Les réfractaires : Le cœur chaud des industries lourdes Chaouki SADIK Universit
Les réfractaires : Le cœur chaud des industries lourdes Chaouki SADIK Université Hassan II, Faculté des Sciences et Technique – Mohammedia, Département de Chimie. Maroc. Université Mohammed V Agdal, Institut Scientifique, Département des Sciences de la Terre, Equipe de Géo-matériaux et Géo-environnement. Maroc. Email : schawki37@gmail.com Résumé Les réfractaires constituent une famille très étendue de céramiques techniques. Leurs fonction principale est de faciliter la production d'autres matériaux, tels que les métaux, les verres, les produits pétrochimiques ou encore les ciments. Ils sont utilisés pour leur propriété de résistance à haute température depuis l'âge de bronze. Sans réfractaires, la plupart des développements scientifiques et technologiques des 100 dernières années n'auraient pas eu lieu. L'industrie réfractaire, par nécessité, a été développée en réponse aux demandes des industries, en particulier à celles du secteur sidérurgique qui utilise actuellement plus de 60% des réfractaires commercialisés. Les réfractaires non façonnés ont eu, durant la dernière décennie, une forte croissance au sein des produits réfractaires. Apprécier l’aptitude d’un produit réfractaire dans un contexte industriel nécessite une approche technique pluridisciplinaire faisant appel à des connaissances de base en génie des matériaux et des procédés, en thermique, en thermomécanique et en physico-chimie des hautes températures. Mots clés : Réfractaire, Température, Corrosion, Alumine-Silice Contenu Introduction Définition et classification Sollicitation des réfractaires Méthode de fabrication Les applications industrielles des réfractaires Corrosion des réfractaires Paramètres dévaluation des réfractaires 1. Introduction Les produits réfractaires sont des céramiques capables de résister