The Ultimate Guide to Stereolithography (SLA) 3D Printing Stereolithography (SL
The Ultimate Guide to Stereolithography (SLA) 3D Printing Stereolithography (SLA) is an additive manufacturing — commonly referred to as 3D printing — technology that converts liquid materials into solid parts, layer by layer, by selectively curing them using a light source in a process called photopolymerization. SLA is widely used to create models, prototypes, patterns, and production parts for a range of industries from engineering and product design to manufacturing, dentistry, jewelry, model making, and education. In this comprehensive guide, you’ll learn about the different SLA systems, various materials and their characteristics, and how SLA compares to other technologies on the market. March 2017 | formlabs.com Table of Contents Brief History . . . . . . . . . . . . . . . . . . . . . . 3 SLA Systems . . . . . . . . . . . . . . . . . . . . . . . . 4 Right-Side Up SLA . . . . . . . . . . . . . . . . . . . 4 Upside-Down (Inverted) SLA . . . . . . . . . . . . . . 5 Understanding Supports . . . . . . . . . . . . . . . . 6 Comparison of SLA systems . . . . . . . . . . . . . . . 7 Materials . . . . . . . . . . . . . . . . . . . . . . . . . . 8 The Polymerization Process . . . . . . . . . . . . . . 8 Characteristics of Resins and Plastics . . . . . . . . . . 9 Composition of Photopolymet Resin . . . . . . . . 9 Isotropy vs. Anisotropy . . . . . . . . . . . . . . . . . 9 Post-Curing . . . . . . . . . . . . . . . . . . . . . . 10 Thermosettings vs. Thermoplastics . . . . . . . . . . . 11 SLA Materials by Application . . . . . . . . . . . . . . 11 Standard . . . . . . . . . . . . . . . . . . . . . 12 Engineering . . . . . . . . . . . . . . . . . . . 12 Dental . . . . . . . . . . . . . . . . . . . . . . 13 Jewelry . . . . . . . . . . . . . . . . . . . . . 13 Experimental . . . . . . . . . . . . . . . . . . . 14 Why Desktop SLA? . . . . . . . . . . . . . . . . . . . . . 15 High Resolution and Smooth Surface Finish . . . . 15 Accuracy and Repeatability . . . . . . . . . . . . 16 Design Freedom . . . . . . . . . . . . . . . . . 16 Rapid Prototyping . . . . . . . . . . . . . . . . 17 Functional Parts for a Wide Range of Applications . 18 Costs and Value . . . . . . . . . . . . . . . . . 19 Printing Process . . . . . . . . . . . . . . . . . . . . . . 20 Design . . . . . . . . . . . . . . . . . . . . . . 20 Prepare . . . . . . . . . . . . . . . . . . . . . 20 Print . . . . . . . . . . . . . . . . . . . . . . . 21 Clean . . . . . . . . . . . . . . . . . . . . . . 