Attendus pour le document 0 Quick Response PDCA [1] [2] [3] [4] [5] [6] [7] [8]
Attendus pour le document 0 Quick Response PDCA [1] [2] [3] [4] [5] [6] [7] [8] [9] [10] [11] [12] [13] [14] [15] [16] [17] [18] Pilote - Indiquer le nom du pilote responsable de gérer le problème, et sa fonction - Indiquer son numéro de téléphone et/ou son adresse email Equipe Indiquer le nom des personnes impliquées dans la résolution du problème et leur fonction, y compris les opérateurs. Indiquer "opérateur" derrière le nom des opérateurs. Numéro d'incident Sartex Indiquer le numéro d'incident Sartex (QIM) ou autre référence interne Numéro d'incident client Indiquer le numéro de référence utilisé par le client Date de la notification client Indiquer la date à laquelle le client a notifié le problème pour la première fois Date et heure d'ouverture Indiquer la date et l'heure à laquelle Sartex a ouvert le PDCA dans la base de données concernée (QIM, SRM…) Origine Cocher la case appropriée selon le type de problème Client / nom du contact Indiquer le client concerné et le nom du contact chez le client avec son numéro de téléphone et/ou son email Véhicule / Moteur / Réf. client Indiquer le véhicule et la motorisation impactés et la référence client Produit (Désignation + Ref) Sartex Indiquer la désignation et la référence Sartex de la pièce concernée Sécurité / Réglementation Si le problème comprend des points sécurité / réglementation, cocher la case "O". Si non, cocher la case "N". Description du problème tel qu'il est vu par le client / localisation du problème sur la pièce Indiquer le problème tel qu'il est décrit par le client, y compris sa localisation sur la pièce. Date du DMS produit Indiquer la date du DMS (démarrage série) pour la pièce concernée chez Sartex Date de la dernière modification Si applicable, indiquer la date de la dernière modification produit ou process Que s'est-il passé ? - Description du problème