Master Insulation Guide Specification For Mechanical System • AP Armaflex® Pipe
Master Insulation Guide Specification For Mechanical System • AP Armaflex® Pipe Insulation • AP Armaflex W Pipe Insulation • AP Armaflex SS Pipe Insulation • AP Armaflex Sheet and Roll Insulation • AP Armaflex SA Sheet and Roll Insulation • ArmaTuff Laminated Sheets and Rolls • UT Solaflex Pipe Insulation • UT Solaflex Roll Insulation • NH Armaflex Pipe Insulation • NH Armaflex Sheet and Roll Insulation • Armafix (IPH and NPH) Insulation Pipe Hangers Master Insulation Guide Specification © 2013 Armacell LLC 2 Master Insulation Guide Specification For Mechanical Systems Part 1 – General 1.01 Scope of Work: A. Provide piping, ductwork and equipment insulation as specified below. 1.02 Definitions: A. Cold Piping/Surfaces: Pipes or surfaces where the normal operating temperature is 60°F or lower. B. Third Party Supervision Testing: Verification testing by a nationally recognized independent testing organization that will conduct sampling of the product through to simulated end use testing. C. Thermal Conductivity: The amount of heat in Btu’s transferred in one hour through one square foot of homogeneous material one inch in thickness when there is a temperature difference of 1°F. D. Compression Fit Method: To allow for expansion and contraction of sheet and roll insulation, leave a 1/2” -wide uncoated border at the butt-edge seams on the surface to be insulated and the insulation surface. Overlap the insulation 1/4” at the butt-edge and compress the edges into place. Apply adhesive to the butt-edges of the insulation. 1.03 Quality Assurance: A. Material shall be delivered in unbroken, factory furnished packaging and stored in a clean, dry indoor space that provides protection against the weather. B. Insulation shall be applied by qualified personnel skilled in this trade. C. Progressive testing of the systems to be insulated shall have been completed, inspected and approved by the owners' representative before the insulation is applied. D. Insulation shall