Liste des figures Figure 1.1: Réseau Global du groupe SEWS ....................
Liste des figures Figure 1.1: Réseau Global du groupe SEWS ......................................................................... 7 Figure 1.2: Sites de production au Maroc .............................................................................. 8 Figure 1.3: Les familles d’un câble d’automobile ................................................................. 9 Figure 1.4: Les processus de production .............................................................................. 10 Figure 1.5: Fils dénudé ........................................................................................................... 12 Figure 1.6: Fils inséré du joint .............................................................................................. 12 Figure 1.7: Fils sertis .............................................................................................................. 13 Figure 1.8: Fils marqué .......................................................................................................... 13 Figure 2.1 : Chaîne de valeur ................................................................................................ 25 Figure 2.2: Construction de la VSM ..................................................................................... 26 Figure 2.3: Diagramme d’Ishikawa ...................................................................................... 30 Figure 2.4: Exemple de diagramme spaghetti ..................................................................... 32 Figure 3.1: Diagramme Pareto des familles de produits .................................................... 36 Figure 3.2: Diagramme de flux de la famille MUX PDB .................................................... 37 Figure 3.3: Répartition des temps d’arrêts dans le processus épissurage ......................... 41 Figure 3.4: Analyse Pareto des causes d’arrêts épissurage ................................................ 41 Figure 3.5: Répartition des temps d’arrêt dans le processus sertissage ............................ 42 Figure 3.6: Diagramme de Pareto des causes d’arrêt sertissage ........................................ 43 Figure 3.7: Répartition des temps d’arrêts dans le processus twistage ............................. 44 Figure 3.8: Diagramme Pareto des causes d’arrêts twistage ............................................. 44 Figure 3.9: Répartition du temps de set up dans le processus épissurage ........................ 47 Figure 3.10: Répartition du temps de set up sertissage ...................................................... 48 Figure 3.11: Répartition du temps de set up dans le processus twistage .......................... 50 Figure 3.12: Répartition du temps de set up dans les trois processus ............................... 51 Figure 3.13: Diagramme Ishikawa des causes de déplacements ........................................ 52 Figure 3.14: Diagramme spaghetti de la section épissurage1 ............................................. 54 Figure 3.15: Répartition des déplacements dans la section épissurage 1 .......................... 54 Figure 3.16: Diagramme spaghetti des déplacements dans la zone sertissage ................. 