CHAPITRES XXVI-XXVII : FONCTIONNEMENT, STRUCTURE ET COMPORTEMENT D’UNE CULASSE
CHAPITRES XXVI-XXVII : FONCTIONNEMENT, STRUCTURE ET COMPORTEMENT D’UNE CULASSE DE MOTEUR DIESEL (TD) A.-F. GOURGUES-LORENZON L’étude de cas constituant ce chapitre s’appuie sur la thèse de Bruno Barlas, soutenue à l’Ecole en 2004, en partenariat avec RENAULT, MONTUPET et l’UTC de Compiègne. Les questions sont en italiques. PARTIE 1 : ANALYSE DE LA CULASSE 1.1 Fonctions de la culasse Parmi plusieurs solutions « matériau », les alliages d’aluminium tels que celui étudié ici sont couramment utilisés pour fabriquer les culasses de moteur automobile telles que celle de la figure 1. Les conditions de fonctionnement sont les suivantes : Pression d’explosion du mélange carburant + air : 180 bar du côté de la chambre de combustion (« face feu ») Force de serrage sur le cylindre : jusqu’à 10 kN en traction sur chaque vis Montage des sièges de soupapes : par frettage Refroidissement par eau (« face eau ») Questions : Quelles sont les fonctions d’une culasse de moteur automobile ? Quelles sont les propriétés (mécaniques, thermiques...) demandées à la pièce ? Quel moyen de fabrication imagine-t-on d’utiliser pour une pièce de forme aussi complexe ? Figure 1 : Vue d’ensemble d’une culasse de moteur Diesel équipée. 1.2 Choix du matériau constitutif de la culasse Au vu des éléments de la question précédente, justifier le choix d’un alliage métallique, puis d’un alliage d’aluminium, puis d’un alliage d’aluminium de fonderie. Etant donnée la température de la face eau (100°C) et la température des gaz de combustion (> 1000°C), la température de la face feu de la culasse