Human Factors Guide for Aviation Maintenance and Inspection TABLE OF CONTENTS C
Human Factors Guide for Aviation Maintenance and Inspection TABLE OF CONTENTS Chapter 1: Human Factors……………………………………………………………………………………….…………1 Introduction………………………………………………………………………………………………………………….……….1 Regulatory Requirements………………………………………………………………………….………………...……….4 Concepts……………………………………………………………………………………………………………………….…..….6 Methods………………………………………………………………………………………………………………………………..8 Guidelines………………………………………………………………………………………………………………………….....13 Where to Get Help………………………………………………………………………………………………………………..21 Example Scenario………………………………………………………………………………………………………………….22 References…………………………………………………………………………………………………………………………...23 Chapter 2: Establishing a Human Factors Program…………………………………………………………….24 Landing Page………………………………………………………………………………………………………………………..24 Introduction………………………………………………………………………………………………………………………….25 Regulatory Requirements…………………………………………………………………………………………….……….26 Concepts……………………………………………………………………………………………………………………………….27 Methods……………………………….……………………………………………………………..……………………………….30 Guidelines…………………………………………………………………………………………………………………………….33 Where to Get Help……………………………………………………………………………………………………………….36 Example Scenario…………………………………………………………………………………………………………………37 References…………………………………………………………………………………………………………………………..38 Chapter 3: Fatigue and Fitness for Duty…………………………………………………………………………….39 Landing Page………………………………………………………………………………………………………………………..39 Introduction………………………………………………………………………………………………………………………...39 Regulatory Requirements……………………………………………..……………………………………………………..41 Concepts………………………………………………………………………………………………………………………………42 Methods…………………………………………………………….……………………………..…………………………………46 Guidelines…………………………………………………………………………………………………………………..……….51 Where to Get Help…………………………………………………..………………………………………………………….54 Example Scenario…………………………………………………………………………….………………………………….54 References………………………………….……………………………………………………………………………………….55 Chapter 4: Facility Design/Usability………………………………………………………………………………….56 Landing Page…………………………………………………………………………………………………..…………………..56 Introduction……………………………………………………………………………………………………………………..….57 Regulatory Requirements…………………………………………………………………………………..……………....58 Concepts………………………………………………………………………………………………………………………..