10/30/21, 10:04 AM Combustion sans flamme et brûleurs hautes performances | Arc
10/30/21, 10:04 AM Combustion sans flamme et brûleurs hautes performances | Archives | Traitements&Matériaux.fr traitementsetmateriaux.fr/Imprimer/fiche/?id=700&from=actualites&type=archive#:~:text=Il faut entendre par « combustion,de combustible à haute imp… 1/5 FIGURE 1 : Principe de la combustion sans flamme. ARCHIVE Combustion sans flamme et brûleurs hautes performances Nicolas Richard, ingénieur à la Direction de la recherche et innovation de GDF Suez | 1 avril 2011 | Traitement et matériaux n° 0409 Dans un contexte industriel où l'amélioration de la productivité, de l'efficacité énergétique et des performances environnementales est de plus en plus essentielle, en particulier pour les fours à hautes températures, le couplage entre les brûleurs régénératifs et la technique de « combustion sans flamme » devient une solution à prendre sérieusement en compte. Durant le siècle dernier, avec l'apparition des contraintes énergétiques, les industriels de la métallurgie ont utilisé pour la plupart la même technique d'économie d'énergie avec des brûleurs à récupération séparée sur les fumées pour le préchauffage de l'air de combustion (jusqu'à 550 °C), diminuant ainsi les consommations de 20 % à 30 %. Dans les années 80 sont arrivés les brûleurs régénératifs basés sur le même principe de préchauffage de l'air mais à des niveaux plus élevés (> 1 000 °C pour les fours de réchauffage) améliorant ainsi le rendement énergétique de l'installation, mais créant en contre partie une augmentation des émissions de NOx. Pour maîtriser cette pollution, de nombreux travaux ont été menés au Japon, aux USA et en Europe (où l'équipe française, auteur de cet article s'est montré