Fédération Internationale des Ingénieurs-Conseils International Federation of C
Fédération Internationale des Ingénieurs-Conseils International Federation of Consulting Engineers Internationale Vereinigung Beratender Ingenieure Federación Internacional de Ingenieros Consultores GUIDE TO QUALITY MANAGEMENT IN THE CONSULTING ENGINEERING INDUSTRY Electronic Edition FIDIC is the International Federation of Consulting Engineers FIDIC was founded in 1913 by three national associations of independent consulting engineers within Europe. The objectives of forming the federation were to promote in common the professional interests of the member associations and to disseminate information of interest to members of its component national associations. FIDIC membership presently numbers over 60 countries from all parts of the globe. The federation represents most of the private practice consulting engineers in the world. FIDIC arranges seminars, conferences and other events in the furtherance of its goals: maintenance of high ethical and professional standards; exchange of views and information; discussion of problems of mutual concern among member associations and representatives of the international financial institutions; and development of the engineering profession in developing countries. FIDIC publications include proceedings of various conferences and seminars, information for consulting engineers, project owners and international development agencies, standard pre-qualification forms, contract documents and client/consultant agreements. They are available from the secretariat in Switzerland. © Copyright FIDIC 2001 All rights reserved. No part of this publication may be reproduced or transmitted in any form or by any means without permission