SERV1810 January 2006 TECHNICAL PRESENTATION AD30 UNDERGROUND ARTICULATED TRUCK
SERV1810 January 2006 TECHNICAL PRESENTATION AD30 UNDERGROUND ARTICULATED TRUCK (UAT) INTRODUCTION SERVICE TRAINING MEETING GUIDE (STMG) GLOBAL SERVICE LEARNING AD30 UNDERGROUND ARTICULATED TRUCK (UAT) INTRODUCTION AUDIENCE Level II - Service personnel who understand the principles of machine system operation, diagnostic equipment, and procedures for testing and adjusting. CONTENT This presentation provides an introduction and describes the components and systems operation of the Caterpillar Monitoring System, engine, electrical system, power train, hydraulic system, steering, brakes, and dual speed control system for the AD30 machines. This presentation may also be used for self-paced and self-directed learning. OBJECTIVES After learning the information in this presentation, the technician will be able to: 1. locate and identify the major components in the Caterpillar Monitoring System, engine, electrical system, power train, hydraulic system, steering, brakes; and dual speed control system; 2. explain the operation of the Caterpillar Monitoring System, engine, electrical system, power train, hoist system, steering, brakes, and dual speed control system; 3. troubleshoot problems in the Caterpillar Monitoring System, engine, electrical system, power train, hydraulic system, steering, brakes, and dual speed control system. REFERENCES "AD30 UAT (DXR) Service Manual" RENR8521 "AD30 UAT (DXR) Parts Manual" SEBP3609 PREREQUISITES "Fundamentals of Mobile Hydraulics Self Study Course" TEMV3002 "Fundamentals of Power Train Self Study Course" TEMV3003 "Fundamentals of Electrical Systems Self Study Course" TEMV3004 "Fundamentals of Engines Self Study Course" TEMV3001 Estimated Time: 8 Hours Illustrations: 162 Handouts: 28 Form: SERV1810 Date: 1/06 © 2006 Caterpillar Inc. TABLE OF CONTENTS INTRODUCTION ........................................................................................................................5 CAB ..............................................................................................................................................7 Interlock Function.................................................................................................................20 CATERPILLAR MONITORING SYSTEM ..............................................................................21 Warning Categories...............................................................................................................24 Modes of Operation ..............................................................................................................31 MACHINE ELECTRICAL SYSTEM........................................................................................36 Electrical Power Supply........................................................................................................36 Engine Start Circuit...............................................................................................................41 Engine Stop Circuit...............................................................................................................43 Engine Shutdown Circuit......................................................................................................45 Hoist Control Circuit.............................................................................................................47 Head Light/Park Light Circuit ..............................................................................................50 Rear Light/Back-up Light Circuit.........................................................................................52 ENGINE......................................................................................................................................54 POWER TRAIN .........................................................................................................................67 Power Train/Chassis Electronic Control System..................................................................69 Transmission Shifting ...........................................................................................................72 Power Train Hydraulic System.............................................................................................79 Torque Converter Hydraulic System ....................................................................................85 HYDRAULIC SYSTEM ............................................................................................................96 Hoist Electronic Control