particulièrement active) sur l'amélioration des systèmes de combustion (étagement de l'air par exemple) pour aboutir au développement au milieu des années 90 de la technique dite de « combustion sans flamme » ou « oxydation sans flamme ». Elle présente une flamme qui n'émet pas dans le visible, d'où son nom. C'est une des nouvelles techniques de « combustion propre » qui permet de réduire les émissions d'oxyde d'azote NOx, tout en ayant des températures de procédé et d'air de préchauffage élevées. Cette technique peut être implémentée dans des applications industrielles avec de fortes températures de chauffe, comme pour les fours de réchauffage et de traitement thermique, en chauffe directe ou indirecte. Principe de la combustion sans flamme Dans les systèmes à oxydation sans flamme, les injections en air (comburant)1 et en gaz (combustible) sont réalisées séparément et à hautes vitesses. Les géométries du brûleur et de la chambre de combustion créent des recirculations des produits de combustion vers le brûleur, diluant ainsi le comburant et le combustible avec les produits de combustion avant même qu'ils soient intimement mélangés. La combustion devient alors homogène dans un volume donné de l'enceinte. On notera que les systèmes de chauffage indirect par tubes radiants sont également en mesures de fonctionner en mode combustion sans flamme, impliquant une chauffe plus homogène le long du tube. Les conséquences sont les suivantes (figure 1) : - Le taux d'oxygène au niveau de la combustion diminue, réduisant ainsi la formation de NOx. - Le profil de température dans l'axe du brûleur devient plus homogène, améliorant ainsi les transferts thermiques et réduisant également la formation de NOx.2 En poursuivant votre navigation sur ce site, vous