Éléments d’usinage et métrologie dimensionnelle / TEC 040 Hiver 2009 i 1 Procéd
Éléments d’usinage et métrologie dimensionnelle / TEC 040 Hiver 2009 i 1 Procédés d’usinage par enlèvement de copeaux ...................................................1-1 1.1 Historique de l’usinage par enlèvement de copeaux .........................................1-1 1.2 Les outils de coupe............................................................................................1-4 1.3 Usinabilité des matériaux ..................................................................................1-5 1.4 Fluides de coupe ...............................................................................................1-6 1.5 Procédés conventionnels d’usinage par enlèvement de copeaux .....................1-7 1.5.1 Sciage .......................................................................................................1-7 1.5.2 Perçage.....................................................................................................1-8 1.5.3 Tournage.................................................................................................1-11 1.5.4 Fraisage ..................................................................................................1-13 1.5.5 Rectification.............................................................................................1-17 1.5.6 Brochage.................................................................................................1-19 1.6 Règles de sécurité...........................................................................................1-21 2 Machines-outils à commande numérique ...............................................................2-1 2.1 Historique ..........................................................................................................2-1 2.2 Aspect économique...........................................................................................2-4 2.3 Comparaison avec les machines-outils conventionnelles..................................2-4 2.4 Comment fonctionne une machine-outil CNC?..................................................2-5 2.5 Système de coordonnées des machines CNC ..................................................2-6 2.5.1 Axes d’une fraiseuse .................................................................................2-6 2.5.2 Axes d’un tour ...........................................................................................2-7 2.5.3 Mouvements d’usinage combinés .............................................................2-7 2.6 Types de Machines ...........................................................................................2-7 2.7 Code G..............................................................................................................2-8 2.8 Décalage des outils .........................................................................................2-11 2.8.1 Le décalage d’outil sur un tour ................................................................2-11 2.8.2 Le décalage d’outil sur la fraiseuse .........................................................2-11 3 Introduction à l’usinage selon les spécifications du dessin .....................................3-1 3.1 Le dessin technique...........................................................................................3-1 3.2 Définitions..........................................................................................................3-3 3.3 Principes de base du dessin technique .............................................................3-5 3.3.1 La cotation.................................................................................................3-5 3.3.2 Les projections ..........................................................................................3-7 3.4 Introduction aux gammes de fabrication............................................................3-9 Éléments d’usinage et métrologie dimensionnelle / TEC 040 Hiver 2009 ii 3.4.1 Outils en fonction de l’opération ..............................................................3-10 3.4.2 Paramètres d’usinage..............................................................................3-10 4 Le phénomène de variation dans le cycle de vie du produit (conception, fabrication, assemblage et inspection)....................................................................4-1 4.1 La norme ASME Y 14.5M-1994.........................................................................4-2 4.2 Pourquoi une tolérance? ...................................................................................4-2 4.3 Quelques principes de base du tolérancement..................................................4-3 4.4 Tolérances dimensionnelles..............................................................................4-4 4.5 Les Datums .......................................................................................................4-6 4.5.1 Les six (6) degrés de liberté ......................................................................4-6 4.5.2 Système 1 : Plan – Plan - Plan..................................................................4-6 4.5.3 Système 2 : Plan – Axe – plan central.......................................................4-7 4.5.4 Référentiel double .....................................................................................4-9 4.5.5 Référentiel ciblé (Datum Targets)............................................................4-10 4.6 Les tolérances géométriques...........................................................................4-12 4.6.1 Planéité ...................................................................................................4-13 