50 2010; 12 (1) CJEM • JCMU ABSTRACT Objective: In recognition of patient wait
50 2010; 12 (1) CJEM • JCMU ABSTRACT Objective: In recognition of patient wait times, and deteriorat- ing patient and staff satisfaction, we set out to improve these measures in our emergency department (ED) without adding any new funding or beds. Methods: In 2005 all staff in the ED at Hôtel-Dieu Grace Hospi- tal began a transformation, employing Toyota Lean manufac- turing principles to improve ED wait times and quality of care. Lean techniques such as value-stream mapping, just-in-time delivery techniques, workplace organization, reduction of sys- temic wastes, use of the worker as the source of quality improvement and ongoing refinement of our process steps formed the basis of our project. Results: Our ED has achieved major improvements in depart- mental flow without adding any additional ED or inpatient beds. The mean registration to physician time has decreased from 111 minutes to 78 minutes. The number of patients who left without being seen has decreased from 7.1% to 4.3%. The length of stay (LOS) for discharged patients has decreased from a mean of 3.6 to 2.8 hours, with the largest decrease seen in our patients triaged at levels 4 or 5 using the Cana- dian Emergency Department Triage and Acuity Scale. We noted an improvement in ED patient satisfaction scores fol- lowing the implementation of Lean principles. Conclusion: Lean manufacturing principles can improve the flow of patients through the ED, resulting in greater patient satisfaction along with reduced time spent by the patient in the ED. Keywords: ED administration, Lean principles, length of stay, time to physician, wait time RÉSUMÉ Objectif : Compte tenu de la