acceptez l'utilisation de cookies permettant à nos services de réaliser des statistiques de visites. Pour en savoir plus et paramétrer les traceurs. Le magazine TRAITEMENTS & MATÉRIAUX #470 Feuilleter un extrait Voir le sommaire Suivez-nous S'inscrire aux newsletters Mon compte ConnexionAccès annonceur 0 10/30/21, 10:04 AM Combustion sans flamme et brûleurs hautes performances | Archives | Traitements&Matériaux.fr traitementsetmateriaux.fr/Imprimer/fiche/?id=700&from=actualites&type=archive#:~:text=Il faut entendre par « combustion,de combustible à haute imp… 2/5 Le terme lui même de « combustion sans flamme » n'est pas utilisé à l'unanimité par les différents acteurs. Il faut Il faut entendre par « combustion sans flamme » un système d'injection séparé de comburant et de combustible à haute entendre par « combustion sans flamme » un système d'injection séparé de comburant et de combustible à haute impulsion. On retrouve donc ce régime de combustion sous différents nom : « oxydation sans flamme » (ou impulsion. flameless oxidation), « combustion diluée » (ou mild combustion), HiTAC (pour high temperature air combustion) et sous différents appellations commerciales. Il est important de noter que le mode de « combustion sans flamme » n'est pas intrinsèquement lié aux brûleurs régénératifs, mais qu'il s'agit plutôt de l'inverse. Ainsi, il est tout à fait possible d'obtenir un tel régime de « combustion sans flamme » avec de l'air préchauffé par un récupérateur centralisé à des niveaux moindres, voir non préchauffé. La seule contrainte est d'avoir une température de procédé supérieure à la température d'auto- inflammation du combustible (de l'ordre de 800 °C pour le gaz naturel). En revanche, l'utilisation d'un système régénératif conduit