4.6.2 Circularité ................................................................................................4-13 4.6.3 Rectitude .................................................................................................4-14 4.6.4 Cylindricité...............................................................................................4-14 4.6.5 Profil d’une ligne......................................................................................4-15 4.6.6 Profil de surface.......................................................................................4-15 4.6.7 Localisation (position)..............................................................................4-16 4.6.8 Coaxialité.................................................................................................4-17 4.6.9 Concentricité ...........................................................................................4-17 4.6.10 Symétrie ..................................................................................................4-18 4.6.11 Angularité ................................................................................................4-18 4.6.12 Parallélisme.............................................................................................4-19 4.6.13 Perpendicularité.......................................................................................4-19 4.6.14 Alignement simple ...................................................................................4-20 4.6.15 Alignement total.......................................................................................4-20 4.7 Cumul des tolérances......................................................................................4-21 5 Analyse des variations dans un assemblage mécanique........................................5-1 5.1 Étapes pour la chaînes de cotes .......................................................................5-1 5.1.1 Identifier le requis fonctionnel....................................................................5-2 5.1.2 Identifier les composantes impliquées.......................................................5-2 5.1.3 Choisir l’origine et la direction....................................................................5-2 5.1.4 Construire la chaîne de cotes....................................................................5-3 5.1.5 Analyse des composantes.........................................................................5-3 5.2 Transfert de cotes..............................................................................................5-4 5.3 Ajustements fonctionnels normalisés ................................................................5-6 5.4 Exercices...........................................................................................................5-7 6 Introduction