SUGGESTIONS FOR PREHEATING STRUCTURAL STEEL Governing codes and standards: CSA
SUGGESTIONS FOR PREHEATING STRUCTURAL STEEL Governing codes and standards: CSA W59 AWS D1.1 Date of issue: 2018 Revision No.: 0 RC Technical Services rctechservices.ca 506 345-2221 Suggestions for Preheating RC Technical Services Page 2 of 10 TABLE OF CONTENTS 1 INTRODUCTION ............................................................................................................. 3 2 WHY SHOULD WE PREHEAT ....................................................................................... 4 3 WHEN SHOULD WE PREHEAT ..................................................................................... 4 4 HOW SHOULD WE PREHEAT ....................................................................................... 4 5 MEASURING PREHEAT ................................................................................................ 5 6 PREHEAT, MINIMUM INTERPASS AND MAXIMUM INTERPASS TEMPERATURE .... 5 7 WHERE TO MEASURING PREHEAT ............................................................................ 6 8 SUMMARY .................................................................................................................... 10 Suggestions for Preheating RC Technical Services Page 3 of 10 1 INTRODUCTION 1.1 This guide is not meant to replace the preheat information on CWB or AWS approved Welding Procedure Specifications (WPS) or Welding Procedure Data Sheet(s) (WPDS). Follow the preheat information on approved WPS or WPDS. 1.2 Use this guide at your own risk. 1.3 Follow the information in: a) CSA W59, latest revision. b) AWS D1.1, latest revision. c) AWS approved WPS d) CWB approved WPS and / or WPDS. e) Company policies and safe practices Suggestions for Preheating RC Technical Services Page 4 of 10 2 WHY SHOULD WE PREHEAT 2.1 Why should we preheat: a) It slows the cooling rate which offers more resistance to cracking. b) The slower cooling rate gives more time for hydrogen to escape, reducing the potential for cracking. c) Reduces shrinkage stresses, especially in highly restrained joints. d) It can help to ensure mechanical properties such as ductility and impact properties. 3 WHEN SHOULD WE PREHEAT 3.1 When should preheat be used: a) When working to welding codes, the minimum preheats must be followed. b) In some cases higher preheat temperatures may be needed with highly restrained joints or for welding repairs. c) Thick base metal. d) Base metal chemistry. e) Low ambient temperature. f) Weld metal hydrogen content. g) Low heat inputs. 4 HOW SHOULD WE PREHEAT 4.1 Choosing the right method for your job, whether it be torch heating, induction, or electrical resistance, could make the difference between a successful weld or a costly error. a) Flame or torch preheating equipment is cheap and is widely used for structural steel. Be careful of the flame