1 École Supérieure de Technologie et d’Informatique ESTI 3ème Année Ingénieur G
1 École Supérieure de Technologie et d’Informatique ESTI 3ème Année Ingénieur GSIL Management de la Qualité Fehmi H’Mida Dr. Génie Industriel 81 L'amélioration continue est une démarche structurée, en groupe de travail, mettant en œuvre des méthodes et des outils, dans une recherche permanente d’une meilleure performance opérationnelle de l’entreprise. VI – Méthodes Qualité : Amélioration Continue 2 82 Dans l’analyse des dysfonctionnements, des non-conformités, des problèmes de qualité, il est important de distinguer les problèmes sporadiques / des problèmes chroniques, car souvent les problèmes sporadiques masquent un niveau de qualité déficient (Pr. JURAN). VI – Méthodes Qualité : Amélioration Continue Zone Application Amélioration Continue Zone Application Action Correc. Action Préven. 83 Fondateur : Pr. William Edwards DEMING (1900-1993), spécialiste en qualité. Aux années 50, il fait de nombreuses conférences au Japon. Il donne son nom au Prix DEMING de la JUSE, Prix Qualité au Japan. Le principe de base de l’amélioration continue est fondée sur le cycle PDCA (Deming). • Plan : Planifier • Do : Réaliser • Check : Vérifier • Act : Améliorer VI – Méthodes Qualité : Amélioration Continue 3 Les applications de l’amélioration continue sont très nombreuses. Nous les décomposons selon 4 domaines : Produits/Services – Qualité Flux - Délai Ressources - Efficacité Hommes - Implication Il existe pour chacun de ces domaines plusieurs outils standards répondant à une problématique identifiée (UN MUDA). 