of the publisher. Published by Fédération Internationale des Ingénieurs-Conseils (FIDIC) P .O. Box 86 CH-1000 Lausanne 12 Switzerland Phone +41 21 654 44 11 Fax +41 21 653 54 32 E-mail fidic@fidic.org WWW www.fidic.org WAP www.fidic.org Contents Preface 1 1. Introduction 2 1.1 Purpose of the Guide 2 1.2 Quality, historically 2 1.3 The concept of Quality Management 3 1.4 Kaizen 2. Quality Management in consulting engineering 4 2.2 FIDIC and Quality Management 4 2.2 FIDIC policy 5 2.3 Eight principles of Quality Management 6 2.4 Why consulting firms should adopt a Quality Management System 12 3. Development of a Quality Management System 15 3.1 Introduction 15 3.2 Committment of senior management 15 3.3 System develoment and implementation 15 3.4 Sustaining the Quality Management process 18 Appendix A - Example of Quality Management procedures in a firm 21 Appendix B - Quality Management checklist 22 Appendix C - Evaluation of Quality Management Systems 27 Appendix D - Misconceptions about Quality Management 30 Appendix E - Further reading 31 Preface Throughout its history, FIDIC has exercised its mandate in the production of various documents, contract forms, guides and manuals to assist Consulting Engineers worldwide to perform and deliver services to their clients. These publications have facilitated the business practice of Consulting Engineers to establish standards or norms which are used by a large and increasing number of Consulting Engineers and their clients. Some of the documents, for example, contract forms, are very specific, while others are more of a guideline. All of the FIDIC products have benefited from the contributions of a number of members, in their production. The present Guide is no exception. The first edition