à des températures supérieures à 1500 °C. De nombreux produits réfractaires se présentant sous des formes et des aspects extrêmement variés s'utilisent dans un grand nombre d'applications industrielles dans l'industrie de l'acier, du fer, du ciment, de la chaux, du verre, de la céramique, de l'aluminium, du cuivre et de la pétrochimie, dans les incinérateurs, les générateurs et les systèmes de chauffage domestique, notamment les blocs de chauffage à accumulation nocturne. Ils sont indispensables aux procédés à haute température et résistent à tous types de contraintes (mécaniques, thermiques, chimiques) tels que l'érosion, la déformation par fluage, la corrosion et les chocs thermiques. La résistance des éléments réfractaires aux températures élevées est définie de telle sorte que leur point de ramollissement ne soit pas inférieur à 1500 °C. On emploie généralement une classification qui distingue les « produits réfractaires », dont le point de ramollissement est entre 1500 et 1800 °C, des « produits hautement réfractaires », dont le point de ramollissement est supérieur à 1800 °C. Initialement fondée sur l'utilisation d'argiles d'une plus grande pureté comme matières premières, la fabrication des réfractaires repose aujourd'hui sur l'emploi de matières premières extrêmement diverses et qui peuvent être naturelles ou synthétiques. La demande en produits réfractaires est étroitement liée aux niveaux de production et d'investissement des pays consommateurs. Ainsi, la quantité de produits réfractaires consommée par tonne de produits manufacturés tels que l'acier ou le ciment a considérablement diminué ces dix dernières années en raison des innovations techniques et des procédés. La durée de vie plus longue des revêtements des fours de fabrication de l'acier ou des poches de coulée, ainsi que des délais de réparation ou d'entretien plus courts ont permis