84 VI – Méthodes Qualité : Amélioration Continue Réduction des 8 MUDAS 85 Classification des outils : Délais – OUTILS flux • Value Stream Mapping (VSM) • Réorganisation des processus • Réimplantation d’atelier • Flux tirés (JIT, Kanban, …) • MPC : Management par les contraintes • Outils de la supply chain (ECR, …) Produits/Service – OUTILS qualité • Résolution de problèmes (MRP / 8D) • Poka-Yoke (Détrompeurs) • AMDEC (Produit / Service) • MSP (Maîtrise Statistique des Procédés) • QFD (Quality Fonction Deployement) • Analyse de la valeur (Ingénierie simultanée) • Design to manufacturing (Ingénierie simultanée) • Design to Cost (Ingénierie simultanée) Ressources – OUTILS efficacité • Résolution de problèmes (MRP / 8D) • TPM : TRS/TRG • SMED • AMDEC (Process / Moyen) • 5S • QRQC • Automaintenance Hommes – OUTILS équipe • Formation • Kaizen - Démarche Projet • Travail en équipe • Management visuel VI – Méthodes Qualité : Amélioration Continue 4 86 Réactivité : S’adapter aux variations de la demande Proactivité : Anticiper les besoins des marchés La roue motrice du progrès est la roue : o Hommes (KAIZEN) – OUTILS équipe Elle entraîne les 3 roues du progrès : o Délais – OUTILS flux o Produits/Services – OUTILS qualité o Ressources – OUTILS efficacité L’Amélioration Continue Délais - Outils Flux Ressources - Outils Efficacité Produit / Service - Outils Qualité Outils Équipe - Kaizen Clients - Marché Réactivité Proactivité La méthode kaizen est fondé par Masaaki IMAÏ (Japan), KAI = Changer ZEN = Bon Amélioration continue Masaaki IMAÏ a fondé un cabinet de management en 1962, et a publié en 1986 le livre "Kaizen : la clé du succès commercial japonais". La même année, il fonde le Kaizen Institute, dont