à la métrologie.....................................................................................6-1 6.1 Principes de base..............................................................................................6-1 Éléments d’usinage et métrologie dimensionnelle / TEC 040 Hiver 2009 iii 6.1.1 L’inspection manuelle................................................................................6-1 6.1.2 L’inspection automatisée...........................................................................6-2 6.1.3 Les erreurs de mesure ..............................................................................6-2 6.2 Appareils de mesure..........................................................................................6-3 6.3 Étalonnage (Calibration) – Confirmation métrologique......................................6-5 6.3.1 Terminologie..............................................................................................6-5 6.3.2 Les étalons dimensionnels industriels (cales étalons)...............................6-7 6.3.3 Utilisation des cales étalons ......................................................................6-8 6.3.4 Précision des cales étalons dimensionnels ...............................................6-8 6.3.5 Principes d'utilisation.................................................................................6-9 6.3.6 Soins des cales étalons...........................................................................6-10 7 Références bibliographiques ..................................................................................7-1 Éléments d’usinage et métrologie dimensionnelle / TEC 040 Hiver 2009 1-1 1 1 Procédés d’usinage par enlèvement de copeaux Parmi les procédés de mise en forme des matériaux métalliques, l’usinage par enlèvement de copeaux est un des plus performants et précis. Nous allons donc effectuer une revue des différents procédés associés à ce mode de mise en forme et des outils de coupe associés. Le principe de l'usinage est d'enlever de la matière de manière à donner à la pièce brute la forme voulue, à l'aide d'une machine-outil. Ainsi, les pièces obtenues sont d'une grande précision et il est possible de les fabriquer en grand nombre. Lors de l'usinage d'une pièce, l'enlèvement de matière est réalisé par la conjonction de deux mouvements relatifs entre la pièce et l'outil : le mouvement de coupe (vitesse de coupe) et le mouvement d'avance (vitesse d'avance). Il existe deux manières de générer la surface recherchée : - travail de forme: c'est la forme de l'outil qui conditionne la surface finalement obtenue; - travail d'enveloppe: c'est la trace de l'arête de l'outil qui travaille (le point générateur) qui donne la surface finale. 