PROCEDES DE MISE EN FORME DES MATERIAUX 1 COURS PROCEDES DE MISE EN FORME DES M
PROCEDES DE MISE EN FORME DES MATERIAUX 1 COURS PROCEDES DE MISE EN FORME DES MATERIAUX Master LMD 2ème année Construction Mécanique Dr. BOUTEGHMES Djamel Année universitaire 2020-2021 UNIVERSITE DE BATNA 2 FACULTE DE TECHNOLOGIE DEPARTEMENT DE GENIE MECANIQUE PROCEDES DE MISE EN FORME DES MATERIAUX 2 MODOLE : PROCEDES DE MISE EN FORME DES MATERIAUX MASTER 1 FABRICATION MECANIQUE La définition compète d’un organe de machine exige la détermination de sa forme, de ses dimensions et de sa matière. Il est indispensable pour étudier et comprendre un matériau de le caractériser (identifier) a l’aide de techniques de caractérisation appropriées. Soit destructive c'est-à-dire endommagent (détérioration) le matériau. Soit non destructive qui n’endommage pas le matériau. I. Les principales techniques de caractérisation peuvent se classer par : Les essais mécanique destructives : Dont le but est de caractériser les comportements mécaniques des matériaux tel que : Le module de Young, la résilience, la limite élastique, la dureté etc.……. Les essaies non destructives qui permettent de caractériser le matériau sans le dégrader par : Les analyses physico-chimique par des méthodes tel que la métallographie, diffraction par rayons x etc.