la vocation est d'aider les entreprises occidentales à intégrer la notion, les concepts et les outils du Kaizen. Kaizen 87 5 La méthode : Le Kaizen repose sur de petites réalisations faites, au plus près du terrain. On ne modifie pas le produit réalisé. Kaizen s'intéresse au cycle de fabrication, et son terrain de prédilection est l'atelier. On n'a pas besoin de faire valider les solutions retenues par le client ni par le marketing, parce que le produit n'est pas modifié. Pour que cela fonctionne, il faut absolument que les suggestions des opérateurs soient très vite mises en application. Il faut : un circuit de décision ultra-court, avec des améliorations peu coûteuses, et du temps de travail disponible. Masaaki IMAÏ « Kaizen signifie amélioration continue impliquant tout le monde, sans grosse dépense d'argent » Kaizen 88 La Démarche Kaizen : 3 Etapes 1. La planification 2. Le pré - KAIZEN 3. L’amélioration Phase 1 – LA PLANIFICATION : A - Obtenir un mandat de la direction. B - Déterminer le site et les opérations à améliorer, préférer un site : qui fourmille d'activités présentant beaucoup de déplacement où l'espace est manquant qui a peu de productivité La Démarche Kaizen 89 6 C - Définir les buts visés (changements significatifs) par exemple : avoir 30% de plus de productivité sur une ligne de production éliminer le temps supplémentaire s'il est significatif récupérer au moins 30% d'espace D - Déterminer les membres de l'équipe kaizen : Possibilité de consultants externes pour les premiers kaizen Libérés totalement l’équipe de leur fonction durant la mission E - Déterminer les propres règles du jeu (quelques