205 Chapitre 7 Management des ressources de la production (MRP2) 1. Gestion des
205 Chapitre 7 Management des ressources de la production (MRP2) 1. Gestion des stocks et MRP2 1.1 Limites des méthodes traditionnelles de gestion des stocks Les méthodes traditionnelles de gestion des stocks décrites au chapitre 5 ont toutes les caractéristiques suivantes : • Les articles sont gérés indépendamment les uns des autres. • On suppose implicitement que la consommation antérieure de chacun des articles se répétera dans le futur. • En supposant que l’on ait effectivement besoin dans le futur de chaque article, on ne se préoccupe pas de la date où ce besoin sera effectif. Gestion de production 206 © Éditions d’Organisation Il en résulte notamment, en cas d’arrêt de la vente d’un produit, une stabilisation du système dans un état où les stocks intermédiaires sont pleins et, inversement, en cas d’augmentation brutale des ventes, une certaine inertie de réaction du système avec risque de ruptures. Ces limitations ont conduit à mettre au point à partir de 1965 aux États-Unis un concept de gestion de la production permettant d’antici- per les besoins exacts avec leur décalage dans le temps. Cette méthode a été initialement appelée MRP (pour Material Requirements Planning, soit « calcul des besoins nets »). Par la suite, une évolution en plu- sieurs étapes a permis d’aboutir au concept de MRP2, où les mêmes initiales ont une signification bien plus globale : Manufacturing Resource Planning que l’on peut traduire par « Management des Res- sources de la Production ». Nous reviendrons par la suite sur cette pro- gression du concept, mais il importe immédiatement de souligner qu’il