Dédicace Remerciement Résumé Les stocks sont toujours la conséquence de problèm
Dédicace Remerciement Résumé Les stocks sont toujours la conséquence de problèmes (surproduction, défauts qualité, attentes) qu’il faut résoudre. Un élément important du Lean manufacturing est la réduction des principaux stocks : produits finis, produits encours ou pièces achetées. Les réduire permet d’améliorer l’état financière de l’entreprise et représente pour les milieux industriels un manque à gagner. Ce rapport retrace l'ensemble de l’expérience passé chez la société Leoni Wiring Systems (Ain Sebaâ) au cours de quatre mois de stage de fin d’étude, durant lequel nous essayons de réduire le stock des encours en implémentant un système KANBAN par petit train dans le but En vue de diminuer le stock d’encours de 4 jours à 2 jours pour la WIP des matières premières, D’assurer la disponibilité des composants au bon moment , au bon endroit et en adoptant DMAIC comme démarche d’amélioration, une analyse du processus est faite sur la ligne DG1 de la famille X62, à l’aide de l’outil VSM permettant de visualiser clairement les gaspillages de production susceptibles d’augmenter les encours. L’étude des données dégagées nous a permis de déceler les causes engendrant les encours, un plan d’amélioration est proposé à la fin, aussi bien pour le WIP des semi-finis que pour celui de la matière première afin d’instaurer le travail en flux tiré suivant le principe de juste- à-temps, puis nous nous sommes concentrées sur les encours de la matière première en étudiant la mise en place du système KANBAN par petit train. À la lumière de cette étude, nous comptons donner plus d’efficacité au