d'améliorer de façon notoire la productivité des industries qui en font usage. L'amélioration continue des produits réfractaires permet - grâce à une meilleure isolation et à une durée de vie plus longue du revêtement - une diminution de la consommation énergétique spécifique par les opérations des industries consommatrices. Les fonctions principales des réfractaires sont donc les suivantes : Assurer la protection physique du personnel et des installations entre la matière chaude (le produit traité) et la carcasse extérieure de l’outil de traitement. Notons que la matière chaude peut se trouver sous toutes les formes habituelles : liquide, solide et gazeuse. Réduire les pertes thermiques. Sans ces matériaux de grande diffusion, notre vie quotidienne serait sans aucun doute beaucoup moins agréable. En effet, nous ne disposerions pas d’acier, de fonte, d’alliages métalliques, de verre, de céramiques, de ciment ou de cracking de pétrole… etc, à un prix raisonnable. 2. Définition et classification 2.1 Définitions D’après la norme AFNOR NF B 40-001, les réfractaires sont des matériaux autres que les matériaux métalliques et leurs alliages, sans que soient exclus ceux contenant un constituant métallique. Dont la résistance pyroscopique est équivalente à 1500°C au minimum. Cette caractéristique correspond à la température à laquelle un échantillon de produit, soumis à une élévation graduelle de température, s’effondre sous son propre poids. Dans leur grande majorité, ces réfractaires sont constitués d’un mélange de composants cristallisés et vitreux. Les matériaux réfractaires font partie de la grande famille des céramiques, cette dernière englobe non seulement les réfractaires, mais aussi la terre cuite, la porcelaine, la faïence, les verres, les réfractaires spéciaux, les composés magnétiques. Cependant, de part de leurs résistances à d’autres conditions