Boite à Outils: Lean Manufacturing (Kaizen) Réalisée par Youness KHNINICH LEAN
Boite à Outils: Lean Manufacturing (Kaizen) Réalisée par Youness KHNINICH LEAN Consulting 20 Rue les Racines Appt N 2 Résidence les Racines Val fleuri, Cite Plateau CP 20390 Casablanca - Maroc Préambule Depuis plus de 50 ans, Toyota a développé et déployé un modèle d’amélioration continue (TPS, Toyota Production System) qui les a conduit à devenir le numéro un mondial de l’industrie automobile. Ce modèle s’appuie sur l’implication totale des différentes composantes de l’entreprise autour d’un projet commun, l’élimination méthodique des gaspillages. Différents outils permettent d’analyser le fonctionnement des organisations pour augmenter la valeur des produits et services en réduisant leurs coûts. Aujourd’hui, tous les constructeurs et leurs équipementiers se sont engagés dans une démarche «Lean». D’autres secteurs d’activité ont suivi (banques, hôpitaux, centres d’appels…). La délocalisation n’est pas la seule solution. Les résultats financiers affichés sont devenus des exemples de réussites sur les marchés. 2 Proposition d'assistance technique Présentation des différents outils Lean Manufacturing Notre boite à outils comprend les outils suivants: • Le 5S : C'est le premier outil à mettre en oeuvre dans une démarche de type Lean Management, et donc à fortiori pour le Lean Manufacturing. Le 5S permet d’éliminer ce qui est inutile, définir une place pour chaque chose, nettoyer, définir les gammes et procédure nécessaires, enfin auditer et mesurer