Troubleshooting Guide for Powder Coating www.marpolind.com WHY POWDER COATING?
Troubleshooting Guide for Powder Coating www.marpolind.com WHY POWDER COATING? INTRODUCTION Thermo setting powder coatings are now generally recognized as having a significant role in the metal finishing industries world- wide. Powder coatings have been a commercial reality now for close to thirty years Powder coatings are used for the same key reasons as any surface finishing process: • To protect the substrate they have been applied to • To enhance the appearance of the item they have been applied to. • The key benefits of powder coatings are often summarized by the five E's of powder coating. • Ease of application • Environmentally friendly • Economical • Excellence of finish • Excellence of performance Other benefits include: • The elimination to a large extent of solid waste disposal problems. • Solvent emissions are virtually eliminated, resulting in much easier compliance with EPA regulations. • Energy costs are greatly reduced and Volatile Organic Component easily controlled. • No solvents are required in mixing, cleaning or maintenance. • Up to 99% of powder overspray can be recovered and reused. The 1% residual can easily be disposed off as a solid. For these reasons there has been a rapid growth in the coating industry. Powder coatings are often used as alternatives to liquid paint finishing. In comparisons with traditional liquid finishing, powder coatings offer two significant application benefits: • they are single coat finishes, with no primer required. • High film thickness can be achieved with a single coat. The powder coating application process is also readily automated, enabling high volume industrial application plants to operate economically with a