longueur des temps d’attente des patients et de la détérioration du niveau de satisfaction des patients et du personnel, nous avons cherché à améliorer ces mesures dans notre service d’urgence sans financement ou lits additionnels. Méthodes : En 2005, l’ensemble du personnel du service d’ur- gence de l’hôpital Hôtel-Dieu Grace a amorcé une transforma- tion, en appliquant les principes de production « au plus juste » de Toyota pour améliorer les temps d’attente et la qualité des soins. La base de notre projet était fondée sur les techniques au plus juste, comme la cartographie des flux de valeurs, la livraison juste-à-temps, l’organisation du milieu de travail, la réduction des gaspillages systémiques, le recours au tra- vailleur en tant que source d’amélioration de la qualité et l’amélioration constante des étapes de nos processus. Résultats : Notre service d’urgence a réalisé d’importantes améliorations en ce qui concerne le déroulement des activ- ités sans avoir ajouté de lits supplémentaires à l’urgence ou dans l’hôpital. La moyenne de temps entre l’inscription et la consultation du médecin a diminué, passant de 111 à 78 min- utes. Le nombre de patients quittant l’urgence sans avoir été vus par un médecin est passé de 7,1 à 4,3 %. La durée de séjour pour les patients qui ont obtenu leur congé a diminué, passant d’une moyenne de 3,6 heures à 2,8 heures. La plus forte baisse a été enregistrée chez les patients ayant un niveau de triage 4 ou 5, selon l’échelle canadienne de triage et de gravité pour les services d’urgence. Nous avons observé une amélioration des scores de satisfaction des patients à l’urgence après l’application des principes de pro- duction au plus juste. Conclusion : Les principes de production