et leurs propriétés mécaniques et chimiques, la famille des réfractaires est principalement constituée d’oxydes, de mélanges d’oxydes pouvant être associés à des carbures ou nitrures par exemple. Dans le domaine des hautes températures, certains alliages métalliques réfractaires peuvent être employés, mais leurs usages restent limités en dessous de 1200°C. Au-delà, seuls les matériaux réfractaires résistent thermiquement et mécaniquement. 2.2 Composition chimique et macroscopique A l’exception des réfractaires électro-fondus, qui sont fabriqués par la fusion des matières premières, les produits réfractaires sont des céramiques fortement hétérogènes, toujours polyphasées, comportant un squelette plus ou moins grossier (les agrégats pouvant atteindre des tailles de quelques millimètres) lié par une matrice de granulométrie fine (schématiquement constituée d’une liaison et d’additifs). S’ajoute à ces différents constituants une phase supplémentaire constituée par la porosité importante (ouverte et fermée) de la céramique qui contribue largement à fixer les propriétés du matériau. Figure 1. Schéma de la microstructure d’un réfractaire En général, les produits réfractaires sont préparés à partir d’un mélange de matières premières de granulométrie définie formé : - d’agrégats (minéraux naturels ou synthétiques) qui constituent le support réfractaire proprement dit : ils conditionnent les caractéristiques principales du réfractaire fini et constituent la répartition granulométrique la plus grossière du produit ; Agrégats naturels Agrégats synthétiques Système silice alumine Bauxite, andalousite, argiles, pyrophyllites, silice vitreuse Alumine fritté, mullite fritté et électro-fondue Système basique Olivine, chromite Magnésie électro-fondue, dolomie frittée Autres (spéciaux) Graphite, sable de zircon Carbure de silicium, zircone dense Tableau 1. Listes de