systématiquement à mettre en oeuvre un mode de combustion à très bas-NOx, à savoir souvent la « combustion sans flamme ». Le couplage de ces deux techniques permet d'obtenir dans la plupart des cas le meilleur compromis entre préchauffage de l'air (et donc efficacité énergétique) et performances environnementales. Principe des brûleurs régénératifs Les premiers brûleurs régénératifs sont nés dans les années 80, époque où les économies d'énergie sont devenues une problématique à part entière. Ils ont été inspirés par les régénérateurs de verrerie. Les brûleurs régénératifs, qui utilisent un matériau réfractaire de stockage de l'énergie récupérable, fonctionnent par paire. Chaque brûleur sert alternativement de brûleur puis de cheminée. Les produits de combustion traversent la capacité thermique et y cèdent leur chaleur. Au cycle suivant (entre 20 s et 2 à 3 min), les rôles des brûleurs s'inversent, et l'air se réchauffe au contact de cette capacité thermique pouvant alors atteindre des températures allant jusqu'à 1 200 °C. Les brûleurs régénératifs se rencontrent sur une plage de puissance allant de 200 kW à 8 MW environ. Ce système de récupération de chaleur est particulièrement performant et permet d'atteindre des rendements de combustion de l'ordre de 80 à 85 %. Un tel rendement de combustion se traduit classiquement d'une réduction des consommations d'énergie de l'ordre de 40 % à 50 % par rapport à un système à air froid et de 20 % par rapport à un système à récupération centralisée « classique » (figure 2). Toutefois, les bacs régénérateurs constitués de billes de céramique ou bien de nids d'abeille peuvent être sensibles aux poussières ou envols provenant de la charge à chauffer et ainsi s'obstruer progressivement. Le nettoyage