Partie I Les modèles de base _________________ Retrouver ce titre sur Numilog.c
Partie I Les modèles de base _________________ Retrouver ce titre sur Numilog.com 1 Le système MRP Une méthode de gestion de production a vu le jour en 1965 aux États-Unis, sous l’impulsion de Joseph Orlicky. Cette méthode permettant d’anticiper les besoins du client et de les planifier dans le temps a été initialement appelée MRP (Material Requirement Planning ou calcul des besoins nets). Suite à l’évolution de la gestion industrielle (Qualité Totale, Juste-à-Temps), cette méthode est devenue plus globale et se nomme MRP2 (Manufacturing Resource Planning ou management des ressources de production1). 1.1 Architecture du système 1.1.1 Principe À partir des prévisions et des commandes clients, la méthode MRP2 gère la production du long terme au très court terme à partir de quatre niveaux de planification et d’un niveau d’exécution (figure 1.1). 1 Terme introduit par Michel Gavaud en 1981. Retrouver ce titre sur Numilog.com 4 Guide de la gestion industrielle Figure 1.1 Architecture du MRP2 À chaque niveau de planification, il s’agit de satisfaire la demande client (priorité du marché) en intégrant la disponibilité des ressources (adéquation charge/capacité). Pour cela, on vérifie la charge plus ou moins détaillée (quantité de travail homme et/ou machine à effectuer) par rapport à la capacité (disponibilité des ressources). Cette méthode répond aux questions suivantes : que fabriquer, combien, quand et avec quelles ressources disponibles ? 