Elément Sous élément Fonction Mode de défaillance Cause Entrainement Moto réduc
Elément Sous élément Fonction Mode de défaillance Cause Entrainement Moto réducteur Entrainer l’ensacheuse Dégradation de la courroie Frottement/Fatigue mécanique Carter complet usure Joint à labyrinthe Contacteur Arachement de la matière Fatigue mécanique Rotor Faire sortir la matière Blocage Grippage du roulement Turbine Blocage Présence du corps etranger Contrôleur de niveau Blocage Frottement/mauvaise manipulation Couvercle stationnaire Permet la fixation du sac alvéolaire usure age Arbre de remplissage Usure Permettant toujours de solliciter pareillement le roulement à billes frottement avec les sacs du ciment casés la bague d’étanchéité à lèvres protègent le carter contre la poussière provenant du silo Etablir, supporter et d’interrompre des courants dans les conditions normales du circuit,y compris les conditions de surcharge en service. Alimenter les becs par le ciment par un mouvement de rotation Alimentation en matière Détecter le niveau du ciment dans la trémie de remplissage frottement avec les sacs du ciment casés Station de remplissage Moteur électrique Commander l’arbre de remplissage Ventilation insuffisante/Fusible grillé Rondelles-ressorts Vérin pneumatique Commande la guillotine Joint torique dégradé Guillotine Ouvre les orifices de remplissage Présence du ciment Usure Manchette Isoler la balance de la partie fixe de la mach Présence des trous Mouvement aller/retour Electrovanne Commande le vérin Joint torique dégradé Fonctionnement répetitif Préssostat Contrôle la présence du sac Balance Pesage du poids des sacs Sous charge , vitesse fortement réduite Assurer une bonne étanchéité entre le tiroir et les plaques d’usure Fonctionement/présence d'eau Effet Criticité G F D C Arrêt de la machine 5 1 1 5 1 1 1 1 1 1 5 5 2 1 2 4 4 2 1 8 2 1 1 2 Arrêt de la machine 4 2 1 8 1 1 1 1 ne 1 2 1 2 Arrêt de la machine 2 1 1 2 1 1 1 1 3 2 2 12 4 2 1 8 3 2 1 6 2 2 1 4 2 2 1 4 4 3 1 12 2 Couvercle stationnaire Valeur de F 1 Défaillance pratiquement inexistante sur des installations s 2 Défaillance rarement apparue sur du matériel similaire exis 3 Défaillance occasionnellement apparue sur du matériel sim 4 Défaillance