Devoir à rendre gestion de production Exercice 1 : goulet d’étranglement : 1.Qu
Devoir à rendre gestion de production Exercice 1 : goulet d’étranglement : 1.Quelle est la cadence journalière (nombre de pièces par heure) de la chaîne ? Les cadences journalières sont : - M1 : 8/0,5 = 16p/j -M2 : 8/0,42 = 19 p/j -M3 : 8/0,53 = 15p/j ==> Cadence journalière de la chaîne est 15p/j. 2. Quel est le poste goulot de la chaîne ? Pourquoi ? M3 représente le poste goulot parce il prend plus de temps pour produire moins . 3. Quelles sont les valeurs des temps morts sur les postes non-goulots ? -M1=> 8-(15×0.5)=0.5H -M2=> 8-(15×0.42)= 1,7H 4.Le responsable de production impose à l’opérateur du poste M1 de produire au maximum de sa cadence pendant 20 heures, pensant que des pièces similaires seront, sans doute, nécessaires ultérieurement dans d’autres commandes. Si ce n’est pas le cas, quelle est la quantité de pièces non utilisées induites par cette décision ? 20/0.5= 40 pièces, cette décision va générer 24 pièces supplémentaires dans le stock (40 pièces – 16 pièces) 5.La machine du poste M3 tombant très souvent en panne du fait de sa vétusté, sa capacité réelle est estimée à 70% de sa capacité nominale. Refaire les questions 1 et 2 dans ces nouvelles conditions : -M3 : 8/0,53×0.7=10.5p/j -Temps opératoire = 8/10.5 = 0.76h ==>Donc le goulot reste M3 . Exercice 