21 Cure . . . . . . . . . . . . . . . . . . . . . . . 22 Finish . . . . . . . . . . . . . . . . . . . . . . 22 Get Started with SLA 3D Printing . . . . . . . . . . . . . . 23 THE ULTIMATE GUIDE TO STEREOLITHOGRAPHY (SLA) 3D PRINTING 3 Brief History The SLA process first appeared in the early 1970s, when Japanese researcher Dr. Hideo Kodama invented the modern layered approach to stereolithography of using ultraviolet light to cure photosensitive polymers. The term stereolithography itself was coined by Charles (Chuck) W. Hull, who patented the technology in 1986 and founded the company 3D Systems to commercialize it. Hull described the method as creating 3D objects by successively “printing” thin layers of a material curable by ultraviolet light, starting from the bottom layer to the top layer. Later, the definition was extended to any material capable of solidification or alteration of its physical state. Today, 3D printing and additive manufacturing (AM) describe numerous individual processes, which vary in their method of layer manufacturing, material, and machine technology used. As patents began to expire at the end of the 2000s, the introduction of desktop 3D printing widened access to the technology, with fused deposition modeling (FDM) first gaining adoption in desktop platforms. While this affordable extrusion- based technology aided the widespread use of 3D printing, the quality of these parts has limited the use of these machines, since repeatable, high-precision results are crucial for professional applications. Prototypes of the Form 1, the first desktop SLA 3D printer. SLA soon followed FDM to the desktop, when Formlabs adapted the technology in 2011. SLA brought the promise of high resolution 3D printing—previously limited to industrial systems—in a much smaller and more affordable setup, with a wide range of print materials. These capabilities made 3D printing accessible for a variety of custom applications, including engineering, product design and manufacturing or the dental and jewelry industries. SLA Systems SLA belongs to a family of additive manufacturing technologies known as vat photopolymerization. These machines are all built around the same principle, using a light source—UV laser or projector—to cure liquid resin into hardened plastic. The main physical differentiation lies in the arrangement of the core components, such as the light source, the build platform, and the resin tank. RIGHT-SIDE SLA Right-side up SLA machines are built around a large tank containing the liquid photopolymer (resin), and the build platform. The UV laser