1.1.2 Les niveaux de planification • Plan stratégique Ce plan, sous la responsabilité de la direction, a pour objectif de définir les orientations stratégiques de l’entreprise en termes de parts de marché, de choix de site de production ou d’organisation générale, de politique sociale et de type de financement. Couramment, sur un horizon de 2 à 5 ans, ce plan est revu tous les 6 mois ou tous les ans. Ce niveau de planification : – donne les objectifs généraux ou stratégiques de l’entreprise (vision ou politique d’entreprise, choix des marchés, achat d’usines…), Plan industriel et commercial (PIC) Charges globales (sites, personnel…) Programme directeur de production (PDP) Charges globales (postes goulets) Calcul des besoins Charges détaillées Ordonnancement d’atelier Gestion de la capacité Plan stratégique Niveaux de planification Long terme Court terme PLANIFICATION EXECUTION Retrouver ce titre sur Numilog.com Le système MRP 5 – est basé sur des études de marché à long terme (enquêtes d’opinion…), – prend en compte les contraintes et les objectifs des fonctions marketing, financière et de la production, – intègre l’évolution des technologies (robotique, automatisme, informatique, centre d’usinage à commande numérique…). • Plan industriel et commercial À partir du plan stratégique, on élabore les plans industriels et commerciaux (PIC) par famille2 de produits. À ce niveau de détail de la planification, ces plans fixent : – les volumes de production par période, – les niveaux de stock en début et en fin de période, – les ressources humaines et matérielles nécessaires, – les besoins financiers. Ces plans doivent satisfaire les objectifs fixés par le plan stratégique. Ils sont le résultat d’un consensus entre les directions marketing, financière et production. Couramment, sur un horizon de 6 à 18 mois, ils