PRATIQUE DU MÉTHODE VSM DANS LE MILIEU INDUSTRIEL Introduction Le Lean Manufact
PRATIQUE DU MÉTHODE VSM DANS LE MILIEU INDUSTRIEL Introduction Le Lean Manufacturing est une méthode d’organisation d’optimisation de la performance industrielle qui vise à mieux respecter les exigences du client en matière de coût-qualité-délai. Il s’agit d’analyser de manière détaillée les différentes étapes qui constituent le processus de production puis, à chasser tous les gaspillages identifiés tout au long du processus de fabrication permettant alors d’être plus efficace et plus rentable. Peut de gaspillage Processus amélioré Présentation du lean manufacturing le Lean Manufacturing est une méthode qui agit sur les gaspillages afin de réduire les coûts de production. La philosophie de Toyota repose sur l’amélioration le flux de valeur, non pas en augmentant la capacité de production, mais en diminuant les gaspillages. T. OHNO identifia huit sources de gaspillages: • Surproduction • Surstockage ou Stocks inutiles • Transports et Déplacements Inutiles • Traitements Inutiles ou Surprocessing • Mouvements Inutiles • Erreurs, Défauts et Rebuts • Temps d’attente La méthode Lean Manufacturing repose sur 2 principes : • Le Just in Time : fabriquer ce qui est nécessaire, lorsque cela est nécessaire et en quantité voulue, le tout dans des délais les plus courts possibles (éliminer les stocks) • Le Jidoka : remédier aux dysfonctionnements le plus tôt possible pour éviter que les problèmes ne perdurent et se propagent (éliminer la récurrence ). Problématique le manager ne sait pas s’il est bien organisé, il ne