avec des faits clairs et précis tels que défini par le client - Information concernant la récurrence - Eléments de traçabilité des pièces défectueuses Pourquoi est-ce un problème ? Grâce à cette cellule, on doit comprendre quel est l'impact du problème pour le site d'assemblage et/ou pour le client final. Ces éléments doivent être quantifiés (données) - Quel est l'effet client du défaut ? - Impact sur la gestion logistique de la pièce - Impact sur la manipulation de la pièce - Impact sur l'assemblage de la pièce - Impact technique dans l'application - Impact sur la fiabilité du produit - Quelle est l'importance du problème ? Quand a-t-il été détecté ? L'objectif est de savoir exactement quand le défaut a été détecté pour la première fois par le client : - Date de la détection du problème - Temps exact, heure, minute - Equipe de fabrication En complément de la date de détection, les données suivantes doivent être ajoutées pour les problèmes garantie : - Kilométrage du véhicule - Date de l'immatriculation du véhicule - Date de notification du défaut à Sartex Qui l'a détecté (nom de l'opérateur) ? Pour savoir qui a détecté le défaut, il est important d'avoir la possibilité de demander des données plus précises. - Nom de la personne ou son numéro d'enregistrement - Fonction de la personne, qualification En complément de la date de détection, les données suivantes, si disponibles, doivent être ajoutées pour les problèmes garantie : - Nom du garage - Nom de l'utilisateur final [19] [20] [21] [22] [23] [24] [25] [26] [27] [28] [29] [30] Où a-t-il été détecté ? - Nom du magasin, plateforme …. - Nom de la ligne d'assemblage - Etape du process d'assemblage y compris les étapes avant et après (réception, magasin, sous assemblage, assemblage, essai, logistique, garage, terrain …) Comment a-t-il été détecté ? La manière et les circonstances selon lesquelles le défaut a été détecté est capital pour comprendre pourquoi