not be applied until all surfaces are clean; dry, and free of dirt, dust, grease, frost, moisture, and other extraneous elements. E. Work shall be performed at the temperatures recommended by the product manufacturer. Part 2 – Products 2.01 Elastomeric Insulation: 2.01.1 Acceptable Manufacturers – These specifications are based on products and data of Armacell and designate the type and quality of work intended under this section. Products of other manufacturers proposed as equivalent must be submitted for written approval by the specifying engineer ten days prior to the bid date. Supporting technical data, samples, published specifications and the like must be submitted for comparison. The contractor should warrant that proposed substitutions, if accepted, will provide performance equal to the materials specified herein. Master Insulation Guide Specification © 2013 Armacell LLC 3 A. Insulation material shall be a flexible, closed-cell elastomeric insulation in tubular or sheet form: AP Armaflex, AP Armaflex W, AP Armaflex SS, or AP Armaflex SA. These products meet the requirements as defined in ASTM C 534, “Specification for preformed elastomeric cellular thermal insulation in sheet and tubular form.” B. Insulation materials shall have a closed-cell structure to prevent moisture from wicking which makes it an efficient insulation. C. Insulation material shall be manufactured without the use of CFC’s, HFC’s or HCFC’s. It is also formaldehyde free, low VOC’s, fiber free, dust free and resists mold and mildew. D. The insulation material shall contain MICOBAN Antimicrobial additive to aid in the prevention of mold and mildew. E. Materials shall have a flame spread index of less than 25 and a smoke-developed index of less than 50 when tested in accordance with ASTM E 84, latest revision. In addition, the product, when tested, shall not melt or drip flaming particles, the flame shall not be progressive and all materials shall pass simulated end-use fire tests. F. Materials shall have a maximum thermal conductivity of 0.25 Btu-in./h-ft2- °F