….. Une analyse de la chimie et de la structure du matériau ce qui est intéressant de corréler avec les propriétés mécaniques et la résistance a la corrosion. Ces essaies sont utilisés pour les matériaux couteux, peu disponible II. Le choix d’un matériau dépend de plusieurs critères : Caractéristiques mécaniques : limite élastique, masse, dureté, résilience… Caractéristiques physico-chimiques : comportement à la corrosion, vieillissement… Caractéristiques de mise en œuvre : usinabilité, soudabilité, trempabilité… Caractéristiques économiques : prix, disponibilité, expérience industrielle… PROCEDES DE MISE EN FORME DES MATERIAUX 3 On peut regrouper les matériaux en familles : /87 III. Mise en forme des matériaux Les techniques de mise en forme des matériaux ont pour objectif de donner une forme déterminée au matériau tout en lui imposant une certaine microstructure, afin d'obtenir un objet ayant les propriétés souhaitées. C'est un travail qui nécessite de maîtriser parfaitement les paramètres expérimentaux (composition du matériau, température, pression, vitesse de refroidissement, etc.). Les techniques diffèrent selon les matériaux (leur solidité, l'usage, etc.). Les performances mécaniques des pièces de structures dépendent fortement du matériau et de son procédé de transformation. La mise en forme des alliages métalliques s’intéressent aux matériaux lors de la transformation par déformation plastique (état solide), solidification(état liquide) ou compactage ( poudre) dans tous les grand secteurs industriels : industrie du transport ( ferroviaire, automobile aéronautique), de l’emballage, de