L’INDUSTRIE CIMENTIÈRE FRANÇAISE et LA RÉDUCTION DES ÉMISSIONS de Sommaire 1. L
L’INDUSTRIE CIMENTIÈRE FRANÇAISE et LA RÉDUCTION DES ÉMISSIONS de Sommaire 1. L’INDUSTRIE CIMENTIÈRE FRANÇAISE page L’industrie cimentière française : quelques chiffres 3 Ciment & béton 4 La fabrication du ciment : process & transports 5 2. LEVIERS PROCESS & PRODUIT page Combustibles alternatifs 6 Valorisation matière 7 Energie thermique & énergie électrique 8 Innovations dans le ciment 9 3. PROSPECTIVES page Piégeage, stockage et valorisation du CO2 10 Recyclage du béton 11 Recarbonatation du ciment & démolition du béton 12 4. CONTRIBUTIONS DU BÉTON page Économie circulaire & filière béton 13 Consommation responsable & durée d’usage 14 Inertie thermique & réductions de CO2 en aval 15 Raoul de Parisot Président du Syndicat Français de l’Industrie Cimentière Réduire les émissions de CO2 est une entreprise complexe qui exige de poursuivre les actions lancées parallèlement sur plusieurs voies ; cela ne se fera pas du jour au lendemain par le biais d’une solution miracle. Il faut arriver à identifier le bon mélange de techniques, d’investissements et de procédés qui feront la différence, tout en maintenant la compétitivité de l’industrie cimentière en France. L’industrie cimentière française pratique une écologie industrielle et territoriale depuis longtemps. Au quotidien et de façon croissante, elle a recours aux combustibles alternatifs de proximité, et à la valorisation, à diverses étapes de son procédé de fabrication, de déchets minéraux d’autres industries locales. La réduction des émissions de CO2 est par ailleurs le dénominateur commun de nombreux programmes collaboratifs de