Diagnostic rationnel en maintenance Mounir DRIDI Zénith Compétences 2021 2 CHAP
Diagnostic rationnel en maintenance Mounir DRIDI Zénith Compétences 2021 2 CHAPITRE 1 MAINTENANCE : ENJEUX ET STRATEGIES 1 - COUT DE LA NON-MAINTENANCE Les quelques exemples qui vont suivre sont souvent le fruit d’une expérience personnelle. Exemple n°1 : dégradation progressive de fonction La biscuiterie Y. fabrique des biscuits enrobés de chocolat. Celui-ci passe dans un tube où il est maintenu à une température lui permettant d’être suffisamment liquide pour enrober, à sa sortie du tube, les biscuits arri- vant sur un tapis roulant. Le chauffage du tube s’effectue grâce à une résistance, mais depuis quelques temps cette résistance montrait des signes de fatigue (le temps de chauffe était plus long). Personne ne s’en est inquiété jusqu’au jour où la résistance a lâché ; le chocolat, n’étant plus chauffé, a durci dans le tube. Conclusions : arrêt complet de la chaîne de fabrication, perte de la production en cours, démontage complet de l’installation pour nettoyage du tube alors que le changement préventif de la résistance n’aurait duré qu’un quart d’heure et n’aurait coûté que quelques Euros. Exemple n°2 : panne durable L’entreprise de Menuiserie Industrielle X s’arrête de travailler pendant 36 heures. Motif : les lignes de fabrication des portes et fenêtres manquent de matière première ! Explication : l’entreprise reçoit directement son bois de l’étranger (bois exotique) sous forme de troncs d’arbre. La première ligne de l’entreprise est dédiée au sciage des troncs sous forme de planches. Un cardan de la chaîne d’entraînement de la scie s’est rompu brusquement. Il n’y en avait pas en stock. La ligne de sciage est d’origine allemande. La pièce commandée est arrivée au bout de 24 heures. Et pourtant, cette panne avait déjà eu lieu !