at a 75°F mean temperature when tested in accordance with ASTM C 177 or ASTM C 518, latest revisions. G. Materials shall have a maximum water vapor transmission of 0.05 perm-inches when tested in accordance with ASTM E 96, Procedure A, latest revision. H. The material shall be manufactured under an independent third party supervision testing program covering the properties of fire performance, thermal conductivity and water vapor transmission. 2.02 Special Elastomeric Insulations – High Temperature and Nonhalogen 2.02.1 Acceptable Manufacturers – These specifications are based on products and data of Armacell and designate the type and quality of work intended under this section. Products of other manufacturers proposed as equivalent must be submitted for written approval by the specifying engineer ten days prior to the bid date. Supporting technical data, samples, published specifications, and related documentation must be submitted for comparison. The contractor should warrant that proposed substitutions, if accepted, will provide performance equal to the materials specified herein. A. Insulation material shall be a flexible, closed-cell elastomeric insulation in tubular or sheet form: UT Solaflex or NH Armaflex. These products meet the requirements as defined in ASTM C 534, “Specification for preformed elastomeric cellular thermal insulation in sheet and tubular form.” B. Materials shall have a flame spread index of less than 30 and a smoke developed index of less than 200 when tested in accordance with ASTM E 84, latest revision, (UT Solaflex shall meet 25/50) In addition, the product, when tested, shall not melt or drip flaming particles, and the flame shall not be progressive. C. UT Solaflex shall have a maximum thermal conductivity of 0.28 Btu-in./h-ft2-°F at a 75°F mean temperature when tested in accordance with ASTM C 177 or ASTM C 518, latest revisions. NH Armaflex shall have a maximum thermal conductivity of 0.275 Btu-in./h-ft2-°F at a 75°F mean temperature when tested in accordance with ASTM C 177 or ASTM C 518, latest