visualise plus ses flux et ne sait pas si ses stocks sont utiles à la production. L’entreprise ne maîtrise plus son Lead time (temps d’écoulement ou de satisfaction client Pour faire de l’amélioration continue conformément au processus Lean Manufacturing, il est nécessaire de cibler toutes les opérations inutiles et sans valeur ajoutée et tenter de les réduire ou de les supprimer Value stream mapping Le flux de production est très souvent associé uniquement au mouvement des matières premières et des produits finis. Mais il y a un autre flux tout aussi important, celui de l’information. Il permet à chaque unité de production de savoir ce qu’elle va faire ou fabriquer dans les minutes ou les heures qui viennent. • La Value Stream Mapping est un modèle de représentation plus complète car elle intègre ces deux catégories de flux : matières et information. Elle a été francisée en Cartographie de la Chaîne de Valeur. • La chaîne de valeur est la décomposition de l’activité de l’entreprise en une séquence d’opérations élémentaires. • la construction de la carte VSM va dans le sens inverse de la chaîne de création de valeur. Présentation d’entreprise MED • L’entreprise MED est un façonnier pharmaceutique qui produit des médicaments de diverses formes (injectables, comprimés, gélules…). Le choix de la famille de produits étudiée a été porté sur la production de trois comprimés (médicaments A, F et C). • Le macro-processus de production est le suivant : Fournisseurs Granulation Compression Enrobage Conditionnement Client Exigences du Client • L‘unique client, un laboratoire pharmaceutique du nom de