55 Figure 3.17: Répartition des déplacements dans la section sertissage manuel ................. 56 Figure 3.18: Diagramme spaghetti de la zone twistage ....................................................... 58 Figure 3.19: Répartition des déplacements dans la section twistage ................................. 58 Figure 3.20: Temps perdu dans les différents processus .................................................... 59 Figure 4.1 : Répartition des temps de changement de série épissurage ............................ 67 Figure 4.2: Temps de changement de série épisssurage avant et après la mise en place du SMED ................................................................................................................................. 67 Figure 4.3 : Temps de changement de sertissage avant et après la mise en place du SMED ...................................................................................................................................... 69 Figure 4.4: Répartition des temps de changement de série sertissage ............................... 69 Figure 4.5: Temps de changement de série twistage avant et après la mise en place du SMED ...................................................................................................................................... 71 Figure 4.6: Répartition des temps de changement de série twistage ................................. 71 Figure 4.7: Taux d’occupations des postes ........................................................................... 75 Figure 4.8: Nouveaux taux d’occupations des postes .......................................................... 76 Figure 4.9: Répartition du temps d’arrêt machine ............................................................. 78 Figure 4.10: Méthodologie de la maintenance autonome ................................................... 79 Figure 4.11: Répartition des causes d’arrêts machine épissurage ..................................... 81 Figure 4.12: Répartition du temps de travail ...................................................................... 85 Figure 4.13: Interface de l’application ................................................................................. 87 Figure 4.14: Feuille de saisie des données ............................................................................ 88 Figure 4.15: Boutons de validations ...................................................................................... 89 Figure 4.16: Graphiques des indicateurs de performance ................................................. 89 Figure 4.17: Base de données par date et par opératrice ................................................... 90 Figure 4.18: Indicateurs par opératrice ............................................................................... 91 Figure 4.19: Appareil du test d’arrachement ...................................................................... 92 Liste des tableaux Tableau 3.1: Répartition du temps de séjour de la famille MUX PDB............................. 39 Tableau 3.2: Taux de rendement global………………………………………..……..….. 39 Tableau 3.3: Temps de set up dans le processus épissurage………………..………..….. 