Safe Machinery Handbook ™ 2 3 For more information call us on 0870 608 8 608 or
Safe Machinery Handbook ™ 2 3 For more information call us on 0870 608 8 608 or visit www.schneider-electric.co.uk Introduction. ........................................................4 Why safety?.........................................................6 Legal framework.............................................10 Risk assessment..............................................16 Safe design and safeguarding...................22 Functional Safety. ...........................................30 Control system standards including worked examples........................38 Sources of information. ................................56 Annexes - architectures...............................58 Contents 4 Introduction 5 There are various guides to machinery safety legislation which tend to present a distorted view of the requirements of that legislation. This handbook is an attempt to provide information that is up-to-date and unbiased in order to help machine builders and users to provide workers with machines that are safe, legal, and efficient. It is not intended as an exhaustive guide to compliance with safety legislation, nor as a replacement for referring to the relevant standards themselves; it is to guide you through the logical steps and to point you to the relevant sources of information. 6 Why safety 7 As well as the moral obligation to avoid harming anyone, there are laws that require machines to be safe, and sound economic reasons for avoiding accidents. Safety must be taken into account right from the design stage and must be kept in mind at all stages in the life of a machine: design, manufacture, installation, adjustment, operation, maintenance and eventual scrapping. New machines - the Machinery Directive In the UK, at present the Machinery Directive 98/37/EC is implemented as the Supply of Machinery (safety) regulations 1992 as amended. From 29 December 2009 the relevant UK regulations will be the Supply of Machinery (safety) regulations 2008, which implement the European Machinery Directive 2006/42/EC. Machines have to comply with the Essential Health and Safety Requirements (EHSRs) listed in Annex I of the Directive, thus setting a common minimum level of protection across the EEA (European Economic Area). Machine manufacturers, or their authorised representatives within the EU, must ensure that the machine is compliant, the Technical File can be made available to the enforcing authorities on request, the CE marking is affixed, and a Declaration of Conformity has been signed, before the machine may be placed on the market within the EU. Design/manufacture Installation Adjustment/operation Maintenance 8 Existing machines – the Work Equipment Directive This is implemented in UK law as the Provision and use of Work Equipment Regulations 1998 (PUWER 1998). It applies to the provision of all work equipment, including mobile and lifting equipment, in all workplaces and work situations where the Health and Safety at Work etc Act 1974 (HSW Act) applies, and extends outside Great Britain to some offshore activities. They require that all equipment is suitable for use, and is inspected and maintained as necessary to ensure that it remains so. The cost of accidents Some of the costs are obvious, such as sick pay for injured employees, whereas some costs are harder to identify. The Health and Safety Executive (HSE) give an example of an accident at a