distance so not to overheat the material in spots. When preheating with a torch, water will form several inches in all directions from the flame, this is a chemical reaction from the gas. Water does not come out of steel. b) Electrical resistance offers more control of the preheat temperature. Can be set up and turned on before the shifts starts and be ready for the welders for the start of a shift. Equipment is costly, thermocouples wires need to be welded on, and some weldments can be time consuming to cover. c) Induction heating is the most costly, but seams the easiest to use. It heats the steel quicker. Water cooled blankets are recommended. The setup is very quick. Suggestions for Preheating RC Technical Services Page 5 of 10 5 MEASURING PREHEAT 5.1 Preheat can be measured in several ways: a) Infrared thermometers are cheap and must be calibrated. The surface condition of the material will have an effect on the reading. Shiny, rusty or painted surfaces will give different readings. Read your instructions to determine the best method to get an accurate temperature reading. If they get dropped or are handled roughly they may need to be recalibrated. b) Contact thermometers must be calibrated and are more accurate than the infrared type. If they get dropped or are handled roughly, they may need to be recalibrated. c) Temperature-indicating crayons such as Tempilstik, in my opinion are the most accurate. They are very cheap and come with documentation of calibration of +/- 1 degree. No need for calibration. This is the only method I use. 6 PREHEAT, MINIMUM INTERPASS AND MAXIMUM INTERPASS TEMPERATURE 6.1 Preheat: Preheat means the minimum preheat temperature before welding. This temperature shall be maintained while welding. The preheat should be uniform thought out and around the joint. Non-uniform heating can cause higher residual stresses and or undesirable metallurgical changes. The heat source should be placed on one side and measure the minimum preheat temperature on the opposite side. Sometimes its imposible to get at the back side. When heating and checking the minimum preheat temperature on the same side, a rule of thumb is to remove the torch, wait 1 minute for every 1" (25 mm) of base metal thickness before checking the temperature. Try a test piece in your shop, preheat from one side only, remove torch, wait a minimum of 1 minute, then check the opposite side to see if the minimum preheat temperature has reached the back side. Equiptment varies from shop to shop, adjust time to thickness as needed in your shop. 6.2 Minimum interpass temperature: To me the minimum interpass temperature is the same as the minimum preheat temperature. Some will refer to this as the temperature below the maximum interpass temperature when welding resumes again. This temperature would be above the minimum preheat temperature. 