R8 Clément GOSSELIN Mon travail porte sur l’impression 3D multi matériaux à gra
R8 Clément GOSSELIN Mon travail porte sur l’impression 3D multi matériaux à grande échelle. Aujourd’hui de nombreuses techniques d’impression 3D voient le jour. Tandis que la taille, la complexité des formes fabriquées ainsi que la diversité des matériaux imprimés ne cesse de croître, les premiers bâtiments imprimés commencent à sortir de terre. Quels enjeux pour l’architecture, quel changement dans les méthodes de conception, quelles outil d’aide à la conception pour utiliser tout le potentiel de l’impression 3D multi matériaux ? L’impression 3D permettait elle la réalisation d’une architecture non standard ? L’impression 3D multi matériau et la performance orienté ? Historique de l’impression 3D Aujourd’hui, de nombreux procédés d’impression 3D voient le jour. Maintenant, la plupart des matériaux peuvent être imprimés : Cellules organiques, métaux, plastiques, céramiques… Le terme technique d’impression 3D est fabrication additive. Cette méthode consiste à mettre en forme un objet par l’ajout de couches successives de matière. Par opposition à la fabrication soustractive, qui consiste à mettre en forme un objet par enlèvement de matière, tel que le fraisage. Il s’agit cependant de méthodes de fabrication assez récente dans le milieu de l’industrie, et qui ont vu le jour dans les années 80. En effet, en 1984, Carl Deckard et Joe Beaman déposent le premier brevet pour une machine de stéréolithographie. Il s’agit de la première machine servant à réaliser des objets tridimensionnels par ajout de strates successives. Cette invention découle de plusieurs recherches. En effet, dès les années 50 des chercheurs s’intéressent à la fabrication couche par couche. Il ne s’agit