Session de communication scientifique étudiante 2021 DÉVELOPPEMENT INDUSTRIEL C
Session de communication scientifique étudiante 2021 DÉVELOPPEMENT INDUSTRIEL CONCERNANT LES MODULES D’UN MOULE D’INJECTION DÉVELOPPEMENT INDUSTRIEL SUR MODULES DE UN MOULE D’INJECTION BARBU Radu-Cristian Faculté: Génie industriel et robotique, Spécialisation: Ingénierie et gestion de projets complexes, Année d’études: 1 IMPC,e-mail: radubarbu0@gmail.com Conseillers scientifiques : Ing. Gannam NASIM – SC Dr Kocher, Morphème lié. Nicolae Onorel POLOVȚEV – SC Dr. Kocher, Prof. dr. ing. Marian GHEORGHE Introduction L’objectif de ces travaux est de présenter des éléments généraux et une étude de cas sur la définition et le développement, dans des conditions industrielles, de certains modules composants d’un moule d’injection. La méthodologie de R&D est structurée en fonction des éléments de référence suivants : le cadre général ; les ressources de conception; génération et simulation du fonctionnement de certains modules du moule d’injection. Considérations générales Selon la nature de certains liens constructifs-fonctionnels, les produits peuvent être du type de pièce ou d’assemblage. L’ensemble est une rencontre de pièces interdépendantes constructivement-fonctionnellement. Un produit est fonctionnel et technologique si toutes ses caractéristiques répondent aux conditions de [G3] : ( N + Ainf ) j ≤ cfjef ≤ ( N + Asup )j , (1)j=1,f ( N + Ainf ) j ≤ ctjef ≤ ( N + Asup )j , (2)j=1,t où: N, Ainf et Aci-dessous sont la valeur nominale, l’écart inférieur et l’écart ci-dessus prescrits à la caractéristique; CFjef et CTjef - les valeurs effectives des caractéristiques fonctionnelles et technologiques considérées. L’ingénierie des produits et des procédés est réalisée par les étapes suivantes : Conception, Conception, Prototype, Fabrication, Livraison (Fig. 1) [S5]. Fig. 3.1. Étapes de l’ingénierie des produits et des procédés [S5] Le moule d’injection est l’élément de type outil d’un système de fabrication technologique [G3], à travers lequel des pièces en plastique sont fabriquées. Les principaux composants d’un moule d’injection (Fig. 2) sont du type: plaque de base mobile,entretoise mobile pl, floe intermédiaire mobile, forme mobile pl, forme fixe pl, tampon intermédiaire fixe, tampon d’espacement fixe, tampon d’espacement fixe, floe de base fixe [S8]. Un moule d’injection peut également être constitué de [S8]: fixations (vis, bagues, pinces), éléments de levage (anneaux, pinces), éléments d’extraction produits (extracteurs, plaque d’extraction), éléments formant des produits (nid, noyau, ferry), systèmes de salle chaude, circuits (électriques, eau, plastique, huile), douilles, connecteurs (mamelons de refroidissement, prises électriques), éléments auxiliaires (cylindres pneumatiques, cylindres hydrauliques, capteurs, etc.). Fig. 3.2. Composants d’un moule d’injection (adaptation après [S8]) L’opération d’injection dans le moule se compose de plusieurs