WELDING TYPES AND TROUBLESHOOTING WELDING GUIDEBOOK DIGITAL MICROSCOPE IMAGING
WELDING TYPES AND TROUBLESHOOTING WELDING GUIDEBOOK DIGITAL MICROSCOPE IMAGING EXAMPLES Generally speaking, welding refers to the method of melting metals to join them together. There are multiple different methods of welding. In fusion welding, the metals to be joined together are melted. In pressure welding, the metals are joined through the application of pressure. In brasing, the base metal is not melted and instead a metal (filler metal) having a melting point lower than the base metal is melted to join the metals together. Compared to mechanical joints using rivets and bolts, welding is an economic method that saves materials and time. What Is Welding? Extra fill Extra fill Penetration Weld metal Heat-affected zone Groove Base metal Toe of the weld View from the top Base metal Bead Term Explanation Weld metal The metal part that is melted and solidifies during welding Heat-affected zone The part whose metallic structure and characteristics are changed due to the effect of the welding heat even though it is not melted Welded part The area specified by the weld metal and the heat-affected zone Extra fill The part in which the weld metal is filled in excess of the necessary dimensions Penetration The maximum distance from the edge of the heat-affected zone to the surface of the base metal before melting Bead Generally, the welded parts of the weld line (weld metal) are called beads. Toe of the weld The boundary between the weld beads and the base metal surface Groove The groove established between the base metals to be welded Welding Terminology 2 What Is Welding? Welding Types and Troubleshooting Observing Welding with a Digital Microscope What Is Arc Welding? Arc welding is the most common welding method. In arc welding, a DC voltage is applied between the welding rod and the base metal. The welding rod and the base metal are melted and joined together due to the heat