au plus juste peu- vent améliorer le déplacement des patients à l’urgence, occa- sionnant une hausse de la satisfaction et une baisse de la durée de séjour des patients à l’urgence. ORIGINAL RESEARCH • RECHERCHE ORIGINALE ED Administration Applying the Lean principles of the T oyota Production System to reduce wait times in the emergency department David Ng, MD; Gord Vail, MD, MSc; Sophia Thomas, MD; Nicki Schmidt, RN From the Emergency Department, Hôtel-Dieu Grace Hospital, Windsor, Ont. Submitted Feb. 21, 2007; Revised Oct. 17, 2009; Accepted Oct. 20, 2009 This article has been peer reviewed. CJEM 2010;12(1):50-7 INTRODUCTION Emergency department (ED) wait times have become a focus for the Canadian public, the media and the gov- ernment. Factors external to the ED, such as improving access to inpatient beds, developing overcapacity proto- cols, adding clinical decision units and reorganizing https://www.cambridge.org/core/terms. https://doi.org/10.1017/S1481803500012021 Downloaded from https://www.cambridge.org/core. Indian Institute of Technology - roorkee, on 07 Apr 2019 at 20:53:22, subject to the Cambridge Core terms of use, available at ambulance services have been proposed to improve ED patient flow.1,2 We have found few published reports that discuss improving internal ED efficiency to reduce wait times. Similar to most hospitals in Ontario, ED overcrowding and ambulance offload delay have been worsening at our site, due in part to a lack of available inpatient beds.2,3 Our ED had previously attempted var- ious solutions to improve wait times and attain recom- mended Canadian Emergency Department T riage and Acuity Scale (CTAS) wait time targets. Specifically, we increased the number of triage nurses