phases: alimentation du matériau (dosage); chauffage et fusion du matériau dans le cylindre de la machine; fermeture de la matrice; introduction du matériau fondu sous pression dans le moule; solidification et refroidissement du matériau dans le moule; ouverture de la matrice; évacuation de la pièce injectée du moule (Fig. 3). Les phases ne sont pas parfaitement délimitées. Ainsi, la planification thermique du matériau commence avant l’ouverture du moule et l’évacuation du produit [S6]. Dans le processus d’injection dans le moule (Fig. 3), la matière première sous forme de granulés est insérée dans l’entonnoir d’alimentation 8, d’où elle tombe dans le cylindre d’injection 5. Depuis le cylindre d’injection, la matière plastique est transportée par l’escargot 7, lors du mouvement de rotation, nànla busendeninjectionn4. nLan rotationnan l’escargotnestn effectuénàl’aide dun système d’exploitation n9. Pendant le transport, les granulés atteignent l’état fondu à la suite du frottement, ainsi que du chauffage du cylindre par les corps chauffants 6. Le plastique fondu est transféré sous pression dans le moule d’injection 2, par l’escargot 7, en raison de la pression exercée par le système d’entraînement 10. Après solidification et refroidissement du matériau dans le moule, la plaque mobile 1 de la machine s’écarte de la plaque fixe 3. Ainsi, le moule s’ouvre et à la suite de l’actionnement du système d’échappement, la partie injectée 11 est retirée du moule [Ş1]. 