2 : goulet d’étranglement : 1. Présenter le schéma d’analyser du temps productifs . ==> atelier1: Heures de présence =3477h Heures de changement =3047.5h Heures de nettoyages =399.5h Heures de fonctionnement=2777.5h Heures de montage = 270 h Heures de marche =2750 h Heures de pause = 27,5 h ==> atelier2: Heures de présence =4100h Heures de changement =3690h (4100×0,9) Heures de nettoyages =410h Heures de fonctionnement=3394,8h (3690×0,92) Heures de montage = 296h Heures de marche =3360,852h (3394,8×0,99) Heures de pause = 33,948 h 2. Calculer les capacités disponibles. Capacités disponible Atelier 1 2750 Atelier 2 3360.85 Atelier 3 4050 3. Calculer les capacités nécessaires. Temps/R1 Temps Total Temps/R2 Temps Total Capacités nécessaires Atelier 1 4 2000 2 1200 3200 Atelier 2 3 1500 3 1800 3300 Atelier 3 2 1000 5 3000 4000 4. Déterminer l’atelier qui présente le goulot d’étranglement . Excédent de capacité (ou manque de capacité) Taux de disponibilité Atelier 1 -450 1.163 Atelier 2 60.85 0.981 Atelier 3 50 0.987 ==>L’Atelier 1 a un taux de disponibilité supérieur à 1 ce qui n’est pas réaliste. Cet atelier présente un manque de capacité de 450 heures ; c’est un goulot d’étranglement. 