fréquemment apparue sur un composant connu Valeur de G 1 Défaillance mineure : aucune dégradation notable du matér 2 Défaillance moyenne nécessitant une remise en état de cou 3 Défaillance majeure nécessitant une intervention de longue 4 Défaillance catastrophique très critique nécessitant une gra 5 Sécurité/Qualité : accident pouvant provoquer des problème Valeur de D 1 Les dispositions prises assurent une détection totale de la c 2 Il existe un signe d avant-coureur de la défaillance mais il y 3 La cause et/ou le mode de défaillance sont difficilement déc 4 Rien ne permet de détecter la défaillance avant que l’effet Indice de fréquence F Fréquence de l'apparition de la défaillance e sur des installations similaires en exploitant, au plus d’un défaut sur la durée de vie de l installation. u matériel similaire existant en exploitation (exemple : un défaut par an) arue sur du matériel similaire existant en exploitation (exemple : un défaut par trimestre) sur un composant connu ou sur du matériel similaire existant en exploitation (exemple : un défaut par mois) Indice de gravité G gravité de la défaillance dation notable du matériel (exemple : TI<10 min). TI=T emps d'intervention ne remise en état de courte durée (exemple 10min<TI 30min) e intervention de longue durée (exemple 30 min < TI 90 min) que nécessitant une grande intervention (exemple TI > 90 min) provoquer des problèmes de sécurité des personnes, lors du dysfonctionnement ou lors de l’intervention Indice de la non détéction F non détéction de la défaillance détection totale de la cause initiale ou du mode de défaillance, permettant ainsi d’éviter l’effet le plus grav e la défaillance mais il y a risque que ce signe ne soit pas perçu par l’opérateur. La détection est exploitable ce sont difficilement décelables ou les éléments de détection sont peu exploitables. La détection est faible. llance avant que l’effet ne se produise : il s’agit du cas sans détection défaillance de vie de l installation. imestre) emple : un défaut par mois) e ou lors de l’intervention ance i d’éviter l’effet le plus grave provoqué par la défaillance pendant la production. La détection est exploitable. les. La détection est faible. Composant Criticité