ALLIAGES D'ALUMINIUM SOMMAIRE 1. Historique et fabrication de l'aluminium. 2. A
ALLIAGES D'ALUMINIUM SOMMAIRE 1. Historique et fabrication de l'aluminium. 2. Avantages techniques et économiques. 3. Influence des éléments d'alliage. 4. Influence des conditions de fabrication - Etats métallurgiques. 5. Caractéristiques typiques des alliages et des états de livraison. 6. Classement des alliages suivant leur utilisation. 7. Formes de produits - Définitions. 8. Technologies de mise en oeuvre. 9. Précautions d' emploi. 1. Historique et fabrication de l'aluminium L'aluminium est le métal le plus récemment découvert puisqu'il n'est utilisé industriellement que depuis la fin du XIX° siècle. Pourtant l'alun, sulfate double d'aluminium et de potassium, le composé d'aluminium le plus anciennement connu, était déjà décrit par Pline l'ancien et utilisé à Rome comme mordant pour les couleurs. Il a fallu attendre 1825 pour que Hans Christian Oersted obtienne l'aluminium à l'état de corps simple sous forme d'une poudre grise contenant encore une très grande quantité d'impuretés. En 1827, Friedrich Wöhler obtint cette même poudre grise d'aluminium contenant cependant moins d'impuretés. Ce n'est qu'en 1854 qu'Henri Sainte-Claire-Deville présente le premier lingot d'aluminium obtenu à l'état fondu, par un procédé mis en application en 1859 de façon industrielle par Henry Merle dans son usine de Salindres (Gard), berceau de la société