ZAC, demande en moyenne par mois : • 840 000 comprimés de A (soit 28 000 boîtes de 30 comprimés, 1 400 cartons de 20 boîtes, 25 palettes de 56 cartons) • 720 000 comprimés de F (soit 36 000 boîtes de 20 comprimés, 1 200 cartons de 30 boîtes, 40 palettes de 30 cartons) • 1 200 000 comprimés de C (soit 12 000 boîtes de 100 comprimés, 500 cartons de 24 boîtes, 10 palettes de 50 cartons) Le poids de chaque comprimé est de 500 mg. Le client demande des lots de fabrication de 60 kg, ce qui représente 120 000 comprimés par lot. Les livraisons au client sont hebdomadaires, et se font par camion. Fournisseurs • Toutes les matières premières nécessaires à la fabrication des comprimés (granulation, compression, enrobage) proviennent d’un même fournisseur, la société PowderPro. Elle livre l’entreprise MED trois fois par semaine, par camion. Un second fournisseur, l’imprimerie Printinstinct livre par camion les lundis et mercredis les produits nécessaires au conditionnement des comprimés, c'est-à- dire les notices, blisters, boîtes et cartons. Gestion de la production Il y a 20 jours de travail par mois. L’usine fonctionne avec 2 équipes, chacune travaillant 8 heures par jour (avec 30 minutes de pause pendant lesquels les machines sont arrêtées). L’entreprise MED : • Reçoit les prévisions de la part de son client à 12, 8 et 4 semaines. • Reçoit chaque lundi la commande hebdomadaire ferme du client pour la semaine suivante • Délivre hebdomadairement au service d’expédition les demandes de livraison du client • Transmet les prévisions de commandes pour les 4 semaines à venir à ses fournisseurs • Confirme