suggestions) : Rechercher des solutions demandant de très faibles investissements Chercher le consensus de plusieurs personnes Valider les solutions apportées avec les employés directement concernés On cherche comment faire plutôt que pourquoi c'est impossible La Démarche Kaizen 90 Phase 2 – LE PRE KAIZEN : Dans un kaïzen d'une durée de 10 jours, 2 journées doivent être consacrées à la sensibilisation des membres de l'équipe : A - l'explication aux membres des principes Kaizen (Démarche, étude de cas, outils) B - la revue sommaire du processus à étudier C - La visite des lieux, schéma en main Le reste du pré-kaïzen (3 jours ) doit être consacré à l'étude de la situation actuelle : D - détailler les étapes du processus E - définir les catégories (famille produits / processus) F - recueillir les données nécessaires à l’identification du problème. En conclusion le Pré-kaizen exige de CREUSER, CREUSER, et CREUSER encore pour bien connaître la situation avant de penser à l'améliorer La Démarche Kaizen 91 7 Phase 3 – L'AMELIORATION : A - Recherche et implantation des améliorations (Application des outils Qualité) B - Faire de petits essais en production C - Faire la présentation des résultats à la direction (avec l'équipe complète) La Démarche Kaizen 92 Kaizen et Amélioration continue Il y a deux approches pour résoudre un problème : - Celle impliquant l’innovation, les hautes technologies, - Celle faisant appel au bon sens et techniques très peu onéreux : Kaizen. Le Kaizen s’inscrit dans un cadre et une culture d’amélioration continue PDCA (Plan, Do, Check, Act). 