…...59 Methods……………………………………………………………………………………………………………………………...63 Guidelines…………………………………….……………………………………………………………………………..……...64 Where to Get Help………………………………………………………………………………………………..……….…...87 Example Scenario………………….…………………………………………………………………………………...……….88 References…………………………………………………….…………………………………………………………………….89 Chapter 5: Shiftwork and Scheduling………………………………………………………………….…………….90 Landing Page………………………………………………………………………………………….…………………………...90 Introduction………………………………………………………………………………..………….……………………………90 Regulatory Requirements…………………………………………………………………………………….……………91 Concepts…………………………………………………………………………………………………………………………...91 Methods…………………………………………………………………………………………………………………………....95 Guidelines……………………………………………………………………………………….…………………………………97 Where to Get Help…………………………………………………………………………………………………………….106 Example Scenario………………………………………………………………………………………………...……………107 References………………………………………………………………………………………………………………….……..108 Chapter 6: Procedures/Technical Documentation………………………………….……….…..………….109 Landing Page…………………………………………………………………………………..………………………….………109 Introduction…………………………………………………………………………………………………………….………….109 Regulatory Requirements…………………………………………………………………………………………………..113 Concepts…………………………………………………………………………………………………………….…..………….114 Methods………………………………………………………………………………………………………….………………….116 Guidelines…………………………………………………………………………………………………………………………..121 Where to Get Help……………………………………………………………………………………………………………..133 Example Scenario……………………………………………………..………………………………………………………..134 References………………………………………………………………………………………………………………………….136 Chapter 7: Error and Error Reporting Systems……………………………………………….…….….………137 Landing Page…………………………………………………………………………………..………………………………….137 Introduction………………………………………………………………………………………………………………………..138 Regulatory Requirements……………………………………………………………………………………………………139 Concepts……………………………………………………………………………………………………………………………..140 Methods…………………………………………………………………………………………………….………………………..142 Guidelines………………………………………………………………………………………………………….………………..147 Where to Get Help……………………………………………………………………………………………..………….……163 Example Scenario………………………………………………………………………………………………………………..164 References…………………………………………………………………………………………………………………………..170 Chapter 8: Technical Writing…………………………………………………………………………………………….171 Landing Page…………………………………………………………………………………..