peut atteindre 280°C. Cette température vous parait-elle élevée pour cet alliage au regard notamment de la durée de vie du moteur ? Quels mécanismes physico-chimiques sont alors susceptibles de se produire ? Etude de cas : culasse de moteur Diesel (TD) 221 1.3 Zone critique et modes possibles de défaillance de la culasse Le pontet intersoupapes (figure 2) est une zone étroite qui, de ce fait, est relativement éloignée des circuits de refroidissement de la culasse. Elle a donc tendance à être davantage chauffée que les zones avoisinantes, qui sont plus massives et mieux refroidies, lors du fonctionnement du moteur. En assimilant cette partie de la pièce à deux zones (le pontet et la zone avoisinante) et en supposant qu’il n’y a aucune contrainte interne au début du fonctionnement du moteur neuf, caractériser le chargement mécanique (ici, thermomécanique) du pontet au cours des cycles de fonctionnement / arrêt du moteur. A quel type de chargement a-t-on principalement affaire ? On constate expérimentalement que les fissures s’amorcent sur la face feu et se propagent progressivement vers la face eau. Deux objectifs s’imposent à l’ingénieur de conception : Retarder et si possible prévenir l’amorçage de ces fissures en modifiant le comportement mécanique de l’alliage Ralentir et si possible arrêter la propagation de telles fissures. On s’intéresse ici à la première étape (l’amorçage de fissure), qui nécessite déjà de bien connaître l’évolution des propriétés mécaniques du matériau au cours du temps. Ce point fait l’objet des parties suivantes de ce chapitre. Figure 2 : Le problème et le coupable : un pontet intersoupapes fissuré. PARTIE 2 : STRUCTURE DE SOLIDIFICATION ET PROPRIETES MECANIQUES ASSOCIEES On considère, dans cette étude, la famille des alliages Al-Si faiblement alliés au Mg. La structure de solidification est essentiellement liée aux éléments Al et Si qui seront seuls considérés dans un premier temps. 2.1 Composition chimique En considérant le diagramme d’équilibre thermodynamique de la figure 3, quelle serait la meilleure composition possible pour couler facilement (c’est-à-dire avec le moins de défauts) le métal dans le moule de la culasse ? Quelle serait, à la température ambiante, la proportion et la composition chimique approximatives des phases à l’équilibre, sachant que l’on peut prolonger les courbes de la figure 2 jusqu’à 20°C ? La composition réelle de l’alliage utilisé (AS7G) est donnée dans le tableau 1. Noter que le faible taux de fer (inférieur à 0,1%), bénéfique pour les propriétés mécaniques, interdit d’employer du métal de deuxième fusion, c’est-à-dire issu du recyclage. En supposant que la solidification est très lente, donner la séquence de solidification de cet alliage. Quelles sont la nature et la composition chimique des phases à l’équilibre après refroidissement complet ? Interpréter alors les contrastes obtenus sur la micrographie de la figure 4. 222 Matériaux pour l’ingénieur Figure 3 : Diagramme d’équilibre binaire Al-Si (d’après Massalski).La figure de droite est un agrandissement de la partie du diagramme du côté de Al. Figure 4 :Microstructure de solidification de l’alliage AS7G. Quelles propriétés mécaniques attend-on des deux phases en présence ? Parmi les morphologies d’eutectiques possibles, laquelle vous paraît alors la