focuses onto the surface of the resin, tracing a cross-section of the 3D model. The build platform then descends a distance equal to the thickness of a single layer, and a resin- filled blade sweeps across the vat to recoat it with fresh material. The process builds consecutive layers on top of the others until the part is finished. Schematic of the right-side up SLA systems. This approach mostly appears in large scale industrial systems, and before the appearance of desktop systems it was the standard approach to stereolithography. Its benefits include some of the largest build volumes in 3D printing, low forces on the parts during the print process, and in turn high detail and accuracy. THE ULTIMATE GUIDE TO STEREOLITHOGRAPHY (SLA) 3D PRINTING 4 Due to the large setup, maintenance requirements, and material volume, right-side up SLA requires a high initial investment and is expensive to run. The entire build area must be filled with resin, which can easily mean 10-100+ liters in raw material, making it a time consuming task to handle, maintain, filter and swap materials. These machines are highly sensitive to being stable and level, any inconsistency can lead to the recoater toppling the part, leading to print failure. UPSIDE-DOWN (INVERTED) SLA As the name suggests, in inverted stereolithography, the process is turned upside down. This method uses a tank with transparent bottom and non-stick surface, which serves as a substrate for the liquid resin to cure against, allowing for the gentle detachment of newly-formed layers. A build platform is lowered into a resin tank, leaving space equal to the layer height in between the build platform, or the last completed layer, and the bottom of the tank. Schematic of the upside-down (inverted) SLA systems The UV laser points at two mirror galvanometers, which direct the light to the correct coordinates on a series of mirrors, focusing the light upward uploads/Geographie/ sla-guide 1 .pdf
Documents similaires
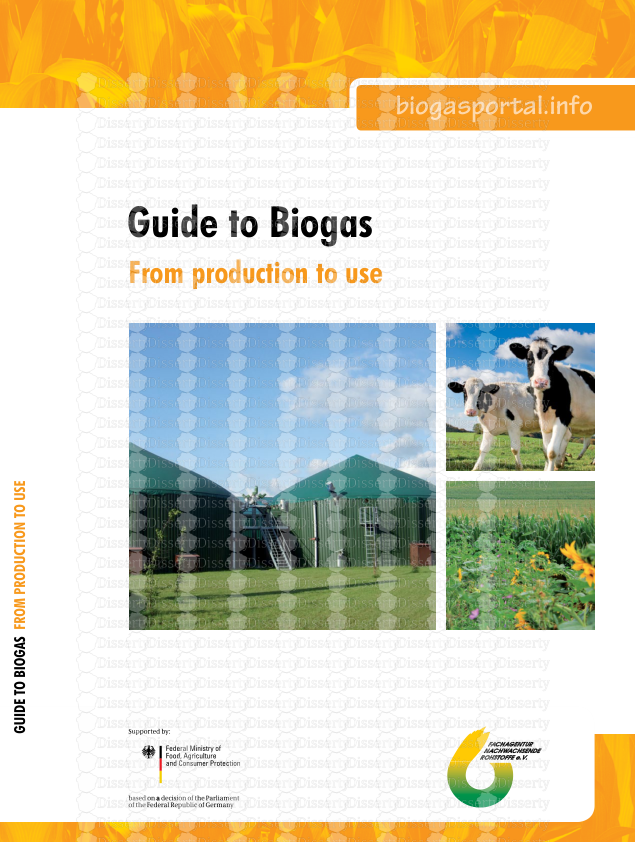
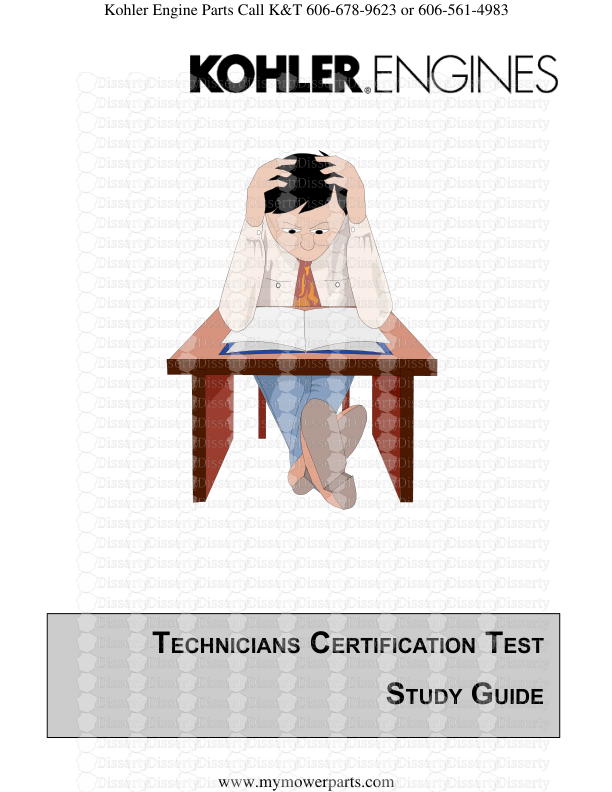
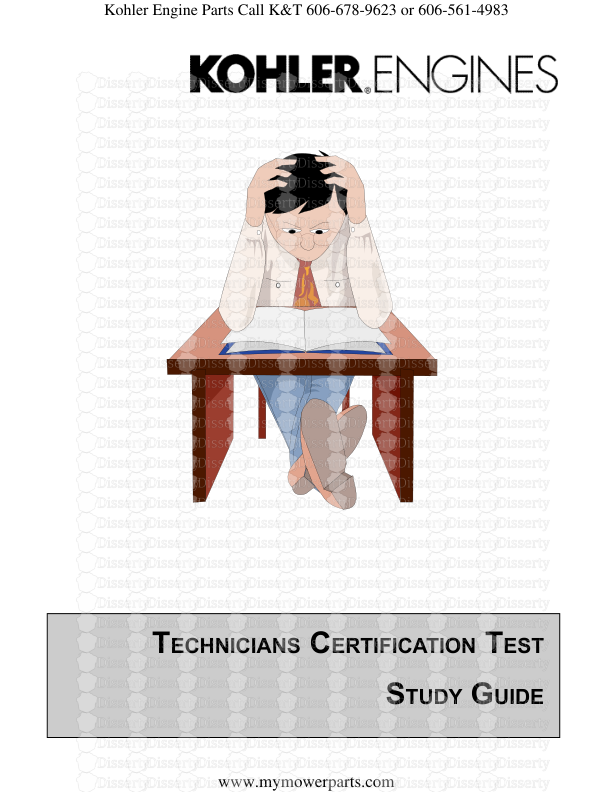
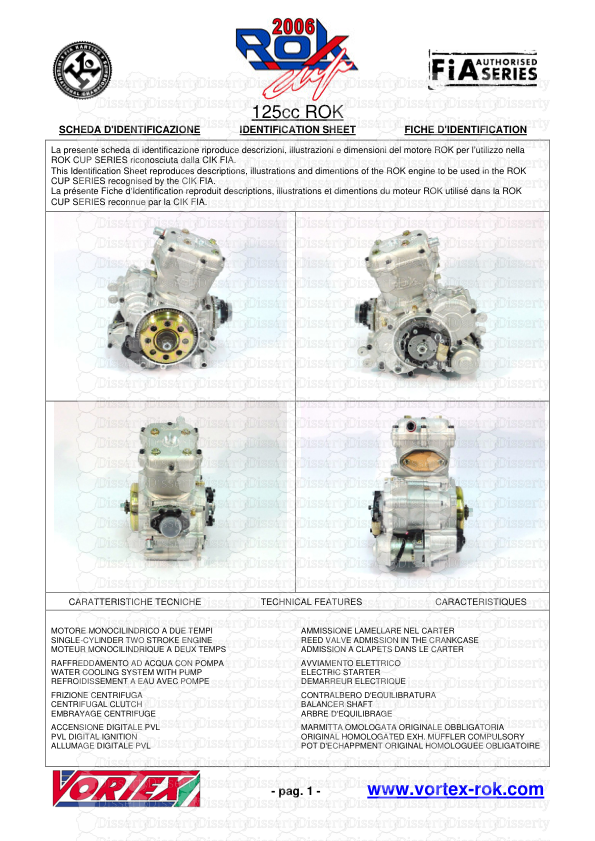
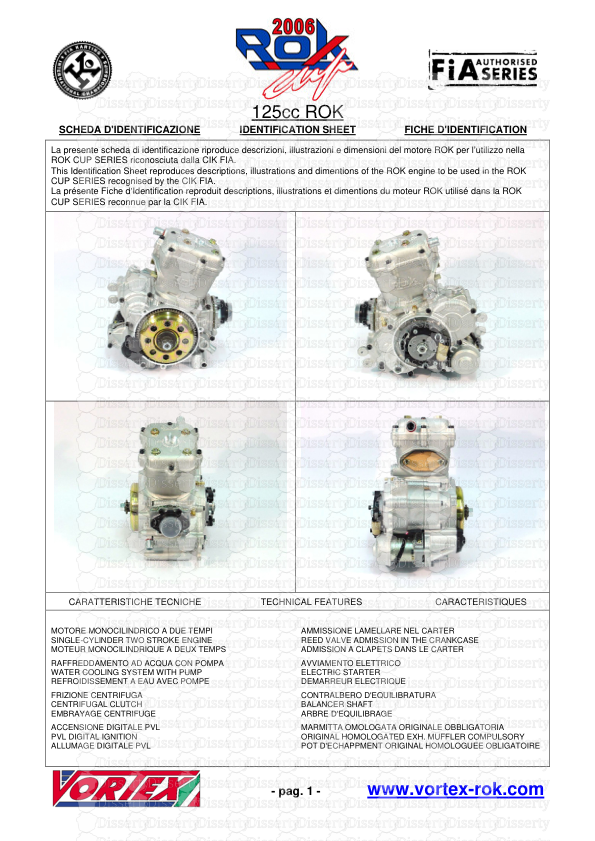
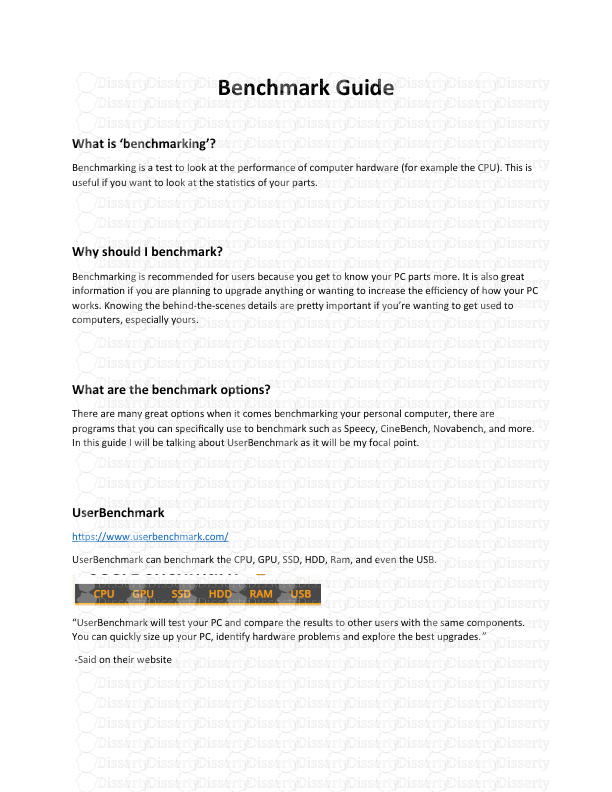
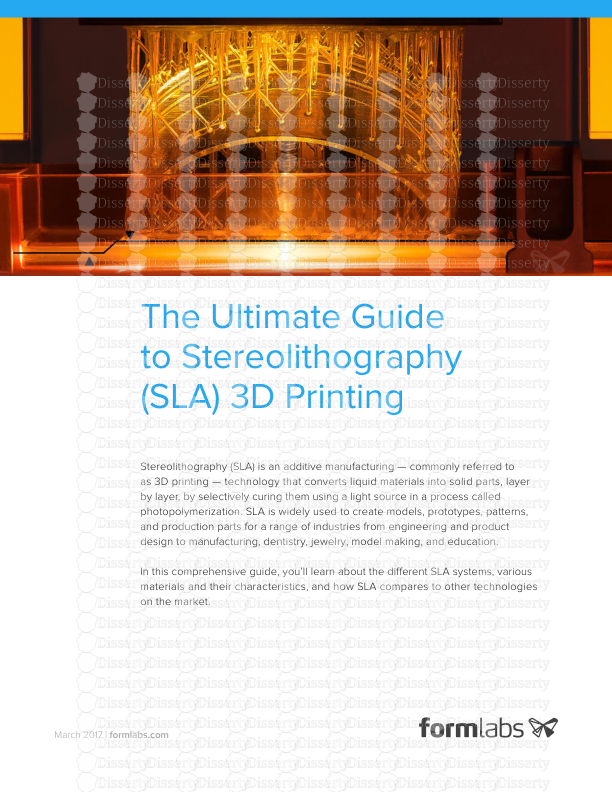
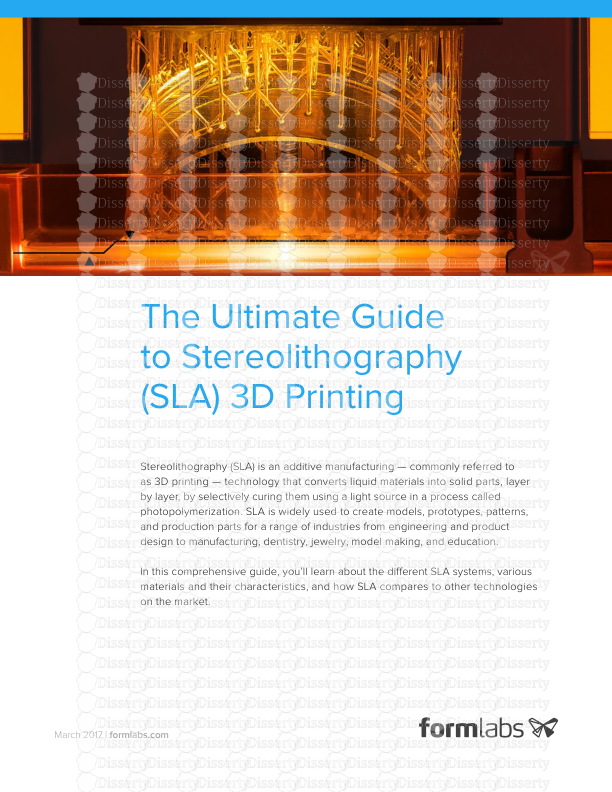
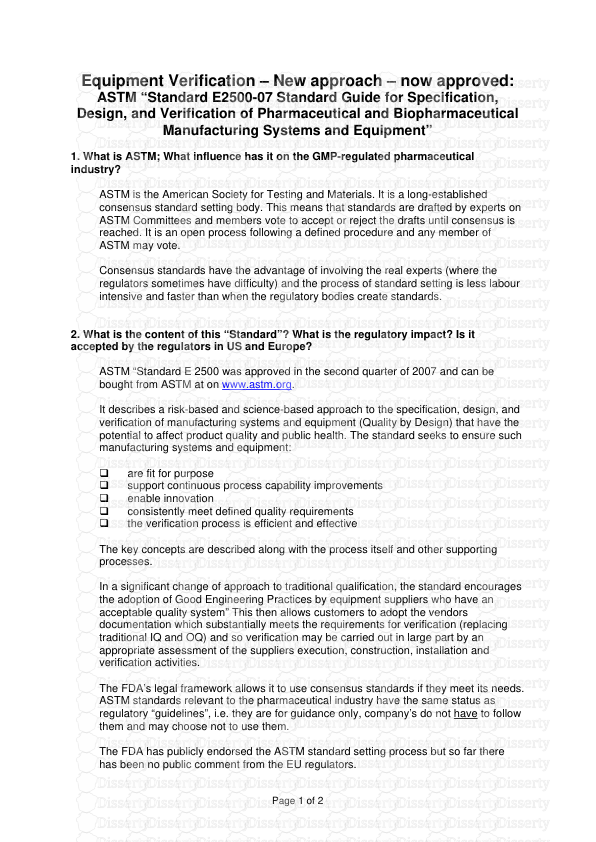
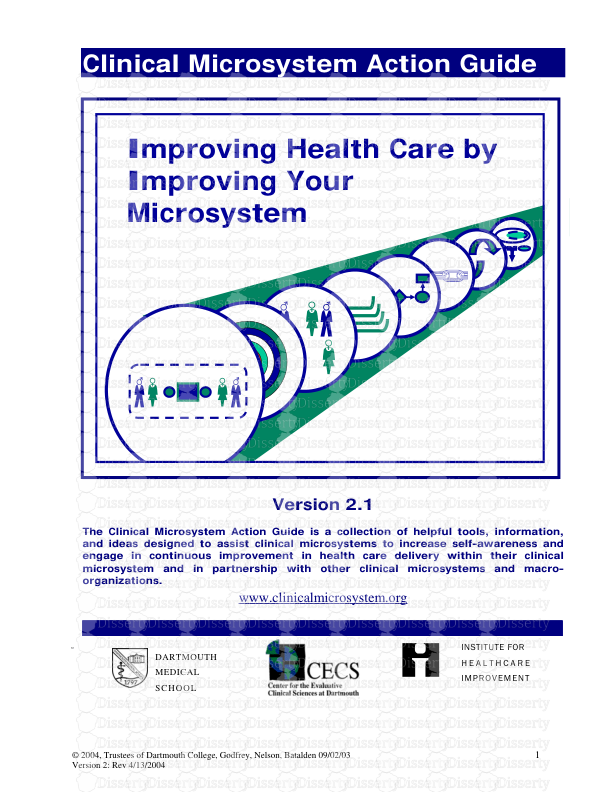
-
103
-
0
-
0
Licence et utilisation
Gratuit pour un usage personnel Attribution requise- Détails
- Publié le Oct 28, 2022
- Catégorie Geography / Geogra...
- Langue French
- Taille du fichier 4.1281MB