of the ionised plasma (arc). The arc has an extremely high temperature of approximately 15000°C, so the metals are melted instantaneously. Weld metal Arc Base metal Welding rod Power supply Molten pool Welding direction Joining method Name Characteristics Fusion Arc welding By passing an electric current through plasma arc within a shielding gas, heat is generated and can be used to melt metal. This is the most common method of welding and it has the advantage of providing fast welds. Gas welding Metal is melted by way of gas combustion. Most commonly, acetylene gas is used. The welding speed is slower than arc welding, but it is easy to check the welding locations, which makes this method suited for the welding of thin plates. Laser welding Typical laser examples are CO2 lasers and YAG lasers. This is a new welding method, but it has been applied to the welding of vehicle bodies in recent years. Pressure Spot welding This type of welding uses electric resistance to generate heat. Pressure is applied to metal plates and an electric current is run through them in order to weld them together. A typical example is the spot welding of vehicle bodies. Seam welding This type of welding also uses electric resistance to generate heat. Because the welding can be done continuously, this method is used in applications that require a hermetic seal such as containers for storing liquids or gases. Brasing Hard brasing In brasing, a filler metal is used to join the desired metals together. The methods are torch brasing and arc brasing. Soft brasing In brasing, a filler metal is used to join the desired metals together. This is commonly referred to as soldering. Common Types of Welding 3 Welding Types and Troubleshooting What Is Pressure Welding? In this welding method, pressure is applied to the base metals and they are energised so that they are joined by their parts (the nugget) melted through the application of heat. Spot welding and seam welding are the