Le système Jidoka Base JIT Bon produit bonne qualité bon délai - Kan ban - Takt
Le système Jidoka Base JIT Bon produit bonne qualité bon délai - Kan ban - Takt time - Flux tiré - 01 pièce flux - VSM - TPM - SMED - TPM Personnel Travail d’équipe - Objectifs communs - OJT - Responsabilité - Reconnaissance R. Problème - Sangentshugui - 05 pourquoi Jdoka Produire la qualité - Stop au 1er défaut - Bon du 1er coup - Andon - Poka Yoke - Autonomie - Contrôle au poste - Réactivité rapide QR Heijunka - Nivelage de la demande - Produire pour livrer - Gestion de stock Coût- Qualité- OTD- Sécurité- Etique Satisfaction Client Efficacité Opérationnelle Travail standardisé - 05 S - Gestion visuelle - Instruction de travail Kaizen/Kaikaku - Elimination Muda - PDCA/FTA - Rapport A3 Piliers Objectifs Orientation Le Temple du Lean Avant Kaizen Après Kaizen Système Anti erreur Le système anti-erreurs évite un montage à l’envers de la pièce Pièce montée à l’envers Buté Le système anti-erreurs (humain & mécanique) nécessaire pour la mise en place du principe Jidoka qui consiste à assurer la qualité dans le processus de production Le système anti-erreurs détecte l’absence du bague encours de processus de soudure Bague Sonotrode Lampe Bipper Exemple • Le Jidoka est l’un des piliers fondamentaux du Lean Production System. Pourtant, ce pilier est bien moins connu et commenté que son célèbre jumeau, le juste-à-temps. • Le Jidoka est souvent difficile à expliciter car, tout comme le juste-à- temps, le concept regroupe plusieurs éléments. La première idée fondamentale du jidoka « construire la qualité dans le produit en