6.3 Maximum interpass temperature: Is needed on multipass welds and is the maximum temperature allowed for a grade of material. This temperature should be checked just before putting the next bead of weld. The temperature should be check at the next bead location or beside the joint preparation. If the temperature is above the maximum interpass temperature, you must wait until the temperature drops. Suggestions for Preheating RC Technical Services Page 6 of 10 7 WHERE TO MEASURING PREHEAT 7.1 AWS D1.1 – 2015: States preheat and all subsequent minimum interpass temperatures shall be maintained during the welding operation for a distance at least equal to the thickness of the part (but not less than 3 in. [75 mm]) in all directions from the point of welding. 7.2 CSA W59 – 2013: States the material to be welded shall be at or above the minimum specified temperature for a distance at least equal to the thickness of the part being welded, but not less than 75 mm (3”), both laterally and in advance of the welding. 7.3 Fillet weld: Apply the preheat on the back side and under the joint. Check the minimum preheat temperature on the opposite sides. Sometimes its imposible to get at the back side. If applying preheat and checking the minimum preheat temperature on the same side, remove the torch, wait 1 minute for each 1” (25 mm) of metal thickness before checking the temperature. D equals the minimum distance required by code for the minimum preheat temperature. TD = total distance. Seel clause 6.1. P o in t o f w e ld in g T T D D D T D Suggestions for Preheating RC Technical Services Page 7 of 10 7.4 Partial penetration T joint: Apply the preheat on the back side and under the joint. Check the minimum preheat temperature on the opposite sides. Sometimes its imposible to get at the back side. If applying preheat and checking the minimum preheat temperature on the same side, remove the torch, wait 1 minute for each 1” (25 mm) of metal thickness before checking the temperature. D equals the minimum distance required by code for the minimum preheat temperature. TD = total distance. See clause 6.1. 7.5 Complete penetration T joint: Apply the preheat on the back side and under the joint. Check the minimum preheat temperature on the opposite sides. Sometimes its imposible to get at the back side. If applying preheat and checking the minimum preheat temperature on the same side, remove the torch, wait 1 minute for each 1” (25 mm) of metal thickness before checking the temperature. D equals the minimum distance required by code for the minimum preheat temperature. TD = total distance. See clause 6.1. Point of welding T T D D D TD TD Point of welding T T D D D TD TD Suggestions for Preheating RC Technical Services Page 8 of 10 7.6 Partial penetration butt joint: Apply preheat on side B and check the minimum preheat temperature on side A. Sometimes its imposible to get at the back side. If