93 8 94 L’Amélioration Continue Délais Outils Flux Value Stream Mapping (VSM) / Réorganisation des processus / Réimplantation d’atelier / Flux tirés (JIT, Kanban, …) / MPC : Management par les contraintes / Outils de la supply chain (ECR, …) Ressources Outils Efficacité MRP / 8D / TPM / SMED / AMDEC (Process / Moyen) / 5S / QRQC / Automaintenance Produit / Service Outils Qualité MRP / 8D / Poka-Yoke / AMDEC (Produit -Service) / MSP / QFD / Analyse de la valeur / Design to manufacturing / Design to Cost (Ingénierie simultanée), … Outils Équipe - Kaizen Clients - Marché Lean Management TPS : Toyota Production System Référentiel d’Excellence : Total Quality Management World Class Manufacturing Classe A 6 SIGMA Réactivité Proactivité L’excellence L’Amélioration Continue 95 LEAN, WCM, TPS, 6σ sont des théories, développées par des entreprises (Toyota, Motorola), des universités (MIT), des fondation (EFQM) ou des cabinets de conseil. L’objectif est de guider l’entreprise vers l’excellence en améliorant ses performances de façon importante. Ces projets d’excellence industrielle cherchent à structurer et employer les meilleurs outils dans un contexte donné. Ils guident le déploiement de l’amélioration continue sur toute l’entreprise. L’excellence L’Amélioration Continue Délais - Outils Flux Ressources - Outils Efficacité Produit / Service - Outils Qualité Outils Équipe - Kaizen Clients - Marché Lean TPS TQM WCM Classe A 6 SIGMA Réactivité Proactivité 9 96 Lean Manufacturing : J. J. Womack Womack & D. Jones & D. Jones T. Ohno T. Ohno S. Shingo S. Shingo Méthodes Méthodes japonaises japonaises TPS House TPS House, Cho, 70’s , Cho, 70’s S. Toyoda, 1890’s S. Toyoda, 1890’s K. Ishikawa, 60’s K. Ishikawa, 60’s « Lean Lean » Livre Livre Lean Lean Thinking Thinking 1996 1996 Lean 97 Lean Manufacturing : Lean est une synthèse développée à partir de l’expérience Toyota. Deux fondateurs du Toyota Production System (TPS) : Taiichi Ohno Shigeo Shingeo Lean 10 La question : Pour Quoi, le client, est-il prêt à payer ? La réponse : Pour satisfaire un besoin. Rien que ce besoin Notion « Valeur » Lean Coût Satisfaction du Besoin Valeur Les 2 vecteurs de la performance industrielle • La vitesse de génération de la valeur ajoutée : C'est le temps écoulé entre la sortie du PF et l'entrée des MP • Le débit de valeur ajoutée : C'est la quantité de VA générée par unité de temps Lean Notion « Valeur » Entreprise Fournisseurs Clients MP PF 99 11 Les 2 vecteurs de la performance industrielle Entreprise Fournisseurs Clients MP PF Lean Notion « Valeur » 100 L’enjeu du lean est d’éliminer, sinon réduire la non valeur ajoutée dans les processus Le uploads/Industriel/ management-de-la-qualite-ecole-superieure-de-technologie-et-d-x27-informatique-esti.pdf
Documents similaires
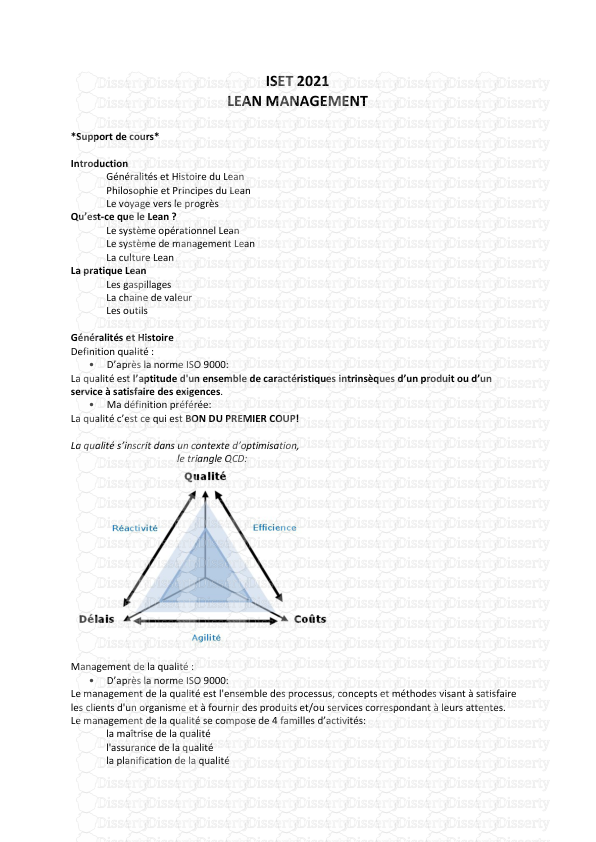
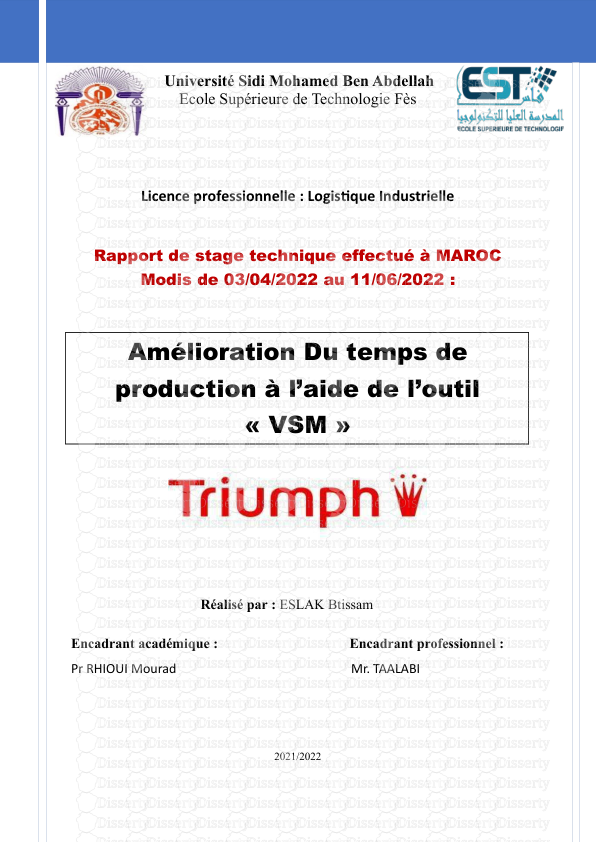
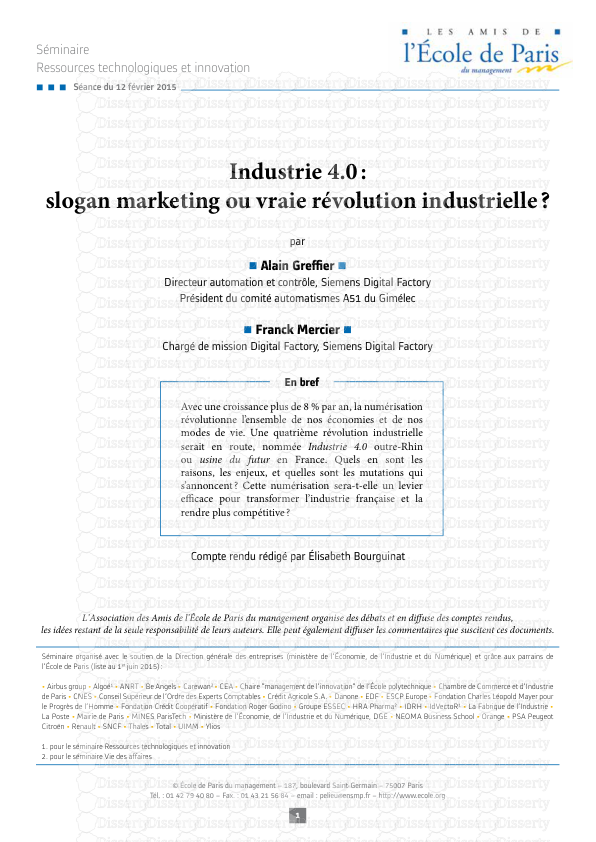
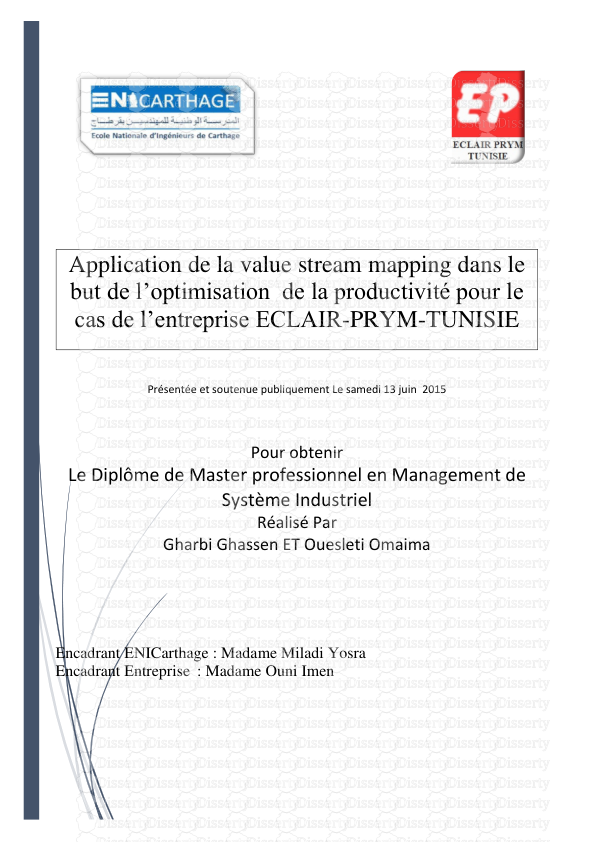
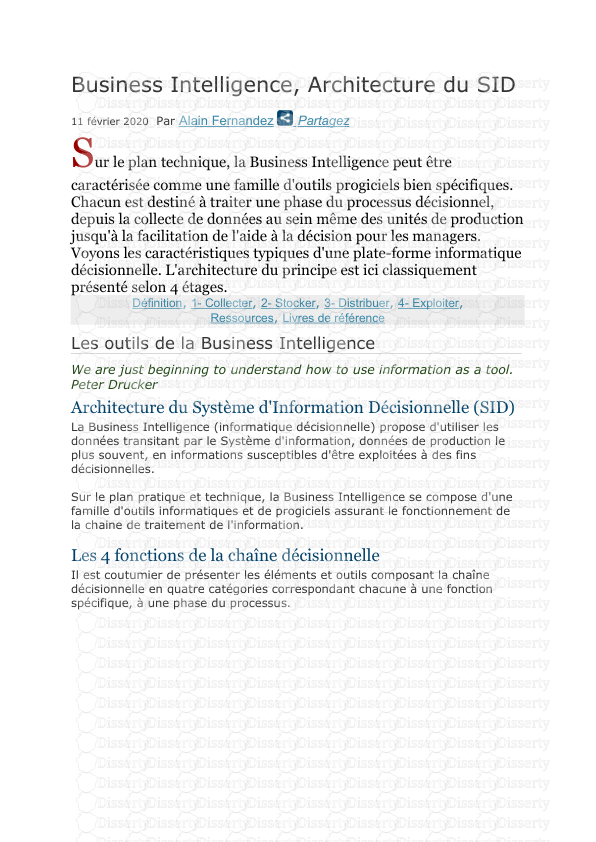
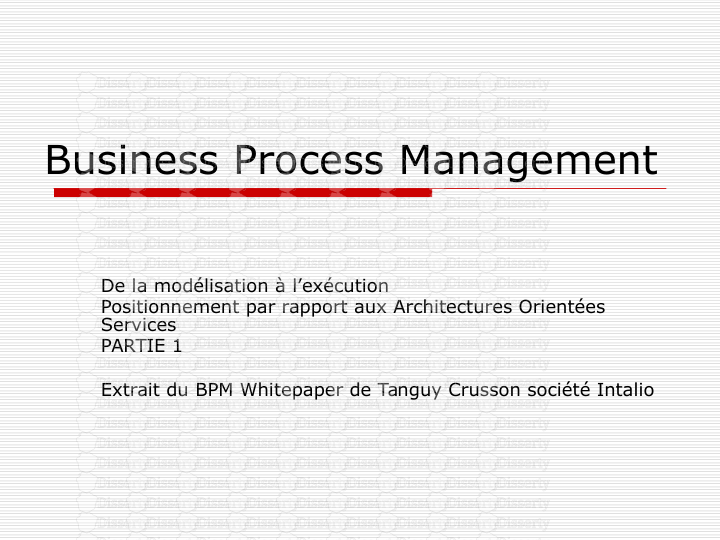
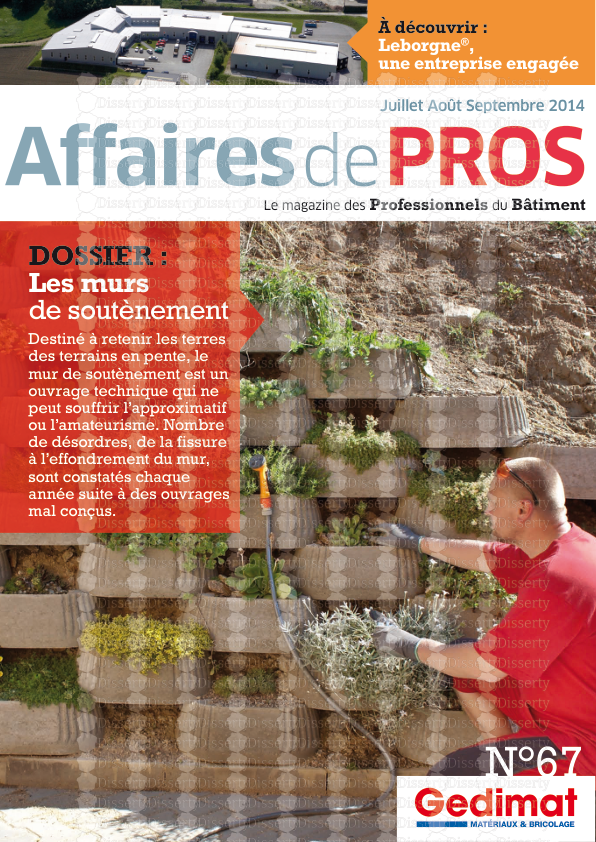
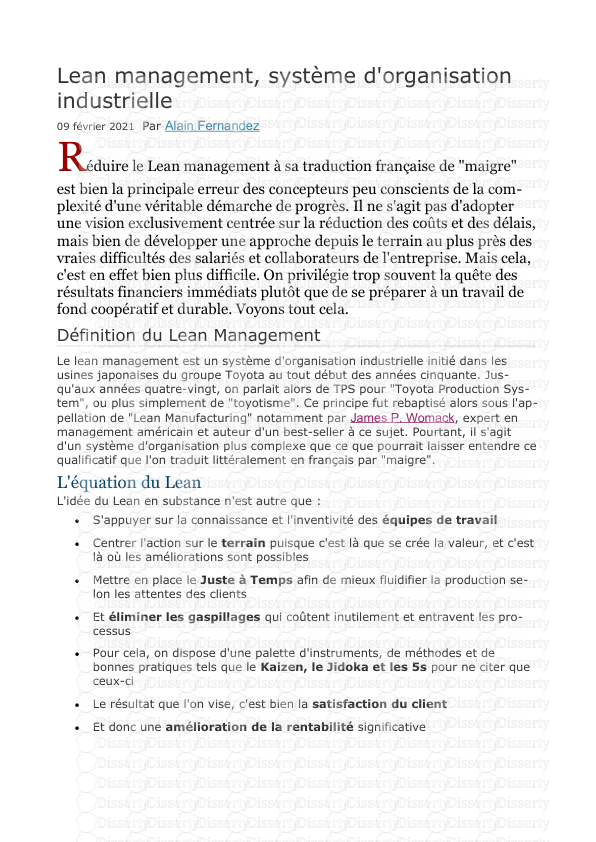
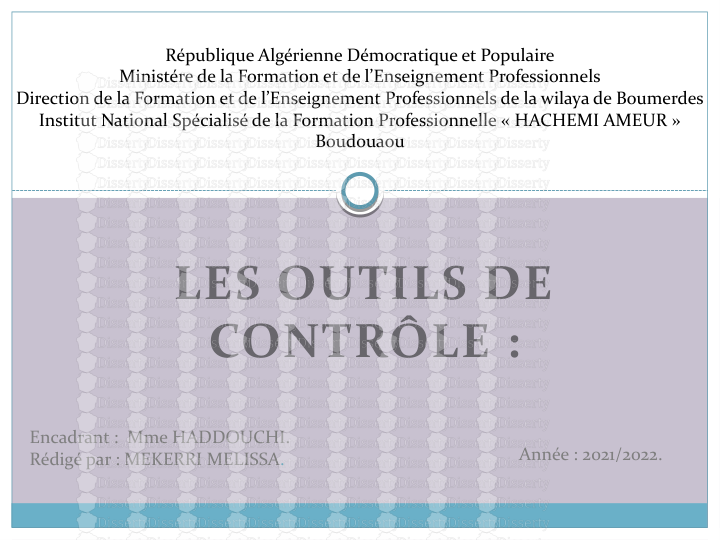
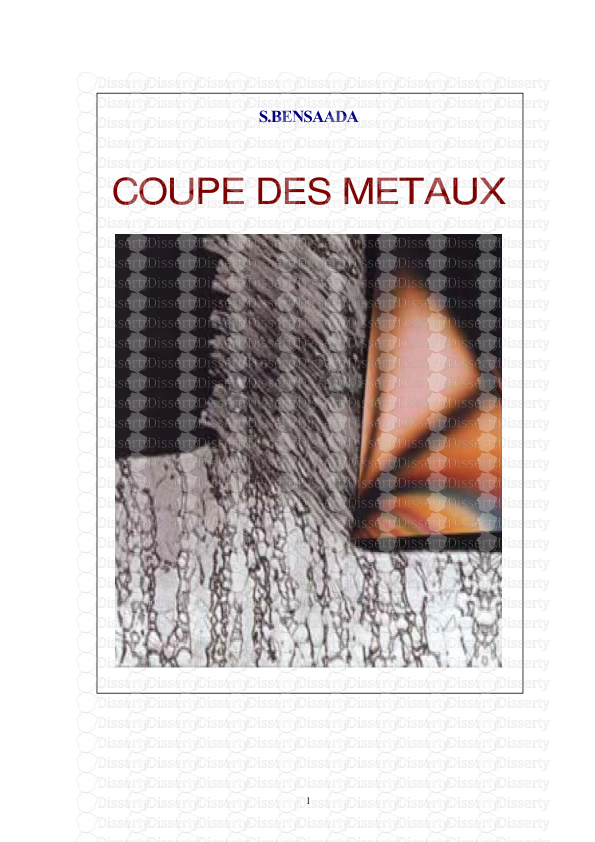
-
62
-
0
-
0
Licence et utilisation
Gratuit pour un usage personnel Attribution requise- Détails
- Publié le Sep 26, 2021
- Catégorie Industry / Industr...
- Langue French
- Taille du fichier 1.3238MB