est nécessaire de préciser, lorsqu’on parle de MRP, de quel stade il s’agit. Ainsi, bon nombre d’entreprises et de logiciels estiment « faire du MRP » dès qu’un calcul des besoins est effectué, alors que mainte- nant le concept MRP doit être appliqué uniquement dans le sens global MRP2 ! 1.2 Schéma global de MRP2 Le concept MRP2 permet de gérer la production depuis le long terme jusqu’au court terme. C’est également une méthode de simulation de l’activité industrielle qui permet de répondre à la question générale « Que se passe-t-il si ? » C’est un outil de communication entre les diverses fonctions de l’entre- prise, notamment les fonctions Commerciale et Production. Il permet à tous les services de l’entreprise de gérer la production en parlant un langage commun. Le schéma 7.1 illustre le principe général de MRP2, avec la planifica- tion déduite de la gestion de la demande (prévisions commerciales et commandes des clients) et l’exécution. Management des ressources de la production (MRP2) 207 © Éditions d’Organisation Figure 7.1 – Principe général MRP2 La figure 7.2 détaille le schéma précédent en présentant les trois niveaux de la planification. Il précise, en outre, l’indispensable gestion des charges et des capacités qui permet de valider chaque niveau afin de maintenir un degré de réalisme indispensable au bon fonctionne- ment du système. Figure 7.2 – Schéma MRP2 avec les trois niveaux de planification Gestion de la demande Planification Plan stratégique Exécution Plan industriel et commercial Prévisions commerciales Programme directeur de production Calcul des besoins nets Charges globales Charges globales Charges détaillées Gestion d'atelier Plan