typical ways of performing pressure welding. Spot welding Seam welding In this welding method, electrode tips clamp together the base metals so they are joined by their parts (the nugget) and melted through the application of heat. The electrode tips wear out, so replaceable cap tips are used. In this welding method, roller electrodes clamp together the base metals so they are continuously joined by their parts (the nugget) melted through the application of heat. With spot welding, the electrodes join the base metals together in a specific spot, but seam welding can be used to perform continuous welding. Electrode tip Base metal Power supply Nugget Roller electrode Base metal Nugget Roller electrode Base metal Power supply Nugget Welding direction Shielding Gas Arc Welding Structure CO2/MAG/MIG welding The welding wire itself is used as the electrode. In order to enable continuous welding, a device that automatically supplies the welding wire is necessary. The welding wire diameter is approximately 0.6 to 2.0 mm. TIG welding A non-consumable tungsten electrode is used. Compared to arc welding that uses a consumable electrode, spattering can be reduced and high-quality welding is possible, but the welding speed is slower. Welding wire Welding wire supplier Shielding gas Shielding gas Nozzle Welding direction Weld metal Base metal Shielding Gases Used for Arc Welding In arc welding, shielding gases are used to provide isolation from the atmosphere in order to prevent nitriding and oxidation. The names differ according to the shielding gas and the electrode. Name Welding rod usage (melting) Shielding gas CO2 arc welding Used 100% CO2 gas is used. MAG arc welding Used The concentration of active gas amid the inert gas (Ar/He) is greater than or equal to the control value. (O2: 2% or more, CO2: 5% or more) MIG arc welding Used 100% inert gas (Ar/He/Ar + He) is used. Alternatively, the active gas concentration must be less than or equal to the control value. (O2: 2% or less, CO2: 5% or less) TIG arc welding Not used A tungsten electrode is used within a composite gas such as Ar/He/Ar + He (Ar + H2) in order to generate an arc and melt the base metal. 