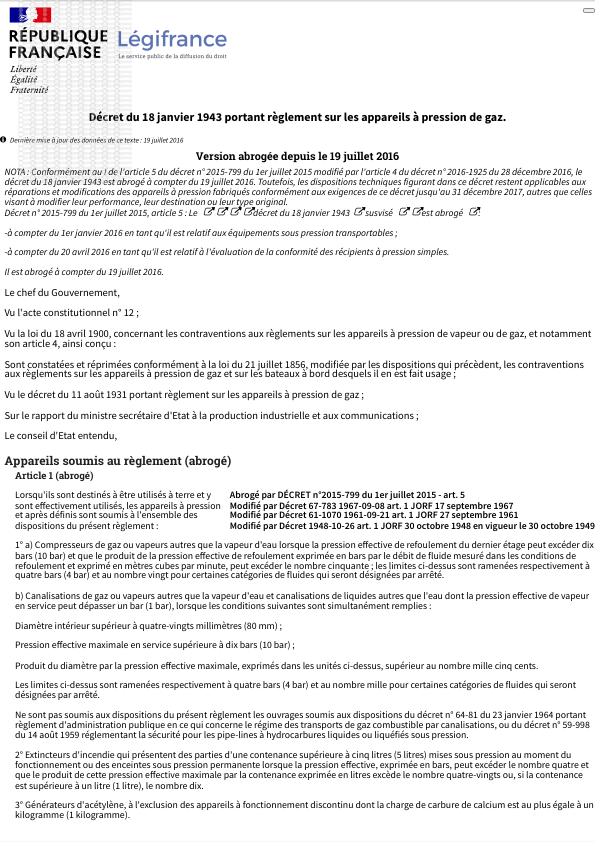
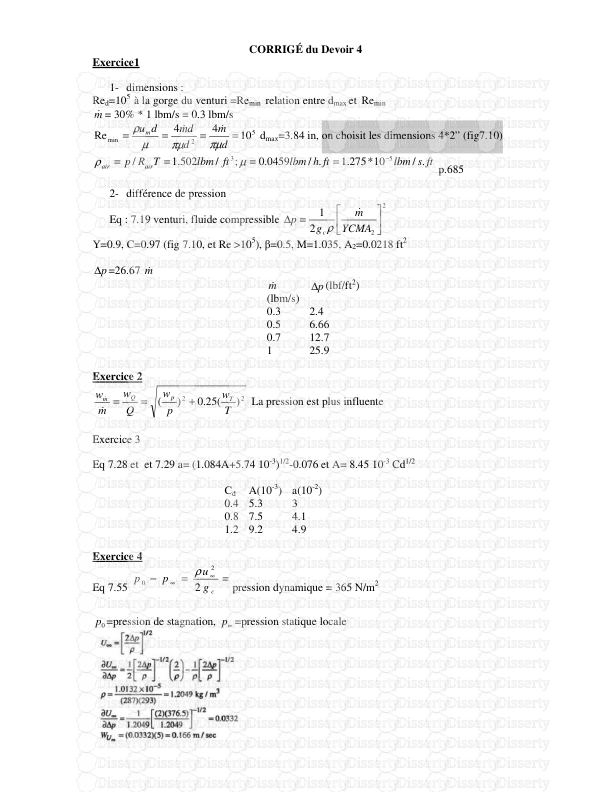
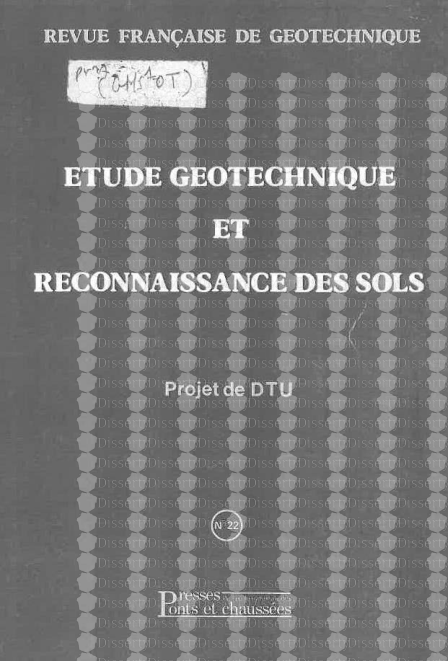
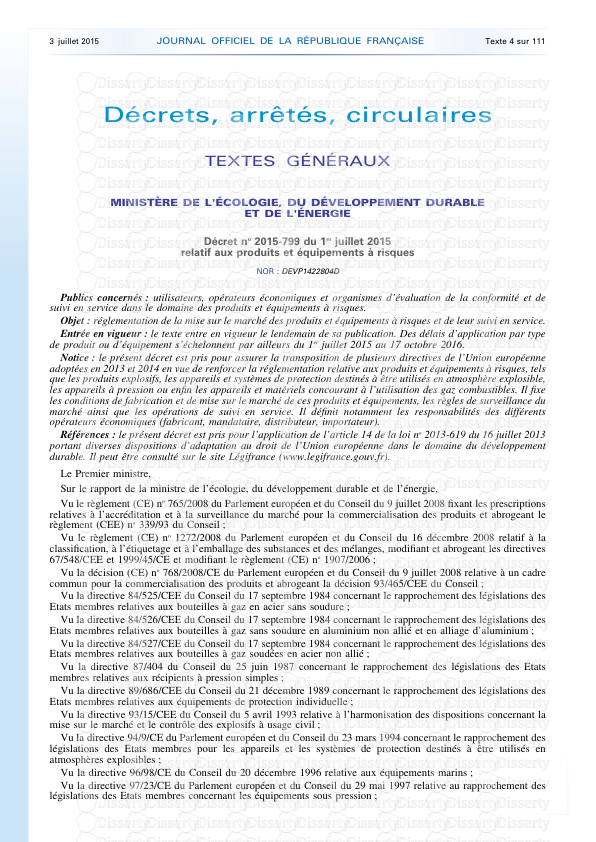
