MANAGEMENT 2 Théorie d’organisation et prise de décision Pr. Mohammed Rida ECH-
MANAGEMENT 2 Théorie d’organisation et prise de décision Pr. Mohammed Rida ECH-CHARRAT CI2 - 2021/2022 UNIVERSITÉ ABDELMALEK ESSAADI ÉCOLE NATIONALE DES SCIENCES APPLIQUÉES DE TÉTOUAN 2CHAPITRE 2: EVOLUTION CHAPITRE 2: EVOLUTION DE LA DE LA THÉORIE D’ORGANISATION THÉORIE D’ORGANISATION DIMENSIONS DE L’ÉVOLUTION POUR L’ENTREPRISE L’ÉVOLUTION POUR L’ENTREPRISE Rappel sur l’évolution industriel Rappel sur l’évolution du capitalisme Evolution de la théorie d’organisation* 3 EVOLUTION DE L’INDUSTRIE 4 EVOLUTION DE L’INDUSTRIE 5 Les Quatre Révolutions industrielles EVOLUTION DU CAPITALISME 6 Adam SMITHEVOLUTION DU CAPITALISME EVOLUTION DU CAPITALISME Fondé par A. Smith et ses disciples Jean-Baptiste Say, Thomas Robert Malthus, David Ricardo La richesse est identifiée au travail productif C’est un courant Libérale : liberté de travailler; propriété privé; concurrence →Marché régulateur et Etat gendarme Se base sur quatre concepts La main invisible →Intérêt individuel mène à l’intérêt générale Concept de Valeur travail Loi des débouchés (la demande était supérieur à l’offre)* La division de travail et spécialisation* COURANT CLASSIQUE (XVIIIème siècle) 7 EVOLUTION DU CAPITALISME Fondé par William Stanley Jevons, Carl Menger, Léon Walras Principes Concentration sur le consommateur (sélectif )* →Analyse microéconomique et utilisation des mathématiques. Valeur travail : Le prix dépend de l’utilité et la rareté (≠Valeur Travail de l’école Classique et marxiste) L’utilité marginale et l’équilibre générale Limites trop de constatation sur le consommateur indépendamment du marché globale →Production non fondée →krach boursier (1929) COURANT NÉOCLASSIQUE 8 EVOLUTION DU CAPITALISME Fondé par John Maynard Keynes Principes La demande est