Matière : Intensification des procédés République Algérienne Démocratique et Po
Matière : Intensification des procédés République Algérienne Démocratique et Populaire Ministère de l’Enseignement Supérieur et de la Recherche Scientifique Université Ahmed Zabana de Relizane Faculté des Sciences et Technologie Département de génie des procédés Année Universitaire 2020/ 2021 Chapitre I : Bases de l’intensification des procédés I.1-Définitions L’intensification des procédés consiste à développer des nouveaux équipements ou des nouvelles techniques qui, comparées aux techniques couramment utilisées aujourd’hui, permettront de diminuer de façon conséquente le rapport taille des équipements/capacité de production, la consommation d’énergie et la formation de produits indésirables de façon à aboutir à une technologie plus sûre et moins coûteuse. Ainsi les buts de l’intensification des procédés sont : – diminution du coût des équipements et d’opération – amélioration de la sécurité des équipements – augmentation de la productivité – diminution de la consommation énergétique – diminution du coût d’opération – préservation de l’environnement en diminuant la formation des sous-produits des réactions. L’intensification des procédés permet de très nombreuses et très diverses applications, que Stankiewicz et Moulin regroupent dans deux catégories : – les équipements (hardware) spécifiques qui sont des appareils nouveaux développés pour atteindre les objectives cités ci-dessus. Il s’agit des équipements mettant en œuvre des réactions chimiques (microréacteurs, réacteurs à disques rotatifs) ou des autres appareils comme les échangeurs de chaleurs compacts ou les mélangeurs statiques. – les méthodes (software) dédiées à l’intensification des procédés, qui sont des exploitations différentes d’équipements déjà existants. Il s’agit des réacteurs multifonctionnels (distillation réactive), des séparations hybrides (distillation extractive), des sources d’énergies alternatives (ultrasons) ou des diverses méthodes (fluides supercritiques). I.2-Principes et applications de l’IP L’intensification des procédés s’attache à concevoir de nouveaux équipements plus propres, plus surs et plus efficaces