User Guide AC variable speed drive for servo motors Part Number: 0475-0001-01 I
User Guide AC variable speed drive for servo motors Part Number: 0475-0001-01 Issue: 1 www.controltechniques.com General Information The manufacturer accepts no liability for any consequences resulting from inappropriate, negligent or incorrect installation or adjustment of the optional operating parameters of the equipment or from mismatching the variable speed drive with the motor. The contents of this guide are believed to be correct at the time of printing. In the interests of a commitment to a policy of continuous development and improvement, the manufacturer reserves the right to change the specification of the product or its performance, or the contents of the guide, without notice. All rights reserved. No parts of this guide may be reproduced or transmitted in any form or by any means, electrical or mechanical including photocopying, recording or by an information storage or retrieval system, without permission in writing from the publisher. Drive software version This product is supplied with the latest version of software. If this product is to be used in a new or existing system with other drives, there may be some differences between their software and the software in this product. These differences may cause this product to function differently. This may also apply to drives returned from a Control Techniques Service Centre. The software version of the drive can be checked by looking at Pr 11.29 (or Pr 0.50) and Pr 11.34. The software version takes the form of zz.yy.xx, where Pr 11.29 displays zz.yy and Pr 11.34 displays xx, i.e. for software version 01.01.00, Pr 11.29 would display 1.01 and Pr 11.34 would display 0. If there is any doubt, contact a Control Techniques Drive Centre. Environmental statement Control Techniques is committed to minimising the environmental impacts of its manufacturing operations and of its products throughout their life cycle. To this end, we operate an Environmental Management System (EMS) which is