l’élément central de la croissance économique* Le marché ne conduit pas à l’optimum →L’intervention de l’état Concentration sur le marché dans sa globalité →Analyse macroéconomique. Aspect contesté État-providence n’encourage pas l’évolution économique COURANT KEYNÉSIEN 9 EVOLUTION DU CAPITALISME Développé principalement par Milton Friedman, Friedrich Hayek Contestation de l’ État-providence Limiter au maximum l’intervention de l’État La mondialisation (et globalisation) Libre circulation des Capitaux, Marchandises, services, etc. Libre choix du consommateur. Les défis à relever Inégalités sociales, Paradis fiscaux, Etc. COURANT CONTEMPORAIN « NÉOLIBÉRALISME » Milton Friedman 10 L’ÉVOLUTION DE LA THÉORIE D’ORGANISATION *(s’adapter à l’environnement) (s’adapter à l’environnement) 11 TAYLORISME Problématique Intégration et direction d’une main d’œuvre abondante et peu qualifiée (majoritairement rurale) afin d’augmenter son rendement en vue de l’augmentation de productivité des usines Frederick Winslow Taylor 1856-1915 12 TAYLORISME Philosophie et fondement de L’OST L’objectif de l’Homme est la prospérité matérielle L’objectif de l’entreprise est la productivité maximale La productivité maximal dépond du rendement des ouvriers L’Homme est paresseux →Principes de L’OST assure l’équilibre entre les intérêts des employés et ceux des employeurs Frederick Winslow Taylor 1856-1915 13 TAYLORISME Principes de l’OST Visant un Encadrement rigoureux et Rationalisant le comportement d’individu Remplacement rationnel de la gestion de type artisanat par une direction scientifique. Et ce en se basant sur plusieurs principes dont les essentiels : Hiérarchie (décomposition verticale) Organisation scientifique (décomposition horizontale) Sélection scientifique des ouvriers Rémunération liée au rendement Supervision Frederick