stratégique Gestion de production 208 © Éditions d’Organisation 1.3 Principe d’Orlicky Une entreprise fabrique et achète des articles selon ses besoins ; c’est en tous cas ce qu’elle devrait faire ! Le concept MRP est consécutif à la mise en évidence, par Joseph Orlicky, de la répartition de ces besoins en deux types fondamentaux : les besoins indépendants et les besoins dépendants. Les besoins indépendants sont ceux qui proviennent de l’extérieur de l’entreprise, indépendamment de sa volonté propre. Il s’agit de façon typique des produits finis et des pièces de rechange achetés par les clients de l’entreprise. Les besoins dépendants, au contraire, sont générés par les précédents. Ils proviennent donc de l’intérieur de l’entreprise elle-même. Il s’agit des sous-ensembles, composants, matières premières..., entrant dans la composition des produits vendus. Ces deux types de besoin exigent un traitement totalement différent, exprimé dans le principe d’Orlicky : Figure 7.3 – Besoins indépendants et besoins dépendants Les besoins indépendants ne peuvent être qu’estimés par des prévisions. Les besoins dépendants, au contraire, peuvent et doivent être calculés (figure 7.3). Clients Automobile Besoins indépendants Prévus Besoins dépendants Calculés Constructeur Calcul des besoins nets Carrosserie Vitres Roues Moteur … Management des ressources de la production (MRP2) 209 © Éditions d’Organisation Les modes de gestion de ces deux types de besoin sont donc totale- ment différents, puisque dans le premier cas ils reposent sur des méthodes de prévision (chapitre 3) alors que, dans le second cas, ils font appel à la technique du calcul des besoins nets (voir section