Pechiney. Mais ce procédé était compliqué ce qui donnait un métal très cher, réservé à des utilisations dans le luxe et l'orfèvrerie. En 1886, Paul Louis Toussaint Héroult en France et Charles Martin Hall aux Etats Unis déposent indépendamment leurs brevets sur la production d'aluminium par électrolyse à chaud de l'alumine, oxyde déshydraté de l'aluminium, dissoute dans de la cryolithe fondue (fluorure double de sodium et d'aluminium). L'invention de la dynamo, qui remplaça la pile comme source d'électricité, et l'utilisation des chutes hydrauliques : la " houille blanche ", rendit possible la production économique du métal. P.L.T. Héroult monte sa première usine en 1887 à Neuhausen en Suisse, sur une chute du Rhin, berceau de la société l'Aluminium Suisse. Il monte une usine en 1889 à Froges (Isère), berceau de l'hydroélectricité française Alliages d' aluminium http://www.euralliage.com/alliage.html 1 sur 15 04/08/2014 12:50 développée par Aristide Bergès, puis une autre à La Praz dans la vallée de l'Arc (Savoie). C.M. Hall monte en 1888 une usine pour la Pittsburgh Reduction Co qui deviendra en 1907 l'Aluminum Company of America. L'aluminium est entré dans sa phase industrielle ; sa production a connu en 100 ans une croissance prodigieuse, le mettant au premier rang des métaux non ferreux et au deuxième de tous les métaux derrière le fer, ainsi que l'illustrent les chiffres suivants : Année Production mondiale (tonnes) 1886 13 