Winslow Taylor 1856-1915 14 TAYLORISME Hiérarchie (Division verticale) Séparation entre les ouvriers, cadres supérieurs et direction. Les cadres supérieurs (contremaîtres) pensent et commandent; Les ouvriers (subalternes) obéissent et exécutent. Frederick Winslow Taylor 1856-1915 15 TAYLORISME Organisation scientifique (Division horizontale) Objet : Standardisation des opérations et spécialisation. En procédant ainsi : 1. Observation du qualifié au travail. 2. Décomposition du travail en opérations, tâches et gestes élémentaires. 3. Assemblage des tâches efficaces et élimination des gestes inutiles 4. Chronométrage et détermination de temps (standard). 5. Détermination de séquence optimale des opérations et des gestes. Le « One best way » 6. Affectation des tâches basé sur la spécialisations Frederick Winslow Taylor 1856-1915 16 TAYLORISME Sélection scientifique des ouvriers Visant la standardisation des opérations et la spécialisation des ouvriers. Une fonction de critères objectifs retenus pour chaque poste de travail. Perfectionnement des ouvriers par un entrainement adéquat pour exécuter des taches répétitives Frederick Winslow Taylor 1856-1915 17 TAYLORISME Rémunération liée au rendement Rémunération varie en fonction des pièces produites. Le salaire suit une fonction connue à l’avance par l’employé qui est de nature : S(n) = Po × (1+X%)× n X=0 si CR<CS Frederick Winslow Taylor 1856-1915 18 TAYLORISME Supervision Quatre contremaîtres pour assurer l’encadrement rigoureux : 1. Inspection 2. Réparation 3. Cadence 4. Chef d’équipe Frederick Winslow Taylor 1856-1915 19 TAYLORISME Frederick Winslow Taylor 1856-1915 Apports Augmentation de la productivité Absorption du chômage Hausses des salaires Baisse des prix Critiques Le « one best way » n’est pas toujours réel L’organisation ne tient pas seulement de