1 EXEMPLE (5/5) Produit Fini 1 Produit 1 1 Cas : 2 composés et 1 composant Prod
1 EXEMPLE (5/5) Produit Fini 1 Produit 1 1 Cas : 2 composés et 1 composant Produit Fini 2 Produit 1 3 Produit Fini Produit 2 Produit 1 1 2 Cas : règle du plus bas niveau Niv 0 Niv 2 Niv 1 Produit 1 1 Produit Fini Produit 2 Produit 1 1 2 Produit 1 1 Réalisé par Mr. Mekamcha.K 2 Exercice1 Réalisé par Mr. Mekamcha.K Produit Fini Produit 2 Produit 1 1 2 Produit 3 0,25 Semaine 0 1 2 3 4 5 6 Besoin Brut Produit fini 200 100 400 300 200 500 Produit Produit Fini Produit 1 Produit 2 Produit 3 2- Etat des stocks (semaine 0) 300 900 1500 500 3- Lot économique de lancement 700 600 1400 100 4- Délai d’obtention (en semaines) 2 3 1 4 3 SOLUTION (1/4) 1- Pour le produit fini Semaines 0 1 2 3 4 5 6 Demande (BB) 200 100 400 300 200 500 SP 300 100 0 300 0 500 0 Quantités à Produire BN -100 0 +400 0 +200 0 Plan de Production OP (fin) 700 700 OP (début) 700 700 Réalisé par Mr. Mekamcha.K 4 SOLUTION (2/4) 2- Pour la produit 1 Semaines 0 1 2 3 4 5 6 Demande (BB) 700 700 SP 900 200 200 100 100 100 100 Quantités à Produire BN -200 +500 Plan de Production OP (fin) 600 OP (début) 600 Réalisé par Mr. Mekamcha.K 5 SOLUTION (3/4) 3- Pour la produit 2 Semaines 0 1 2 3 4 5 6 Demande (BB) 1400 1400 SP 1500 100 100 100 100 100 100 Quantités à Produire BN -100 +1300 Plan de Production OP (fin) 1400 OP (début) 1400 Réalisé par Mr. Mekamcha.K 6 SOLUTION (4/4) 4- Pour le produit 3 Semaines 0 1 2 3 4 5 6 Demande (BB) 350 SP 500 500 150 150 150 150 150 Quantités à Produire BN -150 Plan de Production OP (fin) OP (début) Réalisé par Mr. Mekamcha.K 7 Exercice 2 (1/2) Une entreprise fabrique deux produits, X et Y. Ces produits sont assemblés à partir de trois pièces A, B et C. Le produit X nécessite deux pièces A et deux pièces C. Le produit Y nécessite une pièce B et trois pièces C. l’assemblage du produit X nécessite deux semaines tandis que celui du produit Y nécessite une semaine. La fabrication des pièces A, B et C nécessite une semaine. Les périodes de productions sont de deux semaines (les ordres de production sont donnés toutes les deux semaines). Développez un plan de production pour une période de 8 semaines (en utilisant la procédure MRP) pour les produits X et Y ainsi que pour les pièces A, B et C. Réalisé