LE SOUDAGE Sommaire Généralités Conception d'un assemblage soudé Soudage par fr
LE SOUDAGE Sommaire Généralités Conception d'un assemblage soudé Soudage par friction Soudage par aluminothermie Énergie de soudage Thermique du soudage Métallurgie du soudage Examens, essais et mesures Cet ouvrage fait partie de la collection Technologie Le chapitre présent aborde de manière générale la soudure dans le contexte de la pièce, de l'ensemble fabriqué. Il ne prétend pas être exhaustif, mais donner des orientations générales sur les cas les plus courants. Un produit complexe — machine, structure — est fait de plusieurs pièces assemblées. Cela permet : de simplifier la conception et la fabrication : on ne travaille que sur un sous-ensemble simple à la fois ; de faciliter la manutention, le transport : on transporte en pièces détachées ; d'utiliser des éléments normalisés, fabriqués en grand nombre et par plusieurs entreprises concurrentes, ce qui réduit les coûts et temps de fabrication (économie d'échelle) ainsi que les risque de pénurie. Il existe deux grandes familles d'assemblage : les assemblage démontables : vissage, boulonnage, serrage dans un étau, bridage, … les assemblages indémontables : collage, soudage, sertissage, rivetage, … Les assemblages démontables facilitent la maintenance (démontage de pièces pour les changer ou les réparer), le transport (si l'ensemble doit être déplacé régulièrement), le réglage, le désassemblage