Toute reproduction sans autorisation du Centre français d’exploitation du droit
Toute reproduction sans autorisation du Centre français d’exploitation du droit de copie est strictement interdite. © Techniques de l’Ingénieur, traité Matériaux métalliques M 4 227 − 1 Corrosion sèche des métaux Cas industriels : dépôts, milieux fondus par Laurent ANTONI Docteur-ingénieur de l’Institut national polytechnique de Grenoble, École nationale supérieure d’électrochimie et d’électrométallurgie de Grenoble et Alain GALERIE Professeur à l’Institut national polytechnique de Grenoble, École nationale supérieure d’électrochimie et d’électrométallurgie de Grenoble a corrosion sous dépôt se produit lorsque des dépôts de cendres ou de sels s’accumulent sur les parois métalliques et modifient en conséquence leur environnement. Elle se rencontre dans de nombreuses installations indus- trielles mettant en jeu des combustions, comme les chaudières à gaz, les inci- nérateurs de déchets, les moteurs, les réacteurs en lit fluidisé, les turbines à gaz ou dans les procédés de conversion du charbon. Les réactions mises en jeu sont nombreuses et un mécanisme unique ne permet pas une généralisation de ce type de corrosion. Différents articles de revue ont abordé ce mode de cor- rosion. Nous considérerons dans cet article plus en détail le phénomène de corrosion chaude (hot corrosion) et l’attaque dans les incinérateurs de déchets ménagers. Un autre type de corrosion que nous allons étudier dans cet article est celle qui se produit dans les milieux fondus. Métaux fondus et sels fondus sont uti- lisés pour leurs bonnes propriétés de transfert de chaleur dans les domaines industriels du traitement thermique, des échangeurs de chaleur et du stockage de l’énergie. 