quelques types d’agrégats - d’un liant approprié assurant la cohésion de l’ensemble des constituants des produits réfractaires. Une partie des matières ajoutées comme liant n’a pas toujours un caractère réfractaire : en général, celles-ci sont additionnées en faible quantité et appartiennent toujours à la fraction fine de la granulométrie des produits finis. Le tableau ci-dessous présent les quatre systèmes de liaison existant ; Nature de liaison Céramique Chimique inorganique Chimique organique Hydraulique Liant Argile – oxydes pulvérulents – mullite – Si3N4 – SiAlON - AlN Silicate de sodium – gel de silice – phosphate de sodium – sels de magnésie Goudron – Brai – Dérivés de cellulose Ciment alumineux Tableau 2. Exemples de liants utilisés dans les réfractaires - d’additifs destinés à renforcer les caractéristiques de la matrice du réfractaire. Ils sont ajoutés sous formes de particules ou de poudres de synthèse, fine et ultra fines, et ayant les caractéristiques suivantes : grande pureté, distribution granulométrique étroite, surface spécifique adaptée, grande réactivité chimique… Tableau 3. Quelques exemples d’additifs et leurs propriétés associées Dans tous les cas, ces phases doivent être considérées individuellement quand l’on se trouve en face de problèmes d’altération concernant le matériau réfractaire. En effet, que cela soit la phase liante, les agrégats ou encore la porosité, elles interviennent toutes dans les phénomènes de corrosion par les liquides ou les gaz, de résistance mécanique (fluage, affaissement sous charge, flexion ou compression à chaud….), de résistance aux chocs thermiques, résistance à l’abrasion ainsi que dans les phénomènes de conductivité ou d’isolation thermique. 