UNIVERSITE DE LUBAMBASHI FACULTE POLYTECHNIQUE Département de Chimie Industriel
UNIVERSITE DE LUBAMBASHI FACULTE POLYTECHNIQUE Département de Chimie Industrielle JUIN 2021 AMELIORATION DU CUIVRE TRANSFERE AUX UNITES D’EXTRACTION PAR SOLVANT HAUTE TENEUR DE LUILU PAR MODELISATION ET SIMULATION (ECHELLE PILOTE) Travail présenté et défendu en vue de l’obtention du grade de Bachelier Ingénieur Civil en Chimie Industrielle Par NGOIE KALUMBA Nathan P a g e | II UNIVERSITE DE LUBAMBASHI FACULTE POLYTECHNIQUE Département de Chimie Industrielle ANNEE ACADEMIQUE 2019-2020 AMELIORATION DU CUIVRE TRANSFERE AUX UNITES D’EXTRACTION PAR SOLVANT HAUTE TENEUR DE LUILU PAR MODELISATION ET SIMULATION (ECHELLE PILOTE) Par NGOIE KALUMBA Nathan Directeur : Professeur Ordinaire LUKUMU MULUMBA Emmanuel (UNILU) Encadreur : Msc Ir KABEYA MAKOBO Daniel (UNILU) Travail présenté et défendu en vue de l’obtention du grade de Bachelier Ingénieur Civil en Chimie Industrielle RESUME Il a été constaté à l’usine hydrométallurgique de Luilu, qu’au-delà d’un débit d’alimentation de PLS de 850 m3/h, les entrainements des phases et une baisse du rendement d’extraction sont fréquents dans la configuration série de l’extraction par solvant, ce qui limite la production. Pour augmenter le débit d’alimentation, une alternative était de modifier la configuration des étages d’extraction série en série-parallèle, ce qui augmenterait le débit d’alimentation de 850 m3/h à 1200 m3/h et par conséquent la quantité du cuivre transféré et donc, une augmentation du cuivre produit. C’est dans cette optique, qu’il a été initié pour nous cette étude dont le but est de trouver un modèle de prédiction de la quantité du cuivre transféré dans la phase organique en configuration série-parallèle, tout en étudiant l’influence de paramètres (concentrations en cuivre et en acidité libre dans le PLS, le ratio du couplage série et celui de l’étage en parallèle) sur le cuivre transféré, ainsi que de trouver les valeurs optimums de ses paramètres pour un transfert maximum du cuivre dans la phase organique. Plusieurs tests à l’usine pilote de Kamoto Copper Company ont été réalisés suivant un plan factoriel complet à deux niveaux. Nous avons effectué la modélisation en boite noire et le modèle de prédiction obtenu, a été simulé sur MS-EXCEL pour évaluer les performances de la configuration série-parallèle étudiée. Les résultats de la simulation ont montré que la configuration série-parallèle est une solution envisageable par rapport à la configuration série actuellement