5. Procéder à l’ajustement par les quantités : Le coefficient d’ajustement : m= 1/Td = 1/1.169 = 0.859375 La production ajustée : Budget de vente Production ajustée R1 500 429.6875 R2 600 515.625 Tableau de chargement définitif : A1 A2 A3 Capacité nécessaires R1 1718.75 1288.5 859 R2 1031.25 1546.2 2577 TOTAL 2750 2834.7 3436 Capacité disponibles 2750 3360.85 4050 Excédent de capacité (ou manque de capacité) 0 526.15 614 Taux disponibilité 1.00 0.843 0.848 6. Procéder à l’ajustement par la marge sur coût variable . Calcul de marge par heures de passage et par produit dans l’atelier 1 : R1 R2 Marge sur coût variable 160 110 Le temps nécessaire 4 2 Marge sue coût variable horaire 40 55 Ordre de fabrication 2 1 Le programme de production s’établit ainsi : Produit selon l’ordre de fabrication Quantité Le temps unitaire Temps nécessaire Marge sur coût variable unitaire Marge sur coût variable totale R2 600 2 1200 110 66000 R1 388 4 1550 160 62080 TOTAL 2750 TOTAL 128080 Tableau de chargement définitif : A1 A2 A3 Capacité nécessaires R1 1550 1164 776 R2 1200 1800 3000 TOTAL 2750 2964 3776 Capacité disponibles 2750 3360.85 4050 Excédent de capacité (ou manque de capacité) 0 396.85 274 Taux disponibilité 1.00 0.881 0.932 7. Comparer les résultats de 5 et 6 et conclure : ==> après l’ajustement par le coût variable, les taux de chargement sont inférieurs ou égaux à 1 et l’atelier 2 et 3 sont en chômage seulement de 396.85 heures et 274 heures au lieu de 526.15 heures et 614 heures pour l’ajustement par les quantités. Exercice 