la science, elle tient aussi de l’art. Conflits d’intérêt dans la supervision Déshumanisation du travail : En exécutant des tâches routinière, les ouvriers s’exposent à des maladies psychologique →Trun Over 20 FORDISME Henry Ford 1863 - 1947 Philosophie et principes Transformer un bien de luxe en un bien de consommation de masse « La voiture » C’est la manière de rationaliser le processus d’organisation de production en reprenant les principes de Taylor : les principes de l’OST Réduction des coûts logistiques internes Limiter le Turn Over →augmentation des salaires (5 $ a day) Imposer aux ouvriers le rythme de travail des machines 21 FORDISME Henry Ford 1863 - 1947 Apports et critiques Finalisation du travail à la chaine Production en grande série de produits standardisés réalisant l’économie d’échelle. Consommation de masse : La conversion des ouvriers en clients potentiels Monotonie de travail Incapacité à répondre à une diversification de la production 22 TOYOTISME L’idée a été inventé par un ingénieur japonais travaillant chez Toyota dans les années 50 pour une production personnalisée sans gaspillage Le Toyota Production System vise à éliminer Muda (les gaspillages) Muri (les excès) Mura (La variabilité) 23 TOYOTISME Les principaux gaspillages sont : Surproduction. Stocks inutiles. Transports inutiles. Défaut Mouvements inutiles. Délai. Surprocess. 24 TOYOTISMESURPRODUCTION SURPRODUCTIONProduire trop, trop tôt … Produire trop, trop tôt …Exemple: Stock important, mort … Exemple: Stock important, mort … SURPRODUCTION Produire trop, trop tôt … 25 TOYOTISME STOCK • Stocker plus qu’il n’est nécessaire • Exemple: palettes, produits finis, pièces détachées, consommables … 26 TOYOTISME TRANSPORT • Déplacer les stocks autour des lignes de production • Exemple: Livrer un produit stocké à deux endroits différents. 