Formwork Solutions Guide 2 Trust our formwork solutions Trust FORMrite®, truFOR
Formwork Solutions Guide 2 Trust our formwork solutions Trust FORMrite®, truFORM® and edgeFORM® to perform time and time again, trust they will be straight and true and give you a quality off-form finish. Trust that they have been independently audited and are available FSC® chain of custody certified. Trust our formwork solutions will not only do the job, but do it well. Benefits • Economical – thanks to their durability and reusability • Lighter, straighter and more uniform than traditional alternatives • Faster and easier to install – enhancing productivity reduces forming costs • Improved concrete finish • Engineered Wood Products Association of Australasia (EWPAA) ‘Product Certified’ for peace of mind • Available FSC® ‘Chain of Custody’ certified upon request for Green Star credits For on-site technical and product support, including assistance in sizing freecall 1800 808 131 3 F O R M W O R K S O L U T I O N S Depth (mm) Width (mm) Length (m) Pieces per pack 95 47 Selected lengths of 2.4 m to 6 m (in 600 mm increments) 84 95 65 66 130 77 40 150 77 35 truFORM product range Depth (mm) Width (mm) Length (m) Pieces per pack 100 36 Lengths of 4.8 m or 6 m 50 150 36 40 170 36 35 200 36 30 240 36 25 300 36 20 edgeFORM product range Product range FORMrite is untreated plywood that provides strong support for the forming of concrete walls, floors, roofs, frames and civil engineering structures. Overlaid with a hard durable resin impregnated paper providing a form face suitable to produce a class 2 concrete face. FORMrite is tough and dimensionally stable making it ideal for the rigours of formwork construction. truFORM is structural Laminated Veneer Lumber (LVL) specially manufactured for use in structural concrete formwork applications. edgeFORM is a LVL which has been specially