3 : PIC et PDP 1- Sachant que le stock initial est de 200 et que les lots de production ont une taille minimale de 600 unités, proposer un PDP à stock minimum avec un délai d’approvisionnement d’une période . 0 1 2 3 4 5 6 7 Prévisions 100 250 300 400 250 250 500 Commande fermes 300 250 100 0 0 0 0 Total des besoins 400 500 400 400 250 250 250 Stock 200 400 500 100 300 50 400 500 Réception 600 600 600 600 600 Ordre lancé 600 600 600 600 600 2- Étant donné la variation de la demande sur le marché, établir un PDP qui assure, pour chaque semaine, un stock équivalent à deux semaines de ventes. (Aucune indication sur le stock initial et le délai d’approvisionnement) 0 1 2 3 4 5 6 7 Total des besoins 400 500 400 400 250 250 500 Stock 500 0 400 0 250 0 0 Réception 900 800 500 500 Ordre lancé 900 800 500 500 Exercice 4 : MRP 1.A l’aide de l’annexe, donner les ordres de fabrication et de commande pour le produit A et les composants B, C, D, E et F. (un tableau pour chaque article) Article : A Stock initial : 100 Stratégie de prod : Lot pour Lot Délai : 1 Stock de sécurité : 0 Semaine 0 1 2 3 4 Besoin brut 50 60 50 40 Ordres lancés Besoin net 0 10 50 40 Stock 100 50 0 0 Ordre prévu Fin 10 50 40 Début 10 50 40 Article : B Stock initial : 80 Stratégie de prod : Lot pour Lot Délai : 1 Stock de sécurité : 0 Semaine 0 1 2 3 4 Besoin brut 20 100 80 0 Ordres