Royaume du Maroc Université HASSAN 1er – Settat Mémoire de projet de fin d’étud
Royaume du Maroc Université HASSAN 1er – Settat Mémoire de projet de fin d’étude Réalisé au sein de LEONI Aïn Sebaâ Par Salaheddine BAHEDDA En vue d’obtenir le titre : Ingénieur d’Etat Spécialité : Génie industriel ______________________________________________________ Intégration d’une approche de modélisation dans une démarche Lean Manufacturing visant l’amélioration de la performance du processus « COUPE » ______________________________________________________ Soutenu le 22/07/2015 Devant le jury Ahmed MOUSRIJ Professeur à FST SETTAT Président Hassan GZIRI Professeur à FST SETTAT Rapporteur Wafaa DACHRY Professeur à FST SETTAT Rapporteur Année universitaire : 2014-2015 2 REMERCIEMENT Avant d’d’entamer le détail de notre projet de fin d’études, il nous tient à cœur de remercier toutes les personnes de mérite sans qui ce travail n’aurait jamais abouti. Nous exprimons nos vifs remerciements à mon encadrant pédagogiques M.ALAMI SEMMA pour son soutien inconditionnel, sa disponibilité, ses conseils, son apport dans le projet et l’aide permanente qu’il nous a prodiguée. Très grands sont les sentiments de gratitude et de considération que j’exprime à l’égard de notre tuteur de stage, M.ELKHALFI ABDELLATIF, Responsable du projet KI2/NCR pour ses orientations, ses conseils et son aide précieuse tout au long de notre période de stage. Nous savons gré également aux membres du jury, M.SEMMA, M.ECHCHATBI qui ont eu l’obligeance d’accepter d’évaluer ce travail. Aussi suis-je très reconnaissants à M.FOUAD RIANE, professeur de la Faculté des Sciences et Techniques de Settat, pour son soutien inconditionnel, sa disponibilité, ses conseils. Nous n’omettrons pas de remercier toute l’équipe de production à LEONI AIN SEBAA en particulier M.GHALIL KHALID, M.MOUNIR ESSAFI, M.GRINANE YOUSSEF, et M.SEHLI MOUNIR pour les informations très utiles qu’ils m’ont fournies et pour le temps qu’ils m’ont consacré tout au long de ma période de stage. Enfin, nous remercions toutes les personnes qui ont contribué de loin ou de près à la concrétisation de ce travail. 3 RÉSUMÉ Notre projet de fin étude porte sur un système de production de fils électriques appelés communément repères. Le processus « COUPE », objet de notre étude, est composé de plusieurs machines de coupe destinées à réaliser la coupe, le dénudage et le sertissage automatique des fils. La machine découpe des fils en cuivre, pris dans des bobines, selon une gamme bien définie. Les fils fabriqués sont des fils simples, avec ou sans connexion sur les extrémités, des fils torsadés ou des fils jumelés. Une gamme de coupe est une description complète des caractéristiques des fils. A la fin d’un ordre de coupe, l’opérateur démonte et évacue la bobine de fil de cuivre correspondante. Il procède ensuite au montage de la