1 Qualité L’assurance de produit Management Cours : Gestion de la maintenance C
1 Qualité L’assurance de produit Management Cours : Gestion de la maintenance Chap.1 INTRODUCTION A LA MAINTENANCE 1. Définitions : 1.1. Définition de la maintenance Selon l’AFNOR par la norme NF EN 13306 (avril 2001) : la maintenance est l’ensemble de toutes les actions techniques, administratives et de management durant le cycle de vie d’un bien, destinées à le maintenir ou à le rétablir dans un état dans lequel il peut accomplir la fonction requise. Bien maintenir, c’est assurer l’ensemble de ces opérations au coût optimal. La définition de la maintenance fait donc apparaître 4 notions : Maintenir qui suppose un suivi et une surveillance Rétablir qui sous-entend l’idée d’une correction de défaut Etat qui précise le niveau de compétences et les objectifs attendus de la maintenance Coût optimal qui conditionne l’ensemble des opérations dans un souci d’efficacité économique 1.2. La maintenance comme politique La maintenance est une politique qui prend en compte : a) le choix des méthodes d’entretien (les différents modes de maintenances) b) les améliorations de la fonction maintenance sera alors amenée à établir des prévisions ciblées. c) la place des équipements dans le procédé de fabrication (hiérarchisation) Cependant, tous les équipements n’ont pas le même degré d’importance d’un point de vue maintenance d) la formation continue du personnel d’entretien et de production 1.3. L’environnement de la maintenance La maintenance s’intègre dans le concept global de la Sûreté de fonctionnement, qui lui- même s’intègre dans le concept d’assurance de produit : L’assurance Produit. Le concept de Sûreté de fonctionnement regroupe 4 disciplines : La