l’amélioration. Cette outil de base du Lean a pour principal objectif de changer les mentalités et mettre en route une politique d’amélioration continue. • L'analyse VSM (Value Stream Mapping) : Cette méthode d'analyse du Lean manufacturing permet de définir les principales réserves de productivité d'une unité de production en suivant le flux complet de la production d'une pièce. La mesure du temps d'écoulement des pièces, des niveaux de stock et de leurs valeur, permet de définir un certain nombre de chantiers d'amélioration à mettre en place en priorité dans une démarche Lean Manufacturing. • Le SMED (Single Minute Exchange Die) : Cette méthode du Lean Manufacturing, d’abord utilisée pour réduire les temps de changement d’outillage, peut être employée pour flexibiliser tout processus productif ou administratif. L’objectif est l’élimination progressive des stocks et l’amélioration de la productivité grâce à la mise en place d’une organisation réactive et flexible. • La TPM (Total Productive Maintenance) : La TPM est un outil essentiel du Lean Manufacturing pour mesurer les pannes, les arrêts machine, et les risques associés. Un plan d'action correctif peut alors être mis en place, ainsi qu'un véritable management de la maintenance préventive. • Le Hoshin de flux : Cette méthode regroupe plusieurs outils du Lean Manufacturing pour optimiser les flux grâce à la réduction des temps d’écoulement, l’élimination des stocks intermédiaires, la suppression des temps non productifs, et l’équilibrage des postes de production. • Les