revisions. D. UT Solaflex and NH Armaflex shall have a maximum water vapor transmission of 0.05 perm- inches when tested in accordance with ASTM E 96, Procedure A, latest revision. Master Insulation Guide Specification © 2013 Armacell LLC 4 2.03 Adhesives and Finishes A. Adhesive shall be the insulation manufacturer's recommended contact adhesive: Armaflex 520, Armaflex 520 BLV, Armaflex 520 Black, Low VOC Spray Adhesive or Armaflex HT 625 Adhesive. B. Insulation finish shall be the insulation manufacturer's recommended finish: Armaflex WB Finish. C. Accessories such as adhesives, mastics and cements shall have the same properties as listed above and shall not detract from any of the system ratings as specified above. 2.04 Elastomeric Insulation Duct Liner 2.04.1 Acceptable Manufacturers – These specifications are based on products and data of Armacell and designate the type and quality of work intended under this section. Products of other manufacturers proposed as equivalent must be submitted for written approval by the specifying engineer ten days prior to the bid date. Supporting technical data, samples, published specifications and the like must be submitted for comparison. The contractor should warrant that proposed substitutions, if accepted, will provide performance equal to the materials specified herein. A. Insulation material shall be a flexible, closed-cell or conformable elastomeric insulation in sheet form: AP Armaflex, and AP Armaflex SA. These products meet the requirements as defined in ASTM C 534, “Specification for preformed elastomeric cellular thermal insulation in sheet and tubular form.” B. Insulation material shall be manufactured without the use of CFC’s, HFC’s or HCFC’s. It is also formaldehyde free, low VOC’s, fiber free, dust free and resists mold and mildew. C. The insulation material shall contain MICOBAN Antimicrobial additive to aid in the prevention of mold and mildew. D. Materials shall have a flame spread index of less than 25 and a smoke-developed index of less than 50 when tested in accordance