and stations, added medical directives, increased physician staffing, hired a nurse practitioner and opened a fast track area. Despite these efforts there was little appreciable impact on overall ED wait times. In September 2005 our ED embarked on a makeover of our departmental processes, based on Lean manufacturing principles that were developed at the T oyota Motor Corporation.4 Lean techniques are widely used throughout the man- ufacturing industry to provide just-in-time delivery of product and ultimately to create value for the consumer using the least resources. These techniques have particu- lar relevance to the current medical system in Canada, where the demand is outpacing capacity to provide care in a timely manner. Lean techniques have been adopted in some hospitals.5,6 The product manufactured in the ED can be considered timely, accurate and empathetic medical care. “Lean” is a term related to philosophies derived from the T oyota Production System. The main goals of the Lean system are to create standardized work in order to smooth out the workflow and to eliminate wasteful steps in a process. The Lean system concen- trates on attaining continuous flow through a system by identifying value in each step of a process. If a step fails to add value or results in a redundancy to the next user in the process, it impedes quality and flow, and is elimi- nated (Box 1). By further reducing wait times between steps, and providing exactly what the next user in the process requires, quality and productivity improve. Lean thinking emphasizes identifying the root cause of a delay or problem by going to the worker and workplace to understand the demands of the work. Front-line workers are taught to identify