par Mr. Mekamcha.K 8 Semaine 0 1 2 3 4 5 6 7 8 Produit X 2 1 4 3 2 5 3 1 Produit Y 1 1 2 3 2 4 2 1 Produit X Y A B C 2- Etat des stocks (semaine 0) 3 2 5 5 5 3- Délai d’assemblage/fabrication (en semaines) 2 1 1 1 1 1- Le PDP des produits X et Y 4- Le lotissement La taille du lot n’est pas fixée au départ, elle est déterminée en fonction du besoin Exercice 2 (2/2) Réalisé par Mr. Mekamcha.K 9 SOLUTION (1/6) 1- Pour le produit X Semaines 0 1 2 3 4 5 6 7 8 Demande (BB) 2 1 4 3 2 5 3 1 SP 3 1 0 3 0 5 0 1 0 Quantités à Produire BN 0 +7 +7 +4 Plan de Production OP (fin) 7 7 4 OP (début) 7 7 4 Réalisé par Mr. Mekamcha.K 10 SOLUTION (2/6) 2- Pour le produit Y Semaines 0 1 2 3 4 5 6 7 8 Demande (BB) 1 1 2 3 2 4 2 1 SP 2 1 0 3 0 4 0 1 0 Quantités à Produire BN 0 +5 +6 +3 Plan de Production OP (fin) 5 6 3 OP (début) 5 6 3 Réalisé par Mr. Mekamcha.K 11 X C A 2 2 Y B C 3 1 Semaines 0 1 2 3 4 5 6 7 8 OP (début) X 7 7 4 OP (début) Y 5 6 3 SOLUTION (3/6) Semaines 0 1 2 3 4 5 6 7 8 BB A 14 14 8 BB B 5 6 3 BB C 14 15 14 18 8 9 Réalisé par Mr. Mekamcha.K 12 SOLUTION (4/6) 3- Pour la pièce A Semaines 0 1 2 3 4 5 6 7 8 Demande (BB) 14 14 8 OL 9 