27 TOYOTISME DÉFAUT • Réparer ou recycler n’est pas de la valeur ajoutée • Exemple: retouches après contrôle, palette à refaire. 28 TOYOTISME MOUVEMENT • Est dû à une mauvaise organisation du travail ou des postes mêmes. Bouger n’est pas travailler! • Exemple: faire des allers retours pour chercher des outils , pour regarder quelque chose… 29 TOYOTISME Délai • Attendre que la machine termine / que les pièces arrivent … • Exemple: Attendre une information, du matériel … 30 TOYOTISME Surprocess • En faire plus que le travail demandé 31 TOYOTISME Les approches de TPS sont : Juste à temps Mise en place de systèmes visuel Amélioration Continue(Kaizen) Association des équipes à l’identification des pistes d’amélioration 32 TOYOTISME Juste à temps 33 Flux physiques Flux d’informations Flux physiques Flux d’informations Installer des flux en continu sur l’ensemble des processus Tirer les flux à partir de la demande réelle du client TOYOTISME Juste à temps 34 Organisation en flux poussés Les impératifs de production commandent toute la chaîne logistique. Les flux d’informations vont dans le même sens que les flux physiques, de l’amont vers l'aval. TOYOTISME Juste à temps 35 Organisation en flux tirés Le déclenchement du processus de production, et donc des flux physiques, est fait à partir de la demande. Les flux d’informations remontent de l’aval vers l’amont afin de donner l’ordre de fabrication. TOYOTISME Juste à temps 36 Plusieurs concepts font partie intégrante du JAT. Lorsque l’on implante le juste-à temps et que l’on veut relever les défis de cette méthode, il convient de recourir à différents concepts, tels que le takt time, la cellule en « U », l’« autonomation », le SMED*, KANBAN* TOYOTISME Mise en place de systèmes visuel 37 L’humain collecte l’information via :OUTILS D’ANIMATION ET DE PILOTAGE