pas alors de fabriquer des objets par le biais de cette méthode, mais plutôt d’en démontrer les intérêts (Compacité des objets produits, plus grande liberté géométrique, production d’objets pré- assemblés, production de mécanismes fonctionnels…). Par ailleurs, dans les années 60, plusieurs chercheurs s’intéressent à des méthodes de polymérisation de résine par double rayon lumineux. Cette dernière permet de faire polymériser un point précis dans un bain de résine. C’est cette technique qui est utilisée par la machine à stéréolithographie de Deckard et Beaman. Les premières machines de fabrication additive sont commercialisées en 1987. Elles sont à cette époque destinées à des industriels pour la réalisation de prototypes. Elles permettent de réaliser à moindre coût de nombreux tests avant de passer à une production en série, et ce, quel que soit la complexité de la pièce à réaliser. En effet, cette technique était alors essentiellement utilisée car elle permettait de faire l’économie du moule. En 1990, la fabrication additive commence à être utilisée pour la réalisation de moule. En effet, il existe de nombreuses machines d’impression 3D orientées vers la production de moules, qui servent principalement à la réalisation de pièces de fonderie, tels que les imprimantes à plâtre et à sable. Le terme « imprimante 3D » voit le jour en 1996. Avant on parlait de stéréolithographie ou de fabrication additive. En 2000, la fabrication additive commence à être utilisée pour la réalisation de pièces fonctionnelles. La plupart de ces dernières sont alors utilisées pour la fabrication de pièces mécaniques complexes (aéronautique, satellite, voiture de course…) ou dans le domaine médical (organes fonctionnels, prothèses en titane…), la joaillerie. Les différentes