calcul du besoin fait par le service d’approvisionnement et nous avons estimé un gain considérable. Abstract ملخص LPS : Leoni Production System. Liste des abréviations Table de matières Table des matières Introduction général ................................................................... Error! Bookmark not defined. Chapitre I : Présentation de l’organisme d’accueil ............................................................. 14 INTRODUCTION .............................................................................................................. 14 Partie I : Présentation de l’organisme d’accueil ......................................................................... 15 I.1 Présentation générale ............................................................................................................. 15 I.2 Organisation du groupe LEONI ................................................................................................ 17 I.3 Présentation du site Ain Sebaa ..................................................................................................... 17 Partie II : Processus De Fabrication Des Faisceaux Electriques ................................................. 20 II.1. Réception et contrôle de réception ............................................................................................. 20 II.2. La Coupe : .................................................................................................................................. 21 II.3. Préparation ................................................................................................................................. 21 II.4. L’assemblage ............................................................................................................................. 22 II.5. Le contrôle qualité ..................................................................................................................... 24 Conclusion : ........................................................................................................................ 25 Liste des figures Glossaire : Amélioration continue : Une approche qui consiste à gérer les processus et les ressources au plus juste en éliminant toute sorte de gaspillage. Approvisionnement : Fonction consistant à se doter des composants nécessaires pour fabriquer. Ceci inclut, le calcul et l'expression de besoin en composant, le dimensionnement et la gestion de stocks, les manutentions jusqu'au poste de travail. DMAIC : Désigne une méthode de résolution des problèmes en cinq étapes : Définir, Mesurer, Analyser, Innover, Contrôler. GANTT : un outil utilisé en ordonnancement et gestion de projet et permettant de visualiser dans le temps les diverses tâches liées à un projet. Il permet de représenter graphiquement l'avancement du projet. Just in Time : une méthode d'organisation et de gestion de la production, propre au secteur de l'industrie, qui consiste à minimiser les stocks et les encours de fabrication. KANBAN : (Mot Japonais) signifiant étiquette, une gestion KANBAN se matérialise par un circuit de containers et d’étiquettes entre postes avals et postes amonts. C’est un passage des flux poussés aux flux tirés par la demande. (1) Lean Manufacturing : un concept qui repose sur la réduction des gaspillages. Muda : (Mot Japonais) gaspillage