minimum of rejects. These benefits have enabled powder coatings to take a significant share of the industrial finishing market. APPLICATIONS HOME APPLIANCES In the home appliance industry, powder coatings are well recognized as being a high quality finish for both major and minor applications. In the appliance finishing industry, the advantages of high corrosion resistance with single coat application has resulted in powder coatings being used on a wide variety of electrical appliances, including; air conditioners, clothes dryers, cookers, dishwashers, fans, freezers, microwave ovens, rice cookers, refrigerators, stereo components, television components, video components, washing machines, water coolers. In addition to the major appliances noted powder coatings are also widely used for smaller appliances such as toasters, irons, can openers, juice extractors, food processors, vacuum cleaners and floor polishers. AUTOMOTIVE COMPONENTS Although powder coatings are not yet widely used on auto bodies, they are finding growing applications on components for both interior and exterior applications. In most automotive applications, powder coatings are used for auto performance characteristics as most auto producers still prefer the use of liquid coatings for those areas requiring optimum appearance. Current applications in the automotive industry include: air filter housing, alloy road wheels, brake calipers & components, bright trim molding, bumper bars, door handles engine blocks- iron & alloy, mirror housings, motorcycle frames, oil filter housings, rocker covers, seat frames, steel wheels assemblies, stereo system, components suspension systems, underbody primer, windscreen wipers. FURNITURE The furniture industry is a major market for powder