de ces bacs est donc nécessaire et effectué typiquement annuellement pendant la période d'arrêt du four (à noter que certains secteurs, comme la fusion de l'aluminium sujet à des envols de poussières, doivent effectuer cette opération plus régulièrement). Ce principe de brûleurs régénératifs existe également en version autorégénérative. Ils ne possèdent qu'un seul brûleur dont la capacité thermique a été divisée en deux et le système d'inversion est intégré au brûleur. Contrairement aux brûleurs régénératifs qui ne sont pas réellement limités en puissance, ce type d'équipement est limité à environ 300 kW. Ces systèmes sont d'ailleurs particulièrement adaptés pour un montage sur des tubes radiants à une seule branche (doigt de gant, P, double P). Les brûleurs régénératifs en mode sans flamme Plusieurs constructeurs mondiaux proposent aujourd'hui des brûleurs régénératifs à « oxydation sans flamme ». Certains ont été testés sur les cellules d'essais semi-industriels de la Direction de la recherche et de l'innovation de GDF Suez. Cela a permis de comparer les performances de plusieurs d'entre eux à celles obtenues par des brûleurs conventionnels et d'étudier l'influence des principaux paramètres des brûleurs (températures du four et de l'air, ratio air/gaz, taux d'aspiration...) sur le rendement et le taux d'émission de NOx. Le régime d'oxydation sans flamme permet de réduire considérablement les émissions de NOx (inférieures à 300 mg/Nm3 à 3 % d'O2, avec des températures de four de 1 300 °C et de l'air injecté jusqu'à 1 000-1 100 °C selon les technologies de régénérateurs utilisées) tout en améliorant le rendement (figure 3). Plusieurs partenariats ont été mis en place par la Direction de la recherche et de l'innovation de GDF Suez avec