drilling machine that resulted in costs to the business of £45 000 (HSE INDG355). However this does not include some of the less obvious costs, and some estimates amount to double that figure. An accident analysed by Schneider Electric Ltd, the outcome of which was a reversible head injury, cost the employer some £90 000, of which only £37 000 was insurable. The full financial impact can include increase in insurance premiums, lost production, lost customers and even loss of reputation. Some risk reduction measures can actually increase productivity; for example the use of light curtains to protect access points of machines can allow easier access for loading and unloading; zoning of isolation devices can allow parts of a machine to be shut down for maintenance while other parts remain productive. The regulations apply to all employers, the self-employed, and others who have control of the provision of work equipment. 9 9 10 10 Legal framework 11 Presumption of conformity: When a product conforms to a harmonised European standard, the reference to which has been published in the Official Journal of the European Union for a specific Directive, and which covers one or more of the essential safety requirements, the product is presumed to comply with those essential safety requirements of the Directive. A list of such standards can be accessed at http://www.newapproach.org/Directives/DirectiveList.asp EC Directive: Legal instrument to harmonise the legislation of the European member states Defines the essential health and safety requirements (EHSRs) Transposed into national law (act, decree, order, regulations) Standard: A “standard” is a technical specification approved by a recognised standardisation body for repeated