certified to the International Standard ISO 14001. Further information on the EMS, our Environmental Policy and other relevant information is available on request, or can be found at www.greendrives.com. The electronic variable-speed drives manufactured by Control Techniques have the potential to save energy and (through increased machine/process efficiency) reduce raw material consumption and scrap throughout their long working lifetime. In typical applications, these positive environmental effects far outweigh the negative impacts of product manufacture and end-of-life disposal. Nevertheless, when the products eventually reach the end of their useful life, they can very easily be dismantled into their major component parts for efficient recycling. Many parts snap together and can be separated without the use of tools, while other parts are secured with conventional screws. Virtually all parts of the product are suitable for recycling. Product packaging is of good quality and can be re-used. Large products are packed in wooden crates, while smaller products come in strong cardboard cartons which themselves have a high recycled fibre content. If not re-used, these containers can be recycled. Polythene, used on the protective film and bags for wrapping product, can be recycled in the same way. Control Techniques' packaging strategy favours easily-recyclable materials of low environmental impact, and regular reviews identify opportunities for improvement. When preparing to recycle or dispose of any product or packaging, please observe local legislation and best practice. Copyright © April 2007 Control Techniques Drives Limited Issue Number: 1 How to use this guide This user guide provides information for operating the drive from start to finish. The information is in logical order, taking the reader from receiving the drive through to fine tuning the performance. There are specific safety warnings throughout this guide, located in the relevant sections. In addition, Chapter 1 Safety Information contains general safety information. It