1 – Plateau mobile 2 – Mourir 3 – Plateau fixe 4 – Buse d’injection de la voiture 5 – Cylindre 6 – Corps chauffant 7 – Escargot 8 – Entonnoir d’alimentation 9 – Système d’entraînement par mouvement de rotation 10 - Système d’entraînement de mouvement translationnel 11 – Partie injectée a – injection du matériau dans le moule, b – solidification et refroidissement de la matière fondue, c – ouverture du moule et déchargement de la pièce du moule. ph – pression hydraulique, pe – pression externe, pi – pression interne. Fig. 3.3. Schéma principal d’injection dans le moule (adaptation après [S6]) Fig. 3.4. Le schéma de remplissage du moule [S10] a. b. Fig. 3.5. Modèles 3D de compactage, de refroidissement et de démulgation : a – Module de compactage b - Module de refroidissement et de démulage [S10] L’ensemble du processus d’injection peut être contenu dans les étapes suivantes [S9] : - plastification; - remplir la matrice; - compactage; - refroidissement et démulgation. Les polymères sont fréquemment utilisés dans l’industrie des plastiques et des composites. Les polymères comprennent une gamme de matériaux avec une variété de propriétés. Cependant, ils ont une résistance mécanique inférieure à celle des métaux. Pour résoudre ce problème, des plastiques renforcés de fibres de verre ou de carbone (PRF) ont été pratiquement utilisés et appliqués aux éléments structurels nécessitant une résistance mécanique élevée. La température de fonctionnement est généralement inférieure