Poka-Yoke : Ce sont des systèmes simples permettant d'éviter les erreurs involontaires des opérateurs. Les Poka-Yoke sont aussi appelés "détrompeurs" ou "systèmes anti-erreur" et sont courramment utilisés dans le Lean Manufacturing. • Le Kanban : C'est un système d'ordonnancement de la production à base de cartes (ou via un système visuel simple) permettant de tirer les flux. Le Kanban est fréquemment utilisés dans le Lean Manufacturing pour le management des flux tirés. Il est donc en théorie opposé à la méthode MRP, qui gère les flux en les poussant. Le Kanban, peut toutefois être combiné avec une méthode MRP. Il permet alors le management des flux internes en laissant la gestion des flux externe au MRP. • Standardisation du poste de travail (Standardized Work). Présentation des différents outils Lean Manufacturing Présentation des différents outils Lean Manufacturing • QRQC: Une méthode de résolution de problème pragmatique et terrain tel que le QRQC permet de résoudre rapidement les incidents clients. Cette démarche permet d'impliquer le top management jusqu'a l'opérateur. • AMDEC: Analyse des Modes de Défaillances, de leurs Effets et de leur Criticité. Méthode d'analyse préventive qui permet de recenser, de mettre en évidence et de quantifier les risques potentiels de défaillance d'un produit, d'un processus ou d'un équipement. AMDEC est la traduction de l'anglais FMECA (Failure Modes, Effects and Criticality Analysis). Son but est de hiérarchiser les actions d'amélioration à conduire sur un processus, un produit, un