utilisée aux usines de Luilu. Elle permet de transférer plus de cuivre, soit 304 tonnes/jour contre 240-250 tonnes/jour pour la configuration série, lorsque la concentration en cuivre est supérieure ou égale à 15 g/l avec le ratio du couplage série de 1 et celui de l’étage en parallèle de 2 et que, cette quantité de cuivre transféré est influencée par la concentration en cuivre dans le PLS, le ratio du couplage série et celui de l’étage en parallèle. Mots clés : Cuivre, Extraction par solvant, Hydrométallurgie, modélisation expérimentale, plan factoriel. ABSTRACT It has been found at the Luilu hydrometallurgical plant that beyond a PLS feed rate of 850 m3/h, phase training and a decrease in extraction yield are frequent in the serial configuration of extraction by soil, which limits production. To increase the feed rate, an alternative was to change the configuration of the serial extraction stages in series-parallel, which would increase the feed rate from 850 m3/h to 1200 m3/h and therefore la quantity of copper transferred and therefore, an increase in the copper produced. It is with this in mind that it was initiated for us this study whose goal is therefore to find a model for predicting the amount of copper transferred into the organic phase in series-parallel configuration, while studying the influence of parameters (copper concentrations and free acidity in the PLS, the ratio of the series coupling and the parallel ratio) on the transferred copper, as well as to find the optimum values of its parameters for a maximum transfer of copper in the organic phase. Several tests at the Kamoto Copper Company pilot plant were carried out according to a complete two-tier factorial plan. We carried out the black box modeling and the prediction model obtained, was simulated on MS-EXCEL to evaluate the performance of the series- parallel configuration studied. The results of the simulation showed that the serial-parallel configuration is a possible solution compared to the serial configuration currently used at Luilu's factories. It allows to transfer more copper, i.e., 304 tons / day against 240-250 tons / day for the series configuration, when the copper concentration is greater than or equal to 15 g / l with the ratio of the series coupling of 1 and that of the stage in parallel of 2 and that, this amount of copper transferred is influenced by the copper concentration in the PLS, the ratio of the series coupling and that of the stage in parallel. Keywords: Copper, Solvent