R&D, nationaux et européens, initiés ou accompagnés par le secteur : développement de ciments bas carbone, élargissement du champ d’application du recyclage des bétons de déconstruction, optimisation des avantages du phénomène de recarbonatation dans les granulats recyclés, captation du CO2 par des micro-algues. En aval, la filière béton œuvre à une réduction significative des émissions de CO2 sur l’ensemble du cycle de vie des bâtiments et des ouvrages en béton. Ceci grâce à une conception qui intègre d’office le potentiel évolutif de constructions ayant une espérance de vie centenaire ou par le biais de propriétés qui contribuent – même indirectement – à la réduction des émissions de CO2, comme les bétons clairs à indice albédo élevé. Le projet est ambitieux car des ruptures de technologies seront nécessaires pour tendre vers les objectifs de réduction fixés. Les innovations attendues de la R&D permettront de maintenir une production locale et d’éviter une délocalisation qui ne ferait qu’augmenter les émissions de CO2 dans un marché en forte récession. Raoul de Parisot La réduction des émissions de CO2 est le dénominateur commun de nombreux programmes collaboratifs de R&D, nationaux et européens. L’INDUSTRIE CIMENTIÈRE FRANÇAISE : QUELQUES 3 CHIFFRES Un profil carbone unique 64% décarbonatation 36% énergie Répartition des sources d’émissions de CO2 dans le procédé industriel cimentier CO2 & cycle de vie Sur l’ensemble du cycle de vie d’un bâtiment, les émissions de CO2 liées à sa construction sont de l’ordre de 5 à 7 % alors que la phase d’usage représente 88 à 98 %. 