applying preheat and checking the minimum preheat temperature on the same side, remove the torch, wait 1 minute for each 1” (25 mm) of metal thickness before checking the temperature. D equals the minimum distance required by code for the minimum preheat temperature. TD = total distance. See clause 6.1. 7.7 Complete penetration butt joint: Side A to be welded first, apply preheat on side B, check minimum preheat temperature on side A. If you cannot get to side B, apply the minimum preheat to side A and after taking away the torch wait 1 minute for each 1” (25 mm) of metal thickness before checking the temperature. D equals the minimum distance required by code for the minimum preheat temperature. TD = total distance. See clause 6.1. T D D Side A Side B TD T D D Side B Side A uploads/Management/ preheat-guide.pdf
Documents similaires
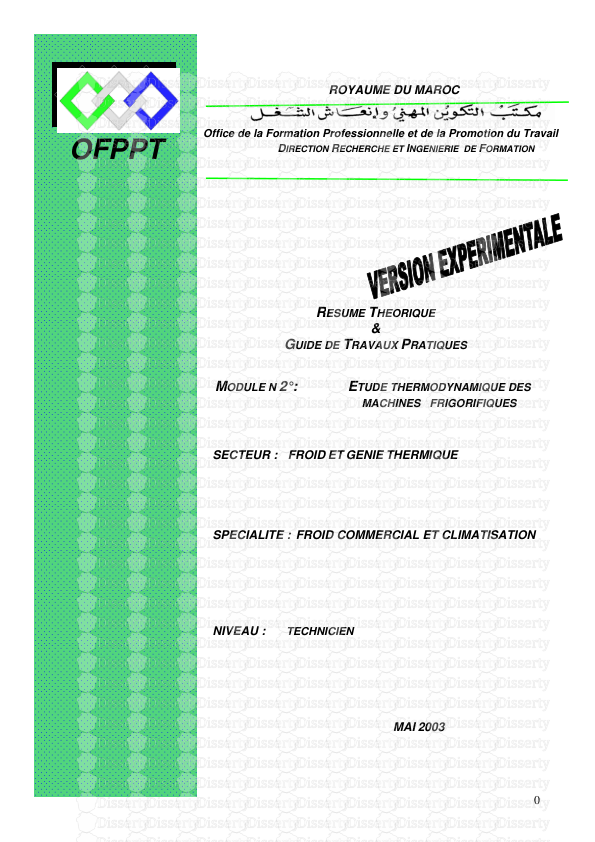
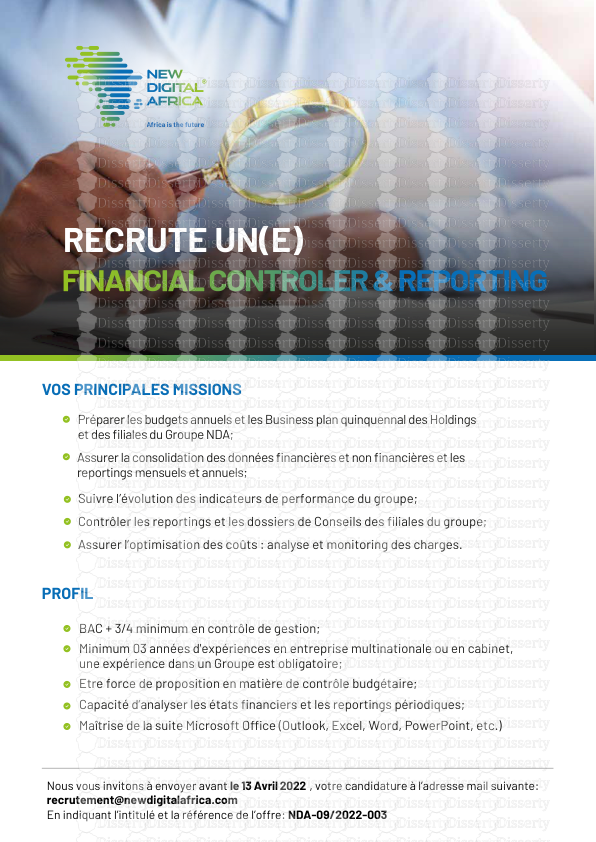
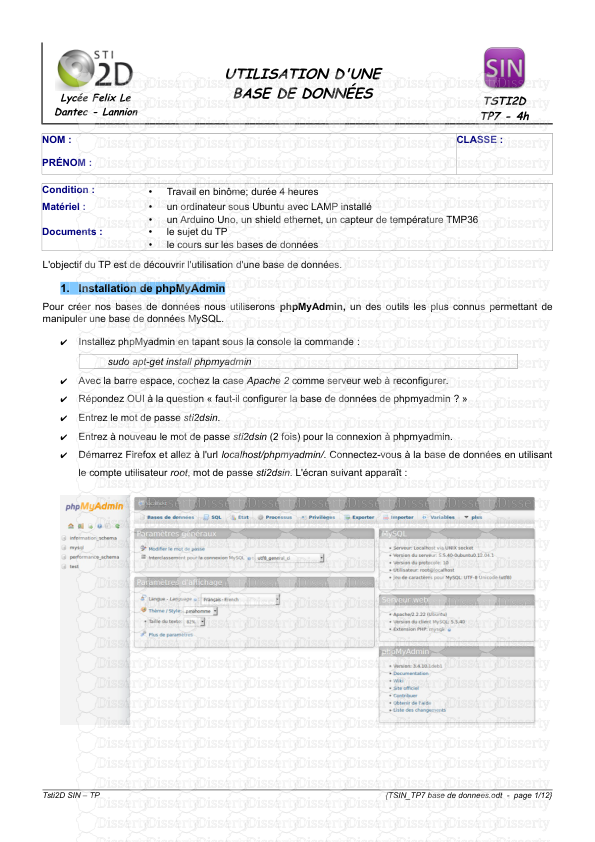
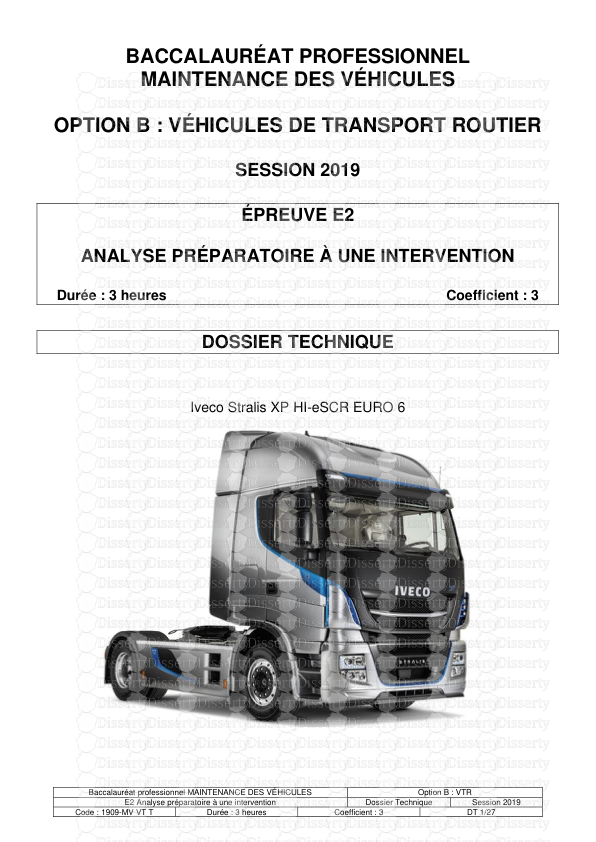
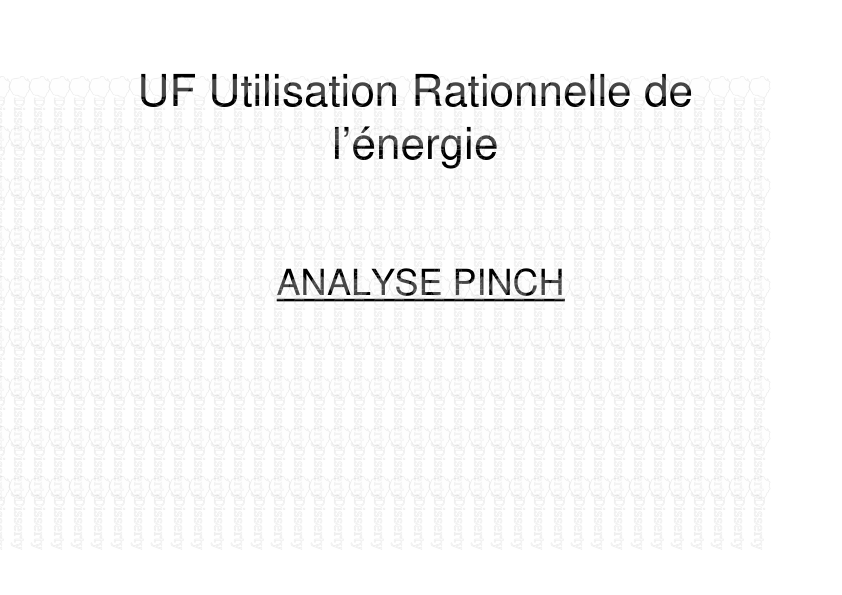
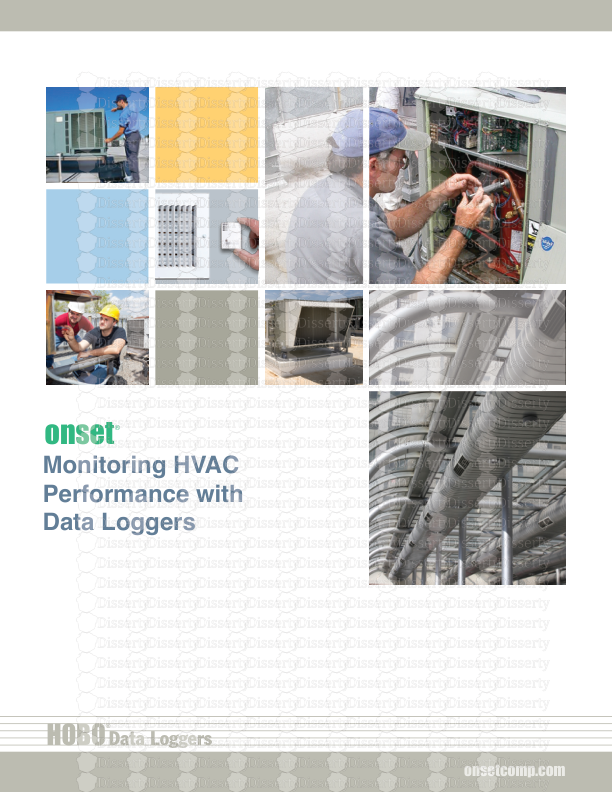
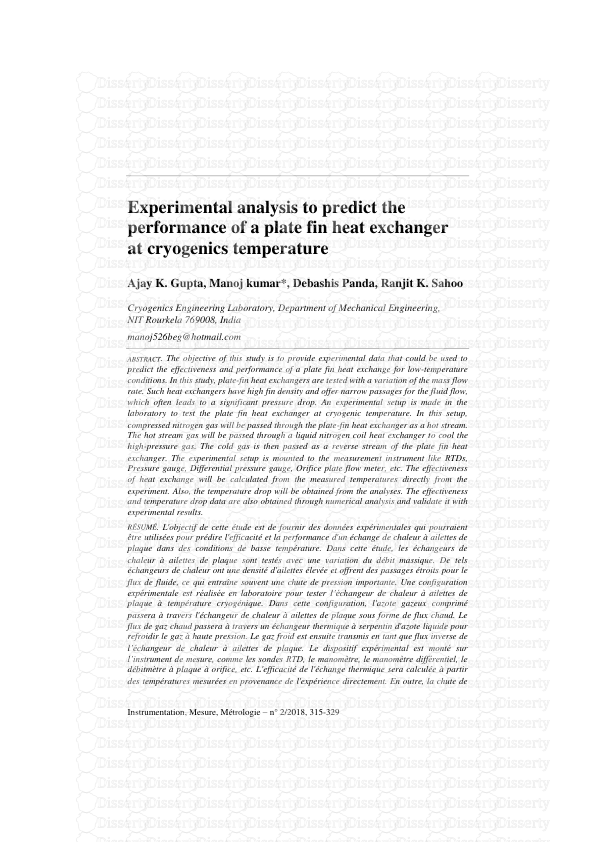
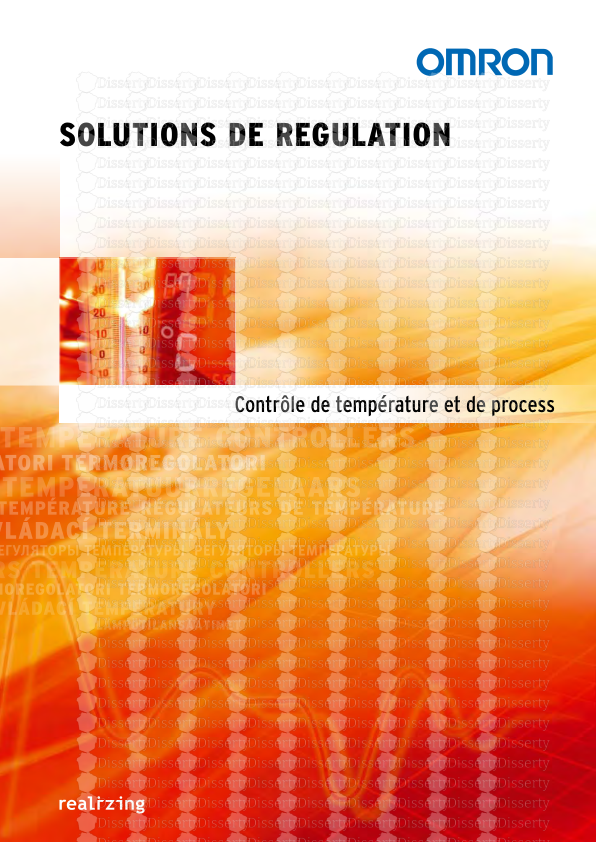
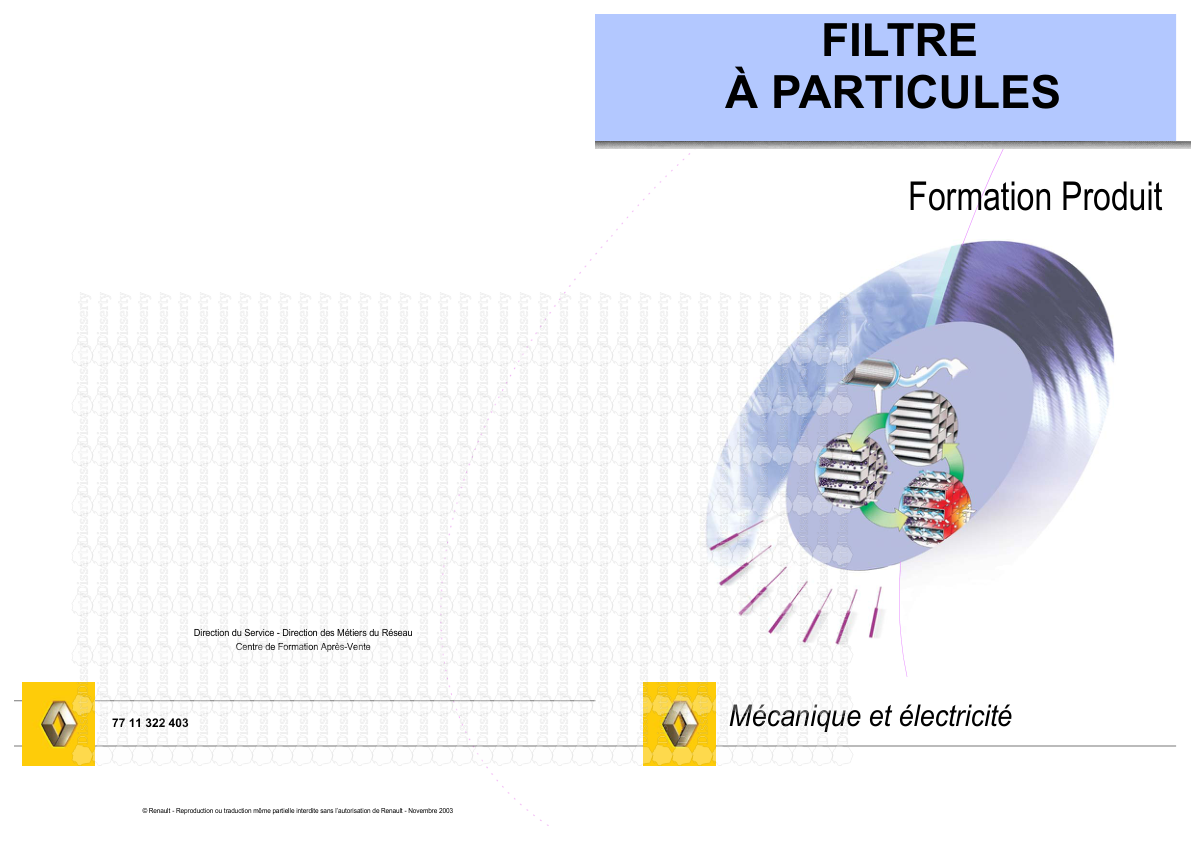
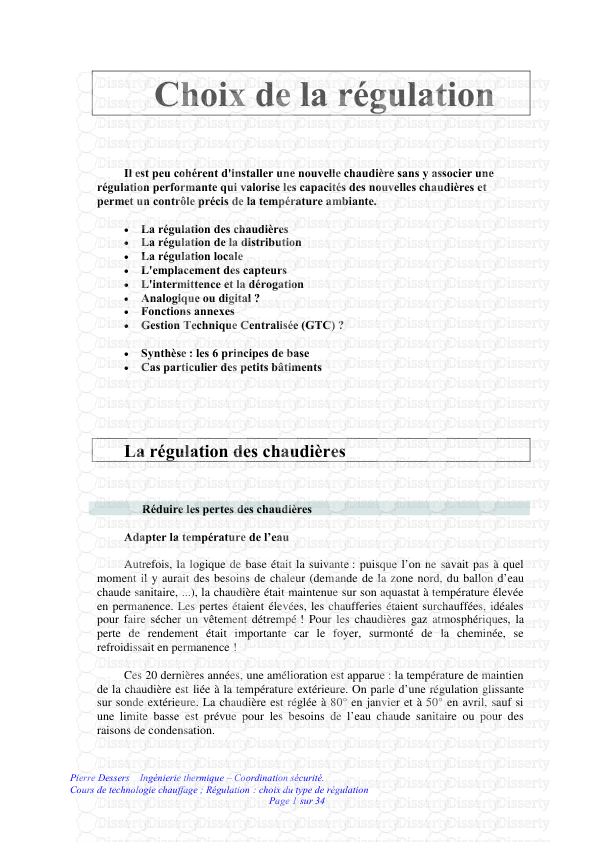
-
49
-
0
-
0
Licence et utilisation
Gratuit pour un usage personnel Attribution requise- Détails
- Publié le Nov 30, 2021
- Catégorie Management
- Langue French
- Taille du fichier 0.0435MB