tout en diminuant la taille des unités en rapport avec leur volume de production, la consommation de ressources (énergies, eau, fossiles) et le cout de production. Elle s’impose donc pour la révolution de l’industrie chimique puisqu’elle nécessite une réelle transformation des usines et implique a repenser différemment les procédés. L’intensification s’articule autour de deux axes : •Un premier concerne les méthodes d’intensification qui reviennent par exemple à coupler plusieurs opérations unitaires pour aboutir à des procédés multifonctionnels, ou encore à détourner des équipements de leurs fonctions originelles. •Un deuxième axe est relatif aux technologies d’intensification telles que Le micro technologies, dans lesquelles les phénomènes de transferts et de mélange sont intensifies, ou encore aux les technologies ayant recours à des matériaux innovants. I.3-Les différents approches de l’IP I.3.1-L’aspect réduction du ratio surface sur volume (S/V) Le principe fondamental de la miniaturisation des appareils revient à accroitre leur rapport surface d’échange sur volume, tout en maintenant leur capacité de production. Les premières conséquences majeures sont l’amélioration des transferts thermiques (grâce à une surface d’échange multipliée) et des transferts de matière (grâce à la diminution des longueurs caractéristiques de diffusion moléculaire). I.3.2-L’aspect microstructuration Les petites dimensions (des canaux) issues de la miniaturisation des procédés imposent un écoulement laminaire au sein des réacteurs et conduisent à de faibles temps de séjour. I.3.3. Intensification du transfert thermique dans les réacteurs échangeurs compacts L’intensification des phénomènes thermiques est primordiale pour traiter des réactions exothermiques. Tout comme pour l’intensification des transferts de matière, le design des canaux, pour lesquels le ratio S/V est très élève est à l’origine de l’intensification des transferts thermiques dans les réacteurs-échangeurs compacts. L’utilisation de matériau très conducteur pour la fabrication des plaques (comme le Carbure de Silicium ou l’Aluminium) va également faciliter les échanges de chaleur entre le fluide réactionnel et la paroi. La