l’énergie du nucléaire et de la santé. De manière générale, la mise en forme des matériaux en métallurgie tient au découpage, formage, soudage, perçage et usinage. S'ajoutent à cela différents traitements (traitement thermique…) visant à donner aux produits des propriétés particulières. Pour les métaux, les techniques de mise en forme sont : Le forgeage : c'est la technique de mise en œuvre la plus ancienne (5 000 ans av. J.-C.), elle consiste à exercer une force sur la matière afin de la former et regroupe aujourd'hui plusieurs méthodes telles que : L'emboutissage , Le laminage , Le tréfilage, Le filage La fonderie : cette technique consiste à fondre et à couler le métal dans un moule. Le choix du moule est un critère à prendre en compte. Il existe ainsi plusieurs PROCEDES DE MISE EN FORME DES MATERIAUX 4 méthodes de moulage : moulage sable, moulage coquille et moulage en cire perdue ; le frittage : ce procédé fait appel à la métallurgie des poudres. Il permet de consolider la poudre sous l'action de la chaleur et la rend ainsi compacte. III.1.Procédés par Formage Le formage est un procédé de fabrication de pièces qui consiste à donner une forme à un sous-produit. III.I.I.Différentes techniques permettant le formage : III.1.1.2.formage à chaud: forgeage, estampage, matriçage, emboutissage, chaud de retrait, etc. formage à froid: pliage, emboutissage, forgeage à froid, extrusion, frappe à froid, tréfilage, étirage , cintrage-roulage par