détectant les anomalies dans le processus ». Le principe en est simple : il s’agit de ne jamais produire de pièces mauvaises et, de ce fait, mieux vaut arrêter la production plutôt que de produire des pièces insatisfaisantes. • le Jidoka permet de mettre en place des boucles courtes d’identification de la non-conformité et de réaction immédiate, ce qui incite le management de site à travailler autant à court terme sur le terrain que dans des analyses de causes fondamentales pour éviter la récurrence des problèmes. Principes de base Arrêt au premier défaut: « Une ligne de production qui ne s’arrête jamais est, soit une ligne merveilleusement parfaite, soit une ligne à problèmes. Dans ce dernier cas, le fait que la ligne ne s’arrête jamais signifie que les problèmes ne remontent jamais à la surface. C’est très mauvais. Il est essentiel d’agencer une ligne pour qu’elle puisse être arrêtée à tout moment si nécessaire. Cela permet de prévenir la génération de produits défectueux, de mobiliser le personnel le plus compétent pour faire progresser les choses et, finalement, tendre vers la ligne parfaite qui ne nécessite jamais d’arrêt. »12 Communiquer le défaut : tableau andon : « Système de contrôle visuel installé dans un atelier, composé d’un tableau électronique suspendu visualisant la situation des opérations de production et signalant les problèmes dès leur apparition. »13 Corriger immédiatement le défaut: « Un contremaître qui arrête la chaîne deux ou trois fois à cause du même problème n’est pas digne de sa fonction. »16 La qualité du premier coup et à tous les coups : est une conviction de ne pas