système en travaillant par ordre de criticité décroissante. Outil 5S DEFINITION La méthode 5S est une méthode structurée visant à organiser le lieu de travail. Un lieu de travail bien organisé motive les personnes. Une démarche 5S améliore la sûreté, l'efficacité du travail, la productivité et favorise un sens de fierté et d'appartenance pour tous les opérateurs de ce lieu de travail. OBJECTIFS - Mettre en place une démarche qualité concrète centrée sur la fonctionnalité et la propreté de l'espace de travail. - Travailler efficacement. - Impliquer les hommes dans la gestion de leur environnement. INTERETS - Obtenir des résultats concrets et visibles rapidement. - Développer le travail en équipe et la communication. - Favoriser la mise en place d'un plan de progrès permanent. METHODOLOGIE • SEIRI : Débarrasser Distinguer l'utile de l'inutile en triant et en éliminant. Eviter d'accumuler le non-nécessaire. • SEITON : Ranger Déterminer la place de tous les articles "utiles". "Chaque place a sa chose et chaque chose a sa place". • SEISO : Nettoyer L'ensemble du lieu de travail et tous les équipements doivent être nettoyés. Eviter l'accumulation de la saleté, des déchets et autres corps étrangers pour que le lieu de travail soit propre et sans danger. Le nettoyage fait partie des taches de maintenance quotidienne de tous. 3 N e t to y e r 2 R a n g e r 1 E lim in e r 5 R e s p e c t e r 4 S ta n d a r d is e r 5 S L e n e tto y a g e q u o tid ie n , c ’e s t in s p e c te r l’é q u ip e m e n t p o u r d é t e c te r le s p