14 8 SP 5 0 0 0 0 0 Quantités à Produire BN 9 14 8 Plan de Production OP (fin) 9 14 8 OP (début) 9 14 8 Réalisé par Mr. Mekamcha.K 13 SOLUTION (5/6) 4- Pour la pièce B Semaines 0 1 2 3 4 5 6 7 8 Demande (BB) 5 6 3 SP 5 5 0 0 0 0 0 Quantités à Produire BN 0 6 3 Plan de Production OP (fin) 6 3 OP (début) 6 3 Réalisé par Mr. Mekamcha.K 14 SOLUTION (6/6) 5- Pour la pièce C Semaines 0 1 2 3 4 5 6 7 8 Demande (BB) 14 15 14 18 8 9 SP 5 15 0 18 0 9 0 Quantités à Produire BN +24 +32 +17 Plan de Production OP (fin) 24 32 17 OP (début) 24 32 17 Réalisé par Mr. Mekamcha.K 15 EXEMPLE MRP 1 (1/3) Sur les Ressources critiques, un calcul de charge est réalisé afin d’identifier en amont les éventuels points de blocage. Familles Acier (tonnes) T.M (Heures std) Bicyclette 0,00057 0,63 Caddie 0,00047 0,24 Trotinette 0,00029 0,39 GAMMES MOIS - Famille Bicycl. 1 2 3 4 5 6 VENTES PREVUES 400 450 600 750 500 400 STOCKS 250 250 250 50 -200 -250 -250 PLAN DE PRODUCTION 400 450 400 500 450 400 CHARGE - Lignes Bicyclettes (h) 252 283,5 252 315 283,5 252 CAPACITES (h) 300 300 300 300 300 300 % 84% 95% 84% 105% 95% 84% x Lissage CRP : Planification de la