accepter de produire même avec un nombre très limité de produits défectueux . Il est indispensable d’adopter non pas seulement la philosophie de zéro défaut mais aussi les pratiques relatives par la maîtriser les risques des défauts et implantation des contre-mesures pour éliminer totalement les risques avant de se manifester en défauts Principes de base C’EST QUOI UN DEFAUT ? ….. └> C’est un écart par rapport à un standard └> Non-conformité └> Non satisfaction du CLIENT Pièce Type Bonne Pièce mauvaise -Panoplie de défaut -Flash Qualité -Mode Opératoire Ensemble des caractéristiques d’une entité qui lui confèrent l’aptitude à satisfaire des besoins exprimés et implicites. QUALITE Aptitude d’un ensemble de caractéristiques intrinsèques à satisfaire des exigences. (exigence : besoin ou attente pouvant être formulé, habituellement implicite ou imposé) - Ne pas recevoir des défauts - Ne pas produire des défauts - Ne pas livrer des défauts Produire la qualité du premier coup et à tous les coups Règles d ’or : Faire toujours le contrôle 100%: Méthode traditionnelle: Pour maîtriser la qualité du produit , on installe des filtres et des barrages pour éviter que le défaut arrive chez le client ( Ctrl 100%, super contrôle , contrôle visuel , audit produit , audit magasin , Tear down etc..) Combien coûte un tel processus de contrôle et par conséquent combien va augmenter le prix de vente ou réduire la marge bénéficiaire de la société? Est ce que vraiment on peut arriver a ne pas livrer des produits défectueux au client on utilisant cette méthode ? Méthode lean ( TQM ) La maîtrise de la qualité du produit est