Fastening & Assembly Fundamental Manufacturing Processes Study Guide, DV03PUB8
Fastening & Assembly Fundamental Manufacturing Processes Study Guide, DV03PUB8 - 1 - Training Objective After watching the program and reviewing this printed material, the viewer will gain knowledge and understanding of the various fastening devices and assembly methods used in manufacturing. • Various mechanical fastener types and assembly devices are shown • Adhesive bonding is explained • Manual and automated assembly systems are demonstrated • Major automated assembly machines are illustrated Assembly in manufacturing consists of fastening various components into either a functioning unit or a higher level subassembly. Ideally, a product design should reduce to a minimum the number of parts requiring assembly. In most situations, however, the fastening and assembly of several component parts is a necessity. Assembly may be performed manually, semi-automatically, or by fully automatic operation using mechanical fastening, and or joining methods, such as adhesive bonding. Mechanical Fastening The most common mechanical fastening methods include: • Integral fasteners • Threaded fasteners • Non-threaded fasteners • Stapling Integral fasteners are formed areas designed into sheet metal products. Integral fasteners function by interlocking or interfering one component with other components during assembly. The three most common types of integral fasteners include: • Embossed protrusions • Edge seams • Hemming Embossed protrusions are formed between two sheet metal components by drawing a small cup-shaped section through