en fin de vie (tri). L'assemblage nécessite en général peu de matériel (tournevis, clefs) et permet d'avoir des tolérances serrées, typiquement 1/10 à 1/100 mm. Mais le serrage peut s'altérer : les vibrations desserrent les vis, l'assemblage prend du jeu. Choix du mode d'assemblage Les assemblages indémontables sont robustes et tiennent dans la durée, mais la réparation ou le démontage définitif nécessitent de découper les pièces. Le soudage est donc choisi dans le cas : d'un assemblage définitif ; ne nécessitant pas de tolérances serrées (typiquement de l'ordre du mm) ; dont les pièces sont faites d'un matériau fusible (qui fond). Notons que l'on peut usiner des surfaces fonctionnelles après soudure, et donc avoir des tolérences serrées. Il faut pour cela prévoir des surépaisseurs — matière à enlever — supérieures aux déplacements relatifs provoqués par la soudure, et disposer d'une machine pouvant usiner l'assemblage, qui est en général de grandes dimensions. Le soudage est donc bien adapté pour la construction métallique (escaliers, passerelles, gardes-corps), les tolérances en génie civil étant en général de l'ordre du cm. Dans le cas de l'assemblage de pièces mécaniques par soudage — ensemble mécano-soudé —, donc avec notion de mouvement, il faut s'assurer que le mécanisme est isostatique afin de pouvoir s'adapter aux imperfection de positionnement et d'orientation (défaut de coaxialité, de concentricité, …). Le