ci- après). Ainsi, pour la voiture de la figure 7.3, des prévisions de ventes seront à la base de l’estimation du volume de production nécessaire en véhicules. Quant aux composants, les quantités à fabriquer ou acheter, nécessaires pour assembler ces véhicules, seront calculées en se fon- dant sur les nomenclatures (voir chapitre 6). Il faut dès à présent remarquer que certains articles peuvent avoir des besoins à la fois indépendants et dépendants. Ainsi, un article peut entrer dans la composition d’un produit (besoin dépendant) et être également vendu en pièce de rechange (besoin indépendant). 2. Le calcul des besoins nets (CBN) 2.1 Généralités Comme cela a été précisé au début de ce chapitre (§ 1.1, « Limites des méthodes traditionnelles… »), historiquement, MRP2 a été initié par le calcul des besoins nets. Et même si ce calcul doit être précédé par une planification plus globale, le calcul des besoins nets constitue le cœur de MRP2. Une étude détaillée du management des ressources de pro- duction doit donc s’y intéresser en premier lieu. Le calcul des besoins nets a pour objet de définir, à partir des besoins indépendants, l’ensemble des besoins dépendants. Il fournit les appro- visionnements et lancements de fabrication de tous les articles autres que les produits finis, dans les périodes à venir. Il vérifie en outre la cohérence des dates de livraison et des dates de besoin, notamment si les besoins changent ou sont décalés dans le temps. Gestion de production 210 © Éditions d’Organisation Pour effectuer le calcul des besoins nets, il faut connaître l’échéancier des besoins en produits finis (quantités et dates de besoin). Nous ver- rons par la suite que c’est le