Fiabilité : « Aptitude d’un dispositif à accomplir une fonction requise dans des conditions d’utilisation données à un instant donné. » Dr. Helali Ali 2 Dépense de maintenance + coût des arrêts Service rendu Cours : Gestion de la maintenance La Disponibilité : «Aptitude d’un dispositif à accomplir une fonction requise dans des conditions d’utilisation données pendant une période donné. » La maintenabilité : «Aptitude d’un dispositif à être maintenu ou rétabli dans un état dans lequel il puisse accomplir une fonction requise lorsque la maintenance est accomplie dans des conditions d’utilisation données avec des moyens et procédures prescrits. » La sécurité : « Aptitude d’un dispositif à éviter de faire apparaître des événements critiques ou catastrophiques. » 1.4. La maintenance et la vie du produit La maintenance commence bien avant la première panne : - Dés la conception : la maintenance s’intègre dans le concept de maintenabilité qui évalue la capacité d’un produit à être dépanné. - à l’achat, c’est un conseil et aussi un argument. - à l’installation, à la mise en route elle apporte une connaissance du produit. - à l’utilisation, le rôle de la maintenance est triple : le dépannage, les actions préventives et la surveillance en cours de la production. En conclusion, l’objectif de la maintenance dans la vie du produit c’est de minimiser le rapport : 1.5. Défaillances Il ne suffit pas de s’intéresser aux conséquences d’un défaut de fonctionnement mais aussi à sa cause. Les différents défauts se manifestant de manières variées, les défaillances suivantes ont été définies (norme NF EN 13306) : défaillance complète : cessation du fonctionnement ; défaillance partielle : altération du fonctionnement ; défaillance progressive : qui pourrait être prévue par une vérification préalable ; défaillance soudaine : qui ne peut être prévue ; défaillance intrinsèque : due à une faiblesse inhérente au matériel concerné ; défaillance extrinsèque : due à des contraintes supérieures aux capacités du matériel ; défaillance mineure : la mission globale du matériel n’est pas affectée ; défaillance majeure : la mission globale du matériel ne peut plus être assurée ; défaillance cataleptique : défaillance soudaine et complète ; Dr. Helali Ali 3 Cours : Gestion de la maintenance défaillances précoces : défaillances dont le taux décroît dans le temps ; défaillances aléatoires : défaillances dont le taux est constant dans le temps ; défaillances d’usure : défaillances dont le taux est croissant dans le temps. L’objectif de la maintenance peut consister, entre autres, à diminuer le nombre de défaillances touchant une machine. On s’intéresse donc plus particulièrement à la probabilité d’apparition de ces défaillances sur la durée de vie de la machine. Cette probabilité, ou taux de défaillance, évolue souvent suivant une courbe en « baignoire » (figure 1) principalement pour les équipements électromécaniques. On remarque que cette courbe est la somme des taux de défaillances précoces, aléatoires et d’usure. Elle comporte trois périodes caractérisées par l’évolution du taux de défaillance. Jeunesse (mortalité infantile, défaillance précoce) : en état de fonctionnement à l’origine (mise en service), période de rodage (pré usure), présélection des composants électroniques (déverminage). Maturité (période vie utile, de défaillances aléatoires) : période de rendement optimal du matériel, taux de défaillance constant. Les défaillances apparaissent sans dégradations préalables