soudage permet également d'assurer l'étanchéité, il est donc utilisé en tuyauterie, et pour la fabrication des cuves, réservoirs, chaudières et appareil de pression (chaudronnerie). Mais tous les matériaux fusibles ne sont pas soudables. Par exemple, les aciers dits « trempés » (rendus durs par un refroidissement rapide) fondent comme tous les aciers, mais la soudure les fragilise. Comme nous l'avons vu précédemment, il existe plusieurs modes de soudage. Le choix dépend des matériaux à assembler, de la résistance attendue, ainsi que de critères économiques. Le coût de la mise en œuvre du procédé dépend : du temps d'opération, donc du « rendement » du procédé ; de la complexité de la soudure, de la qualification requise pour l'opérateur ; du coût des consommables : métal d'apport, gaz de protection ou gaz actif, énergie. Par ailleurs, le mode de soudage peut être imposé par une norme. Voici quelques critères généraux de choix : si les pièces de base ne doivent pas être altérées : brasage (soudure hétérogène) ; le chauffage est modéré, seul le métal d'apport fond, cela nécessite peu de matériel (fer à souder, petit chalumeau), déforme peu les pièces, et permet d'assembler des matériaux très différents comme du verre et du métal, du polymère et du métal (composant sur carte en électronique) ; si l'assemblage doit avoir une grande résistance mécanique : soudage autogène ; le métal de base (c'est-à-dire les pièces) et le métal