or continuous application, with which compliance is not compulsory Harmonised standard: A standard becomes harmonised when published throughout the member states It is of course necessary to ensure compliance with all the other EHSRs as well as those for which a Presumption of Conformity is given by the use of a specific standard. 12 A B & C standards: European standards for the Safety of machinery form the following structure: A B1 B2 C Type A standards (Basic safety standards) giving basic concepts, principles for design, and general aspects that can be applied to all machinery; Type B standards (Generic safety standards) dealing with one safety aspect or one type of safeguard that can be used across a wide range of machinery: - Type B1 standards on particular safety aspects (e.g. safety distances, surface temperature, noise); - Type B2 standards on safeguards (e.g. two-hand controls, interlocking devices, pressure sensitive devices, guards); Type C standards (Machine safety standards) dealing with detailed safety requirements for a particular machine or group of machines. 13 EN ISO 12100 A Safety of machinery - General principles for design - Risk assessment and risk reduction EN 574 B Safety of machinery - Two-hand control devices - Functional aspects - principles for design EN ISO 13850 B Safety of machinery - Emergency stop - Principles for design EN 62061 B Safety of machinery - Functional safety of safety-related electrical, electronic and programmable electronic control systems EN ISO 13849-1 B Safety of machinery - Safety-related parts of control systems - Part 1: general principles for design EN 349 B Safety of machinery - Minimum gaps to avoid crushing of parts of the human body EN ISO 13857 B Safety of