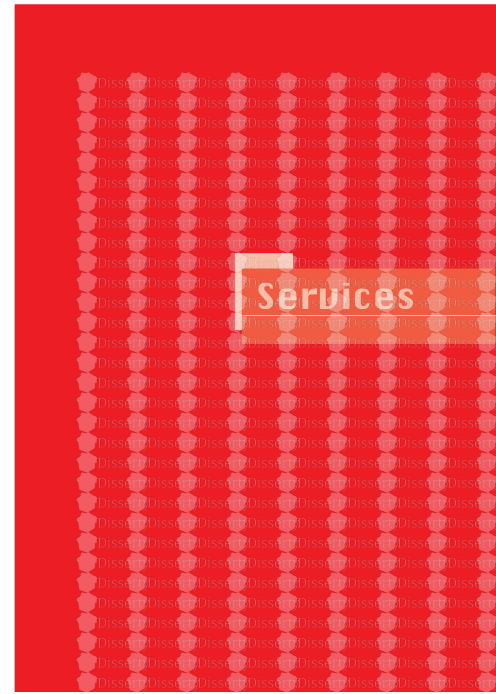
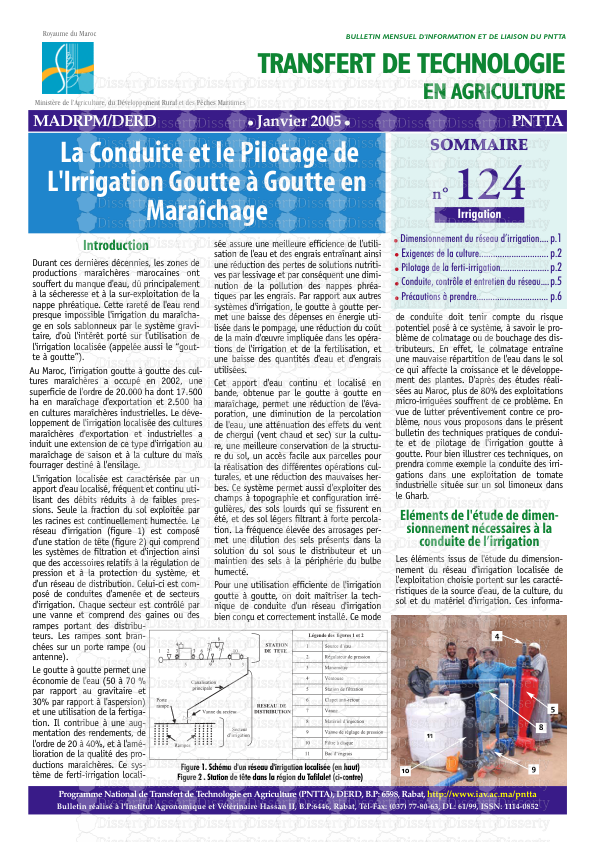
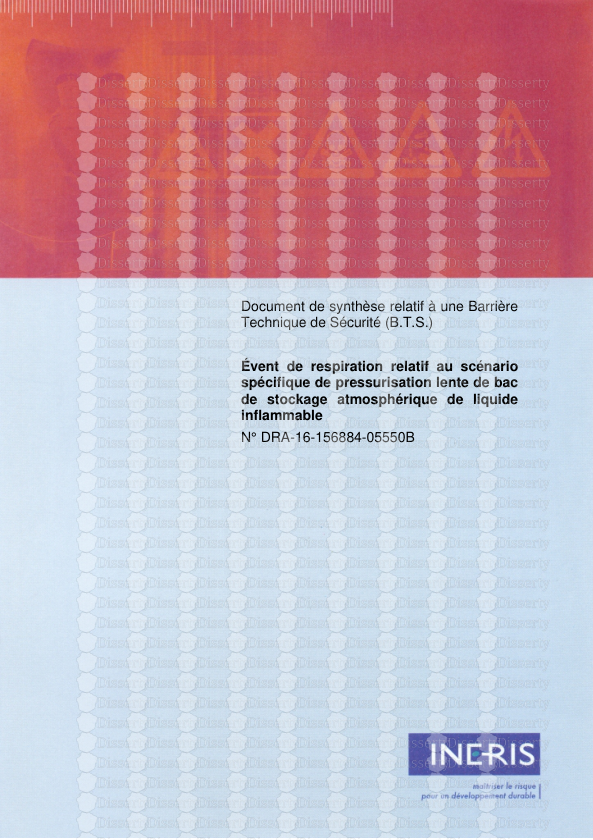
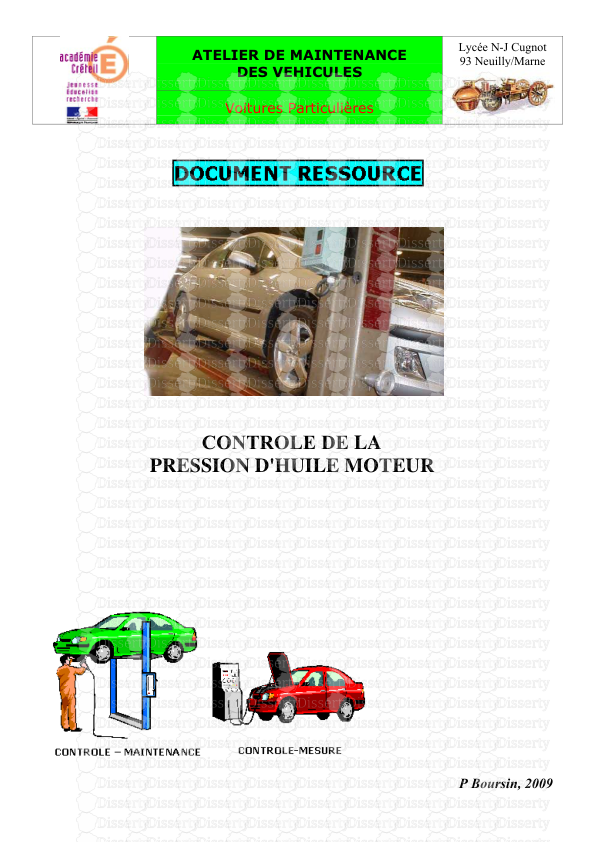
-
51
-
0
-
0
Licence et utilisation
Gratuit pour un usage personnel Attribution requise- Détails
- Publié le Nov 05, 2021
- Catégorie Administration
- Langue French
- Taille du fichier 9.4702MB