of this Guide was issued in 1994 and was prepared by a committee chaired by R.W. Bowes. A significant contribution to the production of the first edition of this Guide was made by Tom Kern of the American Consulting Engineers Council. The present edition of the Guide has been prepared and edited by FIDIC's Quality Management Committee under the chairmanship of Tonny Jensen, Denmark. Significant contributions was made by David Shepherd, Australia, Frank Leblanc, Canada, and Ben Novak, Canada. The Guide has been developed as a living document, subject to periodic review and updating in order to provide Consulting Engineers with comprehensive documentation on Quality Management. The document will be supplemented and enhanced as more experience is gained in its application. This Guide sets out reasons why Consulting Engineers should apply Quality Management in all of their work, and provides an introduction to initiating this Quality Management process in their firms. The development of a Quality Management System in many firms will often be accompanied by improved business practices designed to enhance the quality of business management. Firms and Member Associations are encouraged to take advantage of the FIDIC Training Kit on Quality Management, and of the professional seminars and extensive amount of published material offered by FIDIC and others on the general subject, and to customise the material for their own specific requirements. For further information, reference is made to Appendix E. FIDIC would be pleased to receive feedback from the users of this Guide on its usefulness, and areas for improvement. 1 2 1 Introduction In every age there has been a demand for conforming products. For simple, single component products, the purchaser or user could readily determine the extent to which a product met requirements. With increasing complexity and numbers of components, it ceased to be practical for the ordinary purchaser to assess conformance by simple inspection methods, and reliance was placed on the integrity of the producer. In small communities, the producers would all be known, and reputations would be quickly established. Communities became larger and population mobility increased. Products made outside the community became increasingly available, and the identity of the maker often became indiscernible. An alternative basis of assessing quality was needed. The trade guilds provided a formal basis for the training of tradesmen, and regulated the quality standards of their products. This proved very satisfactory for products that could be produced by a single tradesman with the aid of a few journeymen and apprentices. For major products involving several trades and large numbers of workers, the system did not provide a satisfactory level of assurance that the desired quality would be met. Shipbuilding was a particular concern owing to the high cost in lost ships, cargoes and lives that resulted from product failure. Ship owners and the merchant users of ships were the first to establish what has become known as Quality Assurance. However, whereas the first ship classification society was established in 1748, it took another 90 years before 'survey under construction’, as opposed to final inspection, became the basis of assessment. The mass production of multiple component products set the scene for the advent of the modern quality discipline, that effectively dates from the work of Walter Shewhart at the Bell Laboratories in Chicago. Dr. Shewart’s methods were