produced for use as edge boards for concrete slabs. A better environmental choice Carter Holt Harvey ensures that its wood is legally sourced from managed forests and offers FSC® ‘Chain of Custody’ certified product upon request. FORMrite, truFORM and edgeFORM achieve less than 0.3mg/l Formaldehyde (equivalent to Super E0) emissions from the final product. Compliance and standards FORMrite formwork plywood is ‘Product Certified’ for peace of mind by the Engineered Wood Products Association of Australasia and is suitable for use meeting requirements of the Building Code of Australia as follows: FORMrite is structural plywood specifically manufactured for use in formwork to AS6669. FORMrite can be designed using AS 1720 Timber Structures code to meet the performance requirements of AS3610 formwork for concrete. Quality control for truFORM and edgeFORM is independently audited and product quality certified by the EWPAA. These factors are important considerations where safety and reliable performance are paramount. Storage, handling and maintenance For best durability and longest re-use potential of FORMrite, truFORM and edgeFORM: • Store under cover in well ventilated area • Handle and stack with care to avoid damage • Stack flat clear of ground on at least three evenly spaced bearers • Re-seal cut edges with acrylic paint • Wet members (and sheets) should have spacers between layer to allow to dry out All statements in this manual shall be read subject to the members being properly stored, handled, installed, used and maintained as appropriate to each application in accordance with this brochure, and subject to the governing codes of practice. Product and purpose Our formwork solution consists of FORMrite, truFORM and edgeFORM and can be used as a complete solution or individually to produce a quality concrete finish. Product Identification Code Nominal