……….………………………….171 Introduction………………………………………………………………………………………………..……………………….171 Regulatory Requirements…………………………………………………………………………………………………….173 Concepts………………………………………………………………………………………………………………………………175 Methods…………………………………………………………………………………………………..………………………….177 Guidelines……………………………………………………………………………………………………..………..…………..179 Where to Get Help……………………………………………………………………………………………………………….184 Example Scenario…………………………………………………………………………………………………………………185 References…………………………………………………………………………………………………………………………..186 Chapter 9: Workplace Safety…………………………………………………….………………………………………187 Landing Page…………………………………………………………………………………..…………………………………..187 Introduction………………………………………………………………………………………………………………………….187 Regulatory Requirements…………………………………………………………………………………………………....188 Concepts………………………………………………………………………………………………………………..…………….188 Methods…………………………………………………………………………………………………………………………….…193 Guidelines…………………………………………………………………………………………………………………………….195 Where to Get Help……………………………………………………………………………………………………………..219 Example Scenario……………………………………………………………………………………………………………….221 References………………………………………………………………………………………………………………………….222 Chapter 10: Communication…………………………………….………………………………………………………223 Landing Page…………………………………………………………………………………..………………………………….223 Introduction…………………………………………………………………………………..……………………………………223 Regulatory Requirements…………………………………………………………………………………..………………225 Concepts…………………………………………………………………………………..………………………………………..226 Methods…………………………………………………………………………………..…………………………………….....229 Guidelines…………………………………………………………………………………..………………………….……..…..234 Where to Get Help…………………………………………………………………………………..…………………...…..245 Example Scenario…………………………………………………………………………………..………………….………245 References…………………………………………………………………………………..…………..………………………..246 Chapter 11: Ethics in Maintenance………………………………………………………………………………….247 Landing Page…………………………………………………………………………………..………………………………...247 Introduction…………………………………………………………………………………..…………………………….…….248 Regulatory Requirements………………………..…………………………………………………………..……………248 Concepts…………………………………………………………………………………..……………………………………….249 Methods…………………………………………………………………………………...……………………………………….250 Guidelines…………………………………………………………………………………..…………….