capacité de production Réalisé par Mr. Mekamcha.K 16 EXEMPLE MRP 1 (2/3) Lissage du plan de charge Réalisé par Mr. Mekamcha.K Deux grandes alternatives permettent d’équilibrer la charge et la capacité : Modifier la capacité : Mettre en place des accords de temps flexible Embaucher du personnel ou intérimaires Ajouter une équipe Investir dans de nouveaux équipements Modifier la charge : Agir avec les stocks Engager des actions commerciales Faire appel à la sous-traitance EXEMPLE MRP 1 (3/3) 17 Réalisé par Mr. Mekamcha.K 18 II- LE JUSTE A TEMPS Au japon « les gens des usines ont toujours tendance à faire de la surproduction » Pour cela, le Directeur de l’usine Toyota a cherché le moyen qui permet de produire : • le produit demandé, et pas un autre ; • au moment où il est demandé (ni avant ni après) ; • dans la quantité demandée (ni plus ni moins). 1- Le Juste à Temps Dans un atelier de production, cela se traduit par le fait qu’un poste amont ne doit produire que ce qui lui est demandé par son poste aval qui ne doit lui-même produire que ce qui lui est demandé par son propre poste aval, et ainsi de suite... Le poste le plus en aval ne devant produire que pour répondre à la demande des clients. 