1890 200 1900 5 700 1910 44 350 1920 121 000 1930 269 000 1940 810 000 1950 1 507 000 1960 4 624 000 1970 10 307 000 1980 16 000 000 1999 28 000 000 L'aluminium est d'abord employé à l'état pur pour sa légèreté et son inaltérabilité, mais la mise au point d'alliages d'une plus grande résistance mécanique va être déterminante. Conrad Claessen trouve en 1905 la possibilité de durcir certains alliages par traitement thermique. Alfred Wilm met au point le " Duralumin " (aluminium de Düren), alliage d'aluminium et de cuivre, qui durcit par trempe. Aladar Pacz imagine en 1920 l'alliage aluminium silicium affiné au sodium, " l'Alpax ". La fabrication de l'aluminium se décompose en deux étapes : - extraction de l'alumine de la bauxite, - fabrication de l'aluminium par électrolyse de l'alumine. Les gisements du minerai de départ, la bauxite, sont très nombreux et importants sur tout le globe terrestre. Les plus vieux, aujourd'hui épuisés, étaient dans le sud de la France, en particulier près du village des Baux en Provence, qui a donné son nom au minerai. La bauxite est un mélange d'oxyde d'aluminium, l'alumine, d'oxyde de silicium, la silice, d'oxyde de fer, d'oxyde de titane et d'eau. Les teneurs de ces différents oxydes sont les suivantes : alumine : 40 - 60 % silice : 2 - 12 % oxyde de fer : 18 - 25 % oxyde de titane : 2 - 4 % eau : 10 - 15 % L'extraction de l'alumine s'effectue par attaque de la bauxite à température et