……………………….253 Where to Get Help…………………………………………………………………………………..……………………..…260 Example Scenario…………………………………………………………………………………..………………………….260 References…………………………………………………………………………………..………………………………….…265 Page 1 of 23 FAA Human Factors Guide for Aviation Maintenance and Inspection Chapter 1: Human Factors Author: Michael Maddox Affiliation: HumanCentric, Inc. Contact: mmaddox@humancentric.com Introduction This chapter describes some of the fundamental concepts in the field of Hu man Factors and how they apply to aviation maintenance. Used properly, hu man factors principles and methods can help aviation maintenance supervisors, engineers, technicians, and inspectors perform their jobs with more efficiently, more safely, and with less stress. In this Guide, the terms “human factors” and “ergonomics” are used interchangeably. Any meaningful distinction between the two terms has disappeared, at least for the purposes of the discussion related to aviation maintenance. Aviation maintenance has changed over the years. Newer aircraft contain mate rials, power plants, and electronic subsystems that did not exist in earlier mod els, and the number of older aircraft has increased. Technicians use more, and more sophisticated, equipment and procedures. While the aircraft on which they work have evolved dramatically over the last 50 years, maintenance workers still exhibit all of the capabilities, limitations, and idiosyncrasies that are part of being human. The nature of aviation maintenance is such that AMTs and inspectors often work under conditions that stress their physical, cognitive, and perceptual limits. Maintenance technicians, engineers, and inspectors sometimes work in cramped, awkward, or space-limited loca tions (Photo 1), they also work under intense time pressure, they work on com plex systems (Photo 2), they work both indoors and outdoors (Photo 3), and much of their work is done at night (Photo 4). Page 2 of 23 Chapter 1: Human Factors Photo 1. Working in an awkward position (note special rolling seat). Photo 2. Example of a complex system. Photo 3. Line maintenance outdoors on a ramp Page 3 of 23 Chapter 1: Human Factors The roots of Human Factors are firmly planted in aviation. The first identifiable work in the area of equipment design and human performance was done during World War