à 100oC [S9]. Pendant le processus d’injection, la force qui tend à ouvrir les deux parties principales du moule est peut calculer [S1] avec la relation : Fd = k2p0Aep (3) où: Fd est la force d’ouverture dans le moule; Aep – la zone effective de projection de la pièce injectée sur le plan de séparation de la matrice ; k2 – le coefficient qui prend en compte l’agrégat plastifiant. La différence entre le four et le dessiccateur est liée au principe de « recyclage » de l’air en circuit fermé. Ainsi, dans le cas d’un four industriel, le circuit est alimenté en continu de l’extérieur avec de l’air à température ambiante et de l’air chaud est évacué. Dans le cas d’un dessiccateur, l’air, une fois chauffé et sec, est réintroduit dans le circuit du four après avoir été passé à travers des filtres pour éliminer toute présence potentielle de particules de matériau. Par conséquent, il illustre le principe du circuit fermé. Si un dessiccateur est utilisé, les temps de four peuvent être divisés par deux[S8].- La durabilité, le coût et le temps de fabrication sont des éléments clés dans le processus de développement d’un moule d’injection avec des canaux de refroidissement conformes. L’analyse détaillée des éléments constructifs et de procédé concernant l’injection dans le moule d’une pièce critique (Fig. 4) conduit à des solutions technologiques acceptables [K1]. Fig. 3.6. Modèle CAO et section associés à la pièce moulée par injection [K1] Fig. 3.7. Schéma de principe pour