sont révisés tous les mois. Pour vérifier la faisabilité du PIC, on calcule les charges globales à l’aide de ratios de production (ratio = volume/période). • Programme directeur de production Appelés PDP, ces plans essentiels au niveau de la méthode MRP2 sont élaborés à partir des plans industriels et commerciaux (figure 1.2). À partir des besoins indépendants3 (prévisions et commandes fermes), ils définissent précisément, par produit, la quantité par période en tenant compte des options et variantes. L’horizon du PDP se définit au minimum par le cumul des délais les plus longs d’approvisionnement, de fabrication et d’assemblage pour les composants et le produit fini. 2 D’après l’APICS, une famille est un groupe de produits dont les similitudes de conception et de production facilitent la planification globale, le suivi de leur performance de ventes et occasion- nellement l’agrégation de leur coût. 3 Joseph Orlicky distingue deux types de besoins : les besoins indépendants, ceux qui relèvent des prévisions ou des commandes clients de produits finis ou de pièces détachées et les besoins dépen- dants, ceux qui sont issus du calcul des besoins. Retrouver ce titre sur Numilog.com 6 Guide de la gestion industrielle Il peut varier de trois mois à un an selon les types de produits. Il est revu couramment chaque semaine. Pour le PDP, on calcule les charges globales au niveau des ressources critiques, afin de vérifier la faisabilité. Figure 1.2 Exemple de PDP déduit d’un PIC • Calcul des besoins À partir des nomenclatures et des PDP de chaque produit, on calcule les besoins dépendants de chaque élément, sous-ensemble, matière première à acheter ou à fabriquer. L’horizon