extraction, Hydrometallurgy, experimental modeling, factorial design. P a g e | I TABLE DES MATIERES TABLE DES MATIÈRES ..................................................................................................................... I LISTE DES FIGURES ......................................................................................................................... IV LISTE DES TABLEAUX ..................................................................................................................... V ABREVIATIONS ................................................................................................................................. VI EPIGRAPHE ....................................................................................................................................... VII DEDICACE ......................................................................................................................................... VIII AVANT PROPOS................................................................................................................................. IX INTRODUCTION GENERALE .......................................................................................................... 1 CHAPITRE 1 DESCRIPTION DE L’USINE HYDROMETALLURGIQUE DE LUILU ..... 3 1.1 CIRCUIT CUIVRE ............................................................................................................... 3 1.1.1 Réception des minerais oxydés ..................................................................................... 3 1.1.2 Grillage sulfatant ........................................................................................................... 3 1.1.3 Lixiviation-décantation ................................................................................................. 4 1.1.4 Extraction par solvant(SX)-Electrolyse(EW) ............................................................. 4 1.2 CIRCUIT COBALT .............................................................................................................. 8 1.2.1 Elimination des impuretés ............................................................................................ 8 1.2.2 Précipitation Cobalt ...................................................................................................... 8 1.2.3 Filtration et séchage ...................................................................................................... 8 CHAPITRE 2 L’EXTRACTION PAR SOLVANT DU CUIVRE EN MILIEU SULFATE . 