with ASTM E 84, latest revision. In addition, the product, when tested, shall not melt or drip flaming particles, the flame shall not be progressive and all materials shall pass simulated end-use fire tests. E. Materials shall have a maximum thermal conductivity of 0.25 Btu-in./h-ft2- °F at a 75°F mean temperature when tested in accordance with ASTM C 177 or ASTM C 518, latest revisions. F. Materials shall have a maximum water vapor transmission of 0.05 perm-inches when tested in accordance with ASTM E 96, Procedure A, latest revision. (other than conformable elastomeric) G. The material shall be manufactured under an independent third party supervision testing program covering the properties of fire performance, thermal conductivity and water vapor transmission. Master Insulation Guide Specification © 2013 Armacell LLC 5 Part 3 – Installation 3.01 Piping: A. Install pipe insulation by slitting tubular sections and applying onto piping or tubing. Alternately, whenever possible, slide unslit sections over the open ends of piping or tubing. All seams and butt joints shall be adhered and sealed using Armaflex 520, 520 BLV or 520 Black Adhesive. When using AP Armaflex SS, only the butt joints shall be adhered using Armaflex 520, 520 BLV or 520 Black Adhesive. Armaflex HT 625 Adhesive shall be used with UT Solaflex. B. Insulation shall be pushed onto the pipe, never pulled. Stretching of insulation may result in open seams and joints. C. Tape the ends of the copper uploads/Management/ insulation-guide.pdf
Documents similaires
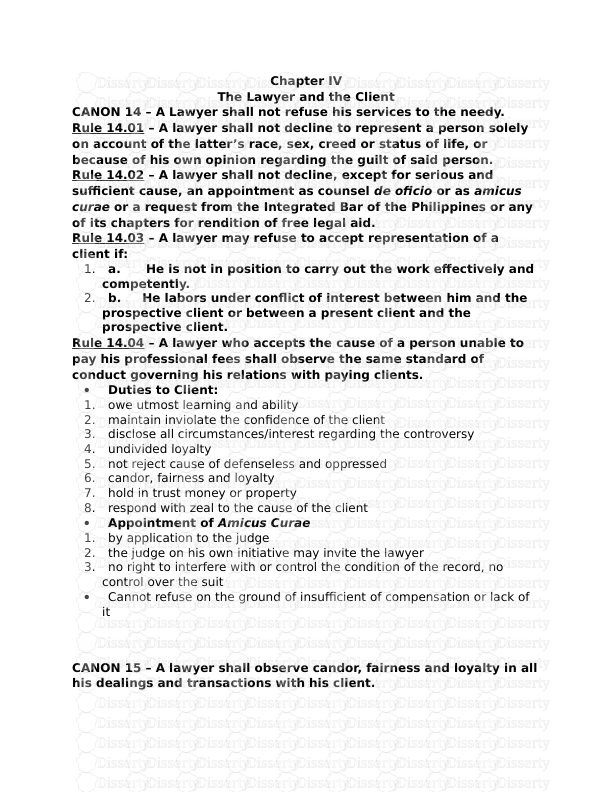
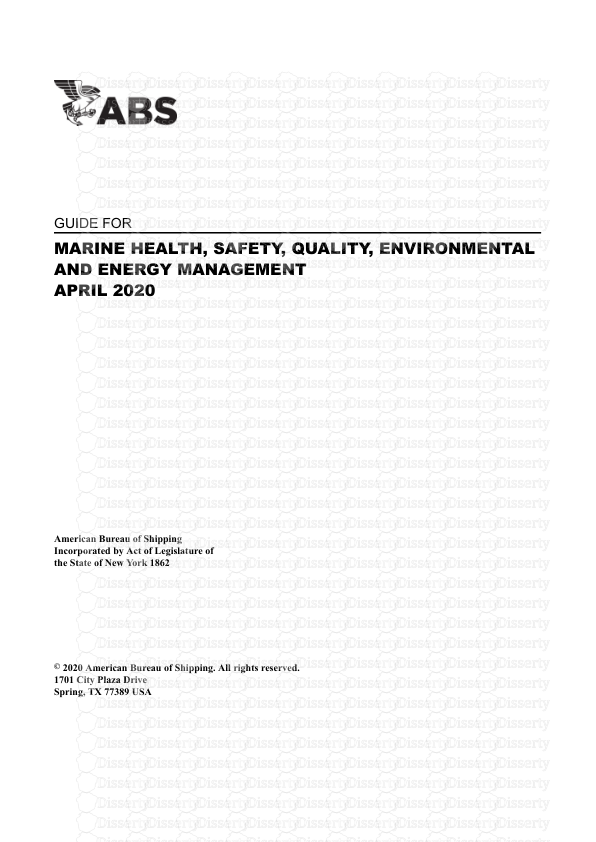
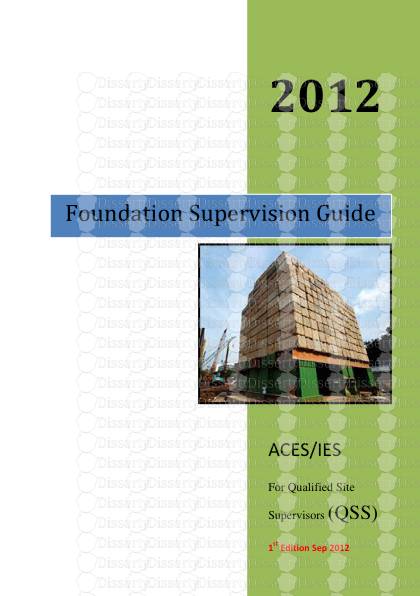
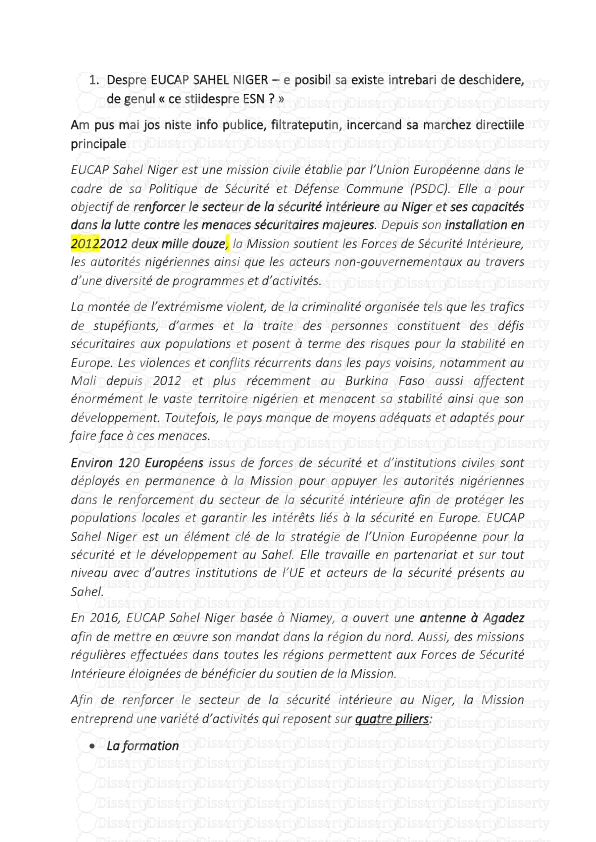

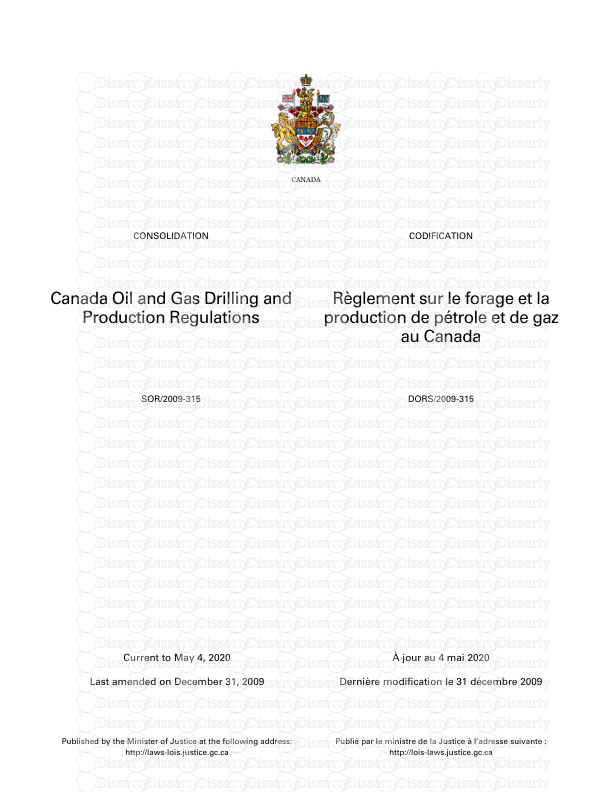
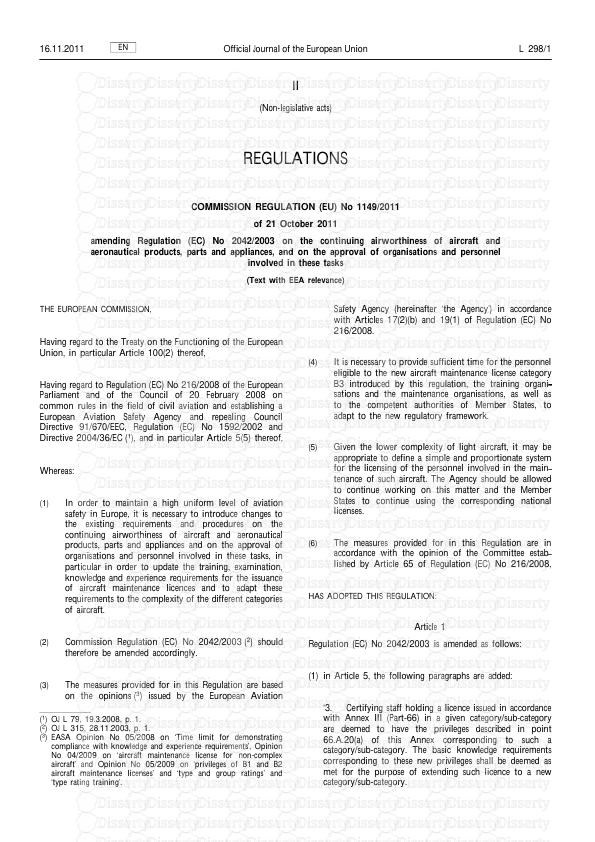
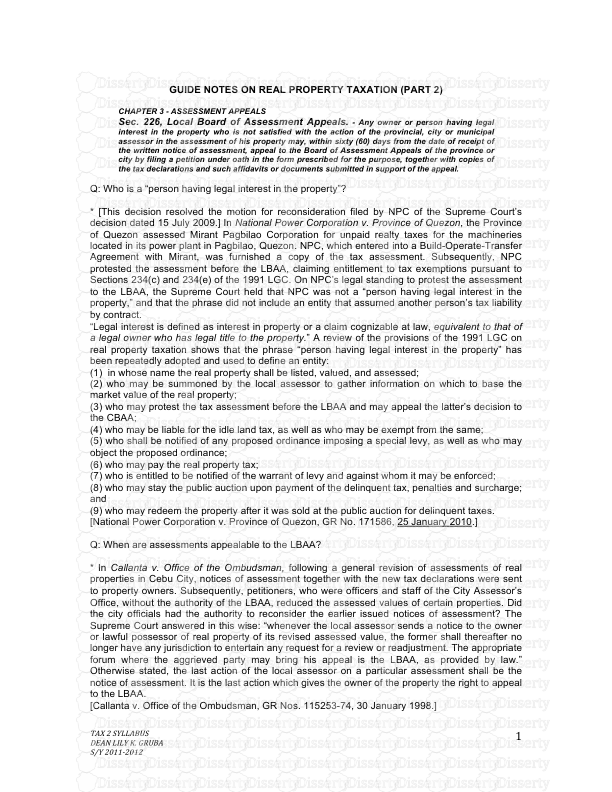
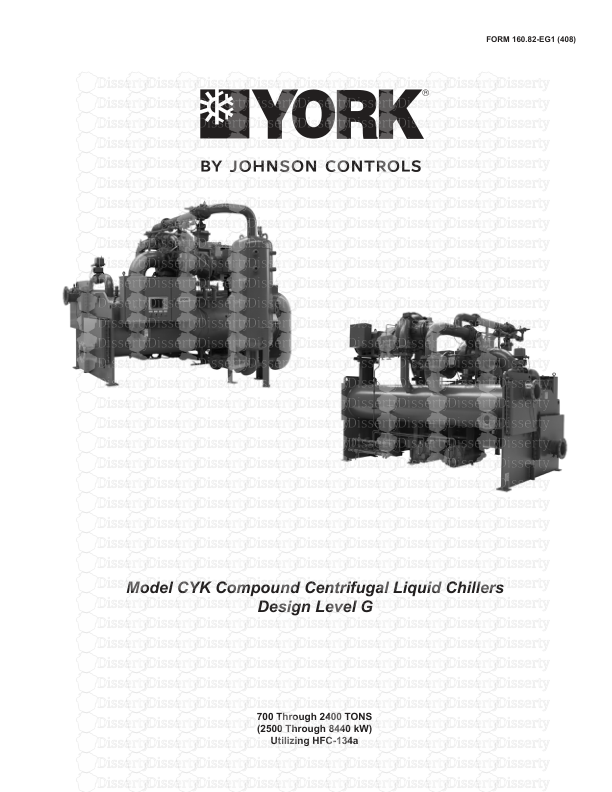
-
48
-
0
-
0
Licence et utilisation
Gratuit pour un usage personnel Attribution requise- Détails
- Publié le Dec 28, 2022
- Catégorie Management
- Langue French
- Taille du fichier 1.3602MB