machinery - Safety distances to prevent hazard zones being reached by upper and lower limbs EN 60204-1 B Safety of machinery - Electrical equipment of machines - Part 1: general requirements EN ISO 13855 B Safety of machinery - Positioning of safeguards in respect of approach speeds of parts of the human body EN 1088 B Safety of machinery - Interlocking devices associated with guards - Principles for design and selection EN 61496-1 B Safety of machinery - Electro-sensitive protective equipment. Part 1: General requirements and tests EN 60947-5-5 B Low-voltage switchgear and control gear - Part 5-5: Control circuit devices and switching elements - Electrical emergency stop device with mechanical latching function EN 842 B Visual danger signals - General requirements, design and testing EN 1037 B Prevention of unexpected start-up EN 953 B General requirements for the design and construction of fixed and movable guards EN 201 C Plastics and rubber machines - Injection moulding machines - Safety requirements EN 692 C Machine Tools - Mechanical presses - Safety EN 693 C Machine Tools - Safety - Hydraulic presses EN 289 C Plastics and rubber machines – Presses - Safety requirements EN 422 C Plastics and rubber machines - Blow moulding machines - Safety requirements EN ISO 10218-1 C Robots and robotic devices - Safety requirements for industrial robots - Part 1: Robots EN 415-3 C Safety of packaging machines - Part 3: Form, fill and seal machines EN 619 C Continuous handling equipment and systems - Safety and EMC requirements for equipment for mechanical handling of unit loads EN 620 C Continuous handling equipment and systems - Safety and EMC requirements for fixed belt conveyors for bulk materials When a Type-C standard