visibles, par des causes diverses. Obsolescence (vieillesse, usure). Un mode défaillance prédominant, généralement visible, entraîne une dégradation accélérée, à taux de défaillance croissant (pour un mécanisme). Souvent on trouve une usure mécanique, de la fatigue, une érosion ou une corrosion. A un certain seuil de (t), le matériel est « mort ». Il est alors déclassé, puis rebuté ou parfois reconstruit. La détermination de T (seuil de réforme), est obtenue à partir de critères technico-économiques. Dr. Helali Ali 4 Cours : Gestion de la maintenance Figure 1 - Courbe d’évolution du taux de défaillance Ex : loi de survie d’un moteur électrique Ex : taux de défaillance d’un moteur électrique Dr. Helali Ali 5 Cours : Gestion de la maintenance Abscisse : temps ou unité d’usage / Ordonnée : probabilité de ne pas tomber en panne en %. Abscisse : temps ou unité d’usage cumulés / Ordonnée : taux de défaillance en panne par temps ou par unité d’usage. L’allure du taux de défaillance montre que les moteurs sont en période de vieillesse. Exemple : pour un moteur Diesel industriel, on considère que la jeunesse couvre un à deux ans, la maturité 10 à 15 ans 2. Types de maintenance : 2.1. La maintenance corrective - Selon l’AFNOR, c’est la maintenance effectuée après défaillance : donc altération ou cessation de l’aptitude d’un bien à accomplir la fonction requise. - La maintenance corrective appelée parfois curative (terme non normalisé) a pour objet de redonner au matériel des qualités perdues nécessaires à son utilisation. Elle peut être exécutée : Immédiatement après la détection d'une panne, mais est retardée en accord avec des règles de maintenance données. D’urgence après détection d'une panne afin d'éviter des conséquences