de planification tient compte des délais d’achat et de fabrication des éléments à fabriquer. Couramment, sur un horizon de un à trois mois, ils sont révisés toutes les semaines, parfois tous les jours. Au niveau du calcul des besoins, on évalue les charges détaillées générées par les ordres de fabrication, qu’ils soient planifiés ou lancés. • Pilotage d’atelier Le but du pilotage d’atelier est de lancer les ordres d’achat ou de fabrication au niveau de l’atelier. L’horizon de planification est de l’ordre de la journée à la semaine, la révision est journalière, parfois horaire. Les ordres de fabrication sont lancés et suivis à l’atelier selon les priorités fixées par le gestionnaire d’atelier. Au niveau du pilotage d’atelier, on contrôle les ordres réalisés par rapport aux ordres planifiés. C’est le tableau de bord du pilotage d’atelier (cf. § 1.6.5). PDP des produits de la famille X Référence XA XB XC XD Somme S1 70 250 200 250 770 S2 70 50 325 445 S3 20 50 350 205 625 S4 70 150 500 400 1 120 Somme 230 500 1 050 1 180 2 960 Famille X 0 2000 4000 6000 8000 Janvier Février Mars Avril Mai Juin Juillet Août Septembre Octobre Novembre Décembre 3 940 3 015 2 960 3 225 4 378 4 789 5 670 5 067 6 789 5 890 4 987 4 230 PDP des produits de la famille X Référence XA XB XC XD Somme S1 70 250 200 250 770 S2 70 50 325 445 S3 20 50 350 205 625 S4 70 150 500 400 1 120 Somme 230 500 1 050 1 180 2 960 Référence XA XB XC XD Somme S1 70 250 200 250 770 S2 70 50 325 445 S3 20 50 350 205 625 S4 70 150 500 400 1 120 Somme 230 500 1 050 1 180 2 960 Famille X 0 2000 4000 6000 8000 Janvier Février Mars Avril Mai Juin Juillet Août Septembre Octobre Novembre Décembre 3 940 3 015 2 