waste, and to improve and stan- dardize their step in the process.7 Although many causes of ED overcrowding are a result of factors beyond the direct control of the ED, such as hospital inpatient capacity, there are factors within the scope of the department that could be changed to improve efficiency and patient satisfaction. The scope of our project involved improving the intradepartmental flow of patients discharged from a tertiary ED in Ontario. In our ED, approximately 85% of patients are treated and discharged. By applying Lean techniques to the population of dischargeable patients, we hypothesized we would improve ED efficiency and productivity, and ultimately reduce ED wait times and improve patient satisfaction. METHODS Setting and design We performed a before and after study. The ED of the Hôtel-Dieu Grace Hospital, in Windsor, Ont., is a regional trauma, cardiac, neurosciences, renal and psy- chiatric referral centre serving a population of 450 000. The annual census of the ED is approximately 55 000 visits. Intervention The project began with a scoping exercise that was facilitated by a Lean consultant, Dr. John Long, to determine the parameters, participants and goals. Those participating were emergency physicians; nurses; nurse practitioners; porters; clerks; cleaning staff; administrators; the ED director, unit manager and edu- cator; the hospital’s senior vice-president; and represen- tatives from diagnostic imaging, laboratory, respiratory therapy, home care and information services. All agreed that the focus would be CTAS-2 to -5 patients deemed at initial triage to be “dischargeable,” as opposed to CJEM • JCMU 2010; 12 (1) 51 Lean principles to reduce wait times in the ED Box 1. The 7 sources