Le béton cellulaire autoclavé Matériau d’avenir Séance d’information technique
Le béton cellulaire autoclavé Matériau d’avenir Séance d’information technique - 08.15 Accueil - 08.30 Présentation technique - 10.00 Questions / Réponses - 10.15 Conclusion Séance d’information technique - 08.15 Accueil - 08.30 Présentation technique - 10.00 Questions / Réponses - 10.15 Conclusion Séance d’information technique - 08.15 Accueil - 08.30 Présentation technique - 10.00 Questions / Réponses - 10.15 Conclusion Sommaire - Historique et production du béton cellulaire autoclavé - Caractéristiques physiques et mécaniques du béton cellulaire - Résistance thermique - Résistance mécanique - Réaction et résistance au feu - Propriétés acoustiques - Réponses à la EPBD (Performance Energétique des Bâtiments) - Construction Basse Energie - Construction Passive - Solutions pour résoudre les nœuds constructifs - Aspects durables du béton cellulaire autoclavé - Produits et applications - Exemples Sommaire - Historique et production du béton cellulaire autoclavé - Caractéristiques physiques et mécaniques du béton cellulaire - Résistance thermique - Résistance mécanique - Réaction et résistance au feu - Propriétés acoustiques - Réponses à la EPBD (Performance Energétique des Bâtiments) - Construction Basse Energie - Construction Passive - Solutions pour résoudre les nœuds constructifs - Aspects durables du béton cellulaire autoclavé - Produits et applications - Exemples Un peu d’histoire • 1854 : Bernardi : Briques de mortier à chaux • 1880 : W Michaelis Mélange