coatings. Powder coatings are used extensively on both commercial and domestic furniture for both their performance and for their appearance. The performance characteristics of powder coatings which make them so suited to the furniture industry include : • toughness • hardness • corrosion resistance ARCHITECTURAL Powder coatings have developed a strong position in the architectural industry as a coating for aluminum profile, cladding and other building components. ELECTRICAL AND ELECTRONIC INDUSTRY Computer casings, computer components, encapsulation, telecommunications equipments. METAL PRE- TREATMENT Metal Pre- treatment prior to powder coating is essential step to ensure proper coating performance. Metal Pre- treatment prior to powder coating is of two types. a) Mechanical surface Preparation. b) Chemical surface Preparation. For powder coating most commonly used surface preparation method is chemical pre- treatment. It is essential for an applicator to know the following: 1.Need for Pre- treatment 2.Surface Preparation 3.De- rusting Processors 4.Activation 5.Conversion coatings for a) Mild steel b) Galvanised steel c) Aluminum d) Mazak 6.Trouble Shooting 1.Need for Pre- treatment: The performance of powder coating on a metallic surface mainly depends on Proper Pre- treatment of the substrate. Proper pre- treatment is an essential factor because of the following advantages (1.Pre- treatment process provides a clear, uniform, oil- grease free surface. (2.Provides good adhesion of film (3.It forms an inert layer which inhibit the corrosion of the paint film General Pre- treatment Process sequence: a)De- greasing Process b)Water- Rinse c)De- rusting d)Water rinse e)Activation f)Conversion Coating g)Water rinse De- greasing Process: Chemical de- greasing