11 2.1 INTRODUCTION ............................................................................................................... 11 2.2 PRINCIPE D’EXTRACTION PAR SOLVANT .............................................................. 11 2.2.1 Aspect Cinétique .......................................................................................................... 12 2.2.2 Coefficient de partage ................................................................................................. 12 2.3 REACTIFS ........................................................................................................................... 13 2.3.1 Extractants ................................................................................................................... 13 2.3.2 Diluants ......................................................................................................................... 14 2.3.3 Modificateurs ............................................................................................................... 14 2.4 PARAMETRES INDUSTRIELS ....................................................................................... 14 2.4.1 Nombre d’étage ............................................................................................................ 15 2.4.2 Rapport des volumes (Ratio) ...................................................................................... 15 2.4.3 pH .................................................................................................................................. 16 2.4.4 Temps de séjour dans le mélangeur ........................................................................... 16 2.4.5 Continuité de phase ..................................................................................................... 16 2.5 CONTAMINANTS .............................................................................................................. 16 P a g e | II 2.5.1 Problèmes liés à la silice soluble ................................................................................. 17 2.5.2 Problèmes liés aux solides finement divisés ............................................................... 17 2.5.3 Problèmes liés au contenu en ions chlorures ............................................................. 17 2.5.4 Problèmes liés au manganèse ..................................................................................... 17 2.5.5 Problèmes liés au contenu en nitrate ......................................................................... 