2014 1990 (en millions de tonnes) Émissions de CO2 brutes 0 5 10 15 - 39 % Émissions de CO2 : - 39 % Une R&D d’excellence 3 centres de recherche industriels en France + Partenariats avec : • enseignement supérieur, • recherche publique, • industries connexes, • industries émergentes, • programmes européens. = entre autres, contribution majeure aux 800 brevets liés au ciment déposés en 2011 à travers l’Europe. Modes de transport du ciment 88,2 % < 100 KM 2014 6,2 % > 200 KM 2014 5,6 % 2014 Source d’emplois INDUSTRIE CIMENTIÈRE FRANÇAISE CARRIÈRES, BÉTON PRÊT À L’EMPLOI, PRODUITS EN BÉTON 4 500 45 900 538 000 MÉTIERS (architectes, BET, etc.), INDUSTRIES (adjuvants, coffrages, etc.) 1 008 000 LIÉS AU BÉTON 470 000 SECTEURS CONSTRUCTION (maison individuelle, génie civil, maçonnerie, etc.) & + + ~ – 4 % de l’emploi en France en 2013 FILIÈRE BÉTON Toujours + de combustibles alternatifs 35,8 % 2014 4,9 % 1990 biomasse comprise 4 CIMENT & BÉTON Le ciment est une matière poudreuse utilisée pour lier entre eux différents composants. C’est une colle, un liant dit « hydraulique » car il durcit au contact de l’eau tout en conservant toutes ses propriétés, y compris sous l’eau. C’est le constituant clé : • du béton = du ciment mélangé à de l’eau, du sable et des granulats, • du mortier = du ciment mélangé à de l’eau et du sable. Tous les ciments courants produits en France sont normalisés et font l’objet, en cours de fabrication, de contrôles garantissant leur conformité à ces normes. Ils sont regroupés en cinq grandes catégories, suivant la nature et la proportion de leurs constituants et sont répartis en trois classes de résistance (ordinaire, haute et très haute) : • ciments Portland CEM I, • ciments Portland composés CEM II, • ciments de haut-fourneau CEM