System ..........................................................................................98 Hoist Hydraulic System......................................................................................................103 STEERING HYDRAULIC SYSTEM......................................................................................127 Pilot Circuit.........................................................................................................................128 Secondary Steering .............................................................................................................139 BRAKING SYSTEM ...............................................................................................................145 Brake Electronic Control System........................................................................................147 Power Train Input Components ..........................................................................................148 Automatic Retarder Control (ARC) System.......................................................................153 Service Brake Circuit .........................................................................................................157 Parking Brake Circuit .........................................................................................................166 Brake Cooling Circuit.........................................................................................................168 DUAL SPEED CONTROL SYSTEM......................................................................................171 SERV1810 - 3 - Text Reference 01/06 TABLE OF CONTENTS (continued) CONCLUSION.........................................................................................................................179 VISUAL LIST...........................................................................................................................180 HYDRAULIC SCHEMATIC COLOR CODE.........................................................................183 HANDOUTS.............................................................................................................................184 SERV1810 - 4 - Text Reference 01/06 INTRODUCTION The AD30 Underground Articulated Trucks are designed specifically for high production, low cost-per-ton hauling in the underground mining environment. The basic machine operating specifications for standard machines are listed below. AD30 UAT (Dump body): • Approximate weight 28300 kg (62390 lb) • Length (maximum) 10160 mm (400 inch) • Width (maximum) 2840 mm (111.8 inch) • Height (top of empty body) 2725 mm (107.3 inch) AD30 UAT (Ejector body): • Approximate weight 32500 kg (71650 lb) • Length (maximum) 10450 mm (411.4 inch) • Width (maximum) 2880 mm (113.4 inch) • Height (top of empty body) 2916 mm (114.8 inch) 1 SERV1810 - 5 - Text Reference 01/06 © 2006 Caterpillar Inc. AD30 UNDERGROUND ARTICULATED TRUCK (UAT) INTRODUCTION AD30 ARTICULATED TRUCK FEATURES - C15 ACERT Engine - Electronically Controlled Transmission - Caterpillar Monitoring System - Fast Hoist Cycle Times - Oil-Cooled Multiple Disc Brakes - Automatic Retarder Control (ARC) - 24 Volt Electrical System The C15 ACERT® engine with an EUI fuel system features advanced electronic control, precision fuel delivery, and refined air management. The electronically controlled transmission provides full power shift with four forward and one reverse speeds standard. The Caterpillar Monitoring System monitors the machine status and provides warning indications to the operator. Diagnostic codes are accessible through the main display module and through a laptop computer with Caterpillar Electronic Technician (Cat ET) software. The hydraulic system and lift geometry provide fast body raise and lower times for less time spent in the dump areas. Caterpillar four-wheel, forced oil-cooled multiple disc brakes are continuously cooled by water- to-oil heat exchangers for exceptional, non-fade braking and retarding performance. Automatic Retarder Control (ARC) electronically controls retarding on grade to maintain optimum engine rpm and oil cooling. Additional braking may be applied using the manual retarder and brake pedal. The 24 volt direct current starting system is coated to resist corrosion in the underground environment. 