caractérisation du transfert thermique passe par l’étude du coefficient global d’échange thermique U. Il est courant de s’intéresser au coefficient d’intensification UA/V, plutôt qu’au coefficient U pour prendre en compte la compacité des réacteurs, A étant l’aire d’échange et V, le volume de fluide procédé échangeant avec la paroi du réacteur. Chapitre II : Les équipements pour l’intensification des procédés II.1-Microréacteurs Les microréacteurs sont des réacteurs chimiques de très petites dimensions qui ont généralement une structure en forme de sandwich constituant d'un certain nombre de tranches (couches) avec micro canaux (10-100 μm). Les couches effectuent divers fonctions, du mélange aux réaction catalytique, échange de chaleur ou séparation. Intégration de ces différentes fonctions au sein d'une seule unité est l'un des avantages les plus importants de microréacteurs. Les très hauts débits de transfert de chaleur réalisables dans les microréacteurs permettent un fonctionnement des procédés hautement exothermiques isothermes, ce qui est particulièrement important dans la réalisation d'études cinétiques. A cause des rapports volume réactif/surface très faibles, les microréacteurs sont potentiellement attractifs pour les procédés impliquant des réactifs toxiques ou explosifs. L'échelle à laquelle des procédés utilisent des batteries de plusieurs microréacteurs devient économiquement et techniquement réalisable. Fig.II.1 : Microréacteur pour modèle réduit d’avion II.2-Réacteur à baffles oscillantes Le réacteur à baffles oscillantes (OBR) est constitué d'un tube muni de chicanes équidistantes présentées transversalement à un flux oscillant. Les chicanes perturbent la couche limite au niveau de la paroi du tube, tandis que l'oscillation améliore le mélange par la formation de vortex. Si un flux net est également superposé à ce mouvement oscillatoire, alors le réacteur se comporte comme de nombreux réservoirs en série bien mélangés. Ainsi, l'OBR est capable d'obtenir un bon comportement d'écoulement à piston (plug flow) lorsque le débit / mélange du piston est découplé du flux net. Leur avantage est la réduction de processus de longue durée de séjour avec des rapports L /D de plusieurs ordres de grandeur plus petits que les réacteurs à écoulement tubulaire conventionnels. Fig.II.2: Intensification des procédés par remplacement d'un réacteur discontinu par un OBR continu II.3-Réacteur à disque tournant Le disque rotatif est une plaque orientée horizontalement qui peut être chauffée ou refroidie et tournée par un moteur pneumatique jusqu'à 5000 tours par minute. Des courants d'alimentation liquides, alimentés à travers le centre de la plaque, se déplacent rapidement à travers la surface et forment un film mince d'épaisseur δ. Le liquide quitte le disque sur son bord, après il peut être recueilli. Ces réacteurs à disque tournant peuvent être utilisés pour différentes réactions, comprenant des réactions mettant en œuvre des substances chimiques agressives, avec une usure minimale au cours du temps. Fig.II.3 : Réacteur à disque tournant II.4- Réacteur à lit de garnissage rotatif (RPB) Les réacteurs centrifuges - souvent appelés les réacteurs à lit à garnissage rotatif (RPB) Ou les contacteurs Higee intensifient le transfert de masse en utilisant les effets d'un champ de gravité élevé. Le liquide est pulvérisé au diamètre intérieur du lit garni par un ensemble de buses bien réparties. La force centrifuge de la filature rotor accélère le liquide radialement vers l'extérieur et crée un film très mince de liquide à la surface du lit garni. Le gaz pénètre dans le logement fixe et traverse le rotor de l'extérieur vers l'intérieur. Un joint dynamique au sommet du rotor assure que le gaz se déplace à travers le lit garni. Un taux de conversion très élevé, presque exempt de sous-produits est causé par l'extrême court temps de rétention. Le champ de gravité élevé permet un temps de rétention court et fournit un contact intensif spontané entre le gaz et le liquide. L'espace d'installation requis, en particulier le la hauteur d'installation est seulement une fraction d'une tour traditionnelle. Lors de l'utilisation d'un alliage spécial matériaux, les coûts en capital de l'équipement peuvent être minimisés de manière significative. Pour la première fois, le lit de garnissage rotatif (RPB) a été mis en oeuvre dans des réactions d'hydrolyse biocatalytique. Le