II. Prior to the war-related research, most people held a fairly simplis tic view of how people interacted with their environment. The idea of humans as infinitely “flexible” seemed to guide most design. It soon became apparent, however, that human users’ interaction with their jobs and equipment is much more complex than we thought. Photo 4. Line maintenance at night. Over the last 20-30 years, aircraft have become more and more reliable. These improvements are especially notable for engines. During that same period, air craft operation has become safer due to the increase in automated flight sup port systems and the diffusion of crew resource management (CRM) techniques throughout the industry. Because of these improvements, the locus of aviation accidents has slowly shifted to improper ground operation and to maintenance, Some estimates now place maintenance errors as the root cause of 20-30% of serious aviation incidents. Beginning with the Aloha Airlines mishap in 1988, the Federal Aviation Admin istration (FAA), along with international regulators and industry organizations, have focused on the design of maintenance tasks, equipment, and training. Page 4 of 23 Chapter 1: Human Factors To be sure, most human factors research in the aviation domain has focused on flight crews, operational procedures, and flight deck design. However, over at least the last 15 years, EASA, the FAA, the Air Transport Association (ATA), and it’s international counterpart, the International Air Transport Association (IATA), have maintained active programs to perform human factors research, develop applica tions, and perform training related to human factors in aviation maintenance. Commercial aviation maintenance and training organizations have also devel oped training programs to support the EASA requirements regarding main tenance human factors. This Guide is part of the continuing emphasis being placed on human factors in aviation maintenance. In most respects, the international aviation regulatory authorities have taken the global lead in imposing human factors requirements on aviation maintenance organizations. The European Aviation Safety Authority (EASA), formerly the Joint Aviation Authority (JAA), is the European counterpart to the FAA. For a num ber of years, the predecessor