méthodes d’impression 3D Il existe deux grandes catégories d’imprimante 3D : Les imprimantes à dépôt sélectif et les imprimantes à solidification sélective. Le premier type regroupe toutes les techniques d’extrusion, telle que la FDM (fused deposition modeling), de jet et de spray. Il s‘agit alors de déposer la quantité de matière dont on a besoin au bon endroit. Le deuxième regroupe toutes les techniques de solidification par chauffe ou ajout d’un liant, tel que le frittage de poudre et stéréolithographie : de la matière sous forme de liquide ou de poudre remplie l’intégralité du bac. Il s’agit alors de solidifier couche par couche les zones constituant l’objet. Chacune de ces méthodes a ses avantages et ses inconvénients : -Le dépôt sélectif est moins précis que la solidification sélective (surtout concernant les méthodes d’extrusion). -Le dépôt sélectif permet de réaliser une impression multi matériaux. -La question des supports durant la phase d’impression se pose davantage concernant la méthode de dépôt sélectif car il n’y a pas de matière autour pour la maintenir. -La question de la trajectoire de l’outil se pose d’avantage concernant le dépôt sélectif, du mois concernant les méthodes d’extrusion. En effet, concernant ces dernières, les propriétés au sein du cordon de dépôt sont différentes des propriétés entre cordons (il y a une rupture plus ou moins marquée à l’interface des cordons). Concernant l’évolution de la fabrication additive, nous pouvons constater deux choses : -une augmentation de la taille des objets imprimés. -l’apparition et le développement des impressions multi matériaux. Ces dernières permettent de mettre en œuvre, lors d’une seule impression, des matériaux possédant des propriétés très différentes (flexibilité, transparence, opacité…) et ainsi de créer des matériaux gradués. L’échelle architecturale La taille des objets réalisables par une machine d’impression 3D est intrinsèquement liée à la résolution de cette dernière. En effet, il est difficile de réaliser des objets de grande dimension possédant une résolution fine car le temps d’impression nécessaire serait trop important. A petite échelle (entre 5 et 50 cm), tout peut être imprimé (pour ainsi dire n’importe quelle forme et n’importe quels matériaux), il y a peu de contraintes géométriques. La gravité est facilement contrecarrée quelle que soit la catégorie de l’imprimante (dépôt ou solidification sélective). Le problème de dévers et porte-à-faux augmentent à mesure que la taille des objets imprimés est importante. Ainsi, la résolution de ces derniers devient cruciale concernant les imprimantes 3D de grande échelle. Des systèmes d’impression 3D d’échelle architecturale commencent cependant à voir le jour. Ces machines conçoivent des objets avec des résolutions de 1 à 3 cm. Il y a des exemples de machines appartenant à chacune des deux catégories d’impression décrites précédemment. Les machines de cette échelle impriment essentiellement des matériaux à matrice cimentaire. Concernant la méthode de solidification sélective, il y a D-shape dirigé par Enrico DINI. Concernant la méthode de dépôt sélectif, il y a Contour Crafting dirigé par Koshnevis et Chinese Matérial qui a en avril dernier réalisé les premiers bâtiments fonctionnels imprimés en 3D. D-shape, entreprise dirigé par Enrico DINI, (méthode par solidification sélective) Chinese Matérial, (méthode par dépôt sélectif) Nous pouvons constater par ces image qu’à grande échelle la solidification sélective permet de réaliser des formes totalement