Pourcentage Vérin pneumatique 12 14% Balance 12 14% Rotor 8 9% Controleur de niveau 8 9% Guillotine 8 9% Manchette 6 7% Moto réducteur 5 6% Le joint a labyrinthe 5 6% Contacteur 4 5% Electrovane 4 5% Préssostat 4 5% T urbine 2 2% Arbre de remplissage 2 2% Moteur électrique 2 2% Carter complet 1 1% Couvercle stationnaire 1 1% Rondelles ressorts 1 1% T otal 85 Pourcentage cumulé Zone 14% A 28% 38% B 47% 56% 64% 69% 75% 80% 85% 89% 92% 94% 96% 98% C 99% 100% Crit Criticité Pourcentage cumulé Vérin pneumatique La dégradation du joint torique(garniture) a cause du fonctionnement successif du et la présence de la poussière ce qui empeche le bon fonctionnement La purge quigère la rapidité de la fermeture et l'ouverture Problème des régulateurs de purge Absence d'étanchiété entre la guillotine et le vérin pneumatique ( difficulté de comm Problèmes rencontrés : Pour réduire la criticité on va choisir une criticité > 8 comme seuil. Toutes les causes dont la criticité dépasse ce seuil doivent être traitée priorité La Zone A (20%) du diagramme PARETO comporte : Vérin pneumatique Balance Balance onctionnement successif du vérin pneumatique Usure des bagues ctionnement Cisaillement des lames de pesage Usure de la chaise Détérioration du balais de charbon matique ( difficulté de commande du vérin) Problèmes rencontrés : té > 8 comme seuil. uil doivent être traitées en te : Balance ames de pesage balais de charbon s rencontrés : Maintenance systéma Graissage Lubrification Une lubrification correcte est indispensable pour que le ROTO-Packer foncti La lubrification doit avoir lieu conformément à la périodicité spécifiée dans utilisant les lubrifiants et quantités mentionnées. Changement systématique des courroies trapézoïdales Problèmes rencontrés Glissement des courroies insuffisamment tendues Une température trop importante des courroies ce qui implique une détério Les gorges des poulies comportent des traces de rouille, de graisse Utilisation de la cire ou des substances similaires pour augmenter le coeffic endommage les courroies. Entretien Pour les poulies a plusieurs gorges Un regraissage doit être effectué toutes les 100 heures de s Maintenance systématique r que le ROTO-Packer fonctionne bien et éviter des