de chaux, sable et eau sous vapeur saturée haute pression Silcates de calcium hydratés hydrorésistants (Grès artificiel) • 1889 : E. Hoffmann : Emulsification de mortiers (à l’aide de chaux et acide sulfurique) • 1894 : Production industrielle du silico-calcaire en Allemagne • 1914 : J.W. Aylsworth et F.A. Dyer : Emulsifiant = poudre d’Aluminium ou poudre de Zinc • 1924 : J.A. Erikson débute la production du béton cellulaire, matériau porteur et isolant (Sable fin, chaux, eau, poudre de métal comme émulsifiant). 1927 : Il combine avec l’autoclavage (Michaelis) • 1927 : Première norme relative au silico-calcaire (DIN 106) • 1939 : K.I.A. Eklund : Sable fin, chaux, ciment, poudre de métal • 1945 : Développement de méthodes de productions industrielles (blocs et dalles) • 1953 : Début de la production de béton cellulaire en Belgique Du plus lourd à l’ultra léger… 1894 : Production du silico- calcaire Matériau lourd et porteur 1900 1953 : Production du Béton cellulaire en Belgique Matériau porteur et isolant 2000 : Isolant Minéral (Multipor) Matériau isolant 2000 Le béton cellulaire autoclavé Aujourd’hui Silico-calcaire • 200 usines en Europe occidentale Production de blocs de maçonnerie et d’éléments de grandes dimensions. Béton cellulaire • Plus de 100 sites de production en Europe (eaaca’s members) • Produit dans 18 pays, 12.000 employés • 15 millions m3 (équivalent de 300.000 maisons) par an Production de blocs de différentes dimensions et de dalles armées Isolant Minéral (Multipor) • Matériau en pleine “expansion” • 2 sites de production