to EASA required human factors training for all certified Aviation Maintenance Engineers (AMEs) and inspectors. AMEs are the equivalent of Aviation Maintenance Technicians (AMTs) in the United States. When the JAA was re-named EASA, human factors training requirements were made obligatory as part of the certification of aviation maintenance organiza tions. These requirements can be found in Part 145 Section ANNEX II, Section 30 (e) of the EASA regulations. Photo 5. Aloha Airlines B-737 after skin de-lamination. Regulatory Requirements Page 5 of 23 Chapter 1: Human Factors Until July, 2005, the Federal Aviation Regulations (FAR’s), which comprise Title 14 of the Code of Federal Regulations (CFR), did not contain explicit human factors requirements. Certain regulations related to maintenance “performance”, such as Parts 43.13 and 43.15, Part 121-Subpart L, and Part 135-Subpart J, are obviously based on human factors types of considerations. However, they do not invoke specific human factors guidelines or standards. In July, 2005, the FAA issued a Flight Standards Handbook Bulletin for Airtwor thiness (HBAW), Order 8300.10 – Appendix 3, that introduced a new human fac tors curriculum requirement in the approval process for Part 145 repair station training programs. The curriculum content mirrored that of the EASA human fac tors training curriculum requirements. In addition to the new handbook chapter, the FAA also issued Advisory Circular (AC) 145-10, which spelled out the position of the FAA regarding human factors as an integral component of Part 145 train ing programs. AC145-10 also explicitly concurred with the EASA position on the importance of human factors training for aviation maintenance. There are presently two other sources of regulatory requirements directly related to human factors in aviation maintenance. The first is the set of regulations that compose the Occupational Safety and Health Administration (OSHA) require ments. OSHA regulations are contained in the Code of Federal Regulations (CFR), Title 29, Parts 1900 to 1910. Only a small fraction of these regulations are directly related to human factors issues. Applicable sections of the OSHA regulations are cited in appropriate chapters of this Guide. The second source of human factors-related regulatory