is essential that the warnings are observed and the information considered when working with or designing a system using the drive. This map of the user guide helps to find the right sections for the task you wish to complete: NOTE 1 Safety information 2 Introduction 3 Getting started 4 Running the motor 5 Basic parameters 6 Optimisation 8 Advanced parameters 9 Diagnostics 7 SMARTCARD operation 4 Digitax ST User Guide www.controltechniques.com Issue: 1 Contents 1 Safety Information .................................5 1.1 Warnings, Cautions and Notes .............................5 1.2 Electrical safety - general warning ........................5 1.3 System design and safety of personnel ................5 1.4 Environmental limits ..............................................5 1.5 Compliance with regulations .................................5 1.6 Motor .....................................................................5 1.7 Adjusting parameters ............................................5 1.8 Electrical installation ..............................................5 2 Introduction ............................................6 2.1 Drive model numbers ............................................6 2.2 Drive nameplate description ..................................6 2.3 Features of the drive .............................................7 2.4 Options ..................................................................7 3 Getting Started .......................................8 3.1 User interfaces ......................................................8 3.2 Keypad operation ..................................................9 3.3 Displaying parameters with non-default values only .....................................................................13 3.4 Displaying destination parameters only ..............13 3.5 Communications .................................................13 4 Running the motor ..............................15 4.1 Quick Start set-up ...............................................18 4.2 Setting up a feedback