exemple en chaudronnerie), martelage, etc.. Magnétoformage a)Pour la mise en forme à chaud de structure massives (filage, laminage, estampage ou forgeage libre. les principaux paramètres influents sont : 1. Température 2. Matériaux et ses caractéristiques 3. Géométrie des outils 4. Vitesse et pression de frappe b) La mise en forme sans enlèvement de la matière et parmi lesquelles on peut citer : Le formage à chaud et à froid La fonderie Le frittage Procédés formage à chaud: Forgeage, estampage, matriçage, emboutissage A) Forgeage Consiste à déformer, par choc ou par pressage entre deux outils, une masse métallique rendue malléable par chauffage. Aussi, par définition, le forgeage est un procédé de mise en forme des métaux par déformations plastiques à chaud ou à froid. On chauffe le métal (fours) à une température convenable afin que le métal devient malléable et forgeable. Le métal est appelé « Lopin » de volume calculé. PROCEDES DE MISE EN FORME DES MATERIAUX 5 Dans le forgeage ordinaire, dit libre, le métal comprimé s’écoule latéralement a l’effort sans aucune retenue. B) Le forgeage manuel : C’est le forgeage traditionnel à l’enclume et l’outillage de frappé à main. C) Estampage, matriçage Le matriçage et l’estampage : Le matriçage et l’estampage sont deux termes synonymes. C’est un procédé de fabrication mécanique exécuté par les presses sur lesquelles sont fixées des « matrices ». Il permet de produire des grandes séries de pièces. Pour