d'apport fondent et se resolidifient, on obtient donc au final une seule pièce (continuité métallique), mais le chauffage est important (température de fusion du métal) et cela déforme l'assemblage ; si les pièces sont en acier : en acier non allié (acier au carbone) à basse teneur en carbone : tous les procédés de soudage peuvent être utilisés ; en acier inoxydable : le bain de fusion doit être protégé de l'oxygène de l'air, on utilise donc essentiellement le procédé MIG (metal inert gas, procédé 131[1]) ou bien TIG (tungstene inert gas, procédé 141), Choix du mode de soudage si les métaux s'oxydent facilement : alliages d'aluminium, de nickel, de titane : le problème est similaire à celui des inox, on utilise le TIG (141). Le soudage au chalumeau — soudage autogène (procédés 311 à 313), brasage (procédés 91, 94 et 971) — est le plus simple à mettre en œuvre (il ne nécessite pas de source d'électricité, le poste avec les bouteille de gaz est autonome). Les procédés à arc (désignation commençant par un 1) sont les plus utilisés industriellement pour le soudage autogène : la fusion est très localisée, ce qui limite la déformation, et la productivité est importante, mais le refroidissement est rapide (phénomène de trempe, contraintes résiduelles). Les cas les plus courants sont : électronique (assemblage de composants sur circuit imprimé — carte polymère) : brasure avec un alliage d'étain et de plomb (par exemple 60 %Sn/40 % Pb, fondant à 190 °C), avec un fer à souder (énergie électrique convertie en chaleur par une résistance) ; plomberie : assemblage de tuyaux de cuivre par soudo-brasage (brasage au chalumeau oxyacétylénique), le métal d'apport est un alliage de cuivre contenant du phosphore, du zinc (laiton) ou de l'argent, ces éléments d'alliage permettant d'abaisser le point de fusion entre 600 et 800 °C (le cuivre fond à 1 085 °C) ; pour les raccords gaz, seul l'alliage cuivre/argent est autorisé (meilleure résistance mécanique) ; fonte, acier galvanisées (recouvert de zinc) : soudo-brasage (procédé 97), le métal d'appport étant un laiton à 40 % de zinc (CuZn40, CW509L selon la désignation européenne) ; acier non allié à basse teneur en carbone (aciers d'usage général, aciers de construction, aciers « à ferrer les ânes ») : on choisit en priorité les procédés suivants : soudage à l'arc avec électrode enrobée (procédé 111) : ne nécessite qu'un poste à souder (en particulier pas de bouteille de gaz), la fusion de l'enrobage produit un gaz qui protège le bain de fusion, c'est le procédé à arc qui a le meilleur rendement (chaleur produite par rapport à l'électricité consommée) ; le cordon doit être meulé entre deux passes pour éviter des inclusions de laitier ; MAG (metal active gas, procédé 135) : la présence d'un gaz actif permet d'abaisser la température et donc de moins déformer les pièces, le métal d'apport est sous forme de fil