programme directeur de production qui donne ces indications et qui constitue donc le point de départ du cal- cul des besoins nets. Voici les informations nécessaires lors du calcul : • les nomenclatures donnant les constituants de chaque article ; • les délais d’obtention des articles (délais de fabrication, d’assem- blage ou d’approvisionnement de produits achetés) ; • les ressources constituées par les articles en stock ou les articles qui vont être disponibles (ordres de fabrication lancés, ordres d’achat en cours et ordres planifiés fermes, c’est-à-dire figés par le gestionnaire) ; • les règles de gestion fixées comme la taille de lot et éventuelle- ment la valeur d’un stock de sécurité ou d’un taux de rebut. Les résultats du calcul des besoins nets sont : • des ordres proposés, c’est-à-dire des lancements prévisionnels en fabrication ou des approvisionnements prévisionnels ; • des messages proposant au gestionnaire les actions particulières à mener (lancer, avancer, reporter un ordre de fabrication) en vue d’une bonne gestion de la production prévue. 2.2 Échéancier du calcul des besoins L’échéancier du calcul des besoins de chaque article géré revêt la forme d’un tableau, représenté à la figure 7.4. Les colonnes correspon- dent aux périodes successives à partir de la date actuelle. La valeur de la période dépend du délai de production dans le processus considéré ; elle est couramment d’une semaine mais peut être d’un jour. L’horizon de planification correspond au nombre de périodes pour lesquelles on effectue le calcul des besoins. Il est évidemment lié au délai d’obten- tion des produits finis et à la position de l’article considéré dans la nomenclature