19 Les entreprises japonaises se sont efforcées de réduire les coûts de commande en allégeant les procédures administratives et en demandant la coopération des fournisseurs. la production " juste à temps " est une approche globale et le système Kanban en constitue un outil. 2- Les Outils du juste à temps TPM (Total Productive Maintenance) SMED (Single Minute Exchange of Die : changement d’outils rapide) 5 S Kanban 20 A- TPM Cette méthode de maintenance vise à maximiser le temps d’utilisation des équipements : elle assure le bon fonctionnement des machines, en pénalisant le moins possible la production et en y associant tout le monde. B- SMED Changer d’outil et effectuer les réglages de la série suivante le plus rapidement possible en équipant les outils de systèmes de verrouillage rapide et en transformant des opérations réalisées normalement « hors temps » de production en opérations en « temps masqué ». En réduisant à l’extrême le temps nécessaire à changer de fabrication, on diminue le coût de revient des petites séries. 21 C- 5 S Seiri Débarasser Seiton Ranger Seiso Nettoyer Seiketsu Ordonner Shitsuke Discipline C’est une technique d’organisation de l’espace de travail pour avoir un lieu plus sécuritaire, propre et bien rangé. Sa mise en œuvre permet d'améliorer les conditions de travail et la motivation des salariés, de réduire les dépenses en temps et en énergie, ainsi que les risques d'accidents et/ou sanitaires. On estime qu’elle apporte un gain de 8% de productivité. 22 3- Le KANBAN L’outil appelé « uploads/Industriel/05-chapitre-04-juste-a-temps-dernier-cours.pdf
Documents similaires
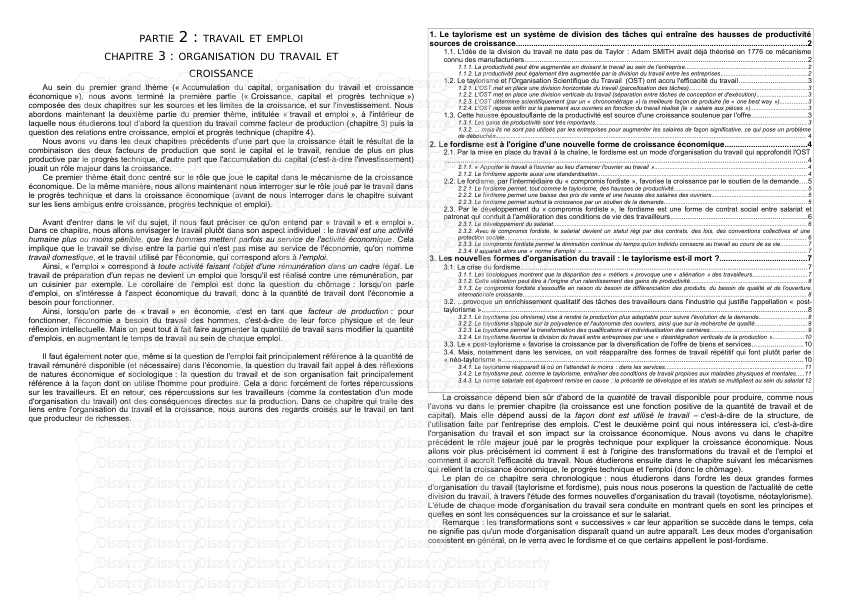
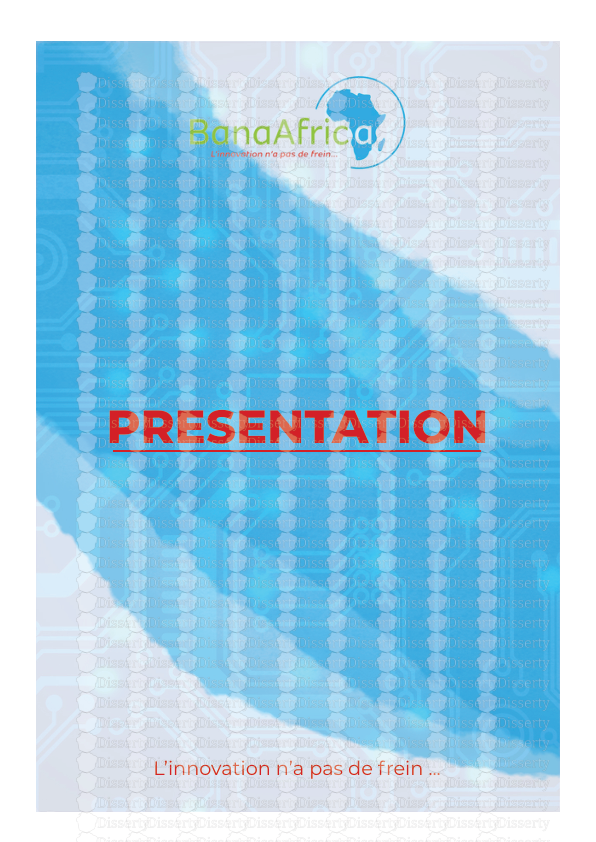
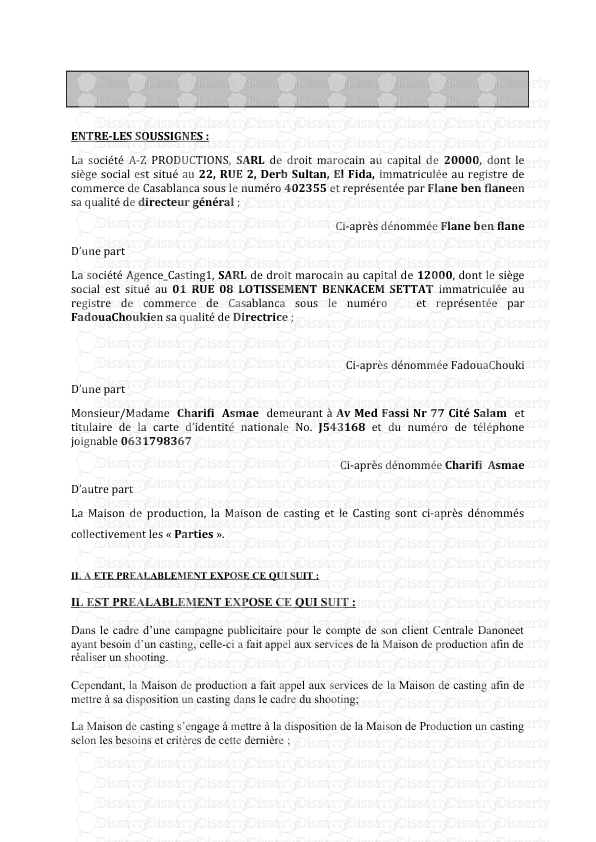
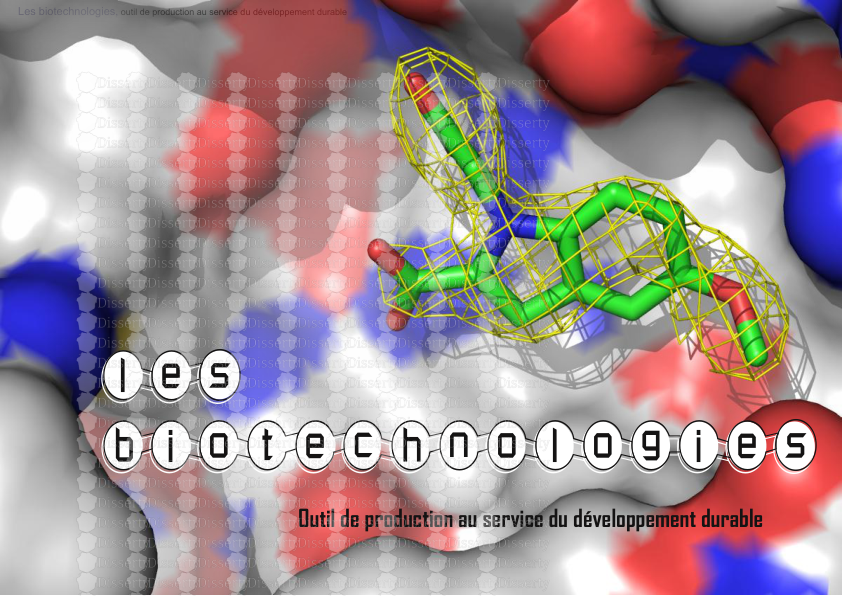
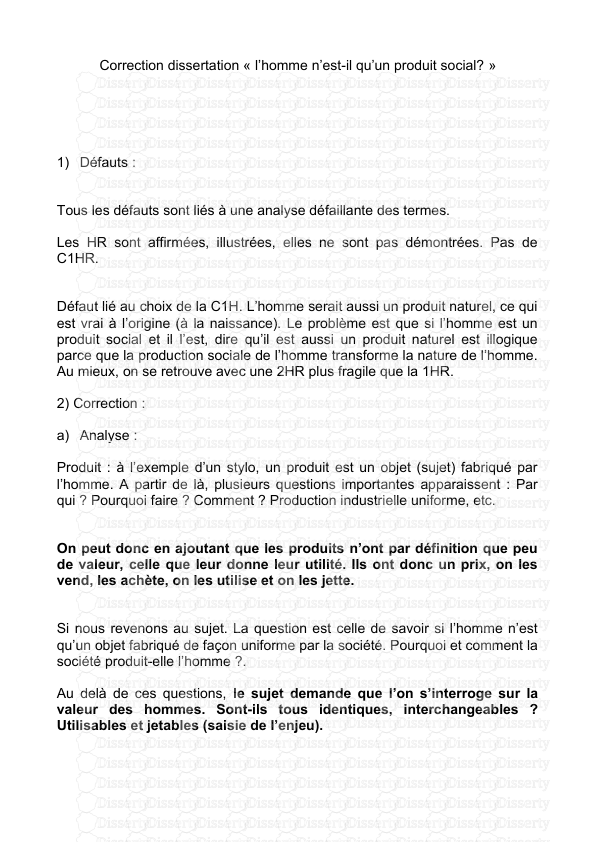
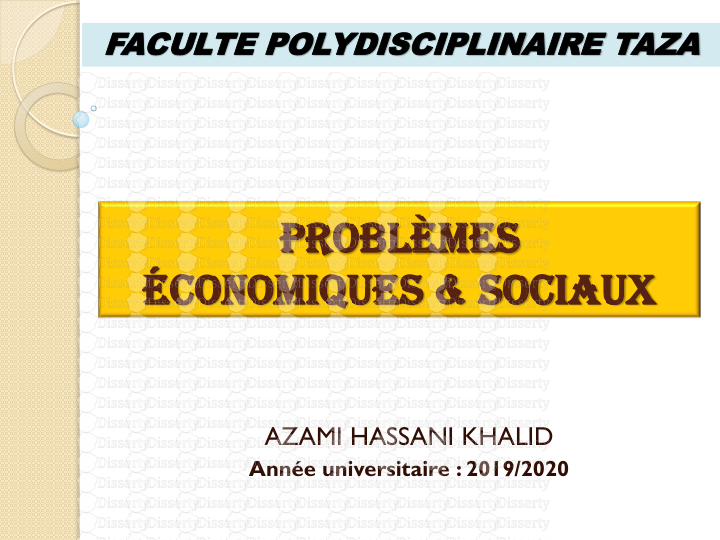
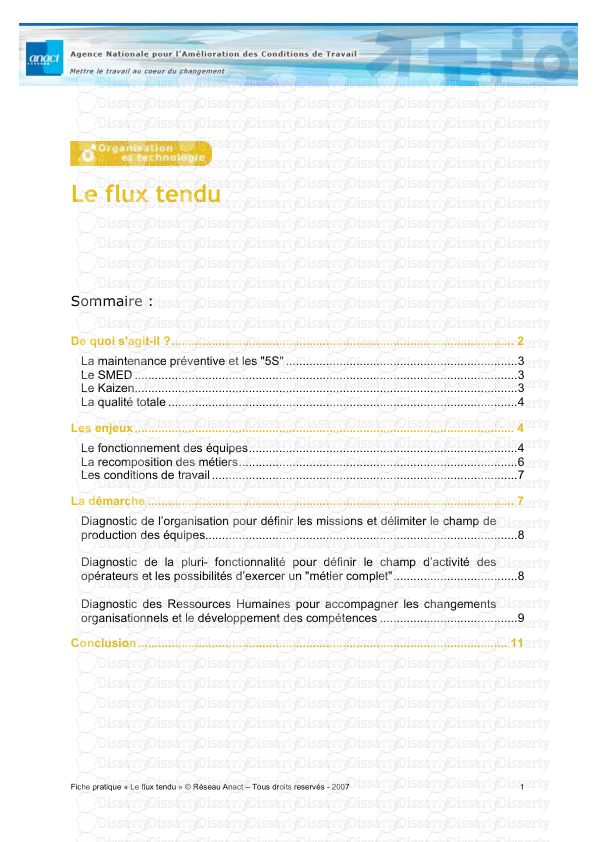
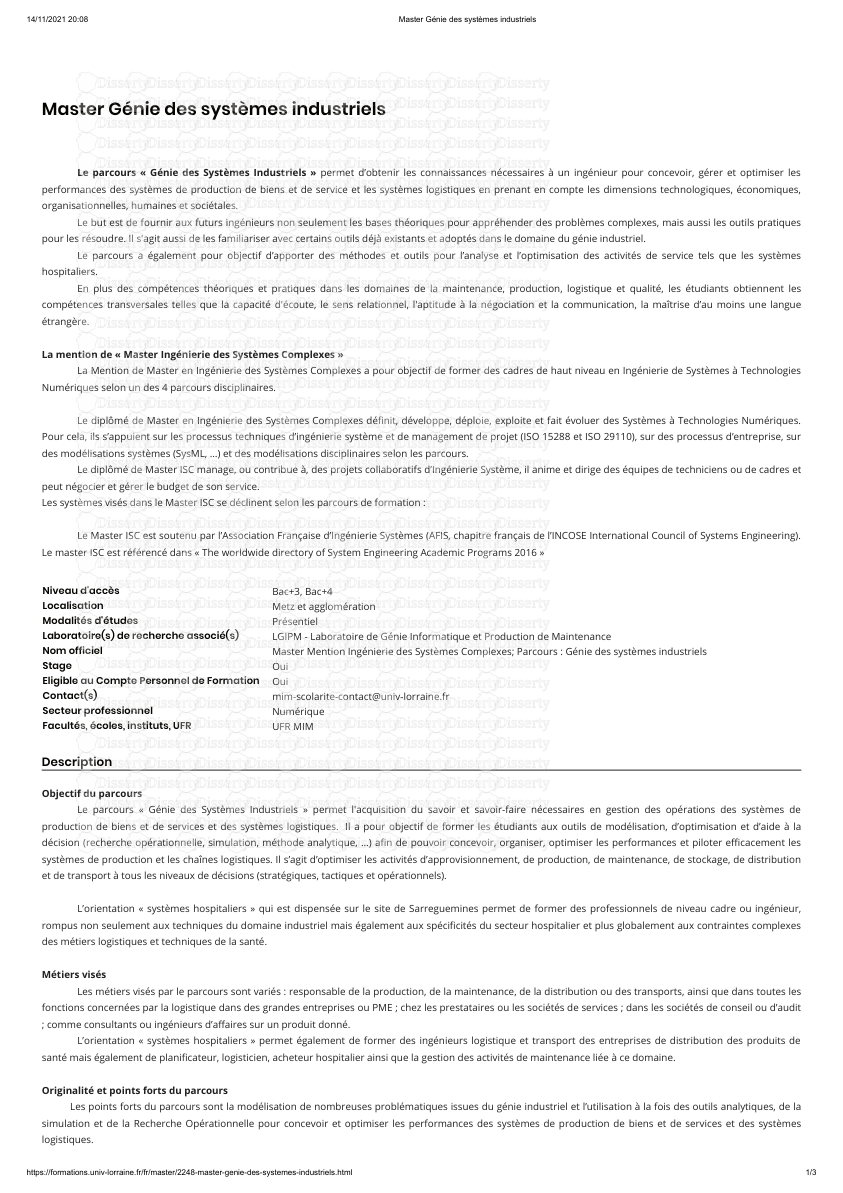
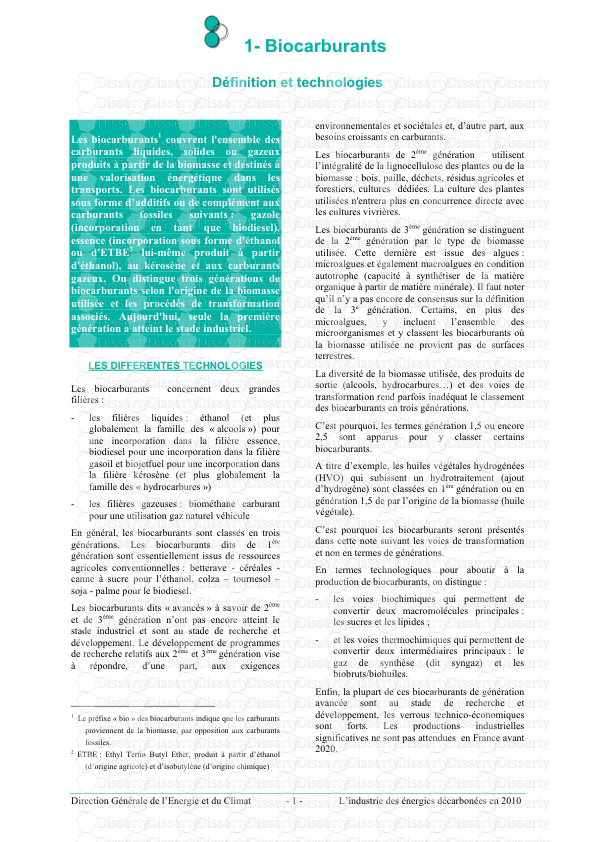
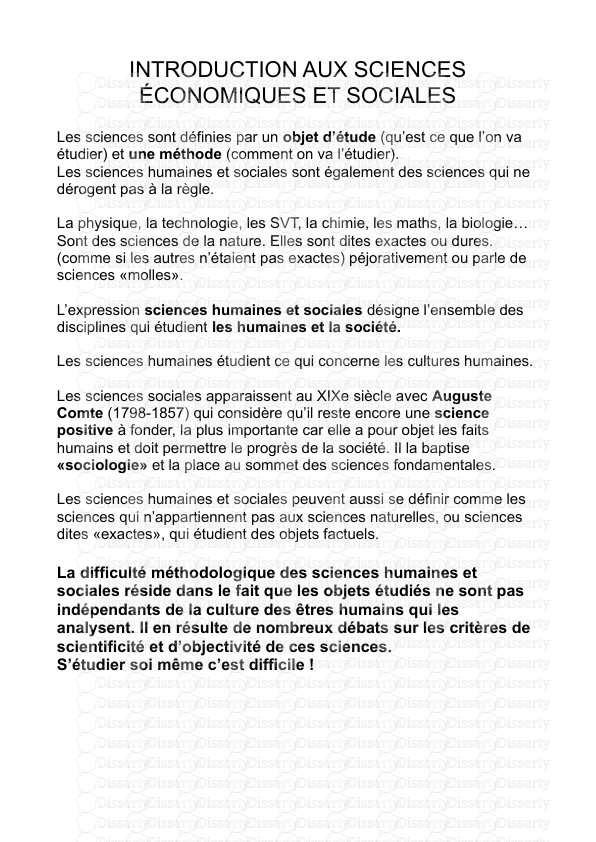
-
51
-
0
-
0
Licence et utilisation
Gratuit pour un usage personnel Attribution requise- Détails
- Publié le Nov 03, 2022
- Catégorie Industry / Industr...
- Langue French
- Taille du fichier 1.1570MB