1. Corrosion sous dépôt.............................................................................. M 4 227 - 2 1.1 Corrosion chaude (hot corrosion ).............................................................. — 2 1.1.1 Fluxage basique.................................................................................. — 4 1.1.2 Fluxage acide ...................................................................................... — 5 1.1.3 Influence de la température............................................................... — 5 1.2 Corrosion dans les incinérateurs................................................................ — 5 2. Autres types de corrosion..................................................................... — 6 2.1 Corrosion par les métaux fondus............................................................... — 6 2.1.1 Corrosion par l’aluminium liquide .................................................... — 7 2.1.2 Corrosion par le zinc liquide.............................................................. — 7 2.1.3 Corrosion par le cuivre liquide .......................................................... — 7 2.1.4 Corrosion par le plomb liquide.......................................................... — 8 2.1.5 Corrosion par le sodium liquide........................................................ — 8 2.1.6 Corrosion par le magnésium liquide ................................................ — 8 2.2 Corrosion par les sels fondus..................................................................... — 8 2.2.1 Corrosion par les chlorures fondus................................................... — 8 2.2.2 Corrosion par les carbonates fondus................................................ — 9 2.2.3 Corrosion par la soude caustique ..................................................... — 9 2.2.4 Corrosion par les fluorures fondus ................................................... — 9 2.2.5 Corrosion par les nitrates ou nitrites fondus.................................... — 9 2.3 Corrosion par les verres fondus................................................................. — 9 3. Conclusion ................................................................................................. — 10 Références bibliographiques ......................................................................... — 10 Pour en savoir plus........................................................................................... Doc. M 4 229 L CORROSION SÈCHE DES MÉTAUX _________________________________________________________________________________________________________ Toute reproduction sans autorisation du Centre français d’exploitation du droit de copie est strictement interdite. M 4 227 − 2 © Techniques de l’Ingénieur, traité Matériaux métalliques L’étude sur la corrosion sèche des métaux présentée dans le traité Matériaux métalliques des Techniques de l’Ingénieur comporte plusieurs fascicules : — M 4 224 - Corrosion sèche des métaux. Cas industriels : oxydation, carburation ; — M 4 225 - Corrosion sèche des métaux. Cas industriels : sulfuration, nitruration ; — M 4 226 - Corrosion sèche des métaux. Cas industriels : halogènes ; — M 4 227 - Corrosion sèche des métaux. Cas industriels : dépôts ; milieux fondus (le pré- sent article) ; — M 4 228 - Corrosion sèche des métaux. Choix des alliages ; — Doc. M 4 229 - Corrosion sèche des métaux. Cas industriels. Pour en savoir plus. Pour une étude théorique du phénomène, le lecteur se reportera aux articles [M 4 220] et [M 4 221] de ce traité. 1. Corrosion sous dépôt La corrosion sous dépôt se rencontre dans de nombreuses ins- tallations industrielles mettant en jeu des combustions (références bibliographiques [1] à [15]). La gravité de cette corrosion est très variable et dépend notam- ment de la nature du fioul utilisé, des impuretés contenues (S, Cl, Na, K, V, Zn, Pb...) et de la quantité d’air nécessaire à la combustion. Ainsi, la corrosion chaude est plus sévère dans les turbines à gaz d’installations industrielles ou marines que dans les turbines à gaz d’avion. La corrosion chaude, associant