them. As the metals are squeezed through the components they impact and expand on a die, producing a interlocked button with a greater diameter than the drawn section. This process is also called clinching or clinch joining. Edge seams interlock the edges of sheet metal parts by folding the edges of both components over each other. Edge seams not only reinforces the entire assembly, but also eliminates sharp edges. Hemming assembles sheet metal parts together by bending the edge of one component more than 180 degrees over the edge of another sheet metal component. Threaded fasteners are a low-cost means of mechanically joining and holding parts together. They are used where subsequent disassembly and reassembly may be required. Threaded fasteners include machine screws, nuts and bolts, and range in size from the miniscule to large diameters and lengths used in bridge and building construction. Threaded fasteners are available in both standard and metric sizes as well as a variety of thread types, thread pitch, tolerances, and classifications. Threaded fasteners may be installed by hand with common hand tools or by automated machinery. In such cases, the screws often have special shaped ends, such as the cone-shaped point, to facilitate automated insertion in mating components. Fastening & Assembly Fundamental Manufacturing Processes Study Guide, DV03PUB8 - 2 - Non-threaded fasteners include: • Rivets • Pins • Washers Rivets are one piece, permanent mechanical fasteners inserted through matching holes in component parts. Various rivet setting devices and tools are then employed to form a head on the opposite end of the rivet, clinching the parts together. Rivets may be solid, semitubular, tubular, or bifurcated (split). Riveting can be done manually or automatically. A slower, but less forceful riveting method is orbital riveting. The rivet head is formed by a rotating spindle mounted tool which is offset three to six degrees. As the rotating tool contacts the work, it displaces material at the end of the rivet shank, forming the head. Orbital riveting is much quieter than conventional riveting. Pins are simple, low-cost mechanical fasteners. Once installed, they can function as locking devices, locating elements, pivots, and bearing faces. Pins may be tapered or straight, with a head or without. Two common pins types include: • Clevis pins • Dowel pins Clevis pins have a drilled hole at one end to receive a cotter pin or a spring-wire pin. Clevis pins are primarily used as pivots and linkages. Dowel pins are used to align mating parts in precise position. Washers are primarily used as bolt and screw seats to help distribute loads and stresses. One common type of washer includes the lockwasher. Lockwashers are available with either internal, external, or a combination of internal and external teeth. They are installed in assemblies which are subject to shock and vibration. Stapling is used extensively in the automotive and furniture industries. Stapling is a permanent method of assembly which is primarily performed manually using semi-automatic stapling guns pre-loaded with strips of staples glued together. Staples vary by length and point types. These point types include: • Chisel point • Chisel