en Allemagne Production de panneaux Isolants pour l’isolation par l’intérieur et l’extérieur D’un bloc porteur à un panneau d’isolation 1881 Michaelis: Silico-calcaire 1ère moitié 20e siècle Eriksson Béton cellulaire 2000 Allemagne 2008 Belgique Isolant minéral 350 - 600 kg/m3 λ = 0,080 - 0.150 W/mK Rés comp (fb): 2 à 6 N/mm2 Porteur et isolant 1400 à 2500 kg/m3 Rés comp (fb): 15 à 28 N/mm2 Porteur 115 kg/m3 λ = 0,045 W/mK Isolant Composition du silico-calcaire Composition • 90% sable • 7% chaux naturelle • 3% eau pure Réaction Dans le réacteur CaO + H2 0 --> Ca(OH)2 Dans l’autoclave SiO2 + Ca(OH)2 + H2 O --> Ca0.SiO2 .H2 O + H2 O Le grès naturel et le silico-calcaire = grains de sable quartzeux (0 à 2mm) dont les espaces intermédiaires sont remplis d’hydrosilicates de calcium qui assurent la liaison. Matériau écologique • Composé principalement de sable • Autoclavé (200°C, 8 à 16 bars moins d’énergie à la production) Composition du béton cellulaire Composition C3/450 C4/550 Sable (kg/m3) 350 420 Chaux (kg/m3) 100 110 Ciment (kg/m3) 25 30 Poudre d’aluminium (kg/m3) 0.5 0.4 Eau (kg/m3) 330 440 Réaction Dans le réacteur : CaO + H2O --> Ca(OH)2 + 65.2kJ/mol 3 Ca(OH)2 + 2 Al + 6 H2O -->Ca3 (Al(OH)6)2 + 3H2 Dans l’autoclave : 6 SiO2 + 5 Ca(OH)2 --> 5 CaO . 6 SiO2 . 5 H2O Ecologique • Peu de matières premières • Autoclavé (moins d’énergie à la production) Composition du béton cellulaire Water Water Lime Lime Sand Sand C3/450 C4/550 (450 kg/m3) (550 kg/m3) Sable pur (kg/m3) 350 420 Chaux (kg/m3) 100 110 Ciment (kg/m3) 25 30 Poudre d'aluminium (kg/m3) 0,5 0,4 Eau (kg/m3) 330 440 Type / Densité Composition 44% 12% 3% 41% 0,06% Sable Chaux Ciment Poudre d'Aluminium Eau Production phase I Production phase I Stucture cellulaire Macrocellules Microcellules Production phase II Production phase II Production phase III Production phase III Béton cellulaire autoclavé = ? Béton cellulaire = Matériau pierreux = Isolant Sommaire - Historique et production du béton cellulaire autoclavé - Caractéristiques physiques et mécaniques du béton cellulaire - Résistance thermique - Résistance mécanique - Réaction et résistance au feu - Propriétés acoustiques - Réponses à la EPBD (Performance Energétique des Bâtiments) - Construction Basse Energie - Construction Passive - Solutions pour résoudre les nœuds constructifs - Aspects durables du béton cellulaire autoclavé - Produits et applications - Exemples Resistance thermique Masse thermique (inertie thermique) Hiver : Le froid reste à l ’extérieur Été : La chaleur est rejetée Chaleur agréable à l ’intérieur La fraîcheur est conservée Masse thermique (inertie thermique) Thermal phase difference en temperature damping Thermal phase difference en temperature damping 0 0 6 6 12 12 18 18 24 24 0 0 6 6 12 12 18 18 24 24 Ext Exté érieur rieur B Bé éton ton cellulaire cellulaire Int Inté érieur rieur 30 30 20 20 10 10 C C Variations de Variations de- - temp tempé érature rature ° ° 30 30 20 20 10 10 C C ° ° Masse thermique (inertie thermique) Pour un bon confort thermique en été : - déphasage important F : 10 à 15 heures - amortissement thermique 2 – 4 % 20 degré de différence en température journalière (30 °C jour/10°C nuit) , il en résulte une différence de température intérieure de 20 x 0,03 = 0,6 degré avec une ventilation normale pendant la nuit. 0 0 6 6 12 12 18 18 24 24 0 0 6 6 12 12 18 18 24 24 ° ° Régulation thermique naturelle = confort Conductivité thermique Source : NBN EN 1745 Conductivité thermique Valeur de calcul Ui ou Ue suivant la norme NBN B 62-002(2008) a) intérieur 23°C et 50 % (humidité relative) Ui = 10dry * efu(u2-u1) avec fu = 4 u2 = 0,026 kg/kg u1 = 0 Facteur Facteur de correction pour de correction pour l l’ ’humidit humidité é : F : F m m = = 1,1096 Fm Conductivité thermique Valeur de calcul Ui ou Ue suivant la norme NBN B 62-002(2008) b) extérieur Ue = 10dry * efu(u2-u1) avec fu = 4 u2 = 0,150 kg/kg u1 = 0 Facteur Facteur de correction pour de correction pour l l’ ’humidit humidité é : F : F m m = = 1,8221 Resistance thermique Resistance thermique totale RT (m²K/W) RT = Rsi + R1 + R2 + R3 + ... + Rse RT = Rsi + d1 / Ui1 + d2 / Ui2 + Rair + d3 / Ue3 + Rse – Rse :resistance surface intérieure (m2K/W) – Rsi : resistance surface extérieure(m2K/W) – Rair : resistance thermique de la coulisse (m²K/W) – R1 ,R2 ,R3 , ... :resistance thermique des différents composants R1 R2 R3 Résistance mécanique Résistance en compression Béton Béton cellulaire autoclavé Résistance en compression Toiture l Toiture lé ég gè ère re 4 m 4 m C2/400 C2/400 fbk fbk 2 N/mm2 2 N/mm2 C3/450 C3/450 fbk fbk 3 N/mm2 3 N/mm2 C4/550 C4/550 fbk fbk 4 N/mm2 4 N/mm2 C2/400 C2/400 C2/400 C2/400 