requirements is the Americans with Disabilities Act (ADA). This legislation mandates, among other things, that all employers must make “reasonable accommodations” for disabled workers. There are other implications of the ADA. For example, ADA provisions directly affect the processes of personnel selection and job assignment. Again, the relevant parts of the ADA are cited as appropriate in this Guide. (e) The organisation shall establish and control the competence of per sonnel involved in any maintenance, management and/or quality au dits in accordance with a procedure and to a standard agreed by the competent authority. In addition to the necessary expertise related to the job function, competence must include an understanding of the ap plication of human factors and human performance issues appropriate to that person’s function in the organisation. “Human factors” means principles which apply to aeronautical design, certification, training, operations and maintenance and which seek safe interface between the human and other system components by proper consideration of human performance. “Human performance” means human capabilities and limitations which have an impact on the safety and efficiency of aeronautical operations. Page 6 of 23 Chapter 1: Human Factors PEAR is an acronym for People, Environment, Actions, and Resources. These four components comprise the essence of what we are typically concerned about in the human factors world. While the “people” component is only one of four in the PEAR model, people are at the heart of the entire model. The science of Human Factors concerns itself primarily with people and how they interact with each other uploads/Philosophie/ hf-guide.pdf
Documents similaires
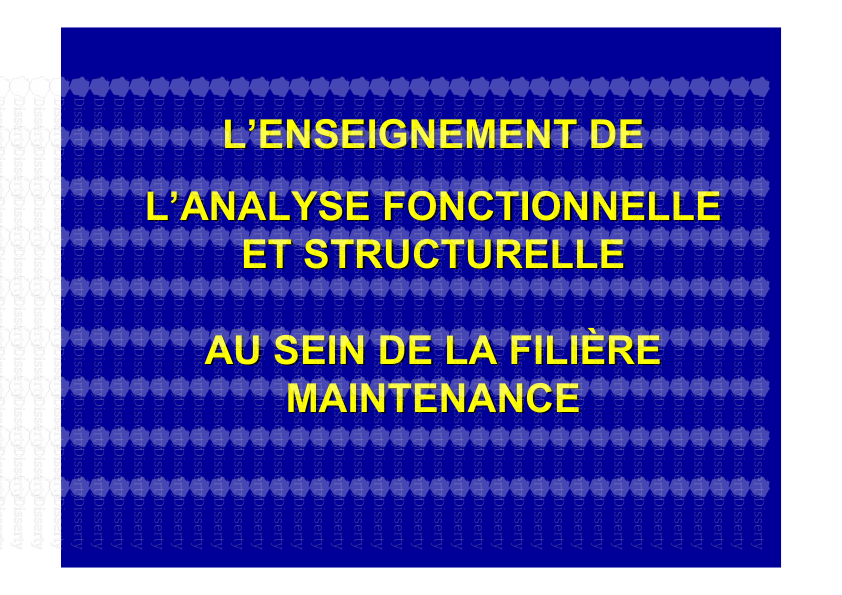
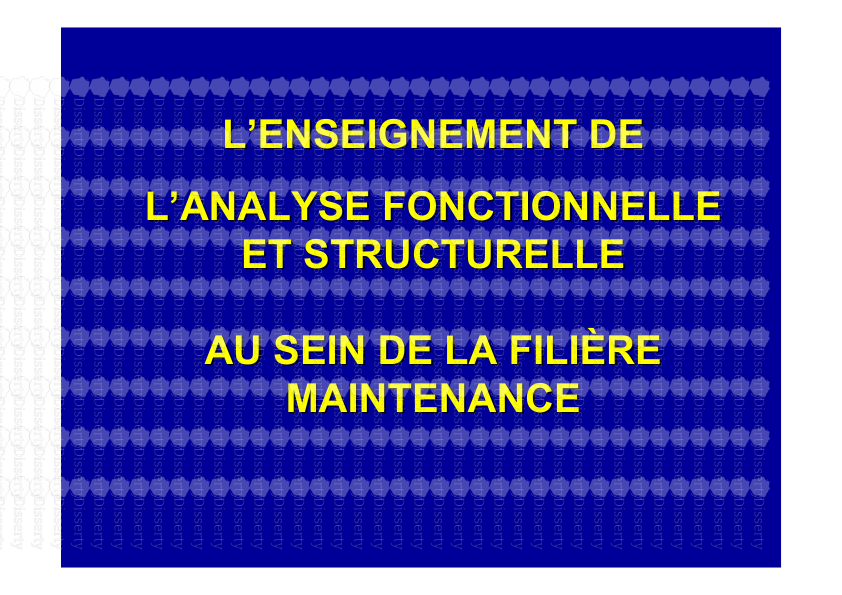
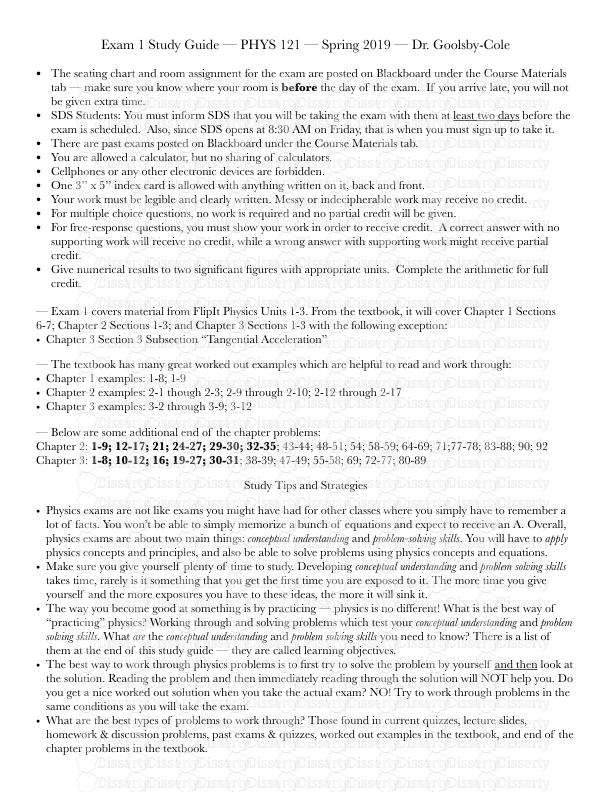
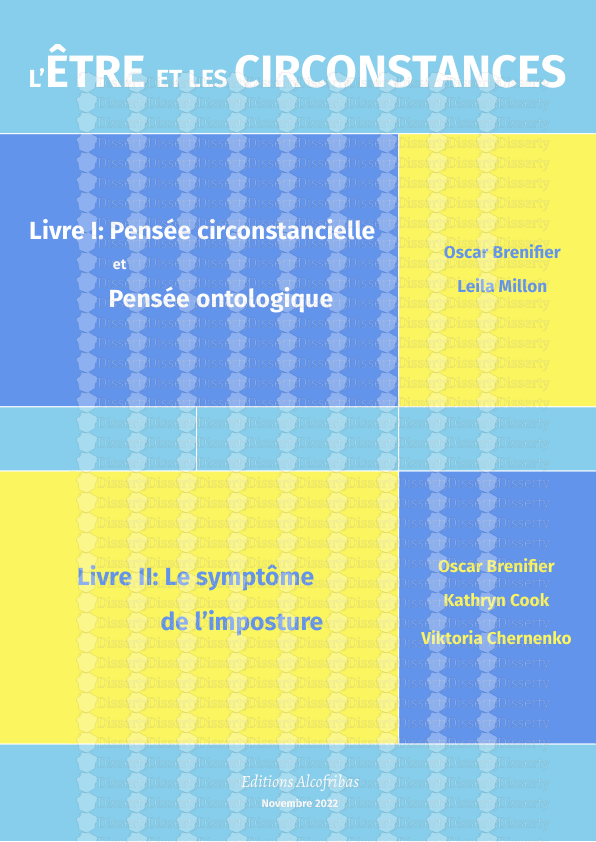
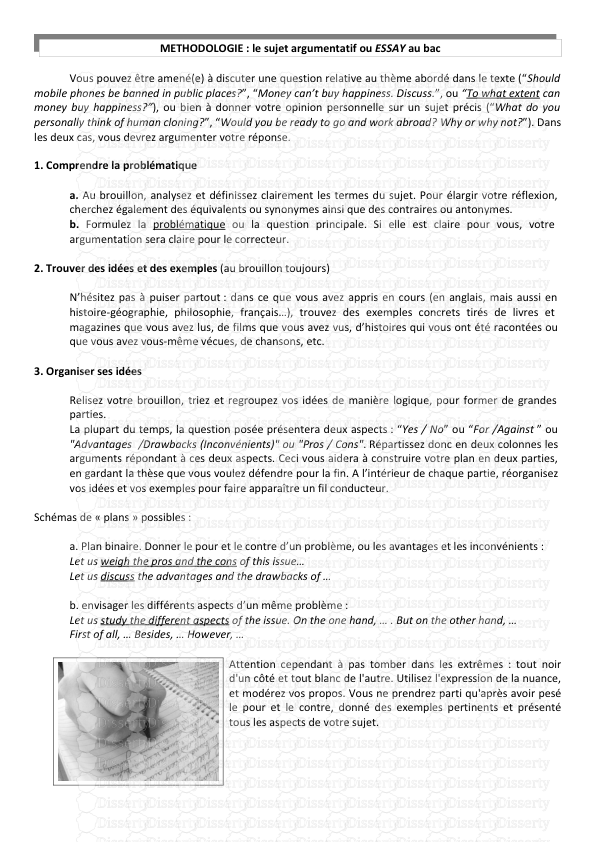
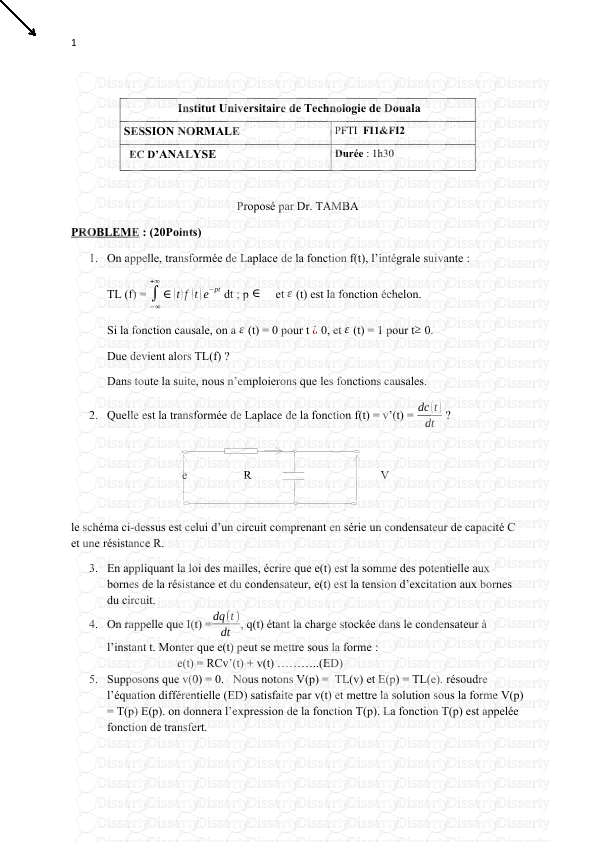
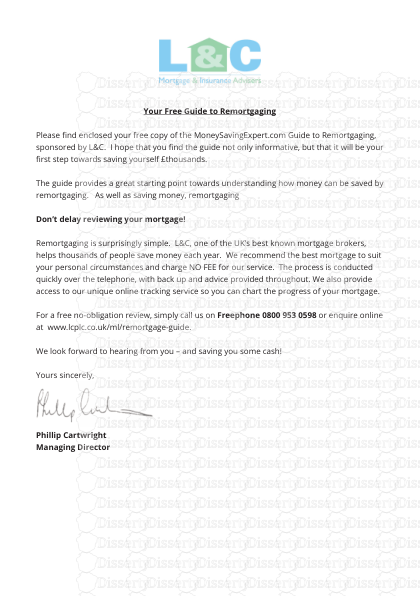
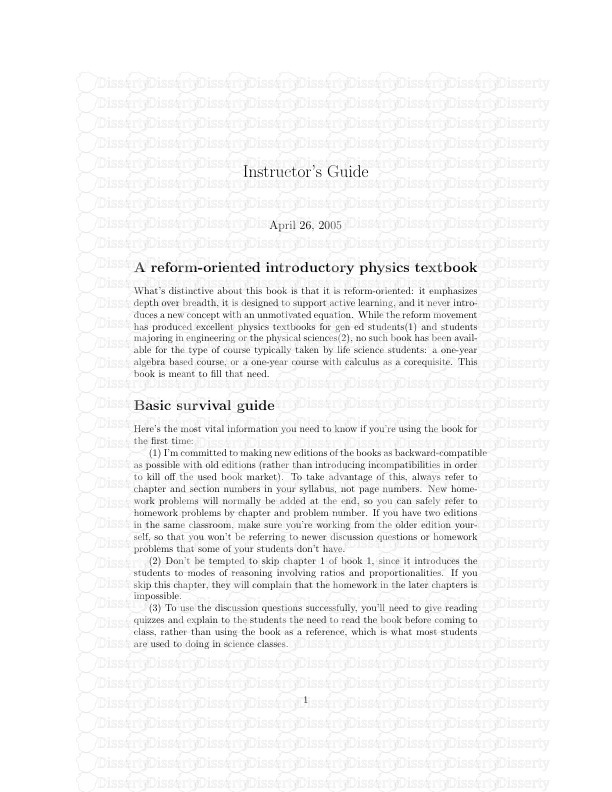
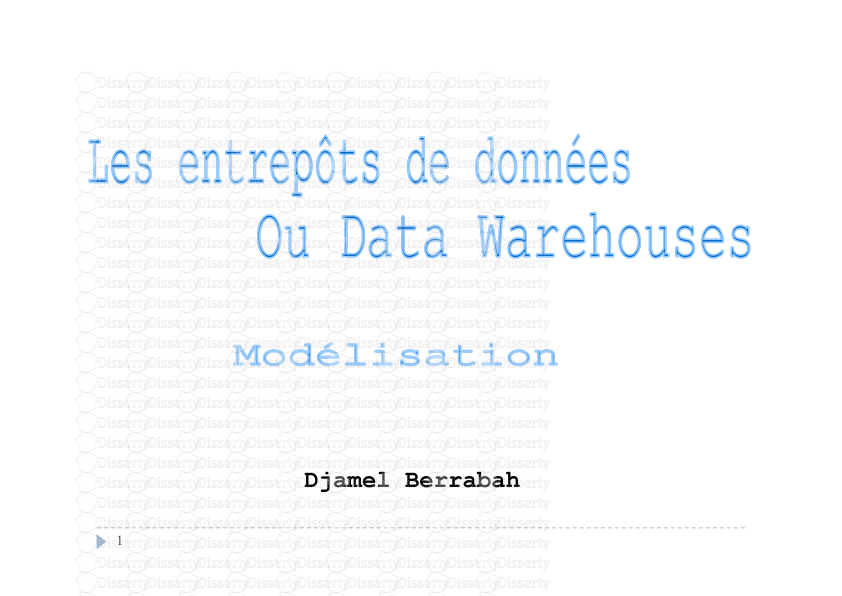
-
59
-
0
-
0
Licence et utilisation
Gratuit pour un usage personnel Attribution requise- Détails
- Publié le Sep 06, 2022
- Catégorie Philosophy / Philo...
- Langue French
- Taille du fichier 7.8097MB