47 Tableau 3.4: Temps de set up du processus sertissage…………………….….………..... 48 Tableau 3.5: Temps de set up du processus twistage…………………………….…….... 49 Tableau 4.1:Les temps des opérations de changement de série dans le processus épissurage………………………………………………………………………..………..… 66 Tableau 4.2: Les temps des opérations de changement de série d’une presse de sertissage manuel…………………………………………………………..………………………....... 68 Tableau 4.3: Les temps des opérations de changement de série du processus twistage……………………………………………………………………………………… 70 Tableau 4.4: Temps standard moyen par opératrice……………………………..…..….. 73 Tableau 4.5: Calcul de charge des postes………………………………………..……...… 74 Tableau 4.6: Nouveau calcul de charge des postes ………………………………..…...….76 Tableau 4.7: Fiche technique de l’appareil du test……………………………..……...… 92 Tableau 4.8: Temps de changement de série et gain en temps de changement de série……………………………………………………………………………………….…. 93 Tableau 4.9: Temps de cycle et gains en opérations de transformations……….……..... 94 Tableau 4.10: Les distances parcourues avant et après achat des appareils du test………………………………………………………………………………….……..… 94 Tableau 4.11: Amélioration en productivité………………………………..………….… 95 1 Projet de fin d’étude Génie industriel Sommaire Introduction générale ............................................................................................................... 5 Chapitre 1: Présentation de l’entreprise et de la problématique ......................................... 6 1. Présentation du groupe SEWS ................................................................................................ 7 1.1 Historique ...................................................................................................................... 7 1.2 Implantation du groupe SUMITOMO, secteur Câblage Industriel.............................. 7 2. SEWS CABIND Maroc ........................................................................................................... 8 2.1 Informations générales .................................................................................................. 8 2.2 Groupe SEWS CABIND Maroc ................................................................................... 8 3. La production chez SEWS CABIND ..................................................................................... 9 3.1 Définition d’un faisceau ................................................................................................ 9 3.2 Composants d’un faisceau ............................................................................................ 9 3.3 Description du processus de production ..................................................................... 10 4. Description des processus ...................................................................................................... 11 4.1 Secteur coupe et sertissage ......................................................................................... 11 4.1.1 Définition ........................................................................................................ 11 4.1.2 Produits de la coupe ........................................................................................ 