inside bevel point • Chisel outside bevel point • Divergent point Fastening & Assembly Fundamental Manufacturing Processes Study Guide, DV03PUB8 - 3 - Adhesive Bonding Adhesive bonding forms permanent joints that cannot be disassembled without destroying components. Adhesive bonding can be defined as molecular cohesion between unlike liquids or solids that resists interfacial separation. Adhesives can take the form of liquids, pastes, and emulsions, or as solids such as films, tapes, rods, pellets, and powders. Adhesives may be applied manually by brush or semi-automatically with extrusion or spray guns. Adhesives also may be applied automatically using production machinery dedicated to a particular part or family of parts. The advantages with respect to the use of adhesive bonding include: • Part stresses are uniformly distributed over a large surface • Similar and dissimilar materials can be joined • Thick and thin parts not suitable for mechanical fastening or welding may be bonded • Joints can be sealed from intrusive atmospheres and substances • The weight of an assembly can be significantly reduced • Costs are much less than with other fastening methods Automated Assembly Assembly can represent one of the highest direct labor costs in manufacturing. These costs can be significantly reduced through automation. To realize these savings, the parts being assembled must be designed to avoid shingling or overlapping. Parts fed into an automated assembly machine can be pre- oriented in stacks, reels, magazines, or trays. The process of presenting parts and then removing completed assemblies can