of waste, with selected examples relevant to the emergency department • Overproduction: creating more work than is required by the next step (e.g., over-triaging) • Motion: extra steps for the worker or moving machinery around (e.g., “Where’s the IV pole?”) • Waiting: time spent waiting for the next step in the process to occur (e.g., waiting for available bed, consultant, lab and diagnostic imaging results) • Conveyance: moving materials around (e.g., lab results on paper) • Processing: non–value added work steps (e.g., shuffling patients and stretchers to accommodate new arrivals) • Inventory: excessive stockpiling of materials (e.g., 1000 tongue depressors in a drawer and no gel) • Correction: reworking or scrapping work that has already been done (e.g., triage nurse reassessing patients in waiting room) IV = intravenous. https://www.cambridge.org/core/terms. https://doi.org/10.1017/S1481803500012021 Downloaded from https://www.cambridge.org/core. Indian Institute of Technology - roorkee, on 07 Apr 2019 at uploads/Sante/ applying-the-lean-principles-of-the-toyota-production-system-to-reduce-wait-times-in-the-emergency-department.pdf
Documents similaires
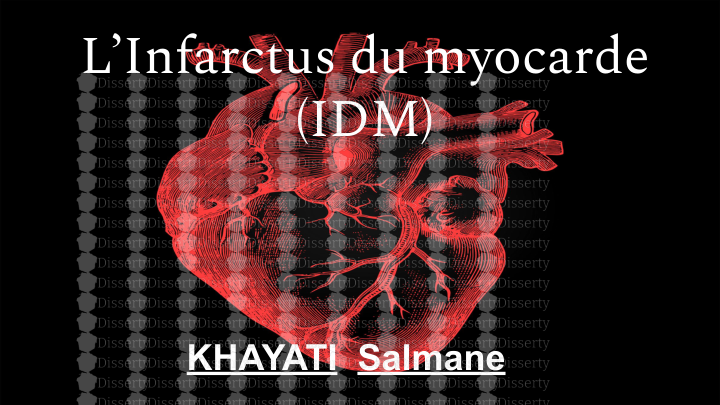
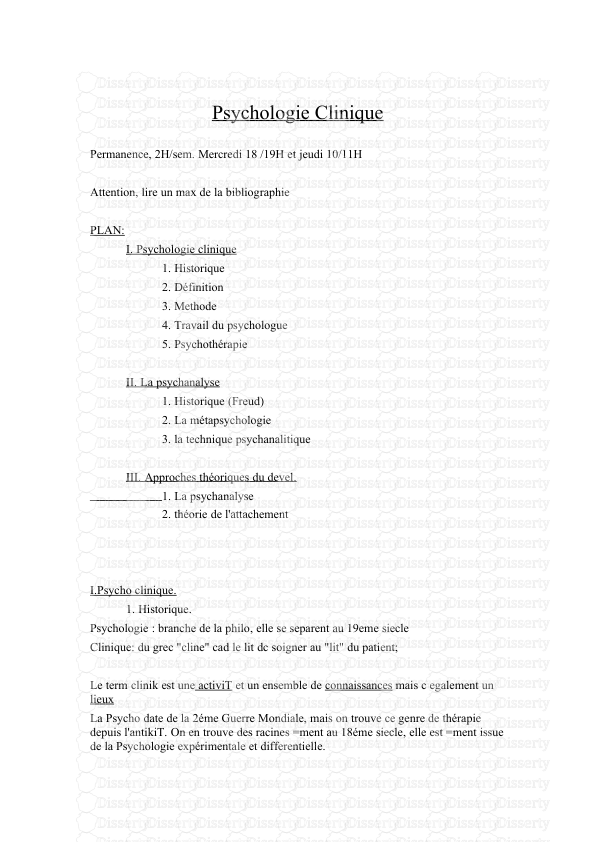
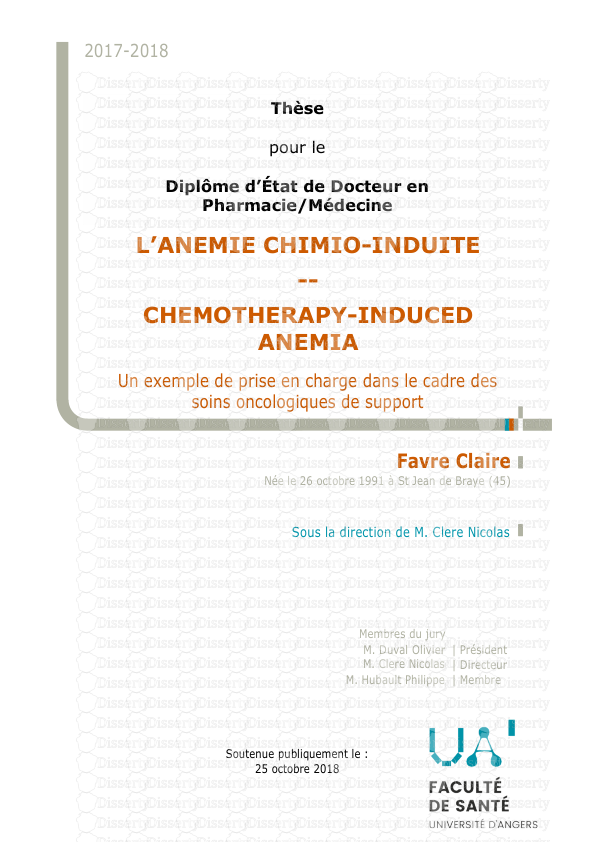
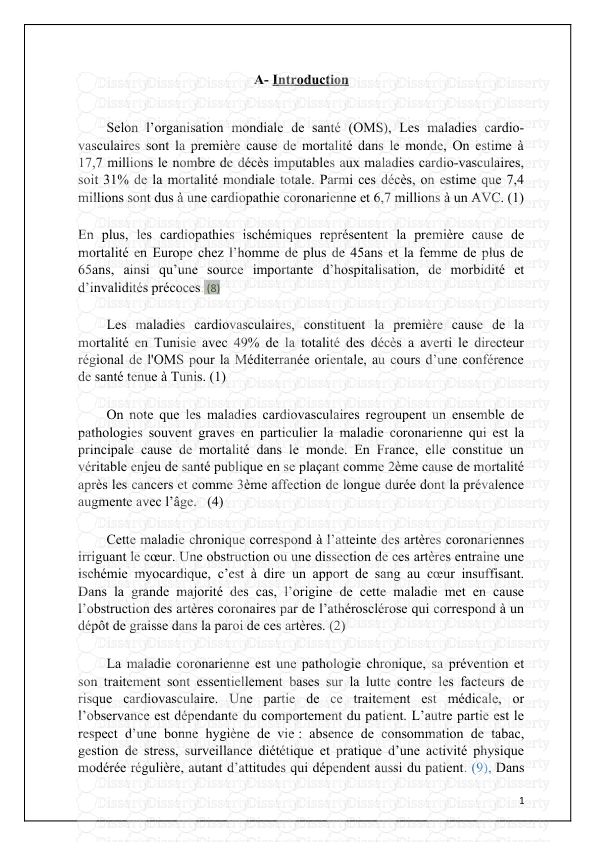
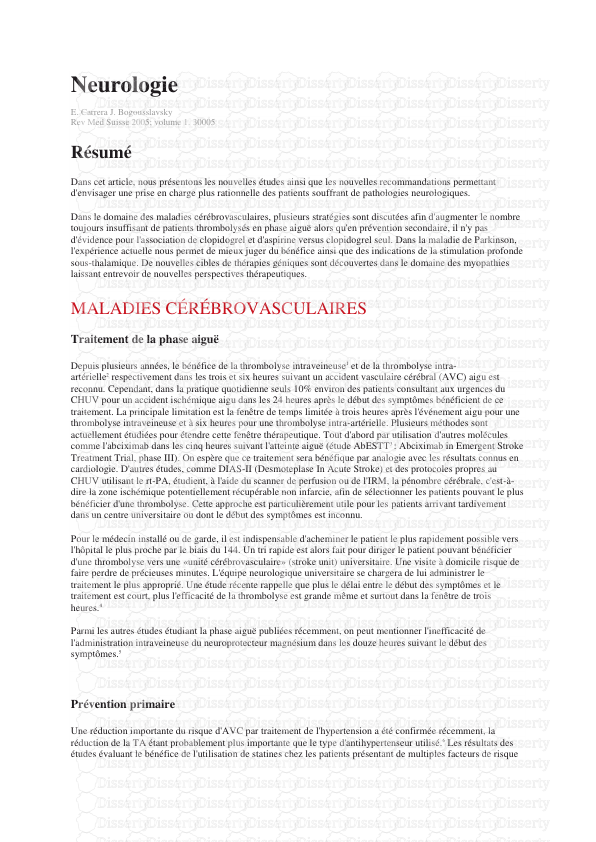
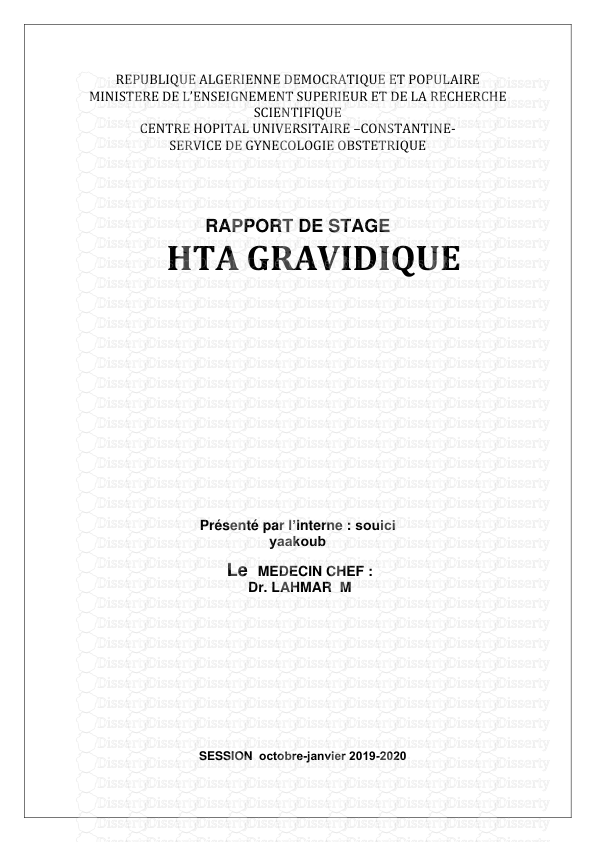

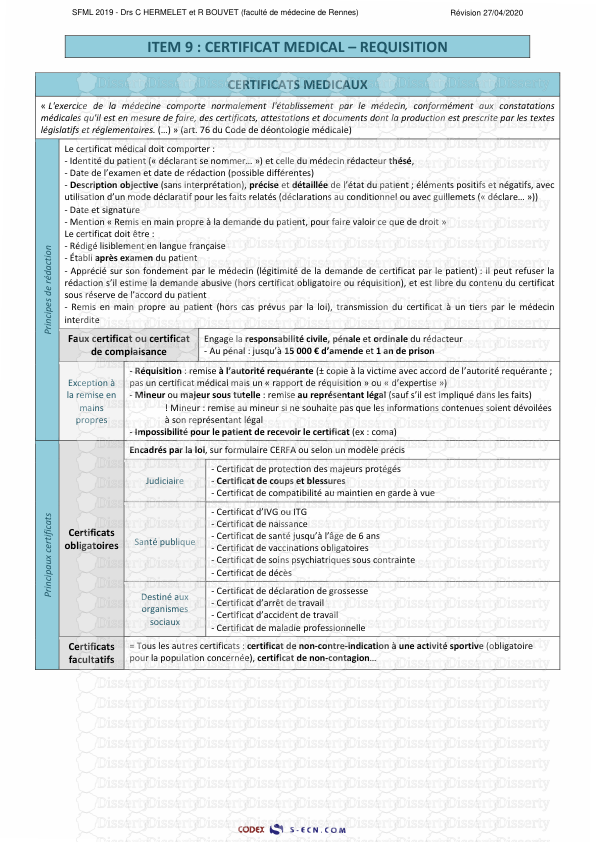
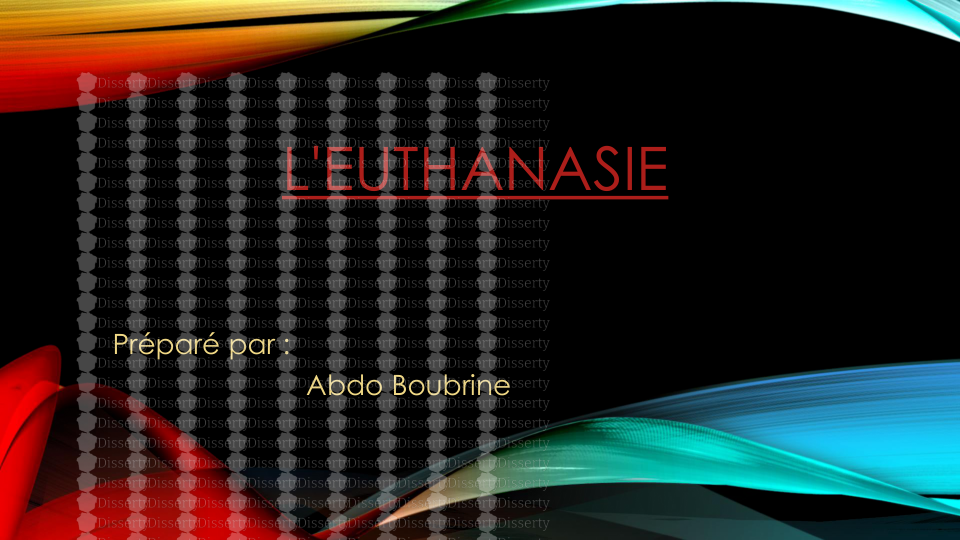
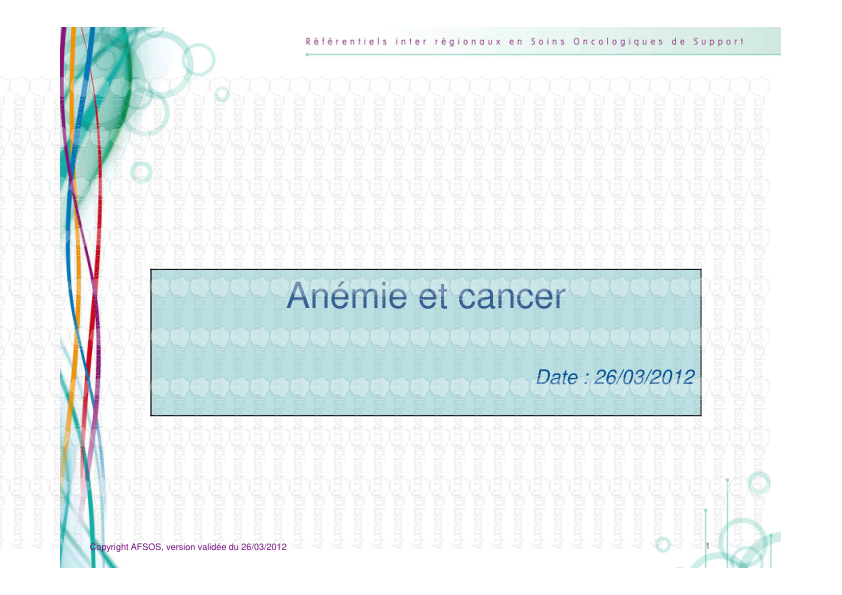
-
66
-
0
-
0
Licence et utilisation
Gratuit pour un usage personnel Attribution requise- Détails
- Publié le Jul 03, 2022
- Catégorie Health / Santé
- Langue French
- Taille du fichier 0.4084MB