inacceptables. Le fonctionnement de cette maintenance s’établie par : - Le diagnostic : qui permet d’identifier la cause d’une panne à l’aide d’un raisonnement logique. S’appuie sur des schémas fonctionnels - des tableaux du type effet, cause, remède. - les tests et - des systèmes experts - L’action curative :la réparation à caractère définitif qui est déduit du diagnostic et qui permet au système de fonctionner correctement. 2.2. La maintenance préventive : - c’est la maintenance exécutée à des intervalles prédétermines ou selon des critères prescrits et destinée à réduire la probabilité de défaillance ou la dégradation du fonctionnement d’un bien. Dr. Helali Ali 6 Cours : Gestion de la maintenance Elle doit permettre d’éviter les défaillances des matériels en cours d’utilisation. L’analyse des coûts doit mettre en évidence un gain par rapport aux défaillances qu’elle permet d’éviter. 2.2.1.Buts de la maintenance préventive : Diminuer les travaux urgents. Faciliter la gestion de la maintenance. Prévenir Favoriser la planification des travaux Rendre possible la préparation, l’ordonnancement et la gestion des stocks Eviter les consommations anormales d’énergie, de lubrifiant, etc. Améliorer les conditions de travail du personnel de production : augmenter la sécurité . Diminuer le budget de maintenance On distingue deux types de la maintenance préventive : 2.2.2.La maintenance préventive systématique : Maintenance préventive exécutée à des intervalles de temps préétablis ou selon un nombre défini d’unités d’usage mais sans contrôle préalable de l’état du bien. Cas d’application : -Equipements soumis à une législation en vigueur (sécurité réglementaire) appareils de levage, extincteurs, réservoirs sous