pression élevées au moyen d'une solution de soude caustique (procédé Bayer). Les impuretés insolubles sont séparées de la solution par décantation et filtration et portent le nom de " boues rouges " en raison de leur couleur due à la présence d'oxyde de fer. De la solution épurée, refroidie et diluée, on peut tirer l'hydroxyde d'aluminium : Al(OH)3 ; celui-ci est calciné à 1200°C pour donner l'alumine : Al2O3, qui se présente sous la forme d'une poudre de couleur blanche. L'alumine est mélangée à de la cryolithe et ce mélange est liquide à 1000°C ; l'électrolyse de l'alumine se fait Alliages d' aluminium http://www.euralliage.com/alliage.html 2 sur 15 04/08/2014 12:50 dans une grande cuve peu profonde, dont le fond est garni de graphite qui sert de cathode (pôle -). Les anodes (pôle +) sont faites avec de la pâte de coke et de brai précuite et plongent dans le bain. Le passage du courant continu décompose l'alumine : l'aluminium liquide à 1000°C se dépose à la cathode, au fond de la cuve, et l'oxygène se dégage aux anodes en les brûlant ; celles-ci sont donc consommées et changées régulièrement. L'aluminium est récupéré par siphonnage dans une poche de coulée. La tension continue appliquée aux électrodes est de 4,5 à 6 V ; l'intensité du courant passant dans la cuve n'a cessé de progresser au fil des ans avec les améliorations technologiques apportées aux cuves : la toute première cuve d'Héroult avait 4000 A ; en 1914, les