qui défile de manière semi-automatique ; il nécessite la présence d'une bouteille de gaz, mais le caractère semi-automatique facilite l'opération. Le procédé TIG (141) peut être utilisé dans tous les cas et donne un cordon de soudure d'excellente qualité, mais : il nécessite une bonne formation de l'opérateur ; il nécessite la présence d'une bouteille de gaz protecteur ; il a un rendement chaleur produite/électricité consommée médiocre ; la température est très élevée (jusqu'à 4 000 °C au niveau du cordon pour une température d'arc pouvant atteindre 19 000 °C[2], contre 3 100 °C pour l'électrode enrobée et le MAG), il y a donc une déformation importante. Le refroidissement d'une soudure est rapide, on se retrouve donc dans des conditions de trempe. Or, la formation de martensite — phase durcissante des aciers trempables — fragilise la soudure. Il faut donc s'assurer que l'on ne formera pas de martensite. Il existe d'autres problèmes métallurgiques. Tout ceci conditionne le choix de la nuance des pièces — métal de base — et de la baguette — métal d'apport. Le premier cas est celui des aciers de construction de type acier d'usage général, S185 (1.0035) à S355JR (1.0045) ; acier pour construction mécanique, E155 (1.003) à E370 (1.0261) ; Choix de l'acier acier pour appareil de pression à haute température, P195GH (1.0348) à P355GH (1.0473) ; Ces aciers sont des aciers à basse teneur en carbone (inférieure à 0,25 % en masse), ils