meilleure, pour la ductilité et la ténacité de la pièce, entre les deux possibilités suivantes : Un eutectique lamellaire où le silicium est de forme allongée Un eutectique globulaire où le silicium est sous forme de particules sphériques dans une matrice (Al) ? TABLEAU 1 : COMPOSITION CHIMIQUE (EN MASSE) DE L’ALLIAGE AS7G DE L’ETUDE Elément Al Si Cu Mg Fe Mn Zn Ti Ca Sr % base 7,1 0,001 0,32 0,06 0,002 0,001 0,13 0,0001 0,010 La morphologie globulaire est obtenue par une faible addition de strontium dans l’alliage. En vous référant à la figure 4, quel commentaire peut-on faire sur la composition chimique donnée dans le tableau 1 ? Toujours d’après le diagramme Al-Si, quelles proportions de dendrites et d’eutectique attend-on juste après la réaction eutectique ? Comparer avec la valeur expérimentale de 20% d’eutectique. Quelles sont les origines possibles de l’écart constaté ? T (°C) Al Si 100 µm 100 µm 100 µm Etude de cas : culasse de moteur Diesel (TD) 223 2.2 Structure et défauts attendus Quels sont les défauts susceptibles d’apparaître sur la pièce moulée ? Comment peut-on prévenir leur apparition ? Le fait que, comme l’eau, le silicium se dilate en solidifiant (ce qui est un comportement exceptionnel !) vous paraît-il bénéfique vis-à-vis de ces défauts ? Lors de la mise en forme, le métal est directement versé dans le moule en sable à la forme de la culasse. Vaut-il mieux, vis-à-vis de l’amorçage des fissures, remplir le moule en commençant par la face feu ou par la face eau ? S’attend-on à ce que l’étape limitante de la ruine de la culasse soit plutôt l’amorçage ou la propagation des fissures ? PARTIE 3 : TRAITEMENT THERMIQUE