first introduced into Europe in 1938, and into Japan by W Edward Deming and Joseph Juran in the 1950s. Scientific method, using the principles of probability and statistics, has been the cornerstone of the stunning advances in world product reliability. Philip Crosby has led a parallel approach, sometimes seen as an alternative to the Deming method, that focused on the positive influence on quality of individuals conscientiously and systematically removing error from their work. The pursuit of world harmonisation in standards, and the removal of barriers to international trade, has led to the International Organization for Standardization (ISO) publishing a group of standards on quality systems collectively referred to as the ISO 9000 Family of Standards. The first edition of these documents, substantially based on British Standard BS 5750 - 1975, appeared in 1987. The ISO 9000 Family of Standards has become one of the most widely published standards in the world, and has been adopted without editorial change by over 75 countries. The short form of the International Organization for Standardization is ‘ISO’, and not ‘IOS’. ISO is in fact a word derived from the Greek isos, meaning equal, which is the root of the prefix iso- that occurs in a host of terms such as isometrics - of equal measure or dimensions - and isonomy - equal of laws, or of people before the law. The name has the advantage of being valid in each of the organisation’s three official languages - English, French and Russian - and avoids the confusion that would arise through the use of an acronym that would not correspond to the title of the organisation in French. The term Total Quality Management (TQM) was coined in 1985 by Nancy Warren, a psychologist This Guide has