le process Sartex n'a pas permis de détecter le défaut en interne - Opération réalisée pour détecter le défaut - Référence au mode opératoire si applicable - Type d'outil ou de machine utilisé pour détecter le défaut - Paramètres process y compris la distance, le temps pour détecter le problème visuellement, les limites ou les pièces types utilisées - Conditions environnementales telles que la lumière, la température et le bruit ambiant … Combien de pièces mauvaises ? - Préciser combien de pièces mauvaises ont été trouvées défectueuses au moment de la détection dans le process client - Préciser quel est le coût si applicable Quelle est la différence entre les pièces bonnes et les pièces mauvaises ? Le défaut doit être décrit comme un écart entre la pièce bonne et la pièce mauvaise. Se focaliser sur la pièce et non sur l'application ou le process client. Ces données préparent l'équipe à regarder dans la bonne direction pour l'analyse. Cette définition va être le point de départ de la FTA. - Description du problème avec des faits clairs et précis, tel qu'il est vu par Sartex La pièce a-t-elle été produite sur le process standard ? Toute dérogation produit ou process, ou rework, ou opération réalisée par une personne non qualifiée doit être prise en compte. Si la réponse est NON, l'écart doit être clairement décrit, et la référence des documents associés mentionnée. Utiliser les informations de traçabilité sur la pièce pour répondre à cette question. Quand a-t-elle été produite par Sartex ? - Date de production de la pièce - Date exacte issue des données de traçabilité des pièces et de leurs composants, peut inclure la date de test de la pièce - Equipe de production - Données de traçabilité si disponible Qui l'a produite ? Ces informations sont relatives à la personne travaillant sur le poste où le défaut a été généré, et à la personne en charge de la détection du défaut. - Nom de la personne et/ou son