le résultat du niveau de maîtrise de la méthode et les moyens utilisés pour son développement Contrôler 100% c ’est faire des contrôle 100% de toutes les opérations élémentaires nécessaires pour produire un article au lieu et au moment de leur exécution - Autocontrôle - Contrôle successif - Pokayoké -Autonomation Faire toujours le contrôle 100%: Comparaison entre le contrôle traditionnel et le contrôle du source Contrôle traditionnel : - Une erreur aura lieu - un défaut apparaît comme résultat - Le défaut est détecté - Un feed back aura lieu - Des actions correctives seront mises en place Contrôle du source - Un système de détection des erreurs est intégré dans le processus - Une erreur aura lieu - Un feed back aura lieu avant que l’erreur devient un défaut - Une action corrective aura lieu - Le défaut n’aura pas lieu Faire toujours le contrôle 100%: L’auto contrôle : L’opérateur effectue en permanence le contrôle de la qualité du produit en même temps il exécute les tâches de son travail - L’opérateur mesure et décide la conformité du produit par rapport à l’exigence - L’opérateur corrige sur place le produit - L’opérateur arrête la production en cas de nécessité et ne la remet pas en route qu’après l’élimination du défauts - L’opérateur doit être équipé des normes ( Les instructions d’autocontrôle ) , des connaissance nécessaires pour juger la qualité de son produit ( Formation ) et des moyens adéquats pour effectuer les retouches Faire toujours le contrôle 100%: Basiques auto qualité Une ligne en auto qualité n’envoie que des pièces bonnes à son client en bloquant les éventuels défauts