bobine de l’ordre de coupe à réaliser. Celle-ci est censée être préparée au pied de la machine, dans une zone d’attente spécifique. L’ordre de coupe nécessite par ailleurs un ensemble d’outils de sertissage, nécessaires pour le sertissage des produits fabriqués. Ces outils de sertissage doivent être montés sur la machine de coupe. Une analyse de la pratique actuelle a permis d’identifier un certain nombre de faiblesses : La répartition manuelle de la gamme de coupe n’est pas efficace vu qu’il utilise un nombre important d’outils de sertissage, et qu’elle surcharge certaines machines au dépend d’autres. Pour cela, nous avons élaboré un programme mathématique qui permet de trouver l’affectation préalable optimale des repères aux différentes machines. Ce programme, codé sous Cplex, nous permet d’affecter 1500 produits à 8 machines de coupe avec une réduction notable des outils de sertissage, environ 43% par rapport à la pratique actuelle. Ceci représente un gain substantiel en temps de changement et outils utilisés, d’autant que les temps de calcul sont négligeables. L’intervention d’une touche humaine au niveau de l’ordonnancement des ordres de coupe, ne permet pas d’en garantir l’optimalité, d’autant que les repères sont d’une diversité considérable. Il était alors question de concevoir et développer une application informatique en langage de programmation VBA, permettant d’ordonnancer les ordres de coupe sur les différentes machines. Ainsi, lors de l’ordonnancement des ordres de coupe, les temps de changement de série seront optimisés. 4 ABSTRACT Our end-of-study project focuses on an electrical wire production system. The process "Cutting", object of our study, is composed of several cutting machines to perform cutting, stripping and wire crimping. The cutting machine cuts copper wire caught in coils, according to a well defined cutting range. The wires made are simple wire, with or without connection on the ends, twisted wire or dual wire. The cutting range is a full description of characteristics of wires. At the end of a cutting order, the operator dismantles and evacuates the corresponding wire coil, then; he proceeds to the mounting of the coil of next cutting order. This is supposed to be prepared in front of the machine, in a specific waiting area. The cutting order also requires a set of crimping tools, necessary for crimping of products made. These crimping tools must be mounted on the cutting machine. An analysis of the current practice has identified a number of weaknesses: The manual repartition of the cutting range is not effective because it uses a large number of crimping tools, and it overloads some machines at the expense of others. For this, we developed a mathematical program that finds the optimal allocation of products to the various machines. This program, encoded as CPLEX, allows to allocate 1500 