cuves avaient 20.000 A, 100.000 A en 1944, 175.000 A en 1980 et elles atteignent aujourd'hui 300.000 A. La consommation électrique de l'électrolyse de l'aluminium est importante, de l'ordre de 13.000 kWh par tonne d'aluminium produite. Pour fabriquer 1 tonne d'aluminium, il faut 2 tonnes d'alumine et 4 tonnes de bauxite. Sommaire 2. Avantages techniques et économiques Les emplois de l'aluminium et de ses alliages se sont développés dans des proportions surprenantes pour des raisons techniques et économiques. Les raisons techniques sont nombreuses : - l'aluminium est un métal dont la densité est faible, ce qui vaut à ses alliages la dénomination d'alliages légers. L'aluminium est le métal le plus léger après le lithium et le magnésium : Métal pur Masse volumique (kg/dm3) Lithium 0,53 Magnésium 1,74 Aluminium 2,70 Titane 4,51 Fer 7,86 Cuivre 8,96 Plomb 11,40 L'aluminium est donc 3,3 fois plus " léger " que le cuivre et 2,9 fois plus léger que le fer ; il " pèse " grossièrement 3 fois moins que les métaux industriels usuels. C'est cette caractéristique qui a valu aux alliages d'aluminium leur développement dans les moyens de transport et en particulier dans l'aéronautique. - l'aluminium conduit bien l'électricité et la chaleur. Sa résistivité électrique est de 2,74 10-8 W.m ; convertie en conductivité électrique comparée à celle du standard cuivre IACS, cela représente 63 %. Les alliages d'aluminium ont une conductivité plus