methods used in any particular application is closely related to the nature of the surface being cleaned and the amount and type of contamination. The various chemical degreasing processes applicable to Mild steel, Galvanised Steel & aluminum substrates, are as follows: Solvent Cleaning: a) Solvent Wipe: Solvent cleaning is the cheapest and best method to remove heavy or sticky oil/grease like substances form nay surface. Since all solvents are almost neutral they do not attack to the base metal. In this process, the parts to be cleaned are wiped with rag of cotton soaked in a suitable solvent such as Kerosene, Benzene, Naptha etc. The following are the advantages and disadvantages of solvent wipe method. Advantages a)Cheapest cleaning method available in the industry to remove heavy oils, greases or sticky press compounds. b)Skilled labours and costly plant installation is not required. c)Suitable for smallest job coater as well as for OEM industry. Disadvantages a)The process is labour intensive. b)Since all the solvents are flammable, a great fire risk is associated with the solvent cleaaning. c)Frequent change of cloth and solvent is essential or otherwise it can affect the quality of cleaning. d)Solvent going into the drainage can cause effluent disposal problem. Vapour De- greasing: Vapour de- greasing is quite a sophisticated method of cleaning. In this method, special type of solvent is used which has following advantages. • Mineral & veg. Oils removal is faster. • Has lower boiling point than water • Non- toxic to human being. This process requires a closed system in which the item to be cleaned is exposed to the condensing vapours of solvent. This method effectively removes light oils, greases but cannot remove heavy oils, greases, and