Thickness (mm) Length (m) +/– 2 mm Width mm +/– 2 mm Sheets per pack 12-24-5 12 2400, 1800 1200 55 17-10-7 17 2400, 1800 1200 40 17-15-7 17 2400, 1800 1200 40 17-24-7 17 2400, 1800 1200 40 FORMrite product range 4 Trust FORMrite FORMrite is a high quality plywood panel produced predominantly from graded Pinus radiata veneers. These are glued with phenol formaldehyde resin and overlaid with a hard durable resin impregnated paper to give concrete a smooth finish. With a durable A-Type Marine bond, FORMrite can withstand the rigours of construction moisture. Its hard phenolic surface and high quality outer veneers make it durable and reusable. FORMrite gives builders a better surface for pouring concrete and offers a class 2 finish on the first pour (when used in accordance with Carter Holt Harvey installation details and AS 3610 recommendations). FORMrite is a cost effective solution: • Significant number of re-uses • Can be used in modern optimised form systems such as table forms and jump forms • Suits a range of frame spacings, concrete slab thicknesses and surface tolerances • Can be used on steel or timber form frame systems • Lighter in weight than typical imported or rainforest hardwood products • Available FSC® ‘Chain of custody’ on request for Green Star credits FORMrite has a cross-laminated construction, so the panel is less likely to expand or contract when exposed to rain and temperature changes, making it easier to lay forms for large decks. * Tolerance: As per AS/NZS 6669 ** Tolerance: +/- 2% Sheet size (mm) Thickness* (mm) Weight** (kg) 1800 x 1200 12 14.7 17 20.6 2400 x 1200 12 19.6 17 27.5 Standard FORMrite sheet sizes and weights Table 1 Nominal Thickness mm Identification Code Surface Overlay1 gsm Available Stress Grade Parallel to face grain Perpendicular to face grain Moment of Inertia Section Modulus Moment of Inertia Section