1.1 Historique de l’usinage par enlèvement de copeaux Les développements principaux associés à ce mode de mise en forme sont relativement récents, ayant évolué de paire avec la révolution industrielle du 18ème et du 19ème siècle, pour connaître une accélération importante durant le 20ème siècle. Durant les débuts de ce procédé de fabrication, la principale limitation était causée par l’absence d’une source énergie essentielle au fonctionnement des machines. Ainsi, l’usinage était réalisé de manière manuelle par les forgerons, ce qui en faisait un procédé lent et peu efficace, les outils de coupe étaient alors tenus à la main, comme le montre la figure 1-1. De plus, tel que le démontre la figure 1-2, la principale source de puissance était humaine. On peut en effet apercevoir la manivelle utilisée pour entraîner en rotation le tour et la poignée utilisée pour déplacer l’outil de l’étau limeur. 1 Tiré et adapté des notes du cours MEC722 Éléments d’usinage et métrologie dimensionnelle / TEC 040 Hiver 2009 1-2 Puis, l’apparition et l’exploitation de sources de puissance comme la vapeur et l’énergie hydraulique a permis un pas de géant des capacités des machines-outils. La puissance était alors acheminée par des arbres de transmission et des courroies plates jusqu’aux machines, tel qu’illustré à la figure 1-3. Maintenant qu’on disposait d’une puissance adéquate pour les machines, il fallait développer des matériaux pour les outils de coupe capable de résister aux efforts et aux températures générés par l’usinage. En effet, avec l’apport de puissance adéquate, la limitation des procédés d’usinage était maintenant associée aux outils de coupe. Le premier matériel utilisé pour la fabrication d’outils de coupe était l’acier au carbone, qui était mis en forme par un forgeron, sur une enclume, pour ensuite être trempé. Toutefois, pour que l’outil conserve sa trempe, il fallait limiter la température que devait supporter l’outil durant l’usinage, ce qui exigeait des vitesses de coupe lente et prohibait l’usinage de tout matériau dur. Figure 1-1: Outils retenus à la main Figure 1-2: Source de puissance manuelle Éléments d’usinage et métrologie dimensionnelle / TEC 040 Hiver 2009 1-3 Figure 1-3: Machine alimentée par courroies La découverte de l’acier Mushet, de manière accidentelle, a permis de hausser les vitesses de coupe jusqu'à 30 pieds à la minute (sfm, surface feet per minute) et d’usiner des métaux plus dur. En effet, des expérimentations sur le manganèse a conduit aux aciers trempables à l’air et à la découverte de tungstène dans l’acier, ce qui a permis de doubler la productivité en tournage grâce à ce nouvel alliage. Puis Frederick Taylor est venu révolutionner le mode de l’usinage durant l’exposition universelle de Paris en 1900. Il a usiné de l’acier à une vitesse de coupe incroyable à l’époque, soit 120sfm, et générait ce qui n’avait jamais été vu alors, des copeaux bleus, à cause de la vitesse de coupe atteinte. Ces démonstrations