faible que celle de l'aluminium pur, variant de 30 % à 50 % IACS. A poids égal de cuivre, l'aluminium a une conductivité électrique 2 fois supérieure, d'où les applications de l'aluminium dans le transport d'électricité haute tension sur grande distance. - l'aluminium n'est pas magnétique. Sa perméabilité magnétique relative est de 1,004 soit 50 fois plus faible que celle des aciers. Cette qualité s'ajoute à ses propriétés de conduction électrique et milite en faveur de son utilisation dans les blindages de câbles, dans les circuits électroniques et dans la réalisation de bon nombre d'appareils de mesure. - l'aluminium a une bonne résistance à la corrosion. L'aluminium a une grande affinité pour l'oxygène, et très vite une couche d'alumine recouvre sa surface ; cette couche est parfaitement couvrante et protège le métal sous-jacent. De plus, il est possible d'accroître cette protection par les traitements d'oxydation anodique (anodisation). - l'aluminium est un métal robuste. Si les caractéristiques de l'aluminium pur sont faibles, comme pratiquement celles de tous les métaux purs, la gamme d'alliage très étendue permet de trouver celui qui correspond aux contraintes d'utilisation envisagée. En effet, les alliages les plus résistants peuvent avoir une charge de rupture supérieure à 700 MPa, donc Alliages d' aluminium http://www.euralliage.com/alliage.html 3 sur 15 04/08/2014 12:50 largement équivalente à celles des aciers