selon le Système de Production TOYOTA. (1) QQOCCP : Outils qui sert à identifier le problème dans son ensemble à partir de 6 questions : Quoi? Qui ? Où ? Quand ? Comment ? Combien ? Pourquoi ? SIPOC : une technique ou une nomenclature permettant de modéliser un processus. C’est l’acronyme de : Supplier, Input, Process, Output, Customer. WIP : (Mot Anglais) Il s’agit de composants, de produits semi-finis ou de produits finis en attente d'une opération de production ou d'une évacuation vers les magasins de stockage. Introduction La recherche de la productivité maximum passe par la suppression de tous les aléas de production et des gaspillages. L’un des trois piliers du LPS, le « Juste à Temps » se concentre sur l’élimination de deux mudas majeurs : les stocks et les mouvements inutiles. Aujourd’hui les postes d’assemblage sont ravitaillés en début d’équipe. Les approvisionneurs remplissent au maximum les racks d’approvisionnement et reviennent ponctuellement remplir les bacs vides ou changer les colis. Ces réapprovisionnements se font de façon irrégulière, ou bien lorsque l’opératrice demande un composant qui lui manque. On constate une grande variabilité dans la tâche de l’approvisionneur qui doit parfois retourner au magasin pour chercher un seul composant. De plus, le niveau d’en-cours composants n’est pas contrôlé. Certains composants ont 2 heures de consommation au poste, d’autres ont jusqu’à 20 jours ! D’où l’intérêt d’une organisation en flux tirés entre le magasin et les lignes d’assemblage. La mise en place du petit train cyclé composants se concentre principalement sur l’amélioration du flux d’approvisionnement des lignes d’assemblage. L’objectif