des universités et des industriels du secteur pour transférer ce savoir vers des applications industrielles et ont conduit aux conclusions suivantes quant à la mise en oeuvre industrielle. Mise en oeuvre industrielle Il existe différentes façon d'intégrer cette technologie, correspondant à des niveaux de modifications plus ou moins « lourds ». Il peut s'agir d'une simple modification du système de combustion comme de la conception d'un four neuf. On peut ainsi réaliser un simple « boosting » d'un four qui consiste à ajouter des brûleurs en début du four, sans pour autant modifier le système de combustion de l'existant, afin d'en augmenter la capacité de production. La solution régénérative permet dans ce cas de ne pas altérer la consommation spécifique de l'installation, ni l'écoulement général des produits de combustion. Le « rewamping » d'un four consiste à modifier tout ou partie du système de combustion. Dans le cas d'un « rewamping » partiel, seule une partie des zones peut être concernée. Il est dans ce uploads/Industriel/ combustion-sans-flamme-et-bruleurs-hautes-performances-archives-traitements-amp-mate 1 .pdf
Documents similaires
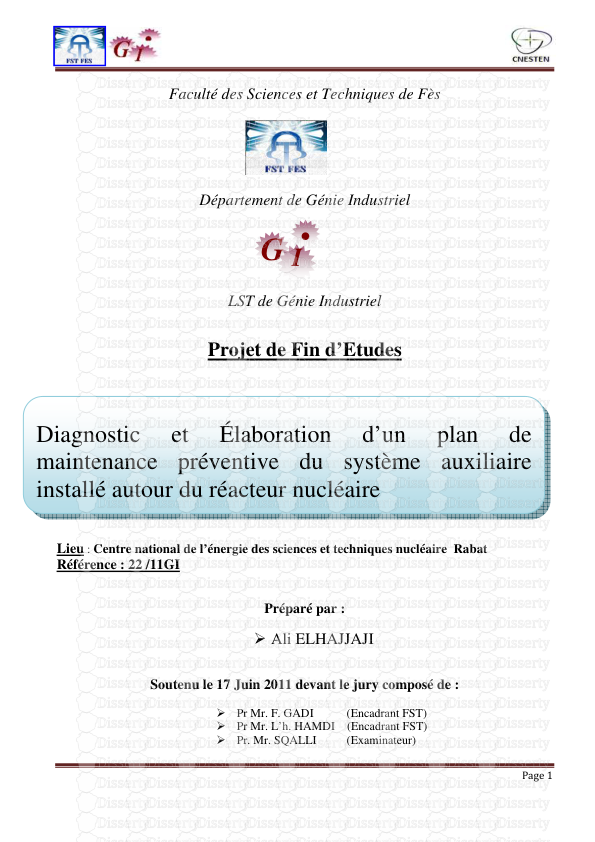
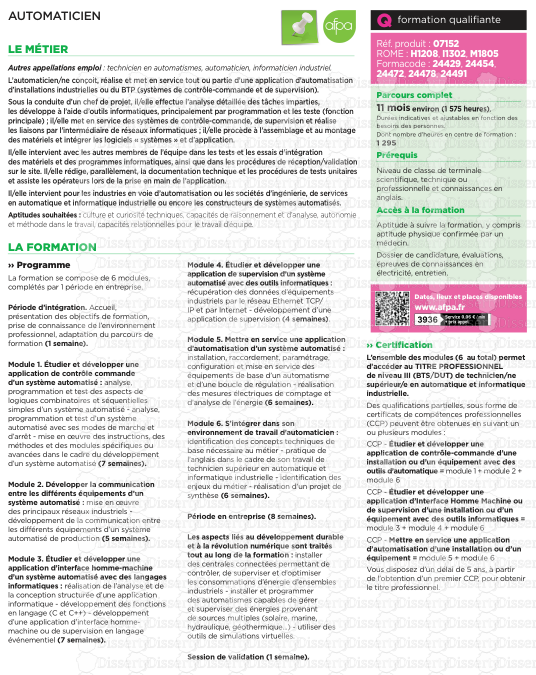
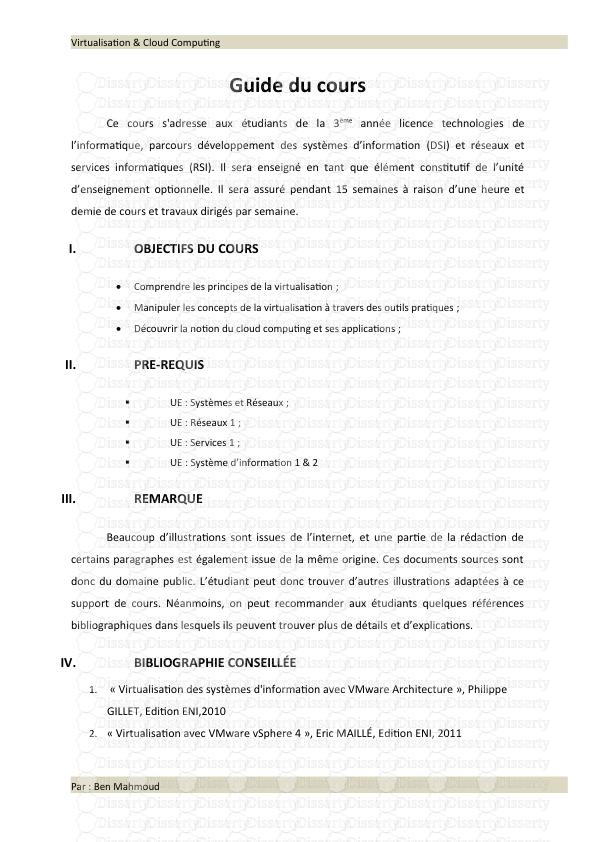
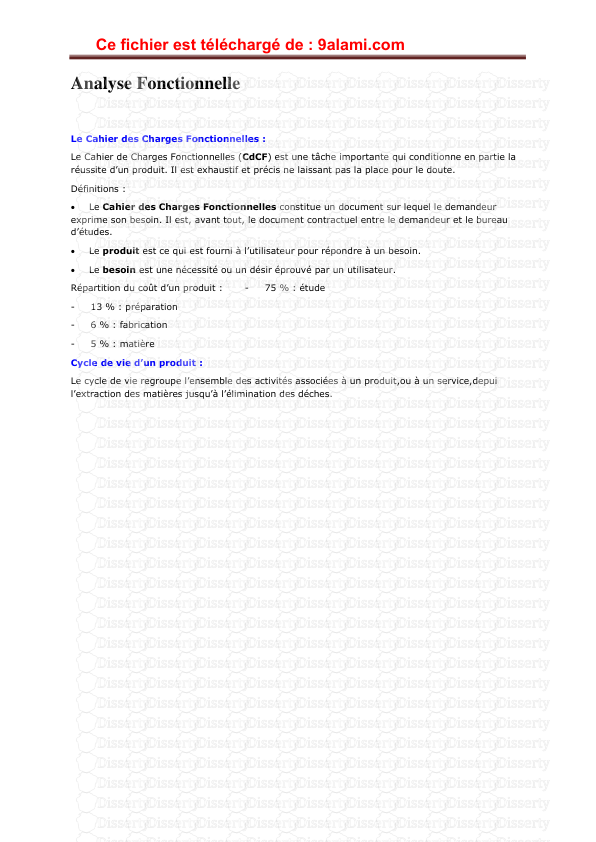
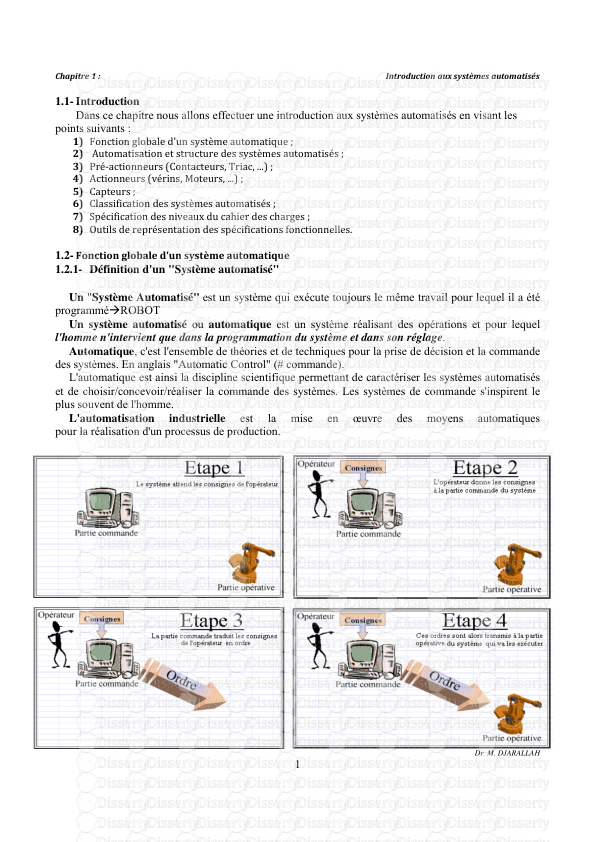
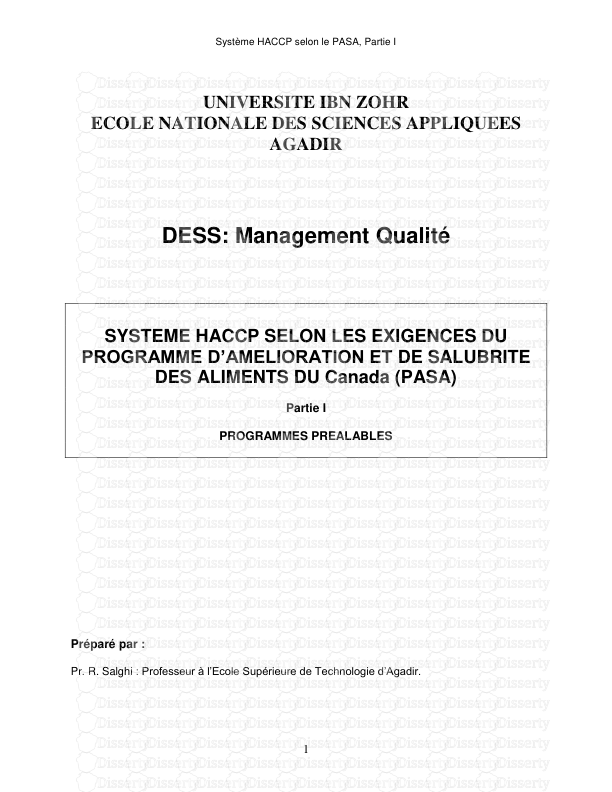
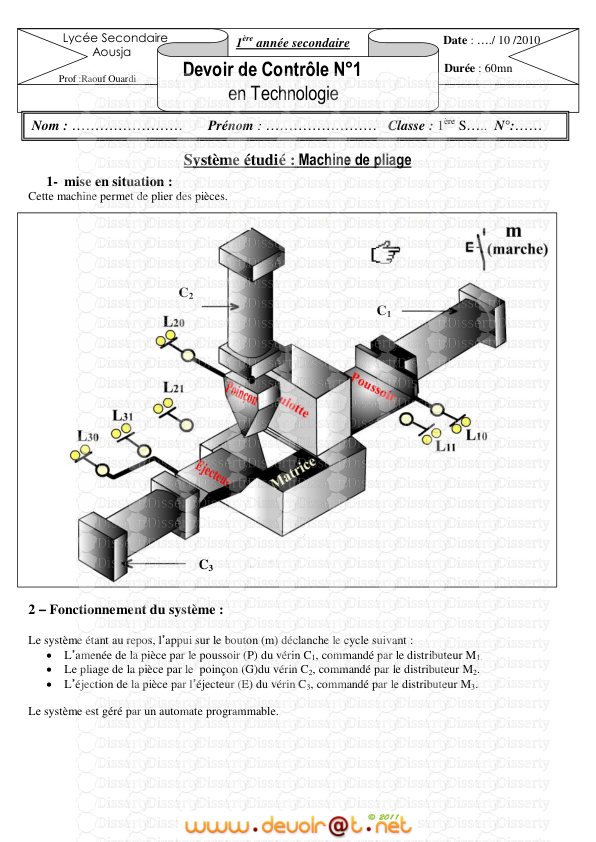
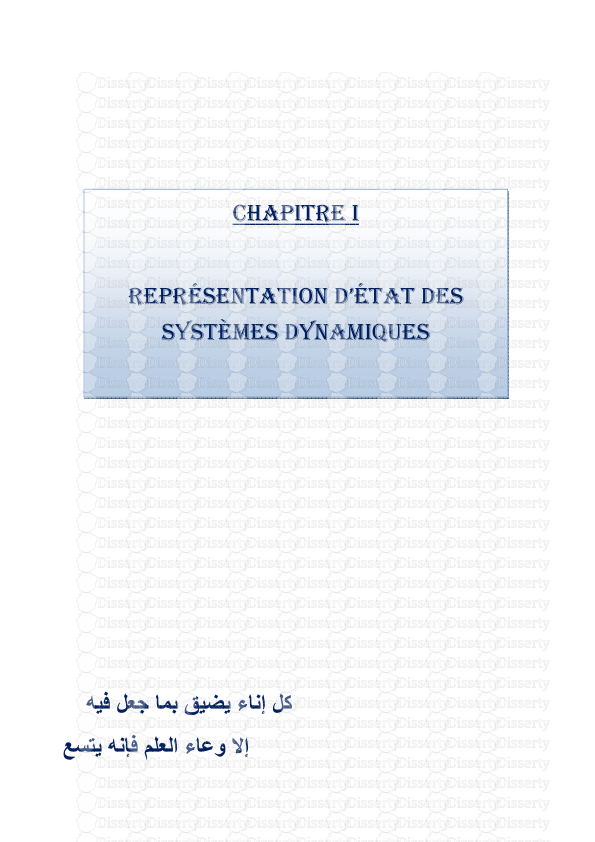
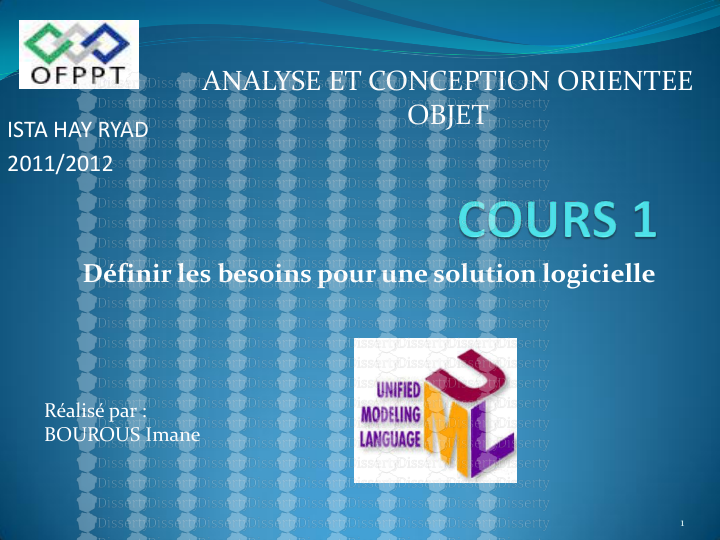
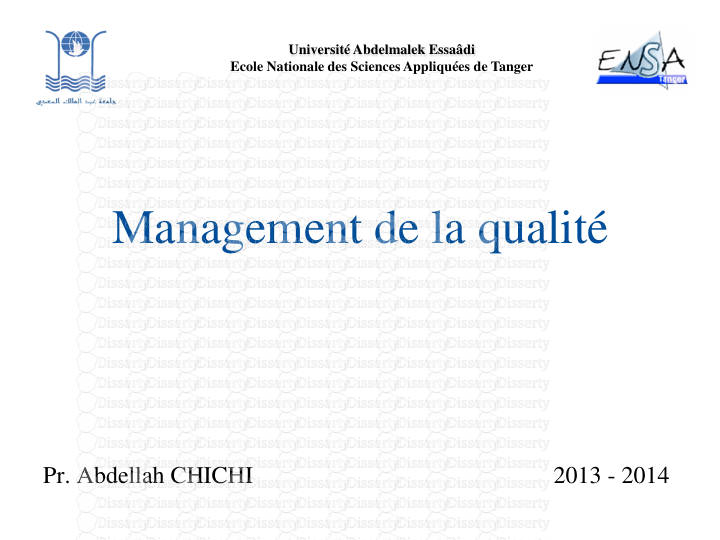
-
50
-
0
-
0
Licence et utilisation
Gratuit pour un usage personnel Attribution requise- Détails
- Publié le Mai 30, 2021
- Catégorie Industry / Industr...
- Langue French
- Taille du fichier 0.2883MB