2.3 Les différentes variétés des matériaux réfractaires Les composants des produits réfractaires industriels, obtenus à partir de matières premières naturelles, et capables de travailler dans les atmosphères de fours, font généralement partie de la famille des oxydes. Il faut y ajouter les substances d’autres familles (carbures, carbone, nitrure), utilisées telles quelles en termes de phase principale ou secondaire ou sous forme d’ajouts de faibles quantités. Les réfractaires généralement multiphasés, ont une fusion incongruente. 2.3.1 Classification selon leur composition Les matériaux réfractaires peuvent être, selon leur composition chimique, classés en six grandes familles : A. Le système silice/alumine, qui va de la silice pure à l’alumine pure. Tableau 4 : Classification du groupe siliceux alumineux La cuisson à haute température des aluminosilicates conduit à la formation de la Mullite utilisé principalement dans l’industrie des réfractaires. Propriétés de Mullite : - Bonne résistance à la compression, à la flexion, et au fluage à haute température - Bonne résistance aux chocs thermiques - Bonne résistance à la corrosion (Ces résistances sont influencées par la présence de la phase vitreuse à haute température) - Faible conductivité et dilatation thermique - Faible ténacité B. Les systèmes des réfractaires basiques, sont à base de MgO, CaO, SiO2, Cr2O3. On distingue : - La uploads/Industriel/ synthese-refractaires 1 .pdf
Documents similaires
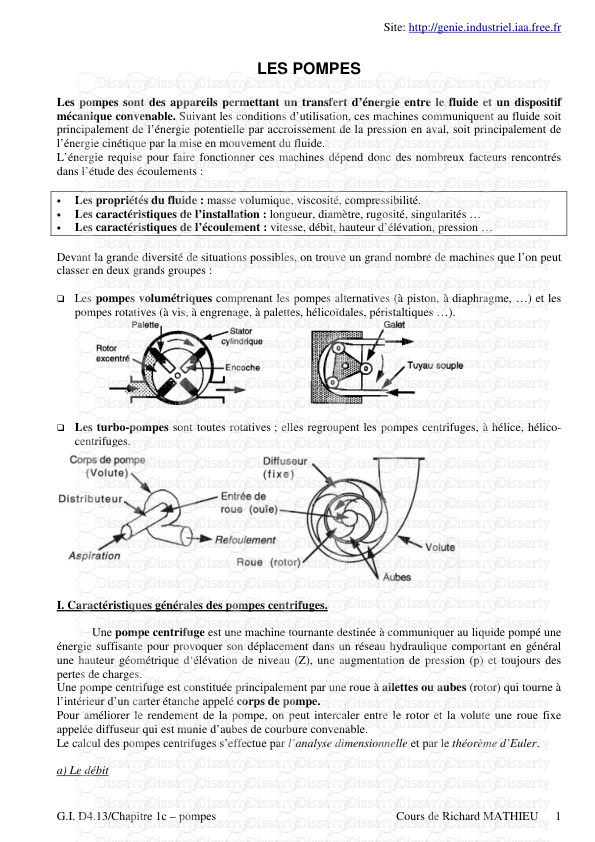
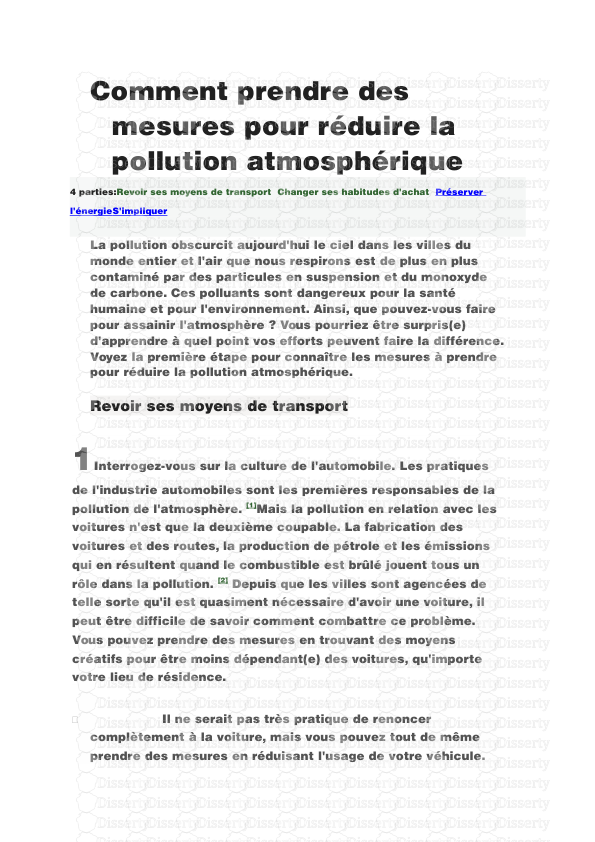
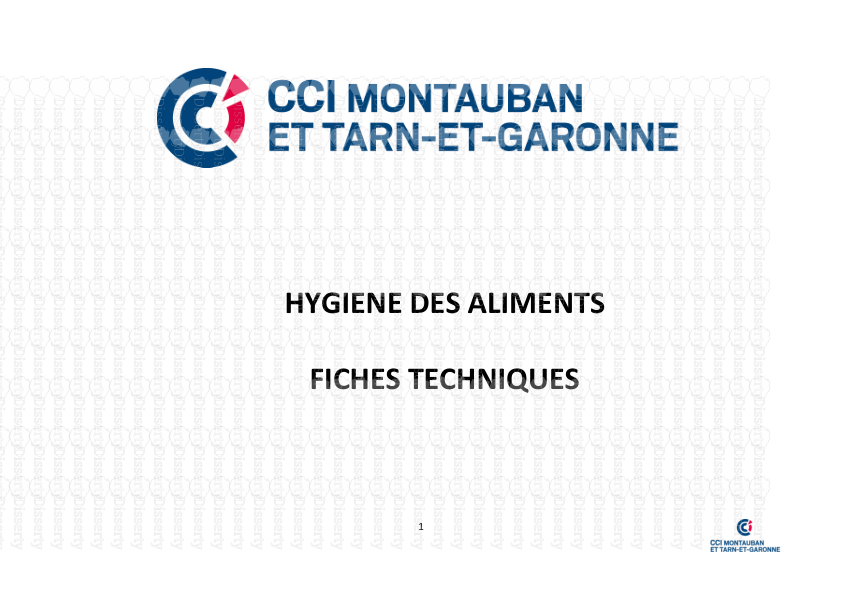
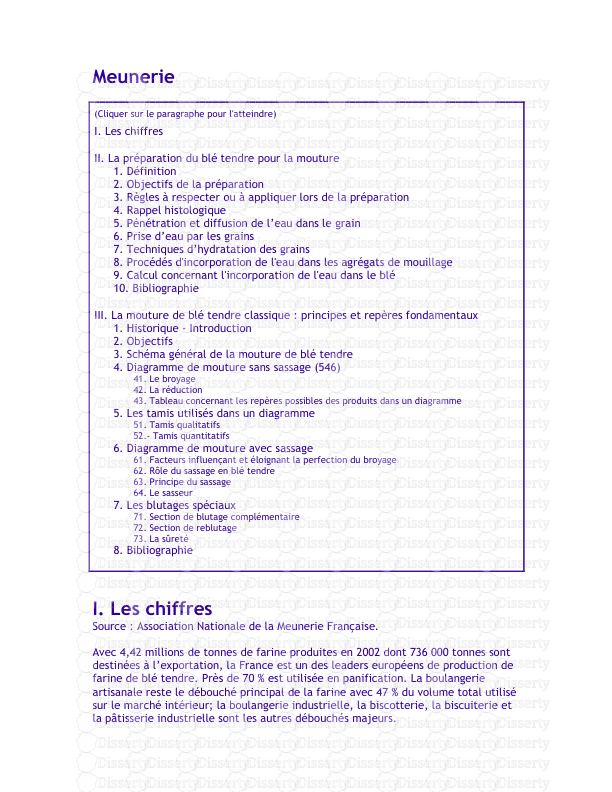
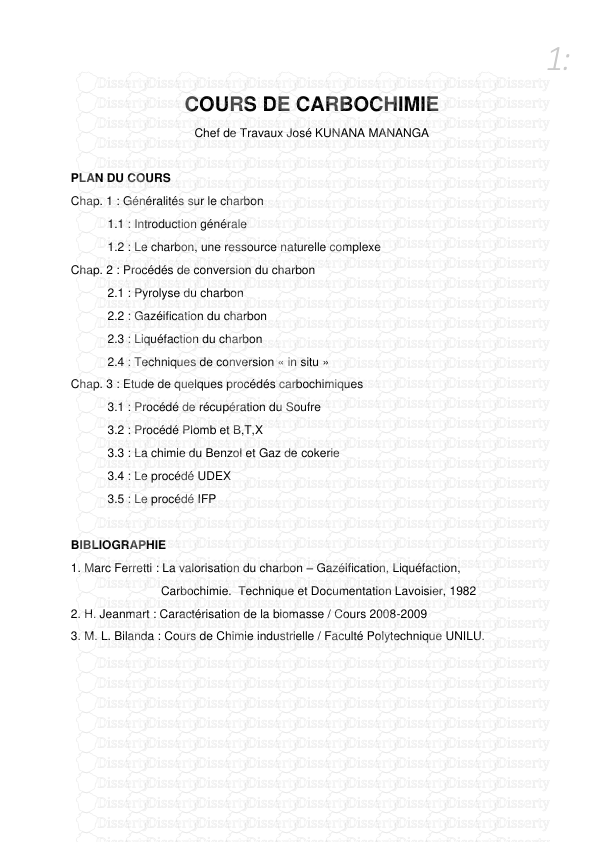
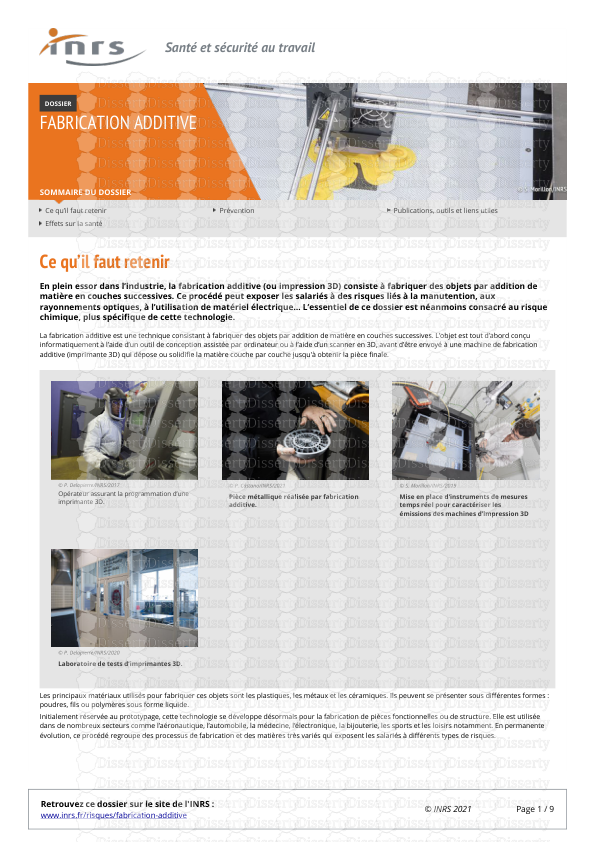
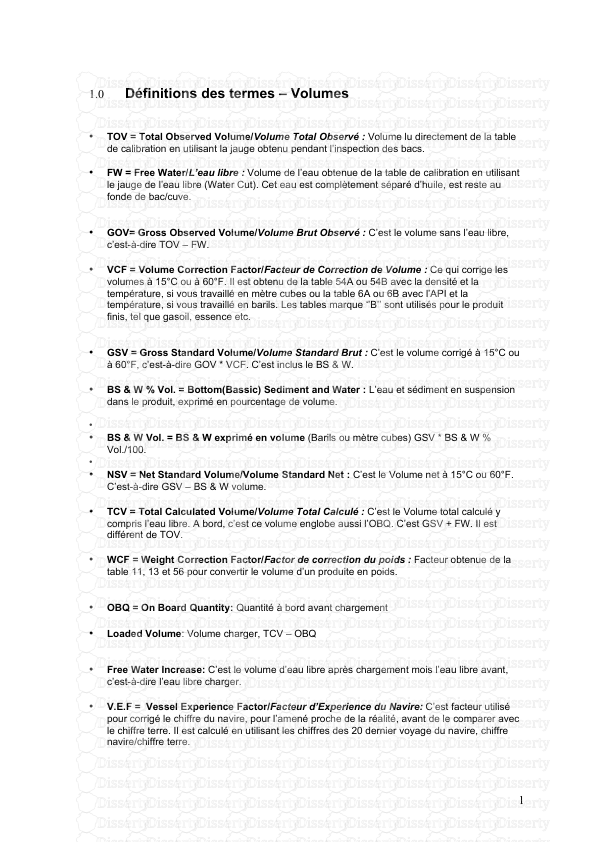

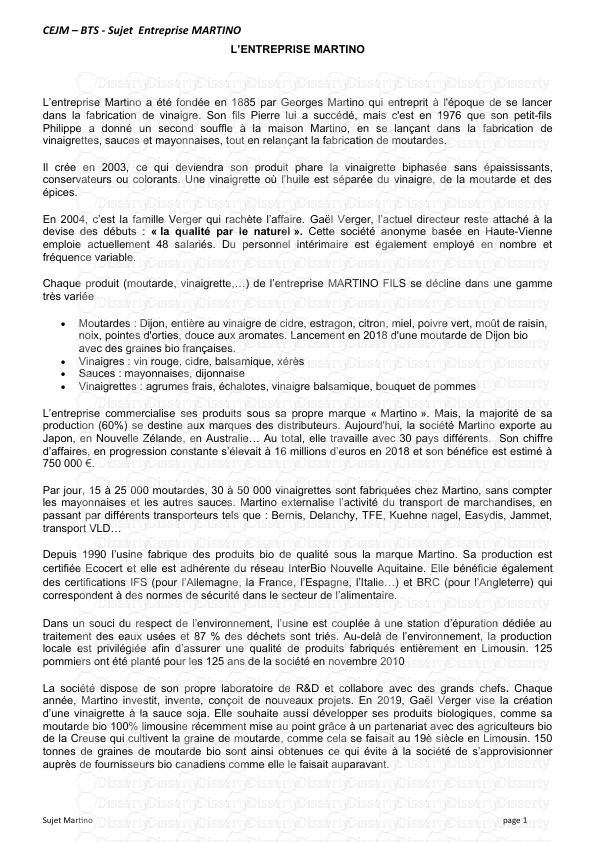
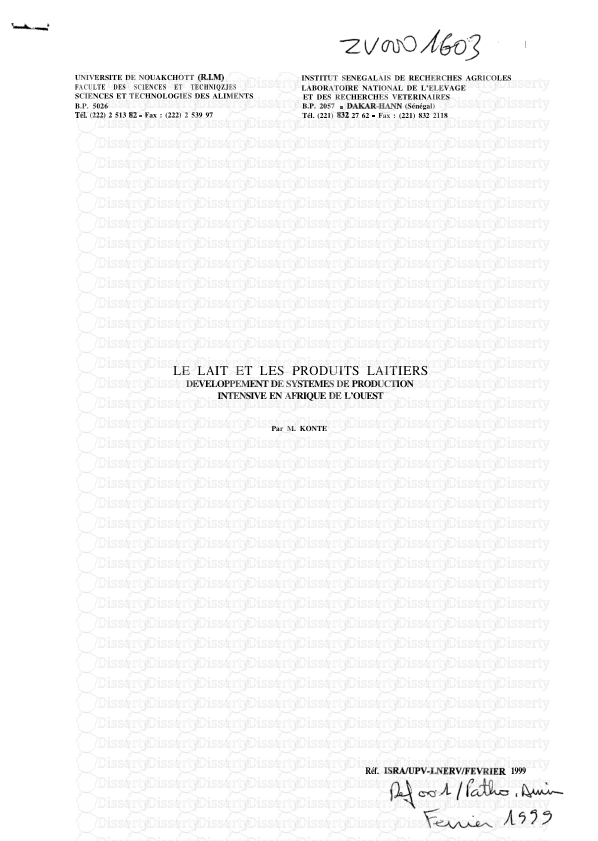
-
59
-
0
-
0
Licence et utilisation
Gratuit pour un usage personnel Attribution requise- Détails
- Publié le Oct 18, 2022
- Catégorie Industry / Industr...
- Langue French
- Taille du fichier 0.4779MB