numéro d'enregistrement - Fonction de la personne, qualification, statut (intérimaire ou Sartex) - Nom de la société si applicable (dans le cas d'un sous traitant) Dans quelle autre application ou process le produit est-il utilisé ? Si applicable, des données précises sont attendues - Désignation du produit - Références Sartex et/ou client - Applications client - Etendre la réponse aux autres différents produits ou process si le même symptôme est potentiellement présent (même machine d'assemblage, par exemple) Est-ce que l'on arrête le défaut quand on réinjecte le produit dans le process standard ? En allant sur le terrain, en utilisant les moyens d'essais ou en appliquant les modes opératoires avec les limites définies, sans avertissement spécifique des opérateurs, arrête-t-on le défaut ? Si la réponse est OUI, préciser les éléments qui conduisent à la détection (référence de la machine, nom et qualification de l'opérateur, mode opératoire utilisé ...) Si les opérateurs concernés ont été prévenu pour faire le test, donner cette information Un problème similaire est-il apparu auparavant chez le client ou en interne ? Consulter les QRQC Ligne, UAP et projet pour répondre à cette question - Si oui, combien de fois, compléter l'information via le graphique Refus Totaux Fin de Ligne (TLR) si applicable. - Désignation et référence produit - Dates de détection des défauts précédents - Localisation de la détection - Quantité de défauts - Référence de l'analyse précédente (QIM ou interne) Pièce mauvaise Insérer une photo ou un dessin de la pièce ou du composant mauvais, montrant clairement quel est le défaut, où il est localisé sur la pièce, et quelle est la différence avec une bonne pièce (y compris les mesures si applicable) Pièce bonne Insérer une photo ou un dessin de la pièce ou du composant bon, dans la même position, même distance, même angle, même éclairage, montrant clairement quelle est la situation