générés. Pour arriver à un tel fonctionnement, il faut : •identifier les défauts •collecter les défauts •remettre les défauts à celui qui les a transmis Chaque opérateur doit identifier les défauts qui peuvent surgir à son poste de travail. Une formation régulière a lieu et une bibliothèque de défauts est facilement consultable. Un système permet de collecter des pièces mauvaises au poste : bacs rouges accessibles, goulottes dans les postes de travail... Un défaut doit remonter à celui qui l’a généré en reprenant toutes les étapes qu’il a suivi pour arriver au poste où il a été détecté. En effet, tous les postes intermédiaires ont laissé passé ce défaut. La collecte et la remise des défauts peut être à chaque équipe, quotidienne, hebdomadaire ou mensuelle selon la gravité, la fréquence des défauts ou la proximité du processus amont. Le Contrôle successif : On sait que l’utilisateur est le meilleur contrôleur du produit , Dans un flux de production le poste P utilise le produit du poste P-1 donc il devrait être vigilent de la qualité du produit qu’il a reçue Le poste P est aussi fournisseur du poste P+1 , donc il doit livrer un produit conforme à son client ( Client fournisseur ) Faire toujours le contrôle 100%: Le Pokayoké ( système anti-erreur ): Un défaut existe habituellement en deux stades: - Lorsqu’il est entrain d’être produit (maîtriser ce stade : la prédiction ) - Lorsqu’il est déjà produit ( Maîtriser ce stade c’est la détection ) Un pokayoké a trois fonction de base : Stopper le processus , contrôler le processus ou alerter l’intervenant sur le processus Faire toujours le contrôle 100%: Les