13 4.2 La zone de préparation ................................................................................................ 14 4.3 Pré montage ................................................................................................................ 15 4.4 Le montage .................................................................................................................. 15 4.5 Contrôle ....................................................................................................................... 15 4.6 L’emballage ................................................................................................................ 16 4.7 L’expédition ................................................................................................................ 16 5. Problématique .......................................................................................................................... 16 5.1 Description de la problématique ................................................................................. 16 5.2 Méthodologie de travail .............................................................................................. 17 Chapitre 2: Généralités sur le Lean Manufacturing et Outils d’analyse de l’état de production ............................................................................................................................... 19 I. Généralités sur le Lean Manufacturing ........................................................................ 20 1. Histoire du Lean Manufacturing ........................................................................................... 20 2. Les principes du Lean Manufacturing ................................................................................. 21 3. Les types de gaspillage .......................................................................................................... 22 4. Les outils du Lean Manufacturing ........................................................................................ 23 2 Projet de fin d’étude Génie industriel II. La cartographie de chaîne de valeur (VSM) ............................................................. 24 1. Présentation de VSM .............................................................................................................. 24 1.1 Définition .................................................................................................................... 24 1.2 La chaîne de valeur ..................................................................................................... 24 1.3 Les avantages de la VSM ........................................................................................... 25 2. Réalisation de la VSM ........................................................................................................... 26 2.1 Construction d’une carte VSM ................................................................................... 26 2.2 Choix de la famille de produit..................................................................................... 27 2.3 Etapes de construction de la VSM .............................................................................. 