réparations coûteuses. a périodicité spécifiée dans la liste des points à graisser et en s. pézoïdales es ce qui implique une détérioration prématurée de celles-ci de rouille, de graisse es pour augmenter le coefficient de frottement mais cela Toujours remplacer les courroies usées par d’autres ayant exactement la Même si une seule courroie est endommagée, remplacer toutes les autre Contrôler la tension des nouvelles courroies au bout de 4-5 heures de fon es les 100 heures de service Liste des lubrifiants convenant a la HAVER 3 uses. utres ayant exactement la même longueur remplacer toutes les autres bout de 4-5 heures de fonctionnement; les retendre si nécessaire. Maintenance préventi T ravaux à exécuter Vérin pneumatique Maintenance préventive Actions a mettre en place Intervalle de vérification Nettoyer les éléments de signaux Hebdomadaire et mensuel Examen des tuyaux à la recherche de porosité et de brisure T enue correcte et étanchéité des raccords de tuyaux Examen des vissages et des conduites fixes à la recherche de points de fuites Étanchéité des soupapes Raccordements des conduites sur les vérins pneumatiques Obstruction des éléments de silencieux T ravaux à exécuter Actions a mettre en place Balance Réglage de la limite de classe de la balance de correction de poids déréglé Vérifier la régularité des sacs sur la selle basculante Vérification de la mobilité de la chaise porte sacs Eliminer les résidus de matériau Vérifier les données d'equilibrage et Rééquilibrer la balance Vérifier l'anticipation gros débit Assurer le raccordement du cable du connecteur de cellule de pesée Intervalle de vérification Hebdomadaire et mensuel Problèmes constatés Emplacement aléatoire des palettes Ciment CPJ 35 Le stock maximal CPJ 45 CPJ 35 nombre de rangées 6 6 nombre de palettes par rangée 36 36 nombre de sacs par couche 5 5 nombre de couche par palette 6 6 nombre de sacs par palette 30 30 poids par sac (kg) 50 50 poids par palette (kg) 1500 1500 Stock maximal (tonne) 324 324 Ciment CPJ 45 uploads/Industriel/ amdec 2 .pdf
Documents similaires
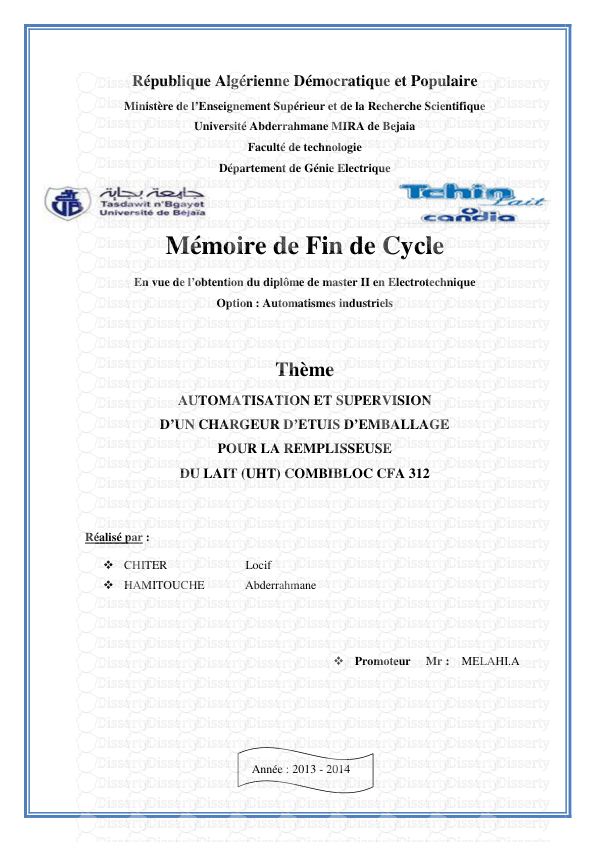
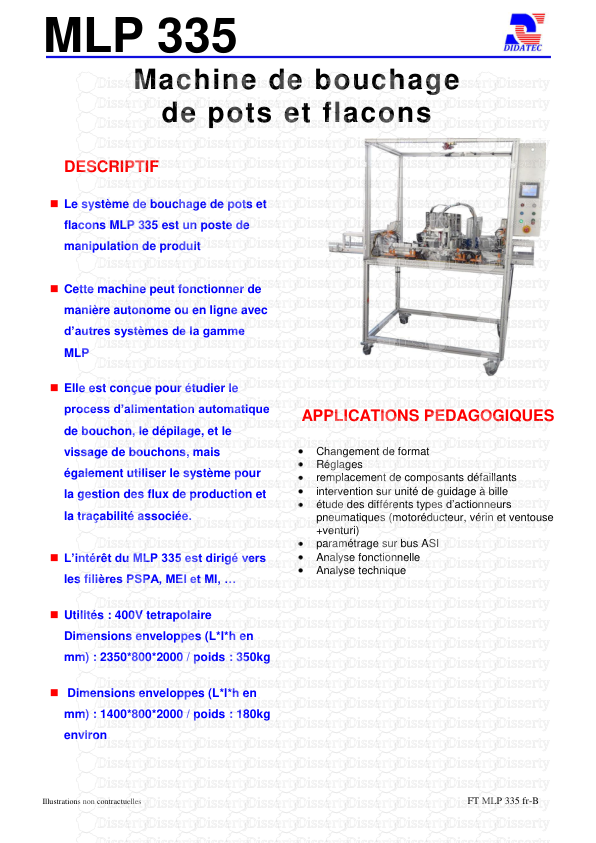
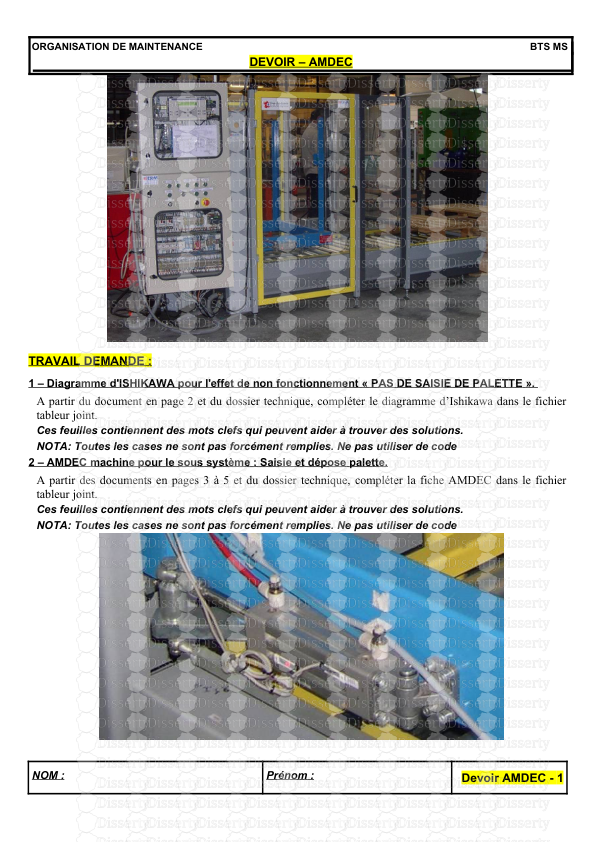
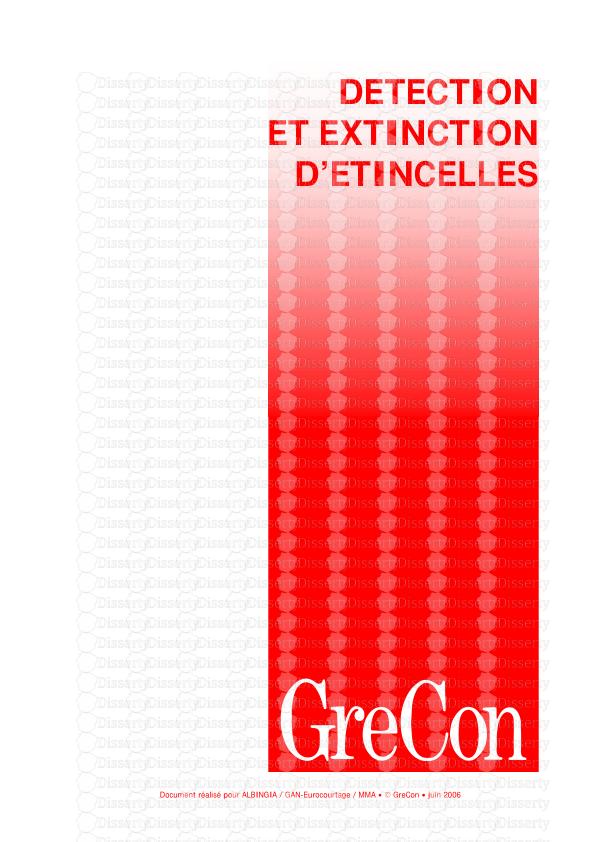