products in to 8 cutting machines, with a significant reduction in crimping tools, approximately 43% compared to current practice. This represents a substantial gain in tool change time, especially as the computing time is negligible. The intervention of a human touch at scheduling of cutting orders, does not guarantee its optimality, especially as products are of a considerable diversity. It was then a question of conception and developing a computer application in VBA programming language, allowing scheduling the cutting orders on different machines. Thus, in the scheduling of cutting orders, the times of series change will be optimized. 5 TABLE DES MATIÈRES RESUME ........................................................................................................................................................ 3 ABSTRACT ..................................................................................................................................................... 4 TABLE DES MATIERES..................................................................................................................................... 5 LISTE DES FIGURES......................................................................................................................................... 8 LISTE DES TABLEAUX....................................................................................................................................10 LISTE DES ABREVIATION...............................................................................................................................11 INTRODUCTION GENERALE...........................................................................................................................12 Chapitre 1 – Contexte générale du projet.....................................................................................13 INTRODUCTION ..................................................................................................................................13 1. PRESENTATION DE L’ORGANISME D’ACCUEIL ..........................................................................................14 1.1. PRESENTATION DE L’ENTREPRISE LEONI .....................................................................................14 1.2. HISTORIQUE ................................................................................................................................15 1.3. ORGANISATION DU GROUPE ........................................................................................................16 1.3.1. Division Wire & Câble Solutions .................................................................................16 1.3.2. Division Wiring Systèmes.............................................................................................16 1.4. PRESENTATION DU SITE AIN SEBAA ...........................................................................................17 1.5. PROCEDES DE FABRICATION .........................................................................................................18 1.5.1. Description physique des câblages ............................................................................18 1.5.2. Les élements d’un câblage moyen ..............................................................................19 1.6. PROCESSUS DE PRODUCTION .......................................................................................................20 1.6.1. La coupe .........................................................................................................................20 1.6.2. Le sertissage ...................................................................................................................21 1.6.3. La préparation ...............................................................................................................22 1.6.4. L’assemblage .................................................................................................................23 1.6.5. Les contrôles..................................................................................................................24 1.7. DEMARCHE QUALITE LEONI........................................................................................................25 1.7.1. QRQC: Quick Response Quality Control .....................................................................25 1.7.2. PDCA FTA: ......................................................................................................................26 1.7.3. Audit interne .................................................................................................................26 2. CONTEXTE DU PROJET ............................................................................................................................27 2.1. PROBLEMATIQUE.........................................................................................................................27 2.3. DEMARCHE .................................................................................................................................29 2.4. PLANIFICATION............................................................................................................................30 6 CONCLUSION .......................................................................................................................................30 Chapitre 2 – Etude de l’existant.......................................................................................................31 INTRODUCTION ..................................................................................................................................31 1. DESCRIPTION DU PROCESSUS « COUPE » .............................................................................................32 1.1. LE DIAGRAMME SIPOC .................................................................................................................32 1.2. LES ACTEURS DU PROCESSUS........................................................................................................33 1.3. IMPLANTATION DE LA ZONE COUPE...............................................................................................34 1.4. PRODUIT......................................................................................................................................35 1.4.1. Matière première..........................................................................................................35 1.4.2. Les types de produit .....................................................................................................35 1.4.3. Les familles de produit .................................................................................................36 1.5. RESSOURCES MATERIELLES ..........................................................................................................37 1.5.1. Les Machines de coupe ...............................................................................................37 1.5.2. L’Outil de sertissage .....................................................................................................38 1.5.3. Le Kit joint ......................................................................................................................38 1.6. DIAGRAMME DE FLUX FONCTIONNEL CROISE................................................................................39 2. CARTOGRAPHIE DE LA CHAINE DE VALEUR ..............................................................................................40 2.1. SELECTION DE LA FAMILLE DE PRODUIT A CARTOGRAPHIER...........................................................40 2.2. CARTOGRAPHIER DE L’ETAT ACTUEL .............................................................................................41 3. IDENTIFICATION ET ANALYSE DES PRINCIPAUX INDICATEURS DE PERFORMANCE .......................................42 3.1. GENERALITE SUR LE TAUX DE RENDEMENT GLOBAL ......................................................................42 3.2. ANALYSE DE L’INDICATEUR TRG ..................................................................................................44 3.3. ANALYSE DE DEROULEMENT D’UN CHANGEMENT DE SERIE ...........................................................49 3.4. ANALYSE DE LA REPARTITION DE LA GAMME DE COUPE ................................................................54 3.5. ANALYSE DE LA FONCTION ORDONNANCEMENT ...........................................................................58 3.5.1. Déroulement normal ....................................................................................................59 3.5.2. Déroulement exceptionnel..........................................................................................60 CONCLUSION .......................................................................................................................................61 Chapitre 3 – Actions d’amélioration................................................................................................62 INTRODUCTION ..................................................................................................................................62 1. OPTIMISATION DE LA REPARTITION DE LA GAMME DE COUPE..................................................................63 1.1 FORMULATION MATHEMATIQUE DU PROBLEME ............................................................................63 1.1.1 Définition des ensembles .............................................................................................63 1.1.2 Construction de la fonction objective .........................................................................64 1.1.3 Construction des contraintes .......................................................................................65 1.1.4 Formulation complète du problème ...........................................................................66 7 1.2 MISE EN ŒUVRE DU MODELE MATHEMATIQUE .............................................................................67 1.3 ANALYSE DES RESULTATS OBTENUS ...............................................................................................68 1.4 PARAMÉTRAGE DE LA RÉPARTITION FUTURE .................................................................................70 2. AUTOMATISATION DE LA FONCTION ORDONNANCEMENT .......................................................................71 2.1 CONCEPTION DE LA SOLUTION ......................................................................................................71 2.2. PREPARATION DES ELEMENTS D’ENTREE .......................................................................................72 2.2.1 Les opérations de changement de série .....................................................................72 2.2.2. Les caractéristiques des repères.................................................................................73 2.2.3. L’affectation des kits joint ...........................................................................................73 2.3 PRINCIPE DE FONCTIONNEMENT ............................................................................................74 LES ETAPES DE L’ALGORITHME : ....................................................................................................74 2.4 MISE EN ŒUVRE DE L’APPLICATION ..............................................................................................77 