trempés. - l'aluminium peut être utilisé dans une large plage de températures. Contrairement à d'autres métaux, tel que l'acier, l'aluminium ne se fragilise pas aux basses températures et ses caractéristiques mécaniques augmentent même aux températures des gaz liquéfiés, d'où son utilisation en cryogénie. Sa température de fusion est basse : 658°C, nettement inférieure à celle du cuivre (1083°C) et à celle du fer (1536°C) ; cela ne lui permet pas de résister aux très hautes températures. Il existe cependant des alliages qui résistent bien à des températures de l'ordre de 200°C souvent atteintes en aéronautique et en astronautique. La charge de rupture de l'aluminium de pureté commerciale en fonction de la température est la suivante : -196°C 160 MPa -80°C uploads/Industriel/ alliages-d-x27-aluminium.pdf
Documents similaires
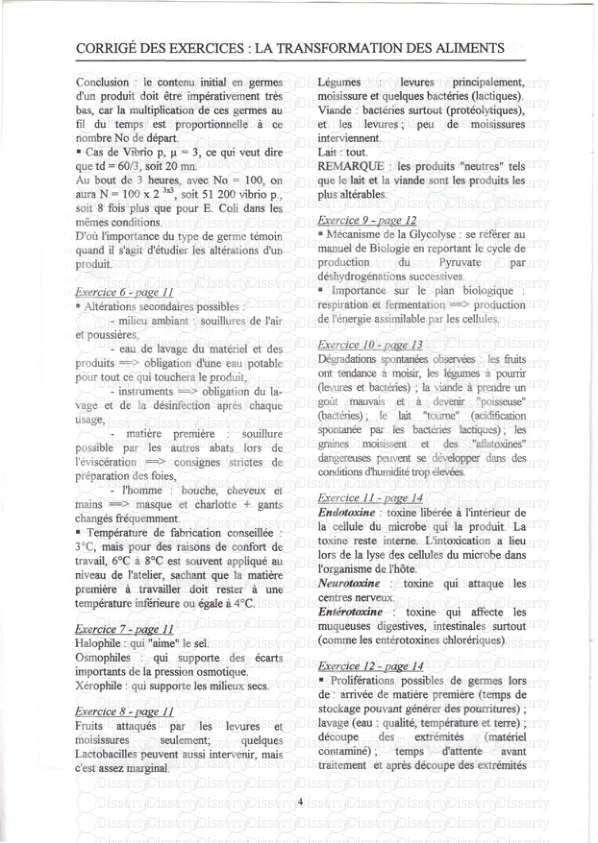
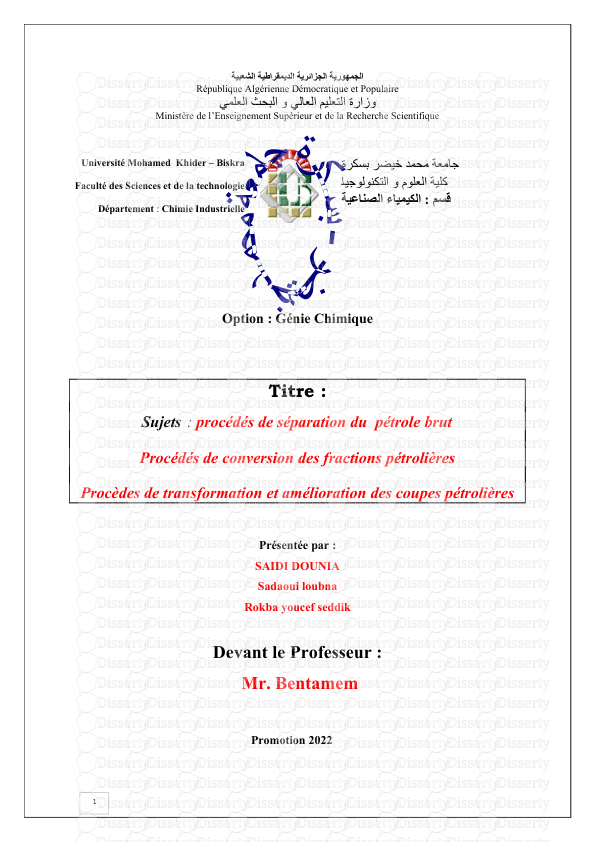
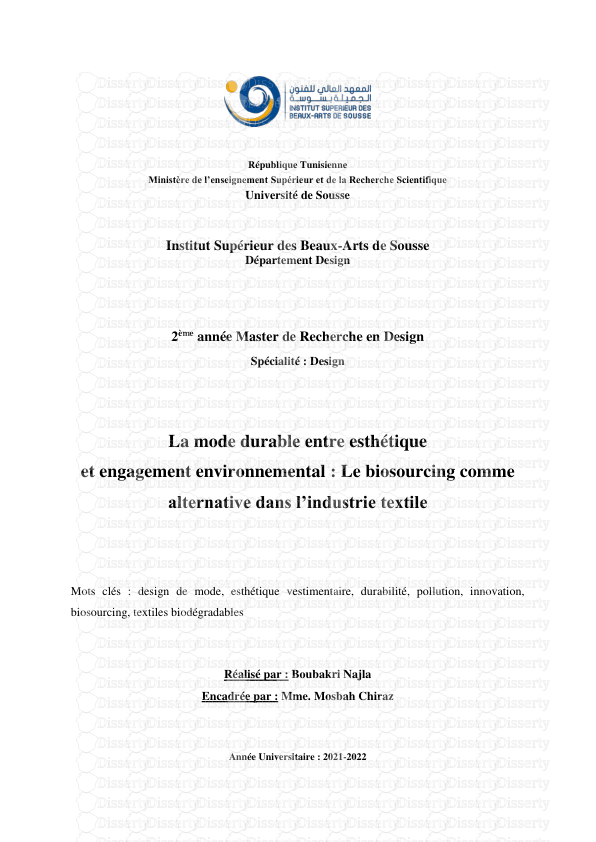
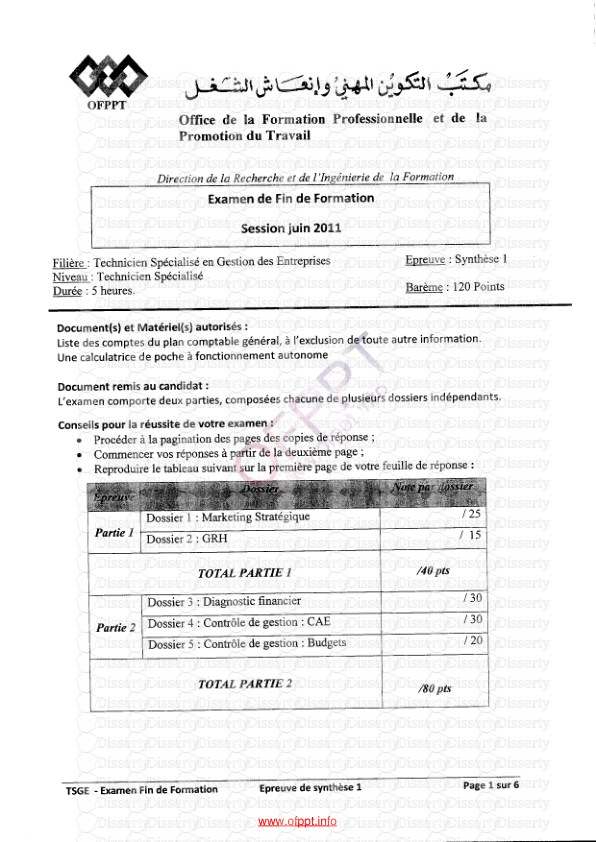
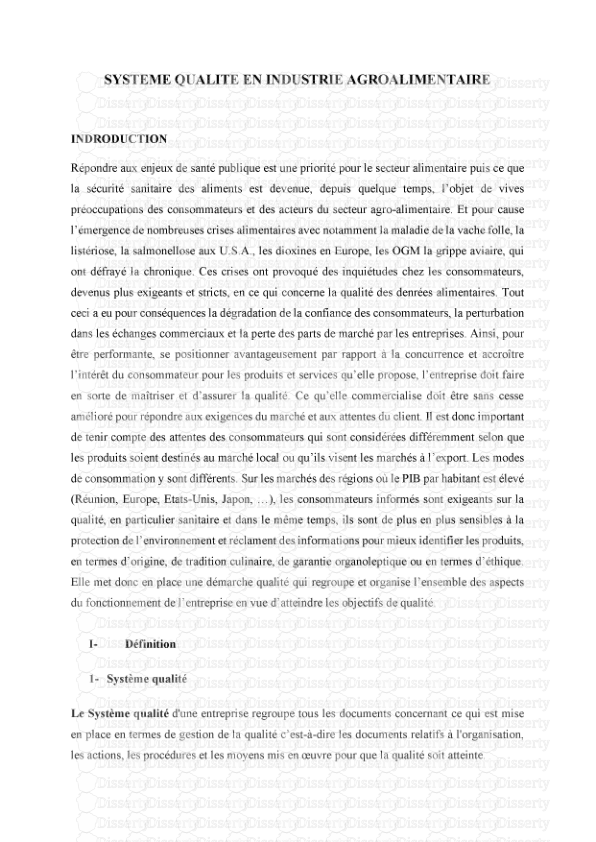
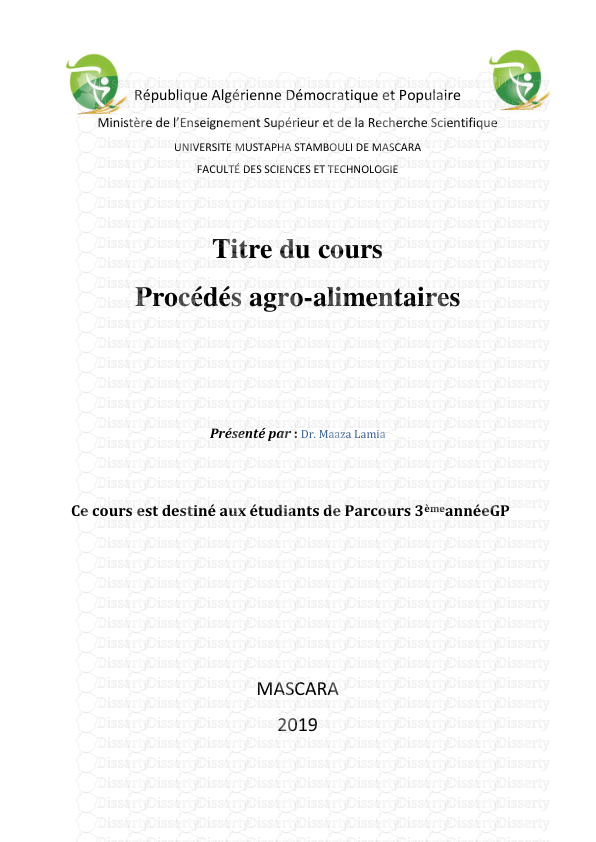
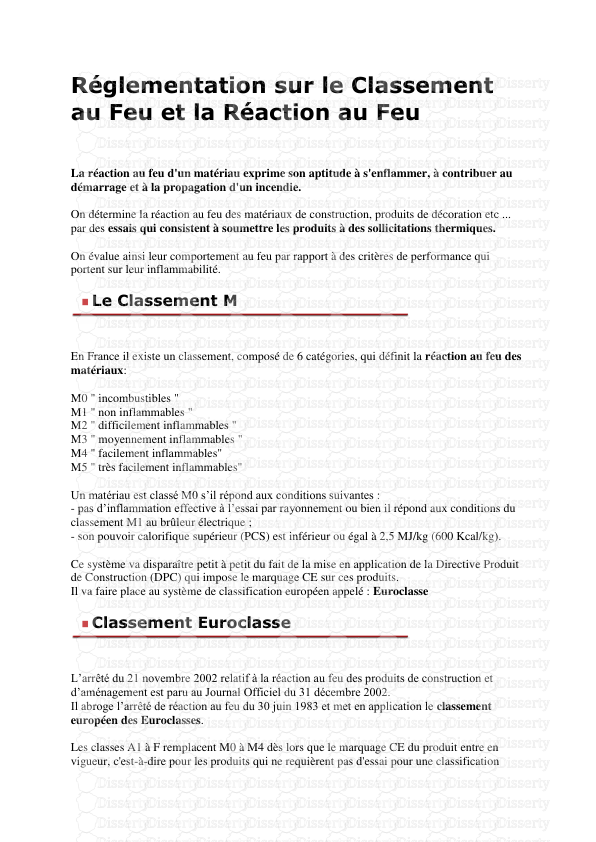
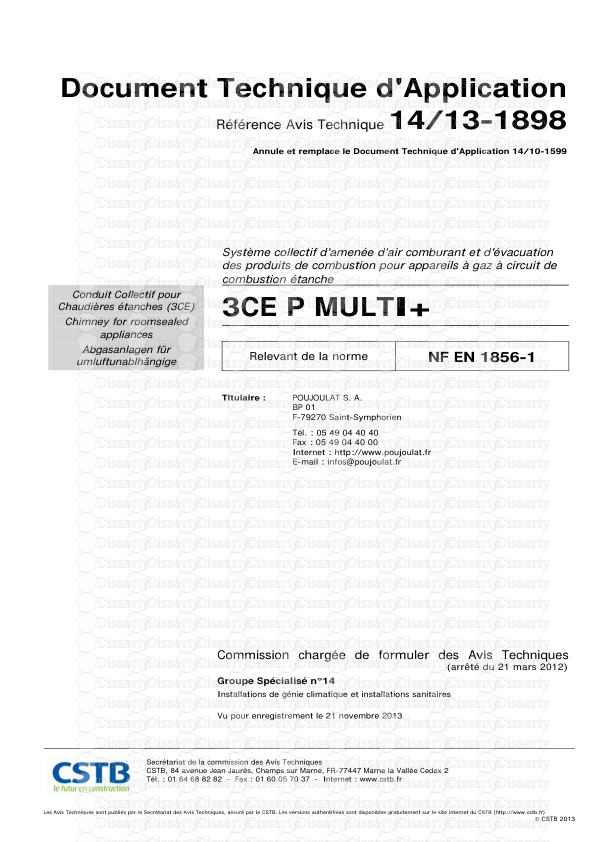
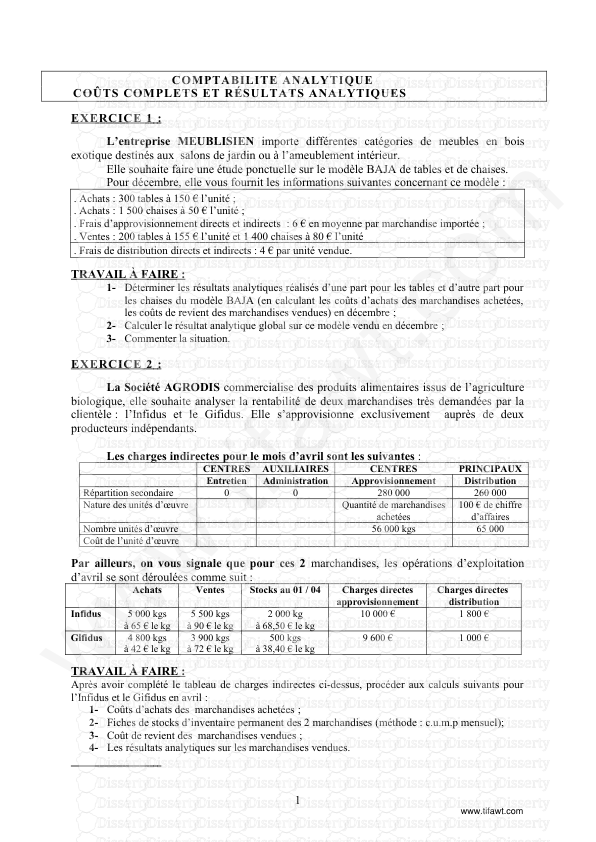
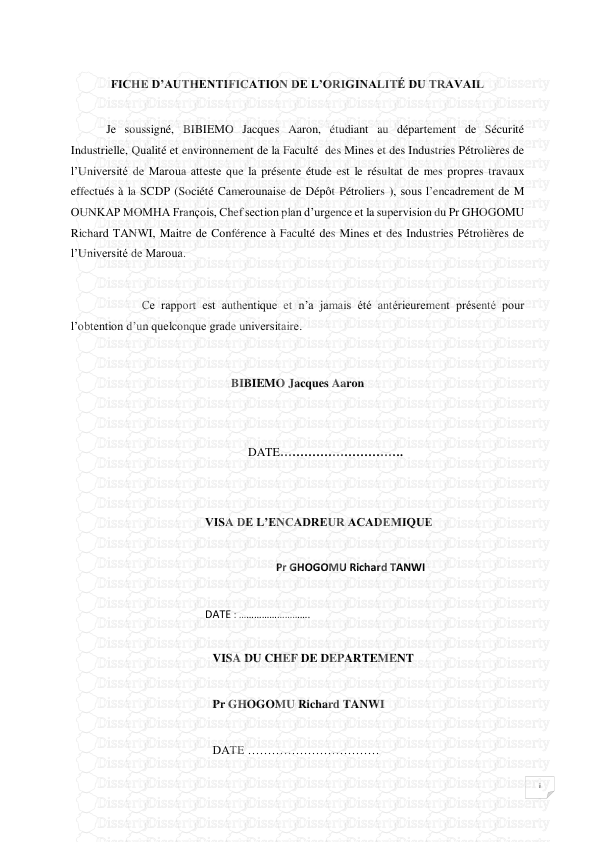
-
44
-
0
-
0
Licence et utilisation
Gratuit pour un usage personnel Attribution requise- Détails
- Publié le Mar 01, 2022
- Catégorie Industry / Industr...
- Langue French
- Taille du fichier 0.1347MB