lancés Besoin net 0 40 80 0 Stock 80 60 0 0 0 Ordre prévu Fin 40 80 Début 40 80 Article : D Stock initial : 30 Stratégie de prod : Lot pour Lot Délai : 1 Stock de sécurité : 0 Semaine 0 1 2 3 4 Besoin brut 10 50 40 0 Ordres lancés Besoin net 0 30 40 0 Stock 30 20 0 0 0 Ordre prévu Fin 30 40 Début 30 40 Article : E Stock initial : 60 Stratégie de prod : Lot pour Lot Délai : 1 Stock de sécurité : 0 Semaine 0 1 2 3 4 Besoin brut 70 120 0 0 Ordres lancés Besoin net 10 120 0 0 Stock 60 0 0 0 0 Ordre prévu Fin 10 120 Début 10+120 Article : C Stock initial : 50 Stratégie de prod : Lot pour Lot Délai : 1 Stock de sécurité : 0 Semaine 0 1 2 3 4 Besoin brut 20 100 80 0 Ordres lancés Besoin net 0 70 80 0 Stock 50 30 0 0 0 Ordre prévu Fin 70 80 Début 70 80 Article : F Stock initial : 30 Stratégie de prod : Lot pour Lot Délai : 1 Stock de sécurité : 0 Semaine 0 1 2 3 4 Besoin brut 60 80 0 0 Ordres lancés Besoin net 30 80 0 0 Stock 30 0 0 0 0 Ordre prévu Fin 30 80 Début 30+80 Exercice 5 : MRP Article : C Stock initial : 35 Stratégie de prod : X20 Délai : 1 Stock de sécurité : 10 Semaine 0 1 2 3 4 5 6 Besoin brut 40 30 15 35 40 25 Ordres lancés 20 20 Besoin net 0 5 0 35 35 20 Stock 35 15 25 10 15 15 10 Ordre prévu Fin 20 40 40 20 Début 20 40 40 20 Exercice 6 : MRP 2. Déterminer les programmes de fabrication et d’approvisionnement. Article : PF Stock initial : 130 Stratégie de prod : Lot pour Lot Délai : 2 Stock de sécurité : 0 Semaine 0 14 15 16 17 18 19 20 Besoin brut 85 110 0 90 120 100 Ordres lancés Besoin net 65 0 90 120 100 Stock 130 130 45 0 0 0 0 0 Ordre prévu Fin 65 90 120 100 Début 65 90 120 100 Article : SE1 Stock initial : 40 Stratégie de prod : Lot pour Lot Délai : 2 Stock de sécurité : 0 Semaine 0 12 13 14 15 16 17 18 Besoin brut 65 90 120 100 Ordres lancés Besoin net 25 90 120 100 Stock 40 40 40 0 0 0 0 0 Ordre prévu Fin 25 90 120 100 Début 25 90 120 100 Article : SE2 Stock initial : 35 Stratégie de prod : Lot pour Lot Délai : 1 Stock de sécurité : 0 Semaine 0 13 14 15 16 17 18 Besoin brut 130 180 240 200 Ordres lancés Besoin net 95 180 240 200 Stock 35 35 0 0 0 0 0 Ordre prévu Fin uploads/s3/devoir-s5.pdf
Documents similaires
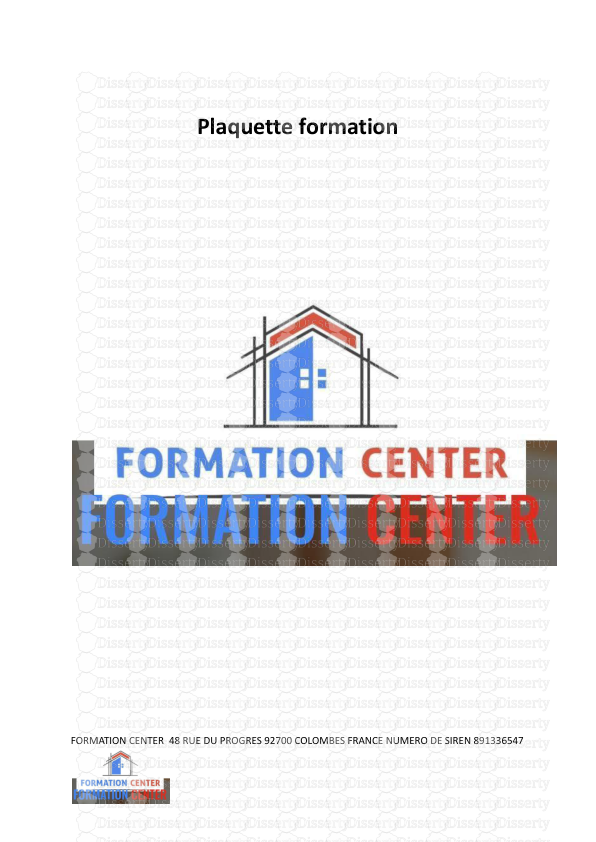
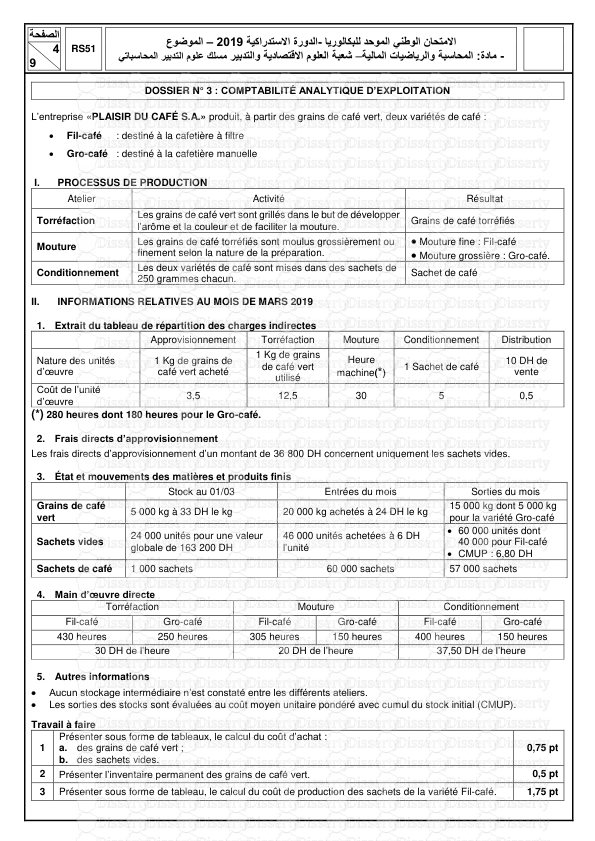
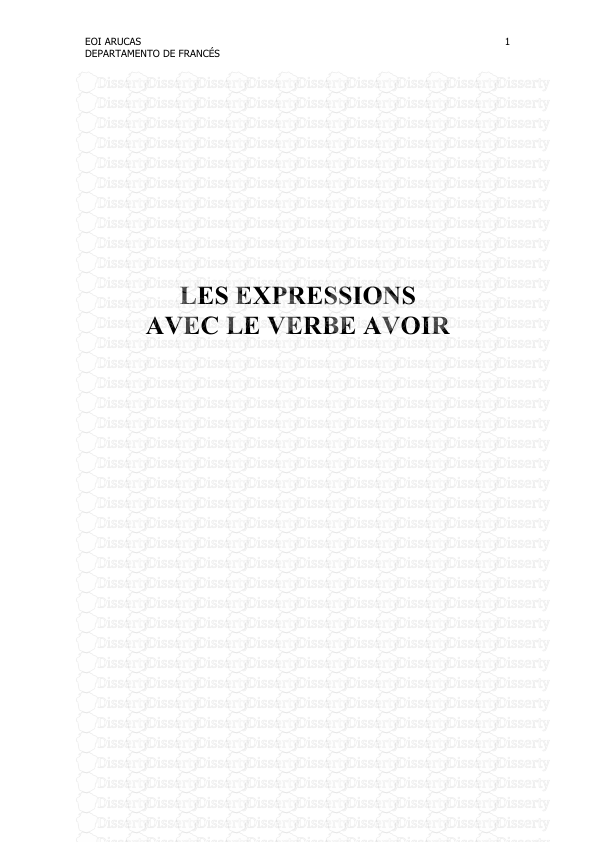
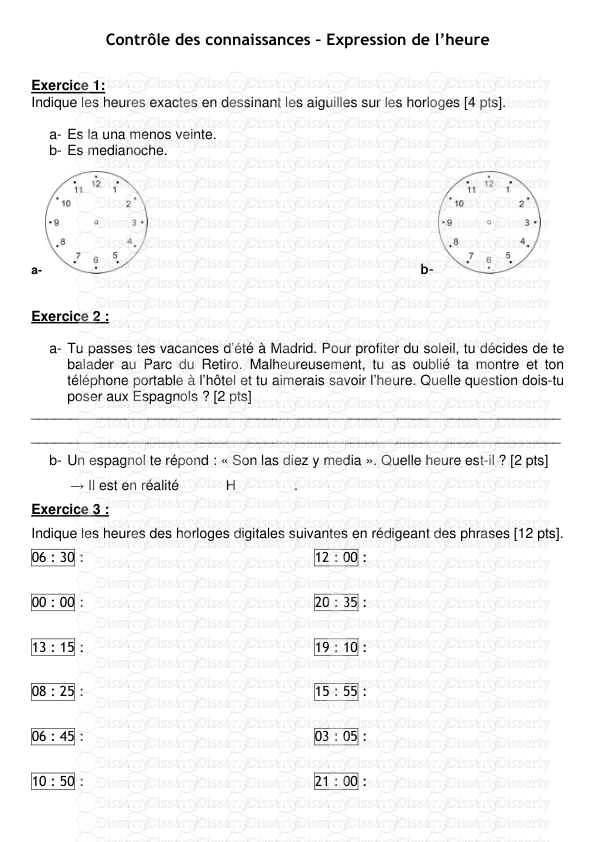
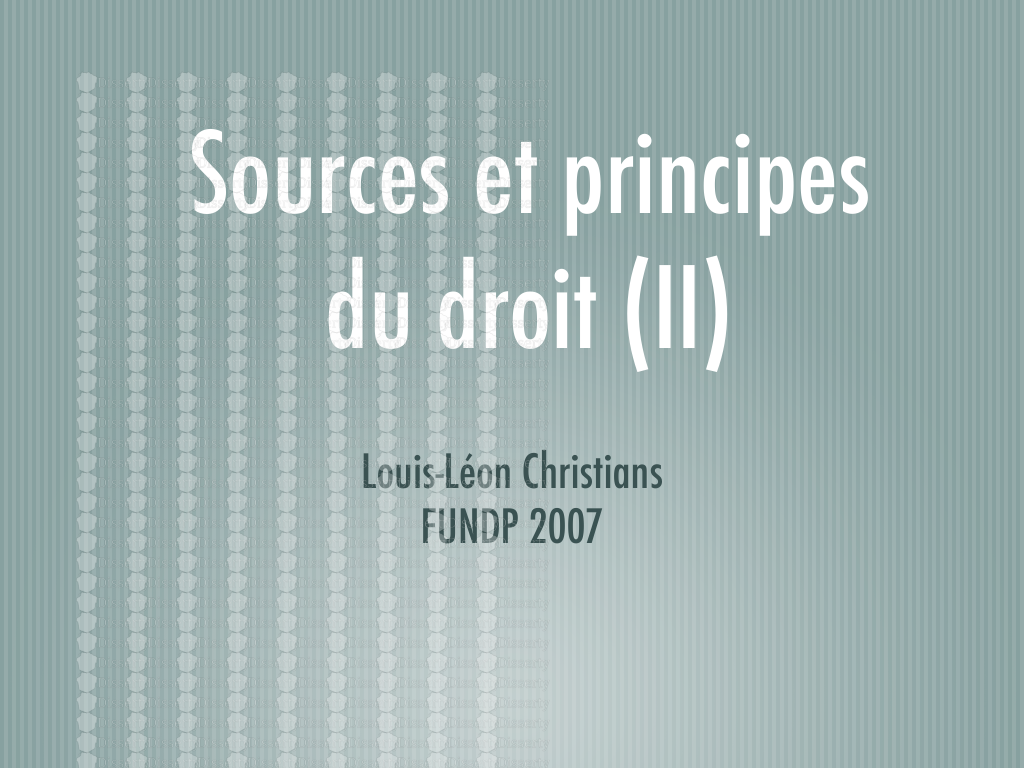
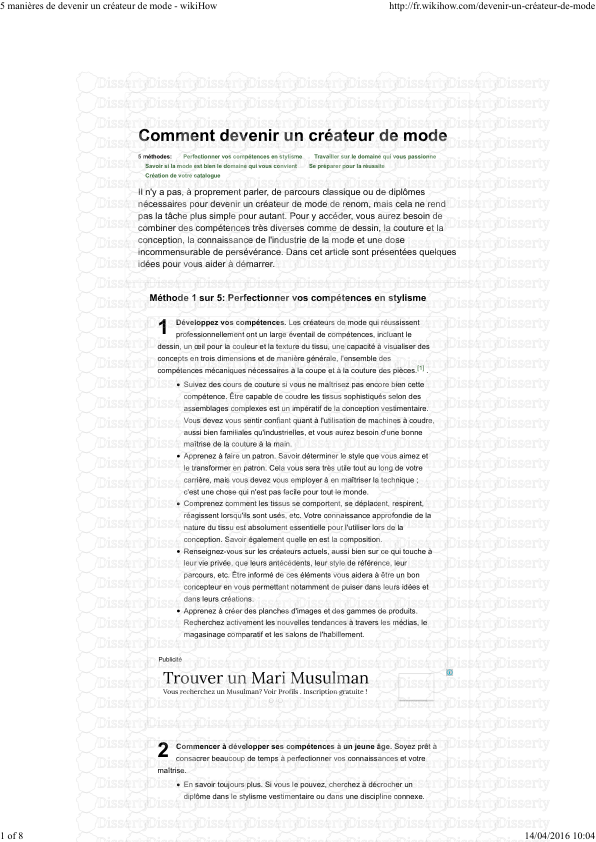
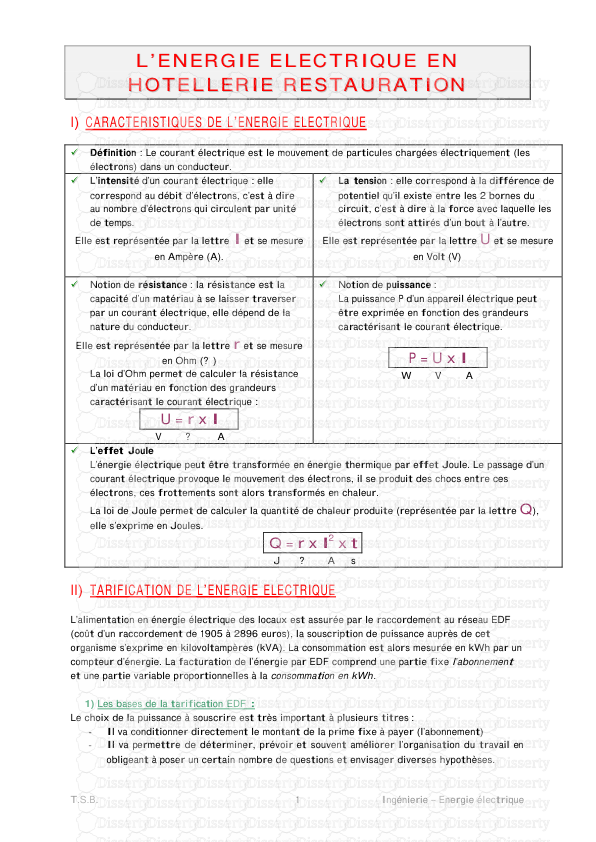
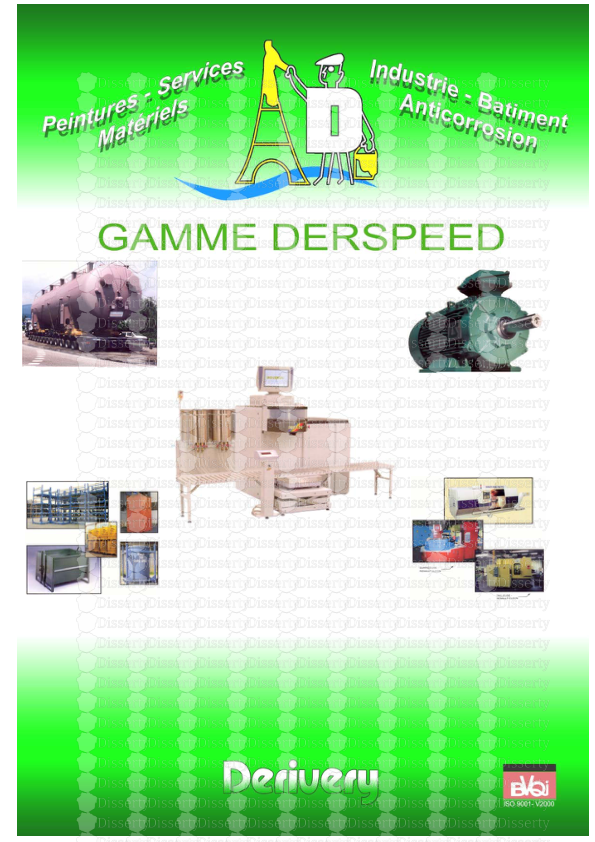

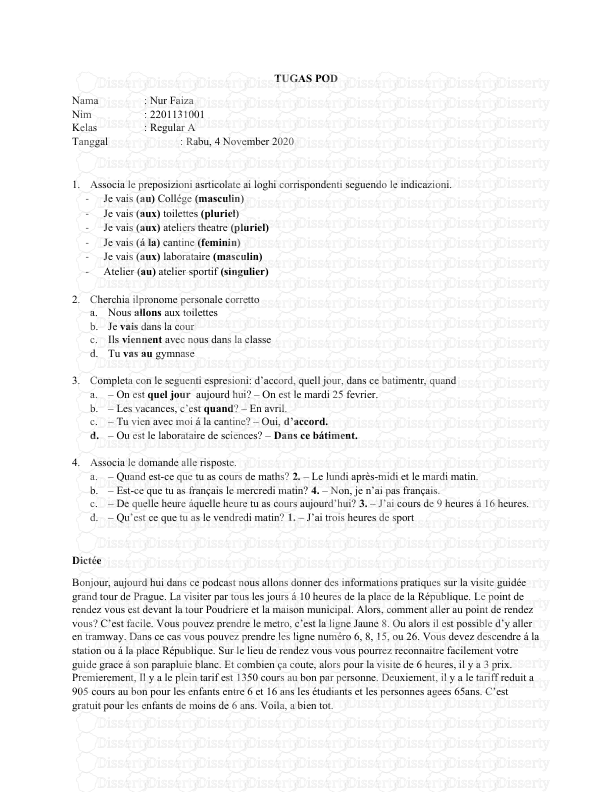
-
44
-
0
-
0
Licence et utilisation
Gratuit pour un usage personnel Attribution requise- Détails
- Publié le Aoû 01, 2021
- Catégorie Creative Arts / Ar...
- Langue French
- Taille du fichier 0.2407MB