three main purposes: 1 To provide background information on, and an introduction to, Quality Management, with convincing evidence that member firms must adopt effective Quality Management practices, focussed on continuous improvement through the involvement of all employees. 2 To outline what constitutes a Quality Management System for consulting firms. 3 To outline what steps to follow to initiate the development of a Quality Management System in a consulting firm. 1.1 Purpose of the Guide 1.2 Quality, historically 3 1 Introduction with the United States Navy. It was introduced as an alternative to the Japanese Total Quality Control. The significance of TQM is that it requires an organisation to apply quality principles to all aspects of its operation, not just those concerned with production or services. Aspects of the organisation often excluded from the quality system, would be included in a TQM system, such as financial management, human resource management, marketing and sales, information technology, and general and executive management of the enterprise as a whole. uploads/Management/ guide - 2023-05-30T051237.859.pdf
Documents similaires
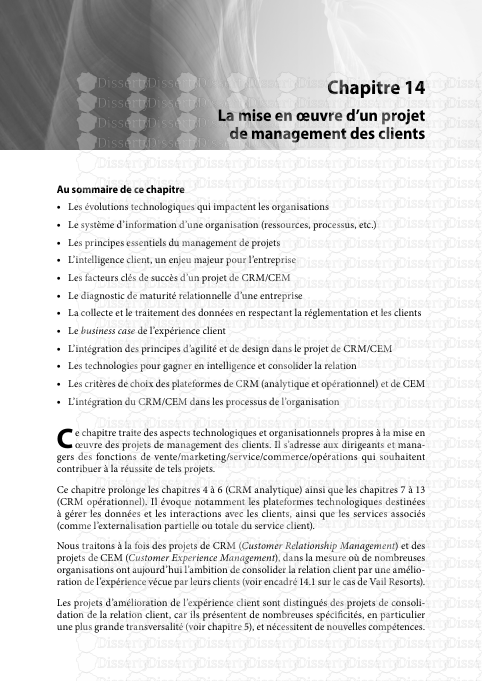
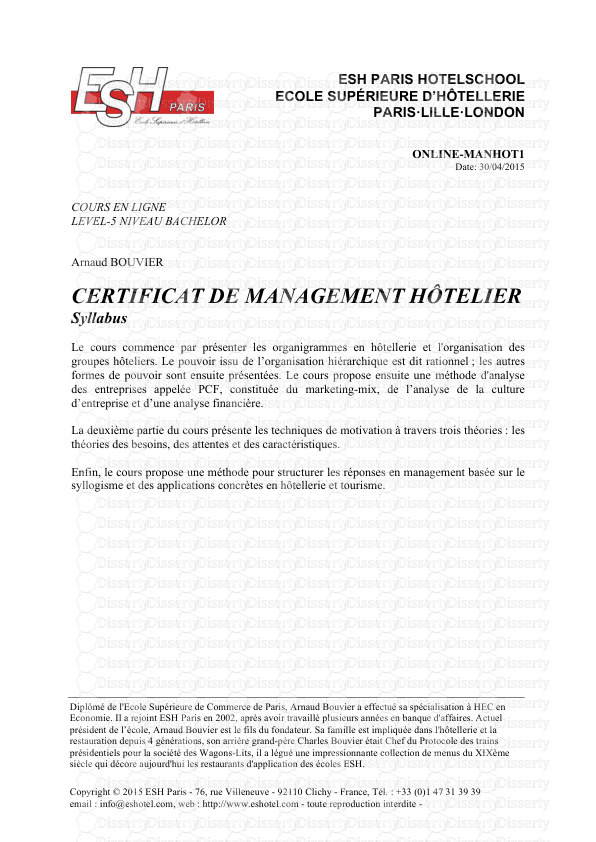
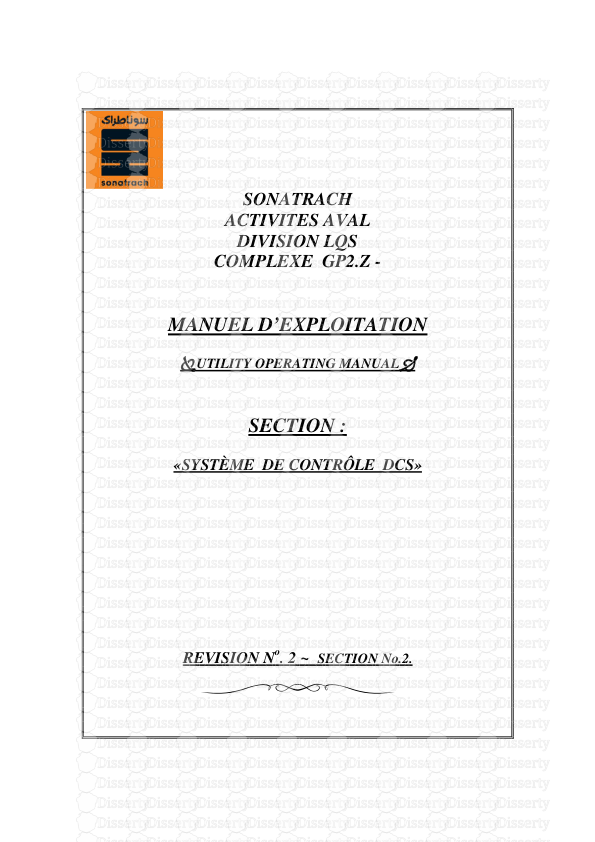
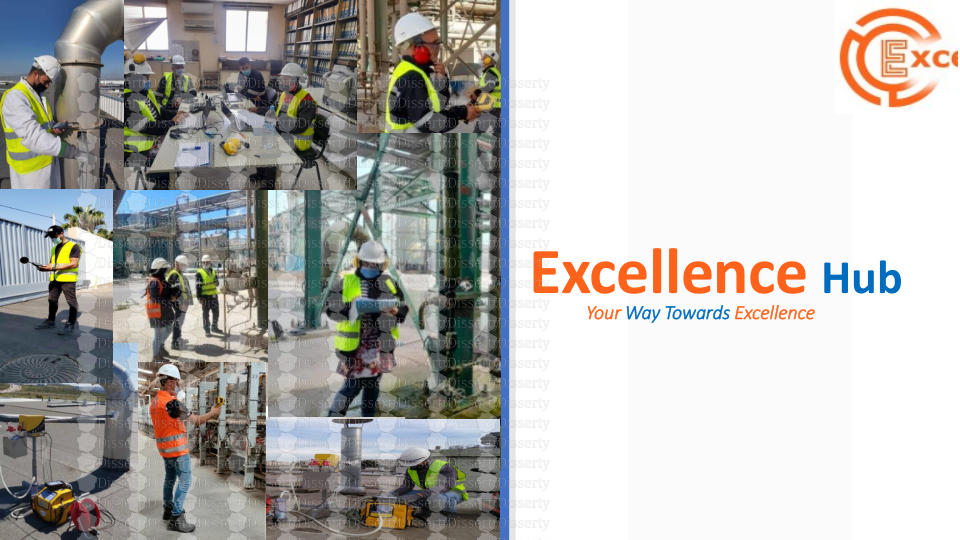
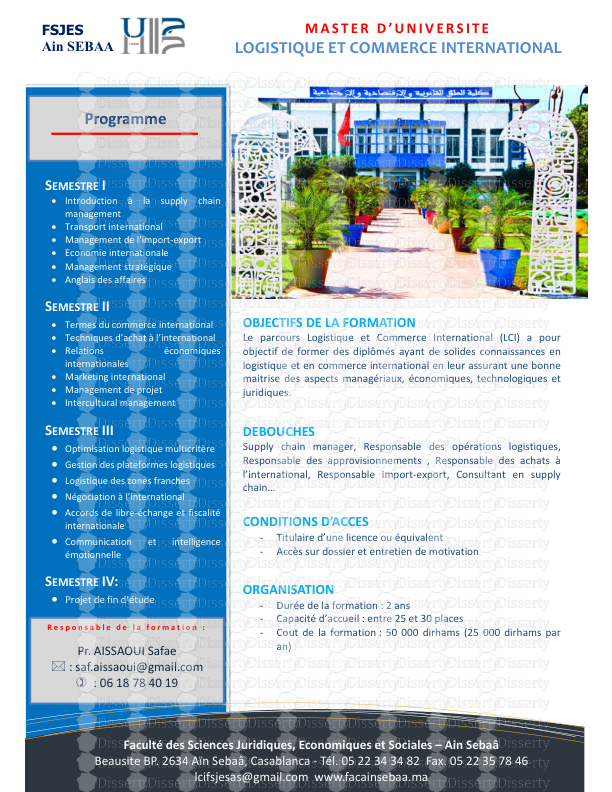
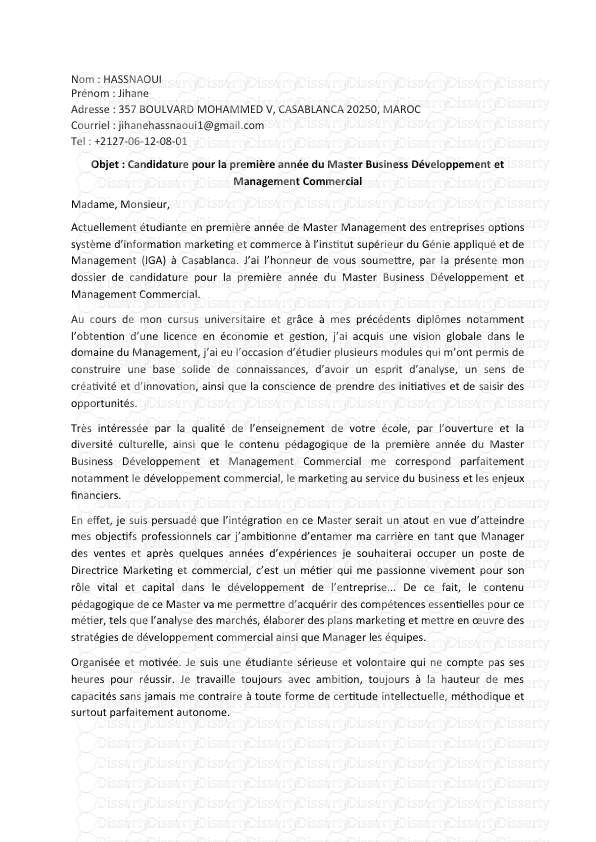
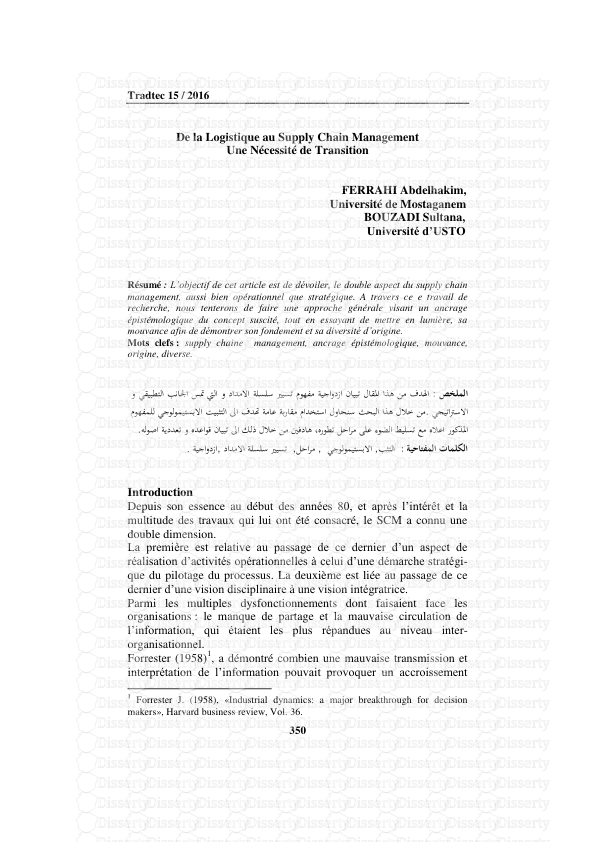
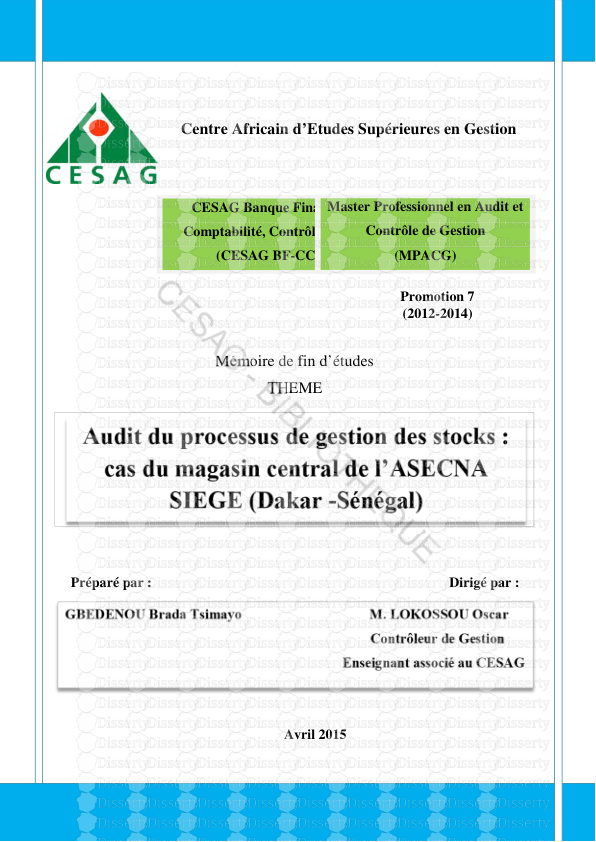
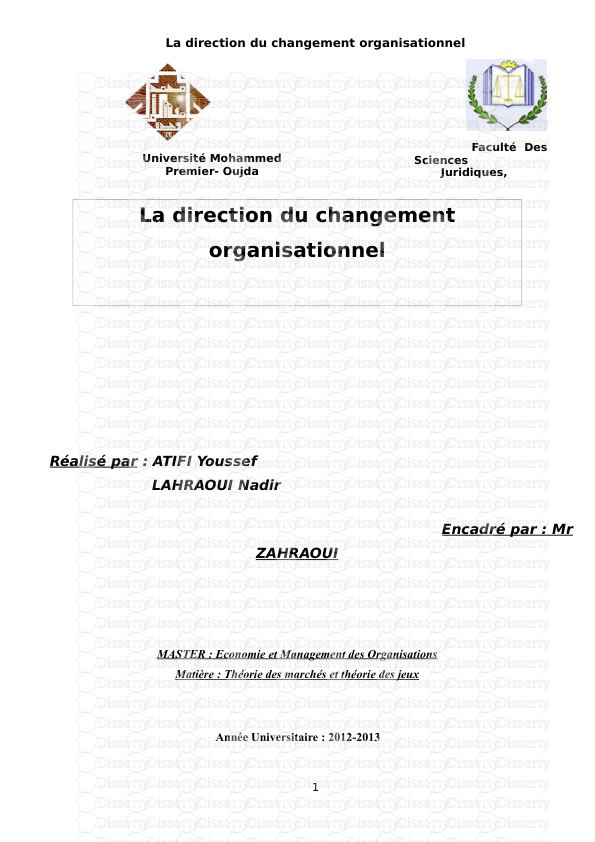
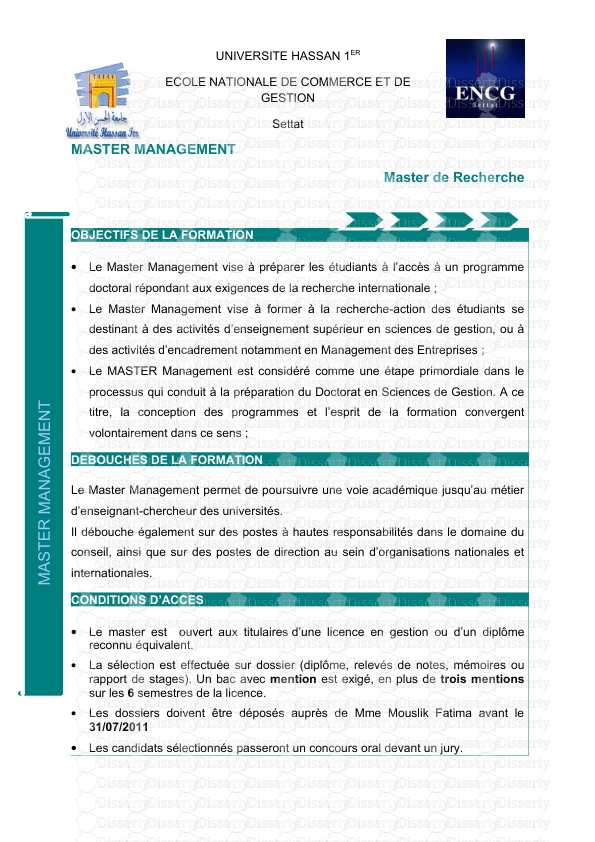
-
56
-
0
-
0
Licence et utilisation
Gratuit pour un usage personnel Attribution requise- Détails
- Publié le Jan 09, 2022
- Catégorie Management
- Langue French
- Taille du fichier 3.3131MB