DES PIECES MOULEES Le traitement thermique après moulage comporte un recuit de mise en solution à 540°C, suivi d’une trempe à l’eau chaude et d’un revenu à 200°C pendant au moins 5 heures. L’alliage est alors à l’état T7 (survieilli), qui détermine les propriétés de la pièce neuve. 3.1 Remise en solution et trempe Quelles sont les phases en présence dans les systèmes Al-Si et Mg-Si (figure 5) à l’équilibre à 540°C ? Combien la phase (Al) peut-elle alors contenir de Si en solution ? Pourquoi doit-on refroidir l’alliage rapidement après cette remise en solution ? Une trempe à l’au froide permettrait un refroidissement plus énergique, c’est ce que l’on fait couramment pour les tôles laminées. Que pourrait-il éventuellement se passer si l’on refroidissait trop brutalement par trempe une pièce de fonderie ? Figure 5 : Diagramme d’équilibre binaire Mg-Si (d’après Massalski) 3.2 Revenu Quelles sont les phases potentiellement présentes à l’équilibre à 200°C d’après les diagrammes Al-Si et Mg-Si ? Il existe, pour la phase Mg2Si, une séquence de précipitation, qui est liée à l’énergie des interfaces interphases des phases métastables, plus ou moins cohérentes avec la matrice (Al), et à la composition chimique de ces phases intermédiaires. Cette séquence est la suivante, si le processus se poursuit jusqu’à l’équilibre : (Al)1 → (Al)2 + zones G.P. → (Al)3 +β’’ → (Al)4 + β’ → (Al)5 + β Les indices 1 à 5 indiquent un changement de composition chimique de la phase (Al), qui passe d’une solution solide sursaturée en Mg et Si à la composition d’équilibre en fin de séquence. En passant des zones de Guinier- Preston (zones G.P., cf. TD sur les traitements thermiques) à la phase stable β (Mg2Si), le précipité est de plus en plus gros et de moins en moins cohérent avec la matrice. 