les commandes fournisseurs chaque semaine pour la semaine suivante • Organise de manière hebdomadaire le lancement des lots et adapte le plan de production au quotidien Détails des étapes du processus Il y a également un stock de produits finis après l’étape de conditionnement, il est en moyenne constitué de 4 lots de chaque type de médicaments. Construction de la carte VSM de l’état actuelle de l’entreprise MED Première phase du dessin : le client Deuxième phase du dessin : Les Processus de Fabrication Troisième phase du dessin : Les Fournisseurs Quatrième phase du dessin : Les Flux d’Information Cinquième phase du dessin : La Ligne de Temps Analyse • Cette etape a pour but l’analyse de l’état actuel afin de réfléchir à l’état futur. Pour cela, il faut s’approprier un nouveau mode de fonctionnement de la fabrication des produits appelée production au plus juste (correspond au juste à temps : l’un des piliers du Lean Manufacturing). La surproduction : Un élément qui surprend lorsqu’on regarde la carte VSM de l’entreprise MED est le temps de traitement (15 heures, l’équivalent d’un jour de travail) comparé au Lead Time (65.3 jours). Le rapport des deux est égal à 0.015, ce qui veut dire que seulement 1.5 % du temps passé par les produits dans l’entreprise est du temps de valeur ajoutée. vsm de l’état futur • Question A - Quel est le Takt Time de la chaîne de fabrication ? Dans le cas de l’entreprise MED, la demande client est de 23 lots par mois. Deux équipes se relaient, chacune travaille 8 heures par jour avec 30 minutes de pause, 20 jours par mois. Tak time MED: 13h • Question B - Les