deviates from one or more provisions dealt with by a Type A standard or by a Type B standard, the Type C standard takes precedence. BS EN ISO 12100 -1, 12100-2, and 14121-1 are Type A standards. Some examples of these types of standards are: 14 Acts of parliament (primary legislation) An Act of Parliament creates a new law or changes an existing law. An Act is a Bill approved by both the House of Commons and the House of Lords and formally agreed to by the reigning monarch (known as Royal Assent). Once implemented, an Act is law and applies to the UK as a whole or to specific areas of the country. An Act may come into force immediately, on a specific starting date, or in stages. The practical implementation of an Act is the responsibility of the appropriate government department, not Parliament. For example, laws relating to transport issues would come under the administration of the Department for Transport. Delegated or secondary legislation Delegated or secondary legislation allows the Government to make changes to a law without needing to push through uploads/Industriel/ machine-safety-guide.pdf
Documents similaires
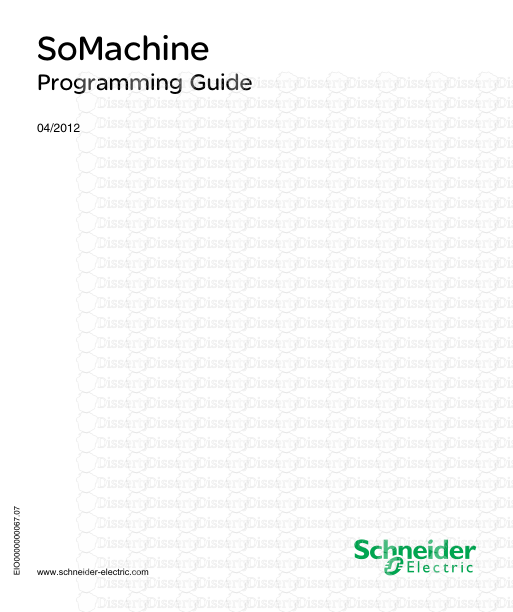
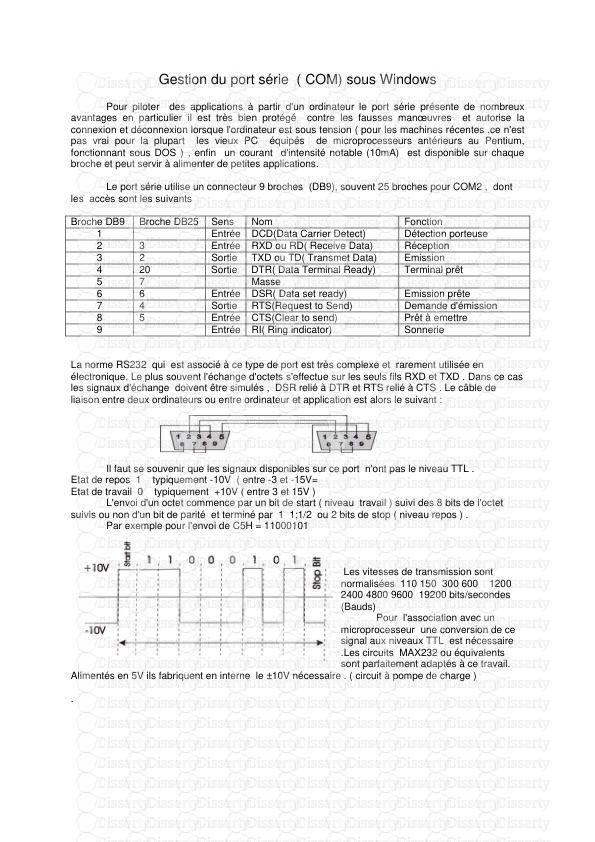
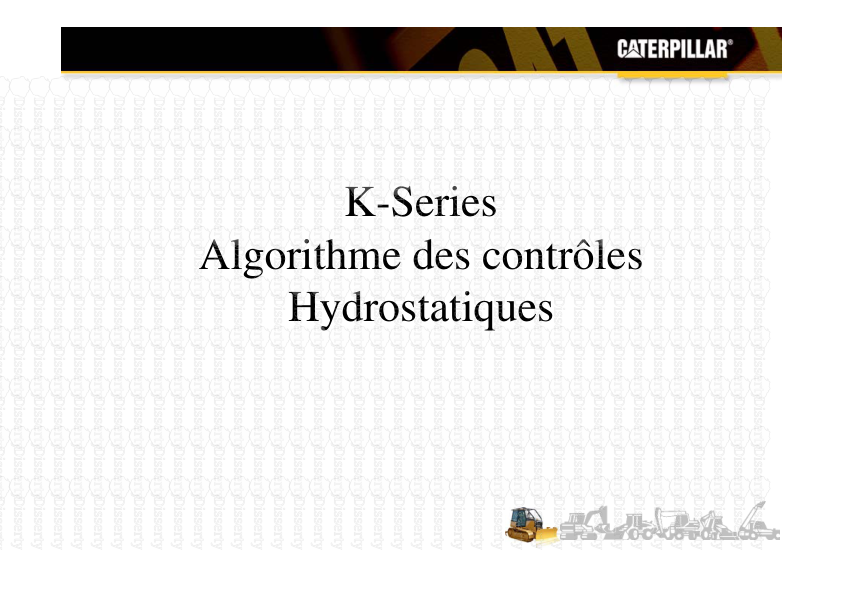
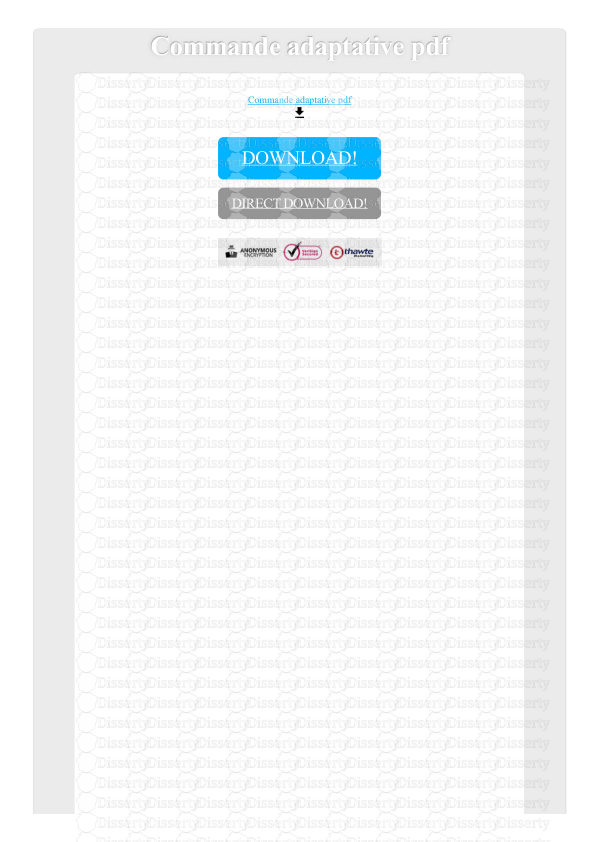
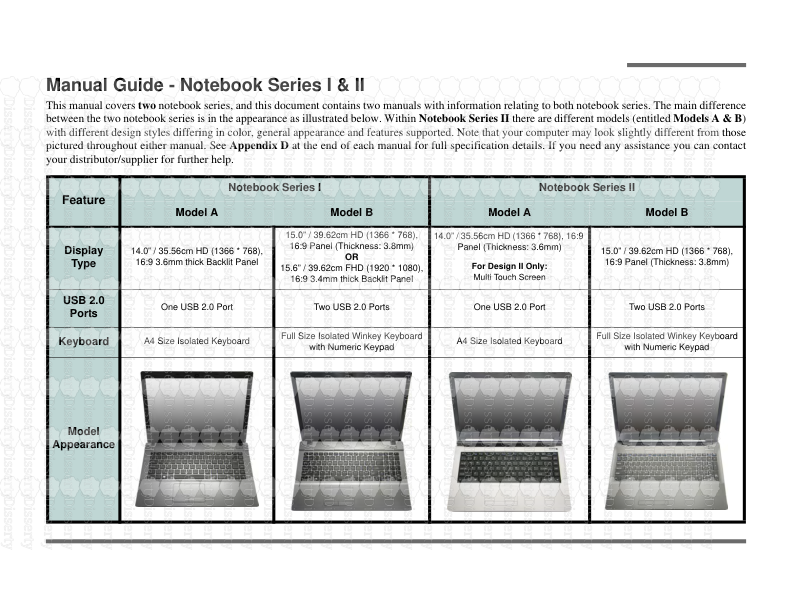
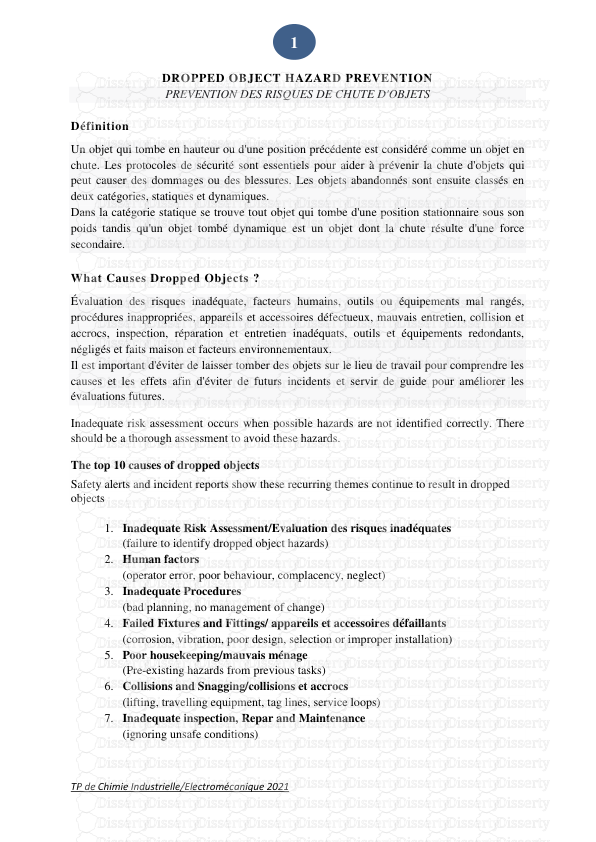
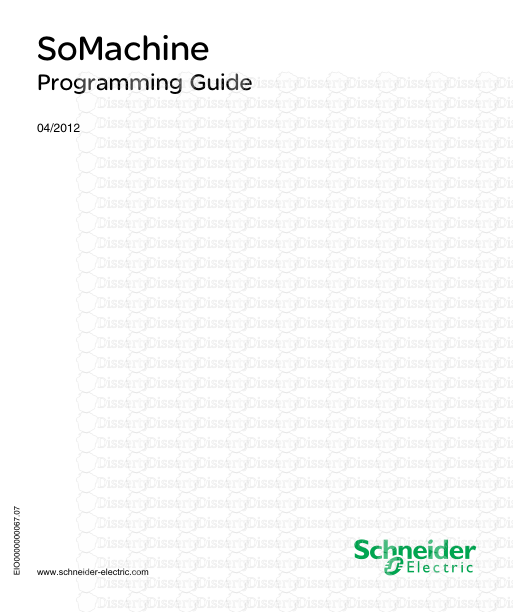
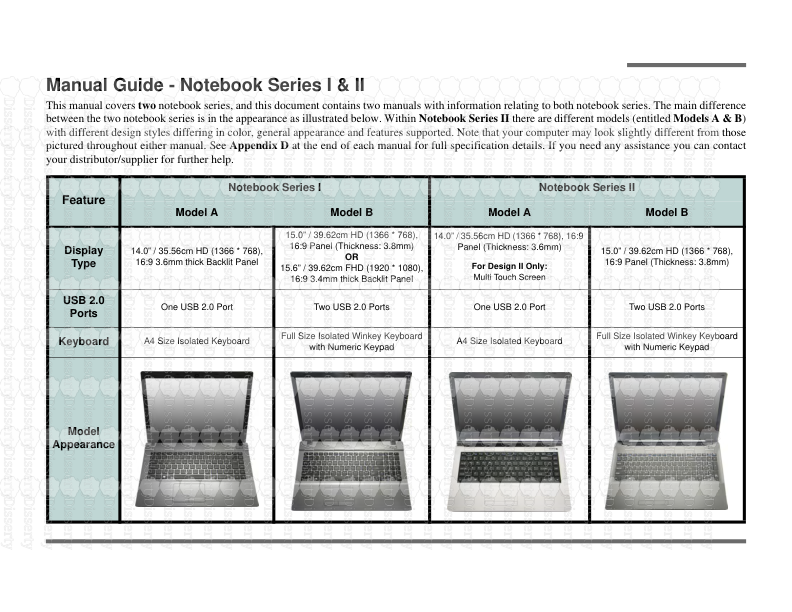
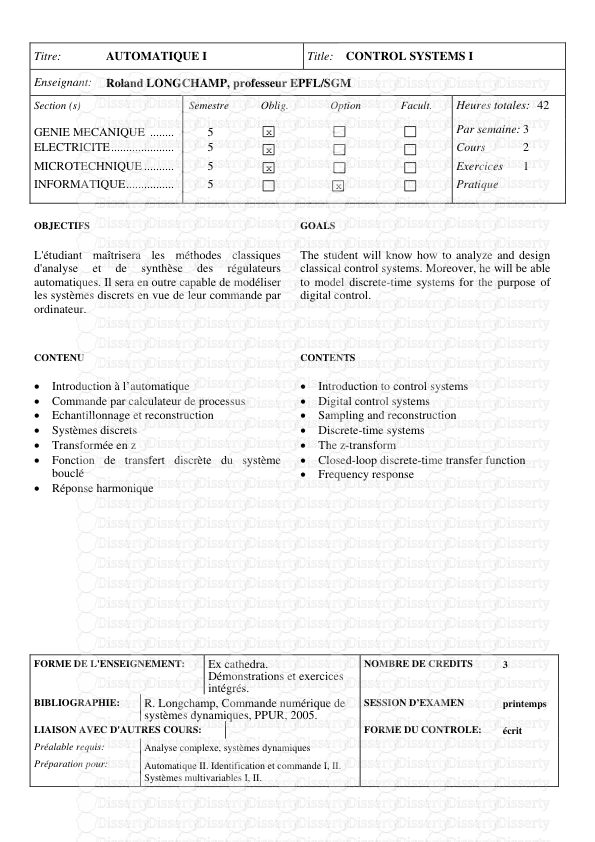
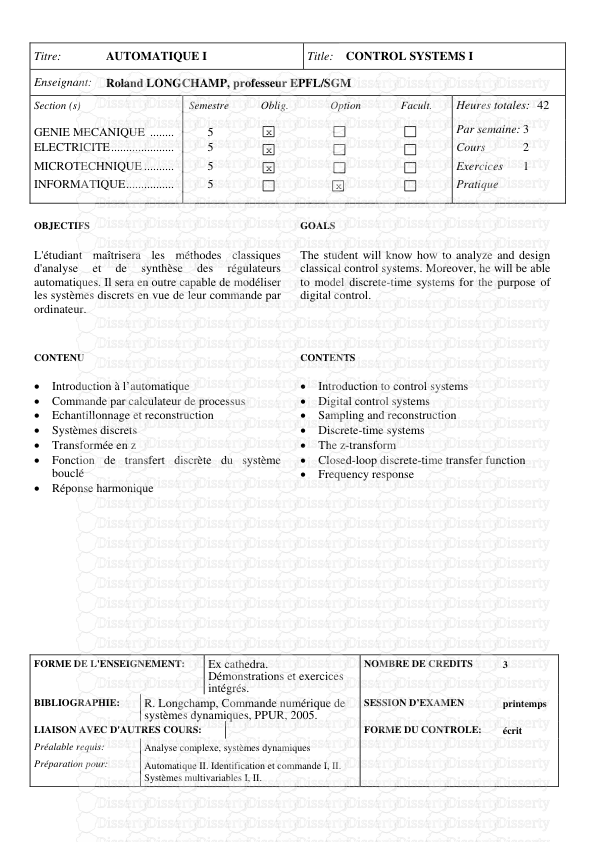
-
35
-
0
-
0
Licence et utilisation
Gratuit pour un usage personnel Attribution requise- Détails
- Publié le Jui 26, 2021
- Catégorie Industry / Industr...
- Langue French
- Taille du fichier 2.8202MB