17 2.5.6 Problèmes liés aux agents tensioactifs ....................................................................... 17 2.5.7 Problèmes liés aux additifs en amont de l’usine d’extraction par solvant ............. 18 CHAPITRE 3 MODELISATION EXPERIMENTALE EN GENIE DES PROCEDES ....... 19 3.1 INTRODUCTION ............................................................................................................... 19 3.2 TYPES DE MODELES MATHEMATIQUES ................................................................. 19 3.3 MODELISATION PAR LES PLANS D’EXPERIENCE ................................................ 19 3.3.1 Introduction ................................................................................................................. 19 3.3.2 Définition des concepts ................................................................................................ 20 3.3.3 Principe ......................................................................................................................... 21 3.3.4 Effet d’un facteur ........................................................................................................ 22 3.3.5 Interactions entre facteurs .......................................................................................... 23 3.4 Modélisation mathématique ............................................................................................... 23 3.4.1 Modèle expérimental ................................................................................................... 23 3.4.2 Système d’équations .................................................................................................... 24 3.5 Plan d’expérience à deux niveaux ...................................................................................... 24 3.6 ANALYSE DE LA VARIANCE ........................................................................................ 26 3.6.1 Probabilité P ................................................................................................................ 27 3.6.2 Coefficients de détermination (R2, R2 ajusté) ............................................................ 27 3.7 LOGICIELS DE PLANIFICATION DES EXPÉRIENCES ........................................... 28 CHAPITRE 4 MATERIEL ET METHODES ........................................................................... 29 4.1 MÉTHODOLOGIE GENERALE ..................................................................................... 