2 SERV1810 - 6 - Text Reference 01/06 CAB The operator's seat can be adjusted to allow full pedal travel. The seat adjustments should be made when the operator is sitting against the back of the seat. The seat and backrest should be periodically readjusted to reduce fatigue. The seat is equipped with the following controls: The seat recline lever (1) pulls up to move the back of the seat to the desired position. The seat back will lock into position when the lever is released. The fore and aft lever (2) is pulled up and held to slide the seat forward or backward to the desired position. Releasing the lever locks the seat into position. The front seat cushion tilt lever (3) and rear seat cushion tilt lever (4) are pulled up to adjust the seat cushions to the desired angle and height. The seat cushion locks into position when the levers are released. 3 SERV1810 - 7 - Text Reference 01/06 1 3 2 4 The lumbar support hand pump (1) increases support to the lower back. The hand pump is located at the right front corner of the seat. A valve button on the hand pump is used to decrease support to the lower back. The suspension damping knob (2) is located at the front of the seat. The dampening knob is turned to change the stiffness of the suspension and is turned until the weight setting on the dial is the same as the operator's weight. The knob should not be turned past the maximum weight setting or past the minimum weight setting. 4 SERV1810 - 8 - Text Reference 01/06 1 2 The cab in the AD30 UAT includes the Caterpillar Monitoring System. The Caterpillar Monitoring System consists of a gauge display (1), an analog tachometer and digital speedometer/gear display (2), and an action alarm, action lamp (3), plus individual alert indicators for each machine system located on the monitoring system display (4). The monitoring system is designed to to alert the operator of an immediate or an impending problem in one or more of the machine systems. Below the indicators lamps is a separate six digit display window (5) linked to various machine systems. The switch panel (6) contains switches for the front lights, rear lights, cab light, Automatic Retarder Control (ARC), operator mode scroll, throttle back-up, and rear window wiper. The parking brake control (7) is a push-pull type switch. The key start switch (8) is used to turn the electrical system on and to start the engine. Service tool port (9) allows the technician to connect a Caterpillar 4C-8195 Control Service Tool for diagnostic access to the Caterpillar Monitoring System, the Engine ECM and Power Train/Chassis ECM. Cat ET service port (10) allows for the connection of a laptop computer using Electronic Technician software to run diagnostics on the Caterpillar Monitoring System, Engine ECM and Power Train/Chassis ECM. 5 SERV1810 - 9 - Text Reference 01/06 1 2 3 4 6 7 5 9 10 8 The gauge cluster monitors four vital engine systems. On each analog gauge, the white band indicates the normal operating range. The engine coolant temperature (1) has a red range to indicate excessive coolant temperature of 107° C (225° F) and above. The brake oil temperature (2) has a red range to indicate brake oil temperatures in excess of 124° C (255° F). The engine oil pressure (3) has a red range to indicate oil pressure below 65 kPa (10 psi). The fuel level gauge (4) indicates the amount of fuel remaining in the fuel tank. The red range of the fuel gauge is an approximate indicator of the last 15 percent of fuel in the tank. The tachometer (5) displays engine speed during machine operation. Below the tachometer is a digital display for the speedometer (6) that indicates ground speed in kilometers per hour or miles per hour. To the right of the speedometer is the actual gear indicator (7) that displays a two digit readout. The left digit is the actual gear. The right digit shows the direction that was selected. 6 SERV1810 - 10 - Text Reference 01/06 1 2 3 4 5 6 7 To access various system data, press the top half of the operator mode scroll switch (1) to scroll through the operator modes as they appear in the display window (2). In Service Meter mode, the six digit display window will show the total number of machine operating hours. If there is an active fault, SERV CODE is displayed in the upper right hand corner of the display. If SERV CODE is displayed during normal operation, an existing problem needs attention. In odometer mode, the six digit display window will show the total distance the machine has traveled. This measurement can uploads/Voyage/ meeting-guide 1 .pdf
Documents similaires
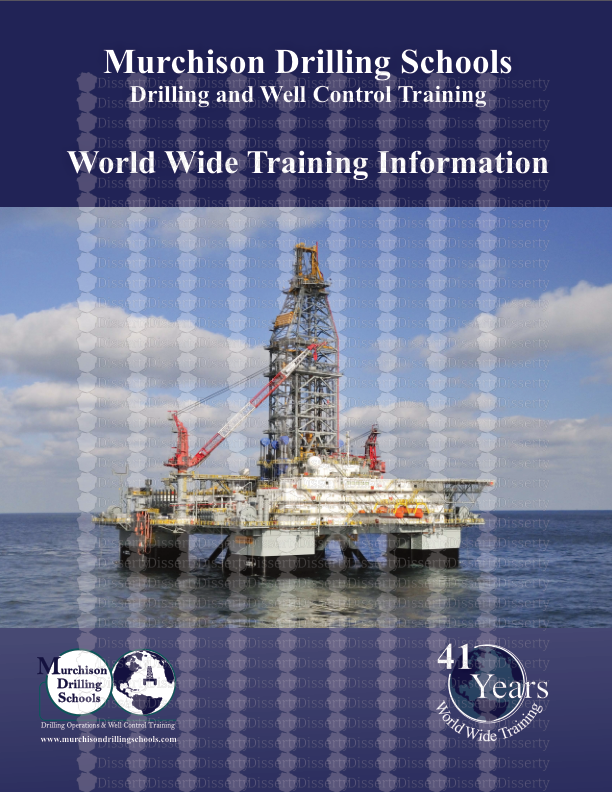
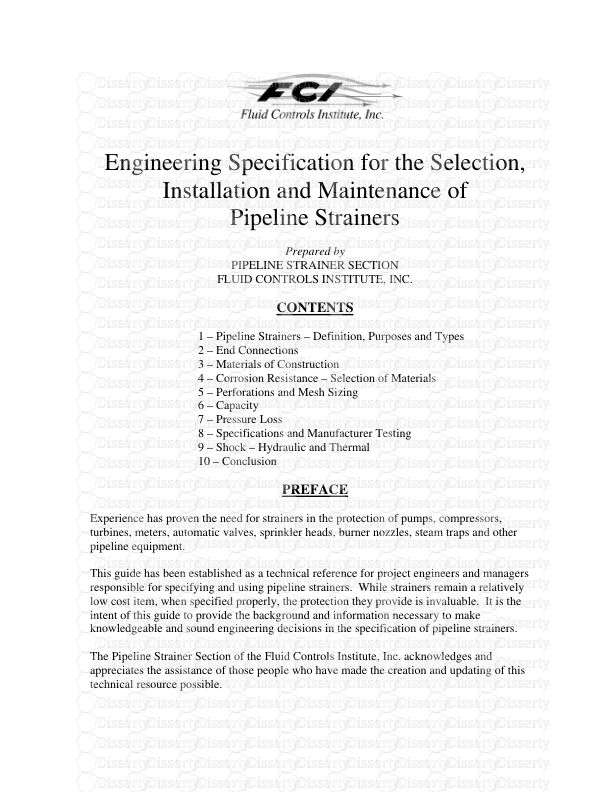
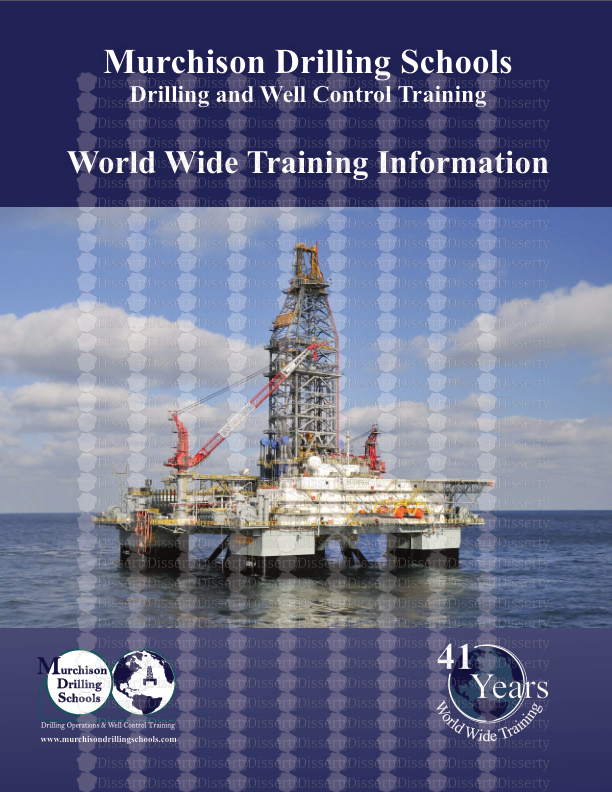

-
68
-
0
-
0
Licence et utilisation
Gratuit pour un usage personnel Attribution requise- Détails
- Publié le Nov 14, 2022
- Catégorie Travel / Voayage
- Langue French
- Taille du fichier 7.4809MB