III, • ciments pouzzolaniques CEM IV, • ciments composés CEM V. Ils sont conformes à la norme européenne EN 197-1 tout comme les suivants : • les ciments courants dits « à caractéristiques complémentaires » : ciment pour travaux à la mer, ciment pour travaux en eau à haute teneur en sulfates, ciment à teneur en sulfures limitée, • les ciments dits « à usage spécifique » : ciment prompt naturel, ciment d’aluminates de calcium, ciment à maçonner. Le béton est donc, par ordre décroissant de proportion de ses constituants, un mélange de granulats (75-80 %) de ciment (12-15 %) et d’eau, et le cas échéant, de petites quantités d’adjuvants qui influencent sa mise en œuvre. Ciments et granulats sont sélectionnés en fonction de l’application envisagée pour le béton. Les granulats sont des matériaux inertes – graviers ou sable – de différentes granulométries, mais aussi… du béton recyclé. La méthode de mise en œuvre du béton dépend de la nature d’un chantier : le matériaux peut être préparé en centrale à béton, préfabriqué en usine ou fabriqué sur place. Quelle que soit la solution retenue, il s’agit toujours d’un process de coulage « à froid », qui fait l’objet d’optimisations continues pour réduire le recours aux ressources naturelles. Depuis toujours, c’est un domaine où l’innovation est primordiale, que le résultat relève du structurel (béton auto- plaçant, bétons fibrés à ultra hautes performances,…), de l’esthétique (bétons translucide, luminescent, scintillant,…), ou du fonctionnel (bétons autonettoyants, bétons dépolluants,…). Une courte introduction au matériau ciment est indispensable pour comprendre le contexte industriel dans lequel s’inscrivent les