générale- ment oxydation et sulfuration (cf. articles [M 4 224] et [M 4 225]), conduit à des attaques plus importantes qu’une corrosion dans la même atmosphère mais en l’absence de dépôt. En effet, ce dépôt (cendres ou sels qui s’accumulent sur les parois métalliques) modi- fie les potentiels chimiques de l’environnement au niveau de son interface avec le métal. En présence d’oxygène et de soufre, le dépôt aura pour conséquence de baisser le potentiel en oxygène et d’augmenter celui en soufre, ce qui rendra plus difficile la forma- tion d’un oxyde protecteur et durable. Ces dépôts, souvent riches en sels, vont augmenter les vitesses de corrosion, et plus particu- lièrement lorsqu’ils deviennent liquides (tableau 1) et dissoudront les oxydes formés pour attaquer le métal. Pour garder une tenue satisfaisante à la corrosion, nous verrons qu’il faut utiliser des alliages à teneur élevée en chrome ou bien des alliages revêtus (cf. article [M 4 224]). 1.1 Corrosion chaude (hot corrosion) La « corrosion chaude » est un phénomène de corrosion accélé- rée survenant quand un sel fondu (généralement Na2SO4) se dépose sous forme de gouttelettes sur la pièce chaude. Il en résulte une vitesse de corrosion bien supérieure à celle de la simple oxy- dation, particulièrement autour des températures de 700 oC et 800 oC comme le montre la figure 1. L’apparition de la corrosion chaude dépend de nombreux para- mètres comme la composition de l’alliage, du gaz environnant et du dépôt, et la température. Cette influence ne se manifeste pas seulement par les vitesses d’attaque élevées mais également par les mécanismes particuliers mis en jeu et déterminés par l’obser- vation après utilisation des matériaux hors d’usage. Des essais en laboratoire ont été mis au point pour simuler les conditions réelles : le test dénommé « burner rig test », des tests dans des fours à atmosphère contrôlée, des tests dans des cellules électrochimiques. Le