… Exemple n°3 : accident grave et image de marque dégradée Le directeur de l’entreprise Z. vient d’être lourdement condamné. Motif : un de ses ouvriers a eu le bras arraché par une des machines de l’unité de production. Cette machine n’était pas entretenue et n’était pas munie des organes de sécurité (ligne de vie) imposés par la législation. Outre la perte de production nécessitée par l’arrêt complet de l’atelier pour dégager l’ouvrier, les pénalités de retard à cause des retards de livraison ainsi que les sanctions financières pénales mettaient en très grosse difficulté l’entreprise (malgré un contrat d’assurance bien choisi). L’entreprise était, jusqu’à cet accident, jugée très performante. Son image de marque s’est brusquement dégradée. Il est difficile de dire, actuellement, si elle va s’en sortir. Exemple n°4 : maintenance mal effectuée Un employé brûlé par un jet de soude : un technicien condamné. Motif : Une erreur de raccordement lors de travaux sur un circuit de tuyauteries, et voici des douches alimen- tées à la soude et non plus à l’eau. La « gravité » de l’accident s’est trouvée limitée par le fait que l’ouvrier qui prenait sa douche avait fermé les yeux au moment où commençait à jaillir le liquide !… Le technicien respon- sable du raccordement et son responsable ont été condamnés à deux mois de prison avec sursis ainsi qu’à rembourser de très lourdes sommes à sa victime et à la Sécurité Sociale. Exemple n°5 : maintenance non effectuée Une personne ouvre la porte d’accès d’un ascenseur située au 13ème étage : elle tombe dans le vide et se tue. L’organisme gestionnaire de l’immeuble lourdement condamné. Motif : La maintenance de l’ascenseur n’avait pas été effectuée depuis quatre ans alors que la loi oblige une visite préventive tous les mois et le changement des organes de sécurité tous les six mois. La société civile Diagnostic rationnel en maintenance Mounir DRIDI Zénith Compétences 2021 3 immobilière gérant l’immeuble a invoqué pour sa défense le manque d’argent dû aux rentrées aléatoires des loyers et que la maintenance n’était pas une priorité !... Le directeur de la société a été condamné à une peine de prison ferme et à verser une prestation financière très lourde à la famille de la