device ..............................19 4.3 Setting up a buffered encoder output ..................21 5 Basic parameters .................................22 5.1 Single line descriptions .......................................22 5.2 Full descriptions ..................................................26 6 Optimization .........................................32 6.1 Motor map parameters ........................................32 7 SMARTCARD Operation .....................35 7.1 Introduction .........................................................35 7.2 Transferring data .................................................36 7.3 Data block header information ............................38 7.4 SMARTCARD parameters ..................................38 7.5 SMARTCARD trips ..............................................40 8 Advanced parameters ........................ 42 8.1 Menu 1: Speed reference ................................... 48 8.2 Menu 2: Ramps .................................................. 52 8.3 Menu 3: Frequency slaving, speed feedback and speed control ............................................... 56 8.4 Menu 4: Torque and current control ................... 60 8.5 Menu 5: Motor control ........................................ 62 8.6 Menu 6: Sequencer and clock ............................ 65 8.7 Menu 7: Analog I/O ............................................ 67 8.8 Menu 8: Digital I/O ............................................. 70 8.9 Menu 9: Programmable logic, motorized pot, binary sum and timers ........................................ 73 8.10 Menu 10: Status and trips .................................. 76 8.11 Menu 11: General drive set-up ........................... 77 8.12 Menu 12: Threshold detectors, variable selectors and brake control function .................. 78 8.13 Menu 13: Position control ................................... 82 8.14 Menu 14: User PID controller ............................. 86 8.15 Menus 15 and 16: Solutions Module set-up ....... 88 8.16 Menu 17: Motion processors ............................ 