C2/400 C2/400 C2/400 C3/450 C2/400 C2/400 C3/450 C2/400 C2/400 C3/450 C2/400 C3/450 C4/550 C2/04 C3/450 C4/550 C3/450 C3/450 Murs extérieurs épaisseur 30 cm Murs intérieurs porteurs épaisseur 20 cm Murs intérieurs non porteurs épaisseur 10 cm Résistance en compression Béton cellulaire autoclavé Terre cuite Blocs béton Calcul effectué selon NBN EN 1996-1-1 Eurocode 6 Résistance en compression • Joint mince collé (2 à 3 mm) • Béton cellulaire = type de bloc ‘ Group 1 ’ (blocs pleins) • Epaisseur (20 ou 30 cm) La résistance des blocs est suffisante pour la plupart des applications de maçonnerie dans la construction Résistance caractéristique à la compression de murs f f k k = K . ( = K . (f f b b ) )a a . . ( (f f m m ) )b b Mortier classique fk = (0,60 à 0,40) fb 0,65 fm 0,25 Mortier colle fk = 0,80 fb 0,85 Mortier allégé fk = (0,80 à 0,70) fb 0,65 NBN EN 1996-1-1 + ANB NBN EN 1996-1-1 + ANB Char. Compr.str. fk in uploads/Ingenierie_Lourd/ beton-cellulaire.pdf
Documents similaires
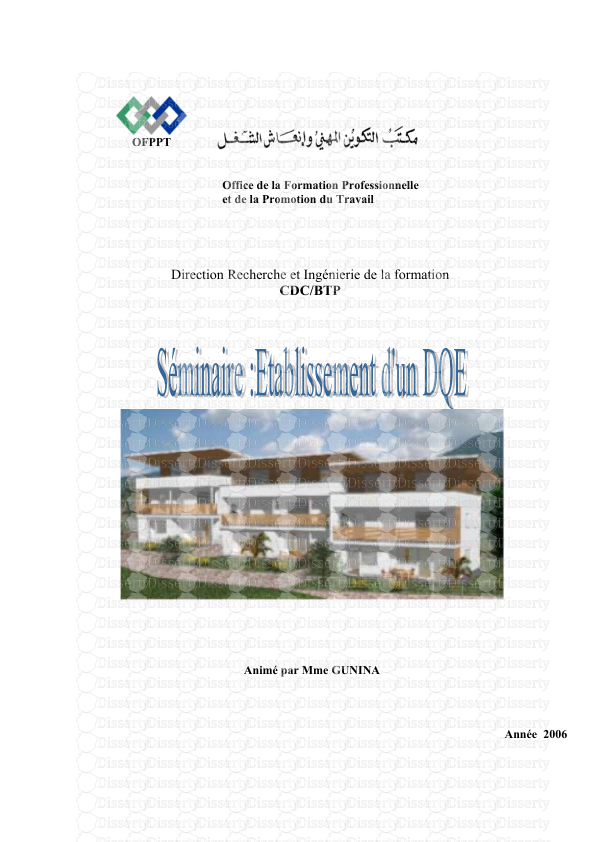
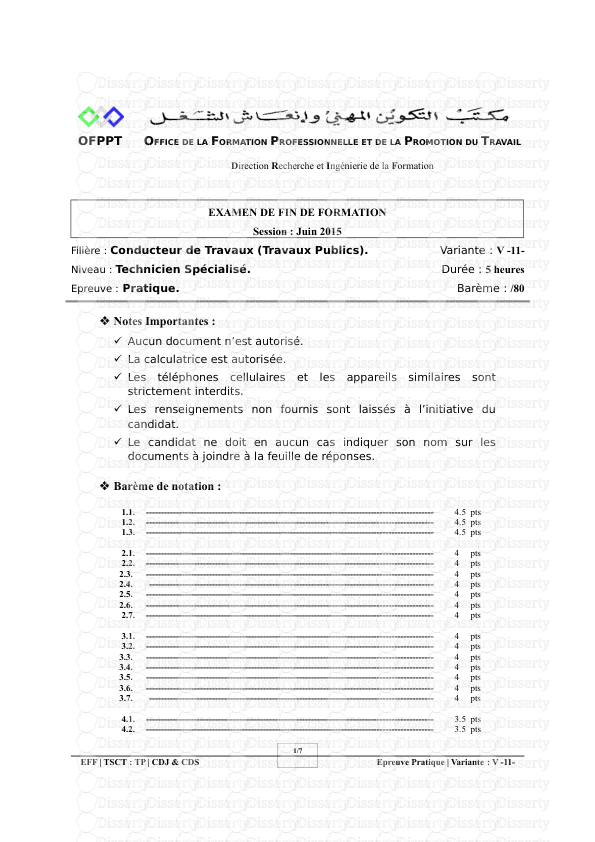

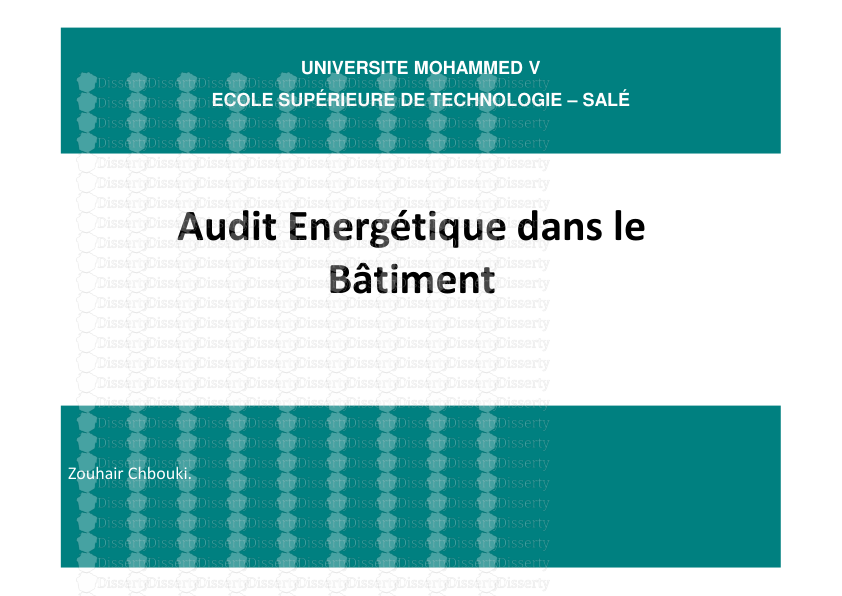
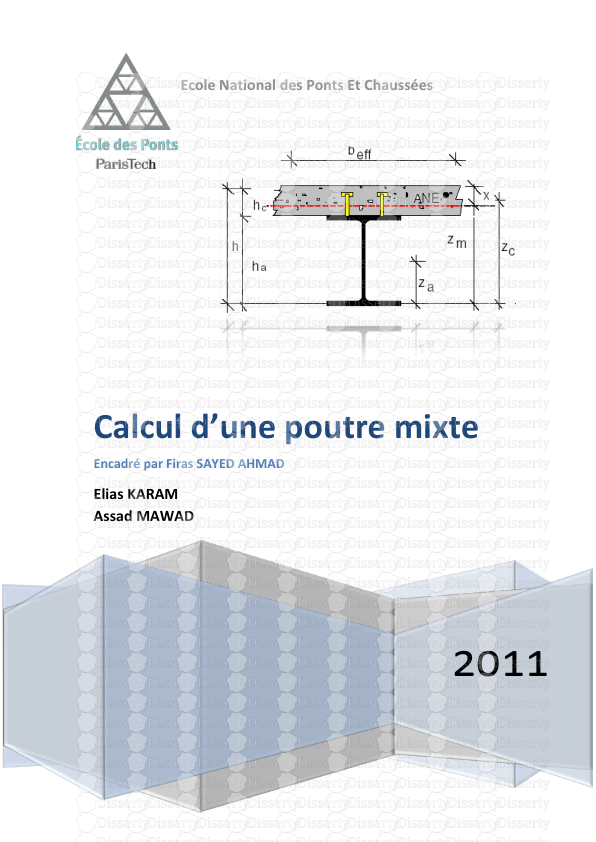
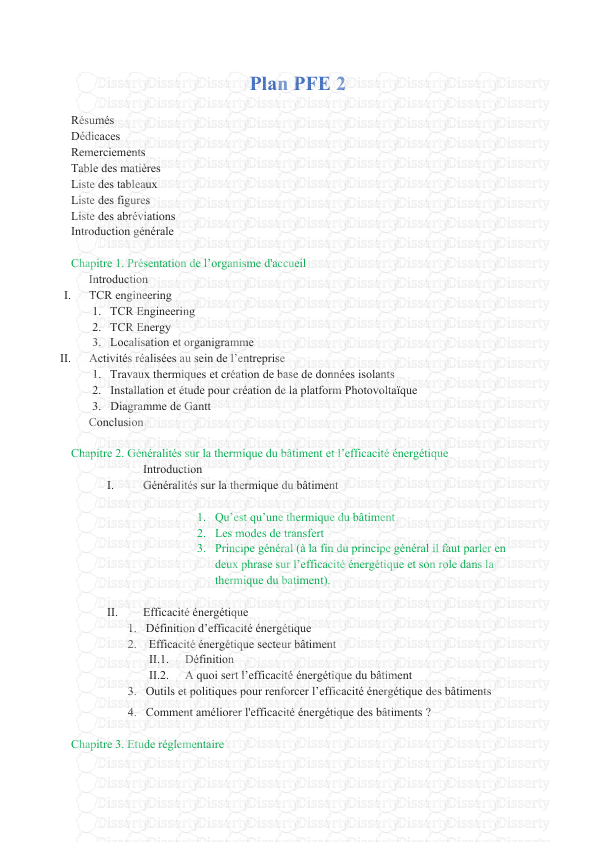
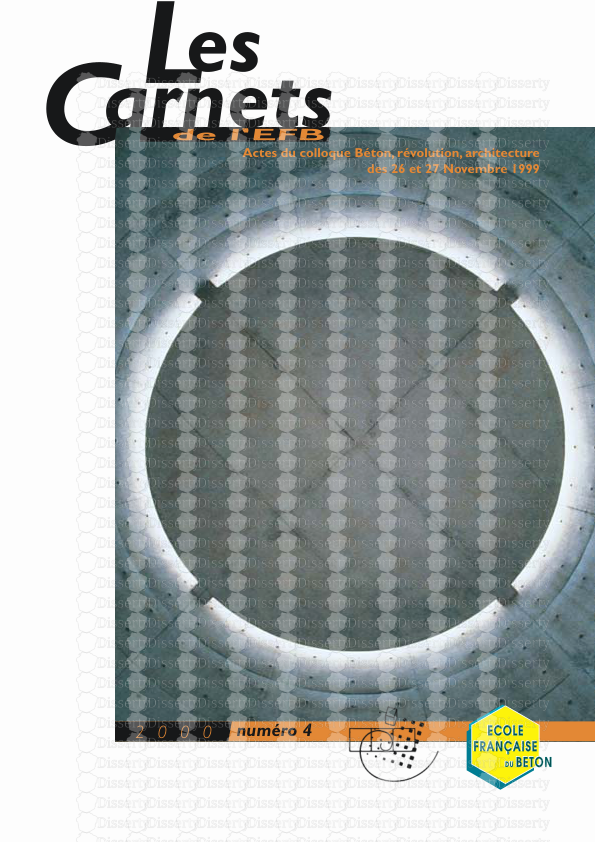
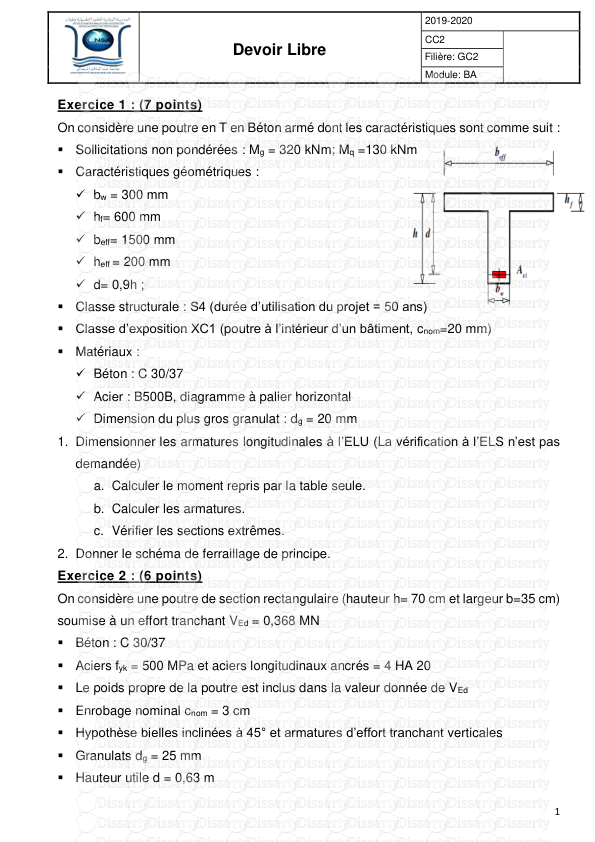
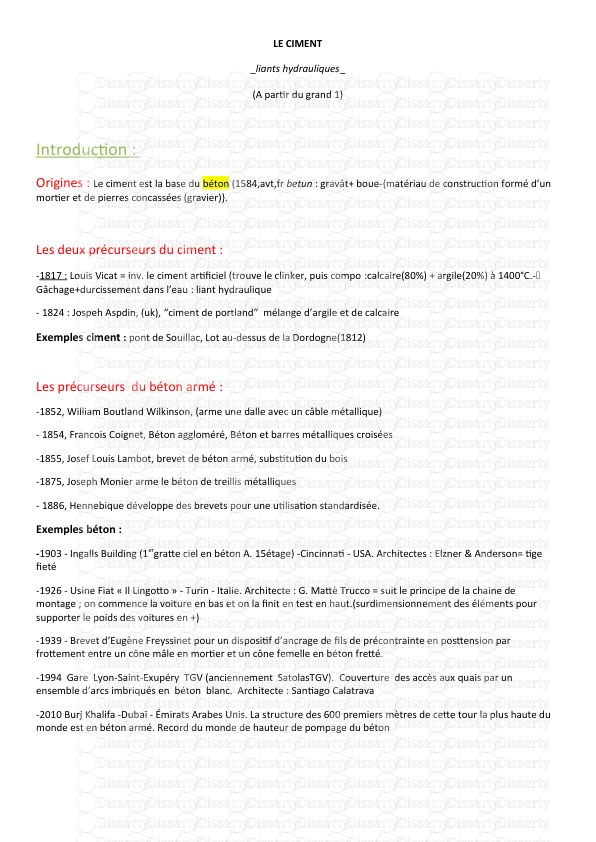
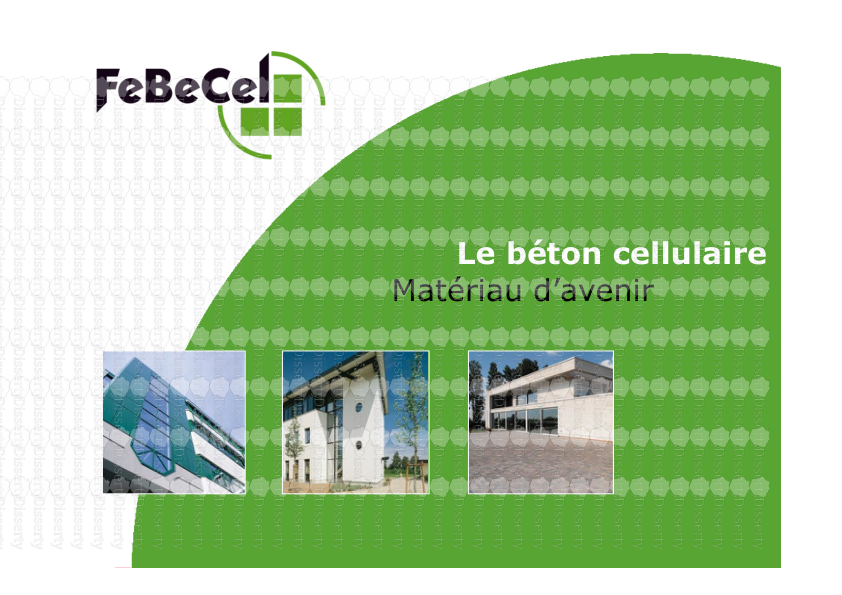
-
54
-
0
-
0
Licence et utilisation
Gratuit pour un usage personnel Attribution requise- Détails
- Publié le Jui 10, 2021
- Catégorie Heavy Engineering/...
- Langue French
- Taille du fichier 7.5368MB