est de répondre au mieux à la demande du client (l’opératrice), pour l’approvisionner régulièrement et sans rupture, tout en améliorant la gestion du niveau d’en-cours. L’utilisation de bacs étiquetés attribués à chaque poste permet d’organiser un kanban de prélèvement. L’approvisionneur doit donc venir fournir les postes selon les composants demandés par l’opératrice. L’équilibrage de l’autonomie de chaque composant sur l’ensemble des postes du process permet d’optimiser l’approvisionnement des composants. En utilisant un train qui circule à fréquence fixe entre le magasin et les lignes, on supprime donc les gaspillages importants liés à un circuit aléatoire. Le petit train cyclé est une application fidèle du principe de « Juste à temps ». Chapitre I : Présentation de l’organisme d’accueil INTRODUCTION Dans cette partie, nous exposons l’organisme d’accueil LEONI au niveau mondial et national, ses critères stratégiques, puis nous introduisons le câblage comme un processus connu dans toutes les multinationales du câblage. Partie I : Présentation de l’organisme d’accueil I.1 Présentation générale Le Groupe LEONI est basé à Nuremberg (Allemagne). Créé en 1917, il s’est consacré à la production des fils et des câbles pour les industries électriques, électroniques et les télécommunications. Le groupe développe aussi des compétences particulières dans le domaine du câblage médical. Les systèmes de câblage représentent 50 % de son activité et sont essentiellement destinés à l’industrie automobile. Le groupe emploie plus de 51 000 personnes dans 70 sites et 8 centres R&D sur 30 pays dans le monde. Il réalise un Chiffre d’affaires consolidé de 1.6 MILLIARD