121 8.17 Menu 18: Application menu 1 ........................... 124 8.18 Menu 19: Application menu 2 ........................... 124 8.19 Menu 20: Application menu 3 ........................... 124 8.20 Menu 21: Second motor parameters ................ 125 8.21 Menu 22: Additional Menu 0 set-up ................. 126 8.22 Advanced features ........................................... 127 9 Diagnostics ....................................... 134 9.1 Alarm indications .............................................. 146 9.2 Status indications ............................................. 147 Index .................................................. 148 Safety Information Introduction Getting Started Running the motor Basic parameters Optimization SMARTCARD Operation Advanced parameters Diagnostics Digitax ST User Guide 5 Issue: 1 www.controltechniques.com 1 Safety Information 1.1 Warnings, Cautions and Notes A Note contains information which helps to ensure correct operation of the product. 1.2 Electrical safety - general warning The voltages used in the drive can cause severe electrical shock and/or burns, and could be lethal. Extreme care is necessary at all times when working with or adjacent to the drive. Specific warnings are given at the relevant places in this guide. 1.3 System design and safety of personnel The drive is intended as a component for professional incorporation into complete equipment or a system. If installed incorrectly, the drive may present a safety hazard. The drive uses high voltages and currents, carries a high level of stored electrical energy, and is used to control equipment which can cause injury. Close attention is required to the electrical installation and the system design to avoid hazards either in normal operation or in the event of equipment malfunction. System design, installation, set-up and maintenance must be carried out by personnel who have the necessary training and experience. They must read this safety information and this guide carefully. The STOP and SAFE TORQUE OFF