Modulus I (mm4/mm) Z (mm3/mm) I (mm4/mm) Z (mm3/mm) 12 12-24-5 205/450 F11 115 19 33 8.3 17 17-15-7 45/130 F14, F17 220 25.5 190 26.5 17 17-24-7 205/450 F11, F17 285 33.5 120 19 1. Phenolic impregnated paper Stress Grades and Section Properties for Standard FORMrite constructions Table 2 Understanding Identification Codes In the example, 17-15-7 is a 17 mm nominal thick panel with a 1.5 mm face veneer and 7 plies. 17-15-7 Overall Nominal Number of Thickness thickness of plies (veneers) face veneer in the panel Specification FORMrite is plywood manufactured and structurally characterised specifically for use in Formwork to the requirements of AS 6669-2007 Adhesive Phenolic Bond Type A (Marine) AS/NZS 2098 and AS 2754 Length and Width +/-1.5 mm Thickness Tolerance +/- 4% (Overlay not included) Pack colour code All FORMrite packs are colour coded for easy identification. Product Stencil / Corner Marks Yellow F22 Green F17 Red F14 Black F14 For on-site technical and product support, including assistance in sizing freecall 1800 808 131 5 F O R M W O R K S O L U T I O N S F O R M W O R K S O L U T I O N S F O R M W O R K S O L U T I O N S Installation Framing and plywood thickness Framing centres depend on the F grade, plywood identification code and the direction of the face grain for a given thickness of wet concrete, as well as the design limit decided by the designer. Sheet layout Maximum joist spacings are provided in Table 3 below for FORMrite sheets laid with the face grain (long edge) across and joists. Allow a 2 to 3 mm expansion gap on all sheet edges. Use polystyrene filler or joint sealer in the expansion gaps if required. For maxiumum sheet performance sheets to be laid with face grain perpendicular to the span (across joists). Note: 1. FORMrite plywood is manufactured and characterised to AS6669:2007 for design using AS1720.1:2010 2. In preparation