bonne (y compris les mêmes mesures si applicable) [31] [32] [33] [34] [35] [36] [37] [38] [39] [40] [41] [42] Origine de la pièce Indiquer quelle pièce a été sélectionnée comme référence de pièce bonne. La pièce bonne doit être aussi comparable que possible avec les pièces mauvaises - Période / date de production ... - Pour la garantie, le kilométrage doit être le plus proche possible du kilométrage de la pièce mauvaise - Machine, cavité du moule - Pour les problèmes projet, préciser quel niveau de développement a été pris en compte pour la pièce bonne (prototype, DV, PV ...) - Si les pièces bonnes et mauvaises ne peuvent être 100% comparables, préciser les limites de la comparaison Activité de tri pour protéger le client Tous les stocks (produits finis + WIP + composants) potentiellement touchés par le problème doivent être triés L'opération de tri doit inclure les stocks SECONDE MONTE internes et externes (y compris VS) si applicable - Formaliser une instruction de tri avec une feuille d'enregistrement pour collecter toutes les données pertinentes permettant d'améliorer la connaissance du défaut - Résultats du tri - Traçabilité des pièces OK/KO avec : - Date, heure, équipe de production - Traçabilité des équipement (moule, cavité, numéro de machine ou de ligne …) - Traçabilité opérateur Situation Refus Totaux Fin de Ligne (TLR) uploads/Industriel/ pdca-fta.pdf
Documents similaires
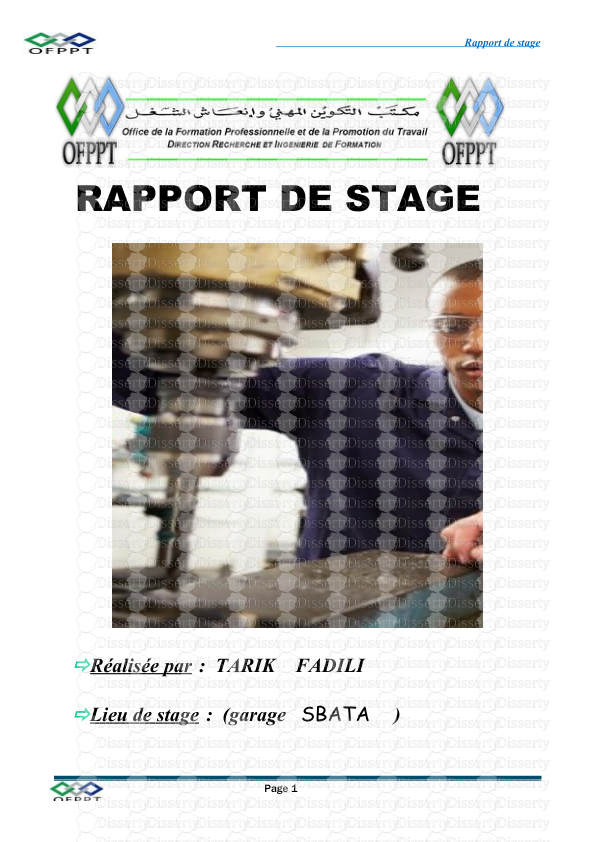
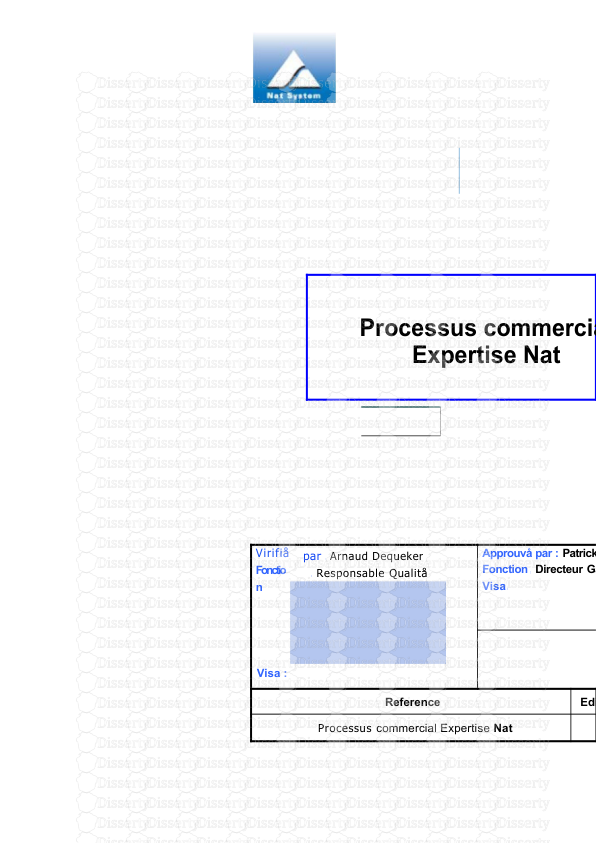

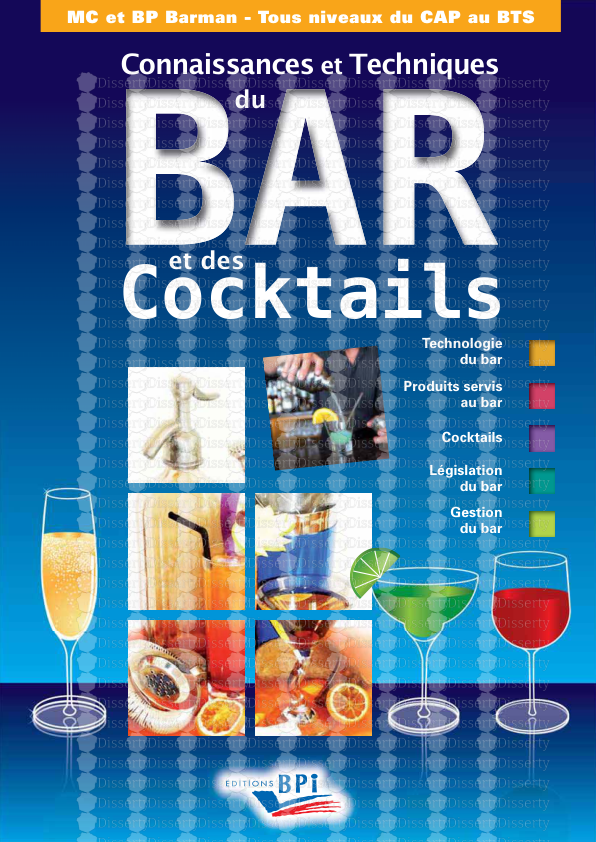
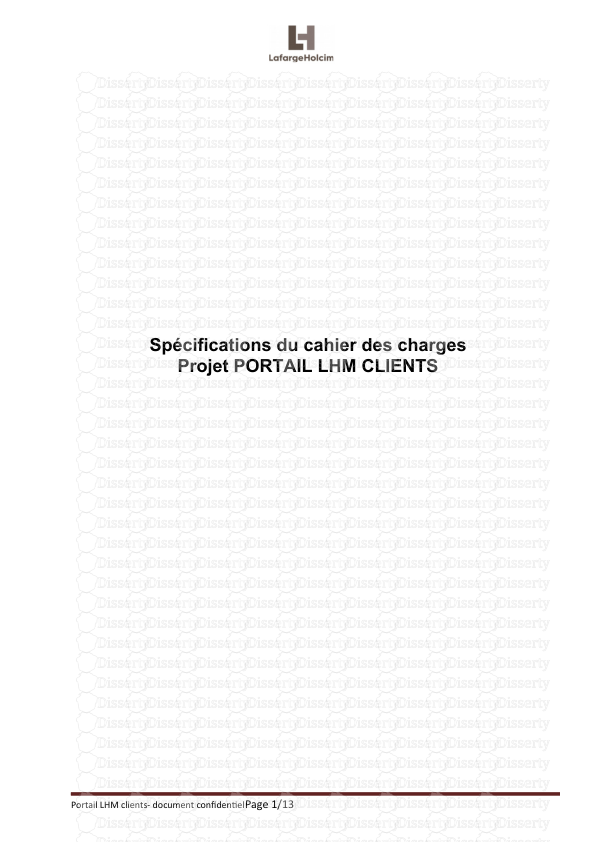
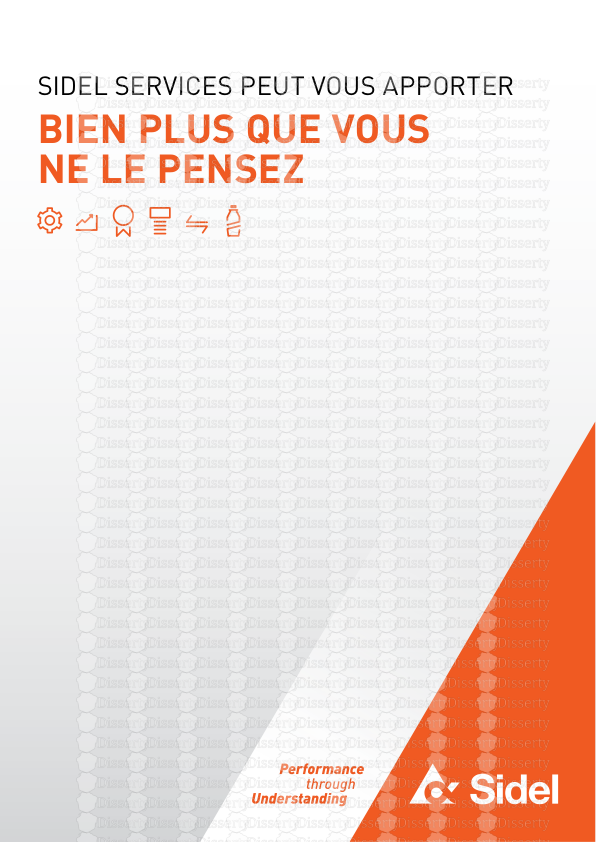
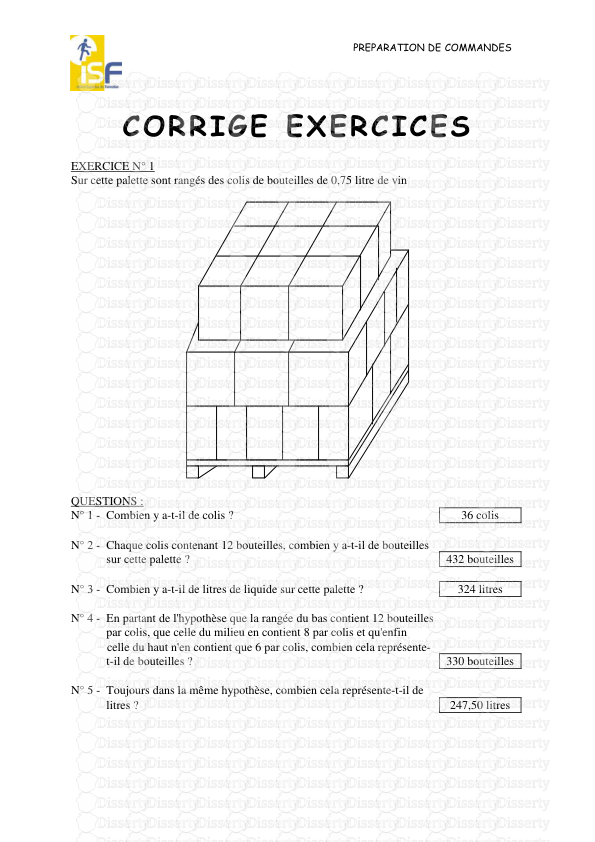
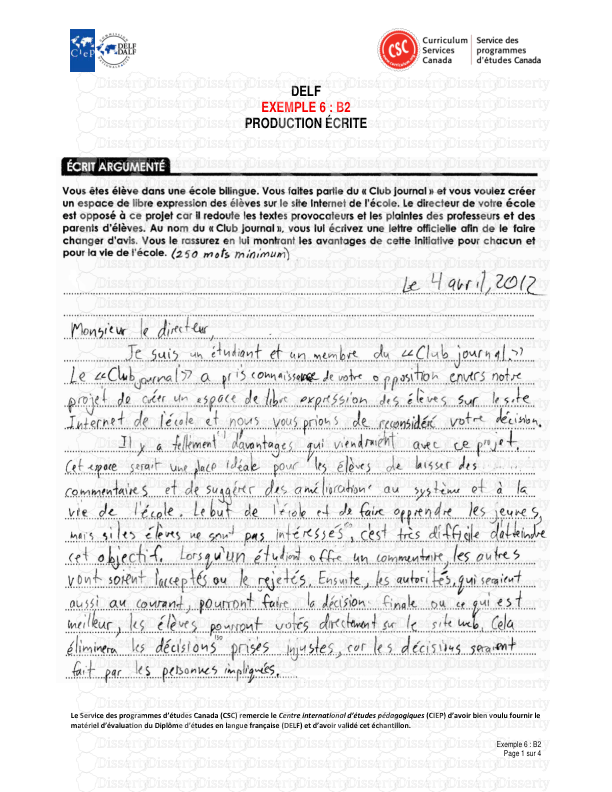

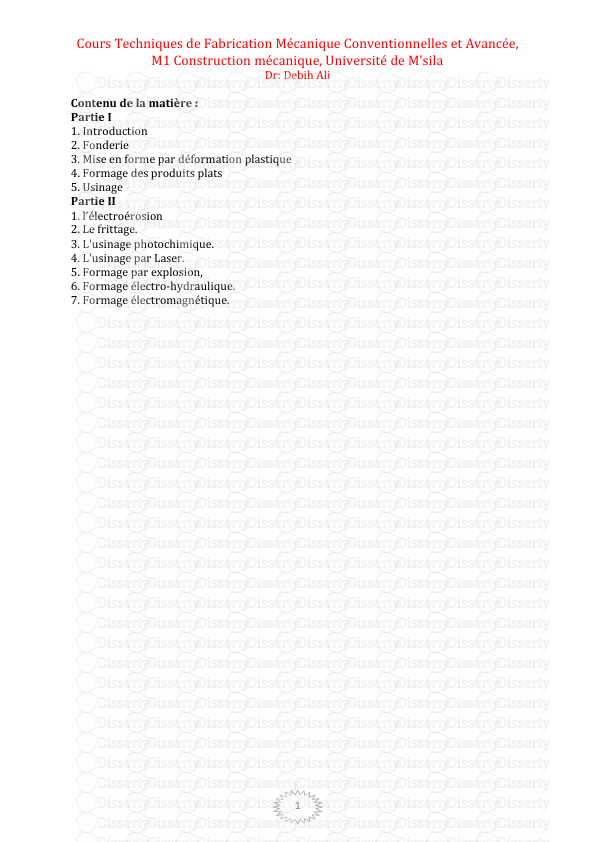
-
42
-
0
-
0
Licence et utilisation
Gratuit pour un usage personnel Attribution requise- Détails
- Publié le Mai 03, 2022
- Catégorie Industry / Industr...
- Langue French
- Taille du fichier 0.3873MB