victime. Ces cinq exemples traduisent la non-efficacité de l’entreprise, parce que dans chaque cas, le chef d’entre- prise, les cadres techniques et administratifs n’avaient pas l’esprit maintenance. Dans quatre cas sur cinq, on a préféré subir la défaillance plutôt que la maîtriser. Pourquoi ? Très certainement à cause d’une politique à court terme : • l’entretien est une nécessité que le responsable de production subit en grinçant des dents, • le financier trouve que c’est trop coûteux (frais d’intervention, frais de personnel, stock de pièces détachées, etc..) et ne voit que ses échéances de fin de mois. Les derniers exemples traduisent l’ignorance du risque de la part des acteurs de l’entreprise. Les accidents du travail – tout comme les accidents de la route – n’arrivent pas qu’aux autres. Dans le troisième cas, il y a ignorance « volontaire » de la législation sur la sécurité de la part du chef d’entreprise. Dans le quatrième cas, c’est la répétition de gestes analogues, effectués dans des conditions analogues, qui conduit à des situations accidentelles ou quasi-accidentelles analogues. L’habitude mais aussi le travail dans l’urgence conduisent à des interventions non préparées, donc fatalement improvisées !... Dans le cinquième, c’est l’inconscience et la vue à court terme du directeur de la société gérante de l’immeuble qui entraîne un accident mortel. Les événements vécus en 1973 (guerre du Kippour) ont aussi aidé à un retour à la mentalité du manque et donc d’économie, d’où les catastrophes comme Seveso en 1976, Bhopal en 1984, etc.. A la fin du 20ème siècle on continue à oublier volontairement qu’un minimum d’entretien est nécessaire. C’est l’exemple de la privatisation du rail anglais en 1996 et ses accidents terribles de 1999 et 2001 qui se sont soldés par la mise sous tutelle administrative de la société Railtrack (responsable de l’infrastructure ferroviaire). L’accident de Paddington aurait pu être évité, ont conclu les experts, si un système de freinage automatique avait été installé et avait