pression, convoyeurs, ascenseurs, monte-charge, etc. -Equipements dont la panne risque de provoquer des accidents graves tous les matériels assurant le transport en commun des personnes, avions, trains, etc. - Equipement ayant un coût de défaillance élevé, éléments d’une chaîne de production automatisée, processus fonctionnant en continu (industries chimiques ou métallurgiques). - Equipements dont les dépenses de fonctionnement deviennent anormalement élevées au cours de leur temps de service. consommation excessive d’énergie, éclairage par lampes usagées, allumage et carburation déréglés (moteurs thermiques), etc. Conclusion C’est une maintenance facile à gérer car les périodes d’interventions sont fixes. Elle permet : - d’éviter les détériorations importantes. - de diminuer les risques d’avaries imprévues Inconvénient : elle ne prend pas en compte les phénomènes d’usure 2.2.3.La maintenance préventive conditionnelle : « Maintenance préventive subordonnée à un type d’événement prédéterminé révélateur de l’état du bien. » Dr. Helali Ali 7 Cours : Gestion de la maintenance Maintenance préventive basée uploads/Industriel/ chap-1-introduction-a-la-maintenance.pdf
Documents similaires

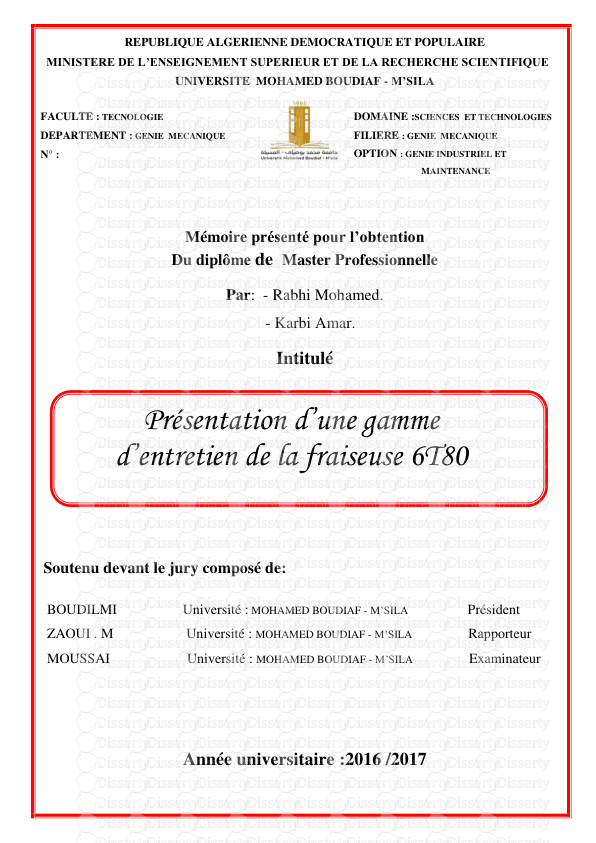
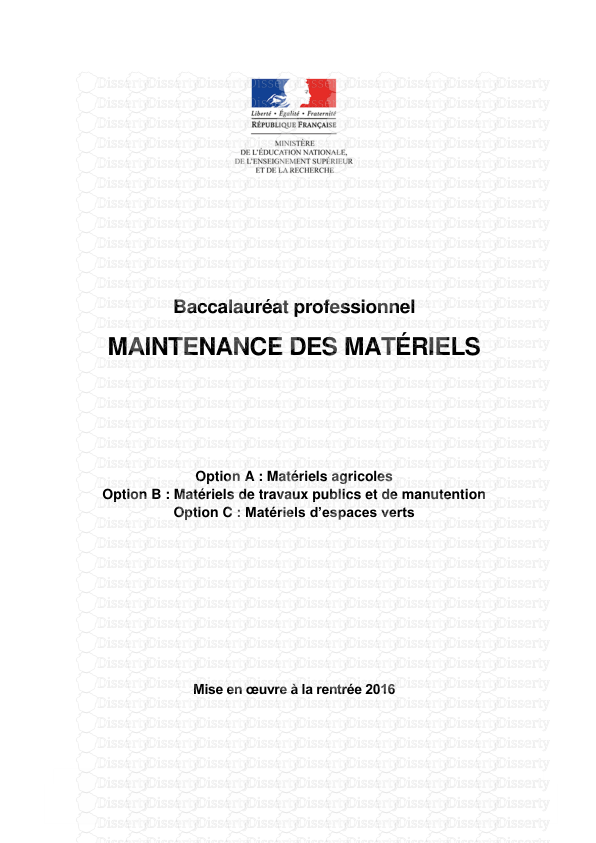
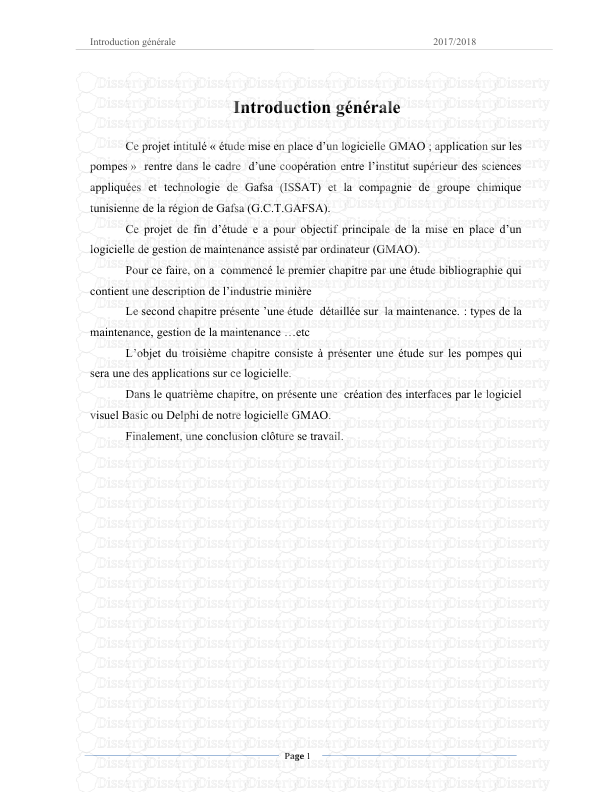
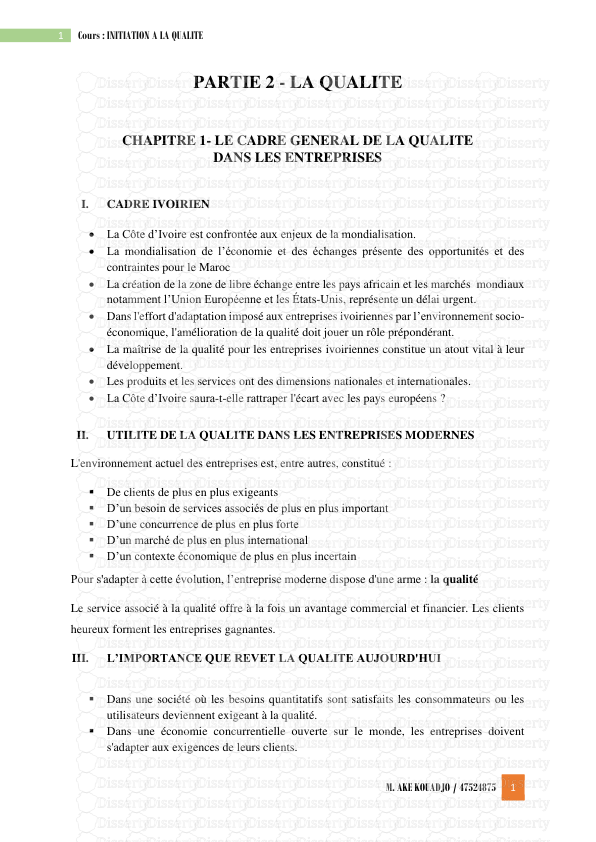
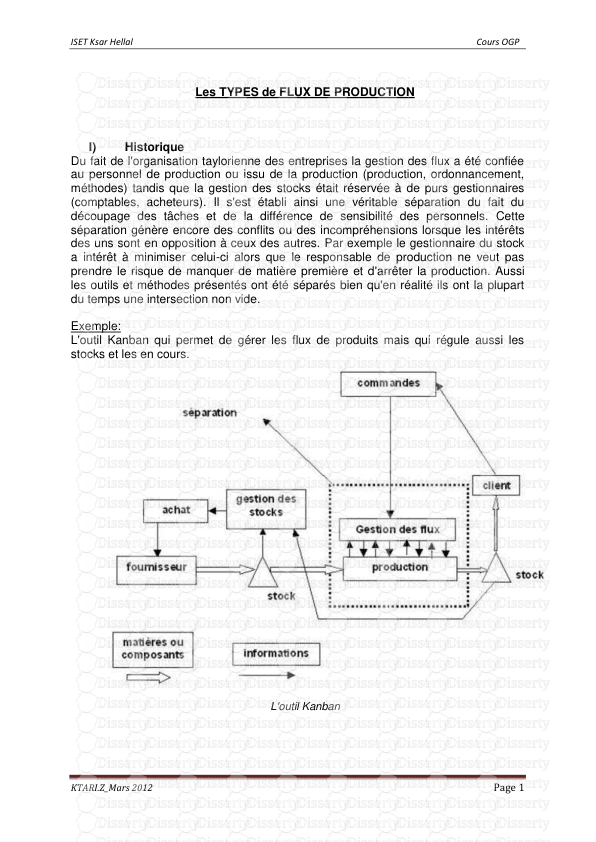
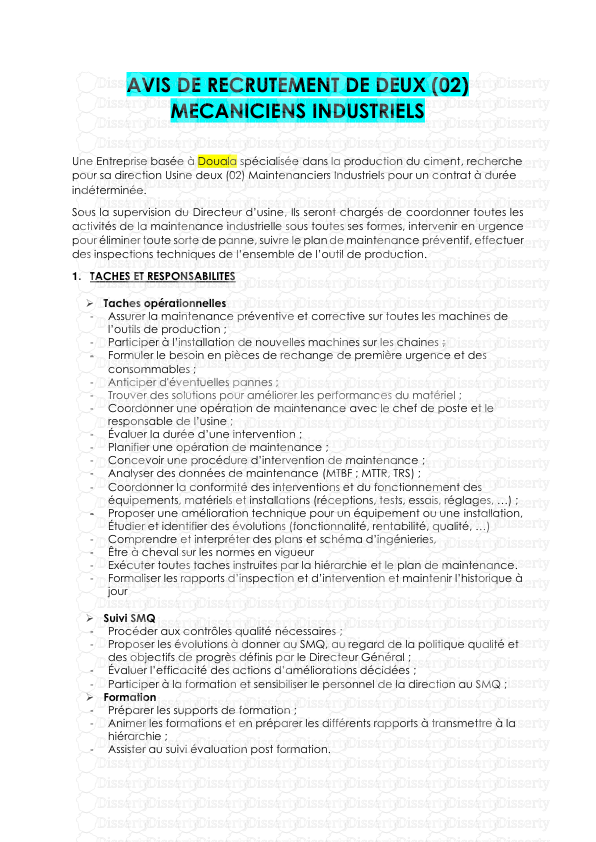
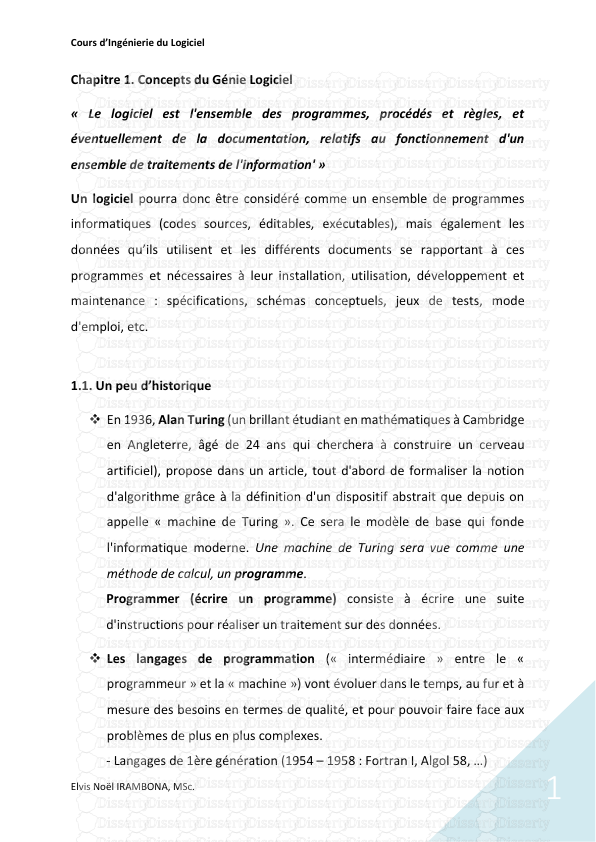
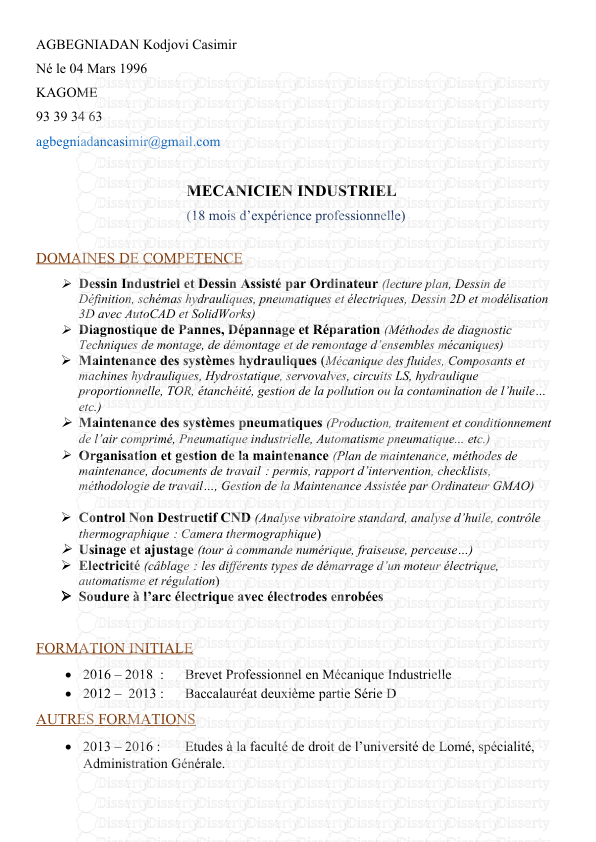
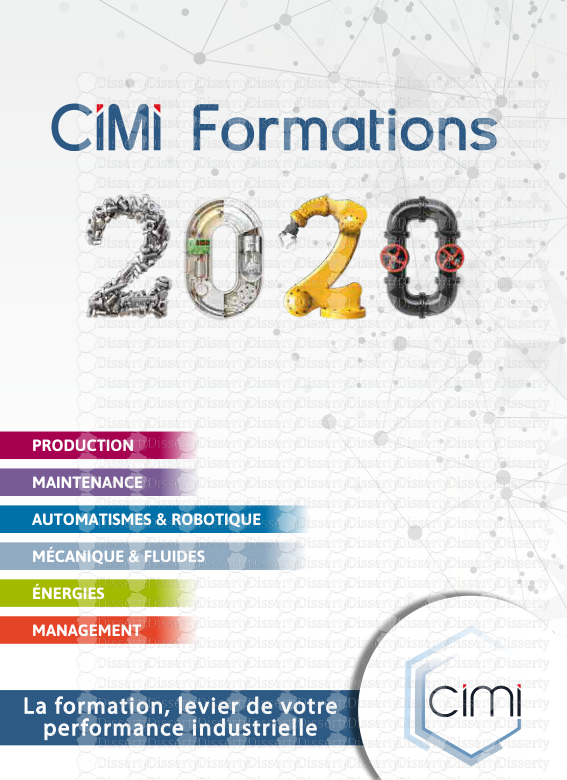
-
56
-
0
-
0
Licence et utilisation
Gratuit pour un usage personnel Attribution requise- Détails
- Publié le Apv 26, 2021
- Catégorie Industry / Industr...
- Langue French
- Taille du fichier 0.3880MB