OUTILS D’ANIMATION ET DE PILOTAGEMANAGEMENT VISUEL MANAGEMENT VISUEL 83% la vue 11% l’ouïe 3.5% l’odorat 1.5% le touché 1% le goût TOYOTISME Mise en place de systèmes visuel 38 TOYOTISME Mise en place de systèmes visuel 39 Exemple : Poka yoke TOYOTISME 40 Exemple : PDCA Amélioration Continue(Kaizen) TOYOTISME Amélioration Continue(Kaizen) 41 Le Standard définie un CAP qu’il faut suivre, une Direction vers le meilleur. Le CAP peut être modifié en fonction des évolutions de la route. Sans standard, pas d’amélioration possible Le management doit porter la culture du standard Le processus conduit au résultat TOYOTISME Association des équipes à l’identification des pistes d’amélioration 42 • 80 % des MUDA peuvent et doivent être traités par les équipes qui les détectent. GÉNÉRALISATION DU TOYOTISME (LEAN MANAGEMENT) Les fondements du Lean Management Le Lean se définit comme une logique d’organisation et un système de management destinés à créer de la valeur pour les clients, à supprimer les tâches sans valeur ajoutée et les gaspillages afin de focaliser les ressources sur l’essentiel. Le Lean est né suite à une étude faite par le MIT sur la performance de l’industrie japonaise automobile comparée à celle des Etat-Unis et uploads/Industriel/ management-2-chapitre-2.pdf
Documents similaires
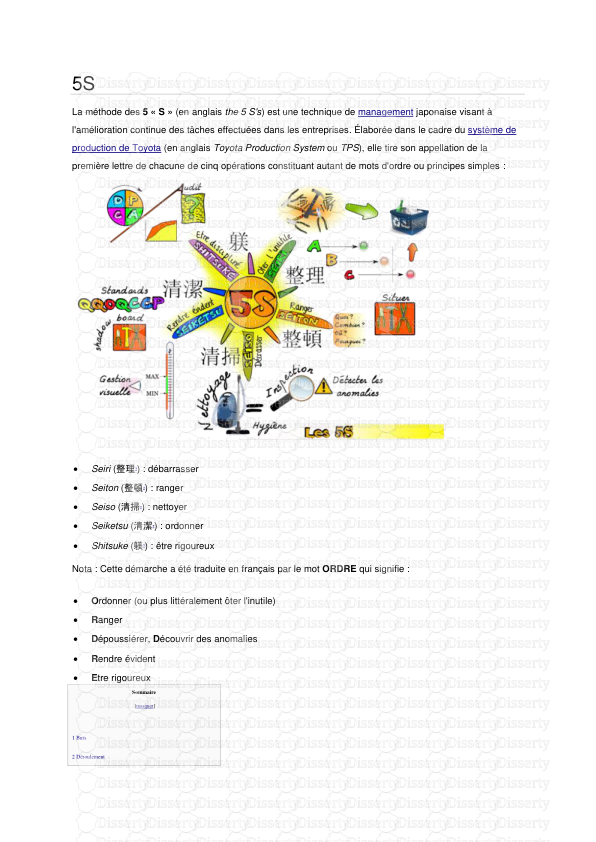
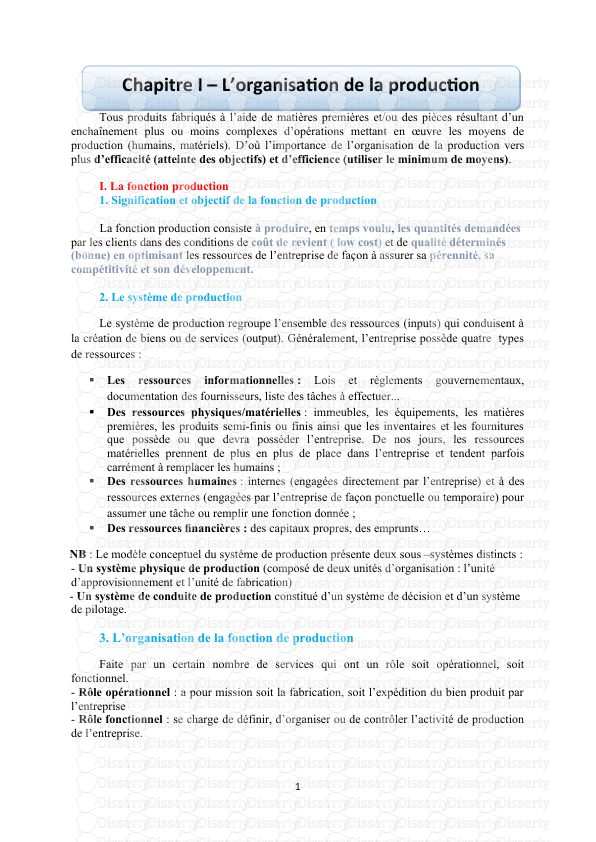
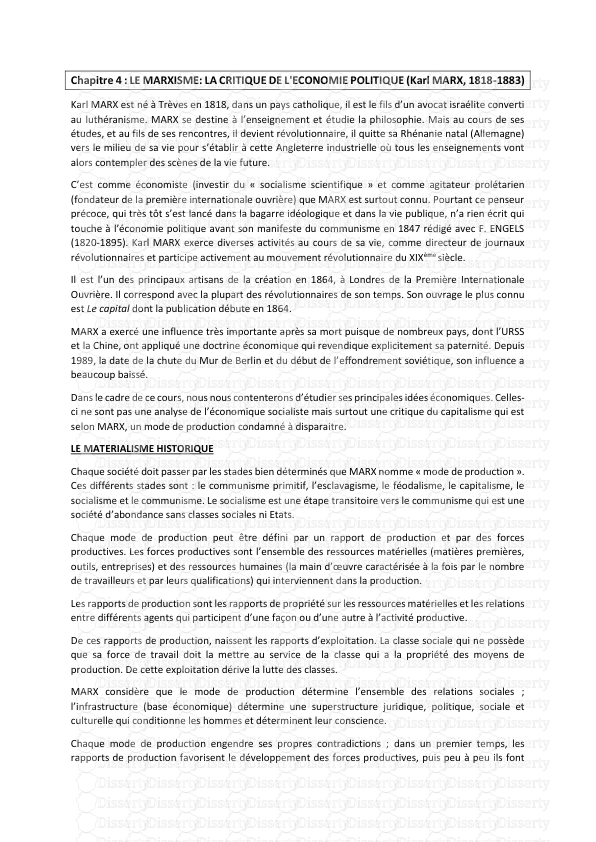


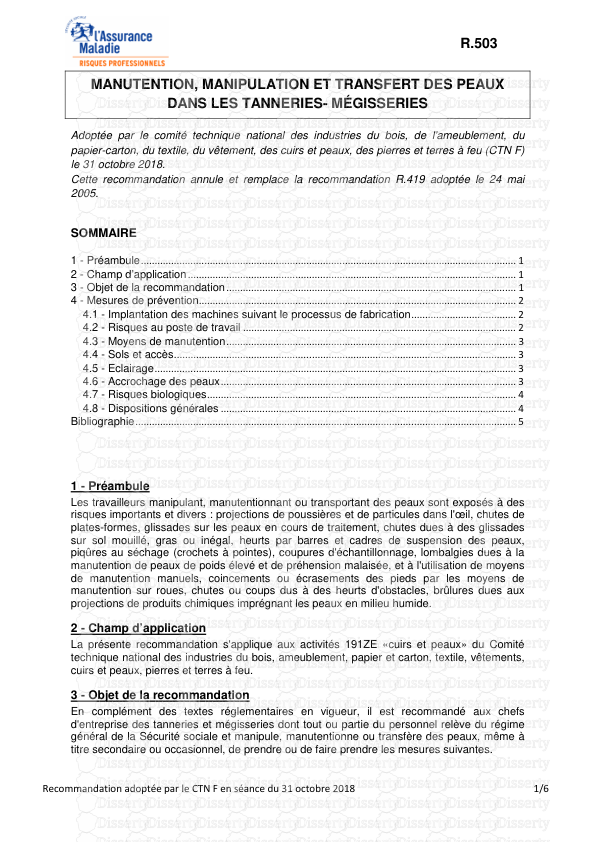
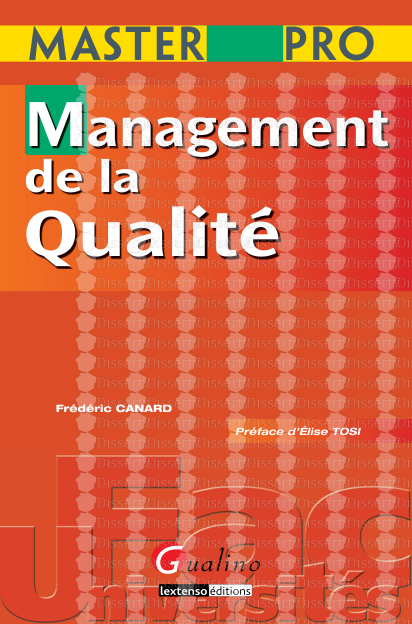
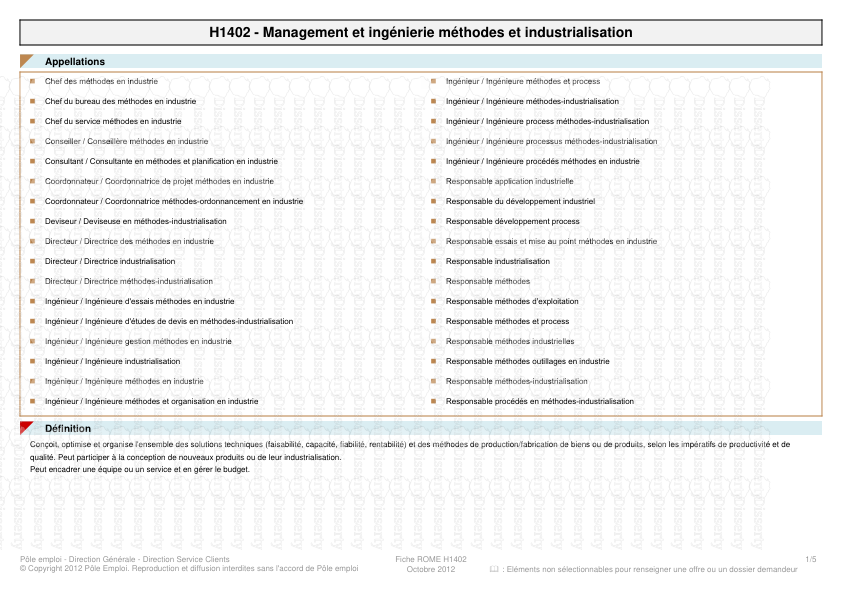
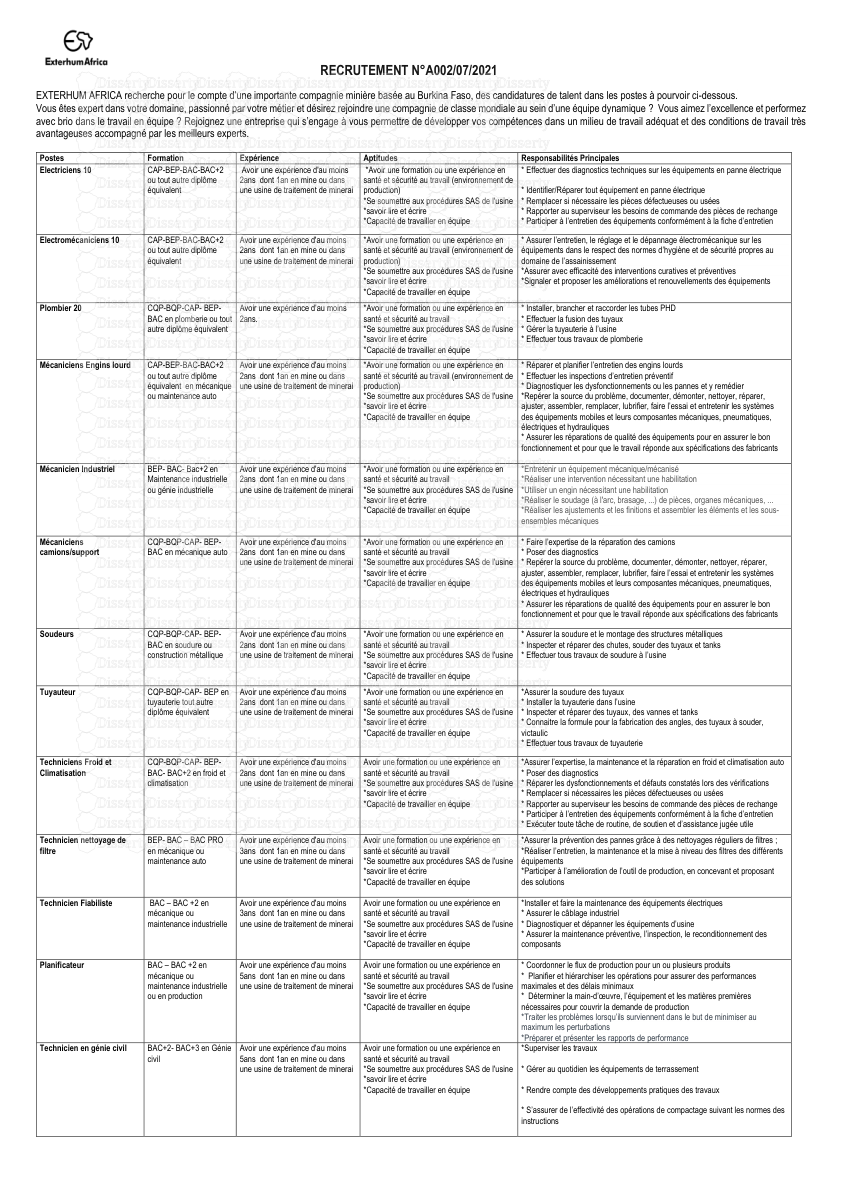
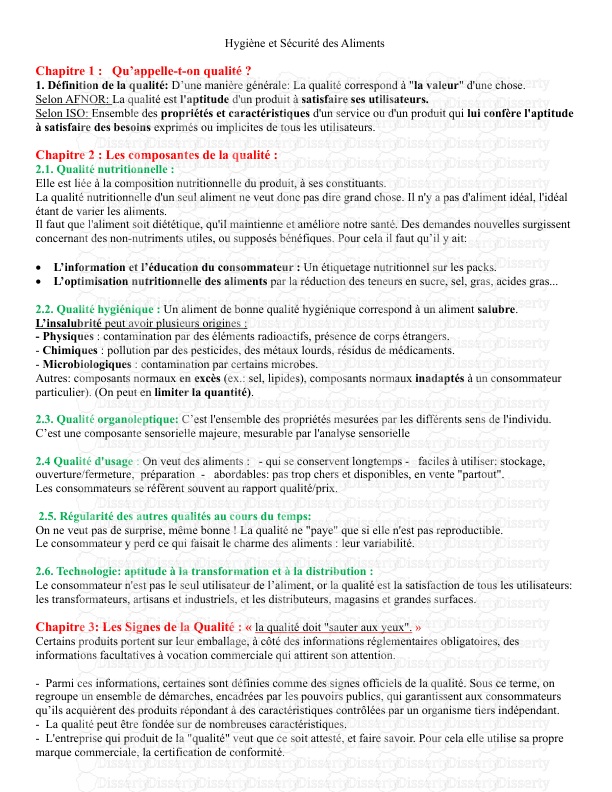
-
46
-
0
-
0
Licence et utilisation
Gratuit pour un usage personnel Attribution requise- Détails
- Publié le Dec 20, 2022
- Catégorie Industry / Industr...
- Langue French
- Taille du fichier 3.1692MB