be done robotically. The three major automated assembly machine configurations include: • Dial, or rotary, index machine • In-line indexing assembly machine • Carousel assembly machine Dial, or rotary, index machines have work stations and tooling mounted around the periphery of the indexing table or on a central column. This type of machine is usually limited to smaller size work of minimum complexity. In-line indexing assembly machine move the components to be assembled in an oval, square, or rectangular path around the periphery of the machine. The circumferential machine type is the most common in-line indexing assembly machine. The carousel machine consists of a series of fixtures attached to a chain or belt which moves the components from one work station to another along a horizontal plane. The selection of any automated process machine is dependent upon many factors, including: • Production rate requirements • Size and weight of parts to be assembled • Number of automated operations involved • The need for additional manual operations • Complexity of assembly operations to be performed Fastening & Assembly Fundamental Manufacturing Processes Study Guide, DV03PUB8 - 4 - Review Questions 1. Integral fasteners are: a. inserted during assembly b. designed into sheetmetal products c. high in cost d. always installed manually 2. In hemming, the edge of a sheetmetal component is bent: a. 100 degrees b. less than 45 degrees c. exactly 45 degrees d. more than 180 degrees 3. Threaded fasteners are: a. a low-cost means of assembly b. used when disassembly is required c. installed by hand or by automated