27 3. Synthèse ................................................................................................................................... 28 III. Outils d’analyse de l’état de production ................................................................... 29 1. Diagramme d’Ishikawa .......................................................................................................... 29 2. Diagramme de Pareto ............................................................................................................. 30 3. Diagramme spaghetti .............................................................................................................. 31 Chapitre 3: Analyse de l’existant .......................................................................................... 33 Introduction ............................................................................................................................ 34 I. La gestion des flux de matière et d’information au sein de la zone préparation ...... 35 1. Mode de pilotage des flux au sein de la zone préparation ................................................. 35 1.1 Les flux de matières .................................................................................................... 35 1.2 Les flux d’informations ............................................................................................... 35 2. Cartographie de la chaine de valeur (VSM) ........................................................................ 35 2.1 Choix de la famille à étudier ....................................................................................... 35 2.2 Diagramme de flux de la famille MUX PDB ............................................................. 36 2.3 Le dessin de la VSM ................................................................................................... 37 2.4 L’analyse de la performance des flux ......................................................................... 39 II. Analyse des arrêts de production ............................................................................... 40 1. Méthodologie de travail ......................................................................................................... 40 2. Application aux processus ..................................................................................................... 41 2.1 Processus d’épissurage ................................................................................................ 41 2.2 Processus sertissage .................................................................................................... 42 2.3 Processus Twistage ..................................................................................................... 43 3. Synthèse et suggestions d’améliorations ............................................................................. 45 III. Analyse du temps de Set up ........................................................................................ 46 3 Projet de fin d’étude Génie industriel 1. Méthodologie de travail ......................................................................................................... 46 2. Analyse du set up des différents processus ......................................................................... 