libre, mais a le désavantage de requérir le déplacement d’une très grande quantité de matière. En effet, même si la poudre utilisée comme support peut être réutilisée pour fabriquer un autre objet, il est nécessaire de déplacer, au moins le volume englobant de l’objet (la « bounding box »), auquel il est nécessaire d’ajouter le volume dû aux pentes d’écoulement de la poudre. Ainsi, pour réaliser l’objet que nous voyons sur les photos, qui a pour dimension environ 3x3x3m, il a fallu déplacer à deux reprises (pour l’utiliser comme support puis pour le retirer une fois l’objet achevée) au moins 18m3 de matière. Ainsi, la solidification sélective tourne, en augmentant l’échelle, en une gigantesque opération de terrassement. Cette méthode d’impression semble donc plus adaptée à des échelles plus réduites. Par ailleurs, cette méthode ne permet pas de réaliser une impression multi matériaux, et rend impossible la fabrication in situ étant donné la non transportabilité de la machine (on est obligé d’avoir une structure qui englobe tout le bâtiment). La méthode de dépôt sélective, quant à elle (toujours, d’après les photos), semble ne permettre que la réalisation de formes en 2.5D, soit des extrusions linéaires d’un dessin plan. Cette méthode permet cependant de réaliser une impression multi matériaux. Par ailleurs, il n’est pas nécessaire d’avoir une machine englobant le bâtiment, la tête d’impression peut être indépendante d’une structure extérieure. Ainsi, le dépôt sélectif semble plus approprié pour la grande échelle que la solidification sélective. Par ailleurs, la thèse datant de 2002 de Hongkyu Kwon décrivant les débuts des expérimentations du procédé de fabrication Contour Crafting (qui est un procédé de dépôt sélectif), parlait déjà de réalisation