4 Typical Arc Welding Defects and Countermeasures Type Cause Countermeasure Blow hole/pit Due to poor shielding gas, foreign materials such as rust, dirt, oil, and water from the base metal surface mix in, which causes an air bubble to form within the molten metal. When the blow hole reaches the surface, the opening is called a pit. Clean the metal surface and allow the welding material to dry. Melting defect The weld metal and the base metal have not penetrated sufficiently due to insufficient welding current or voltage or due to the welding speed being too fast. Increase the welding current or voltage and decrease the welding speed. Undercutting This is a groove that occurs at the end of the weld beads (the toe of the weld) when the welding current is too high or the welding speed is too fast. Decrease the welding current and the welding speed. Overlapping The molten metal fails to penetrate into the base metal and instead overflows onto the base metal where it piles up. Decrease the welding current and increase the welding speed. Cracking Causes of this defect include mechanical stress during welding, the mixing of impurities, and incorrectly setting the welding temperatures. Eliminate impurities and dry the welding material. Perform preheating and reduce mechanical stress. Slag inclusion Slag inclusion occurs more easily if a fusion defect, undercutting, or overlapping occurs. Use a shielding gas for which a minimal amount of slag occurs. Change the welding conditions. What Is Welding? Welding Types and Troubleshooting Observing Welding with a Digital Microscope 5 Observing Welding with a Digital Microscope Glare removal function Examples of Images Captured by Digital Microscope Wide magnification range Examples of Images Captured by Digital Microscope 