fonctionné. Pour l’ensemble des accidents, la sécurité est mise en accusation, mais on a préféré enrichir les actionnaires…. Dans ce contexte, la connaissance des mécanismes qui ont conduit à ce type de situations et des mesures prises pour les prévenir est fondamentale pour mettre en place, dans les usines, les services ou les immeubles, les procédures et conditions de travail propres à réduire les accidents. Cette non-efficacité coûte, on s’en doute, très cher à l’entreprise non seulement en terme financier mais aussi en terme de crédibilité. Pour diminuer cette non-efficacité, il est donc important de la situer. Pour cela, nous emprunterons à M. BOUCLY [6] un diagramme très significatif (figure 1.1 page suivante). Qui est inefficace ? • la production, car elle est responsable des micro-arrêts, des ralentissements, des arrêts pour changement d’outils, de production, • la maintenance si les arrêts pour entretien sont mal planifiés, si les dégradations de fonction sont ignorées, si les pannes durent trop longtemps, • les dirigeants qui n’ont pas su appréhender les problèmes de maintenance, qui n’ont pas su (ou voulu ?) investir en moyens humains compétents. Cependant, le concept de coût ne saurait justifier à lui seul le développement de la fonction Mainte- nance en entreprise. Nous retiendrons aussi la sécurité des biens et des personnes (industries nucléaires, aéronautiques, transports, etc..) et la notion de qualité si l’on se réfère à la norme ISO 9001 et à l’ISO 14000 pour l’environnement. Mais, les hommes de l’entreprise, en général, sont aussi responsables de l’inefficacité dès lors que les consignes d’utilisation des machines et de sécurité ne sont pas respectées. Alors comment faire ? C’est toute la problématique de l’entreprise d’aujourd’hui. 2 - PROBLEMATIQUE DE L’ENTREPRISE D’AUJOURD’HUI La fonction principale de l’entreprise, qu’elle soit industrielle ou de service, est de produire, mais selon trois objectifs techniques bien précis : • fonctionnalité des lignes de production ou des services (assurer les fonctions prévues), • performances (réaliser les fonctions avec les performances requises), • sûreté de fonctionnement (réaliser les fonctions quand on le désire et avec sécurité). Diagnostic rationnel en maintenance Mounir DRIDI Zénith Compétences 2021 4 CAUSES Avaries graves Pannes durables Microarrêts Ralentissements Dégradation de fonction Arrêt pour entretien Changement de série, d'outil CONSEQUENCES Dommages corporels et matériels Indisponibilité Perte de rendement Non qualité COÛTS Coûts des dommages Coûts des mesures palliatives Pénalités contractuelles Manque à gagner pour perte de production Coûts des stocks intermédiaires Coûts des équipements excédentaires Coûts de non qualité Incidences sur l'image de marque Figure 1.1 - Mise en évidence des coûts de non-efficacité Diagnostic rationnel en maintenance Mounir DRIDI Zénith compétences 2021 5 Si la fonctionnalité des lignes est liée directement à leur conception, leurs performances et leur sûreté de fonctionnement vont être fonction de l’environnement dans lequel elles vont travailler. Elles doivent donc bé- néficier d’un processus de soutien, au sens de la norme ISO 9001 : 2000, qu’on appelle « soutien logistique ». La Maintenance est par définition un processus de soutien de la Production. La volonté de conserver et d’entretenir les biens matériels ne date pas d’hier. En 97 ans après JC, Sextus Julius Frontimus, curateur des eaux à Rome, avait uploads/Industriel/ chap-1-enjeux-et-strategie.pdf
Documents similaires
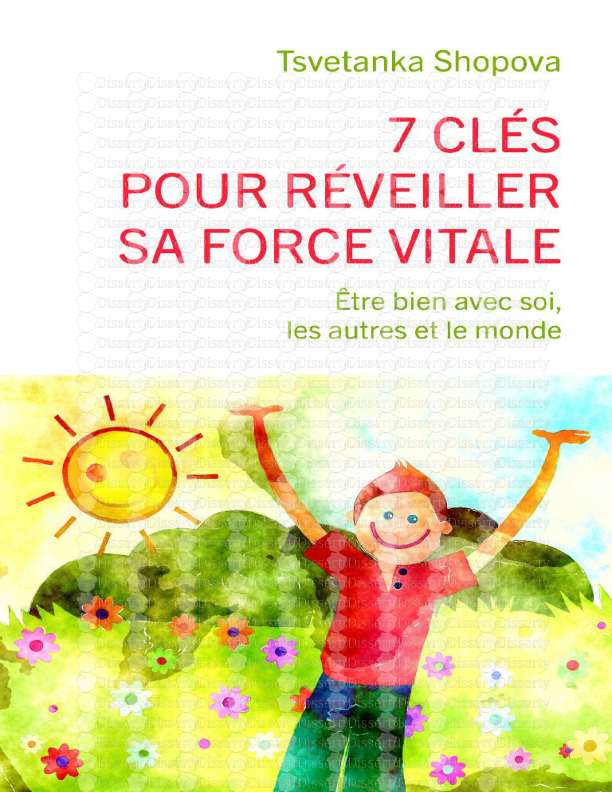

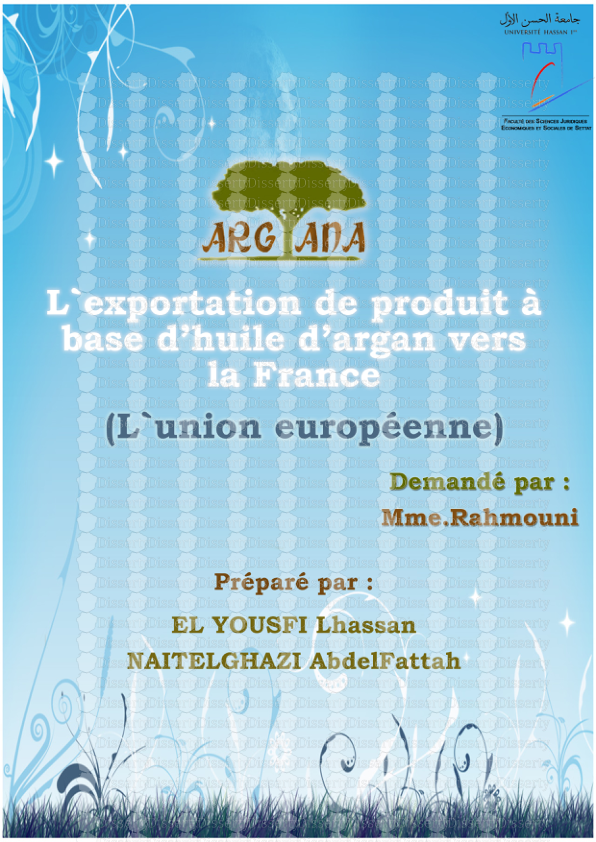
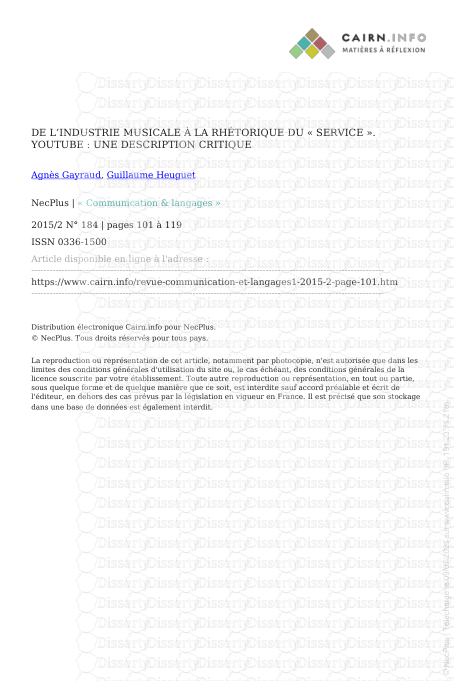
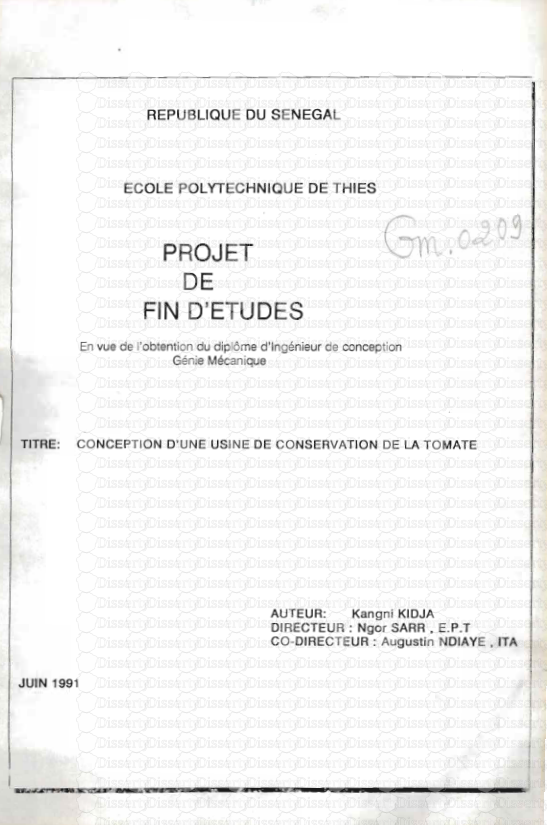
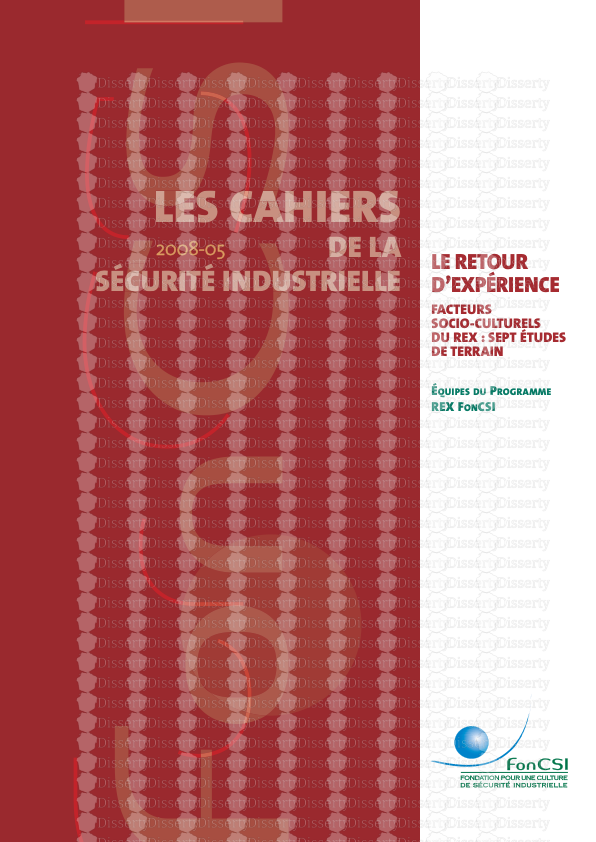
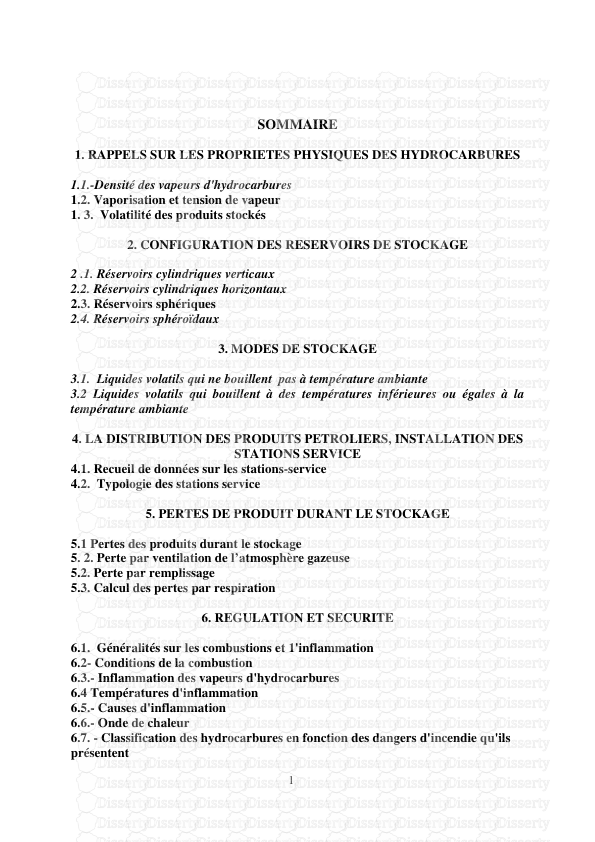
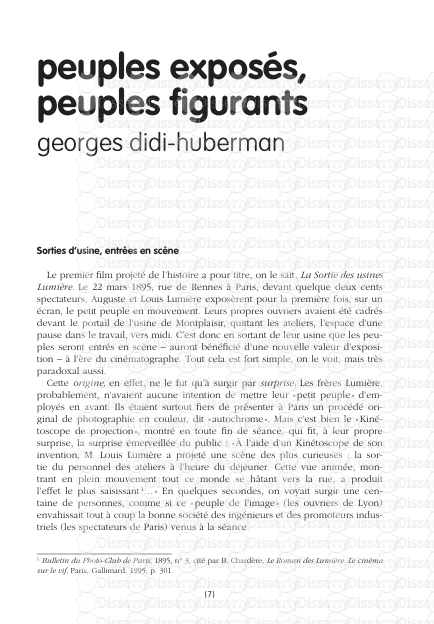
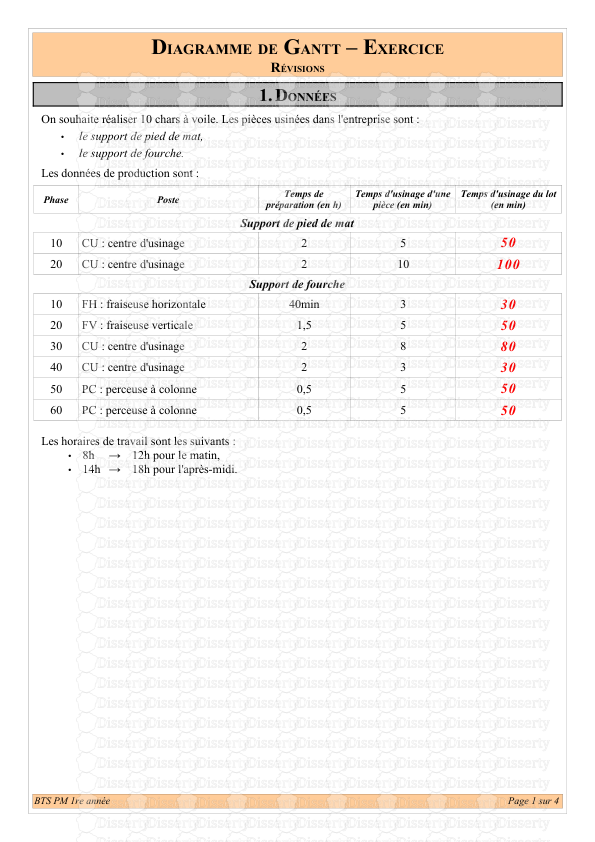

-
68
-
0
-
0
Licence et utilisation
Gratuit pour un usage personnel Attribution requise- Détails
- Publié le Fev 05, 2021
- Catégorie Industry / Industr...
- Langue French
- Taille du fichier 0.3406MB