ne sont pas trempables, le problème ne se pose pas. Par contre, c'est le carbone qui permet d'élever la limite élastique. Si l'acier doit avoir une résistance importante, en particulier pour réduire la masse de l'ensemble, on choisira des nuances particulières : des aciers à haute limite d'élasticité (HLE) soudables. Pour ces aciers, on ajoute de petites quantités d'éléments d'alliage — niobium, titane, vanadium, … — qui durcissent l'acier tout en diminuant sa trempabilité (alphagènes) : aciers formables à froid de type S315MC (1.0972) à S700MC (1.8974) ; le suffixe M indique un formage thermomécanique (typiquement laminage) et le C un formage spécial à froid (cold forming) ; aciers soudables à grain fin de type S275N (1.0486) à uploads/Industriel/ soudage-conception-d-x27-un-assemblage-soude.pdf
Documents similaires
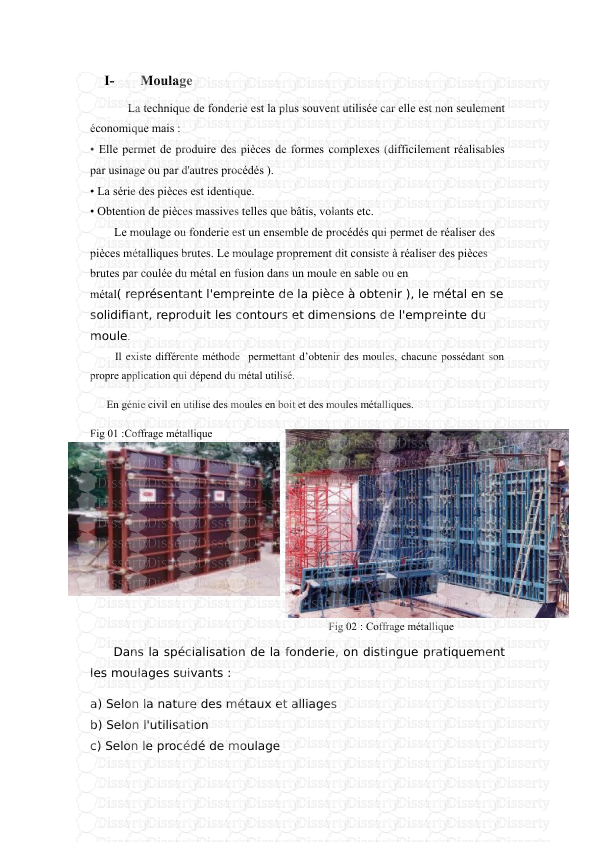
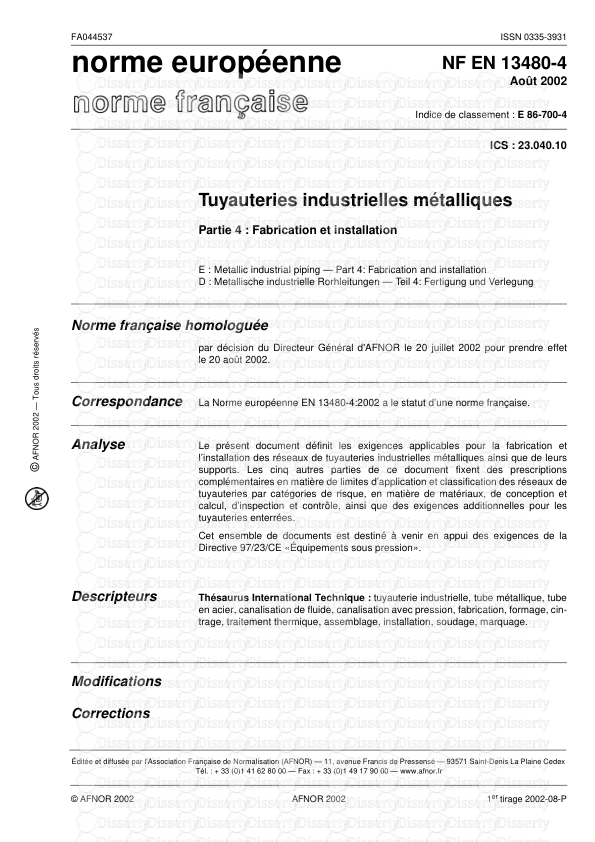
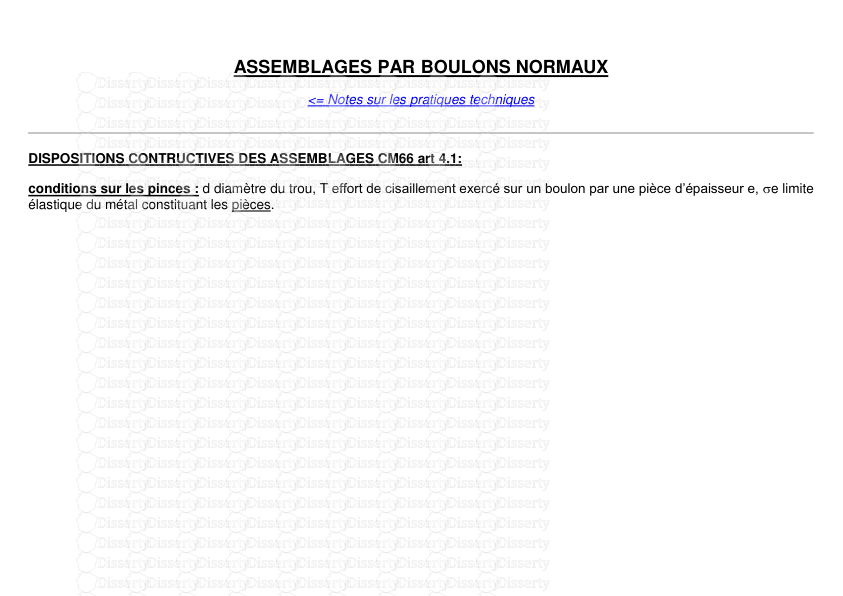
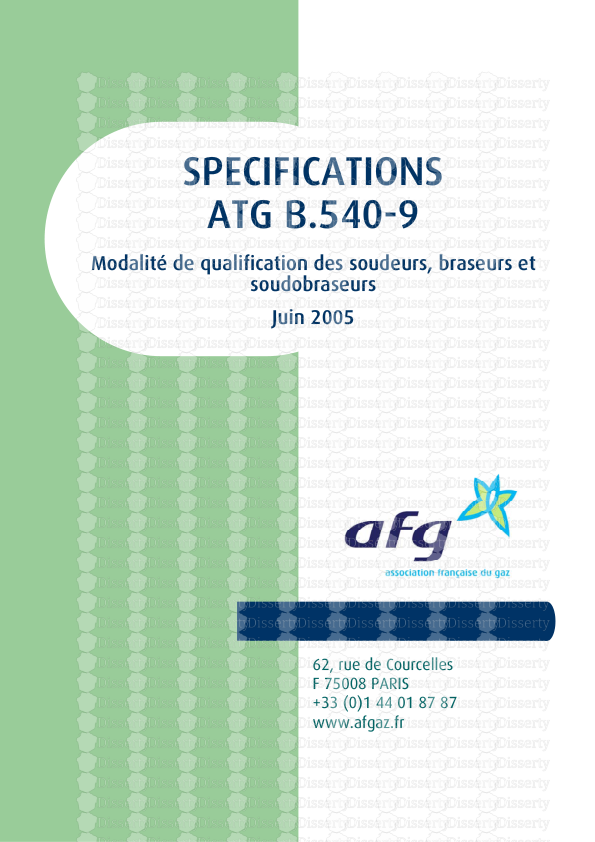
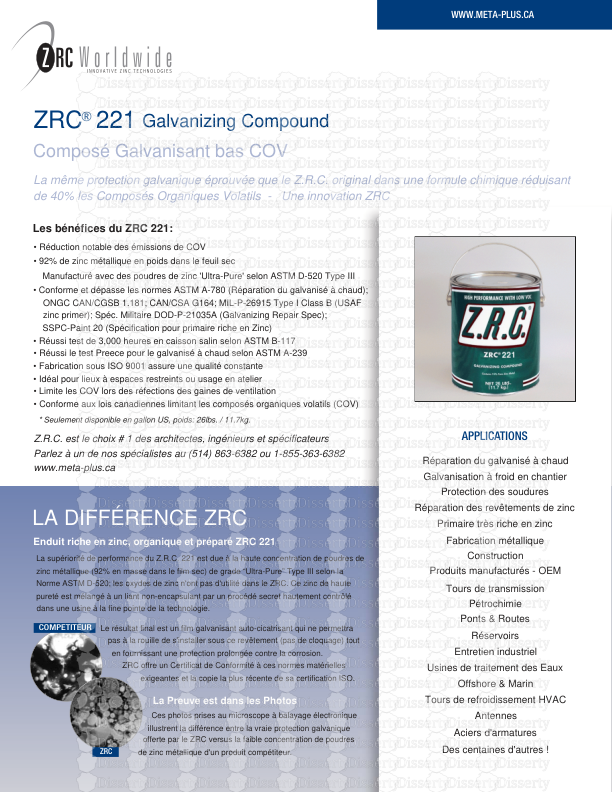
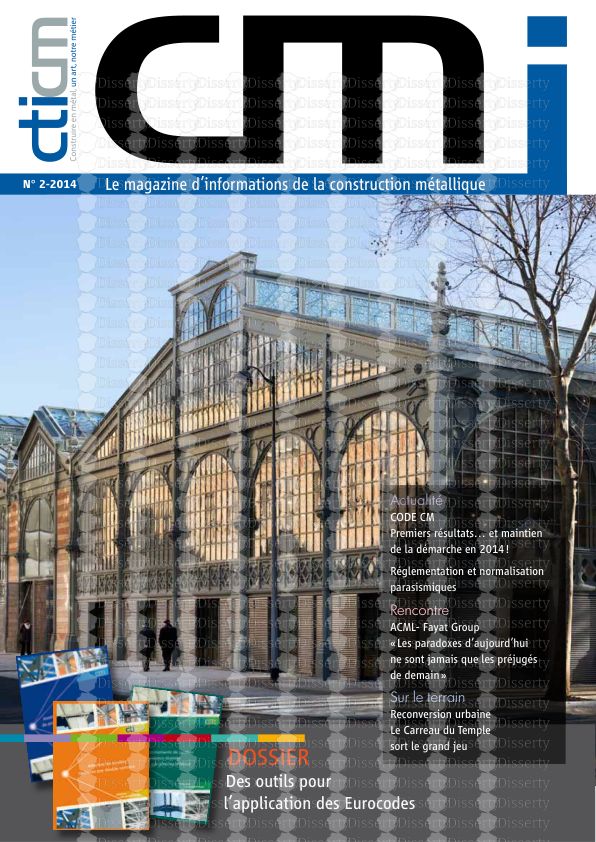
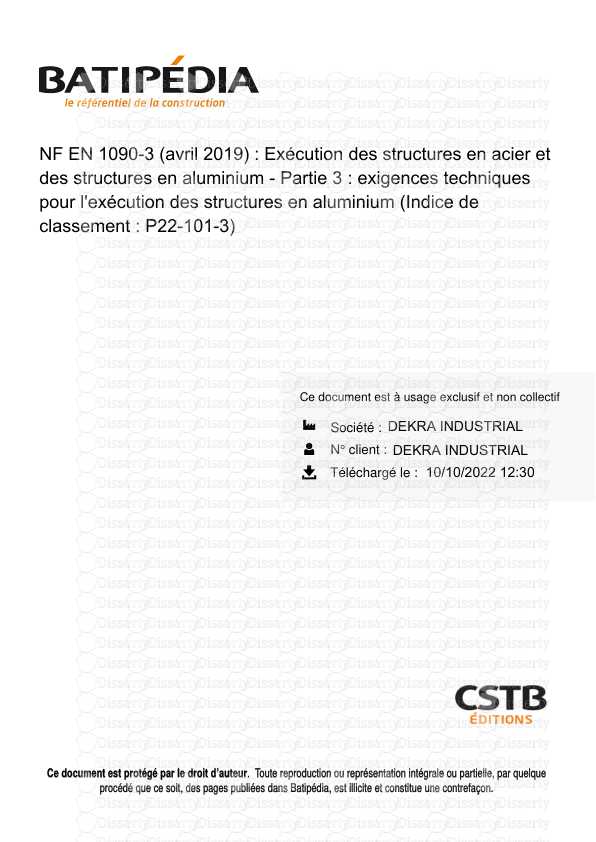
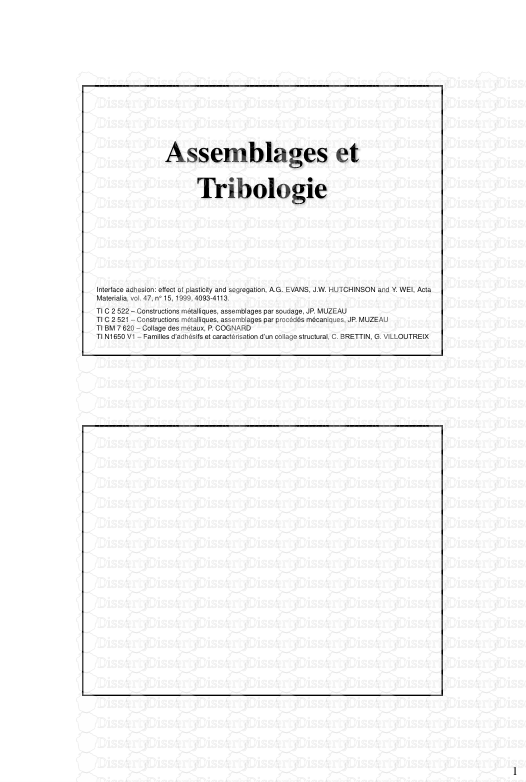
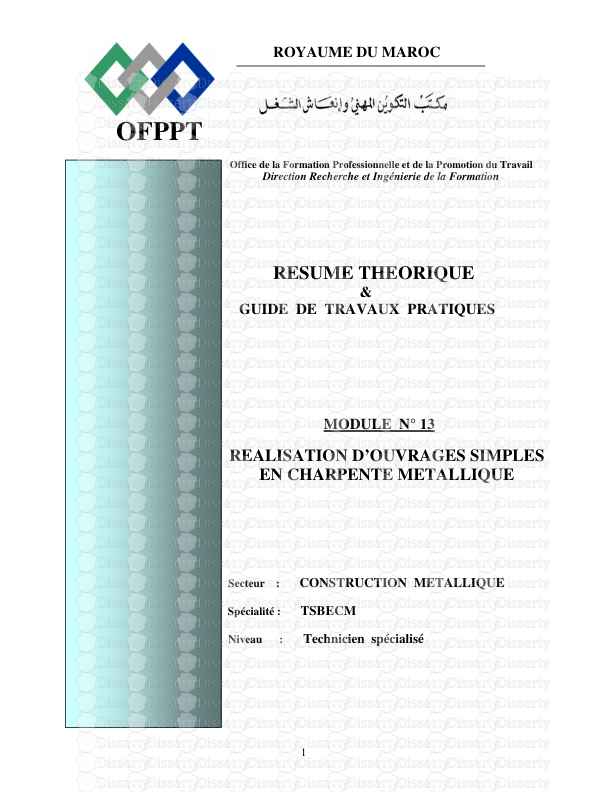
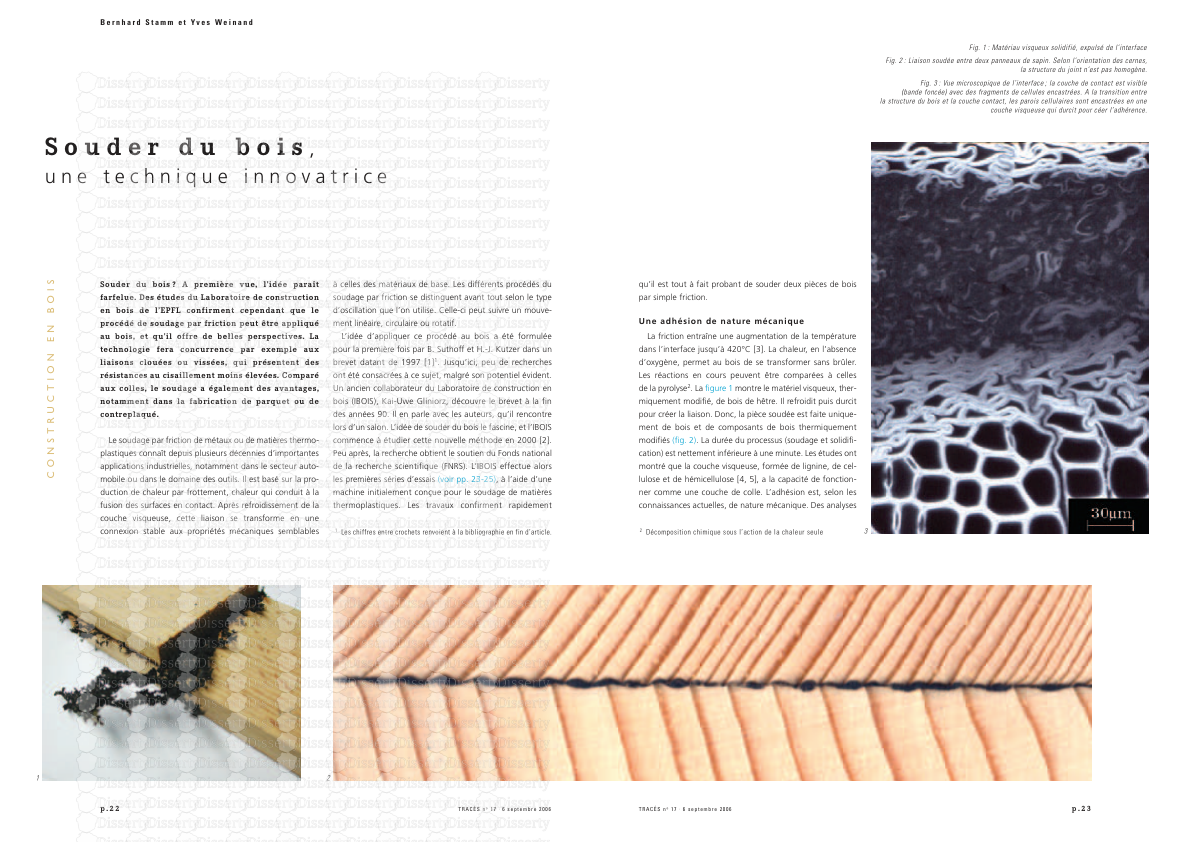
-
50
-
0
-
0
Licence et utilisation
Gratuit pour un usage personnel Attribution requise- Détails
- Publié le Mai 06, 2022
- Catégorie Industry / Industr...
- Langue French
- Taille du fichier 0.6394MB