sticky press compounds. Advantages a)Very good method for cleaning light oils, greases. b)Less risk of fire hazard, minimum pollution as it is a closed system. c)Since the solvent used is a not- toxic there is no danger for the operating worker. Disadvantages a)Require costly plant installation and skilled labour. b)Frequent removal of oil & grease is required or otherwise they increase the boiling point of solvent. c)Thin sheets having heavy oil grease or sticky press compounds can not be removed by the process as there is no mechanical action on the parts. d)Costly process. Emulsion Cleaning: Emulsion cleaners are popular as they are based on mild Alkalis and hence suitable to all substrates (Iron, Galvanised steel Mazak etc.) and operate at room temperature. Emulsion cleaners are generally based on either kerosene- emulsifier or turpentine- emulsifier. These cleaners are generally milky in appearance. Emulsion cleaners have a limited cleaning tendency and they leave a very thin film of solvent/emulsifier over the substrate even after water rinsing. Hence, Emulsion Cleaning is always followed by Alkali cleaning. In case of spray process the parts to be cleaned are suspended in a funner wherein they are constantly exposed to the spray solution for 2 to 5 minutes at a pressure of 2- 3 kgs/cm² for better results. In dip process, the parts to be cleaned are simply immersed in a bath of the cleaning solution. This process has following advantages and disadvantages Advantages a)Operates at a lower temperature (45- 50ºc) hence consume less energy. b)Suitable for all the substrates such as Mild steel, Mazak, Aluminium, Galvanised etc. Disadvantages a)Limited cleaning ability as it can not remove heavy grease, oil etc. b)Not suitable for higher temp. As the