960 3 225 4 378 4 789 5 670 5 067 6 789 5 890 4 987 4 230 Retrouver ce titre sur Numilog.com Le système MRP 7 1.1.3 Base de données Tout système de gestion de production fonctionne à partir d’une base de données structurée et suffisante. • Données statiques (données techniques) – Fichier articles : il décrit les produits pris en compte par le système (produits finis, sous-ensembles, pièces achetées ou fabriquées et matières premières). On y trouve notamment l’identification de l’article (code, description), les données de gestion (taille de lot, stock de sécurité, délai d’obtention, lieu de stockage), les données économiques (coûts standards). – Fichier nomenclatures : il précise les composants (sous-ensembles, pièces et matières premières) entrant dans la composition de l’article parent (composé). On utilise des liens entre les niveaux de nomenclatures qui précisent la quantité de composant nécessaire (coefficient d’emploi4). Une nomenclature peut se présenter sous différentes formes (arborescente, modulaire, fantôme, matricielle, valorisée, décalée…). – Fichier centre de charges : c’est une unité de fabrication constituée d’une ou plusieurs personnes et/ou machines. On y trouve notamment l’identification du centre (code, description, emplacement), les données de capacité (nombre de personnes, de machines, capacité disponible, les taux d’efficacité et d’utilisation), les données économiques (taux de l’heure de préparation, de fabrication…), le poste éventuel de remplacement… – Fichier gammes : il décrit les opérations à réaliser et leur séquencement pour transformer une pièce (article) de son état initial à son état final. La gamme précise des données générales (désignation, code, date de création et de mise à jour, commentaires, conditions d’emploi, outillages…), les centres de charge utilisés, les temps standards (préparation, exécution, technologique, transfert, attente…). Il en existe différents types (usinage, assemblage, remplacement, contrôle, transfert). Les gammes sont généra- lement élaborées par le bureau des méthodes… – Fichier fournisseurs et sous-traitants : il précise l’identification (code, nom, adresse, coordonnées téléphoniques) et les conditions générales (délai d’obtention, prix d’achat…). 4 Nommé coefficient d’emploi par l’APICS. Certains auteurs utilisent également le terme de coeffi- cient de lien ou coefficient de nomenclature. Retrouver ce titre sur Numilog.com 8 Guide de la gestion industrielle – Fichier clients : il précise l’identification (code, nom, adresse, coordonnées téléphoniques) et les conditions générales (remise, qualité…). • Données dynamiques (données de flux) – Fichier prévisions : il estime par article la demande future. Les prévisions sont uploads/Industriel/ partie-i-les-modeles-de-base.pdf
Documents similaires
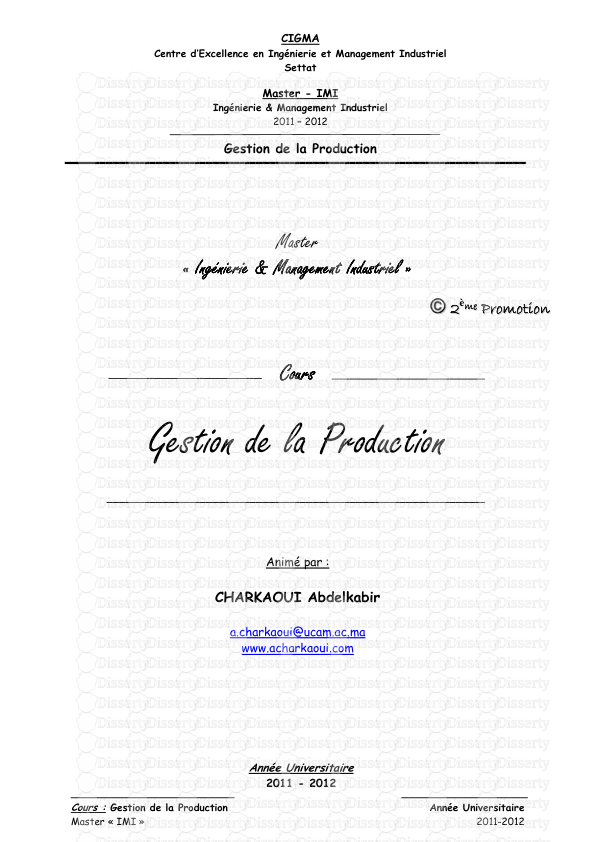
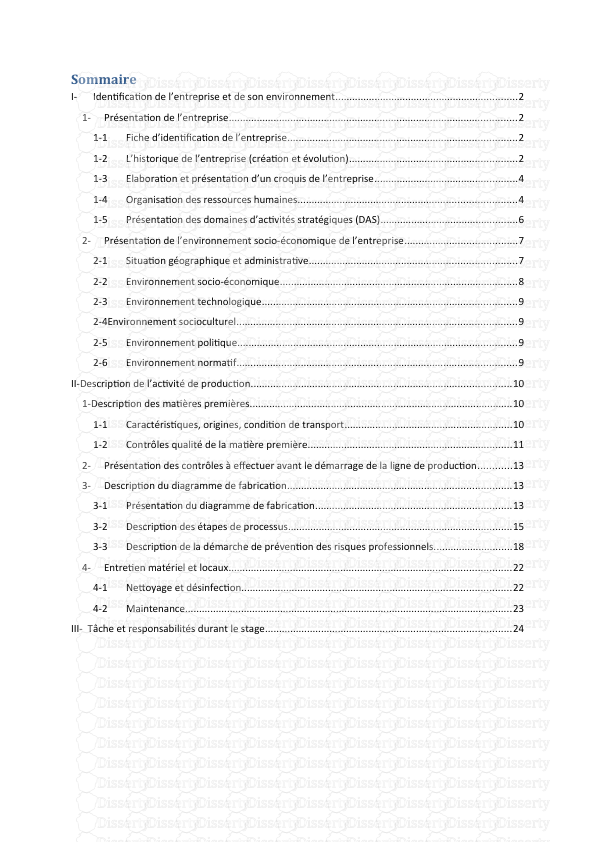

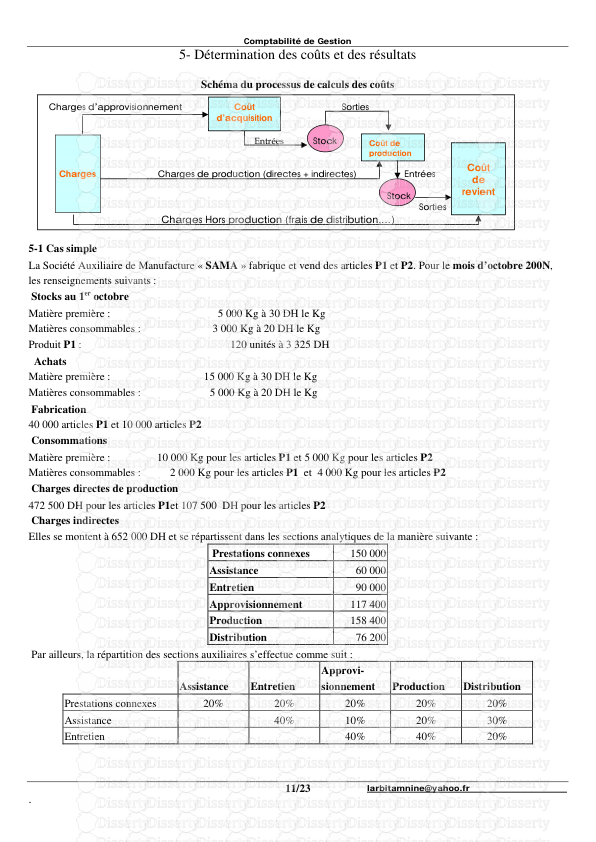
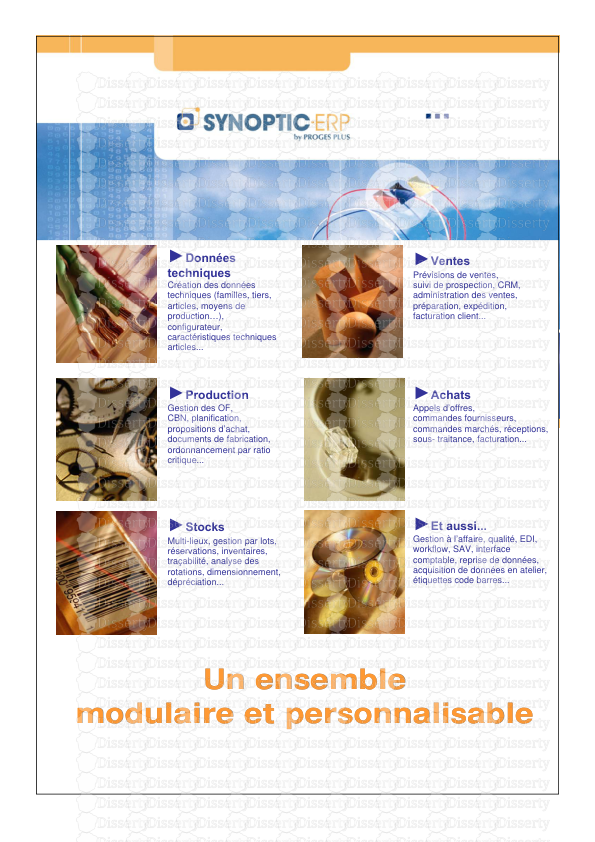
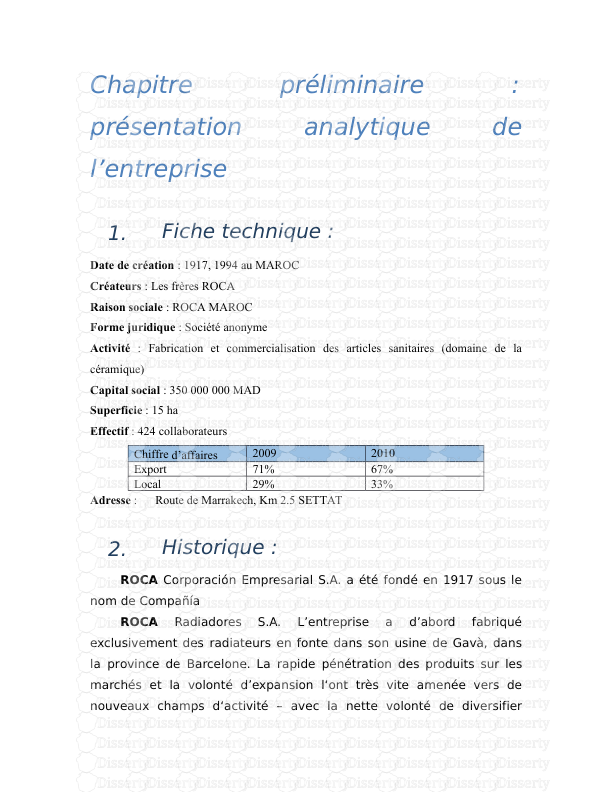
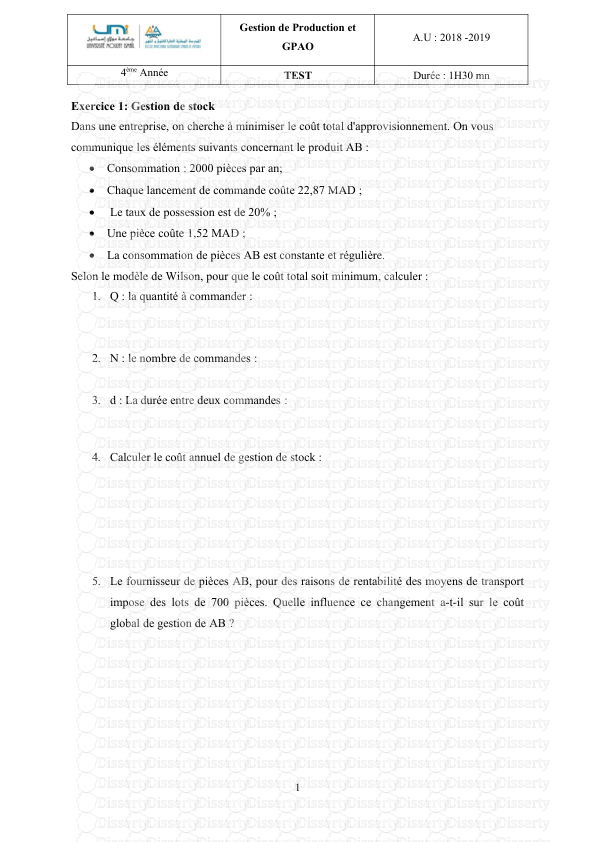
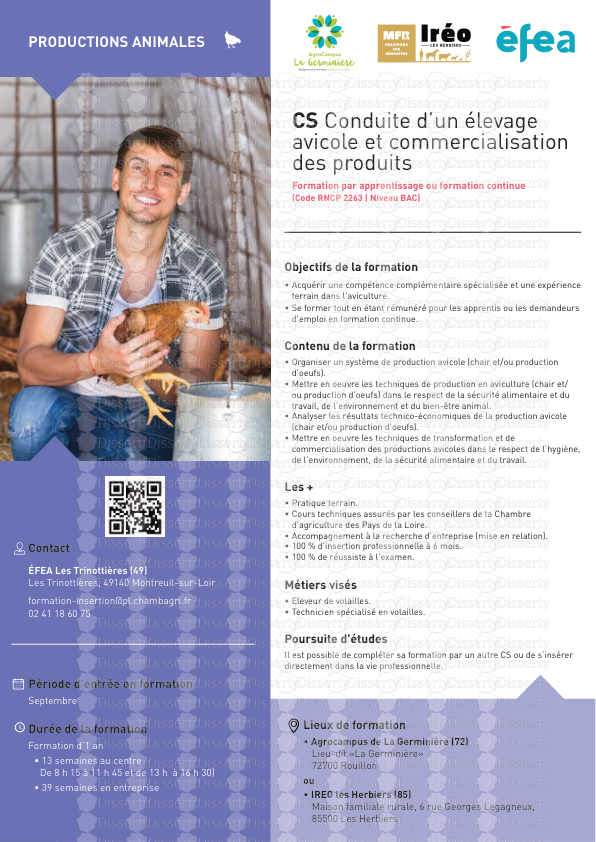
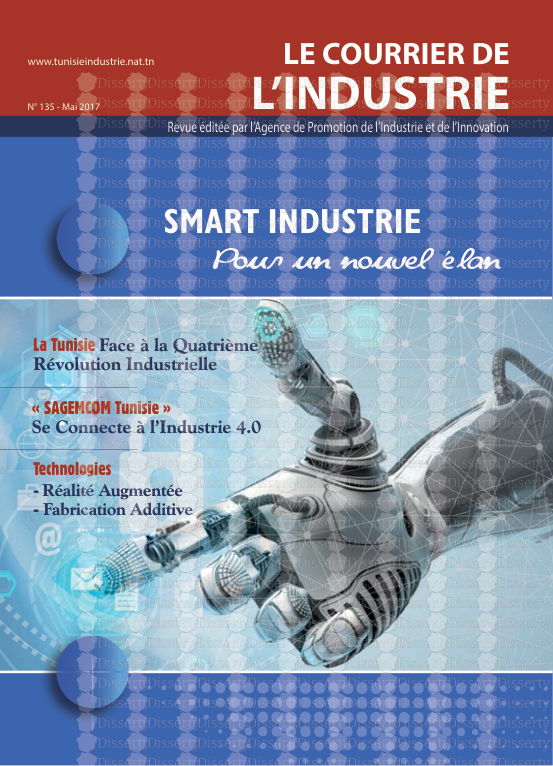
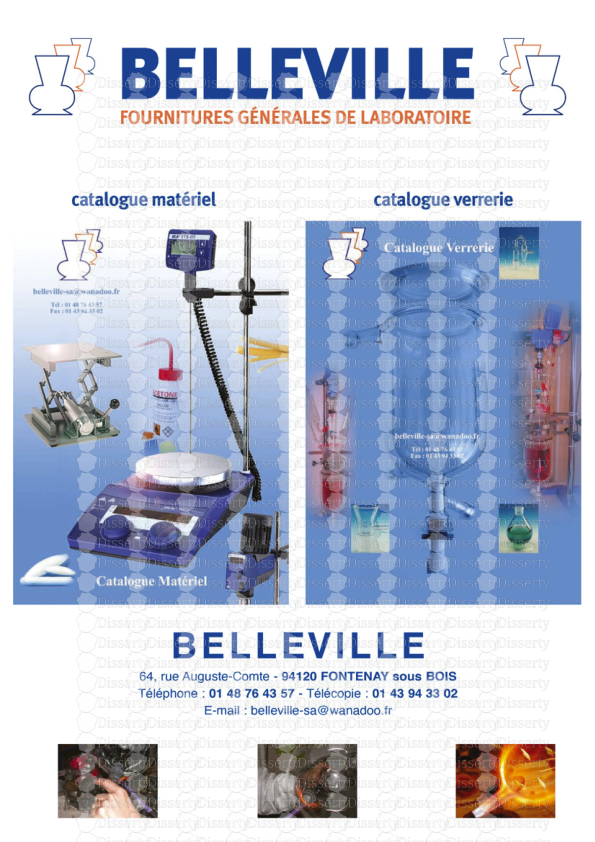
-
58
-
0
-
0
Licence et utilisation
Gratuit pour un usage personnel Attribution requise- Détails
- Publié le Mar 21, 2022
- Catégorie Industry / Industr...
- Langue French
- Taille du fichier 0.1645MB