29 4.1.1 ECHANTILLONNAGE.............................................................................................. 30 4.1.2 CARACTERISATION DES ECHANTILLONS ...................................................... 30 4.1.3 ESSAIS D’EXTRACTION ......................................................................................... 31 4.2 MODÉLISATION MATHÉMATIQUE ........................................................................... 36 4.2.1 Choix de la réponse ..................................................................................................... 36 4.2.2 Modélisation théorique de la configuration .............................................................. 36 CHAPITRE 5 PRESENTATION ET ANALYSE DES RESULTATS .................................... 38 5.1 NOMBRE THEORIQUE D’ETAGES D’EXTRACTION .............................................. 38 5.2 RÉSULTATS DE MODÉLISATION ................................................................................ 39 5.2.1 Résultats des essais d’extraction ................................................................................ 39 P a g e | III 5.2.2 Expression du modèle mathématique ........................................................................ 40 5.2.3 Analyse des effets des facteurs sur le cuivre transféré ............................................. 41 5.2.4 Analyse des interactions .............................................................................................. 42 5.2.5 Analyse statistique du modèle .................................................................................... 43 5.3 RESULTATS DE L’OPTIMISATION DU CUIVRE TRANSFERE PAR SIMULATION SUR EXCEL ........................................................................................................ 47 CONCLUSION GENERALE............................................................................................................. 51 REFERENCES BIBLIOGRAPHIQUES .......................................................................................... 53 ANNEXE ................................................................................................................................................ A ANNEXE 1 : TABLE DE LA LOI BILATÉRALE DE STUDENT ................................................. A ANNEXE 2 : TABLE DE PROBABILITE DE FISHER-SNEDECOR A 95 % ............................. B ANNEXE 3 : IMAGE DU SIMULATEUR DE LA CONFIGURATION ........................................ 3 P a g e | IV LISTE DES FIGURES Figure 1.1:Structures de cetoximes et des aldoximes ................................................................ 