emulsions are based on solvents which gets separated above 70ºc from the emulsion phase. Alkali Cleaning: Alkali cleaners enjoy superior position in the Pre- treatment industry due to following advantages. • They operate at room temp. • Bath stability is higher compared to all other degreasing processes, low foaming tendency. • Simple bath control. • Costly plant installation is not always required. • High capacity to absorb oil. These cleaners are based on strong alkalies such as Sodium hydroxide, Sodium silicates, other filters and builders such as soda ash etc, surfactants and additives. The parts to be cleaned are immersed in this bath at a recommended temperature and time. Strong alkaline cleaners are avoided in case of Manganese phosphate process as they can cause inferior quality coating. Strong alkaline cleaners are also not suitable for non- ferrous substrate such as Zinc, aluminum, Brass, Copper, Glass, Galvanised Steel, because all these metals readily get attacked by strong alkalies. De- rusting: Corrosion is common phenomenon for metals. Iron or steel when exposed to humid uploads/Management/ marpol-troubleshooting-guide.pdf
Documents similaires
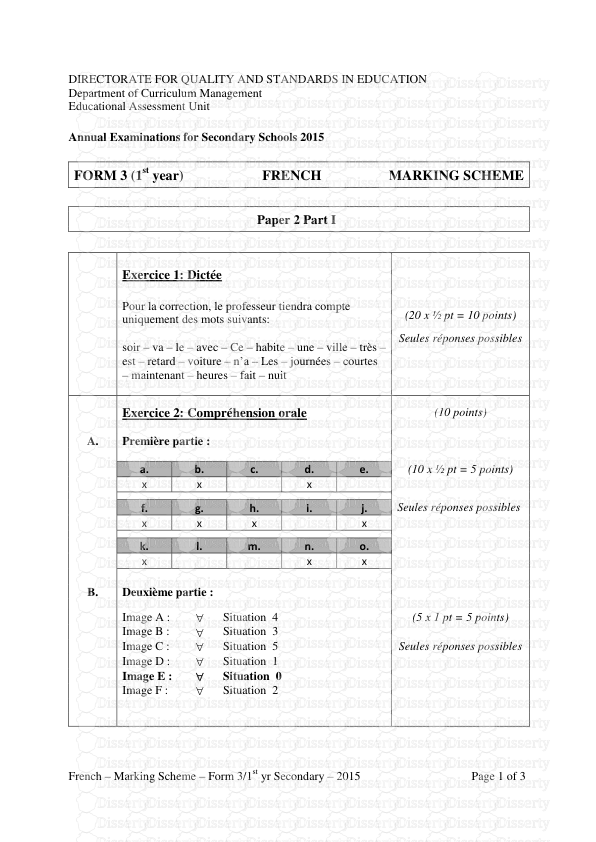
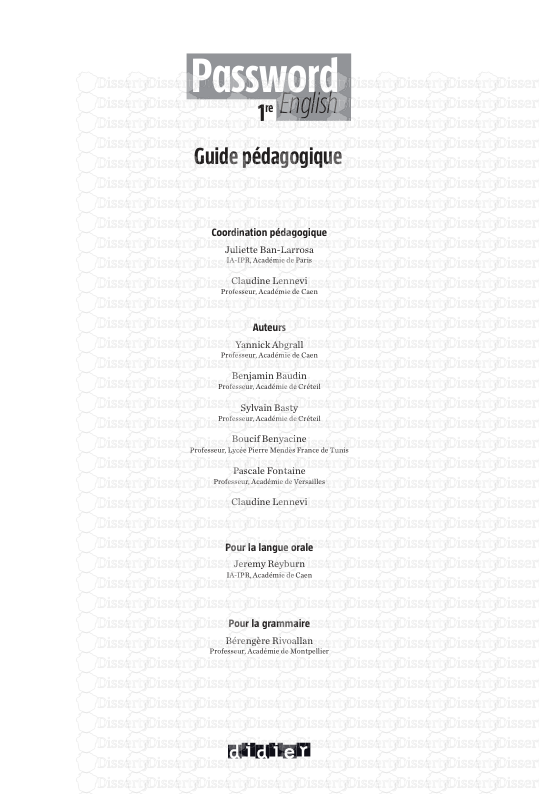
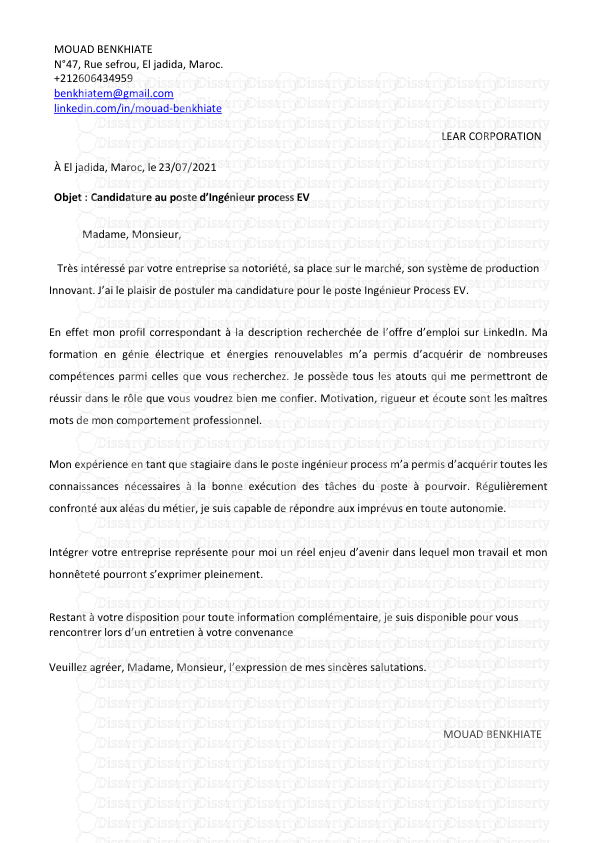
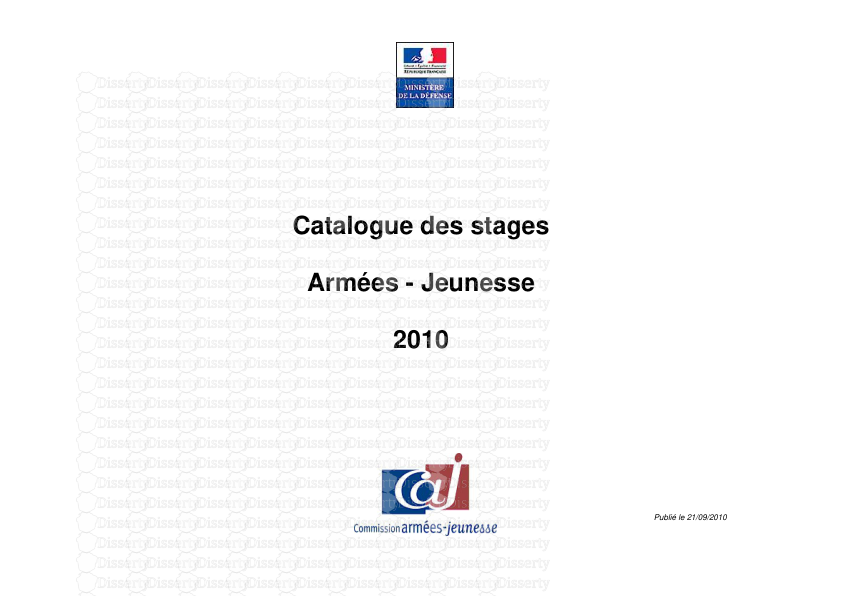
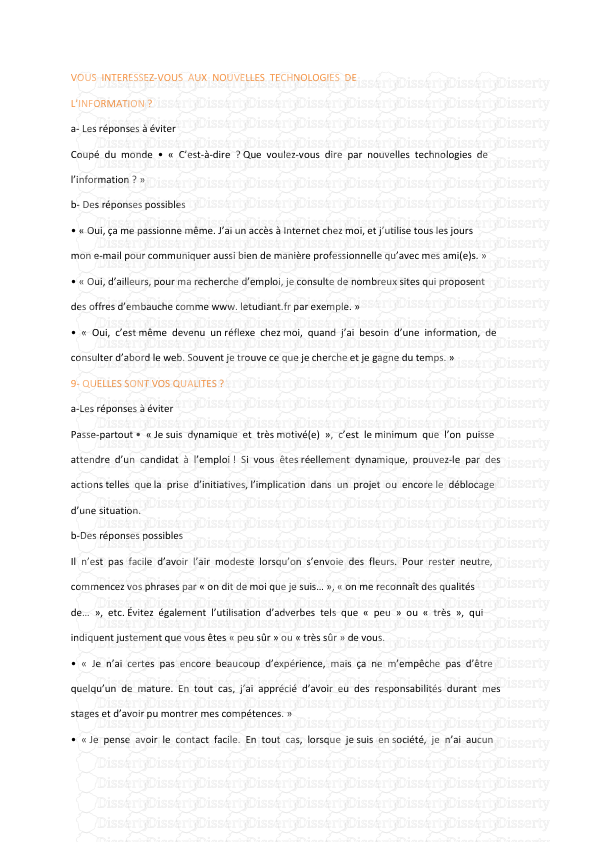
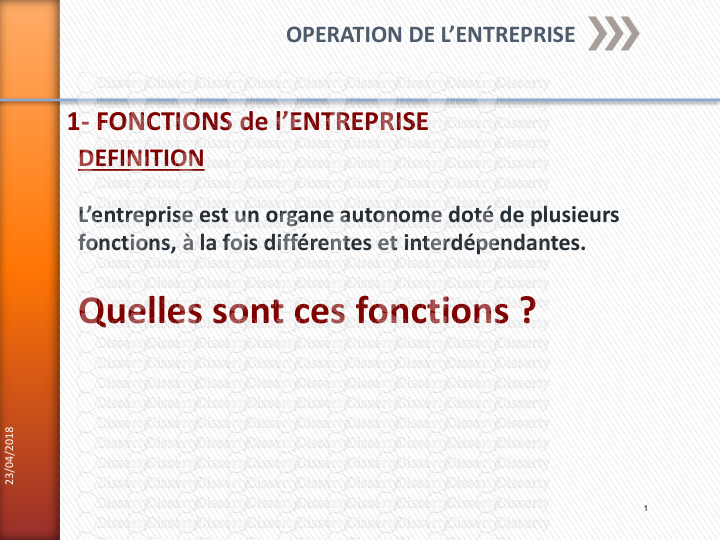
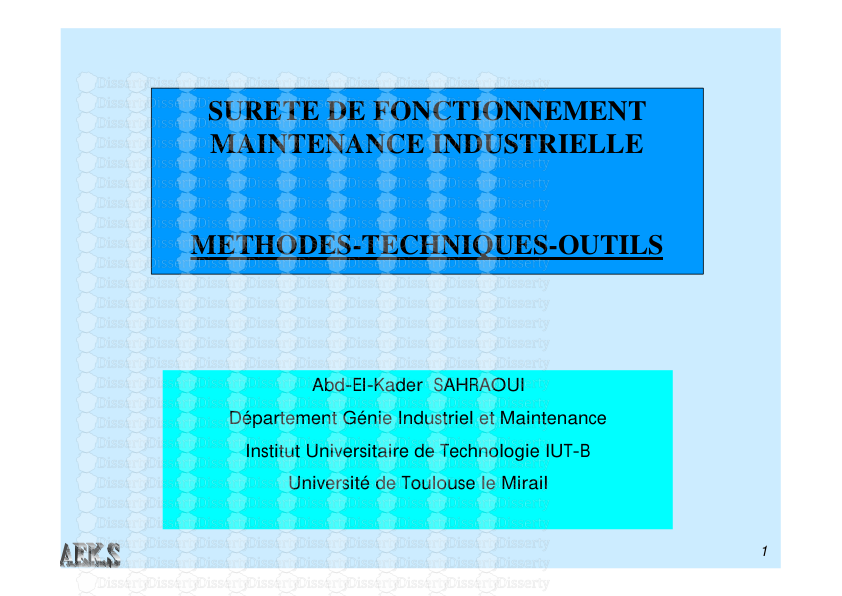
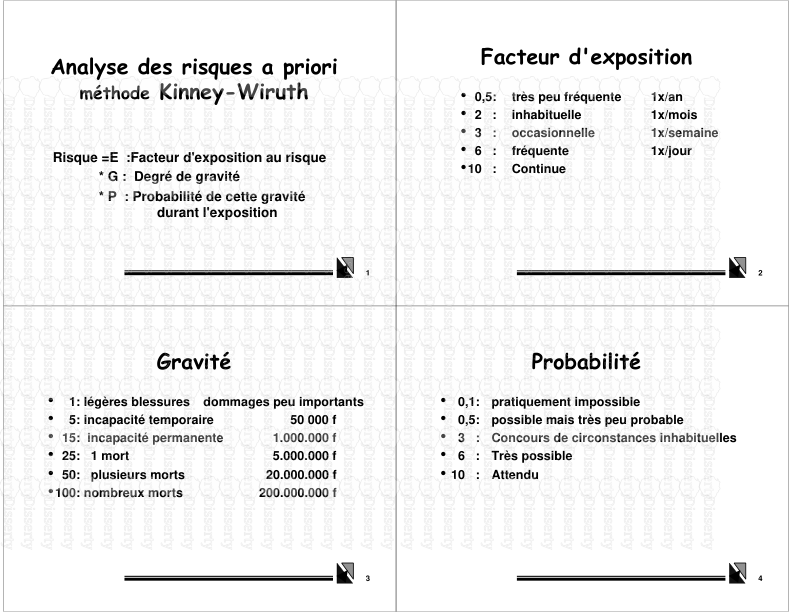
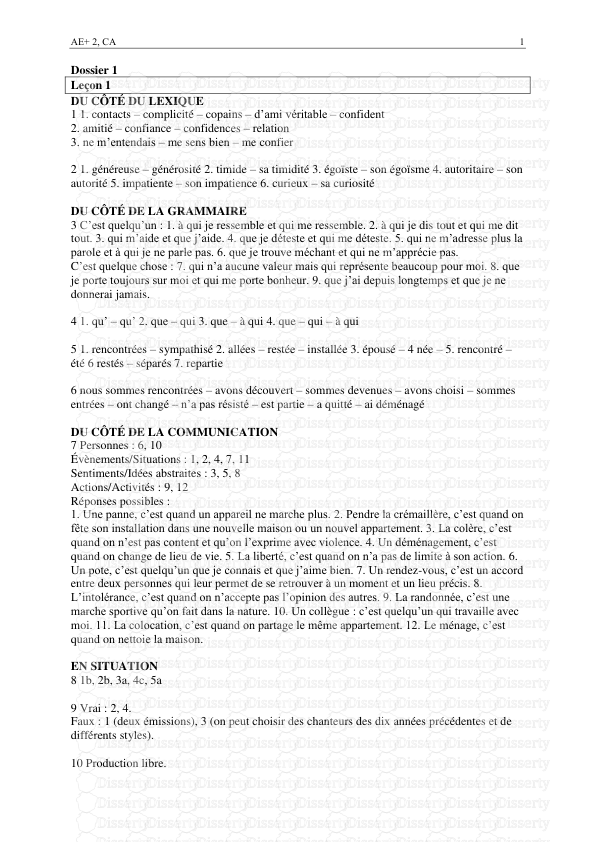
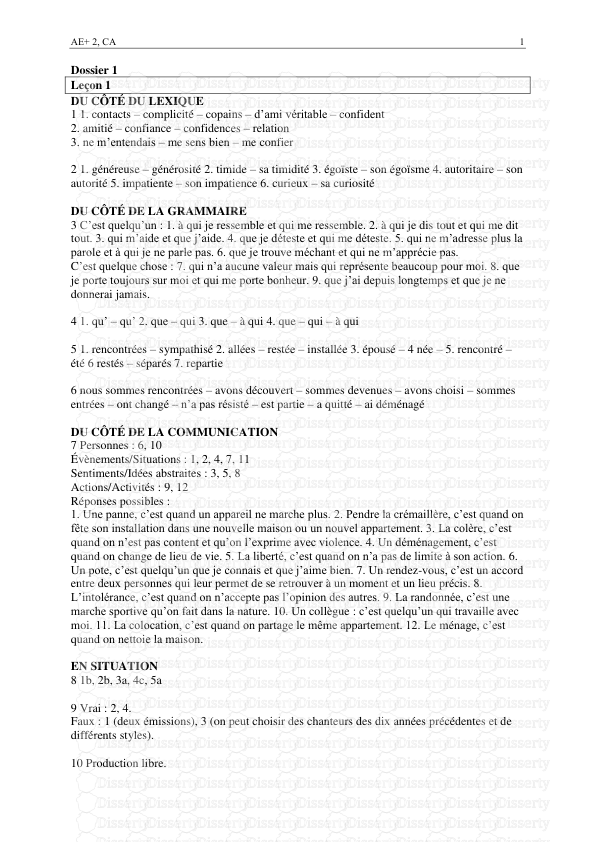
-
44
-
0
-
0
Licence et utilisation
Gratuit pour un usage personnel Attribution requise- Détails
- Publié le Mar 18, 2021
- Catégorie Management
- Langue French
- Taille du fichier 0.0680MB