les canaux de refroidissement des moules[S8] Les canaux de refroidissement sont souvent négligés lors de l’entretien de la matrice ou de l’analyse des dérives de processus, en raison du fait qu’ils sont « cachés » et qu’il est difficile de faire des recherches sans être démontés[S8]. Ces canaux sont conçus pour avoir un refroidissement aussi proche que possible de la pièce et des zones de chauffage critiques. Sur le diagramme ci-dessus, vous pouvez voir un moule d’une pièce ronde, avec l’entrée et la sortie du fluide de régularisation. Les tableaux ci-dessous répertorient les principaux systèmes de canaux de refroidissement utilisés[S8]. Fig. 3.8. Diagramme représentatif du système de noyau de moule [S8] Le système de base a le même principe que celui à mâchoires, avec une différence : il est entraîné par un piston hydraulique, dans la plupart des cas, ou pneumatique pour les petits noyaux[S8]. Il peut être utilisé avec le moule ouvert, comme dans le cas de corps creux à l’intérieur, par exemple, ou avec le moule fermé, pour appliquer des trous latéraux. Dans presque tous les cas, le pilotage se fait via la machine, qui peut gérer plusieurs entrées/sorties de base en même temps[S8].. Les cœurs sont privilégiés aux ferries dans les cas suivants: - de grands corps, creux à l’intérieur, qui nécessiteraient l’extraction des doigts du moule ou des mâchoires trop grandes. - garantir la sécurité du moule. En effet, les noyaux, une fois placés dans le menu presse et réglés