a n n e s p o te n t ie lle s . R e n d r e é v id e n t l’e s p a c e d e tr a v a il L e s ta n d a r d e s t-il re s p e c té ? S i n o n , p o u rq u o i? E s t- c e fa c ile à tr o u v e r? C o m m e n t r e tr o u v e r s a p la c e ? S u is - je à l’a is e p o u r to u c h e r à m a m a c h in e ? Y - a t-il d e s tr a c e s ? Q u e lle r è g le p o u r to u s ? E s t- c e u tile ? Outil 5S • SEIKETSU : Ordonner, dans le sens de fixer des règles d'organisation Il s'agit d'entretenir les 3 premiers "S". Pour maintenir la propreté et éliminer les causes de désordre, il est indispensable de les inscrire comme des règles ordinaires, des standards. • SHITSUKE : Rigueur Veiller à l'application des règles, les remettre en mémoire, et s'il y a lieu corriger les dérives. CONCLUSION 5 S, 5 étapes : 1. J'élimine les objets inutiles, 2. Je range, 3. Je nettoie, 4. Je standardise, 5. Je respecte les règles et j'améliore. Outil Cartographie des processus (VSM) DEFINITION La Value Stream Mapping est une cartographie descriptive des flux dans le processus étudié, qui dans l'idéal couvre la supply chain entière; de l'approvisionnement des matières à la livraison au client consommateur. Dans la pratique, le VSM est le plus souvent limité aux portes de l'entreprise, éventuellement étendu aux fournisseurs et sous-traitants stratégiques. OBJECTIFS Cet outil sert à : - Visualiser le flux de création de valeur dans le processus, - Discriminer les tâches à valeur ajoutée des tâches à non valeur ajoutée, - identifier les sources de gaspillage, de