d’euros. Figure 1 : Répartition des divisions de production du groupe LEONI I.1.1 Répartition des sites industriels de LEONI dans le monde 70 sites de production de LEONI sont répartis sur l’Europe, et 4 usines de production sont répartis sur l’Afrique du nord dont 3 sont situés au Maroc : LEONI de Ain Sebaâ, LEONI de Bouskoura et Leoni Berrechid ; Avec 84 % de sa force de travail établie hors de la République fédérale, LEONI joue pleinement la carte de la mondialisation : la société produit en Europe (Allemagne, France, Portugal…), en Amérique (USA, Mexique, Brésil). La concurrence internationale dans le domaine du câblage est particulièrement âpre et le coût de la main-d’œuvre y est déterminant alors elle s’est ouverte sur l’Afrique (Maroc, Tunisie, Égypte, Afrique du Sud) et plus récemment en Asie (Chine, Inde), en plus de l’Europe de l’Est (Pologne, Ukraine, Roumanie, Hongrie, Slovaquie, Turquie). Figure 2 : Emplacement des sites de LEONI au monde I.1.2 Succès et compétences En plus des produits pour l'industrie automobile, LEONI est spécialisée en particulier dans la fabrication des câbles spéciaux : des systèmes par câble « prêt à installer », des modules câblés, des lignes de données et des composants de réseau, des conduites haute tension isolées, des lignes de contrôle, des câbles d'instrumentation, des coaxiaux, des cordons d’alimentation, des câbles de raccordement au secteur, des fils de cuivre et fils tresses. Ses clients, sont surtout des corporations de l'automobile, des fournisseurs d’appareils électriques, de biens d'équipements et de communication ainsi que l’ingénierie médicale. La figure suivante présente les principaux clients