ont amené une destruction complète du tour qu’il utilisait en moins de 1 mois, les machines de l’époque n’étant pas conçues pour résister aux efforts et aux vitesses associées à ce type d’usinage. On venait donc d’assister à la première utilisation de l’acier rapide (HSS, High Speed Steel) pour les outils de coupe. Puis en 1915 est apparu le « cast alloy » comme matériau pour les outils de coupe, un alliage à base de tungstène, de cobalt et de chrome. Cet alliage pouvait supporter jusqu’à 800oC sans perte appréciable de dureté, ce qui en faisait un outil de coupe très performant à l’époque. Grâce aux nouvelles possibilités offertes par ces nouveaux outils de coupe, les fabricants de machines outils on conçu des machines de plus grande capacité, plus précises et puissante, tel qu’illustré à la figure 1-4. Puis sont apparus, durant les années 30, les carbures cémentés, augmentant encore les performances des procédés d’usinage. A titre d’exemple, une pièce typique qui prenait 100 minutes à usiner avec des outils en acier au carbone n’en prenait que 26 avec des outils en HSS, avec des outils en « cast alloy » et 6 minutes avec les carbures cémentés. Éléments d’usinage et métrologie dimensionnelle / TEC 040 Hiver 2009 1-4 Figure 1-4: Fraiseuse de grande dimension – années 30 1.2 Les outils de coupe C’est principalement l’évolution des outils de coupe qui a permis l’évolution des procédés d’usinage. Au début du 20e siècle, les outils en acier au carbone étaient les plus populaires. Ensuite le HSS (High Speed Steel) est apparu et, de nos jours, le substrat des outils de coupe avec plaquettes est toujours en carbure, mais les améliorations se font au niveau du revêtement des plaquettes (tungstène, manganèse céramiques, etc.), permettant d’augmenter les vitesses de coupe par les capacités réfractaires et lubrifiantes de ces revêtements. Figure 1-5: Outils au carbure Éléments d’usinage et métrologie dimensionnelle / TEC 040 Hiver 2009 1-5 Figure 1-6: Effet de l'évolution des outils sur la capacité de production Le choix de l’outil de coupe a une très grande influence sur l’usinage des pièces. Voici les principaux facteurs à tenir compte lors du choix d’un outil : • L’opération : ébauche vs finition, tolérance, etc. • La forme de la uploads/Industriel/ notes-de-cours-tch040-h2011.pdf
Documents similaires

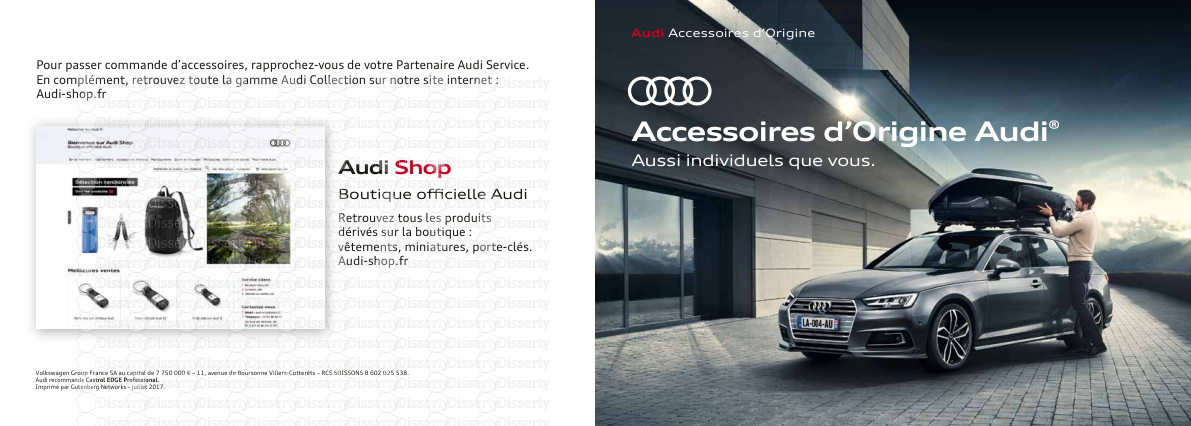

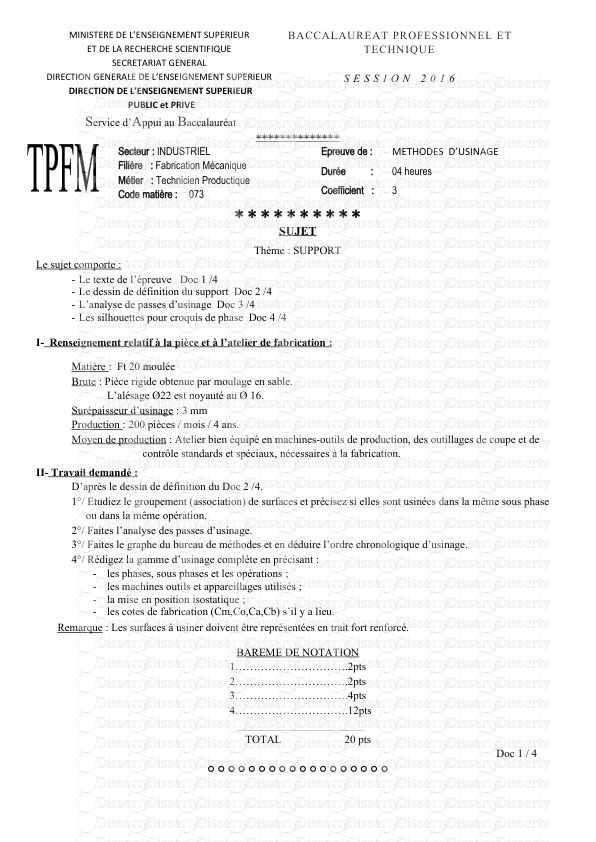
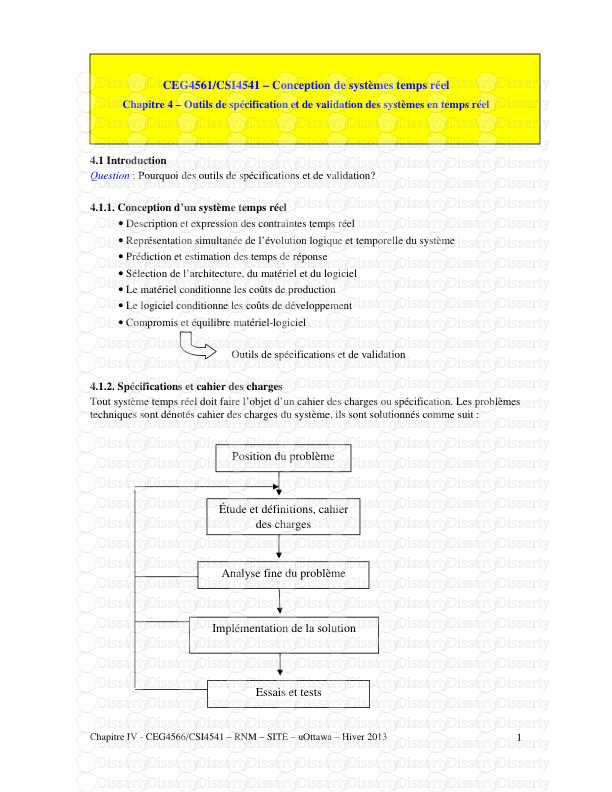
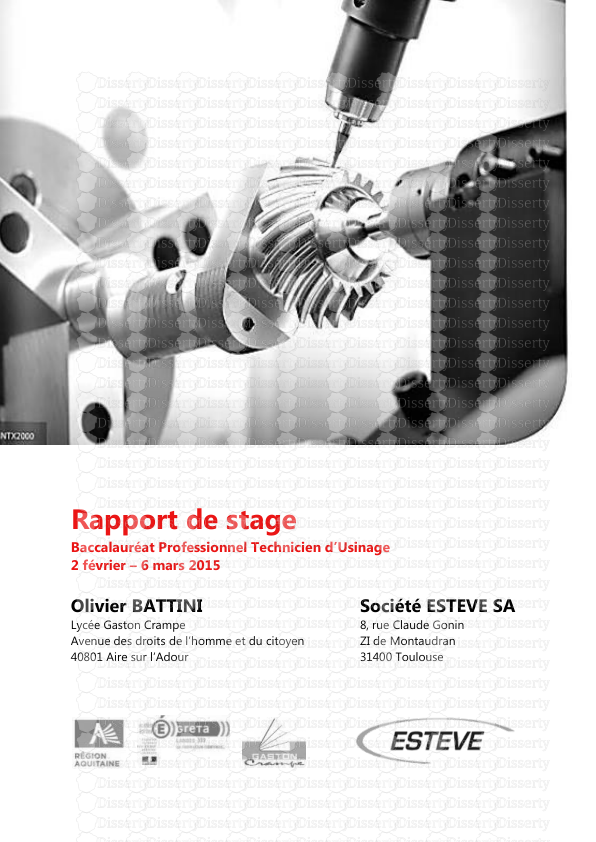
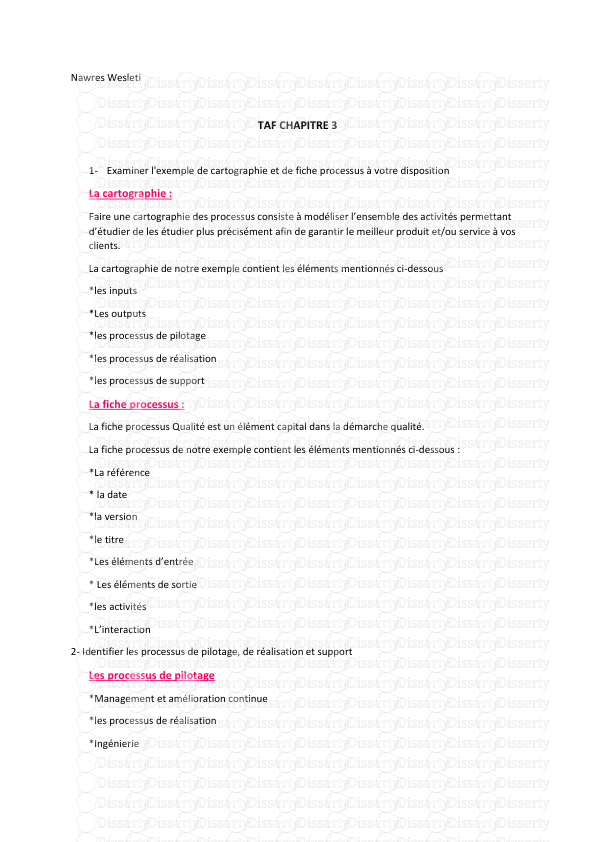
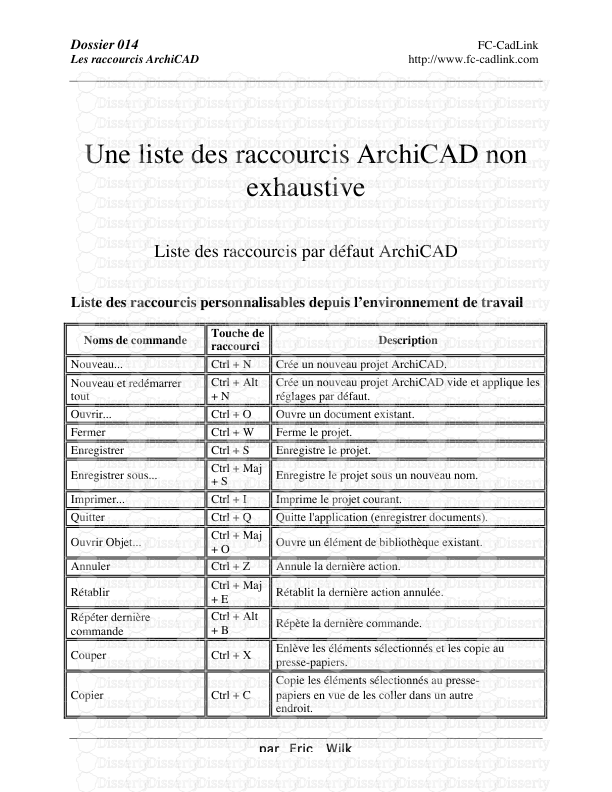
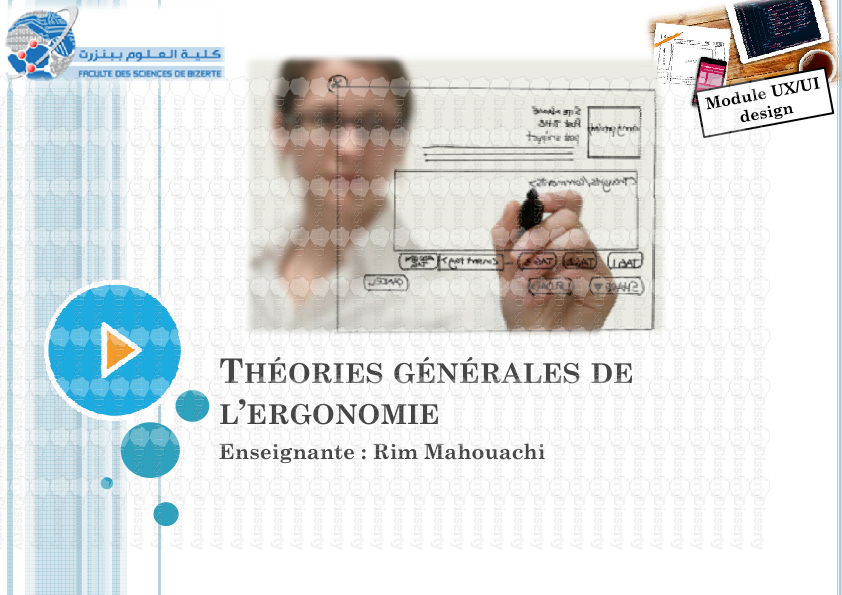
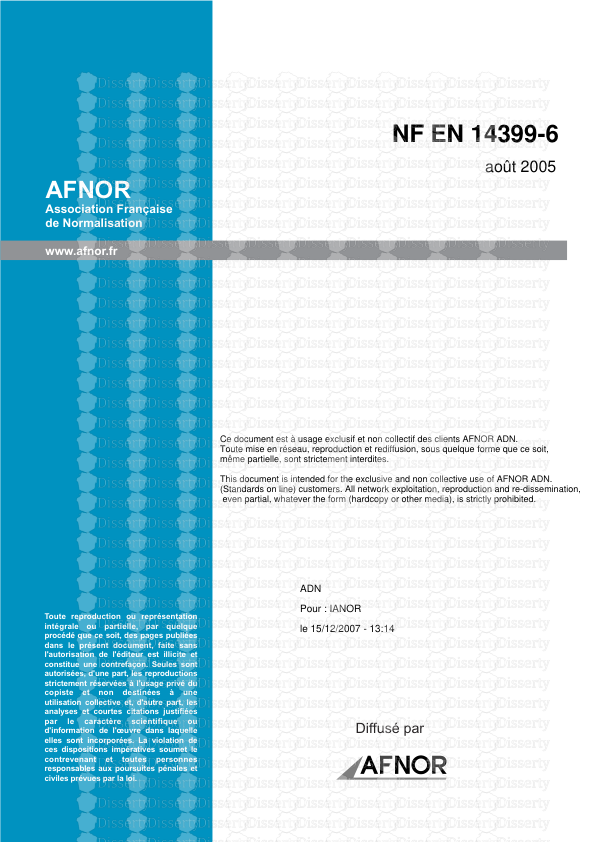
-
41
-
0
-
0
Licence et utilisation
Gratuit pour un usage personnel Attribution requise- Détails
- Publié le Jan 25, 2022
- Catégorie Industry / Industr...
- Langue French
- Taille du fichier 2.8525MB