du produit fini. Il peut être par exemple d’un an. Management des ressources de la production (MRP2) 211 © Éditions d’Organisation Figure 7.4 – Échéancier du calcul des besoins nets Dans les colonnes, toutes les valeurs sont valables en début de période, sauf le stock prévisionnel : les « besoins bruts » doivent être satisfaits en début de période, les « ordres lancés » (en attente de production ou achats en cours de livraison) sont disponibles en début de période, les « ordres proposés » ont des dates de début et fin en début de période, et en revanche les « stocks prévisionnels » donnent la valeur en fin de période. Un tel tableau va permettre d’effectuer le calcul en se plaçant au début de la première période. En tête du tableau figurent : • Le stock de départ (St = 150) qui est le stock réel d’articles au moment du calcul. Avec les conventions indiquées, nous plaçons le stock actuel dans la case située à gauche de la première période, sur la ligne stock prévisionnel. • La taille de lot (L uploads/Management/gestion-de-production-planification.pdf
Documents similaires
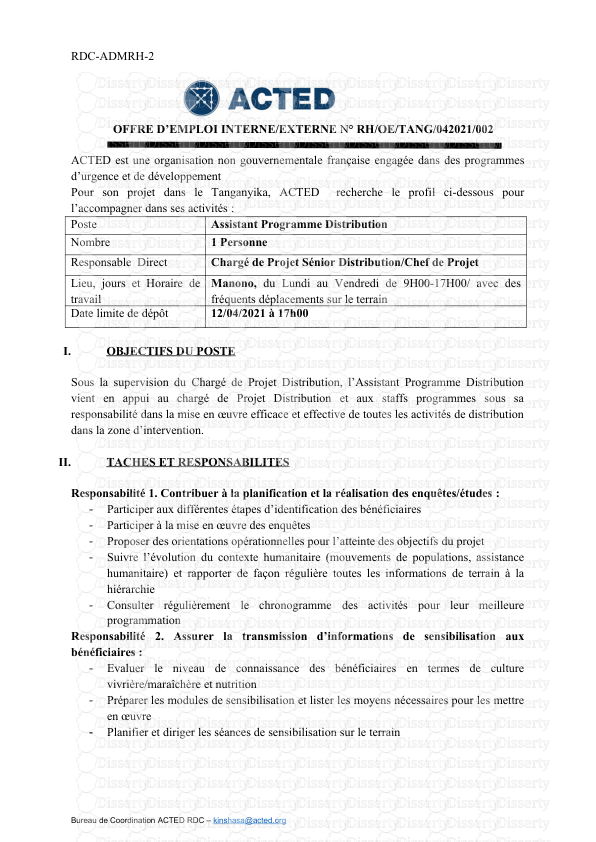
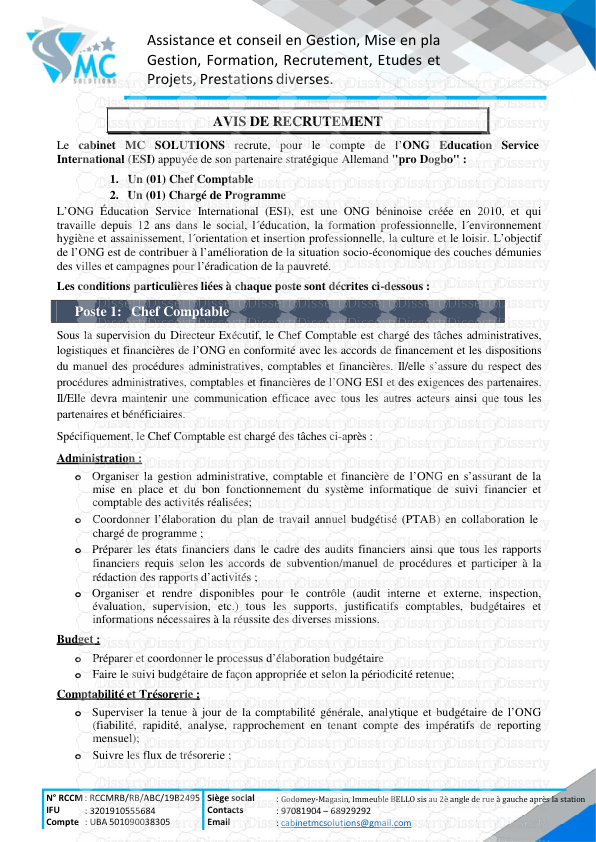
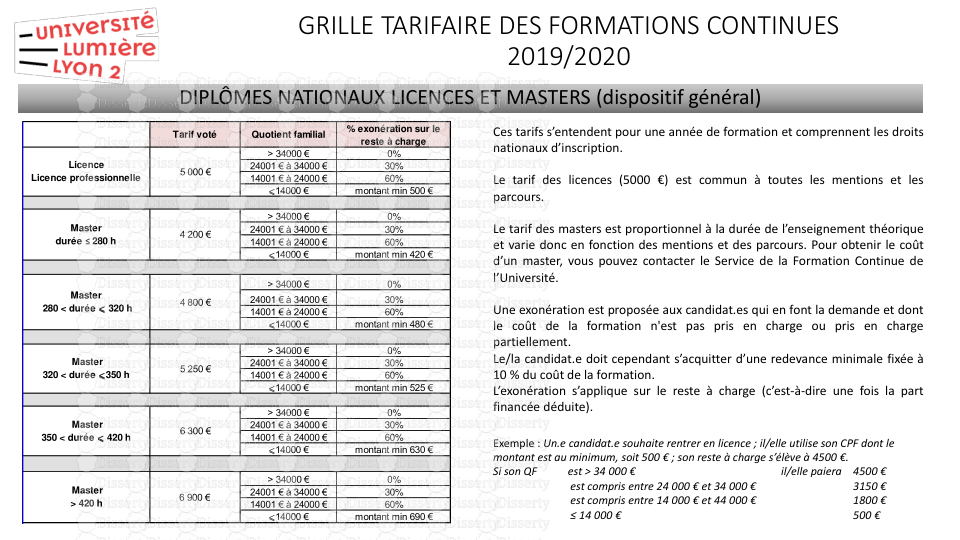
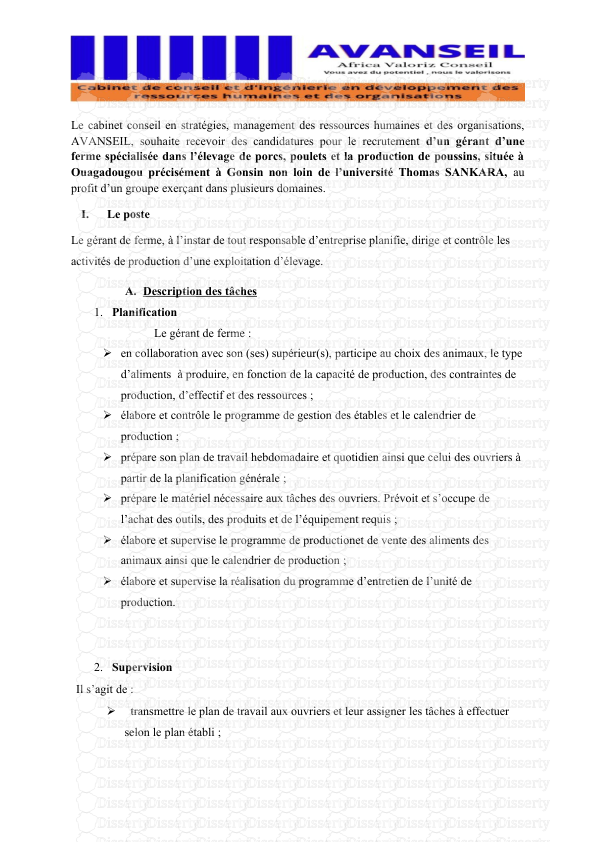
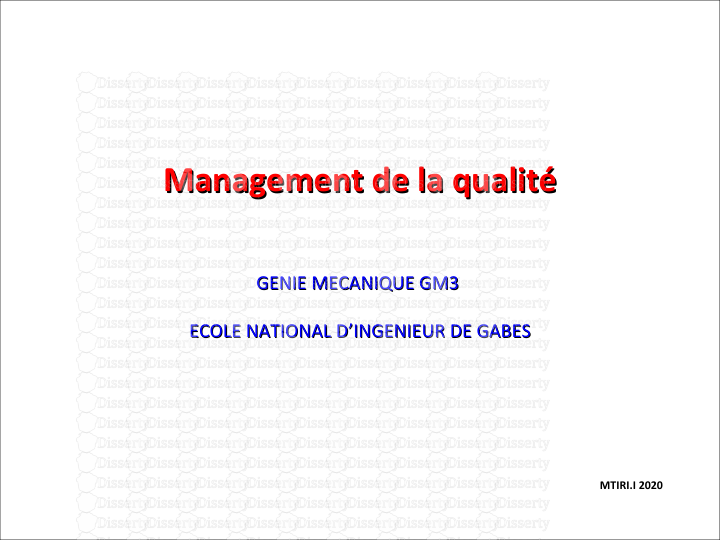
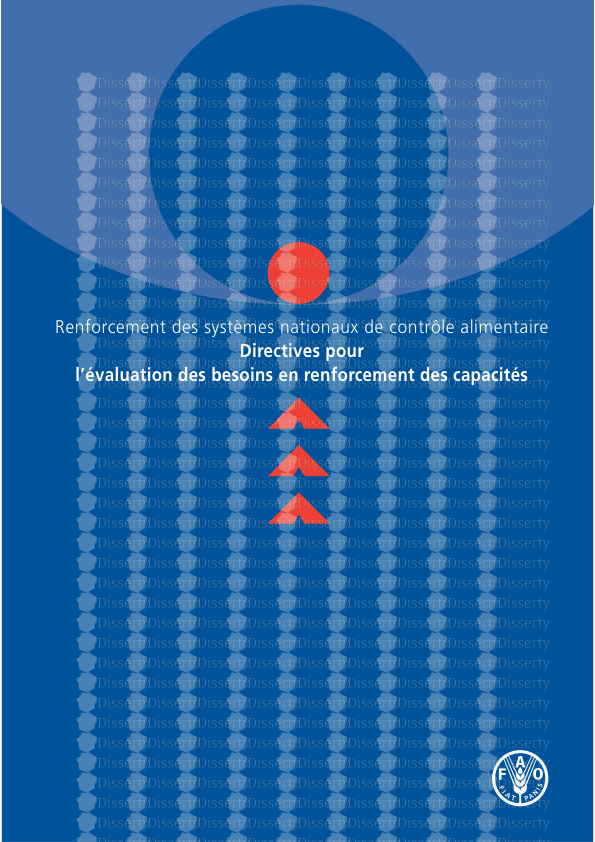
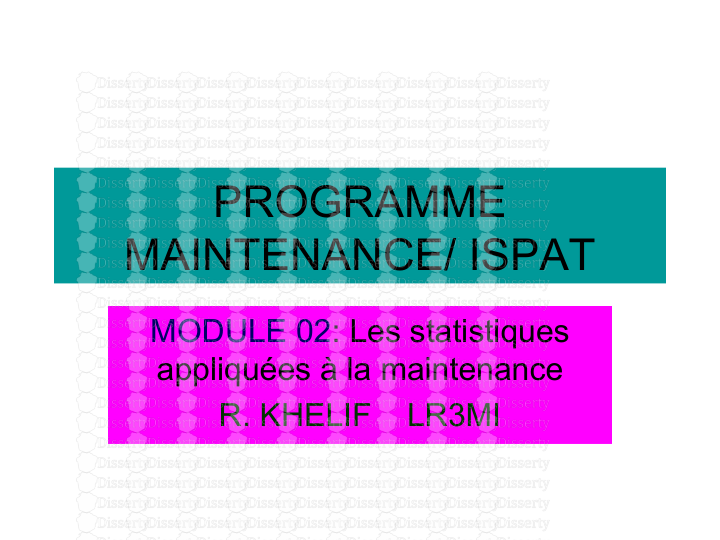
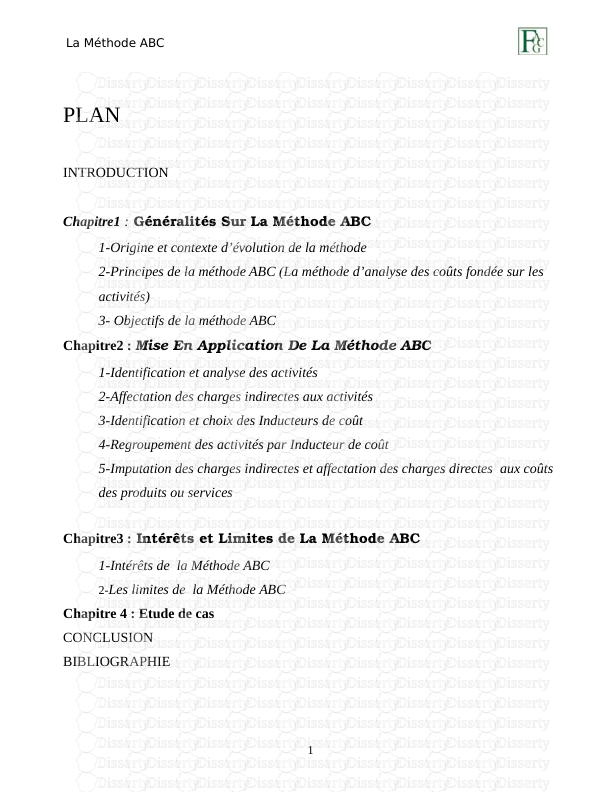
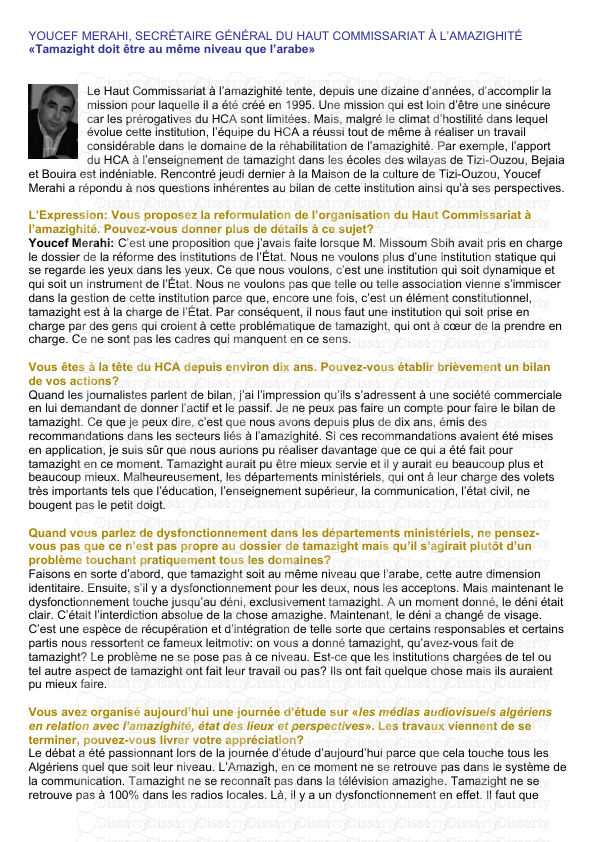
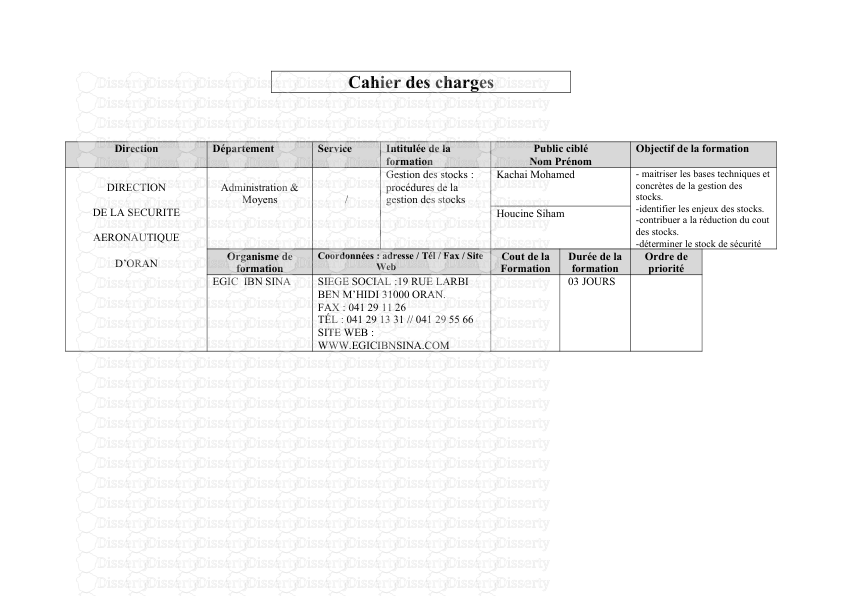
-
69
-
0
-
0
Licence et utilisation
Gratuit pour un usage personnel Attribution requise- Détails
- Publié le Fev 11, 2021
- Catégorie Management
- Langue French
- Taille du fichier 0.4545MB