produits finis vont-ils séjourner dans un dépôt ou seront-ils directement acheminés au quai d’expédition ? Les lots de médicaments A, F et C sont des produits dédiés : la production se fait sur commande. Il n’est donc pas possible de constituer un stock de produits finis à la fin de la chaîne de valeur et d’attribuer les lots en fonction de la demande client. Les lots de médicaments seront par conséquent directement acheminés au quai d’expédition. • Question C - Où est-il possible d’établir un flux continu ? • Question D - Où est-il nécessaire de mettre en place un flux tiré ? Un couloir FIFO ? • Question E - Quel sera le processus régulateur ? • Question F - Comment sera lisser la charge ? • Question G - Quel sera le pas de production ? • Question H - Quelles sont les autres améliorations à mener ? Question C - Où est-il possible d’établir un flux continu ? Le Graphique 1 présente les temps de cycles des différents processus qui composent la fabrication des médicaments A, F et C au sein de l’entreprise MED. Tous sont inférieurs au Takt Time, temps de changement de fabrication inclus. Il apparaitrait donc cohérent de rassembler certains d’entre eux en flux continu et ainsi de réduire le nombre d’étapes. Cependant, il est important de garder à l’esprit que les équipements nécessaires à l’enrobage et au conditionnement ne sont disponibles qu’à 60 % pour la production de A, F et C. Cela est dû au fait qu’ils sont également utilisés pour d’autres médicaments. Ils ne peuvent pas être intégrer à un flux continu commun aux quatre étapes, car ils seraient alors dédiés aux seuls médicaments