engagements de l’industrie cimentière française et pour le distinguer de son utilisation principale - le béton - avec lequel il est souvent confondu. CI-CONTRE : Incrusté de microbilles, utilisé en éléments de voirie, de signalisation ou en façade, le béton scintillant réfléchit toutes les sources lumineuses, naturelles ou artificielles, et permet une illumination ponctuelle au plus juste des nécessités d’un site. 5 LA FABRICATION DU CIMENT PROCESS & TRANSPORTS 1 Extraction des matières premières. 2 Concasseurs primaires & secondaires : réduisent les matières premières en éléments d’une dimension maximale de 150 mm. 3 Hall pré-homogénéisation : mélange les matières premières de manière à obtenir une composition homogène. 4 Broyeur sécheur du cru : broyage de la matière première en une farine très fine, le « cru ». Pour fournir tous les constituants minéraux nécessaires à la production du clinker - fer (Fe2O3), alumine (Al2O3), ou silice (SiO2) - on peut y ajouter de faibles proportions de matières naturelles (bauxite, oxyde de fer, schiste, argile ou sable), ou de déchets minéraux de composition chimique identique. 5 Silo d’homogénéisation du cru. 6 Tour de préchauffage + Précalcinateur : en passant par cette tour, le cru va atteindre une température de 900 °C, grâce au flux de gaz chauds sortant du four qui remontent la tour à contre-courant. C’est là que débute la décarbonatation, réaction qui détache des molécules de CO2 contenues dans le calcaire, le transformant en chaux. Certaines cimenteries sont équipées d’un précalcinateur 6a , foyer complémentaire dans la partie inférieure de la tour. 7 Filtre à manche : filtre les poussières des gaz sortant du four avant leur passage dans la cheminée 7a . 