3D imaging Examples of Images Captured by Digital Microscope Even for targets with metallic lustre, it is possible to capture images without any glare. Images can be captured from low magnification to high magnification with a single lens. (The minimum magnification is 0.1× and the maximum magnification is 5000×.) The 3D imaging function can be used to capture 3D images of the weld metal. What’s more, optional 3D measurement software can be used to measure profiles. Normal image/VH-Z20 20× Image with glare removal VH-Z00 5× 10× 20× 50× 3D composite image/100× Profile measurement example 6 2D image stitching 20,000 × 20,000 pixels 3D image stitching Bright-field (coaxial illumination), welded and polished surface VH-Z20U 20× Magnified image Magnified image DIC Measurement of weld penetration/VH-Z00 5× 123 Image stitching Examples of Images Captured by Digital Microscope Light shift functions Examples of Images Captured by Digital Microscope Quantification Examples of Images Captured by Digital Microscope The image stitching function can be used to capture images over a wide area without reducing the image resolution of the lens. By using the light shift functions, it is possible to select from a variety of lighting methods such as bright-field, dark-field, DIC, polarisation, combination illumination, and transmitted illumination. Simply
Documents similaires
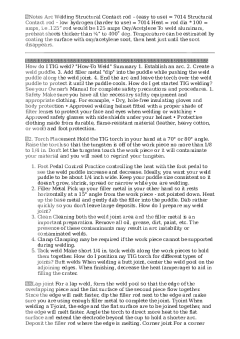
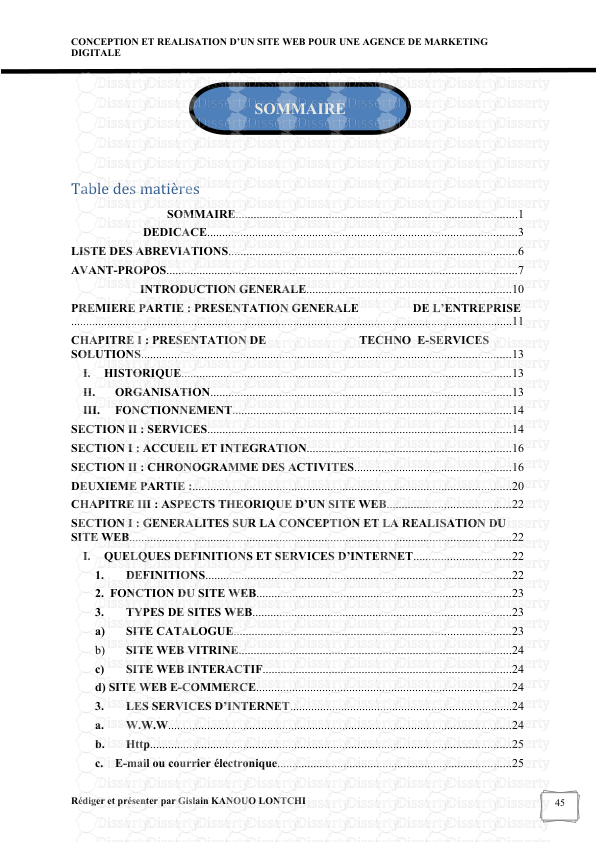
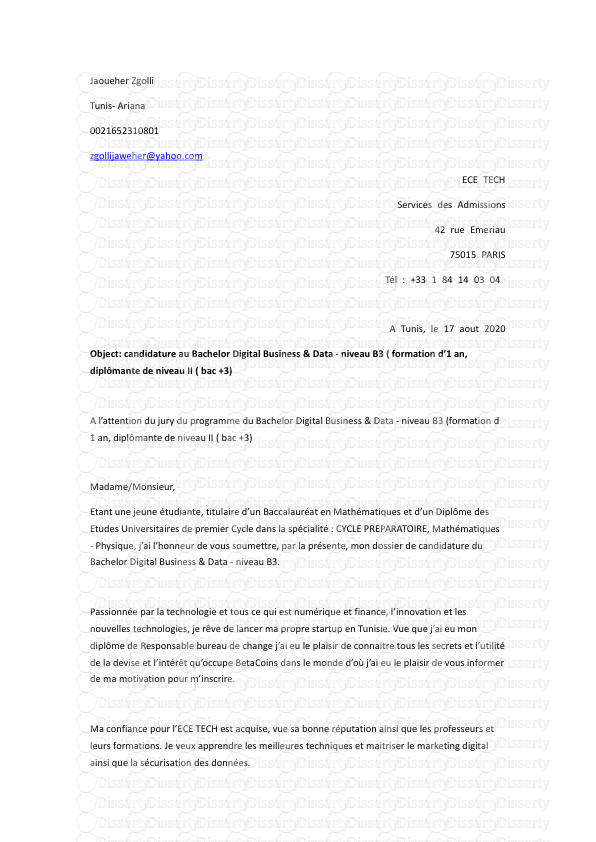
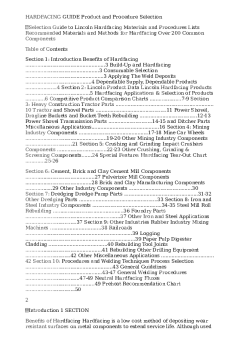
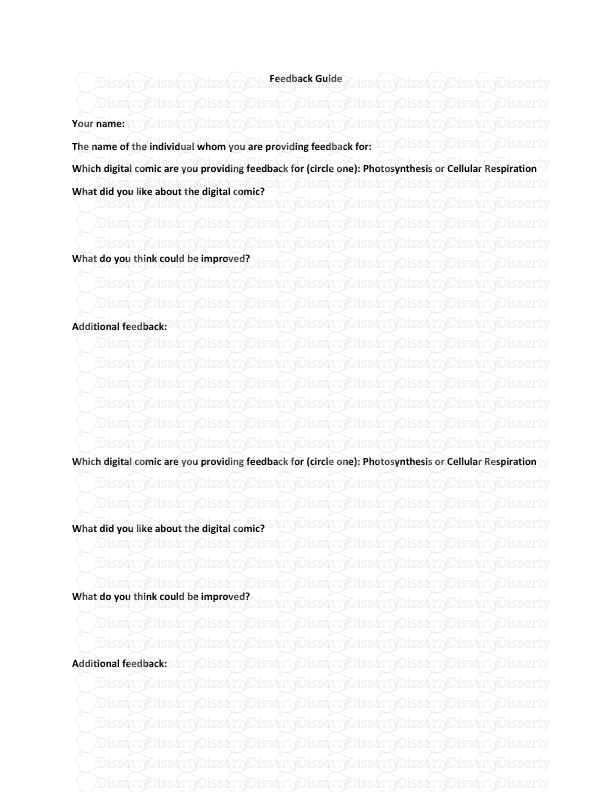
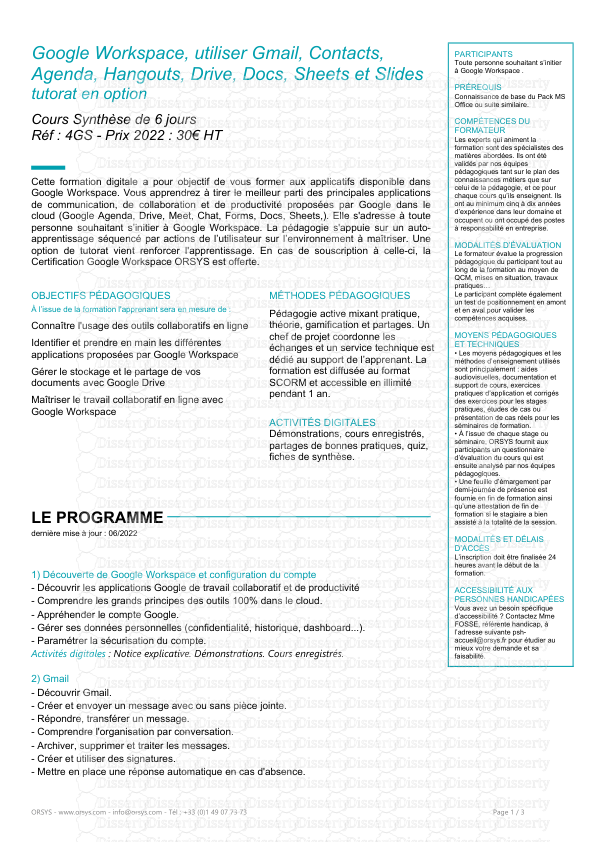
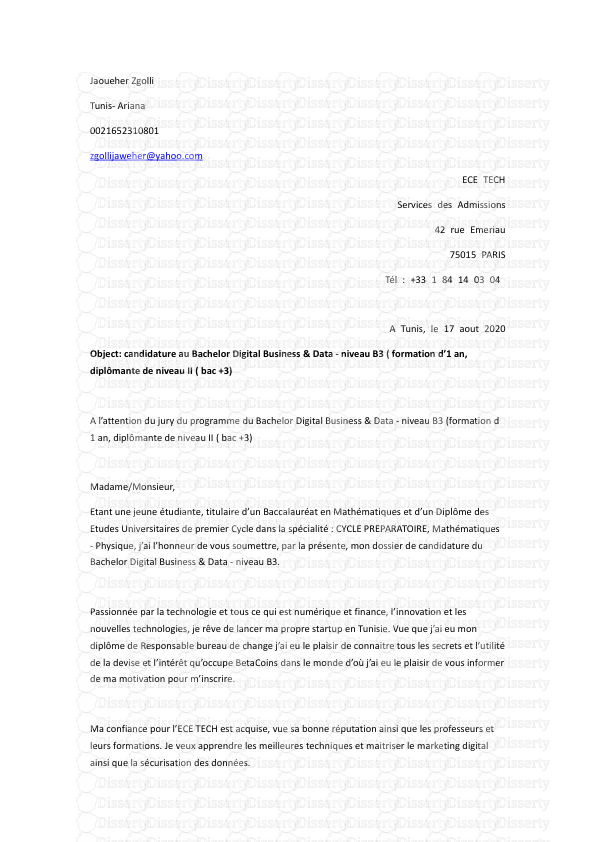
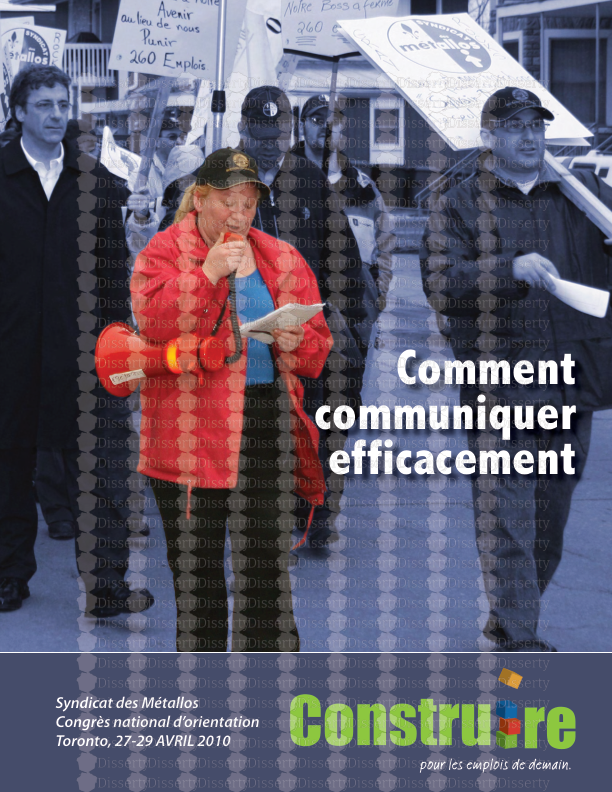
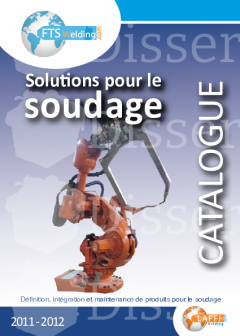
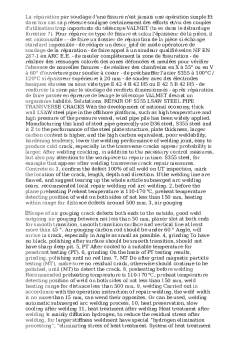
-
35
-
0
-
0
Licence et utilisation
Gratuit pour un usage personnel Attribution requise- Détails
- Publié le Sep 22, 2021
- Catégorie Administration
- Langue French
- Taille du fichier 0.4415MB