appartenant à la famille de produits étudiée : A, F et C. Un flux continu qui joindrait seulement les étapes d’enrobage et de conditionnement n’est pas non plus envisageable sans savoir si, pendant les 40 % du temps de non disponibilité, les équipements (lit d’air fluidisé et chaîne de conditionnement) fonctionnent ensemble. En ce qui concerne les étapes de granulation et de compression, le cumul de leurs temps de cycle équivaut à 10 heures, et leurs changements de fabrication Batch to Batch durent respectivement 1 heure et 0.75 heure, le total est donc de 11.75 heures : inférieur au Takt Time (13 heures). Les temps de changement de fabrication Product to Product ne sont pas pris en compte car les équipements sont dédiés aux médicaments A, F et C qui ont la même composition. Il n’y a donc pas de changement de produit, mais seulement des changements de lot. Question D - Où est-il nécessaire de mettre en place un flux tiré ? Un couloir uploads/Industriel/ pratique-du-methode-vsm-dans-le-milieu-industriel25.pdf
Documents similaires
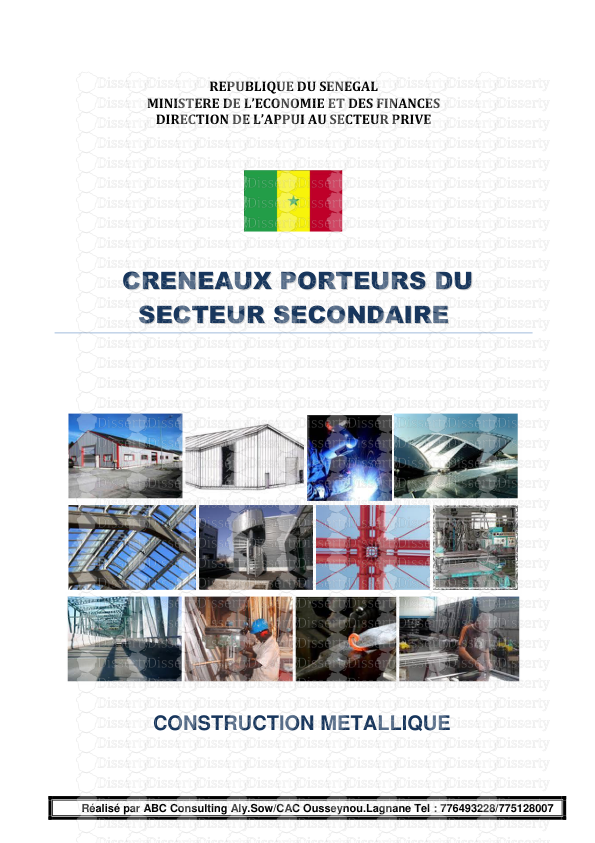
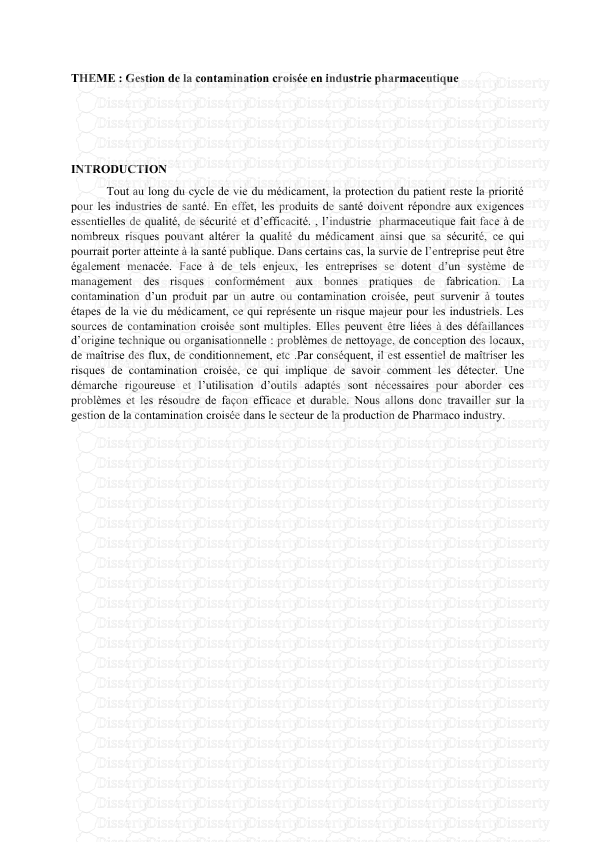

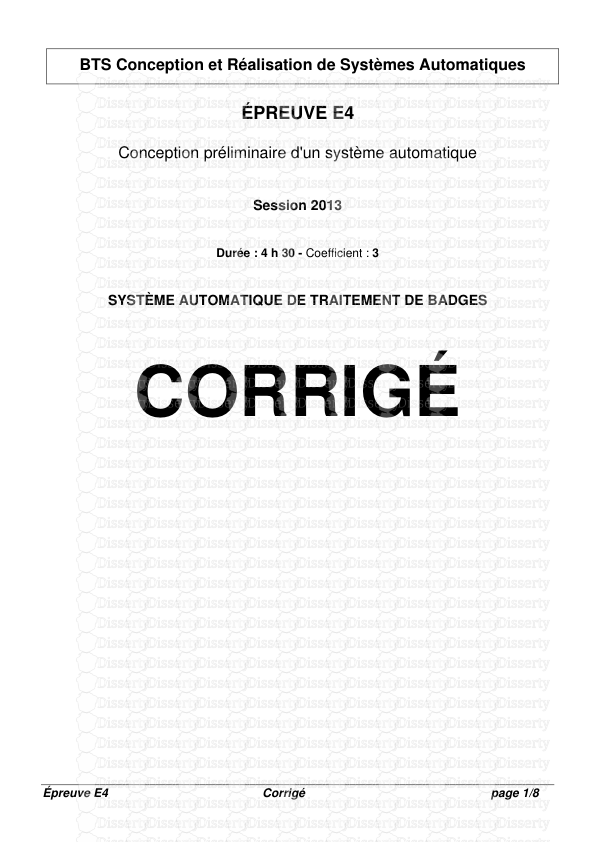
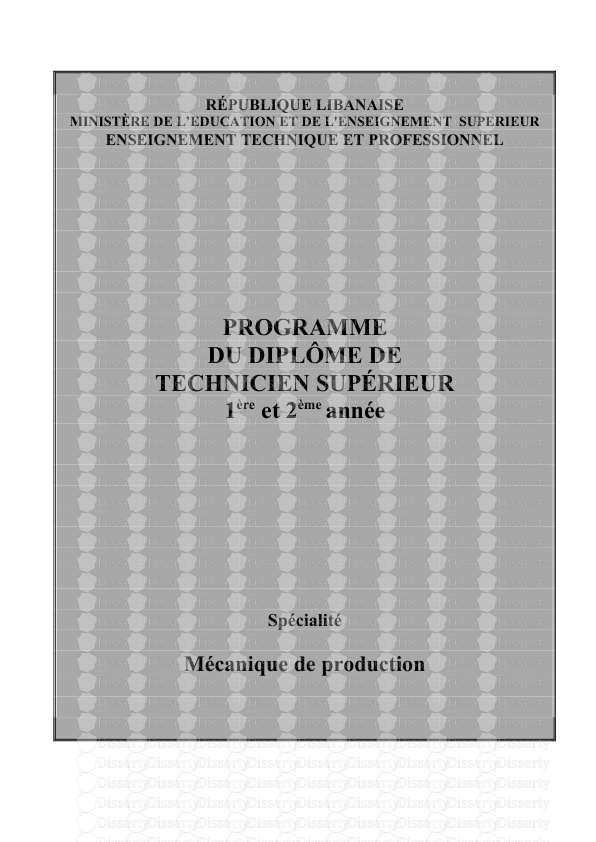
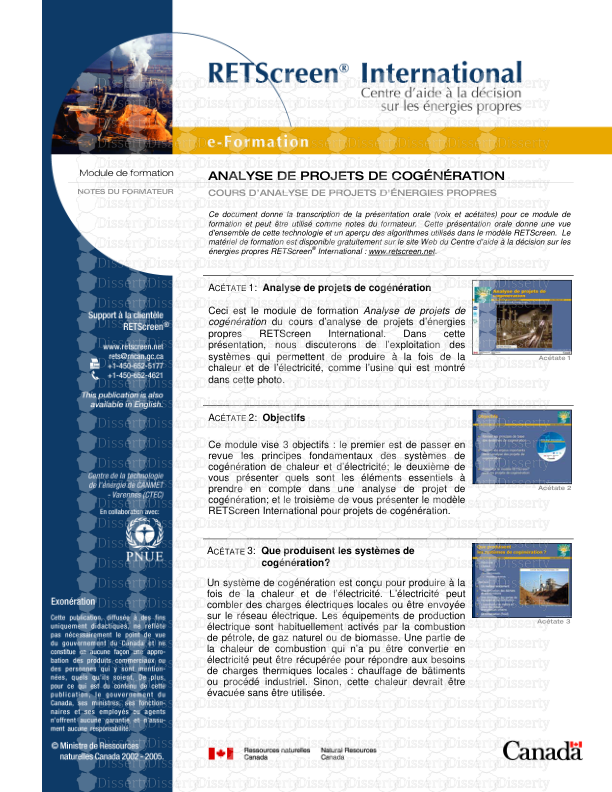
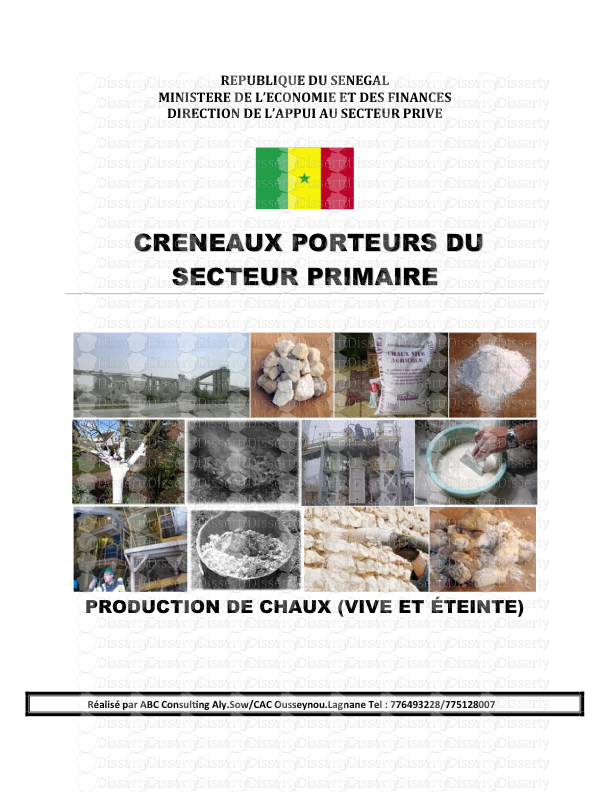
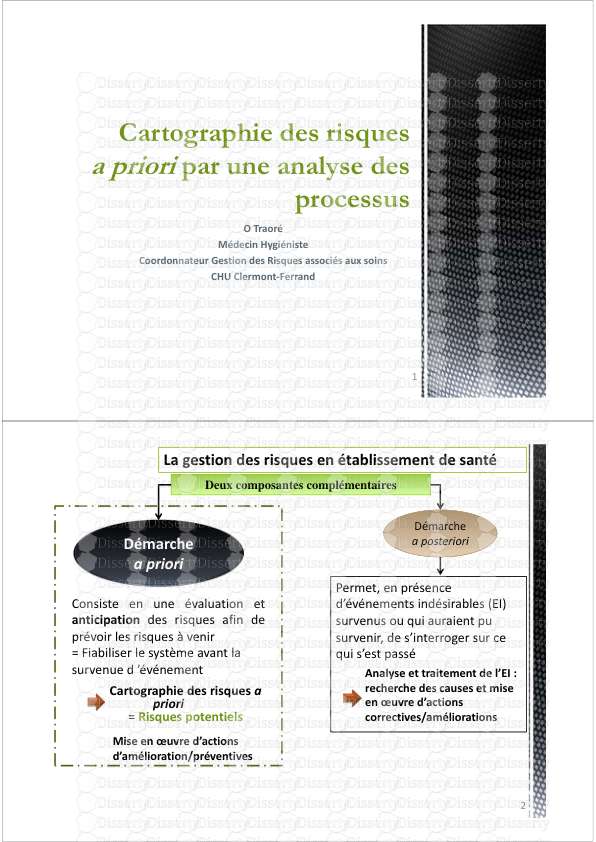
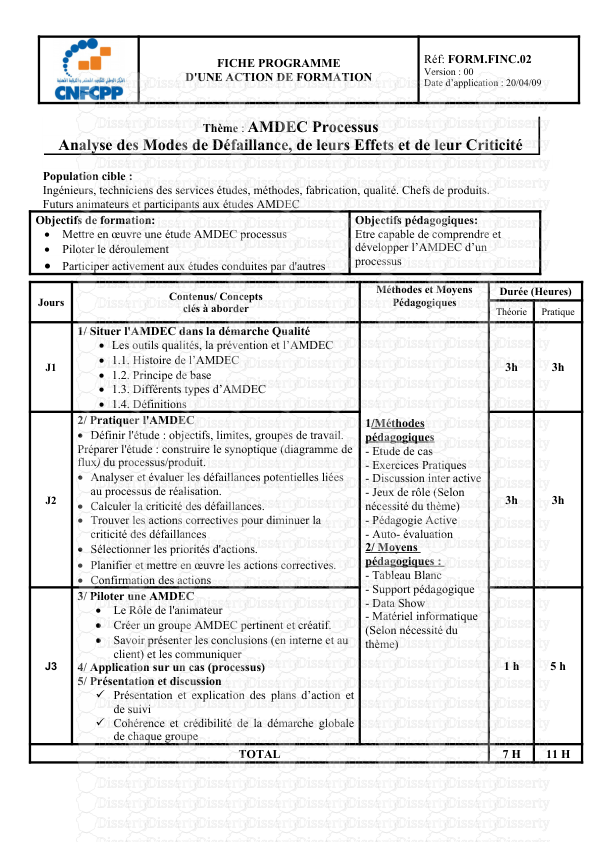
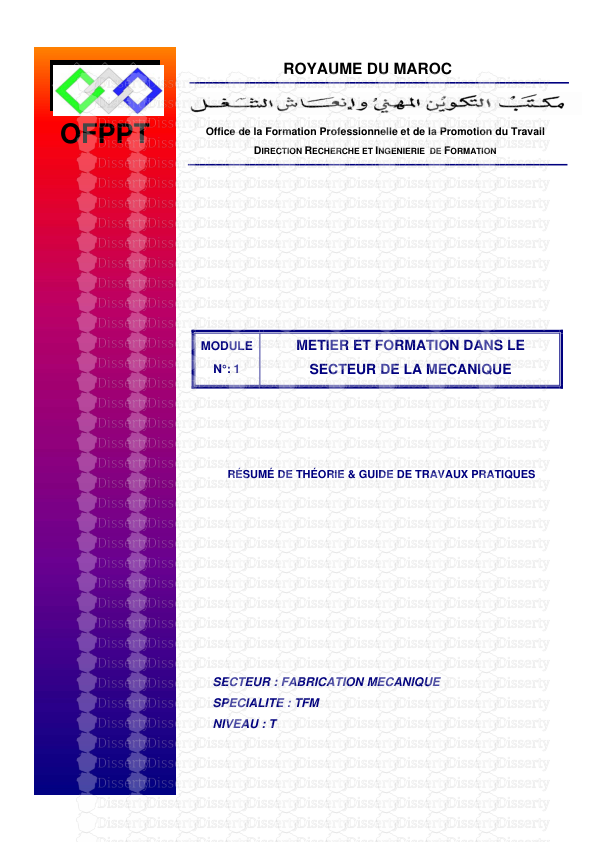
-
82
-
0
-
0
Licence et utilisation
Gratuit pour un usage personnel Attribution requise- Détails
- Publié le Sep 01, 2021
- Catégorie Industry / Industr...
- Langue French
- Taille du fichier 0.4610MB