5 Figure 1.2:Presentation d'un train d'extraction par solvant 3E2S de l'usine de Luilu.............. 7 Figure 1.3:Flow-Sheet général de l'usine de Luilu .................................................................. 10 Figure 2.1:Description du processus (COGNIS,2005). ........................................................... 12 Figure 2.2: Diagramme de McCabe-Thiele pour l'extraction d'un métal ............................... 15 Figure 3.1:Illustration de la modélisation en boite noire ........................................................ 21 Figure 3.2: Effet d'un facteur sur la réponse(J.GOUPY, 2006) .............................................. 22 Figure 3.3: Effet des interactions sur la réponse ..................................................................... 23 Figure 3.4: Differents écarts .................................................................................................... 27 Figure 4.1: Étapes suivies pour modéliser et simuler l’unité d'extraction SX de Luilu.......... 29 Figure 4.2: Illustration des pompes d'alimentation à l'usine pilote SX de Luilu .................... 35 Figure 4.3: Illustration des mélangeur-décanteur à l'usine pilote SX de Luilu ....................... 35 Figure 4.4:Configuration série-parallèle de l'extraction......................................................... 36 Figure 5.1:Diagramme de McCabe-Thiele pour un PLS de 15,56 g/l ..................................... 39 Figure 5.2:Diagramme des effets principaux .......................................................................... 41 Figure 5.3: Diagramme de Pareto des effets normalisés ......................................................... uploads/Industriel/ amelioration-du-cuivre-transfere-aux-unites-d-x27-extraction-par-solvant-haute-teneur-de-luilu-par-modelisation-et-simulation-echelle-pilote.pdf
Documents similaires
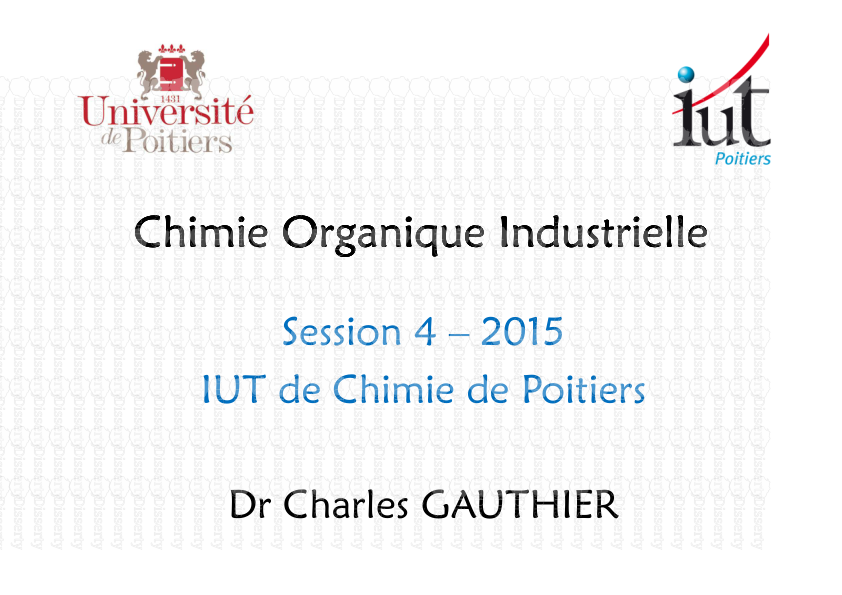
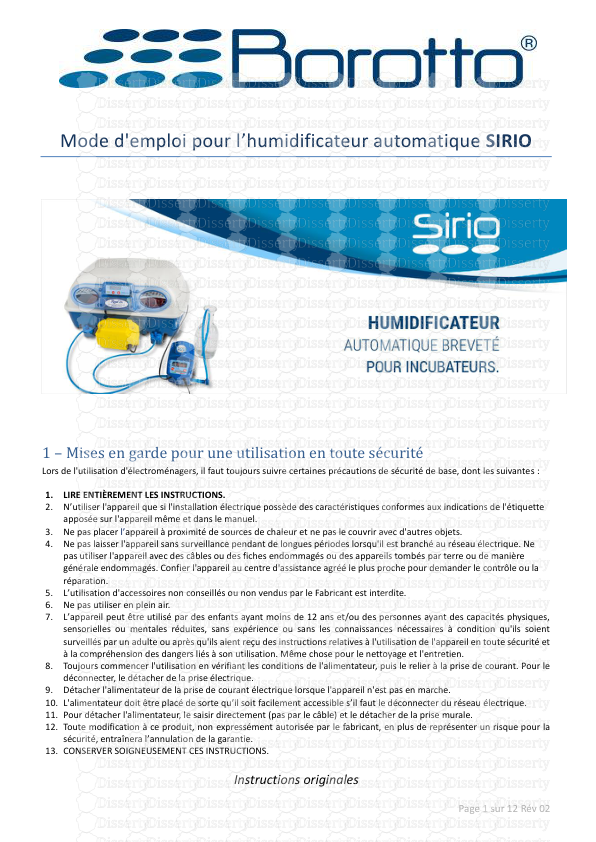
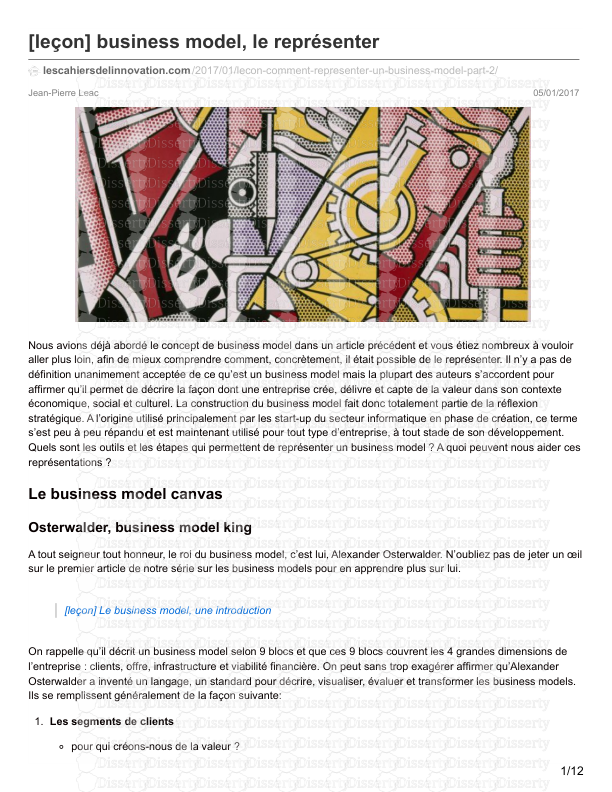
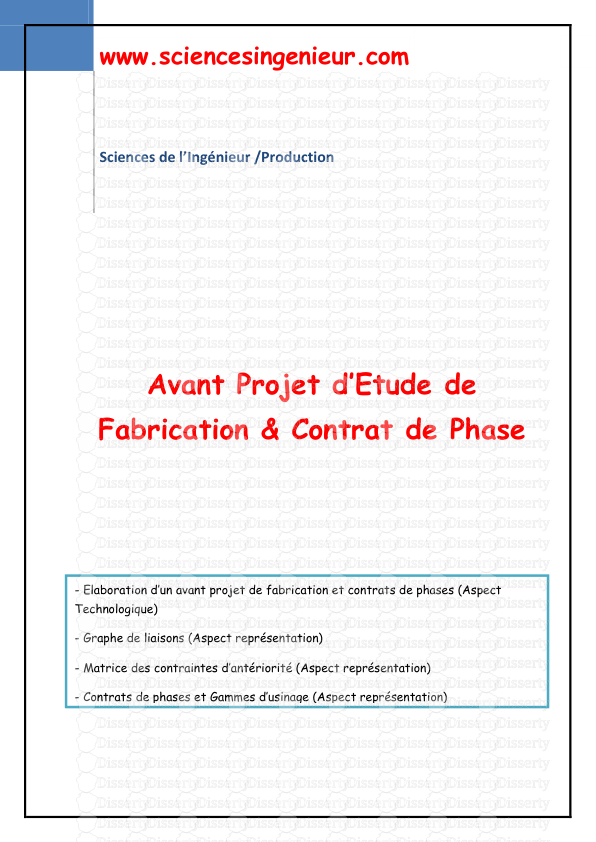
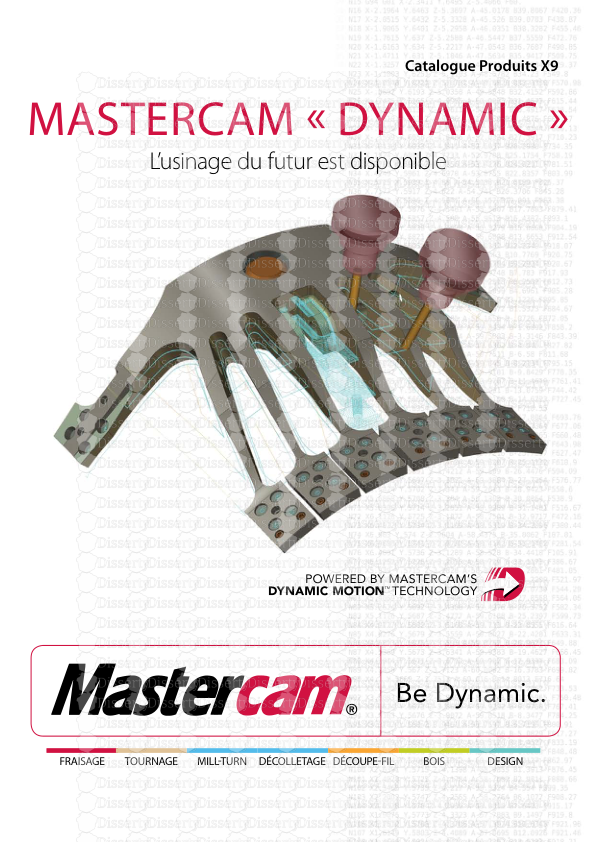
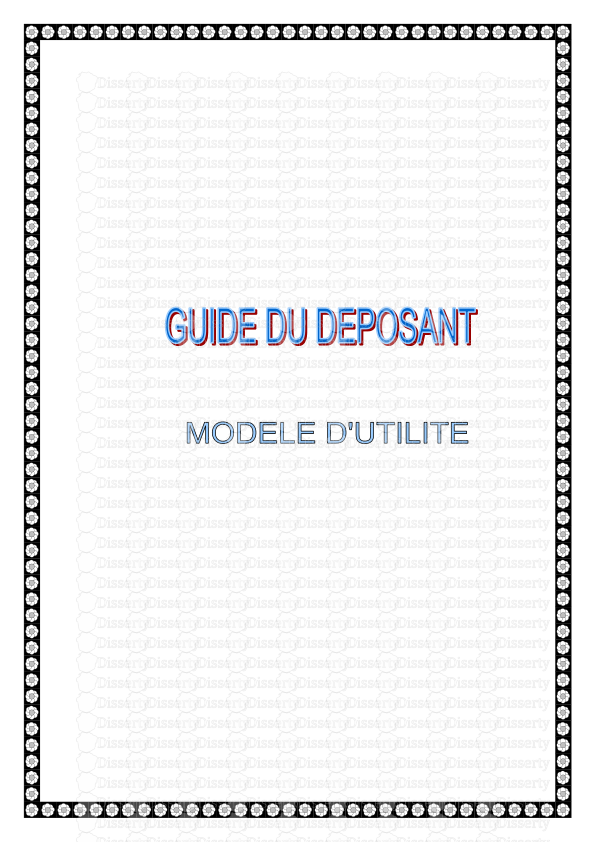
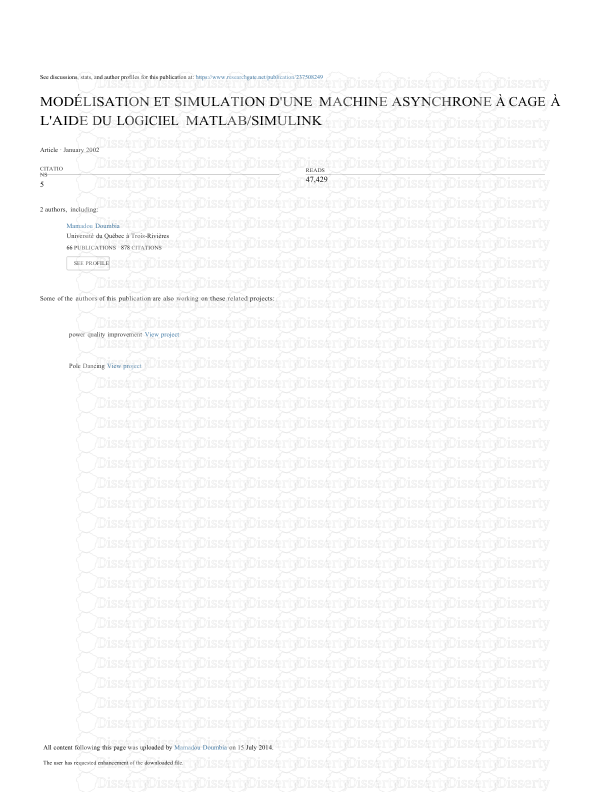
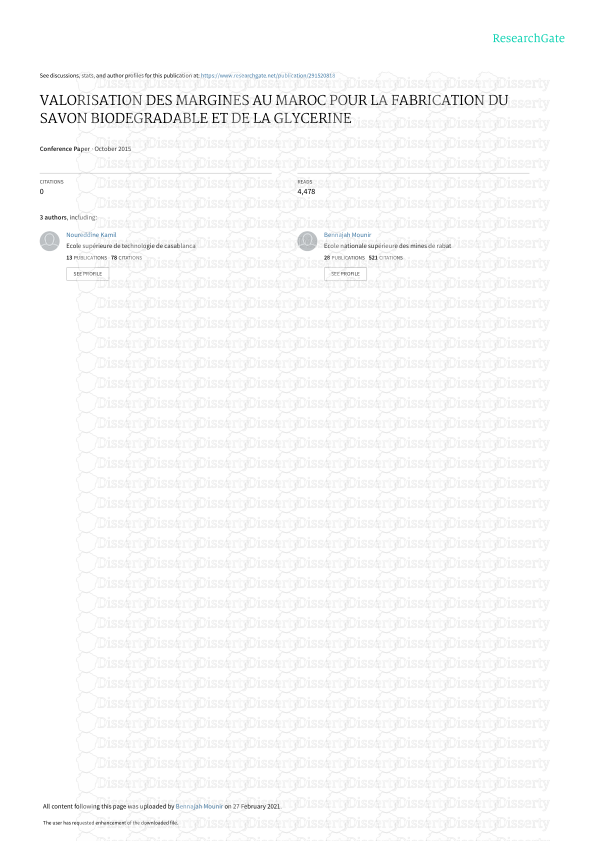
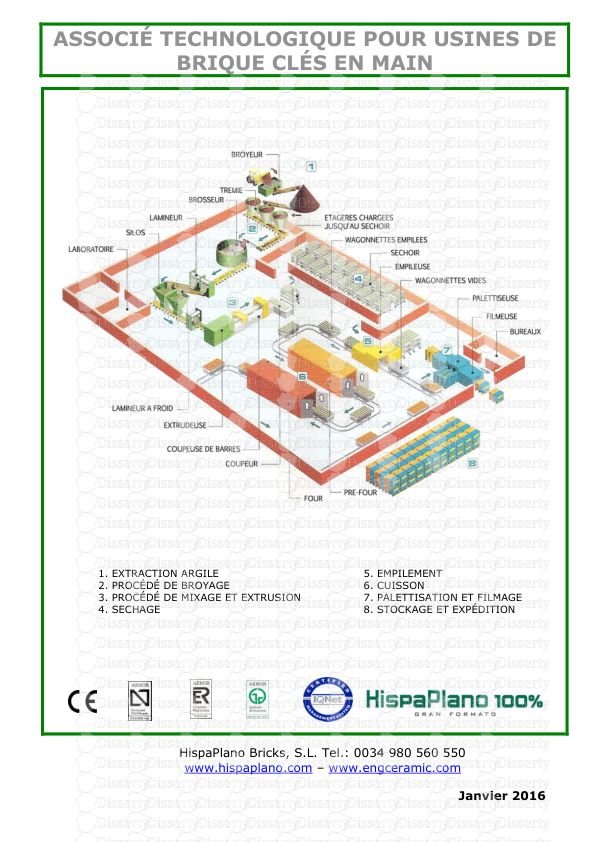
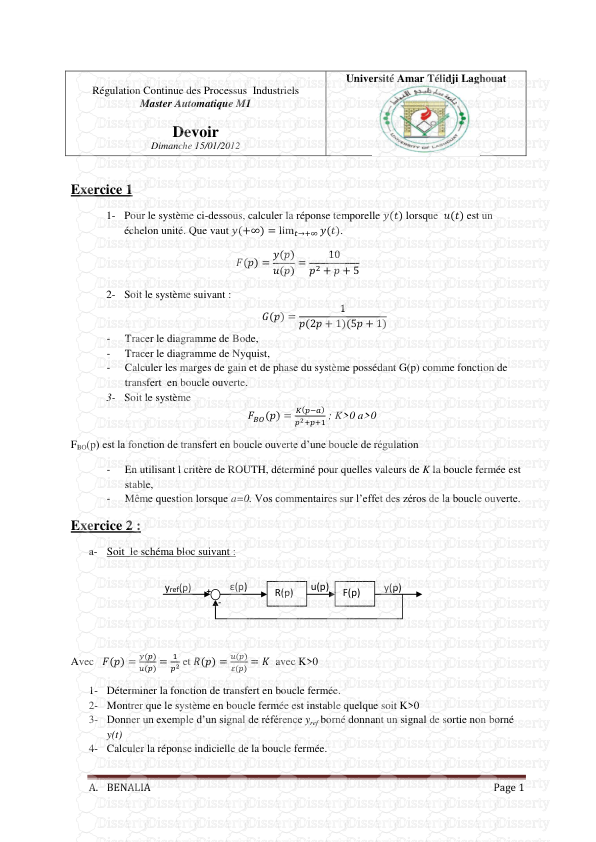
-
59
-
0
-
0
Licence et utilisation
Gratuit pour un usage personnel Attribution requise- Détails
- Publié le Sep 02, 2021
- Catégorie Industry / Industr...
- Langue French
- Taille du fichier 3.3180MB