processus de forte intensification a amélioré le micro mélange du substrat et de la lipase, qui était fournie par la force centrifuge du RPB. Fig.II.4 : Réacteur à lit de garnissage rotatif (RPB) II.4- Extracteur centrifuge Un extracteur centrifuge, également appelé contacteur centrifuge ou contacteur centrifuge annulaire-utilise la rotation du rotor à l'intérieur pour mélanger deux liquides immiscibles à l'extérieur du rotor et à séparer les liquides dans le champ de gravité à l'intérieur du rotor. Un extracteur centrifuge génère une extraction continue d'une phase liquide dans une autre phase liquide. Deux liquides non miscibles de différentes densités sont alimentés et sont rapidement mélangés dans l'espace annulaire entre le rotor tournant et l’espace stationnaire. Les phases mixtes sont dirigées vers le centre du rotor par des ailettes radiales dans la base du boîtier. Comme les liquides pénètrent dans l'ouverture centrale du rotor, ils sont accélérés vers le mur. Les phases mixtes sont rapidement accélérées à la vitesse au rotor et la séparation commence lorsque les liquides sont déplacés vers le haut. Un système de déversoirs au sommet du rotor permet à chaque phase de sortir du rotor où elle atterrit dans un anneau collecteur et sort de la scène. Les contacteurs centrifuges agissent ainsi comme un mélangeur, une centrifugeuse et une pompe. Fig.5 : Les réacteurs échangeurs compacts Chapitre 3 : Les méthodes de l’Intensification des procédés III.1-Distillation réactive La distillation réactive est l’un des procédés chimiques intensifiés les plus reconnus, qui intègrent la séparation et la réaction au sein d’un même appareil. Les principaux avantages de la uploads/Finance/ cours-intensification-complet.pdf
Documents similaires
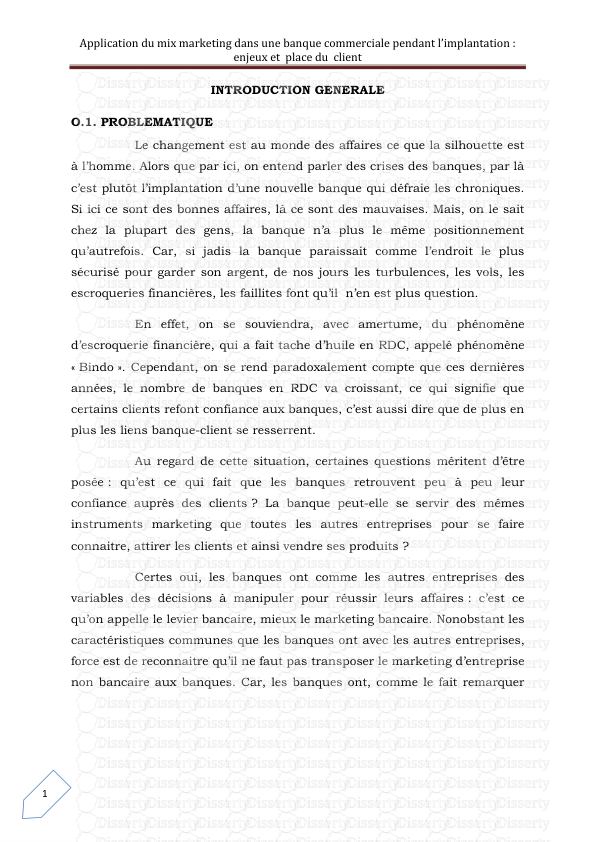
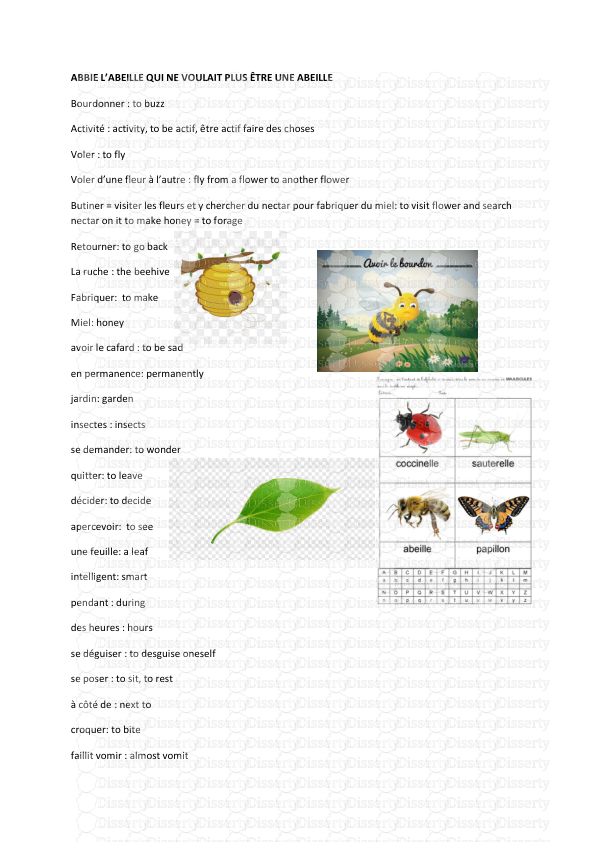
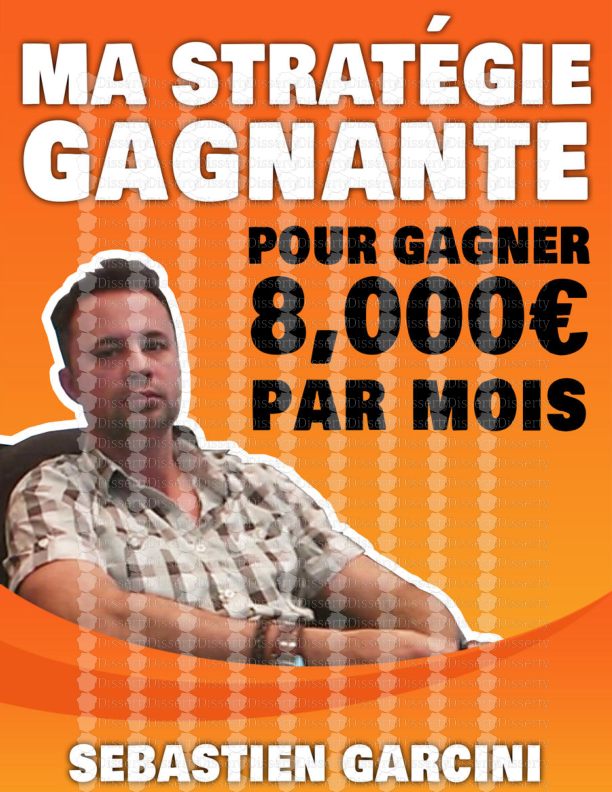
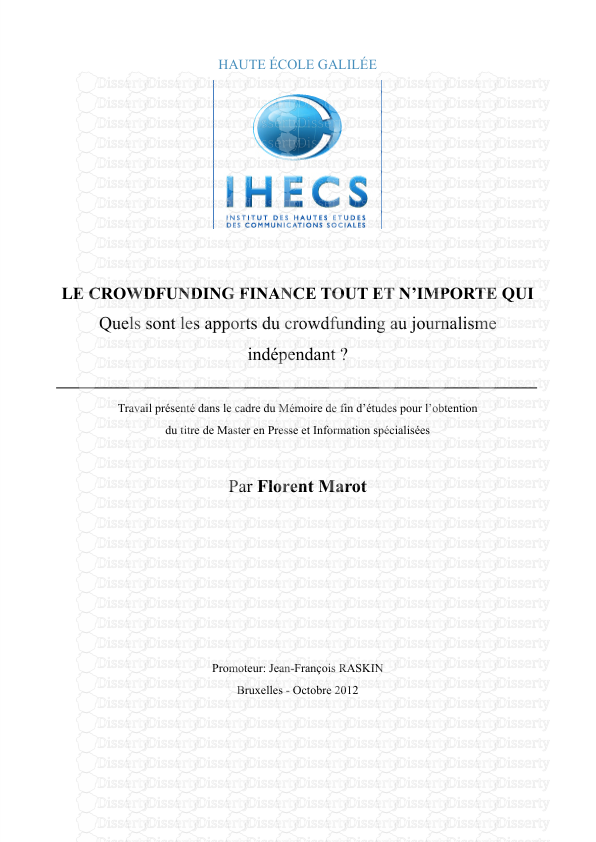
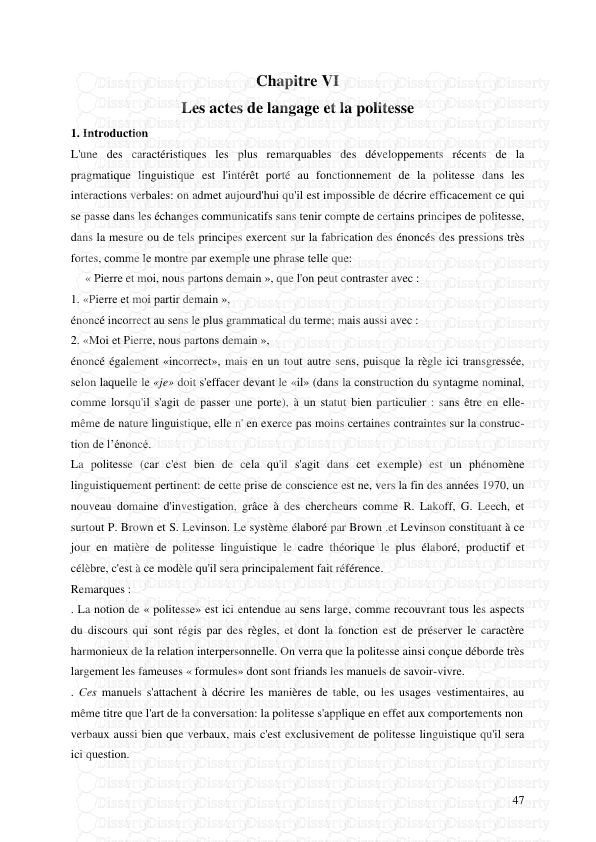
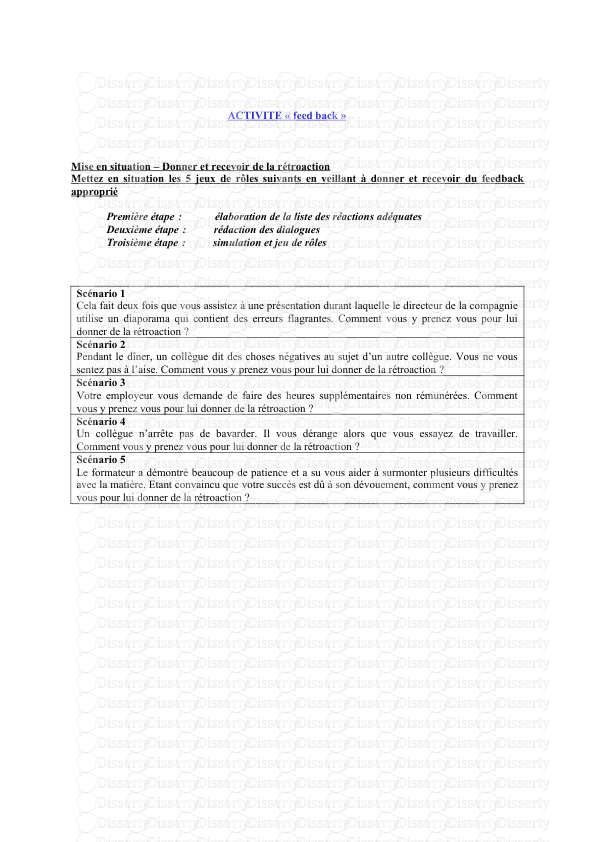
-
66
-
0
-
0
Licence et utilisation
Gratuit pour un usage personnel Attribution requise- Détails
- Publié le Jul 24, 2022
- Catégorie Business / Finance
- Langue French
- Taille du fichier 0.9212MB