8 Four rotatif : le cru préchauffé pénètre dans ce tube (3-6 m large x 50x90 m long) légèrement incliné qui tourne sur lui-même, et progresse ainsi à travers des zones de plus en plus chaudes jusqu’à atteindre les 1 450 °C. Cette chaleur intense, générée par la tuyère où sont brûlés combustibles fossiles et déchets, termine la décarbonatation et provoque la transformation du cru en clinker. 9 - 10 Refroidisseur + silo de stockage clinker : le refroidissement brutal du clinker par air soufflé finalise sa transformation. Il est stocké dans des silos sur site, et utilisé sur site au fur et à mesure des besoins de production ou envoyé vers des installations de broyage extérieures. 11 Autres constituants : d’autres matières finement broyées (laitier de haut-fourneau, cendres volantes, schistes calcinés, calcaire, fumées de silice) peuvent être ajoutées à la composition finale, pour produire un ciment répondant à des besoins spécifiques. Cela réduit d’autant la teneur en uploads/Ingenierie_Lourd/ industrie-cimentiere-reduction-emissions-co2.pdf
Documents similaires
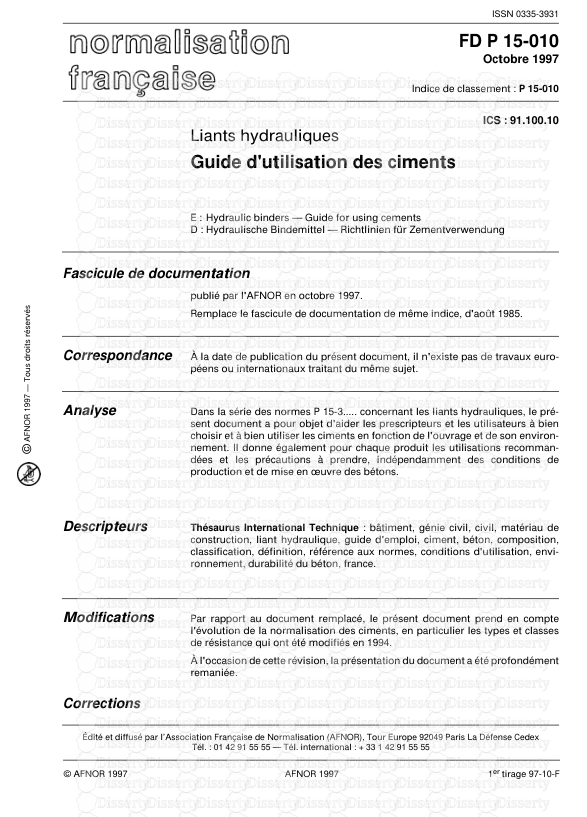
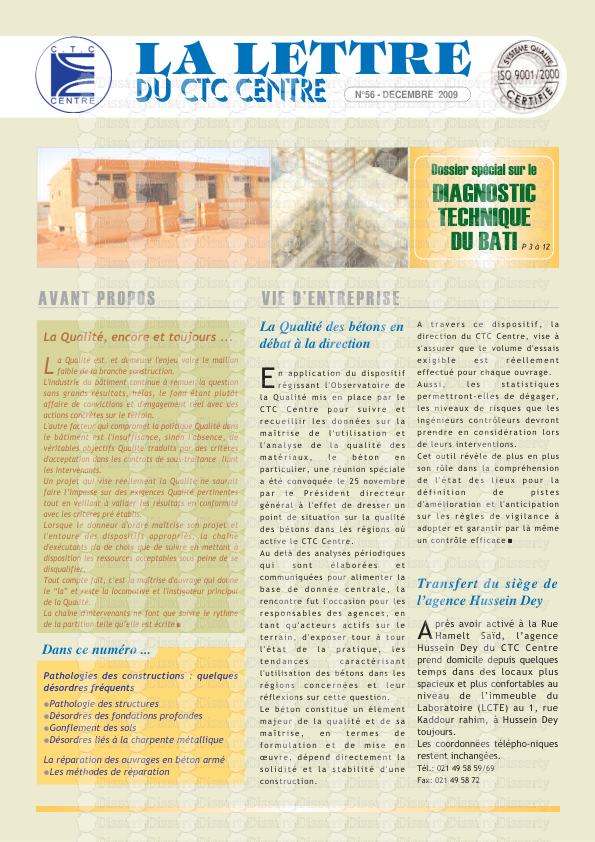
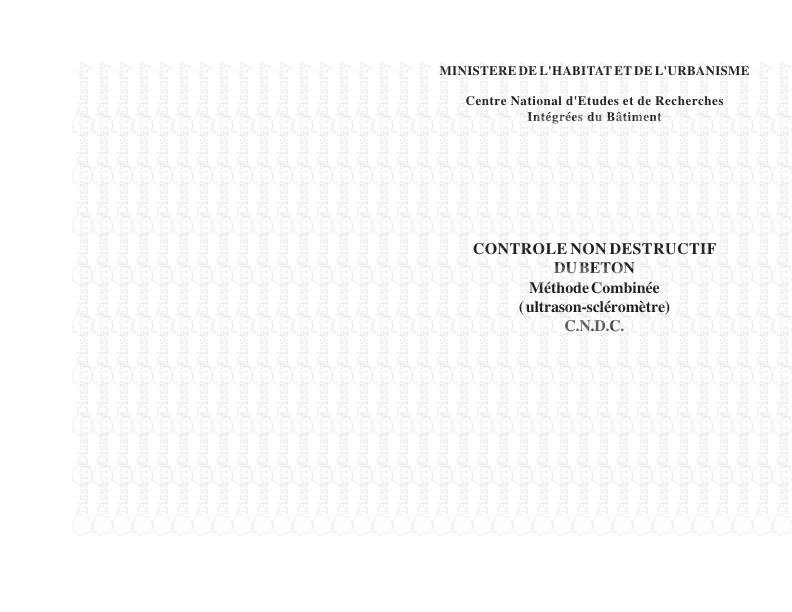
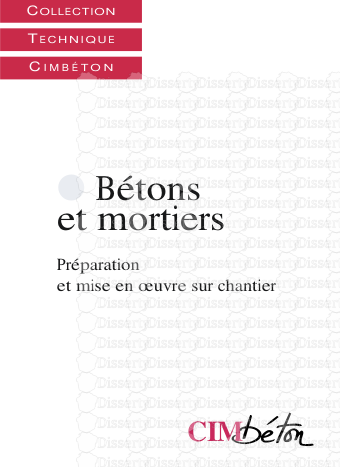
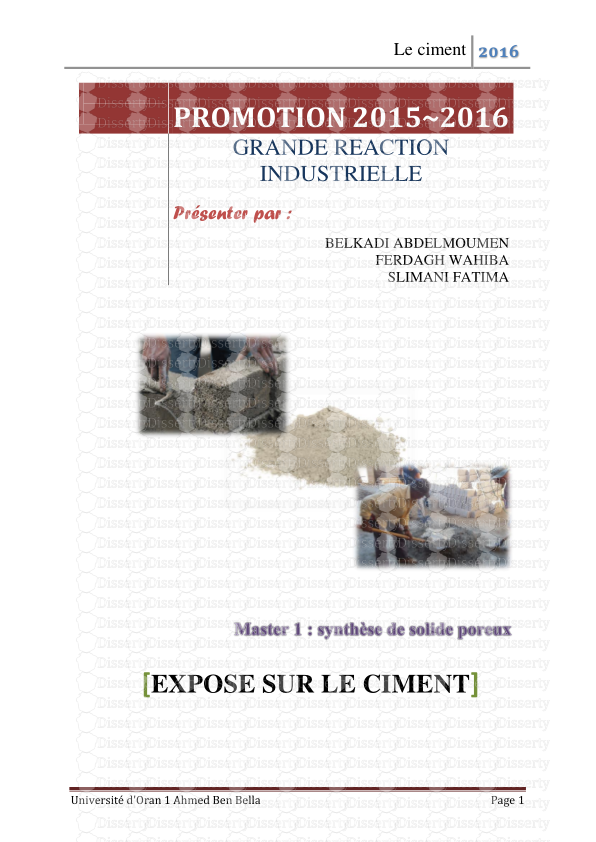
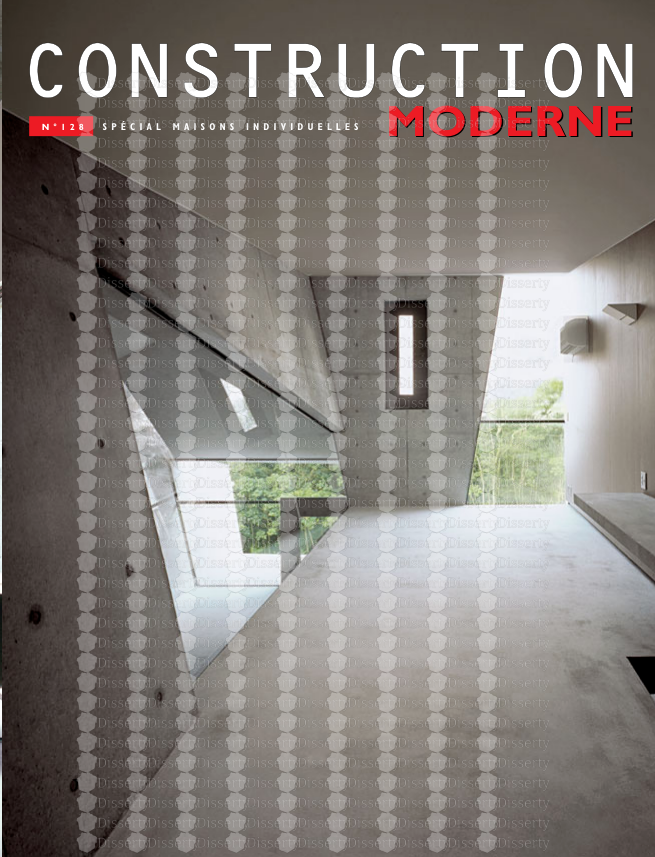
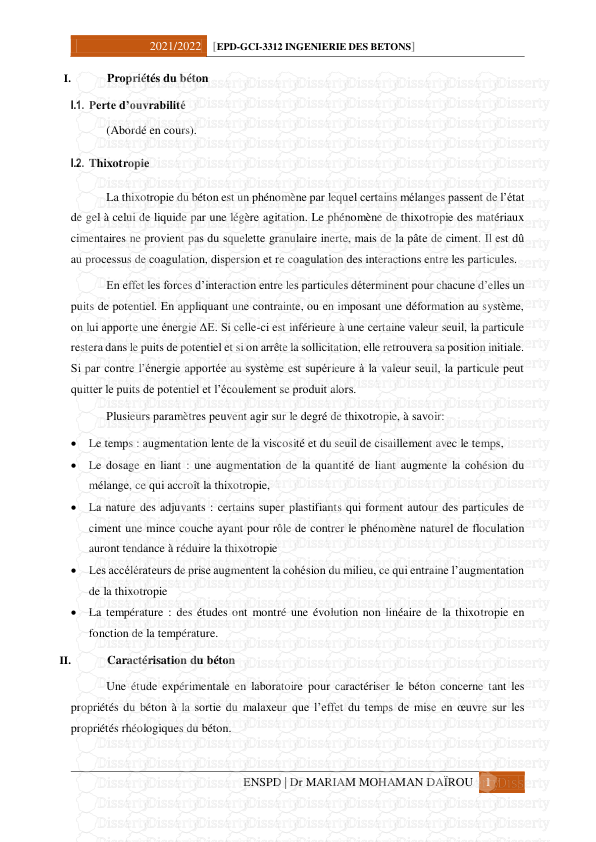
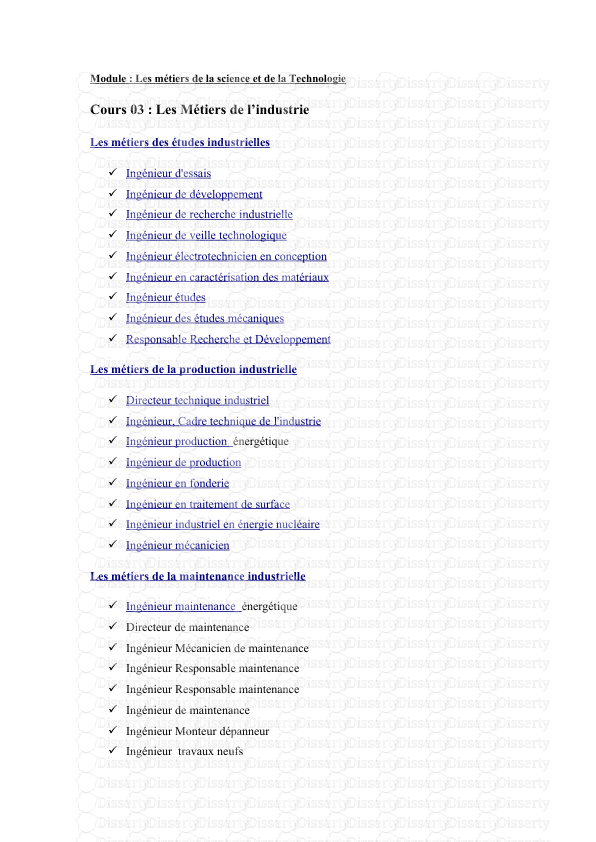

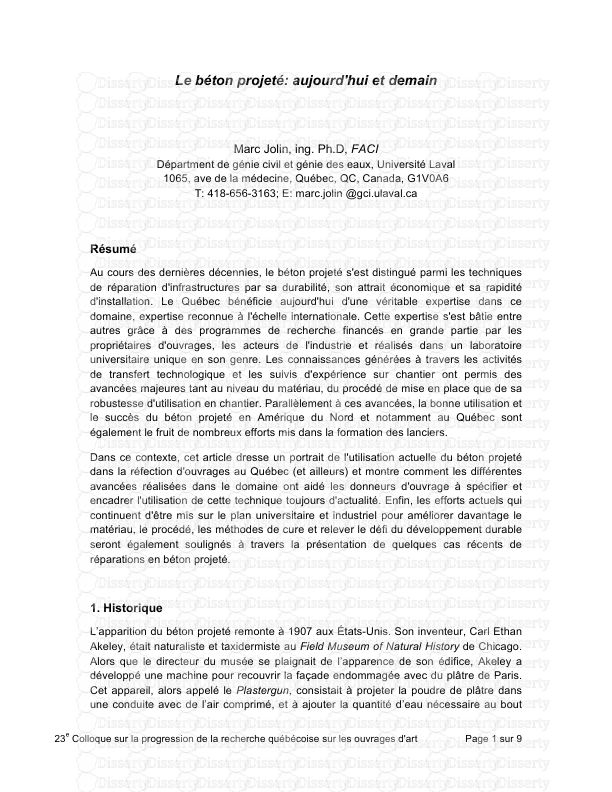
-
61
-
0
-
0
Licence et utilisation
Gratuit pour un usage personnel Attribution requise- Détails
- Publié le Jan 10, 2021
- Catégorie Heavy Engineering/...
- Langue French
- Taille du fichier 8.3151MB