224 Matériaux pour l’ingénieur Afin de déterminer les phases réellement présentes dans le matériau à la fin du revenu, on prélève un échantillon de culasse et on lui fait subir, dans un calorimètre différentiel à balayage, un cycle thermique dont la partie « chauffage » est représentée sur la figure 6. On dispose des températures caractéristiques des transformations de phase dans des conditions proches, tirées de la littérature (tableau 2) et on relève la position des pics sur le thermogramme de la figure 6. Figure 6 : Thermogramme obtenu au chauffage sur un échantillon d’AS7G à l’état T7 (calorimétrie différentielle à balayage) A quelles transformations de phase les pics repérés 1 et 2 sont-ils respectivement associés ? En déduire l’état de précipitation du matériau à l’état T7. Dans la suite de cette étude, on considère l’évolution structurale uploads/s3/ ch-26-27-culasses-td-pdf.pdf
Documents similaires
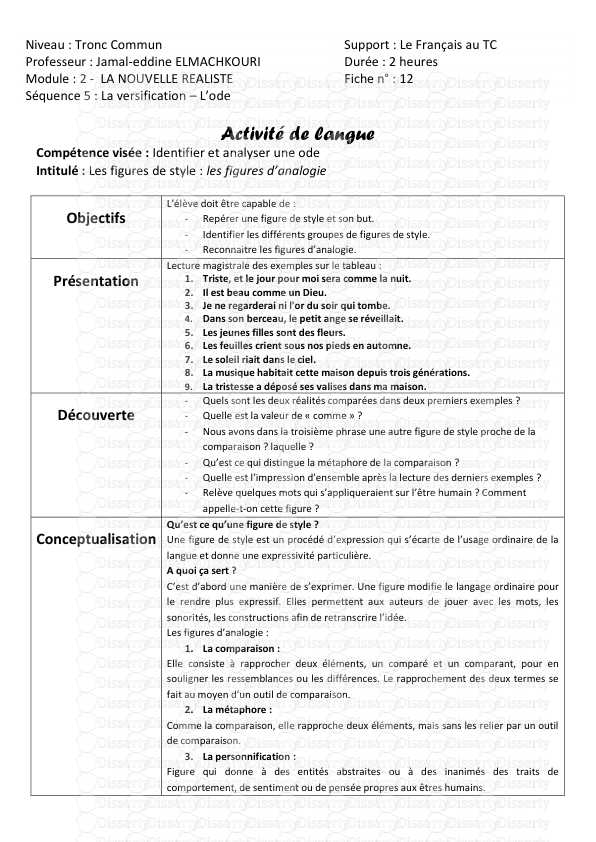
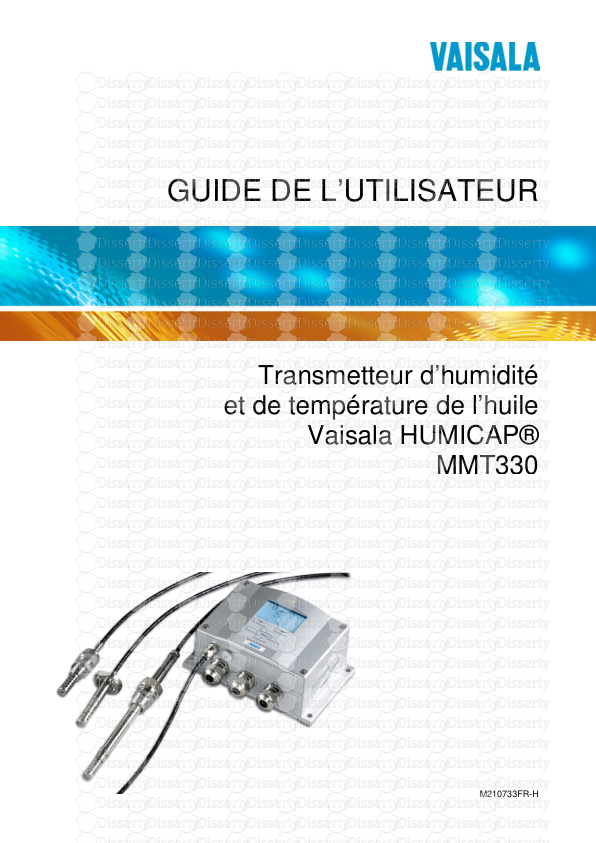
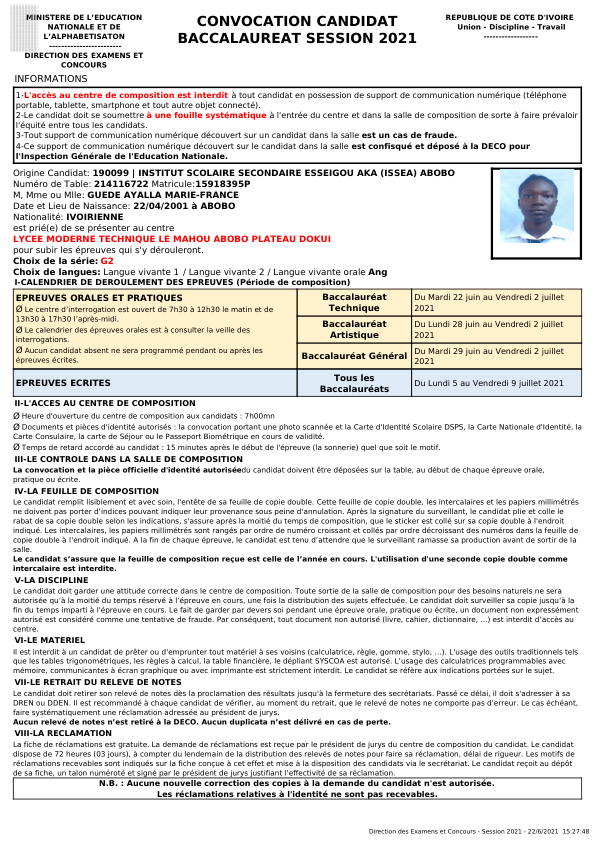
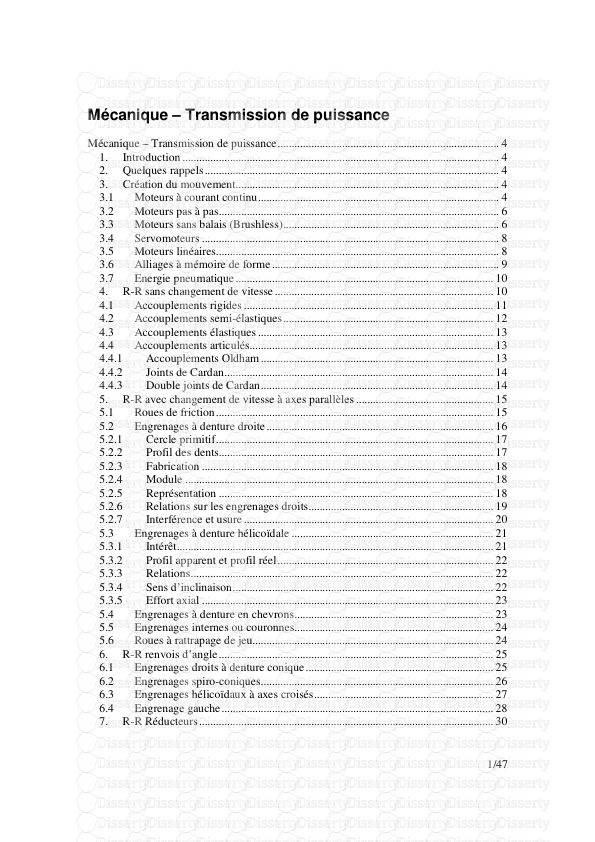
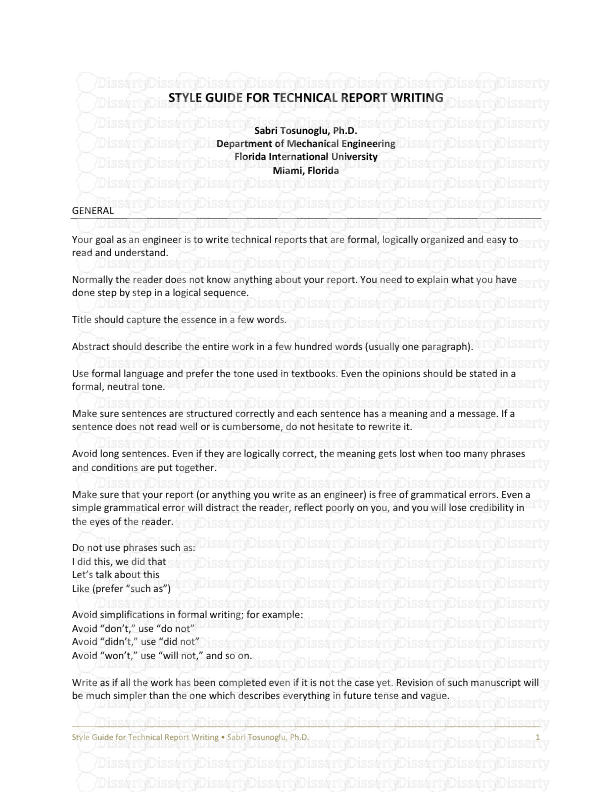
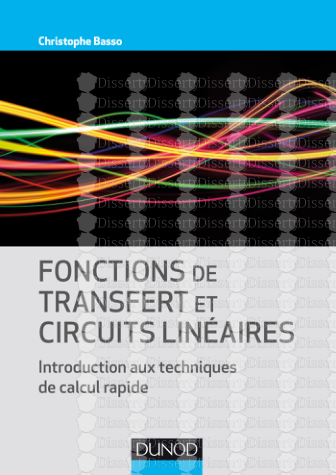
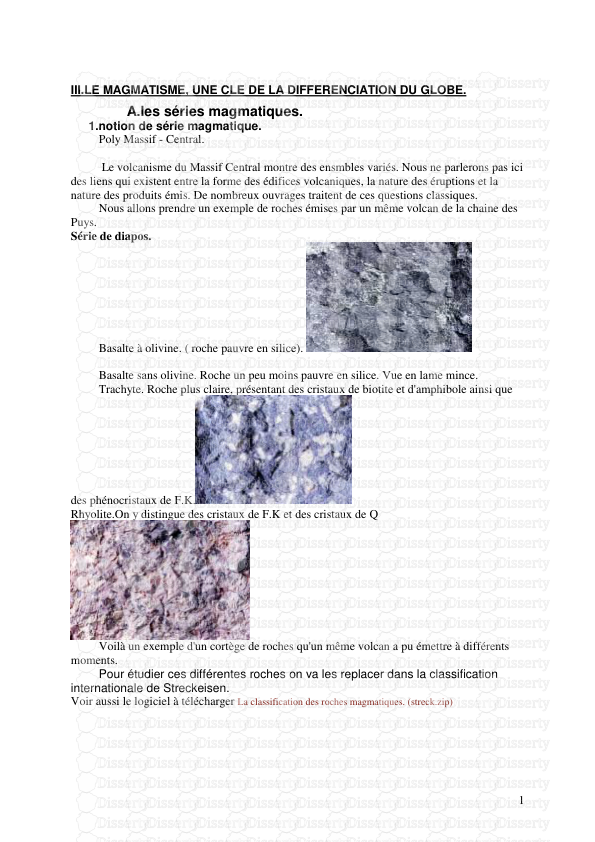
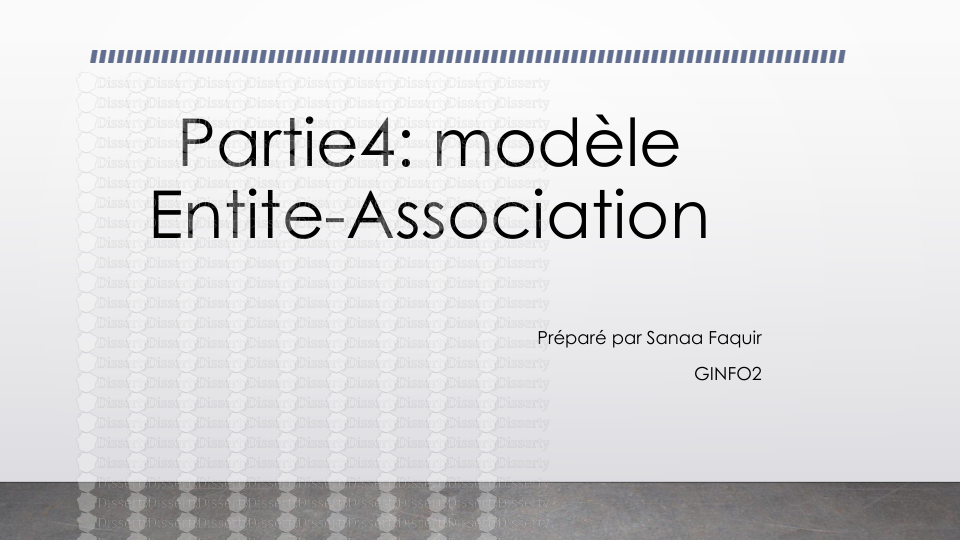
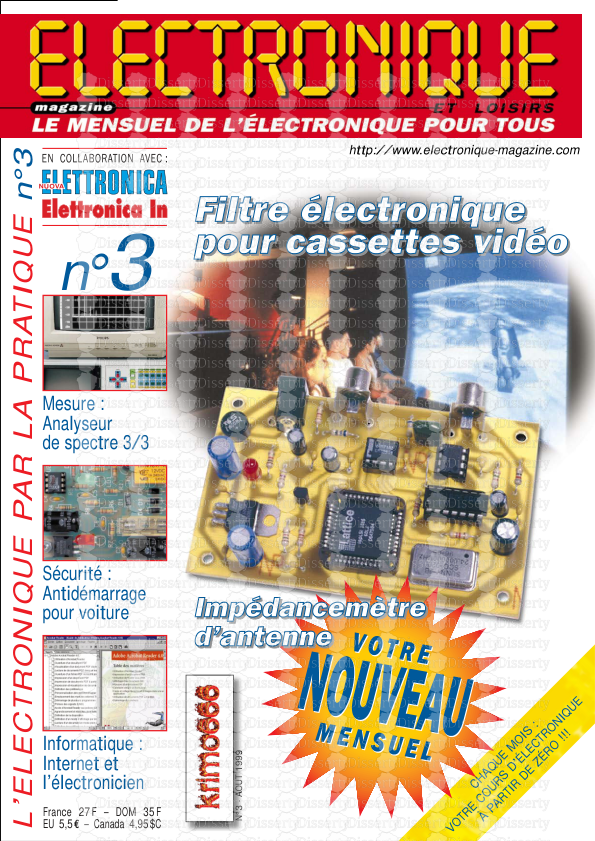
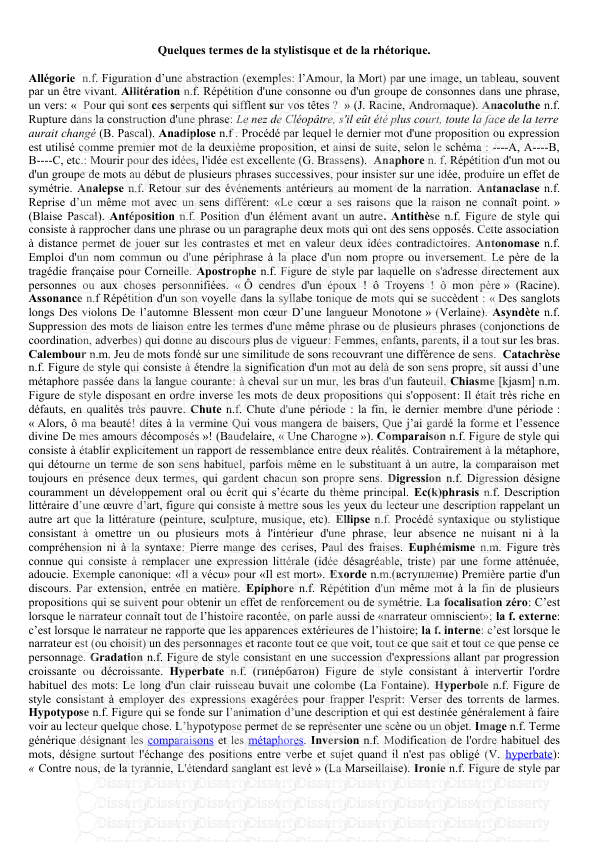
-
44
-
0
-
0
Licence et utilisation
Gratuit pour un usage personnel Attribution requise- Détails
- Publié le Sep 05, 2022
- Catégorie Creative Arts / Ar...
- Langue French
- Taille du fichier 0.3922MB