46 2.1 Processus épissurage ................................................................................................... 46 2.2 Sertissage .................................................................................................................... 48 2.3 Twistage ...................................................................................................................... 49 3. Synthèse ................................................................................................................................... 50 IV. Analyse des déplacements ........................................................................................... 52 1. Analyse des causes des déplacements inutiles .................................................................... 52 2. Les diagrammes spaghetti des différentes sections de la zone étudiée............................ 53 2.1 Epissurage 1 ................................................................................................................ 53 2.2 Sertissage manuel ........................................................................................................ 55 2.3 Epissurage 2 ................................................................................................................ 56 2.4 Twistage ...................................................................................................................... 57 3. Synthèse ................................................................................................................................... 59 Conclusion ............................................................................................................................... 60 Chapitre 4 : Propositions d’amélioration ............................................................................. 61 Introduction ............................................................................................................................ 62 I. Application de la méthode SMED ................................................................................. 63 1. Présentation de la méthode .................................................................................................... 63 1.1 Objectifs de la méthode SMED .................................................................................. 63 1.2 Etapes de la méthode SMED ...................................................................................... 64 2. La mise en place du SMED ................................................................................................... 65 2.1 Epissurage ................................................................................................................... 65 2.2 Sertissage manuel ........................................................................................................ 67 2.3 Twistage ...................................................................................................................... 69 II. Equilibrage de la charge des postes ........................................................................... 72 1. Préalable de l’étude ................................................................................................................ 