premier test vise à simuler les conditions réelles d’utilisation et, plus particulièrement, celles rencontrées dans les turbines à gaz. L’appareillage consiste en un brûleur à gaz ou à fioul liquide, une chambre de combustion et une chambre de travail où sont situés les échantillons. On ajoute des contaminants dans la chambre de combustion ou dans le fioul pour provoquer la formation de dépôts sur les échantillons. Les vitesses de corrosion sont généralement bien supérieures à celles mesurées dans la réa- lité. Une utilisation des vitesses de corrosion mesurées sera donc à faire avec précaution pour prédire les durées de vie des instal- lations. Ce test est en revanche approprié à la comparaison du comportement des différents alliages. Les essais dans les fours de laboratoire sont utilisés pour comprendre les différents méca- nismes de la corrosion chaude et l’influence relative des différents paramètres (température, environnement, dépôts). Les dépôts sont généralement réalisés par pulvérisation à chaud (≈ 100 oC) de solutions contenant le composé à étudier. Pour ces essais en labo- ratoire, les cinétiques peuvent être mesurées par un suivi gravimé- trique (gain, perte de métal), mais on préférera les mesures de perte de métal et de profondeur d’attaque interne à partir de coupes. Les microstructures obtenues lors des essais de labora- toire sont également à comparer à celles observées sur les échan- tillons prélevés sur les installations pour s’assurer que les mécanismes mis en jeu sont bien identiques. Figure 1 – Variation de la vitesse de corrosion en fonction de la température dans le cas de la corrosion sous dépôt [18] 700 850 Vitesse de corrosion Température (°C) Oxy dati on p ure Corrosion Oxydation Corrosion chaude induite par SO3 Corrosion Corrosion type II Corrosion type I Corrosion type II Corrosion type I Fluxage acide ou basique _________________________________________________________________________________________________________ CORROSION SÈCHE DES MÉTAUX Toute reproduction sans autorisation du Centre français d’exploitation du droit de copie est strictement interdite. © Techniques de l’Ingénieur, traité Matériaux métalliques M 4 227 − 3 (0) La corrosion chaude se produit suivant un processus en deux étapes : initiation de l’attaque puis propagation. Durant la phase d’initiation, l’attaque reste faible et comparable à celle observée sans le dépôt dans la même atmosphère. Nous retrouvons l’évo- lution des couches observée lors des phénomènes de sulfuration (cf. article [M 4 225]) ou de chloruration (cf. article [M 4 226]). La diminution du caractère protecteur de ces couches, associée à la formation de composés à bas point de fusion, accélère la dégrada- tion des oxydes et conduit à une forte augmentation des cinétiques de corrosion (phase de propagation). L’amélioration, de la tenue à la corrosion chaude passe donc par une augmentation de la durée de la phase d’initiation, c’est-à-dire par la formation d’une barrière capable de résister aux différents mécanismes de propagation illustrés (figure 2). La perte du caractère protecteur d’une couche d’oxyde est obte- nue par : — un phénomène d’oxydation catastrophique (cf. article [M 4 221]) dans le cas où uploads/Industriel/ corrosion-seche-des-metaux 1 .pdf
Documents similaires
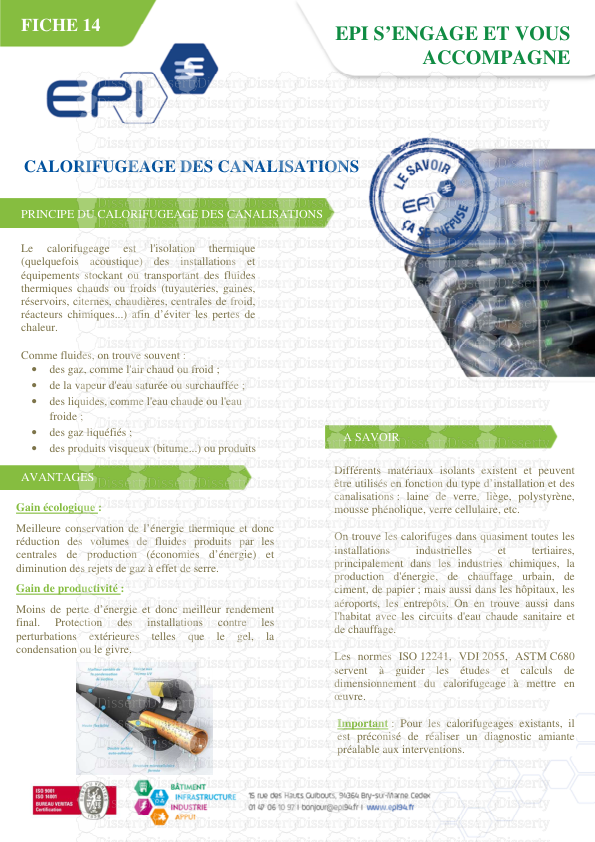
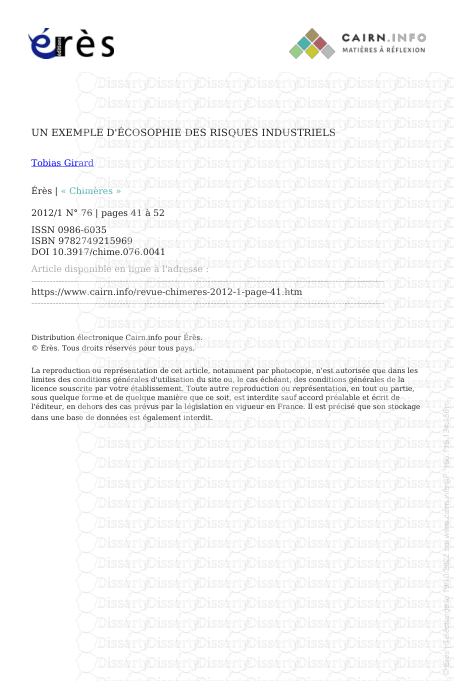
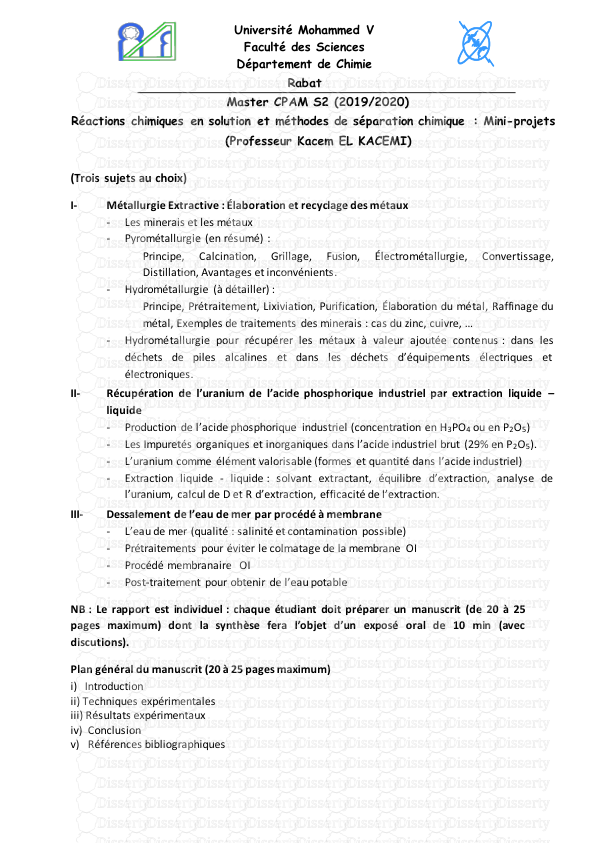
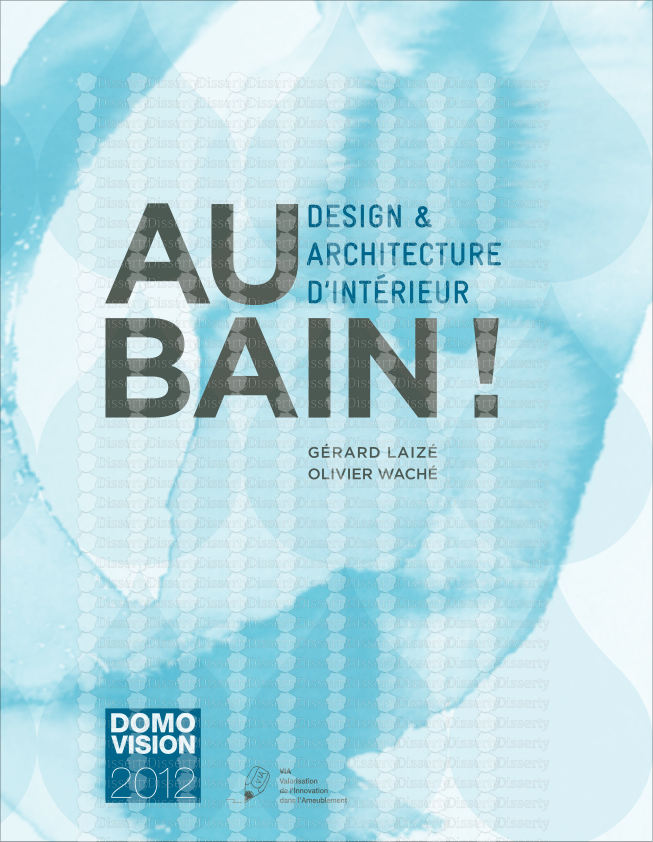
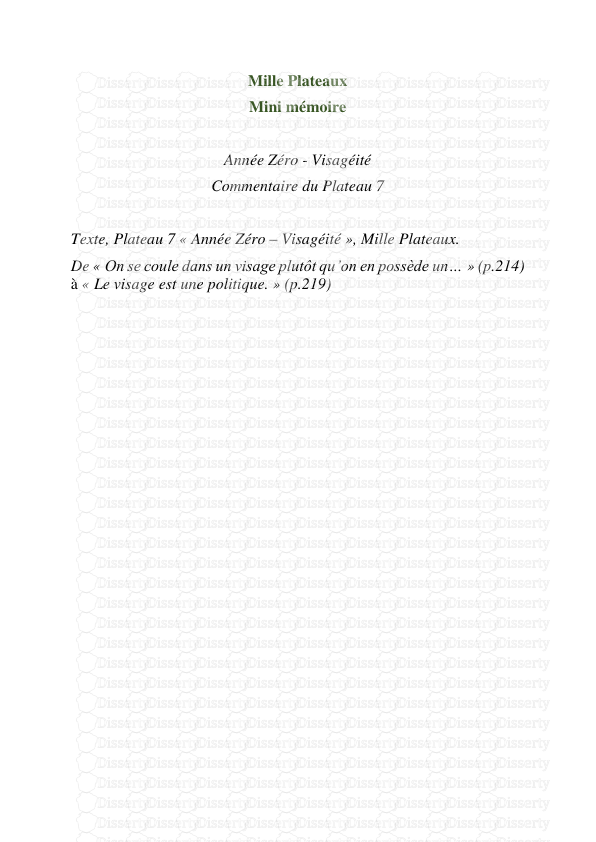
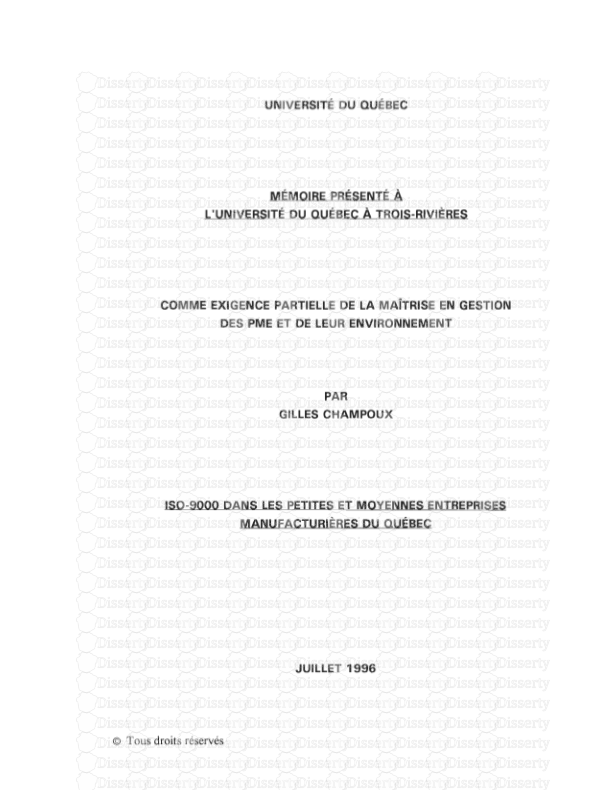
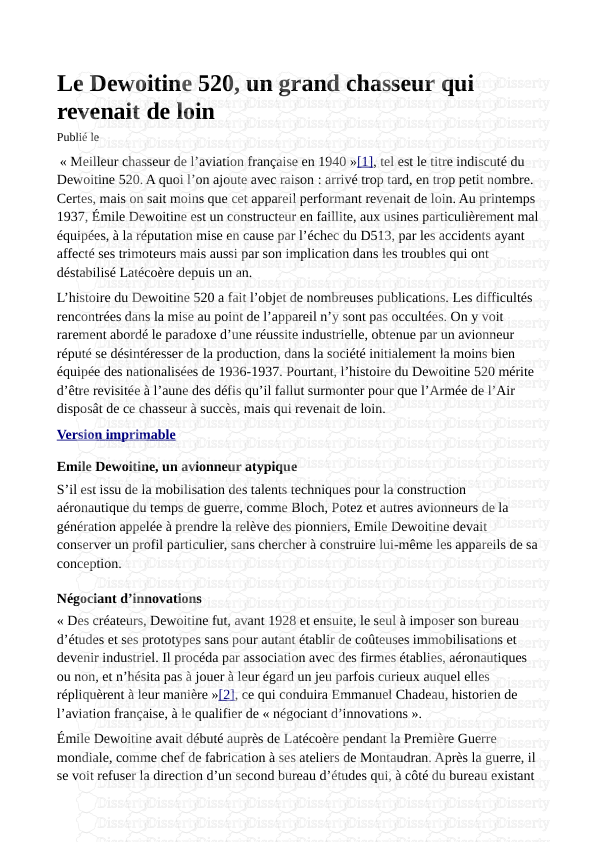
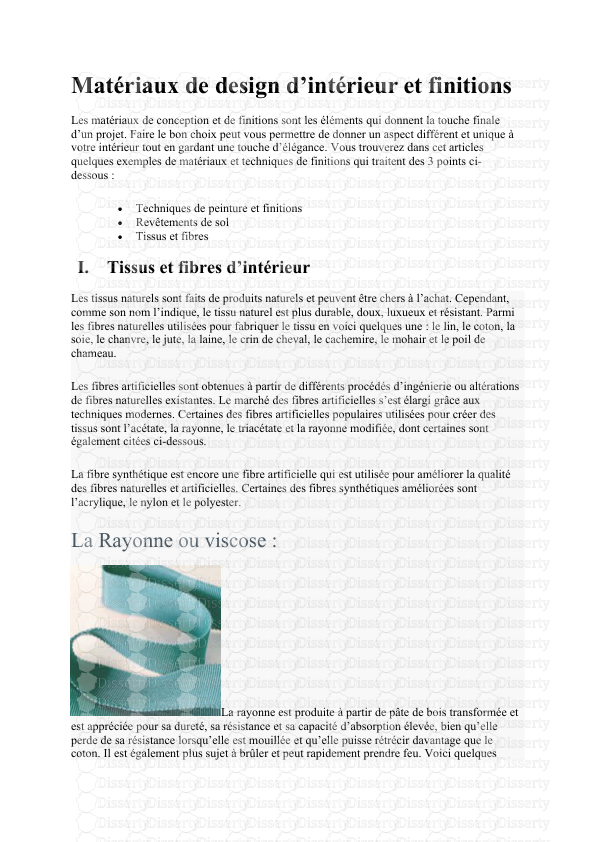
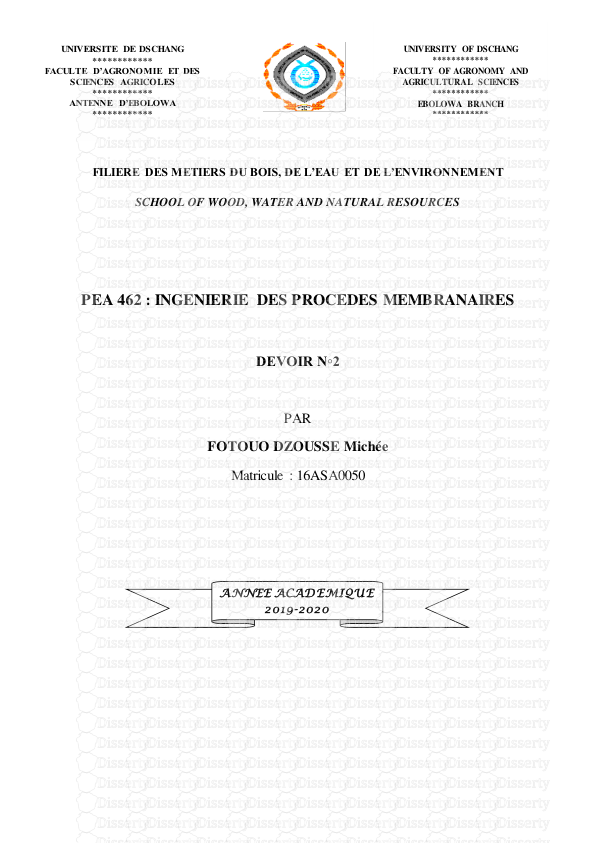
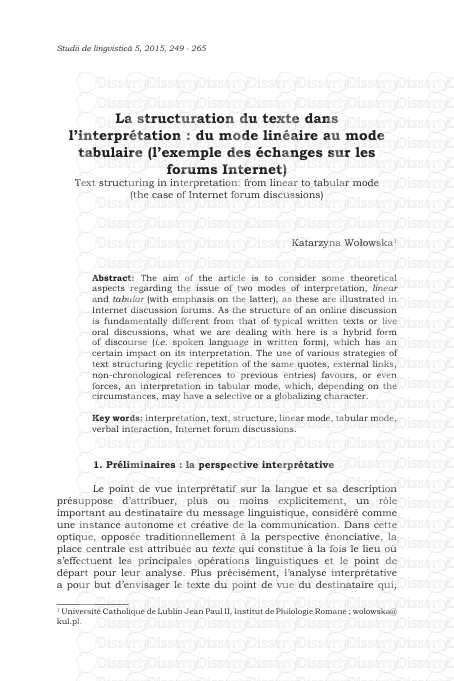
-
58
-
0
-
0
Licence et utilisation
Gratuit pour un usage personnel Attribution requise- Détails
- Publié le Jui 20, 2021
- Catégorie Industry / Industr...
- Langue French
- Taille du fichier 0.5034MB