techniques de pokayoké: Systèmes de guidage : pins , détrempage , tige de guidage etc. Système de détection et d’alerte ( visuelle , sonore ) Système des capteurs ( buté fin de course , mesure de charge etc . ) Système de compteur ( Nombre de pièces , dosage , etc.. ) Système de check list Faire toujours le contrôle 100%: Les Formules anti-erreurs: - Formule outils : en cas d ’erreur le travail suivant devient impossible ce qui oblige l’opérateur à s’en rendre compte - Formule indicateur : En cas d’erreur , une lampe s’allume pour attirer l’attention des opérateurs - Formule prévention : Afin d’éviter les erreurs on utilise une check- list ou on coche chaque fois qu’on effectue le travail ( les travaux administratifs ) Faire toujours le contrôle 100%: L’autonomation : L’autonomation c’est rendre une machine autonome pour exécuter les tâches suivantes: - Automatiser la détection des défauts - Automatiser l’arrêt du processus quand un défaut se uploads/Industriel/09-jidoka.pdf
Documents similaires
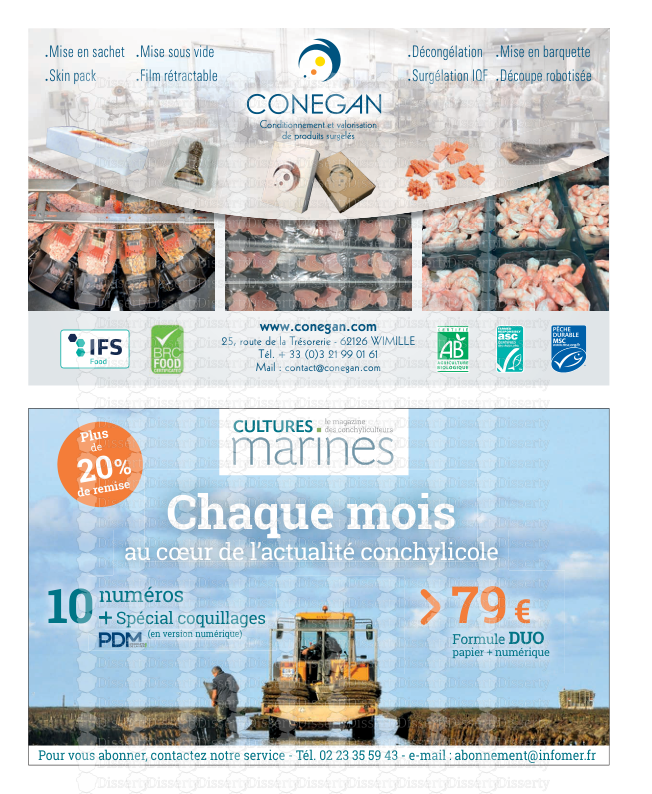
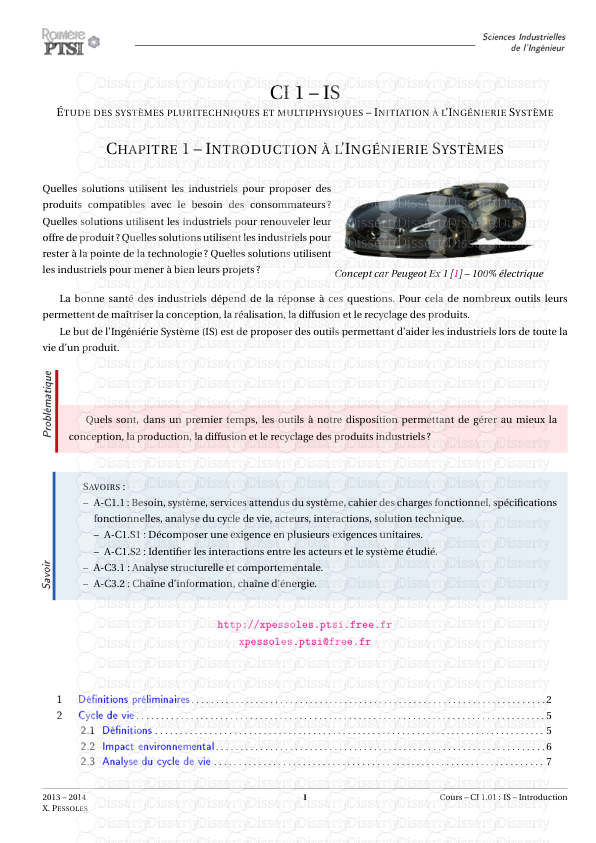
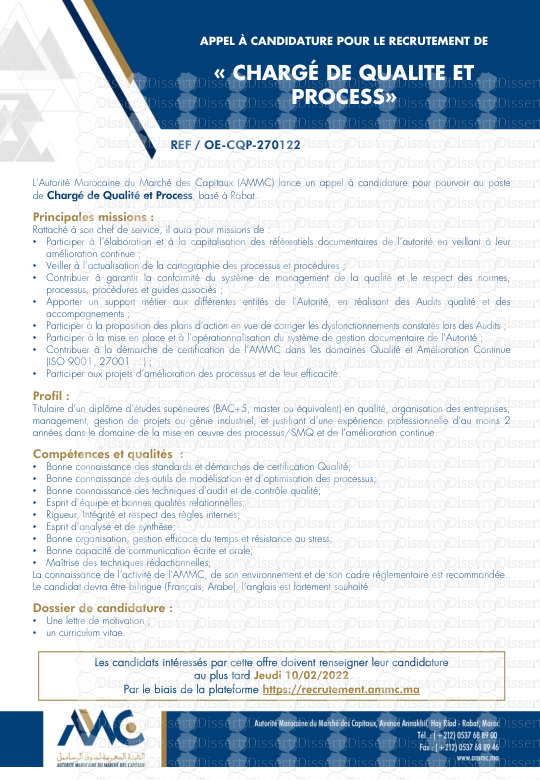
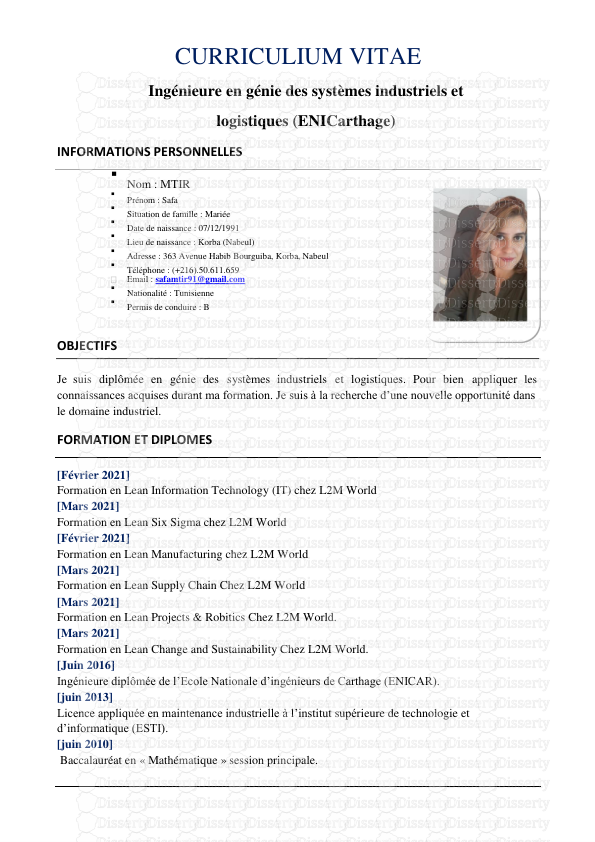
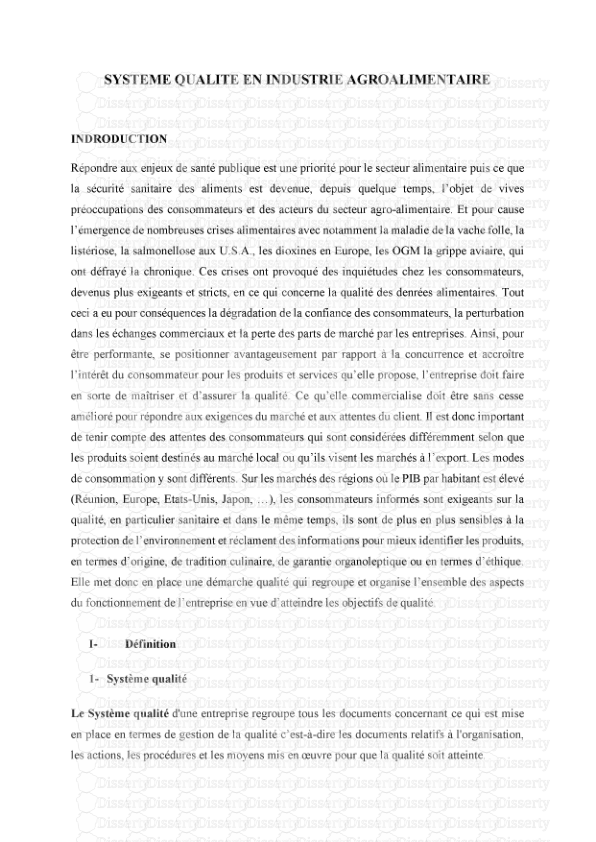
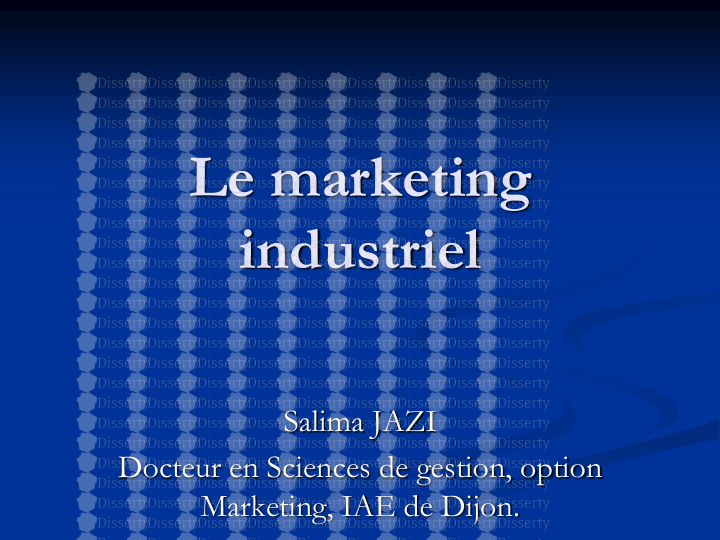
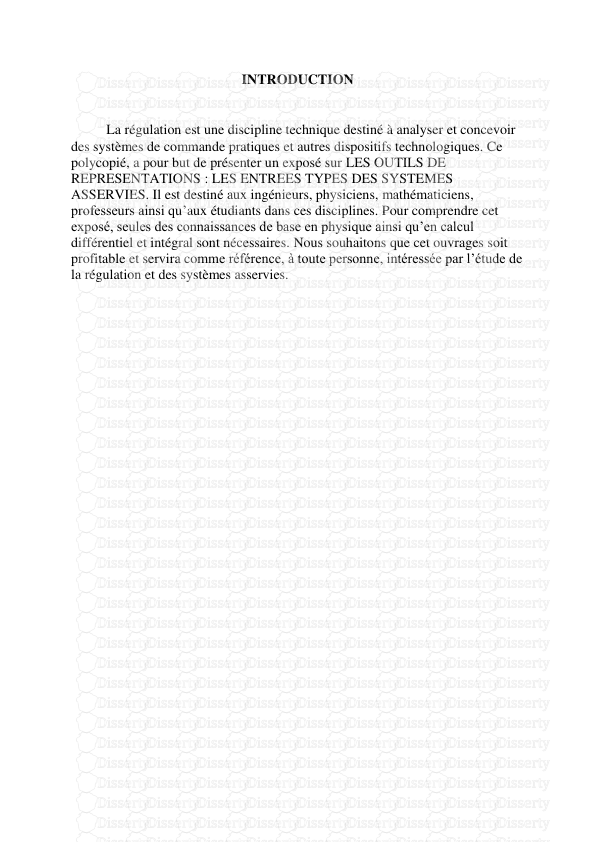
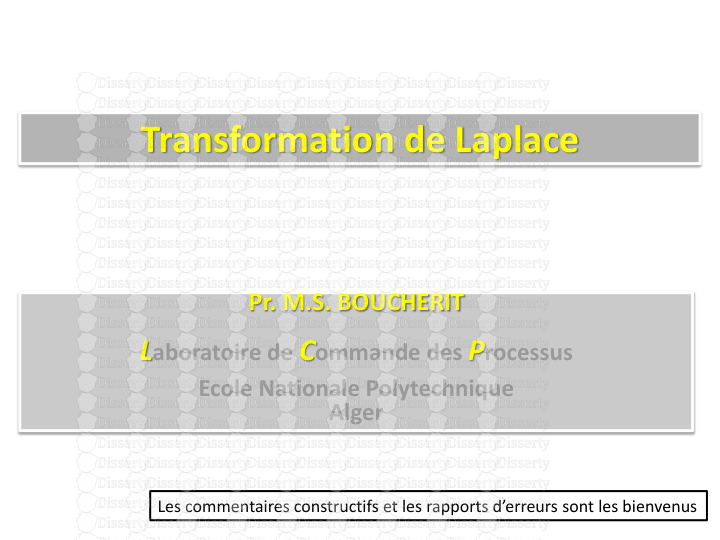
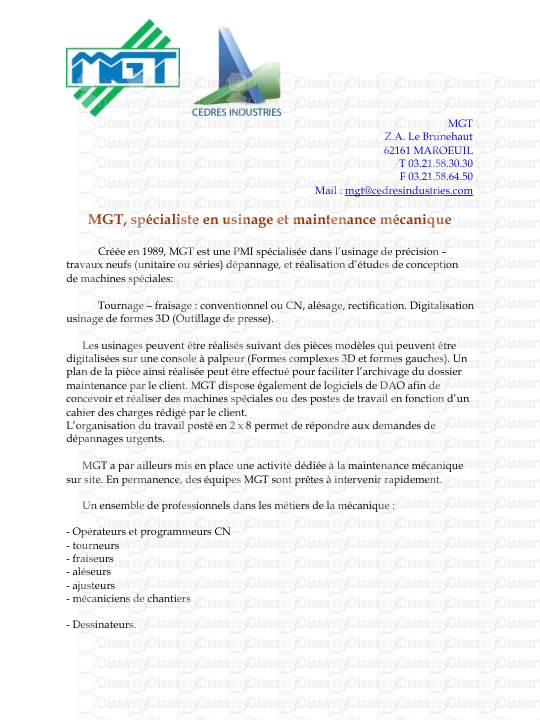
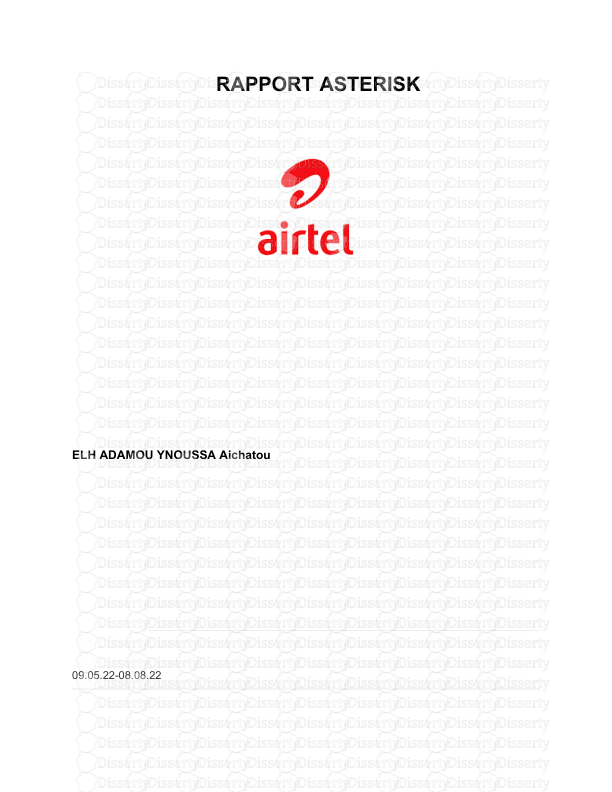
-
67
-
0
-
0
Licence et utilisation
Gratuit pour un usage personnel Attribution requise- Détails
- Publié le Oct 16, 2022
- Catégorie Industry / Industr...
- Langue French
- Taille du fichier 3.6169MB