72 1.1 Constitution du groupe de travail ................................................................................ 72 1.2 Collecte des données ................................................................................................... 72 2. Etude de la première hypothèse ............................................................................................ 73 3. Etude de la deuxième hypothèse ........................................................................................... 74 4. Proposition d’une nouvelle affectation des saldes aux postes .......................................... 75 5. Essai de la nouvelle répartition sur le terrain ...................................................................... 77 4 Projet de fin d’étude Génie industriel III. Application de l’auto maintenance ............................................................................ 78 1. Introduction ............................................................................................................................. 78 2. La maintenance autonome. .................................................................................................... 79 2.1 Définition .................................................................................................................... 79 2.2 Méthodologie et étapes ............................................................................................... 79 2.3 Les niveaux d’intervention des opérateurs.................................................................. 80 3. Application aux processus ..................................................................................................... 81 IV. Elaboration d’une application informatique pour la gestion du tableau de bord. 83 1. Objectifs de l’application ....................................................................................................... 83 2. Choix des indicateurs de performance ................................................................................. 84 3. Calcul des indicateurs de performance ................................................................................ 84 3.1 Taux de disponibilité ................................................................................................... 84 3.2 Taux de qualité ............................................................................................................ 84 3.3 Taux de performance .................................................................................................. 85 uploads/Industriel/ total-rapport-1.pdf
Documents similaires
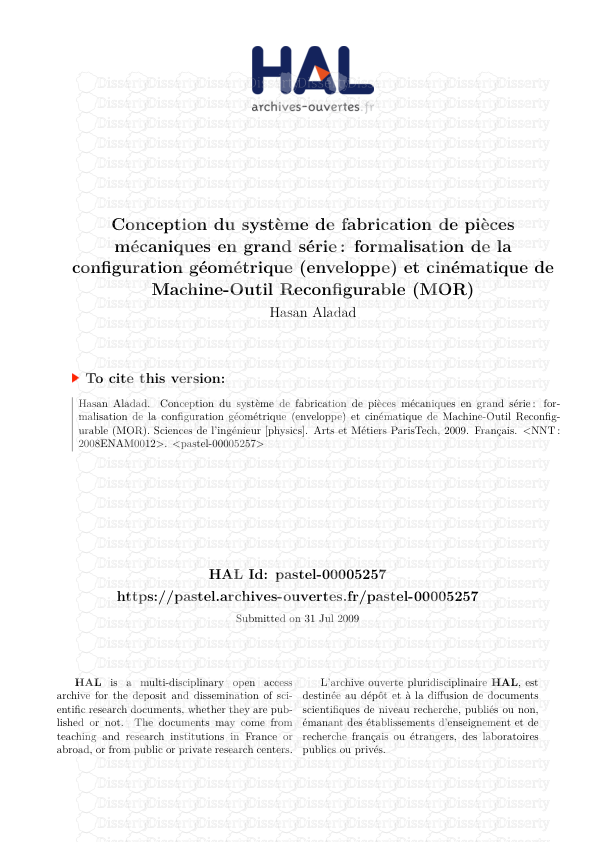
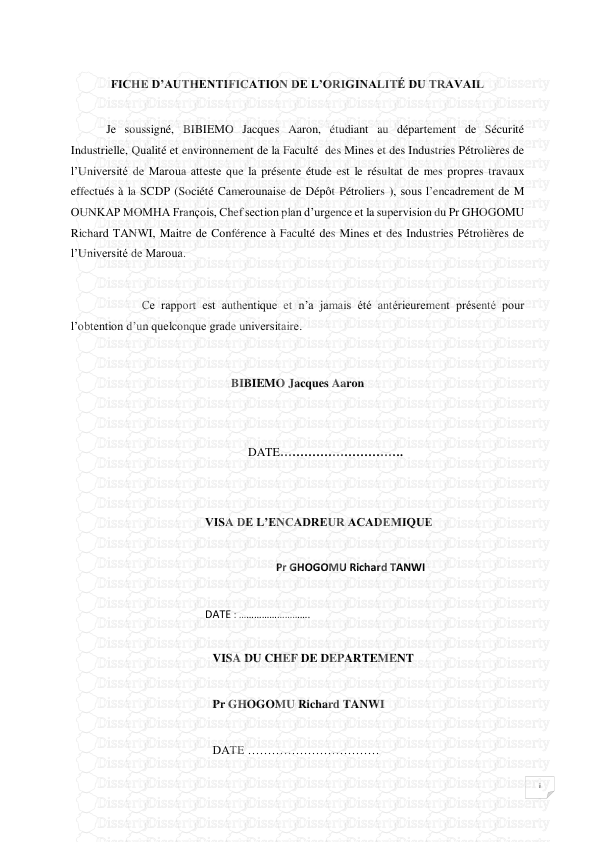
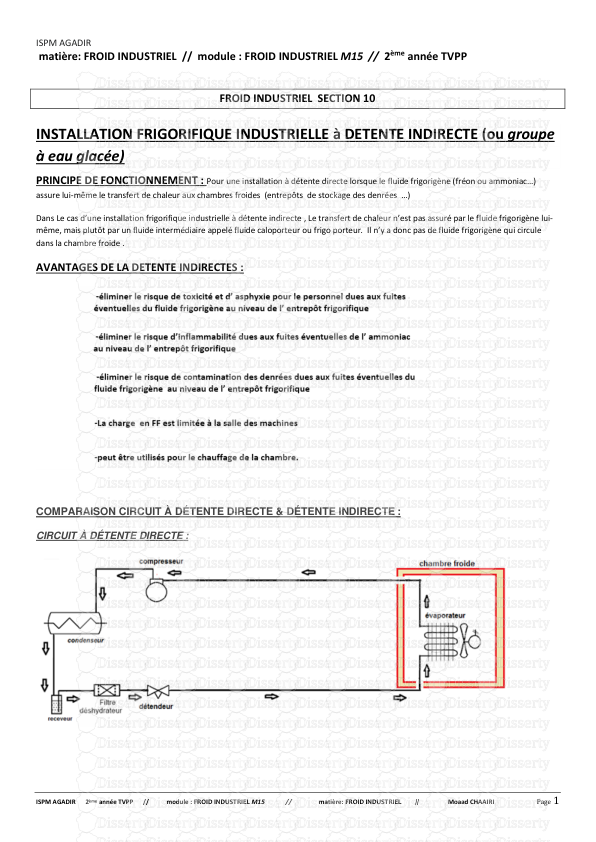
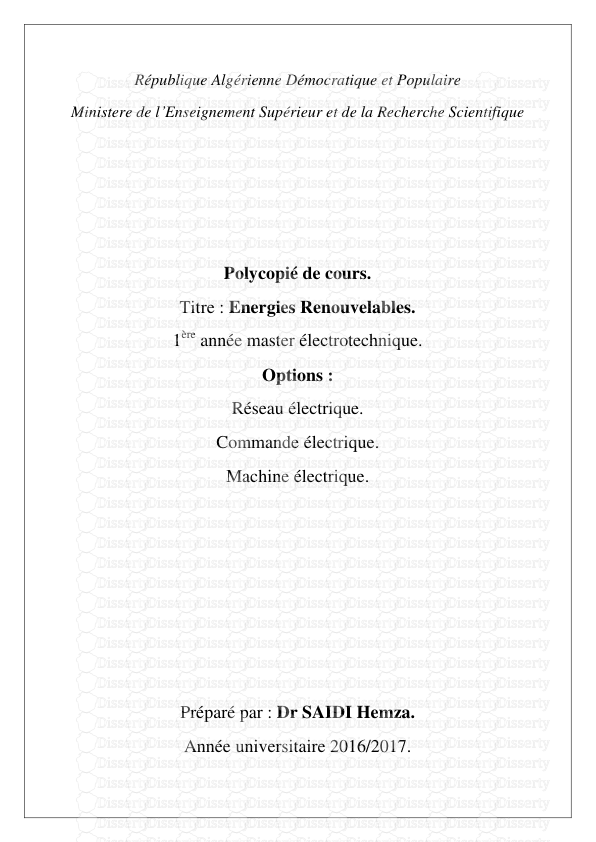
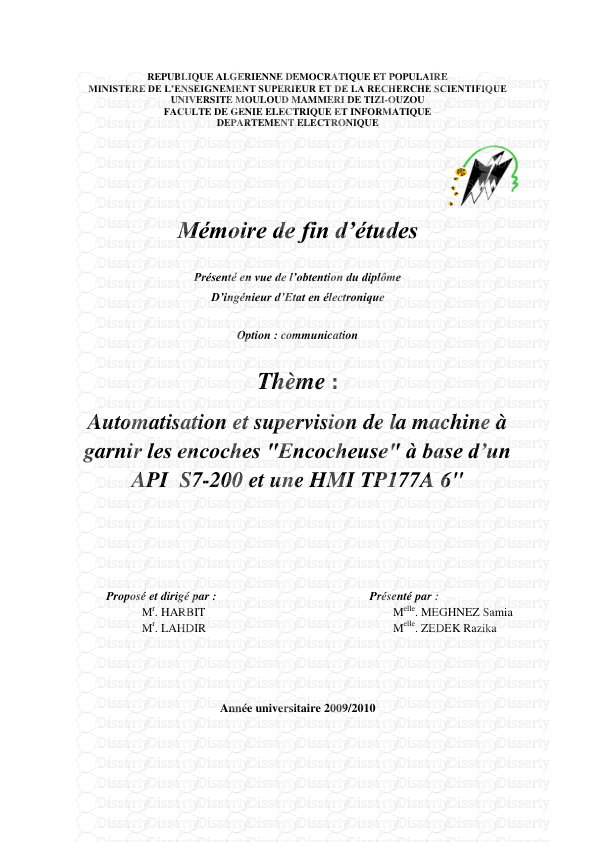
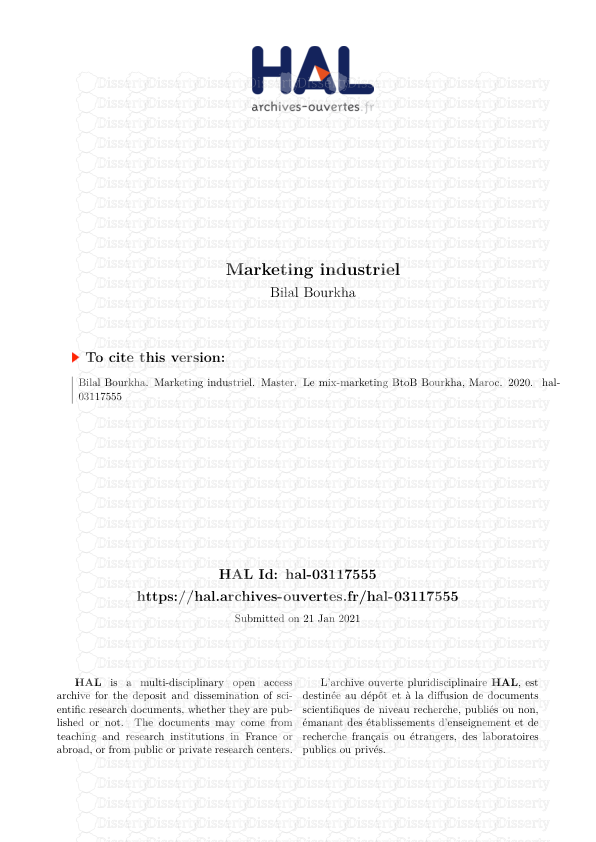
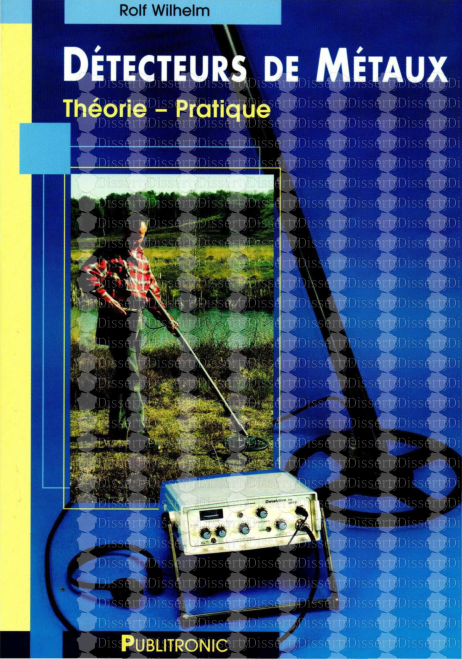
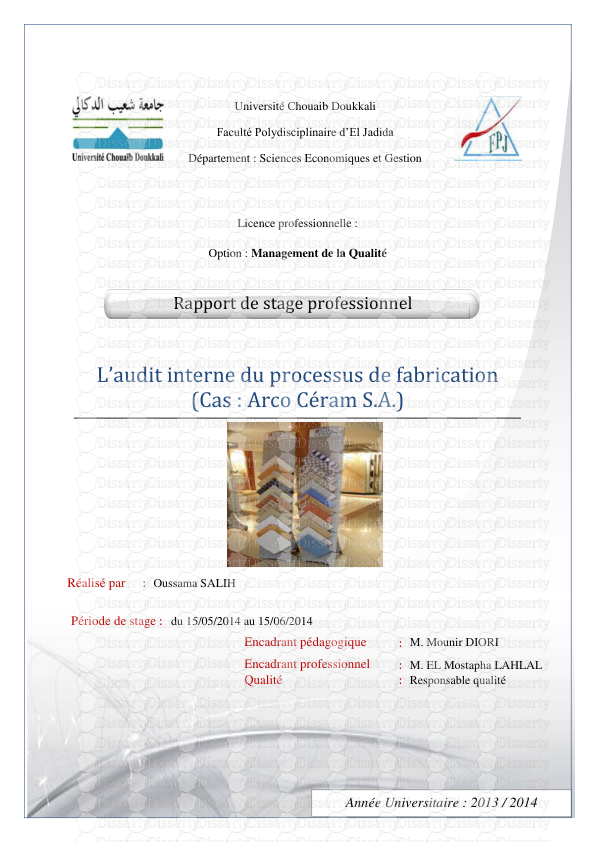
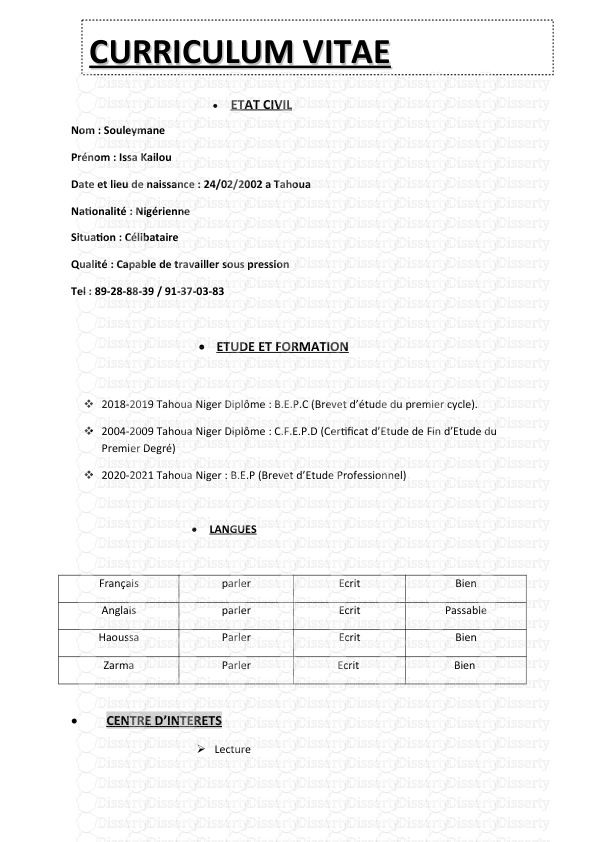
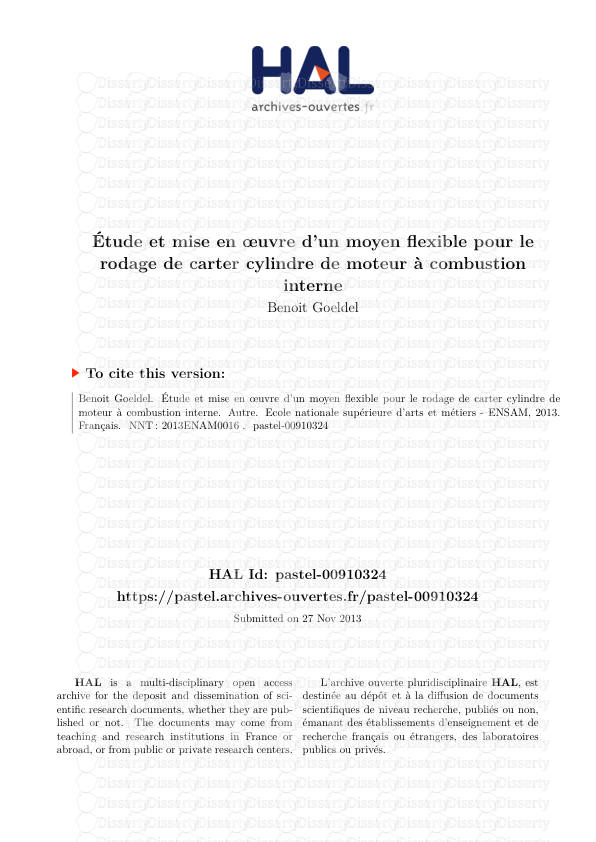
-
47
-
0
-
0
Licence et utilisation
Gratuit pour un usage personnel Attribution requise- Détails
- Publié le Fev 21, 2022
- Catégorie Industry / Industr...
- Langue French
- Taille du fichier 3.7200MB