le matriçage la matière de départ les barres sont rondes ou carrées rarement méplates de section constante obtenues au moyen de laminoirs. Estampage L’estampage est un forgeage en matrice. Il faut entendre par la que la déformation du métal est gênée par les parois d’une cavité creuse dans des outils particuliers nommées : matrices. Le métal emprisonné entre les deux matrices qui se rapprochent l’une de l’autre subit de leurs part une contrainte qui l’oblige a s’écoule latéralement, mais l’écoulement latérale est frainé par le passage de la matière entre les faces des matrices a la sortie de la gravure. Il se développe une pression de caractère pseudo-hydrostatique au sein du métal qui le contraint d’épouser la forme des gravures et de remplir la cavité. La partie du métal qui s’échappe hors de la gravure se nomme bavure. IV. Mise en forme par déformation plastique : Procédés utilisant l’aptitude du matériau à la déformation plastique (encore appelée ductilité). La capacité de déformation est une fonction de : Matériau (rhéologie) Procédé (mode d’application des contraintes) Conditions opératoires (tribologie, température, vitesse) PROCEDES DE MISE EN FORME DES MATERIAUX 6 IV.1. Forgeage libre : La matière d’œuvre est comprimée suivant une direction et se déplace librement suivant les deux autres. Le forgeage libre s'apparente au martelage des forgerons. Température de forgeage : Alliage ferreux 1 100 < T °C < 1 300 Alliage d’aluminium 450 < T °C < 550 Alliages cuivreux 750 < T °C < 900 Forgeage libre Moyens : IV.2. Forgeage mécanique : Engins travaillant par pression (V ≤ 1 m/s) : Presse hydraulique Engins travaillant par choc (V≥ 6 m/s) : Marteau-pilon, mouton PROCEDES DE MISE EN FORME DES MATERIAUX 7 Forgeage libre – Moyens : Marteau-pilon : Méthodes de forgeage libre : Etampage : Calibrage de la section à l’aide de deux étampes reproduisant chacune la demi-forme de la pièce IV.3. Laminage conventionnel Opération de mise en forme par déformation plastique, destinée à réduire la section d’un produit de grande longueur, par passage entre deux ou plusieurs outils axisymétriques tournant autour de leur axe ; c’est la rotation des outils qui entraîne le produit dans l’emprise par l’intermédiaire du frottement. PROCEDES DE MISE EN FORME DES MATERIAUX 8 Laminage C’est un procédés de réduction de l’épaisseur ou de changement de la section transversale d’une pièce par l’application de forces de compression a l’aide de jeux de rouleaux. Les produits fabriqués par ce procédé sont les plaques, les tôles et les feuilles. Les plaques ou tôles épaisse sont généralement d’épaisseurs supérieures à 6 mm ou 10mm. Elles sont utilisées pour des applications structurales telles que les coques de navire ou des structures de semi remorques. Les tôles sont généralement de moins de 6mm et plus de 0 ,15mm. Elles sont utilisees pour les revêtements de bâtiments, les carrosseries d’automobiles, structures d’avion, produits d’emballages, cannettes, produits de cuisine. Les feuilles d’aluminium utilisees pour l’emballage des aliments, des produits pharmaceutiques etc.