correctement, ne peuvent pas dévier sans arrêter la machine (sauf si la prise centrale est déviée), ce qui assure un plus de sécurité par rapport à l’utilisation des mâchoires. Fig. 3.9. Le phénomène du jet libre [S10] Un autre phénomène important rencontré lorsque la fonte s’écoule dans le nid de matrice est le jet libre. Il se réfère à la tendance de la fonte à pénétrer dans le nid de la matrice sous la forme d’un jet sans toucher les surfaces du nid de la matrice autour du barrage et donc le remplissage du nid aura lieu en rassemblant le jet à l’extrémité où il entre en contact avec la surface du nid de la matrice vers le brise-lames de la matrice, conduisant ainsi à l’apparition de phénomènes qui nuisent à la qualité de la pièce injectée, tels que : lignes de desudura, uploads/Industriel/ developpement-industriel-concernant-les-modules.pdf
Documents similaires
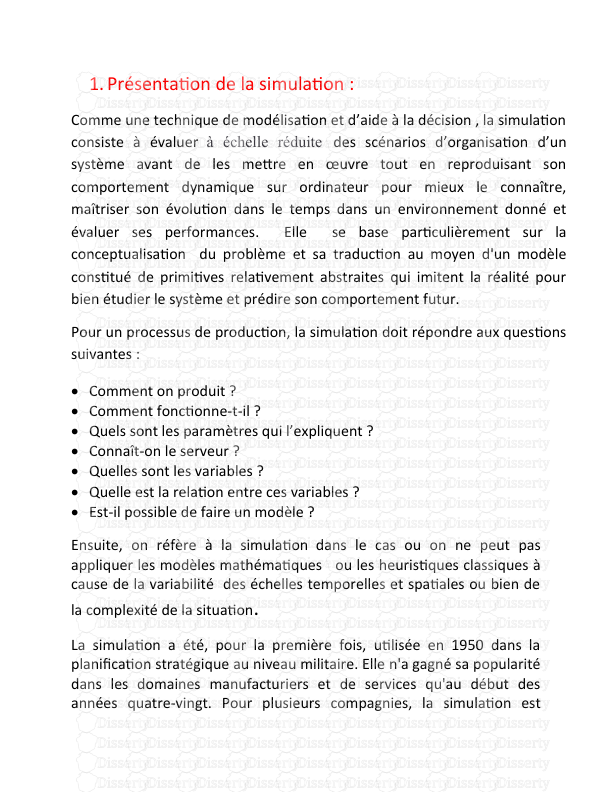
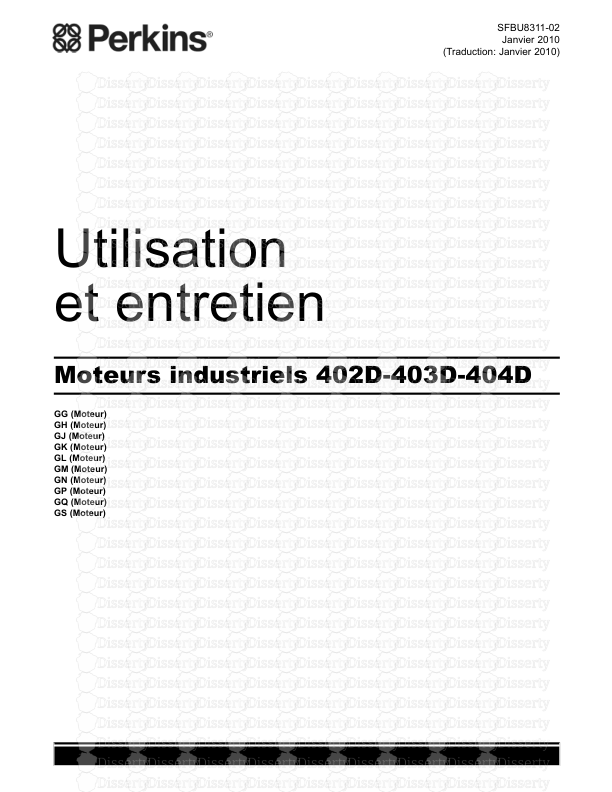
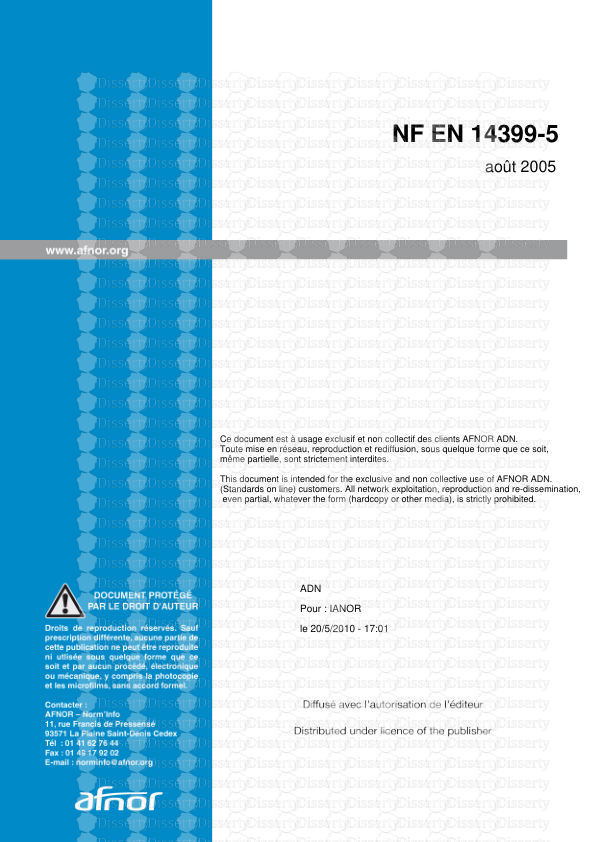
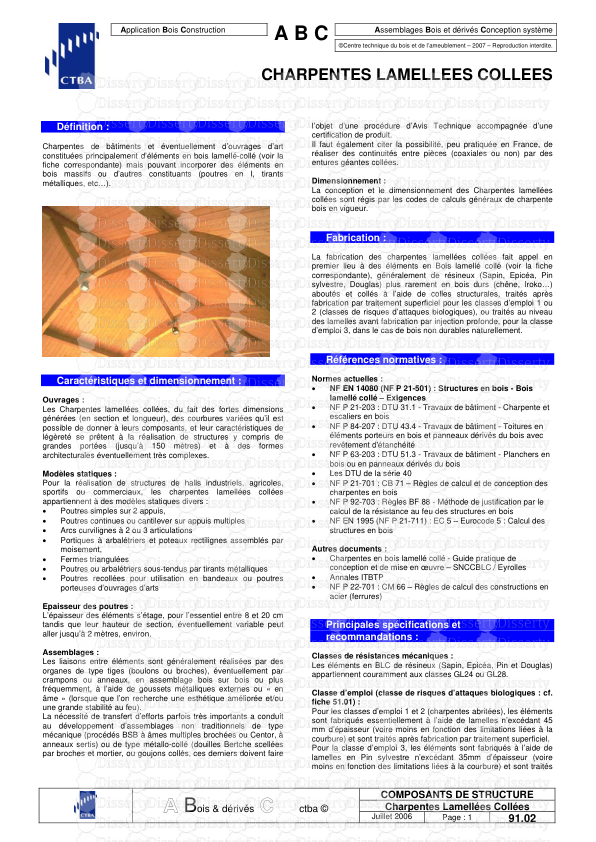
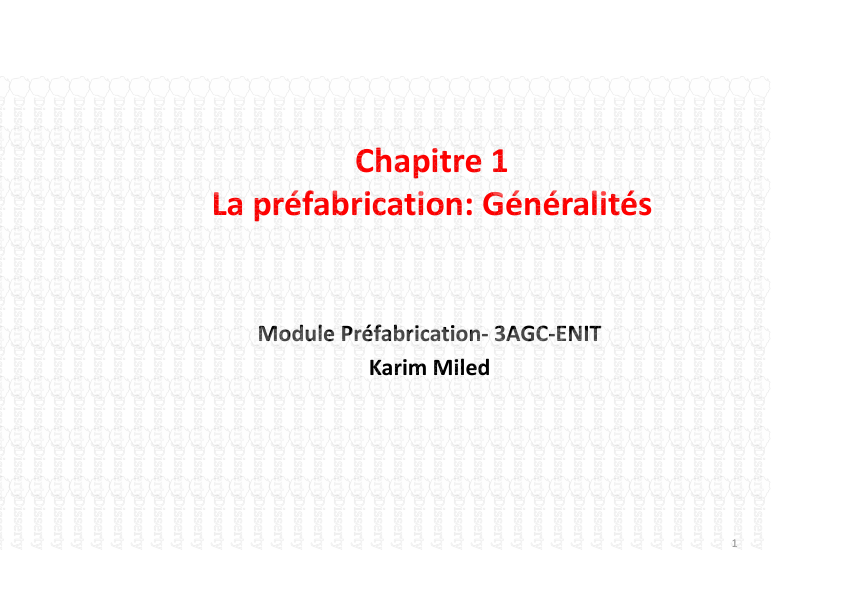
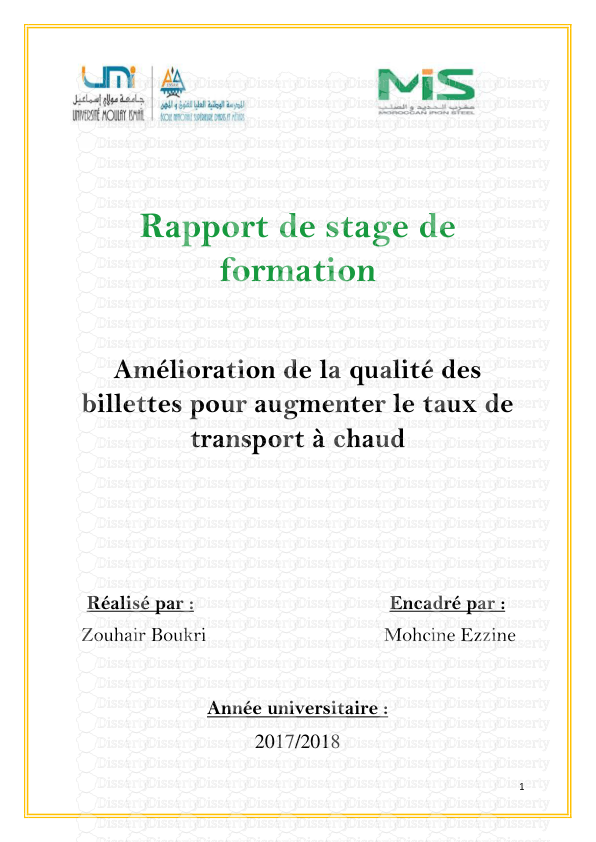
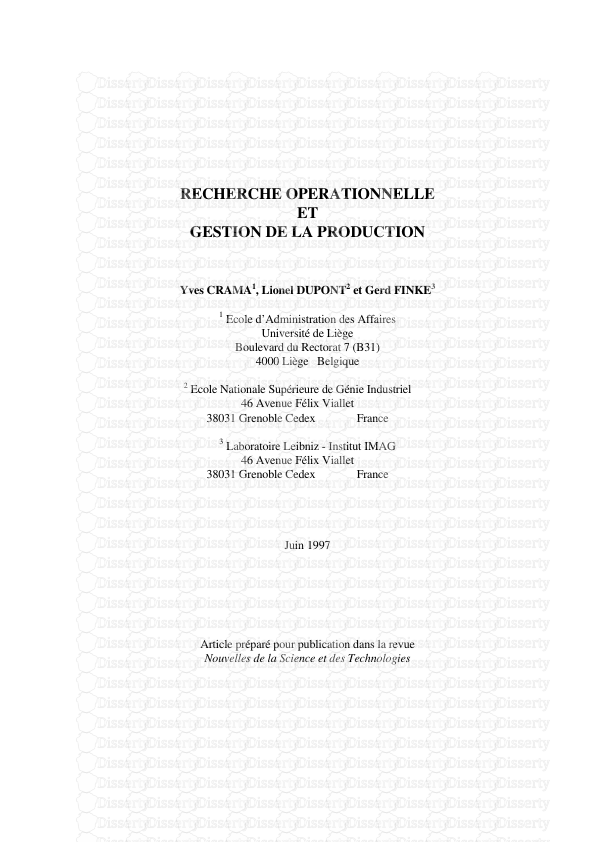
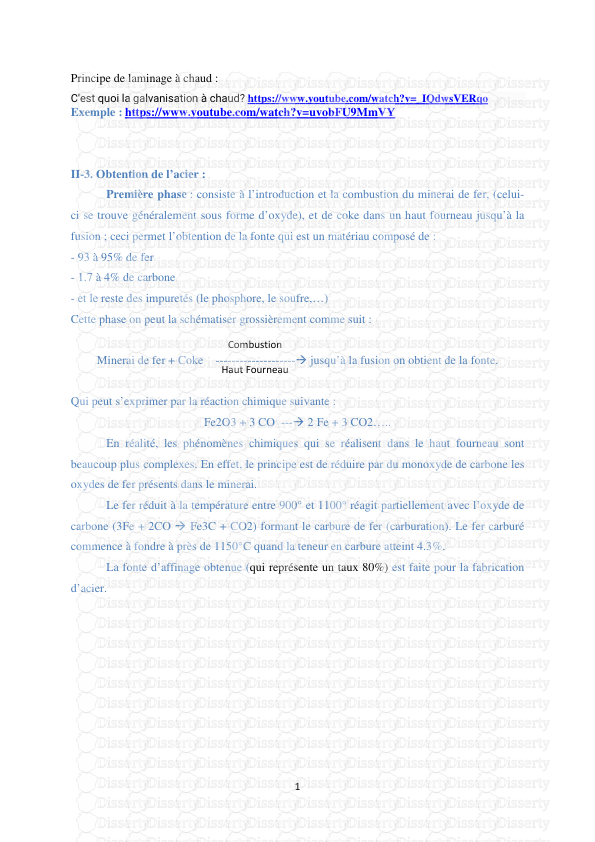
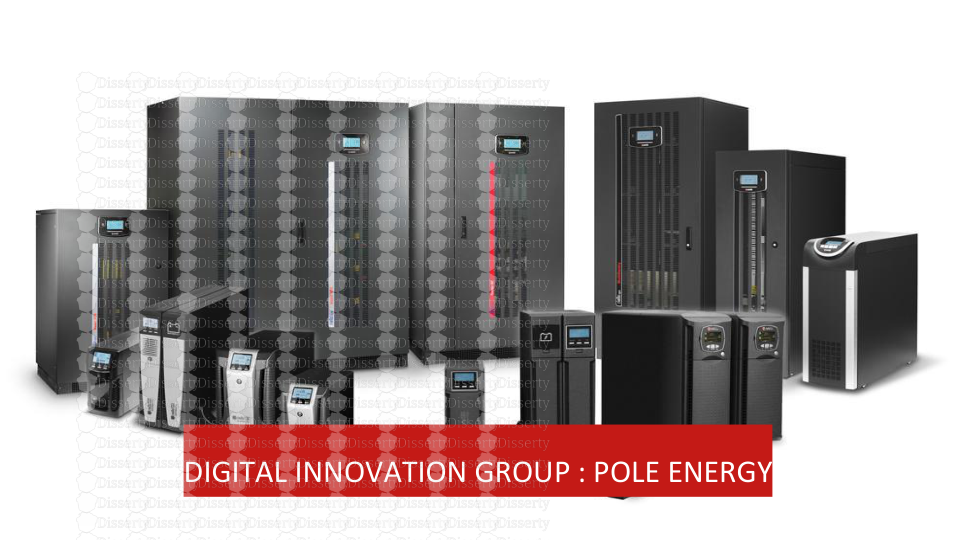
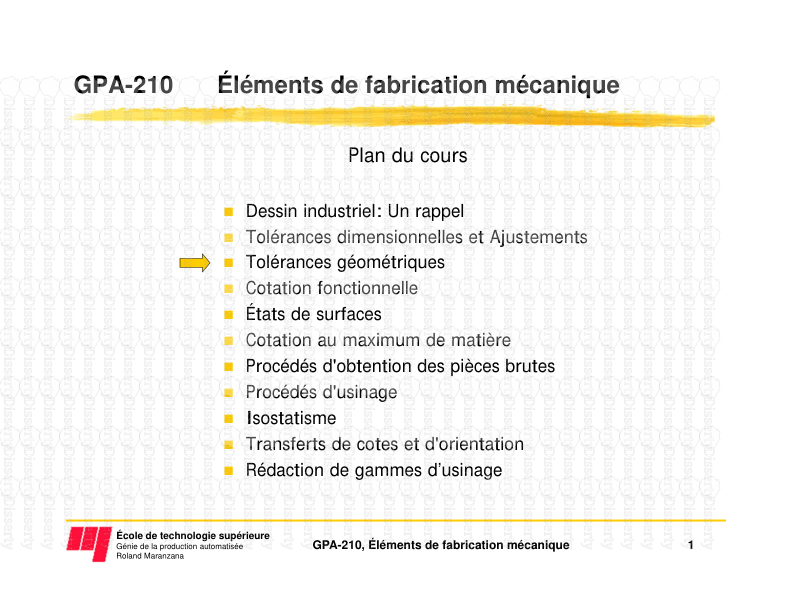
-
44
-
0
-
0
Licence et utilisation
Gratuit pour un usage personnel Attribution requise- Détails
- Publié le Oct 10, 2022
- Catégorie Industry / Industr...
- Langue French
- Taille du fichier 1.0377MB