du groupe : Figure 3 : Principaux clients de LEONI La tendance va aujourd’hui, dans le secteur de la construction automobile, vers des modules prêts à installer. Pour faire face à la concurrence acharnée, LEONI dispose aussi d'une compréhension des exigences environnementales et des besoins des utilisateurs, pour créer des produits et des solutions optimales. I.2 Organisation du groupe LEONI Deux Divisions regroupent aujourd’hui les activités de la corporation LEONI : La Division Wire & Cable Solutions et la Division Wiring Systems. I.2.1 Division WIRE & CABLE SOLUTIONS La division Wire&Cable Solutions dispose d'un programme de fabrication large qui offre de nombreuses possibilités. Une attention particulière est donnée à la confection de câbles prêts à installer et/ou au raccordement des câbles ainsi qu’au développement et à la fabrication de systèmes complets. En outre, à côté de la fabrication de fils et tresses ainsi que câbles flexibles, deux types de câbles sont produits : Câbles uploads/Industriel/ petit-train-logistique.pdf
Documents similaires
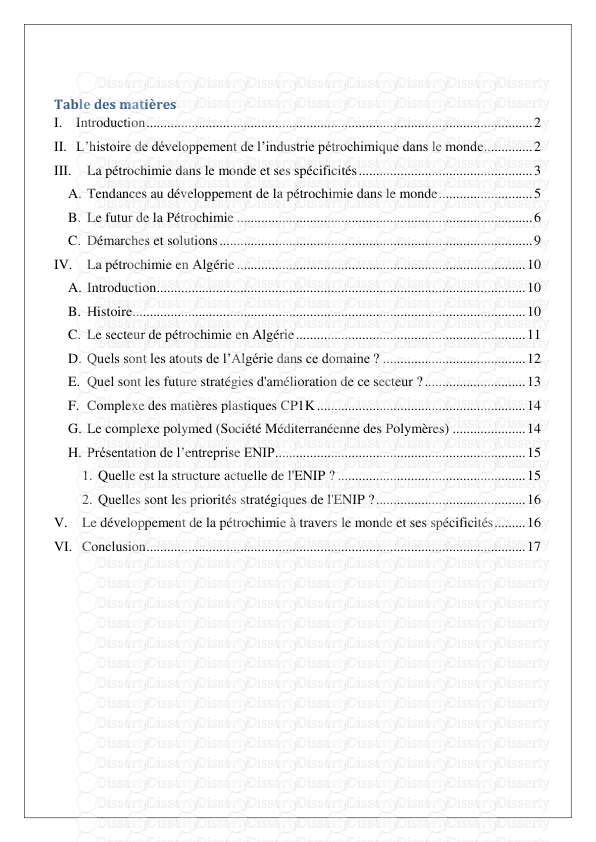
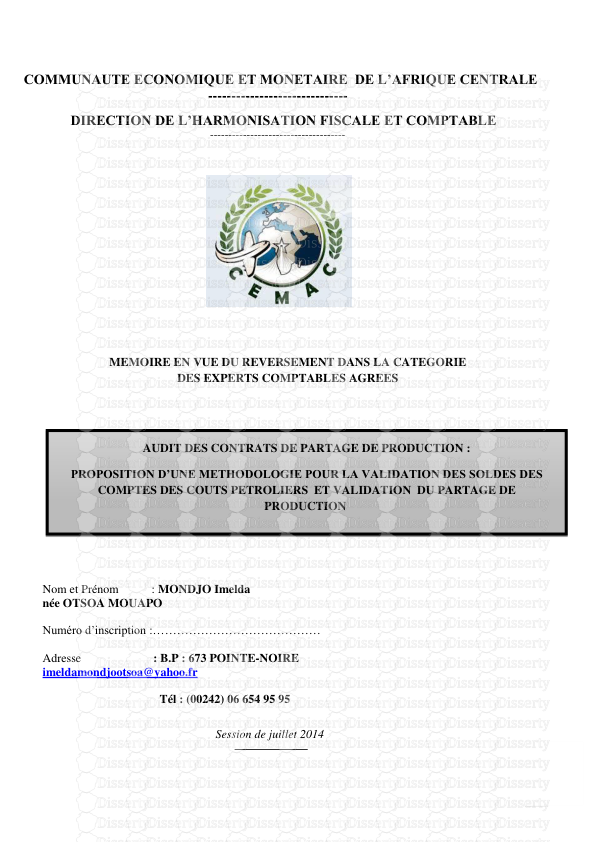
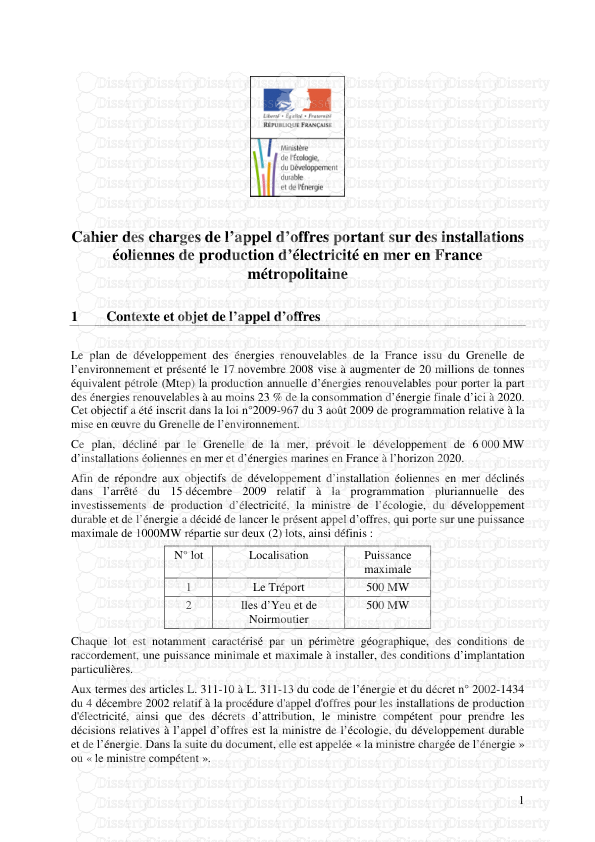
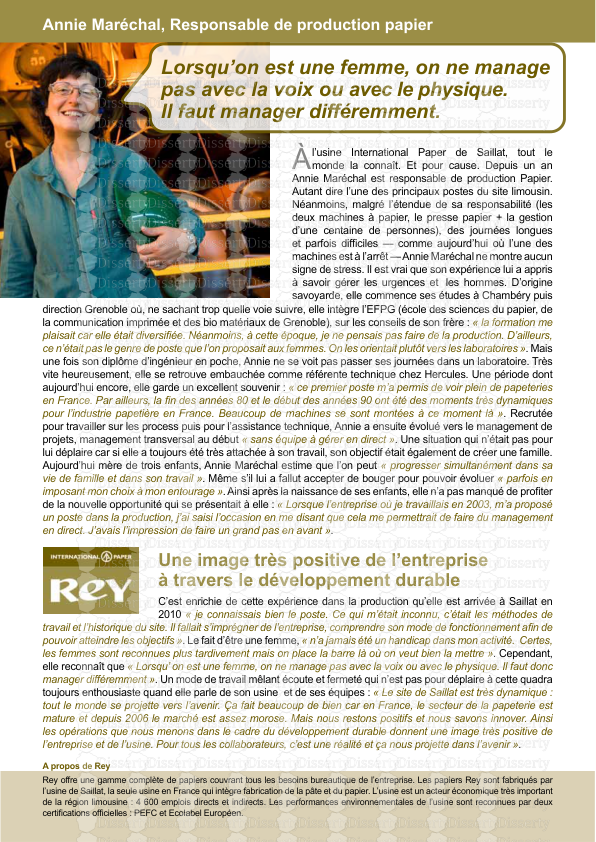
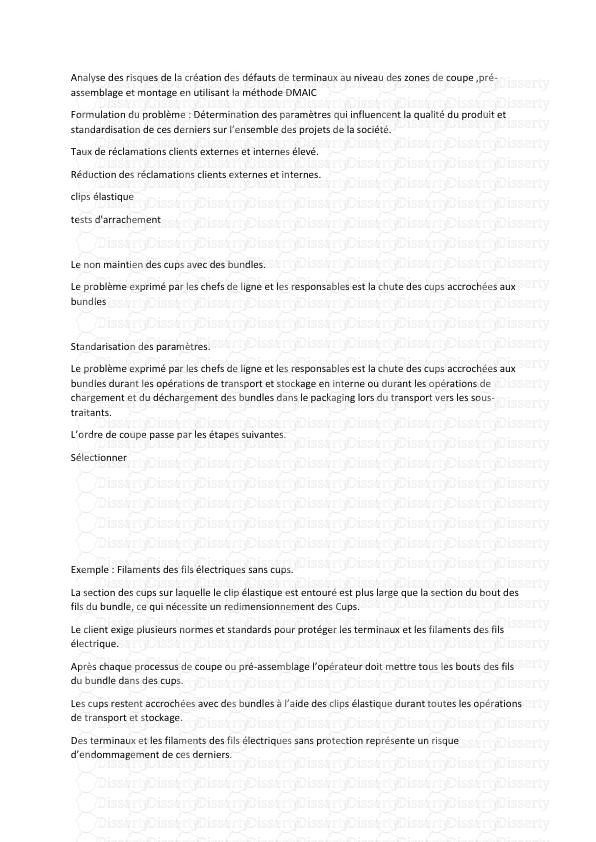
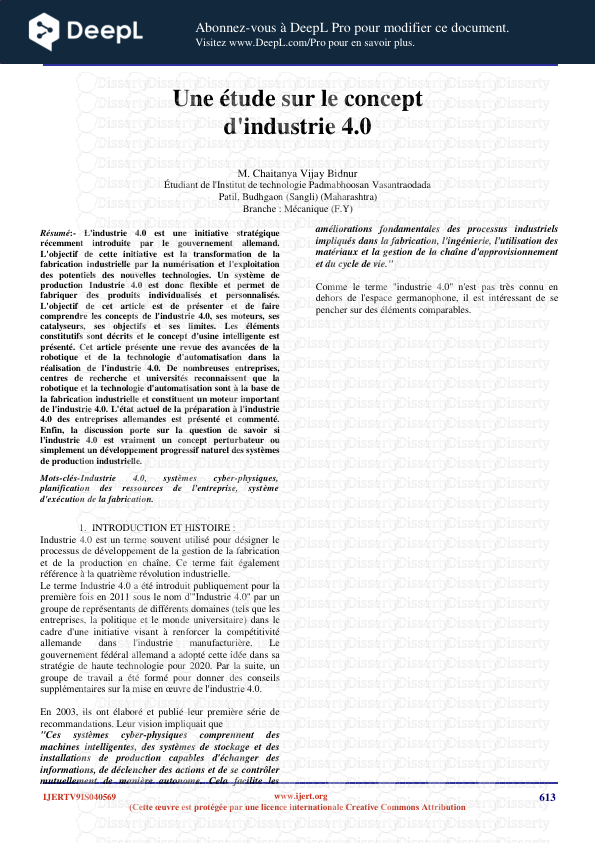
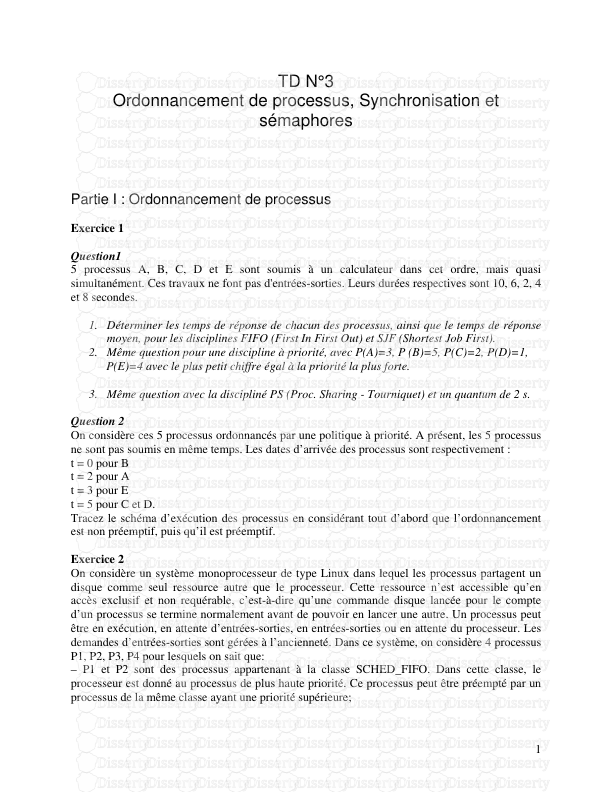
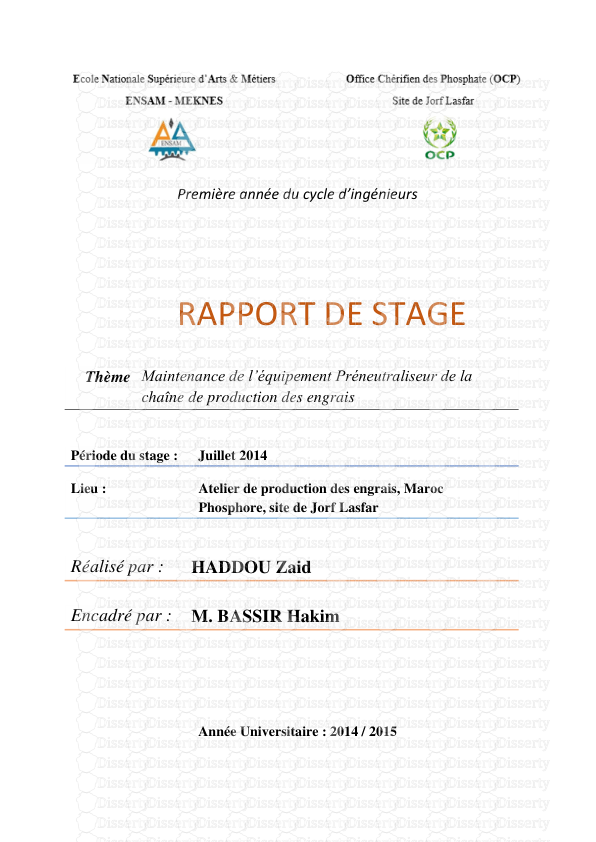
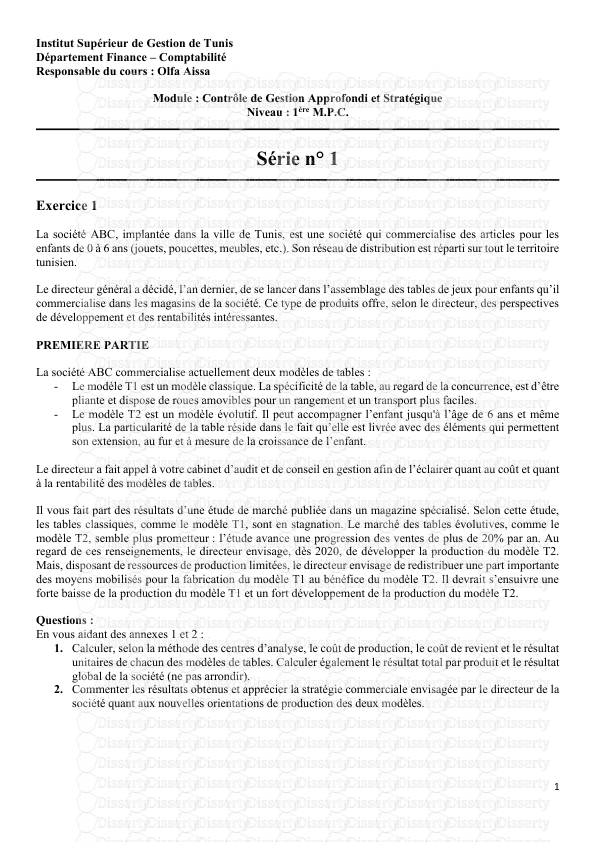
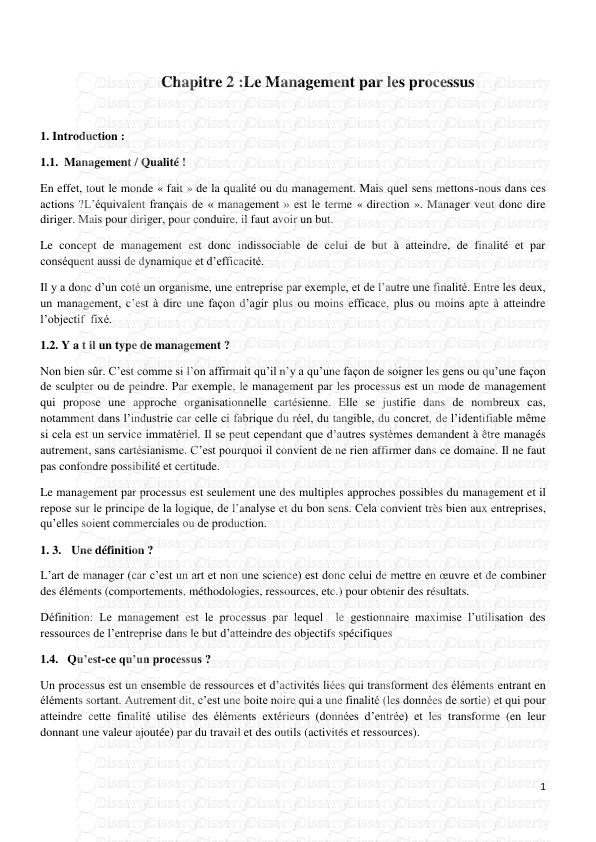
-
60
-
0
-
0
Licence et utilisation
Gratuit pour un usage personnel Attribution requise- Détails
- Publié le Fev 24, 2022
- Catégorie Industry / Industr...
- Langue French
- Taille du fichier 4.5641MB