3. AMELIORATION DU TEMPS DE REGLAGE DE L’OUTIL DE SERTISSAGE ........................................................82 4. AMELIORATION DE L’APPROVISIONNEMENT DE LIGNE.............................................................................84 CONCLUSION .......................................................................................................................................85 Chapitre 4 – Contrôle des améliorations ......................................................................................86 INTRODUCTION ..................................................................................................................................86 1. SUIVI DE L’INDICATEUR TRG ...................................................................................................................87 2. STANDARDISATION DE LA REPARTITION DE LA GAMME DE COUPE ............................................................88 4. EXTENSION DE L’APPLICATION D’ORDONNANCEMENT .............................................................................88 CONCLUSION .......................................................................................................................................89 CONCLUSION GENERALE ET PERSPECTIVE .....................................................................................................90 BIBLIOGRAPHIE ...........................................................................................................................................91 WEBOGRAPHIE ...........................................................................................................................................91 ANNEXES ....................................................................................................................................................92 ANNEXE A : MODELE MATHEMATIQUE EN LANGAGE OPL .............................................................93 ANNEXE B : FICHIER ALIMENTATEUR DU MODELE MATHEMATIQUE ...............................................94 ANNEXE C : MATRICE D’AFFECTATION DES PRODUITS ...................................................................95 ANNEXE D : MATRICE D’AFFECTATION DES uploads/Industriel/ pfe-salah-eddine-bahedda.pdf
Documents similaires
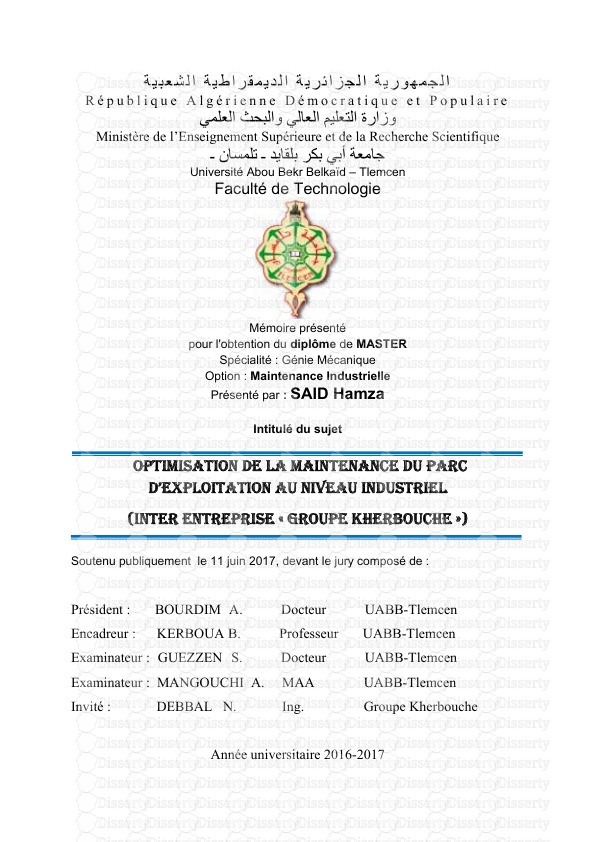
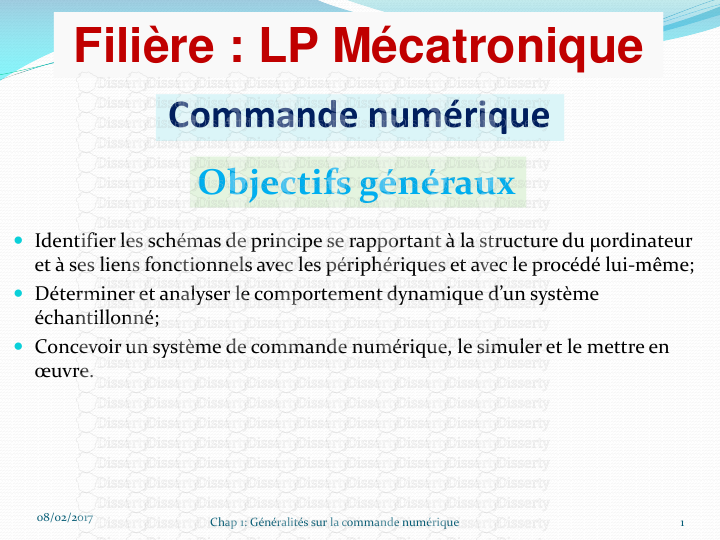
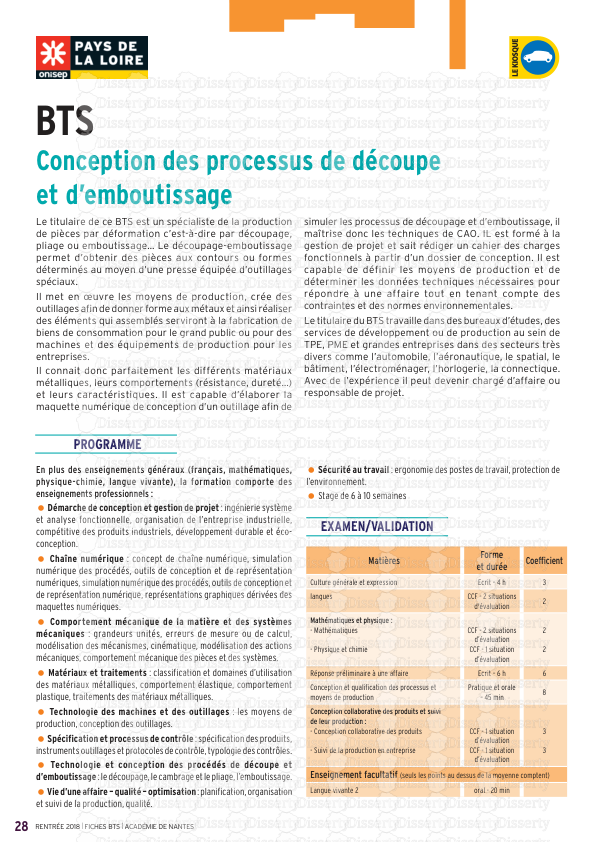
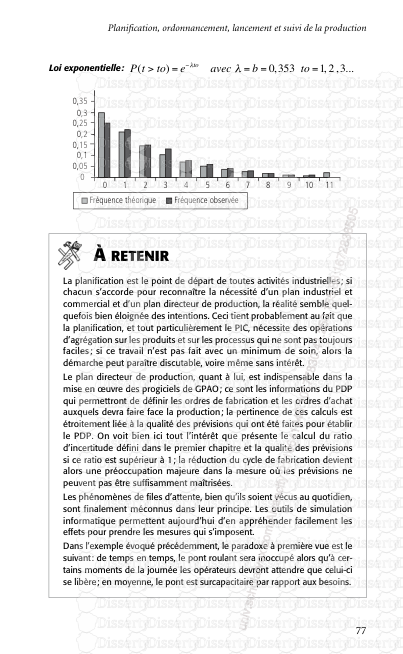
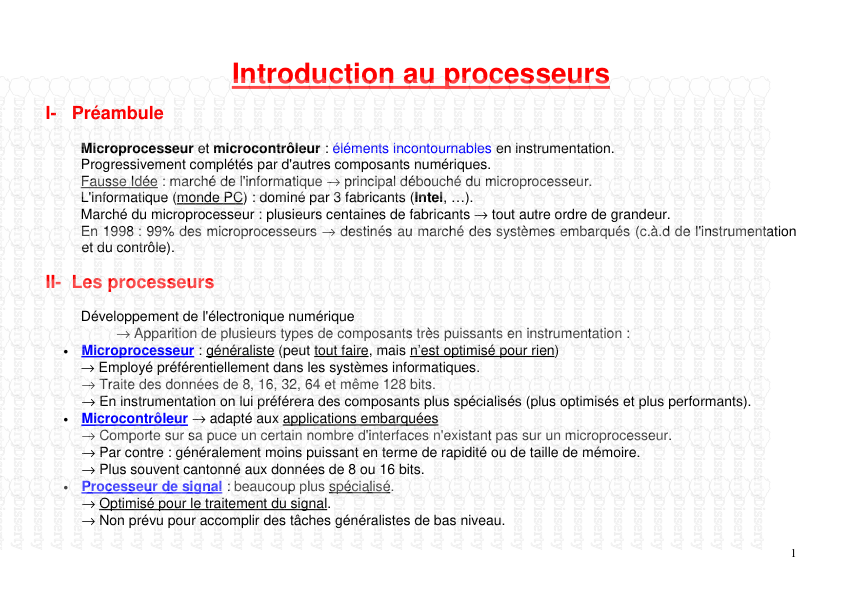
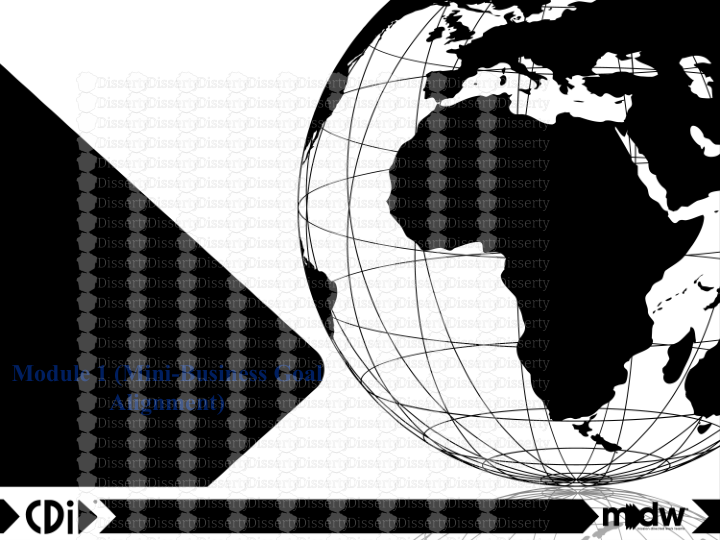
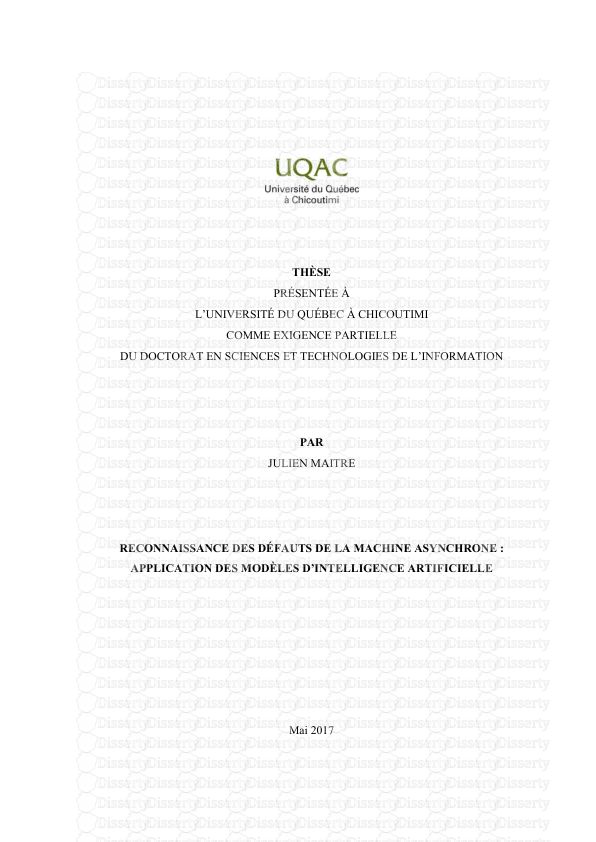
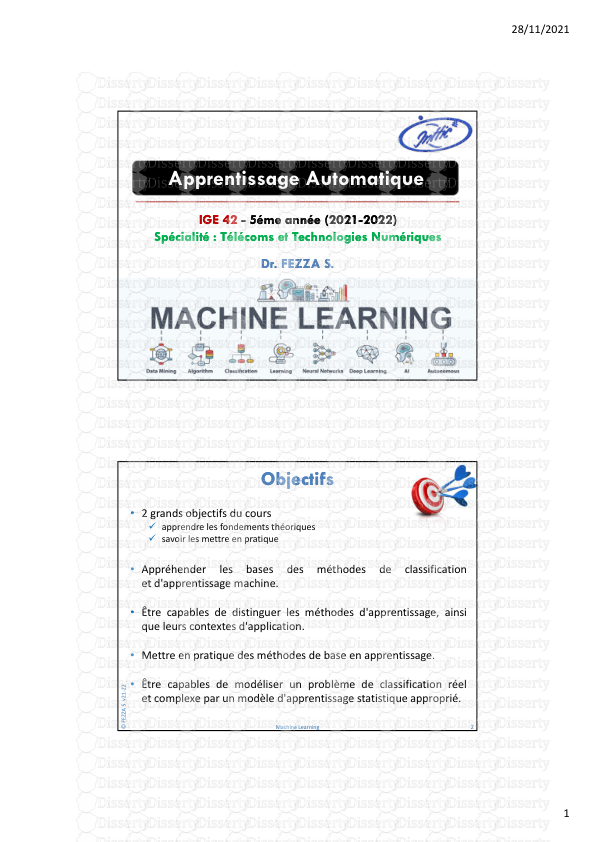
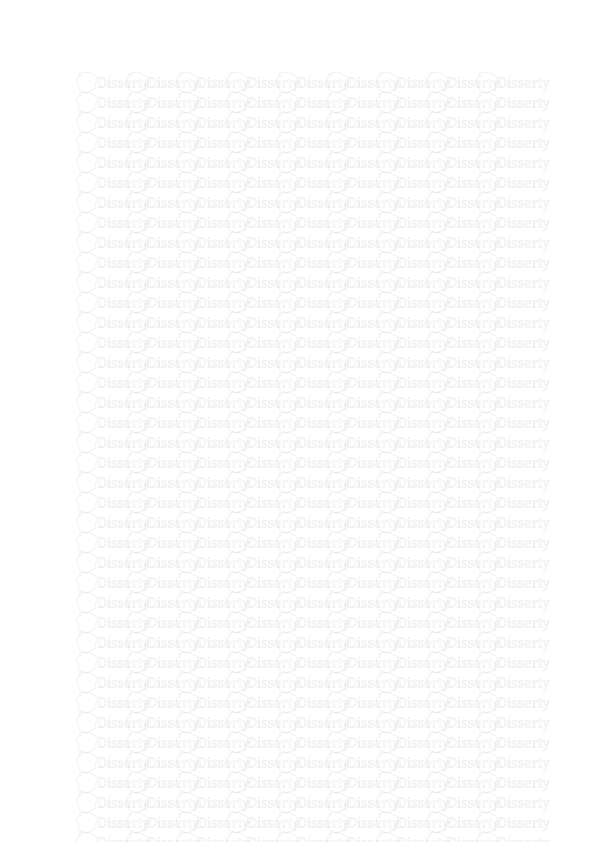
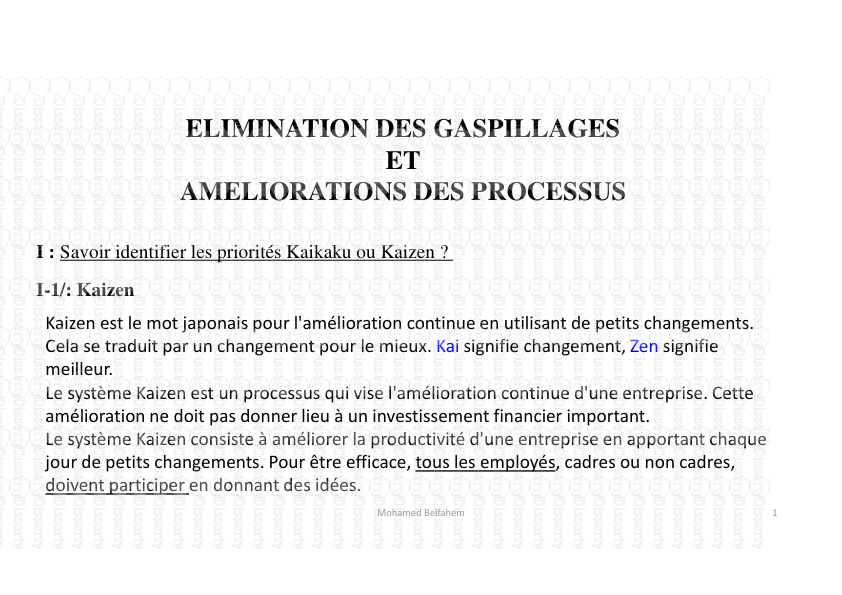
-
63
-
0
-
0
Licence et utilisation
Gratuit pour un usage personnel Attribution requise- Détails
- Publié le Jul 14, 2022
- Catégorie Industry / Industr...
- Langue French
- Taille du fichier 4.5511MB