of the above table, deflections were limited to the lesser of span/270 or 3 mm. (Class 2 finish to AS3610) Finish quality however is dependent upon combinations of sheeting, joist, bearer, support deformation and the accuracy and alignment in set-up. The use of the table should not therefore be interpreted to necessarily guarantee achievement of a class two finish. 3. The design has assumed, (a) the most consecutive of two or three span, (b) all spans equally loaded, and (c) all spans equal CONCRETE SLAB THICKNESS (mm) PLYWOOD IDENTIFICATION CODE STRESS GRADE 100 150 200 300 400 600 1000 FACE GRAIN PERPENDICULAR TO SPAN (ACROSS JOISTS) MAXIMUM ALLOWABLE JOIST SPACING (mm) 12-24-5 F11 450 400 400 300 300 300 225 17-15-7 F11 480 480 480 450 400 400 300 17-15-7 F14 600 480 480 480 450 400 300 17-15-7 F17/F14 600 480 480 480 480 400 300 17-24-7 F14 600 600 480 480 480 450 300 17-24-7 F17 Formwork assembly The objective of fixing the elements of a formwork assembly is to provide an appropriately strong rigid form that has ease of handling, erection and stripping. The formface fixing should be designed to: 1. Hold joints tightly together; 2. Fix the plywood and framing so the formwork assembly becomes a cohesive structure for handling and stripping; and 3. Enable easy dismantling and uploads/S4/ formwork-solutions-guide 1 .pdf
Documents similaires
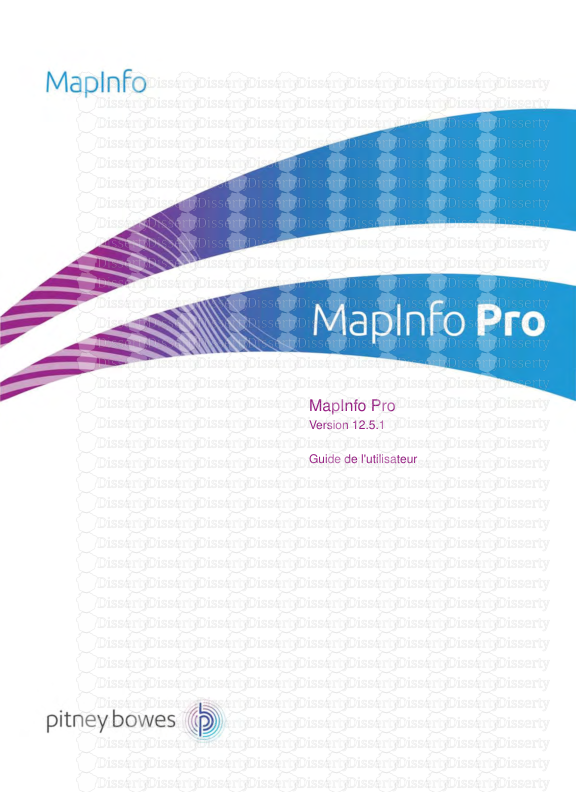
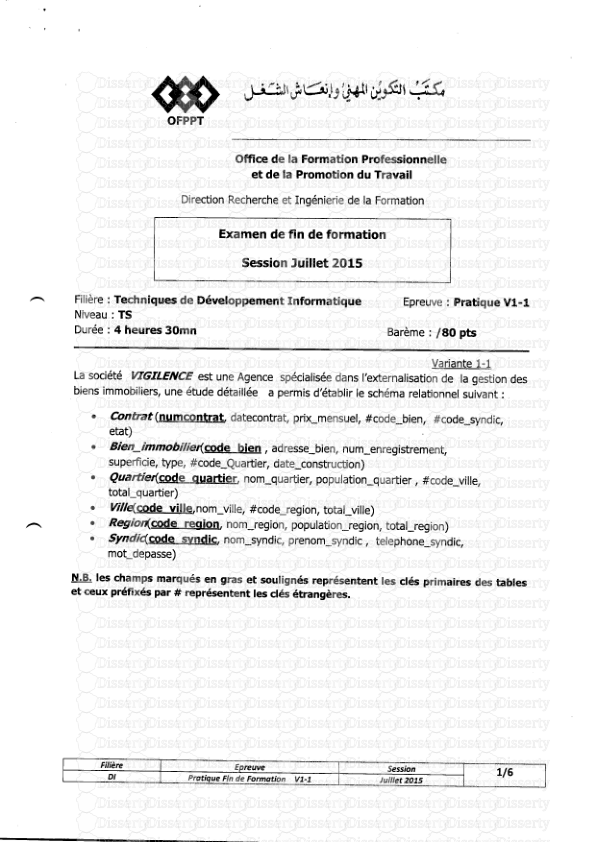
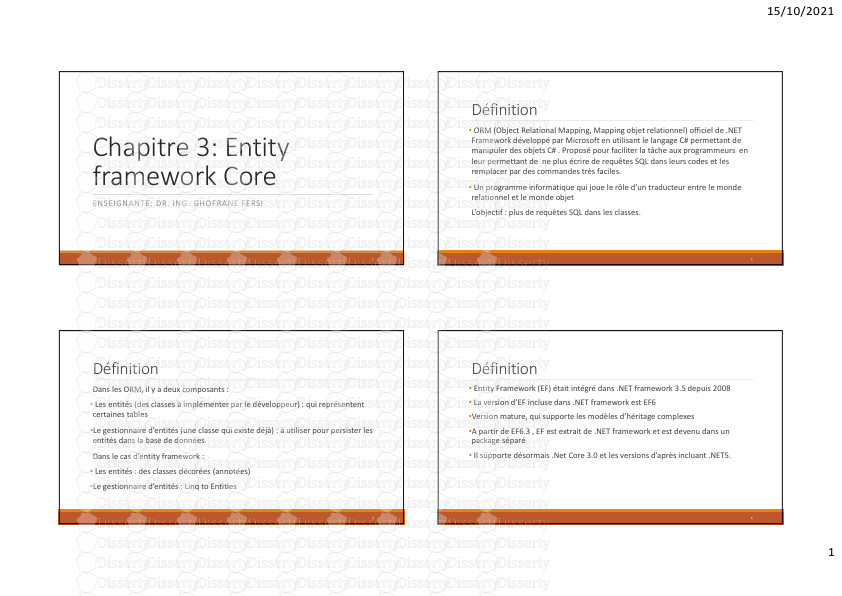
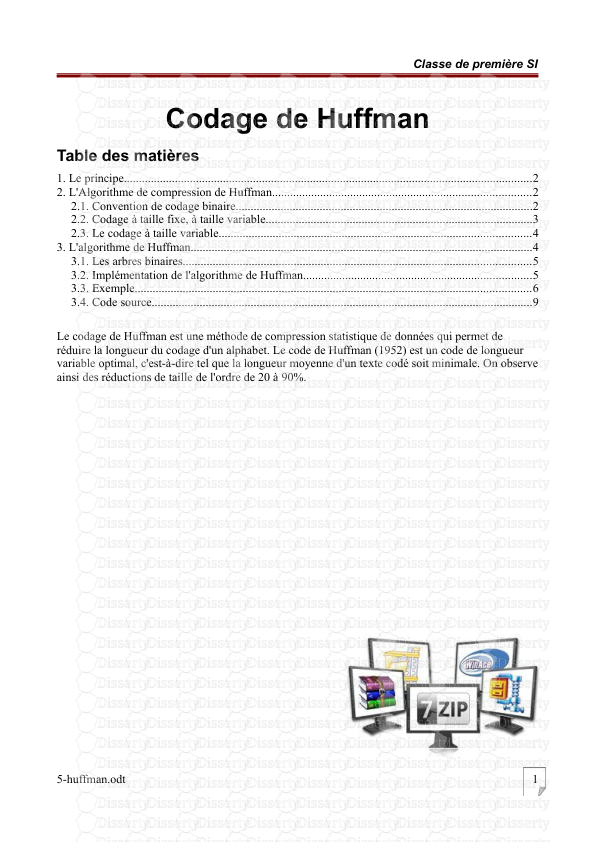

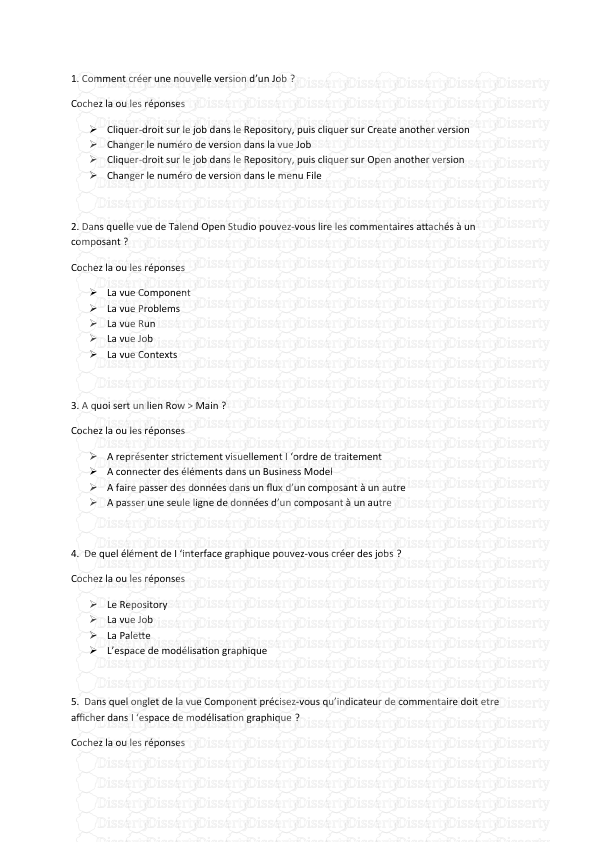
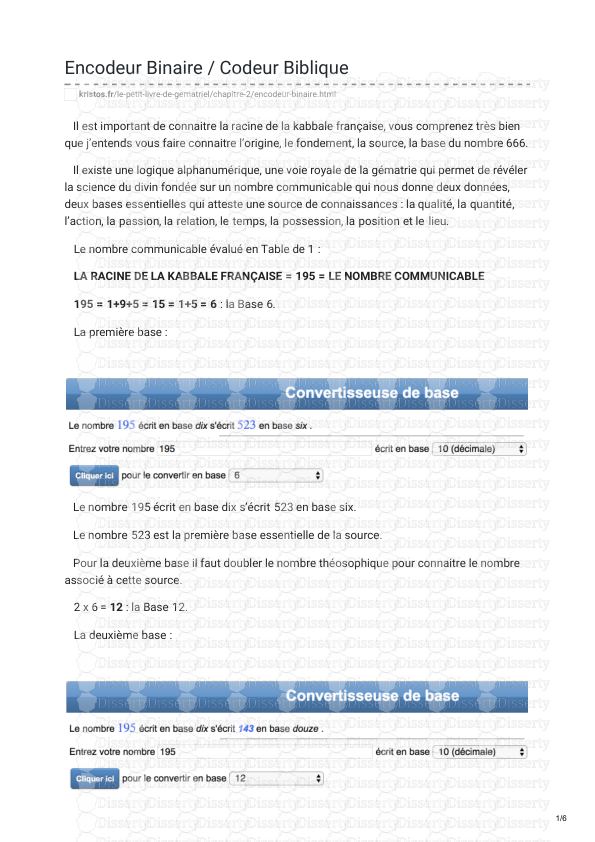
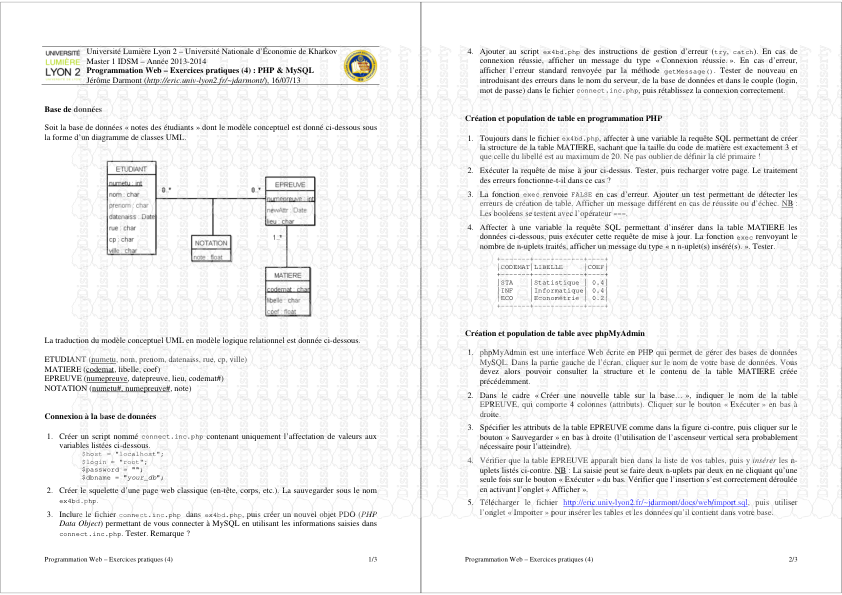
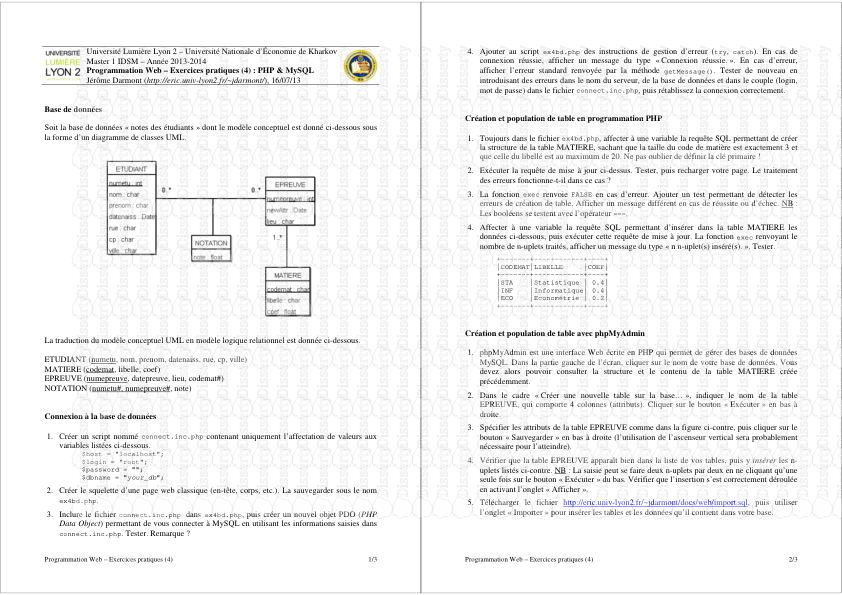

-
43
-
0
-
0
Licence et utilisation
Gratuit pour un usage personnel Attribution requise- Détails
- Publié le Aoû 24, 2021
- Catégorie Law / Droit
- Langue French
- Taille du fichier 2.0504MB