machinery d. all of the above 4. To facilitate automated insertion, screws: a. are pre-lubricated b. are made slightly undersized c. are produced with special shaped ends d. are always inserted vertically 5. Pins used to align precise assemblies are called: a. dowel pins b. clevis pins c. cotter pins d. locking pins 6. Adhesive bonding: a. is never performed automatically b. may allow for disassembly c. uniformly distributes stresses over a large surface d. is a high-cost assembly option 7. A dial index machine is also called a: a. rotary index machine b. circumferential index machine c. carousel index machine d. in-line indexing assembly machine 8. An in-line indexing assembly machine has the work: a. passing through it b. aligned in work trays c. on a moving belt or chain d. moving around its periphery Fastening & Assembly Fundamental Manufacturing Processes Study Guide, DV03PUB8 - 5 - Answer Key 1. b 2. d 3. d 4. c 5. a 6. c 7. a 8. d uploads/Industriel/ study-guide 72 .pdf
Documents similaires
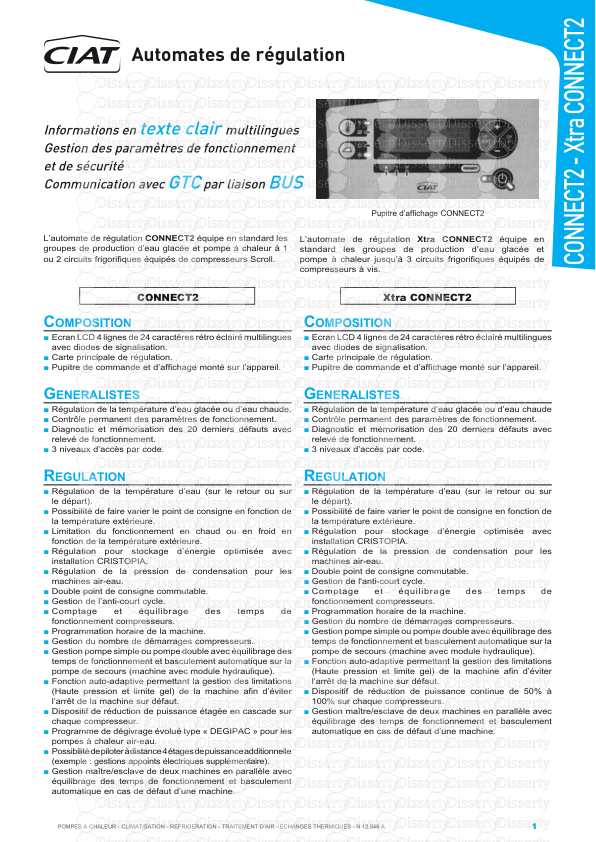
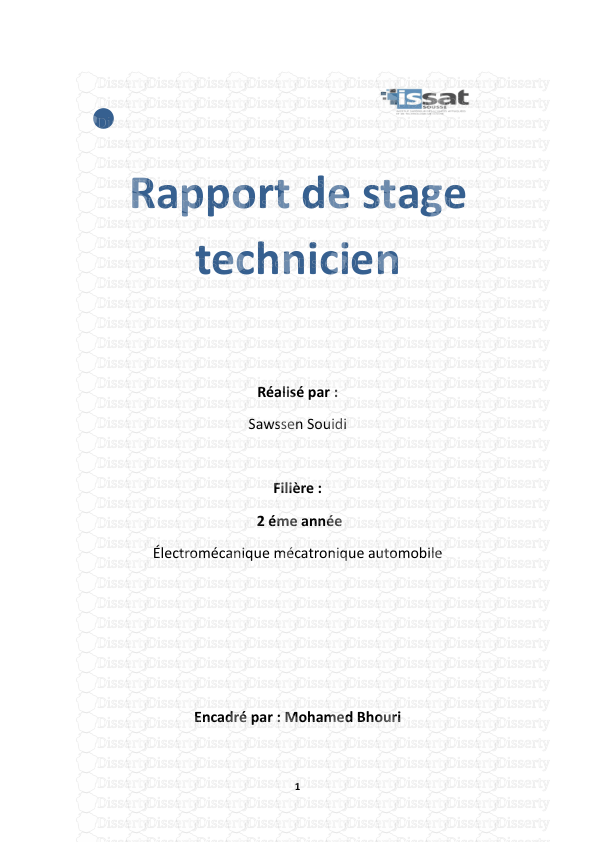
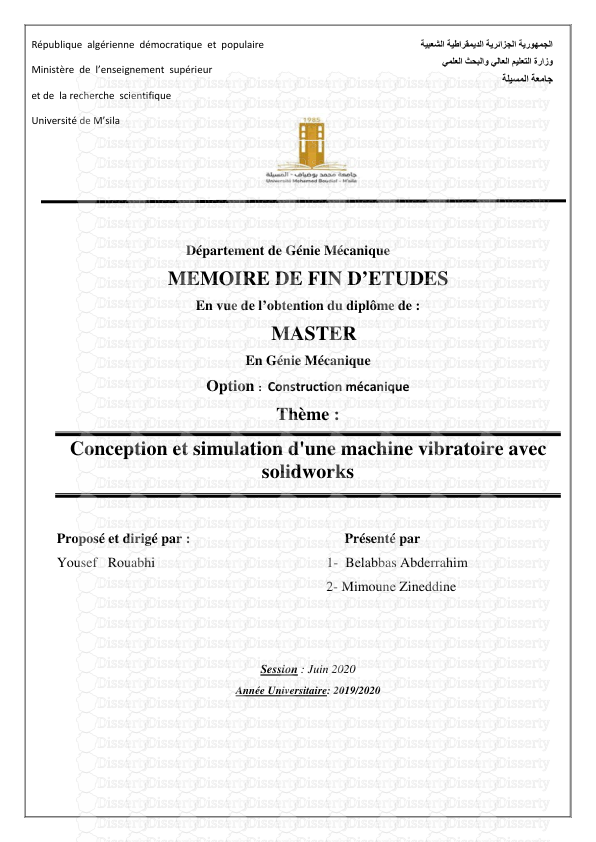
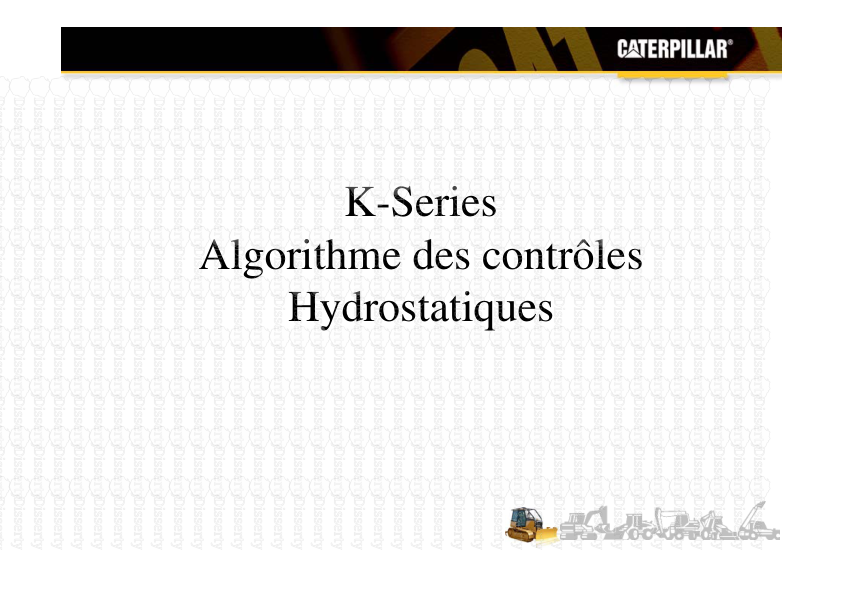
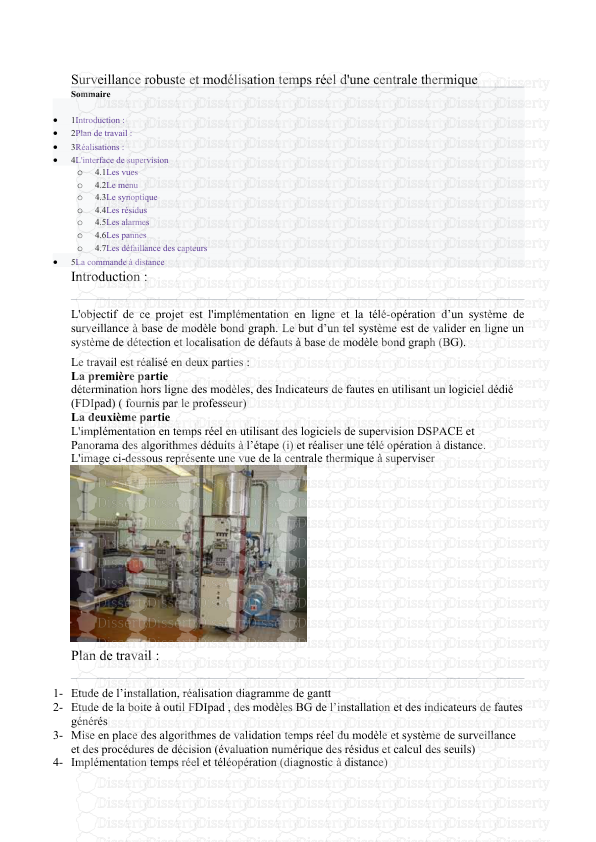
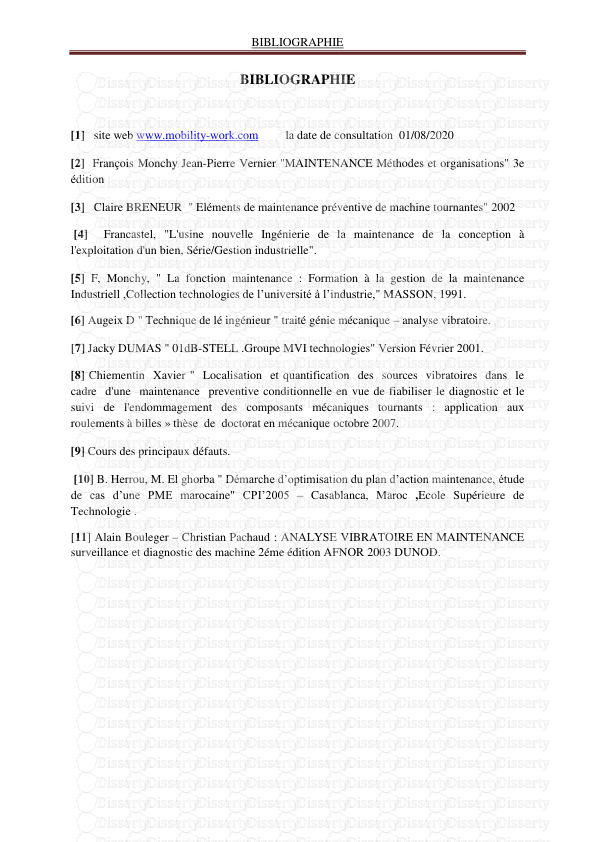
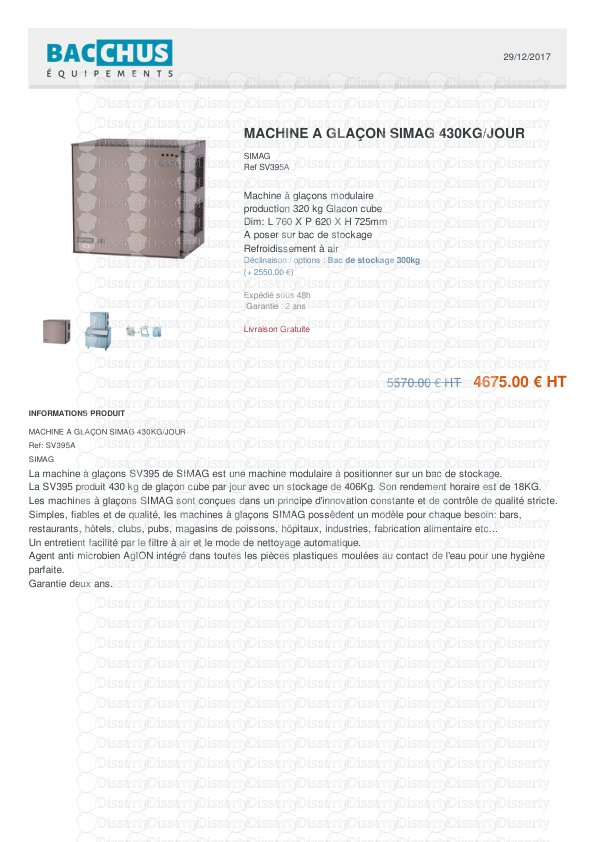
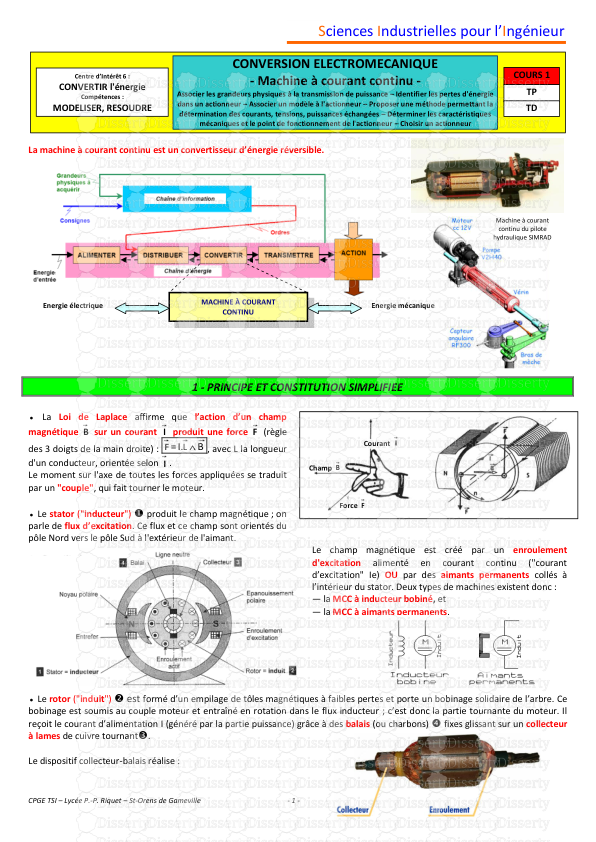
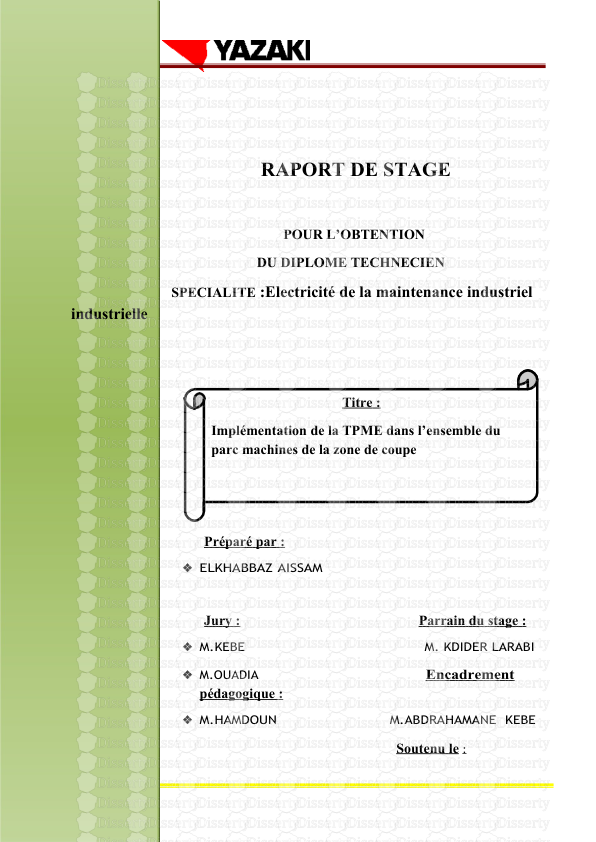
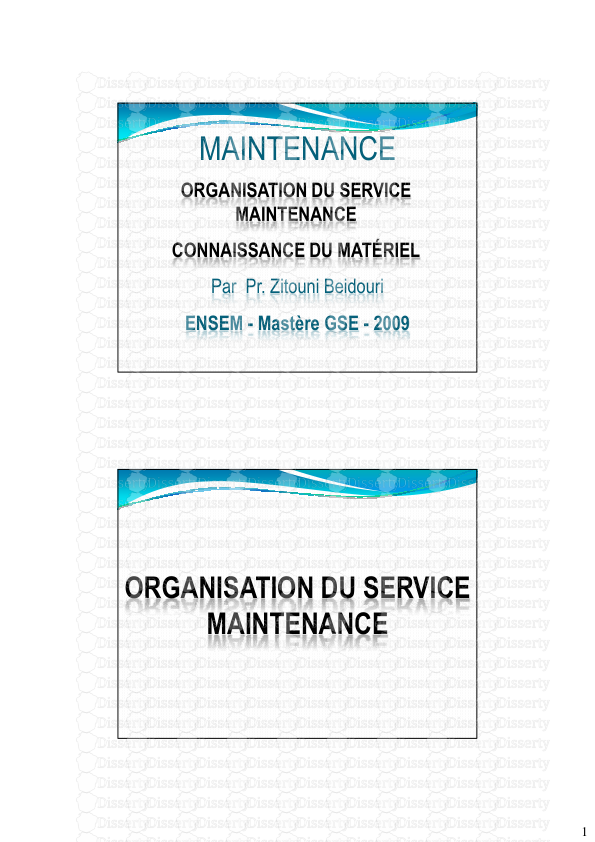
-
48
-
0
-
0
Licence et utilisation
Gratuit pour un usage personnel Attribution requise- Détails
- Publié le Jan 24, 2021
- Catégorie Industry / Industr...
- Langue French
- Taille du fichier 0.0931MB