de forme tridimensionnel, c'est-à-dire possédant des dévers et porte-à-faux. Dans cette thèse il commençait également déjà à parler de Co- extrusion en vue d’imprimer différent types de matériaux. L’expérimentation : mécanique, programmation, matière et trajectoire. Mon travail portant sur les méthodes d’impression 3D multi matériaux, j’ai cherché à réaliser une tête d’impression me permettant d’extruder des matériaux aux propriétés différentes. Le but de cette expérience est tout d’abord d’identifier, en termes de mise en œuvre, les différences d’un tel procédé, comparé à des méthodes traditionnel. Puis d’analyser le potentiel de ce procédé dans la construction. Ce procédé permet théoriquement de mettre en place un file to factory permettant de réaliser des formes libres. Ceci est-il toujours envisageable concernant de grandes échelles d’objets ? Ce type de procédé pose la question de la répartition de la matière dans un objet. Quels procédés de conception sont les plus appropriés pour réaliser une telle opération. Pour simplifier le problème, j’ai commencé par identifier des dualités de performances propres aux matériaux uploads/s3/ clc3a9ment-gosselin-r8 1 .pdf
Documents similaires
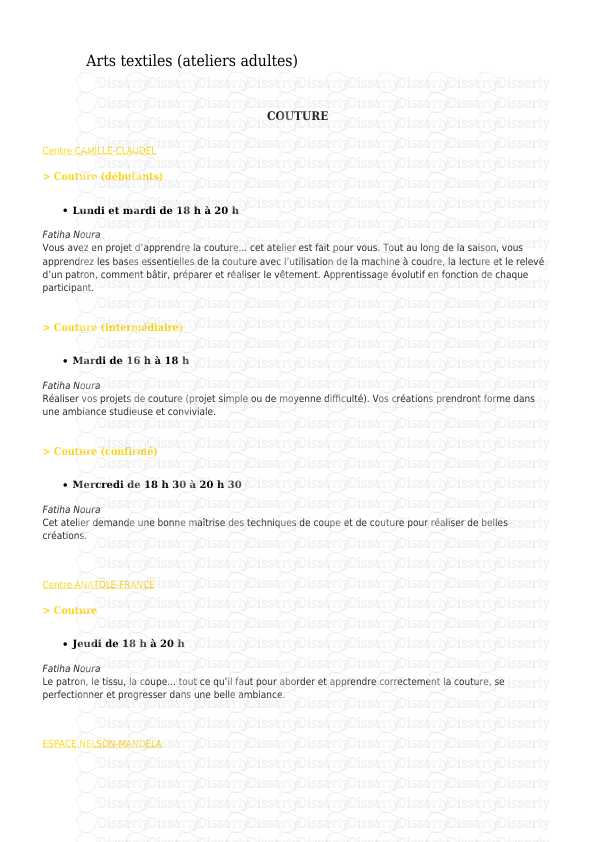
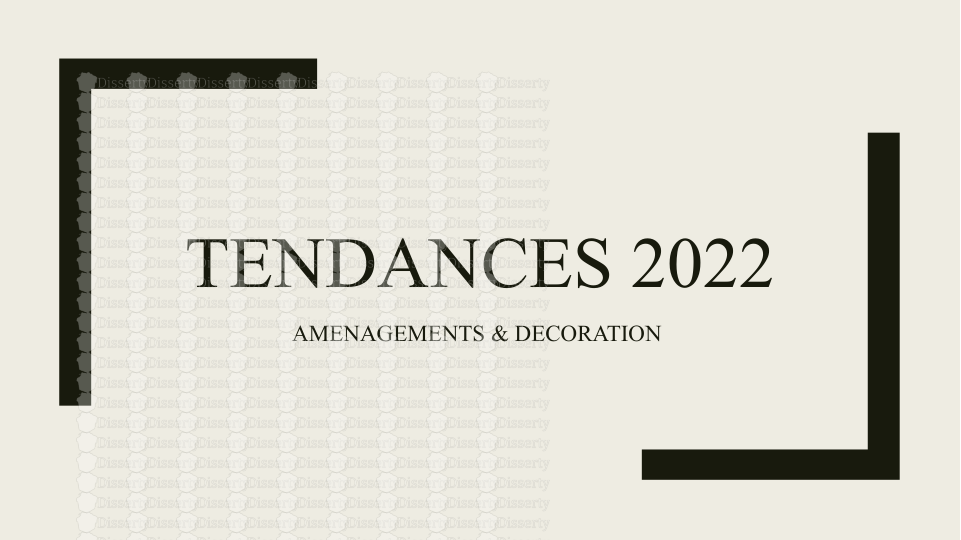
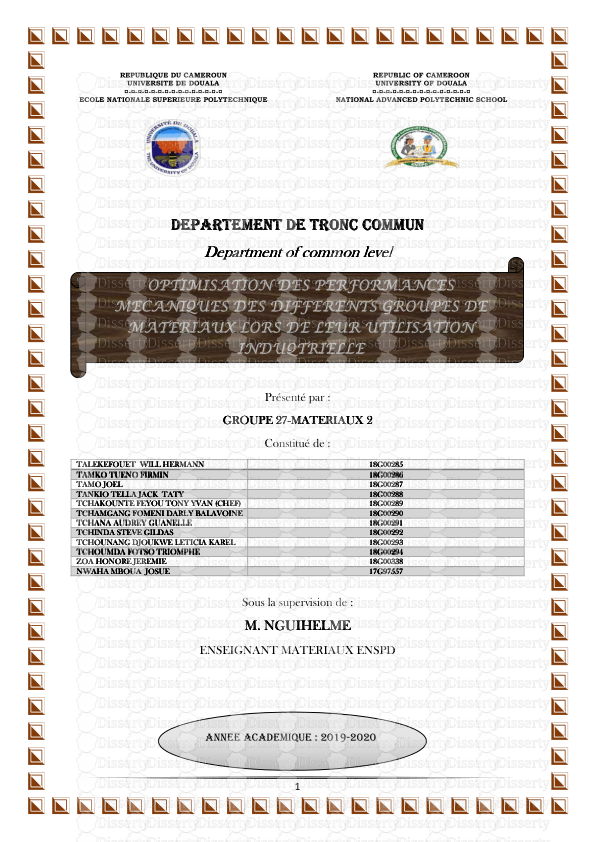
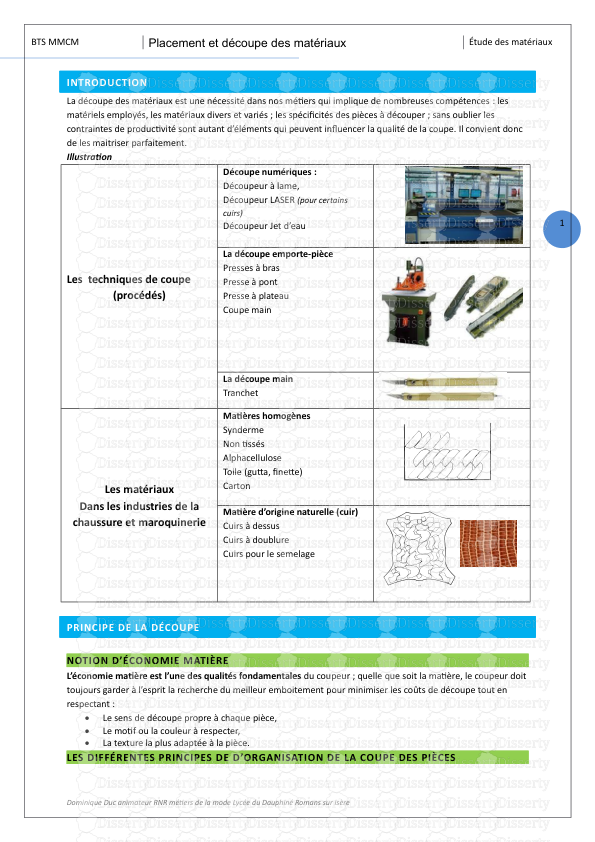
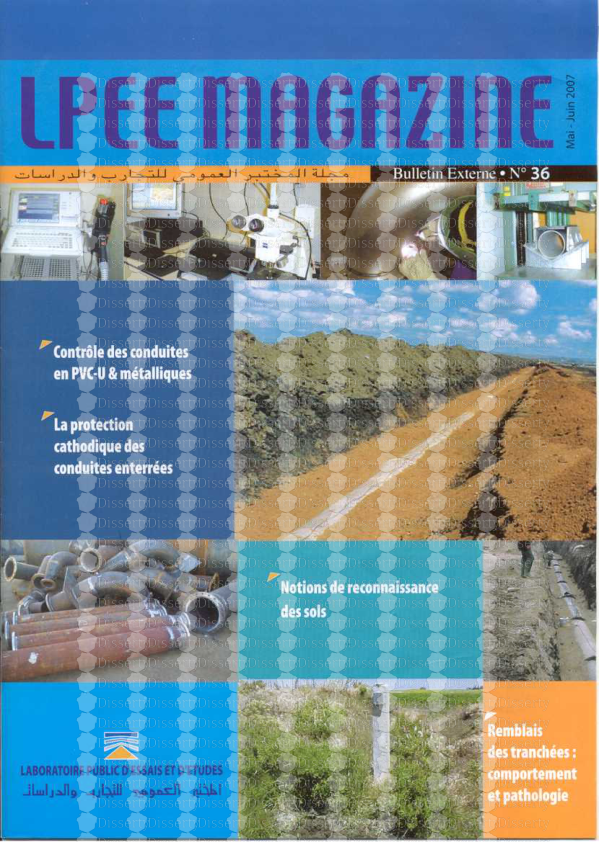
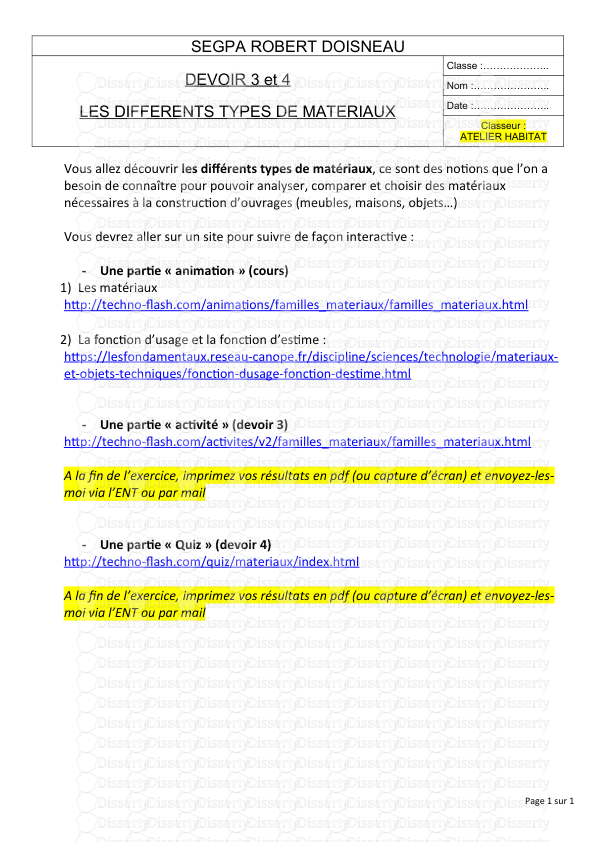
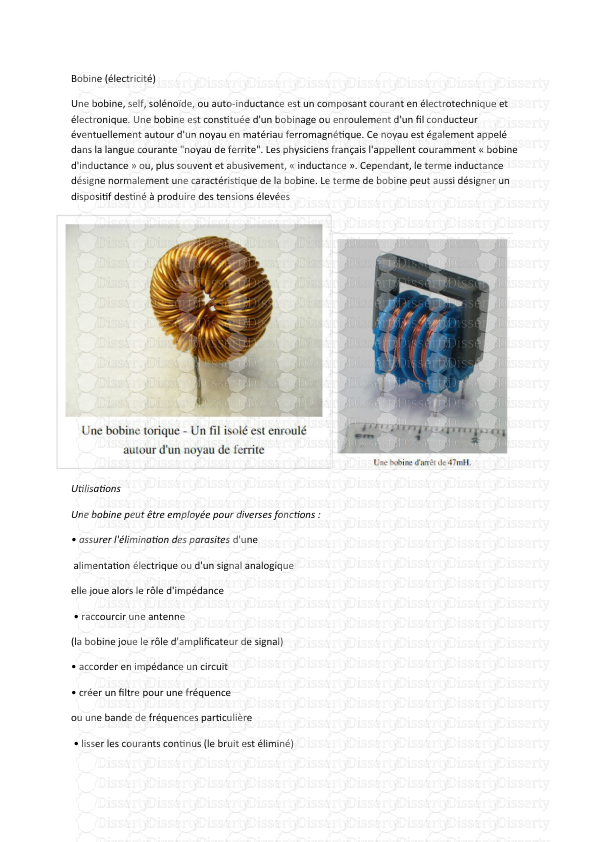
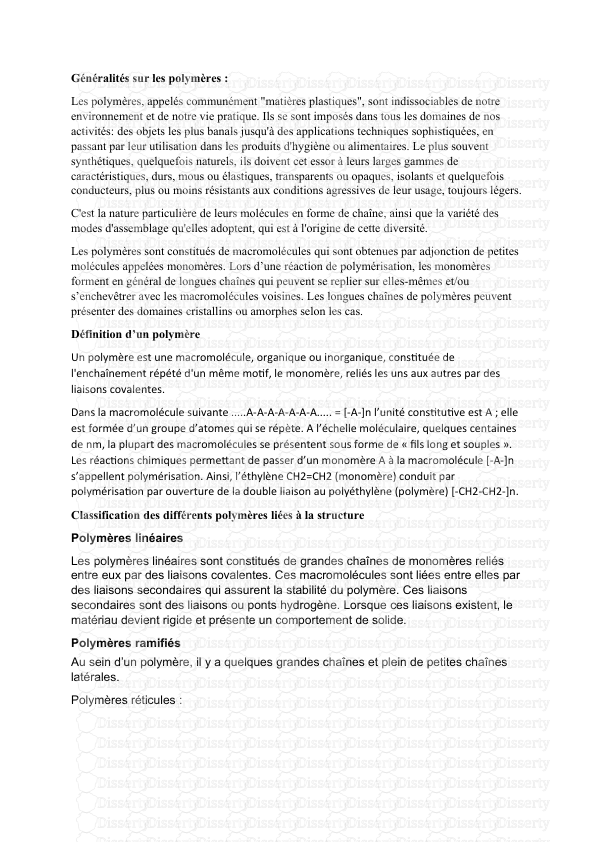
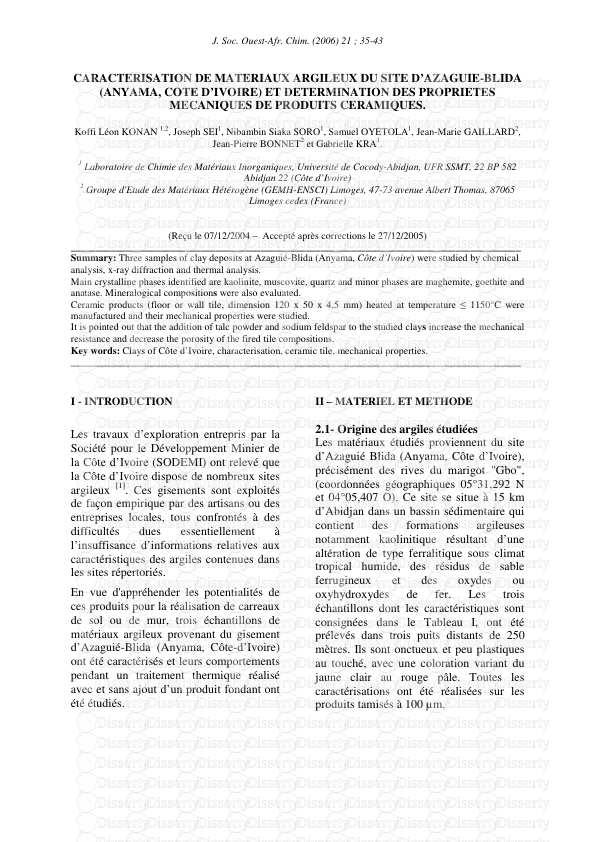

-
59
-
0
-
0
Licence et utilisation
Gratuit pour un usage personnel Attribution requise- Détails
- Publié le Apv 29, 2022
- Catégorie Creative Arts / Ar...
- Langue French
- Taille du fichier 2.8767MB