functions of the drive do not isolate dangerous voltages from the output of the drive or from any external option unit. The supply must be disconnected by an approved electrical isolation device before gaining access to the electrical connections. With the sole exception of the SAFE TORQUE OFF function, none of the drive functions must be used to ensure safety of personnel, i.e. they must not be used for safety-related functions. Careful consideration must be given to the functions of the drive which might result in a hazard, either through their intended behaviour or through incorrect operation due to a fault. In any application where a malfunction of the drive or its control system could lead to or allow damage, loss or injury, a risk analysis must be carried out, and where necessary, further measures taken to reduce the risk - for example, an over-speed protection device in case of failure of the speed control, or a fail-safe mechanical brake in case of loss of motor braking. The SAFE TORQUE OFF function has been approved1 as meeting the requirements of EN954-1 category 3 for the prevention of unexpected starting of the drive. It may be used in a safety-related application. The system designer is responsible for ensuring that the complete system is safe and designed correctly according to the relevant safety standards. 1Independent approval by BGIA is pending. 1.4 uploads/Industriel/ digitax-st-guide.pdf
Documents similaires
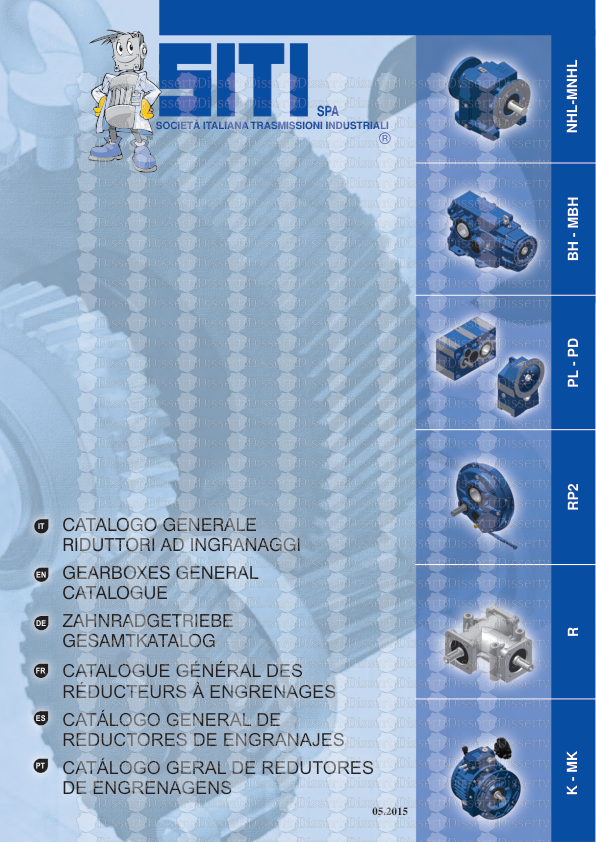
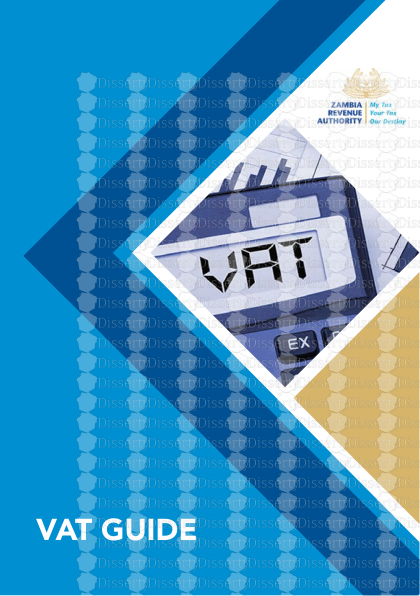
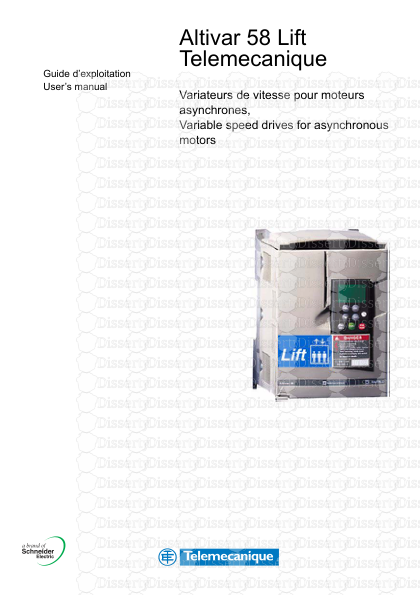
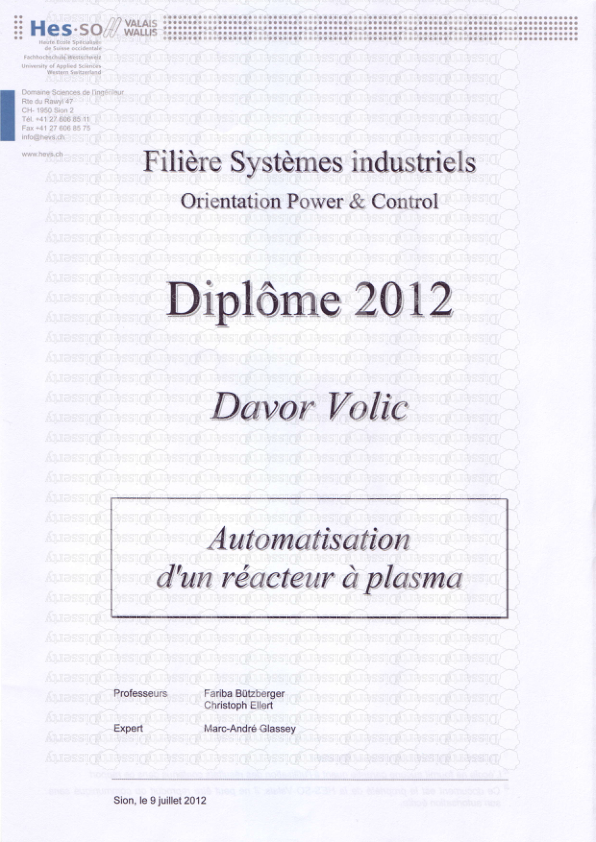
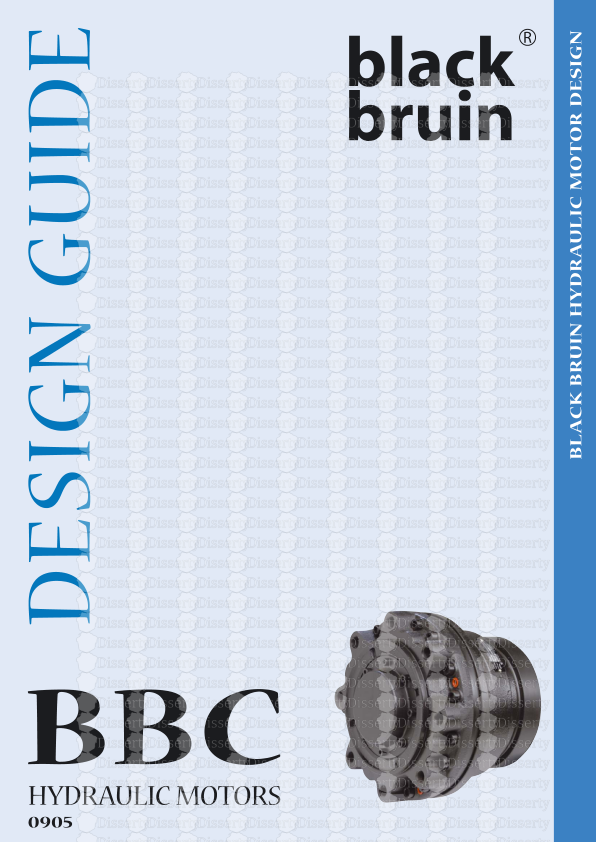
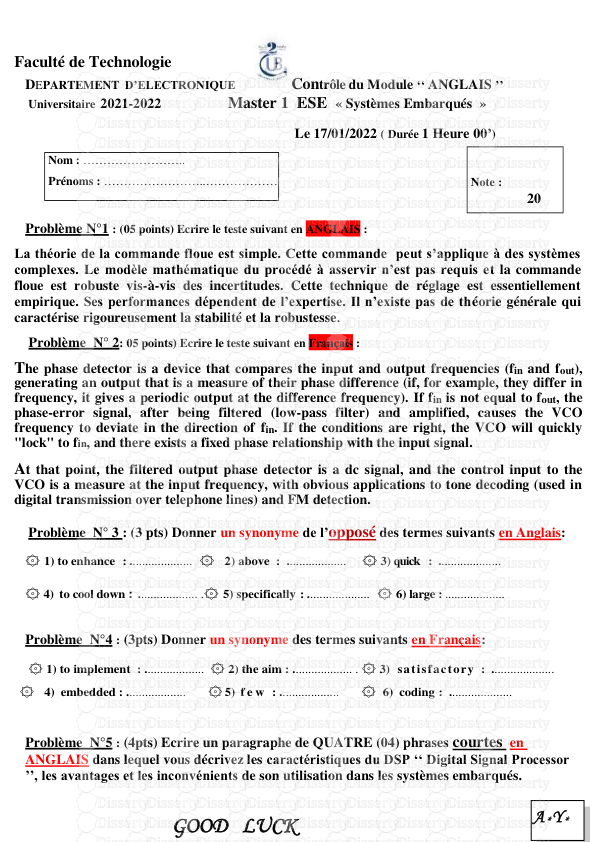
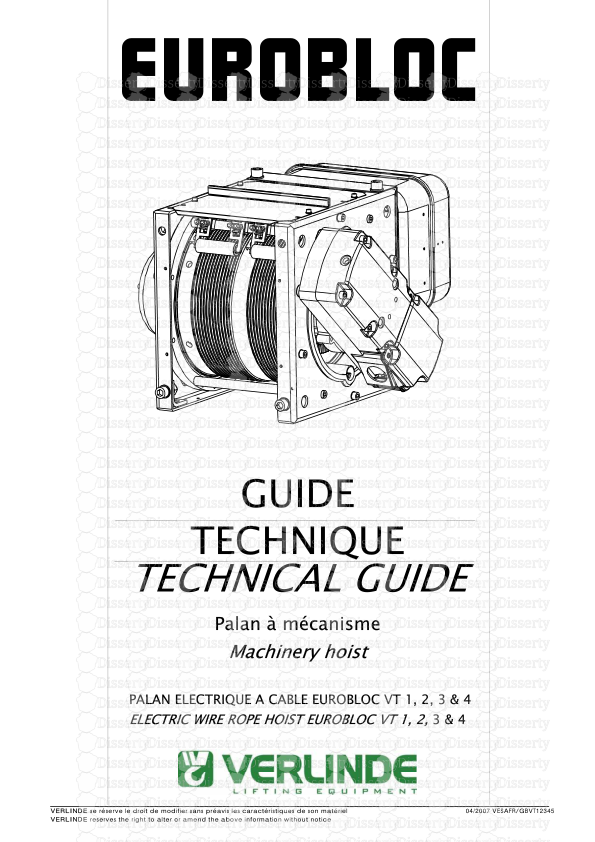
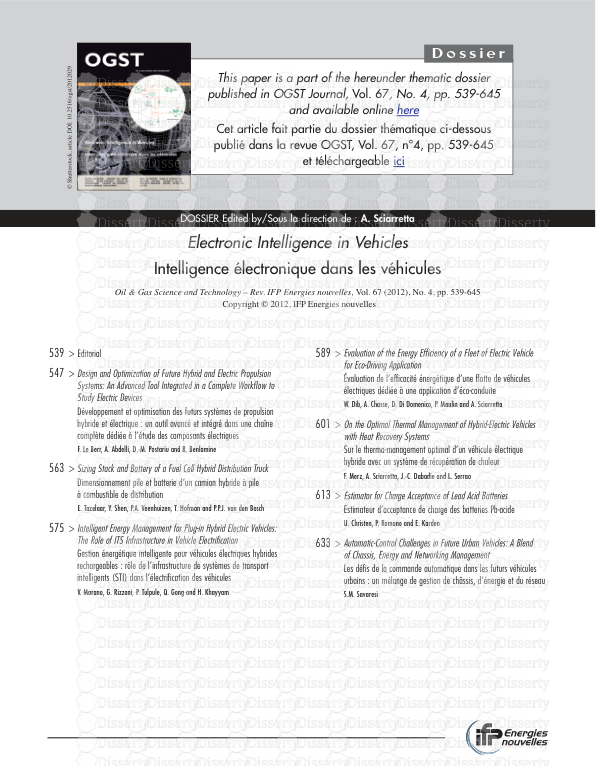
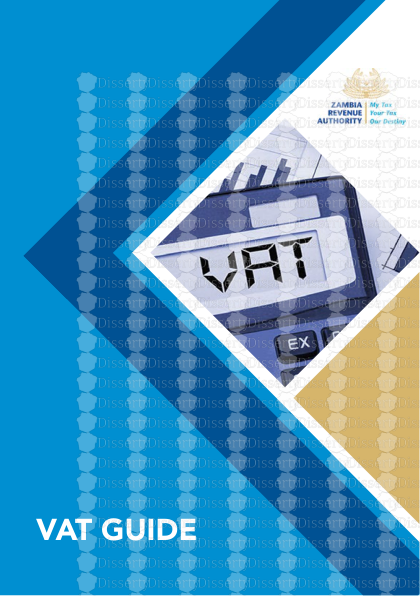
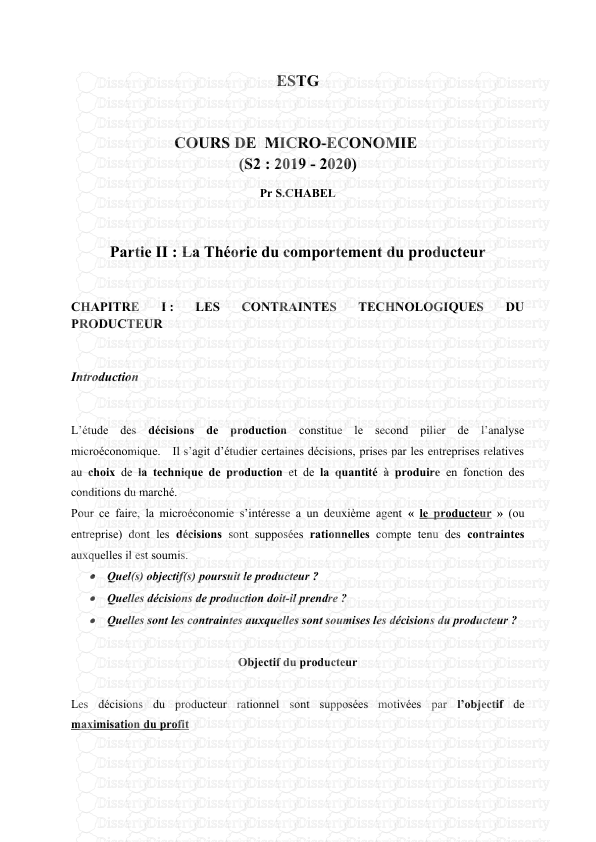
-
42
-
0
-
0
Licence et utilisation
Gratuit pour un usage personnel Attribution requise- Détails
- Publié le Mar 01, 2022
- Catégorie Industry / Industr...
- Langue French
- Taille du fichier 6.5110MB