non performance du processus actuel, - Réduire les stocks et encours et améliorer les temps de traversée (lead time) Outil Cartographie des processus (VSM) METHODOLOGIE Outil SMED DEFINITION Le SMED l'abréviation de l'anglais Single Minute Exchange of Die, littéralement « changement d'outil de presse en une minute », expression qui est généralement traduite en français par « changement rapide d’outil ». Avec un peu plus de précision single minute correspond à un temps dont l'ordre de grandeur est la minute (soit de quelques minutes). OBJECTIFS La méthode SMED est utilisée dans le cadre de changements de fabrication. Elle a pour objectif de réduire ces temps, et permettre ainsi de réduire la taille de lot minimale. En effet, si les temps de changement de série deviennent nuls, on peut alors envisager une fabrication à l'unité sans augmenter les coûts. METHODOLOGIE -Réalisation d'un 1er changement de série uploads/Management/boite-a-outils-lean.pdf
Documents similaires
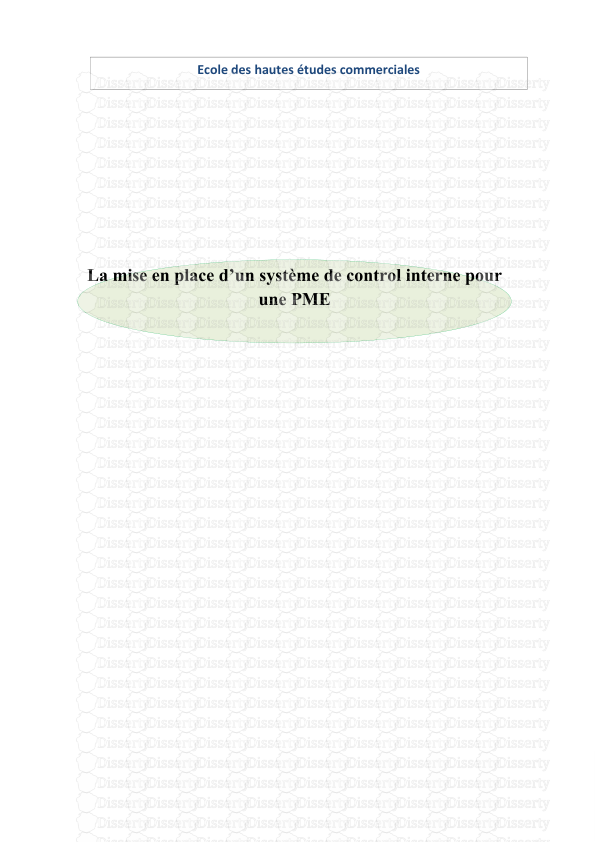
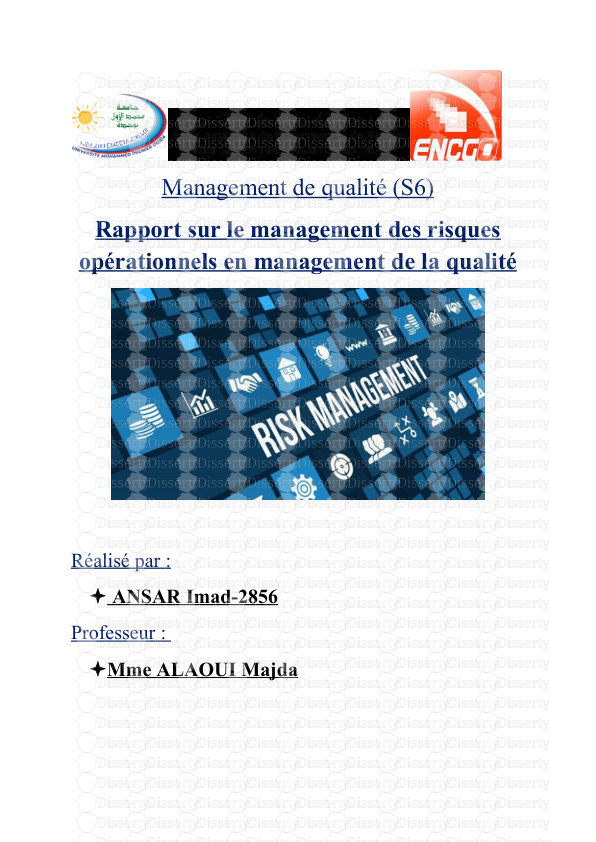
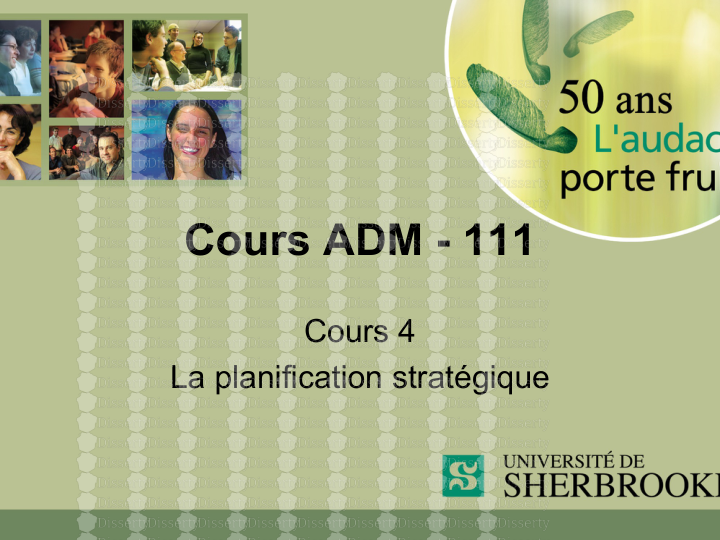
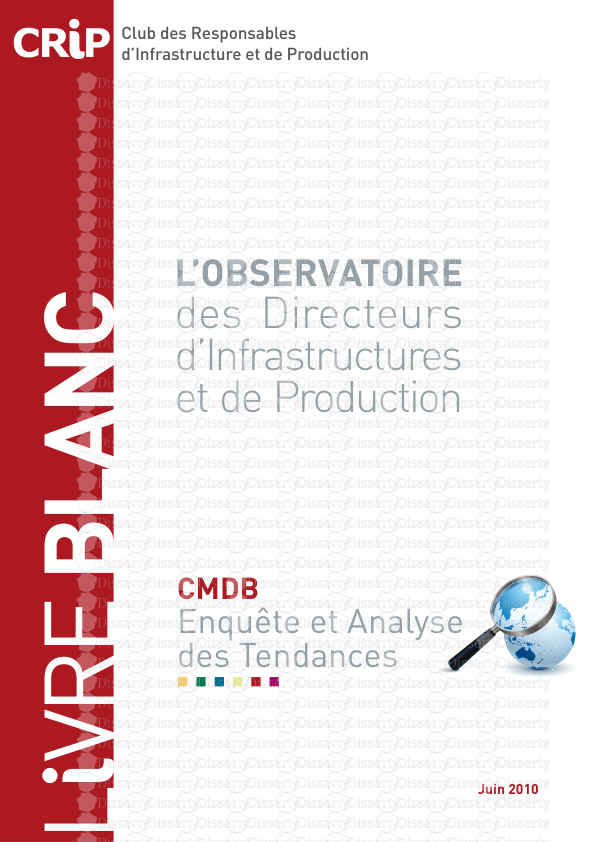
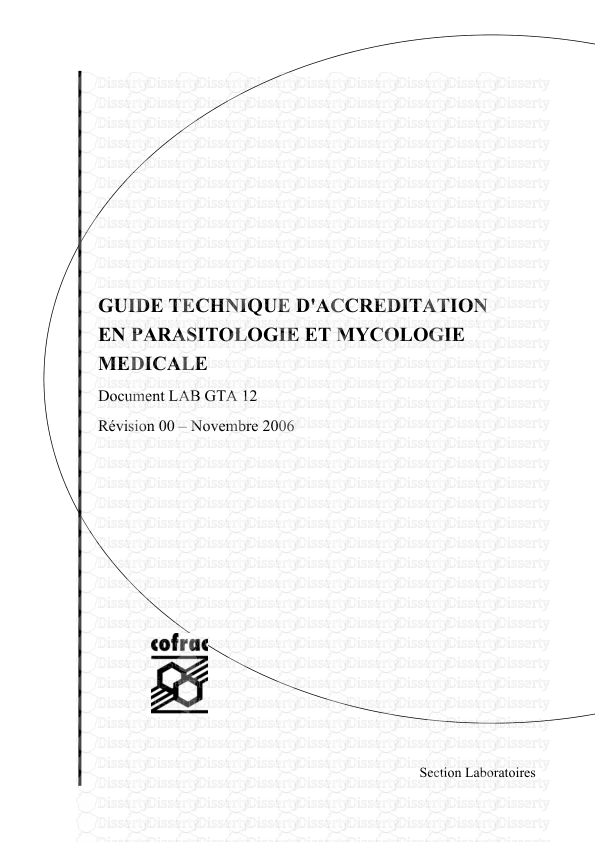

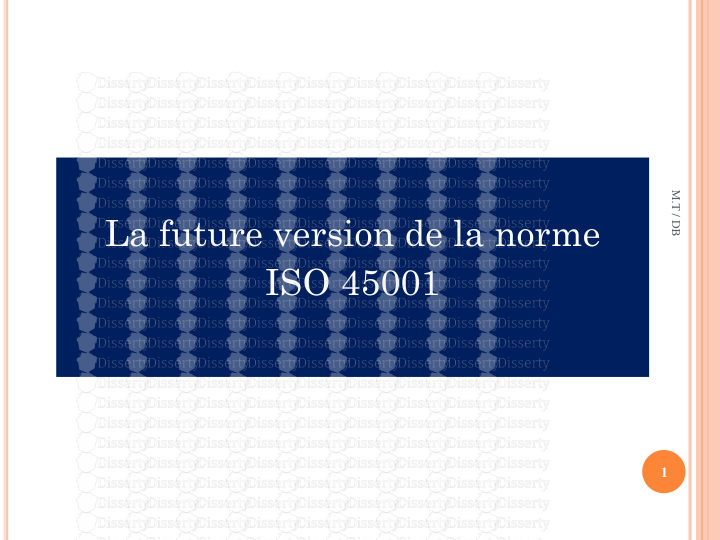
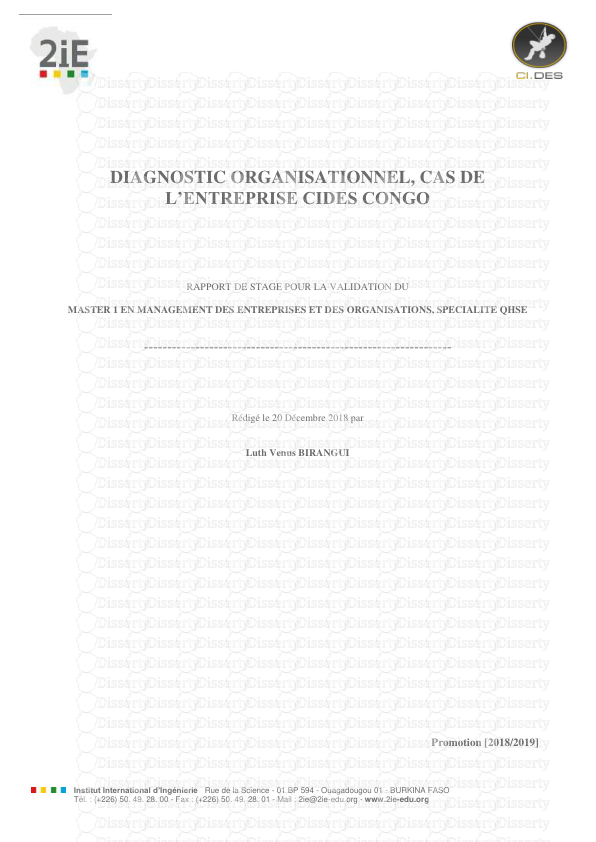
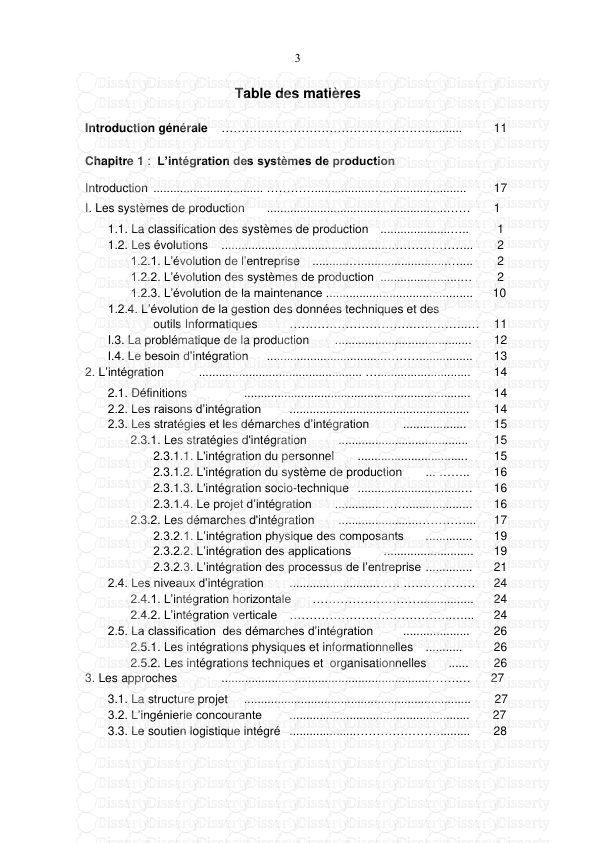
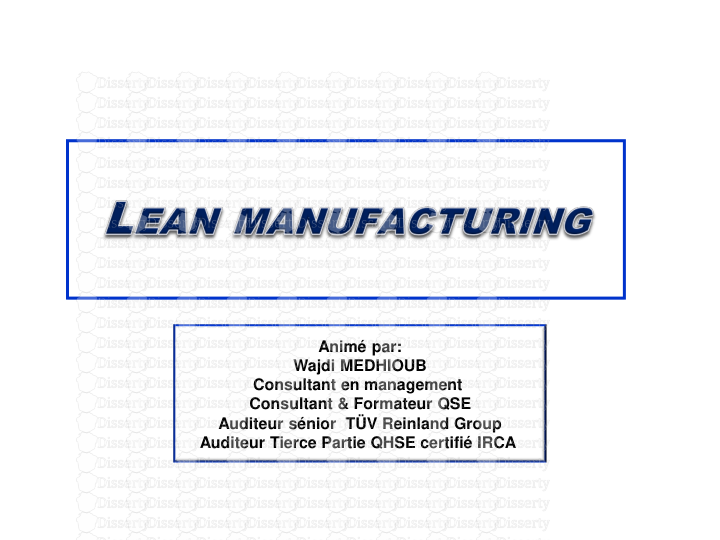
-
46
-
0
-
0
Licence et utilisation
Gratuit pour un usage personnel Attribution requise- Détails
- Publié le Jui 26, 2022
- Catégorie Management
- Langue French
- Taille du fichier 0.6489MB