…… Elles ont une épaisseur inferieur a 0,15mm. IV.4. Estampage : Le lopin, préalablement chauffé, est comprimé entre deux blocs (cas le plus fréquent) comportant des gravures (matrices). PROCEDES DE MISE EN FORME DES MATERIAUX 9 Filage: Au moyen d’une compression ou d’un choc, le lopin est passé dans une filière qui lui donne sa forme. PROCEDES DE MISE EN FORME DES MATERIAUX 10 IV.5. Le filage direct Filage: Le filage s’effectue à froid pour les métaux les plus malléables (Al par exemple) à chaud pour les autres. IV.6. Etirage : L’ébauche est soumise à une traction longitudinale et passe à travers uploads/s3/ procedes-de-mise-en-forme-des-materiaux-m1-fmp-2o21.pdf
Documents similaires
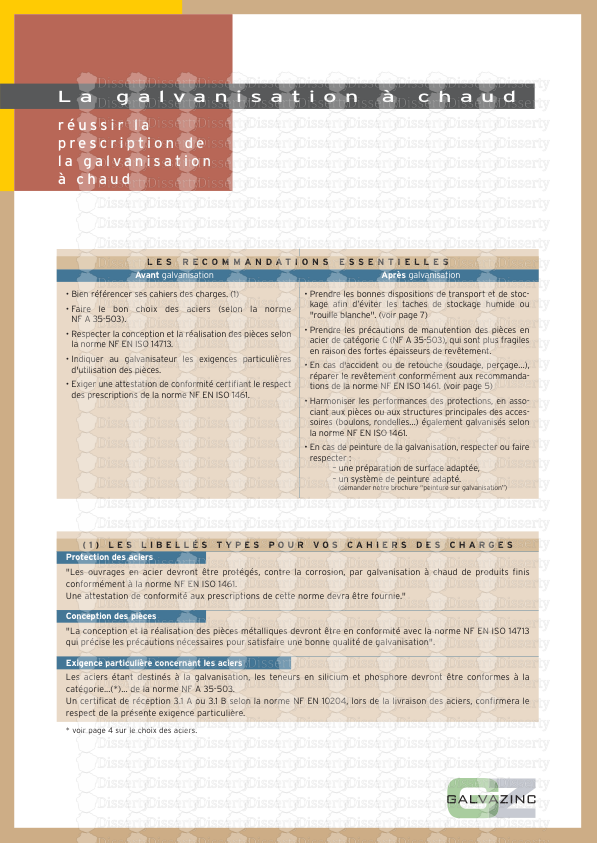
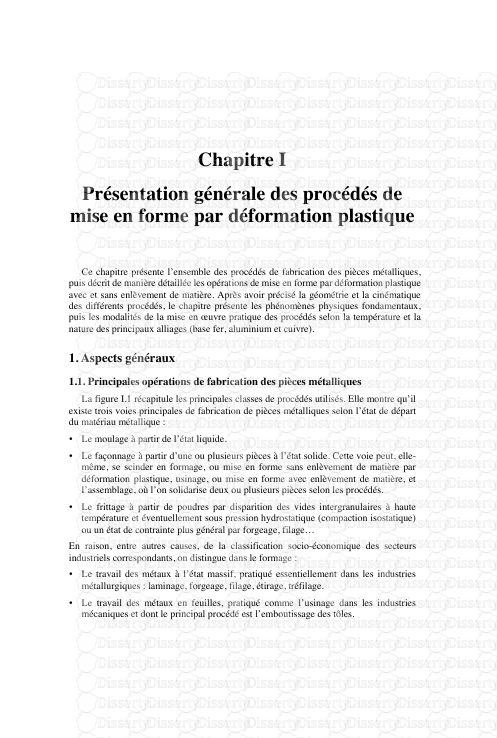
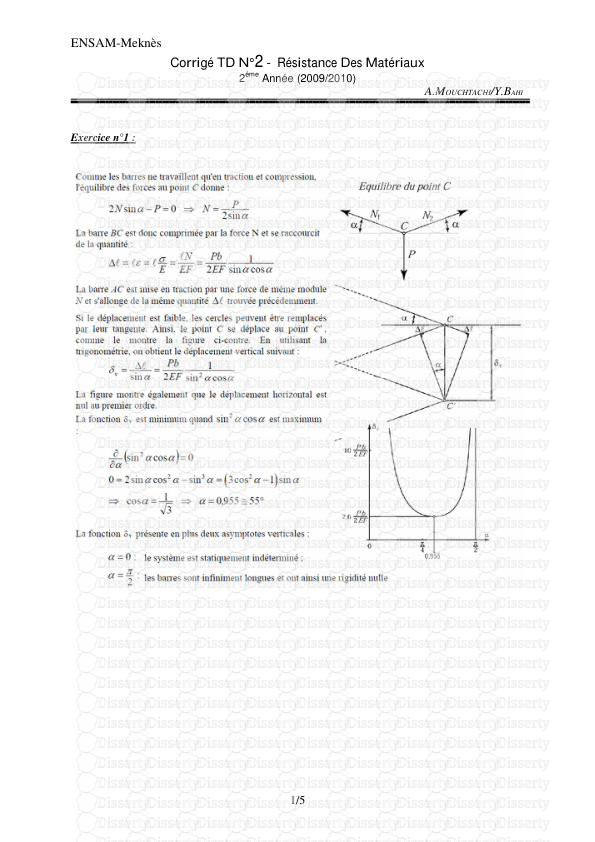
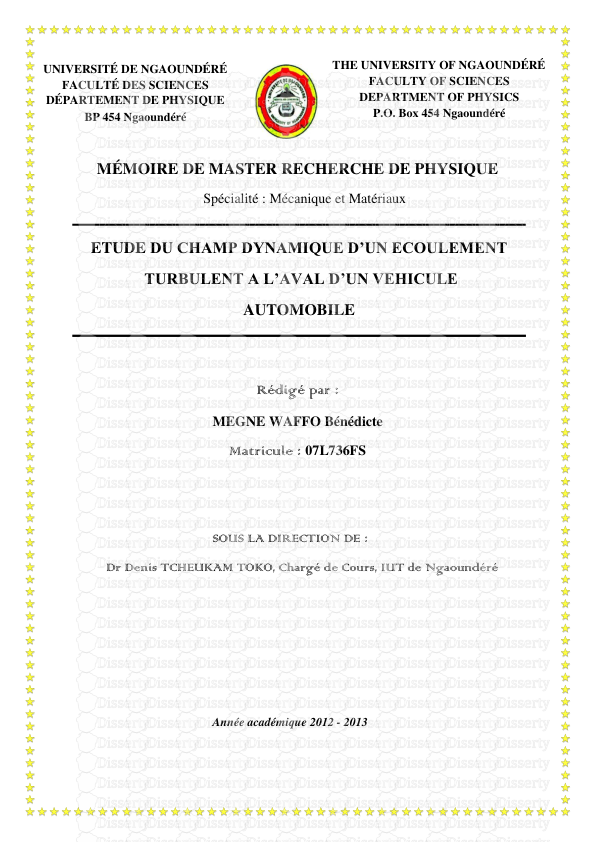
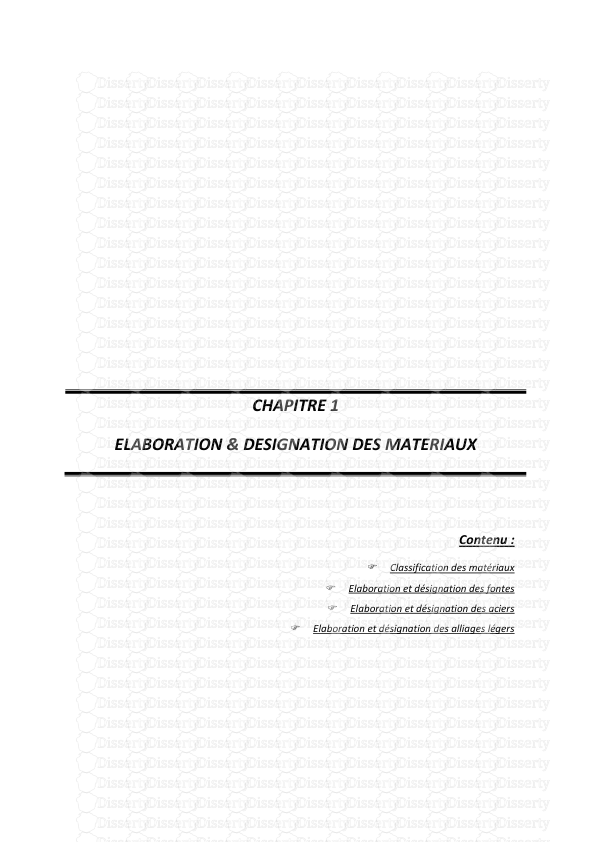
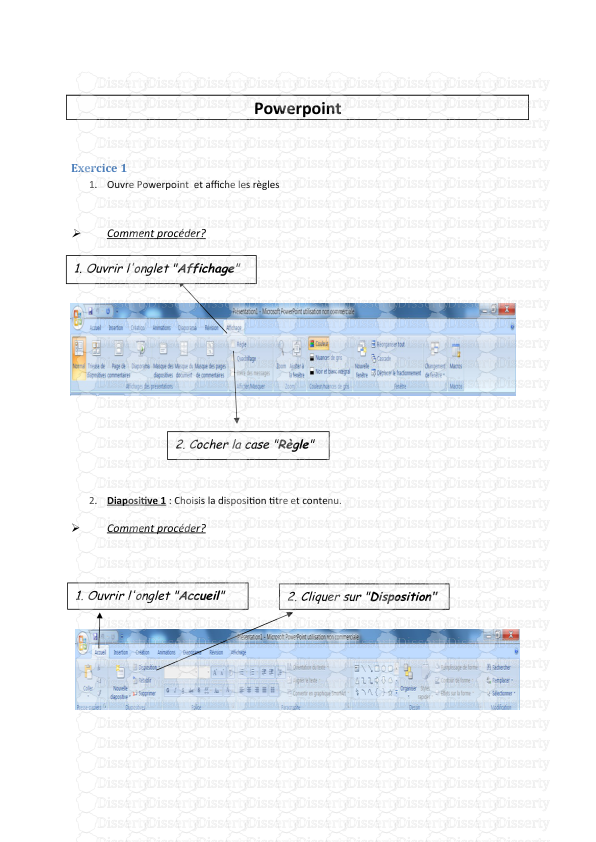
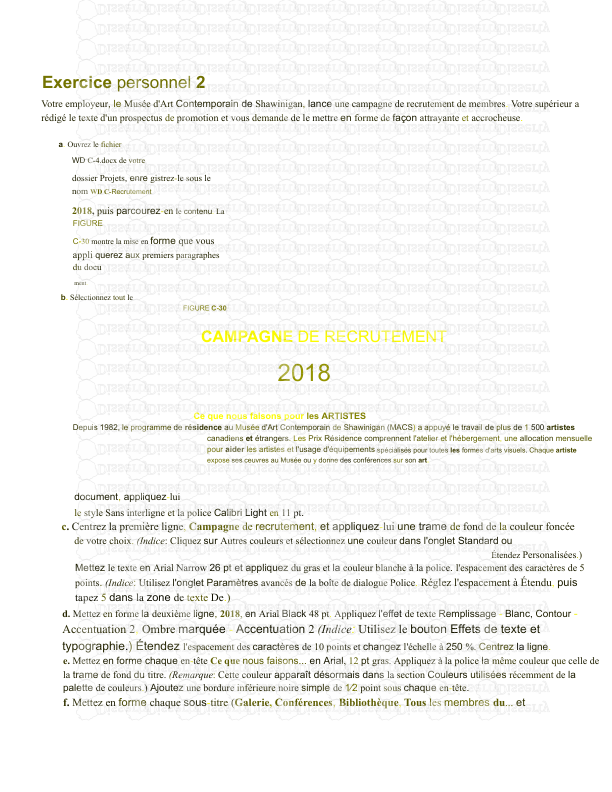
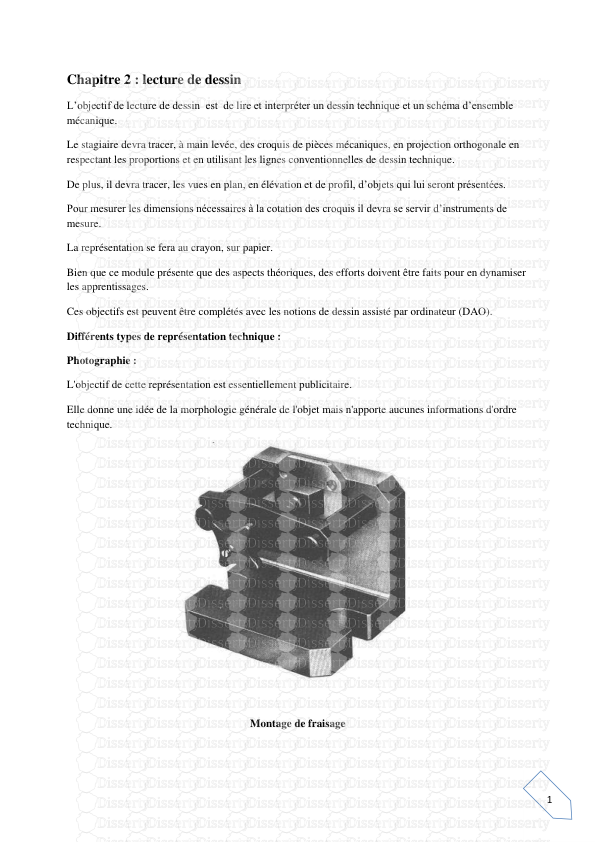
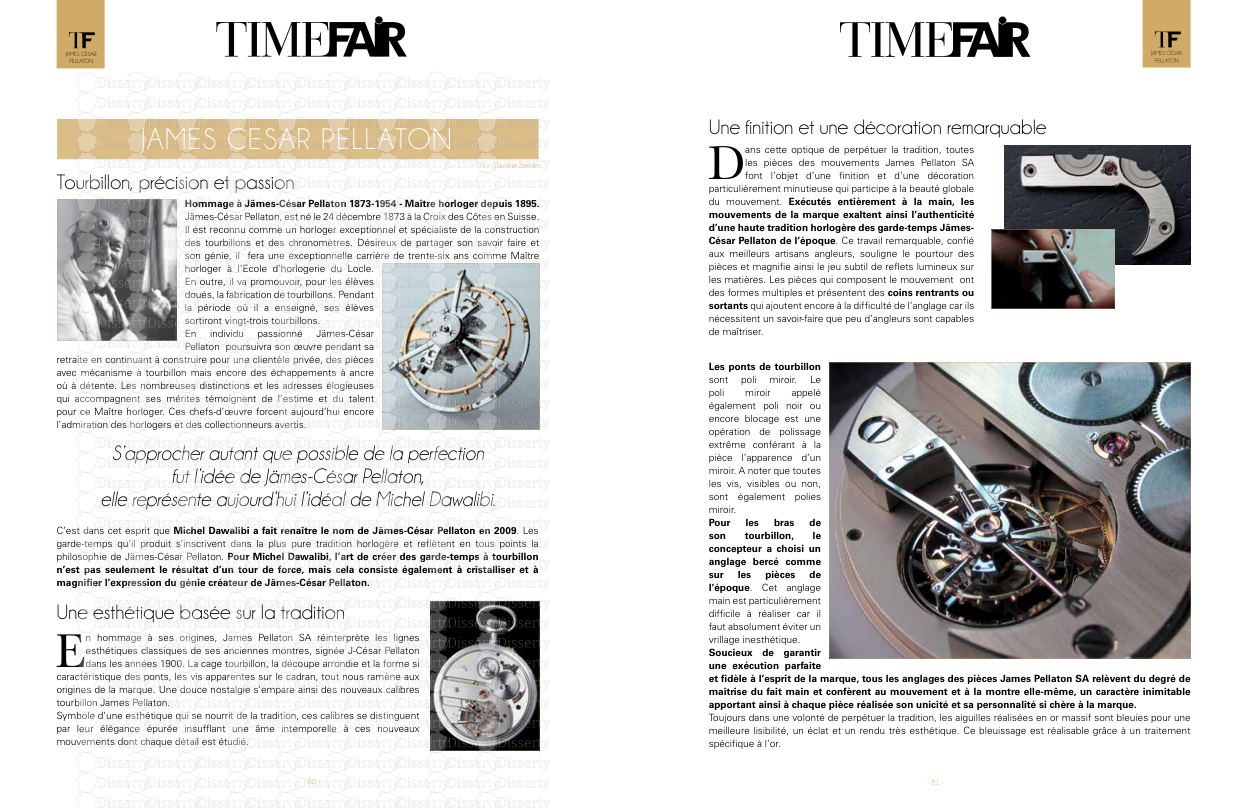
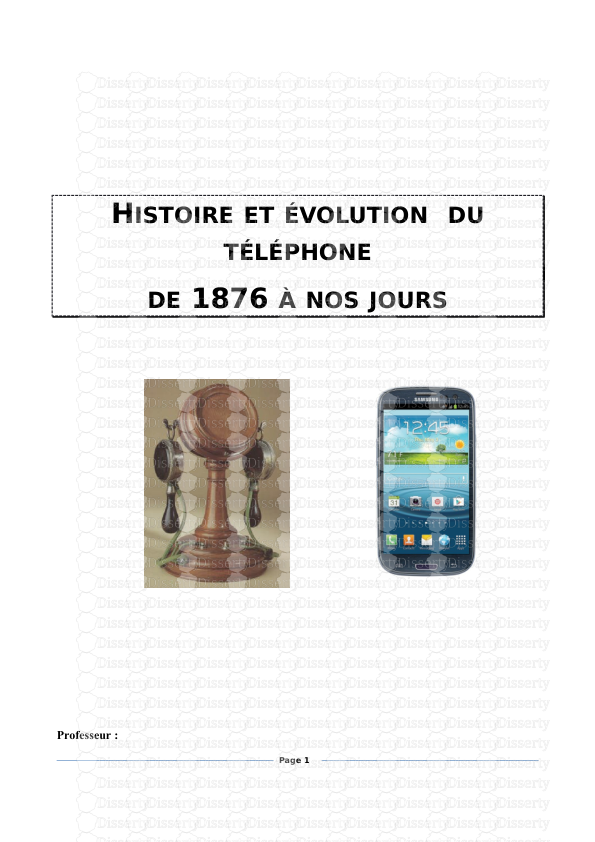
-
47
-
0
-
0
Licence et utilisation
Gratuit pour un usage personnel Attribution requise- Détails
- Publié le Dec 09, 2022
- Catégorie Creative Arts / Ar...
- Langue French
- Taille du fichier 1.1594MB