Gestion de la Maintenance TPM 1 MAINTENANCE PRODUCTIVE TOTALE 1 - INTRODUCTION
Gestion de la Maintenance TPM 1 MAINTENANCE PRODUCTIVE TOTALE 1 - INTRODUCTION Toutes les grandes entreprises sont allées au Japon voir sur place pourquoi les en- treprises japonaises étaient plus performantes. Elles en sont revenues avec la méthode TPM. Cette approche est de longue haleine et de nombreuses entreprises manufactu- rières se sont lassées avant une mise en place définitive. L’européanisation de la méthode (par exemple, la Topomaintenance, appellation déposée par Usinor Sacilor) et son adap- tation aux PME en fait actuellement une méthode plus facile à mettre en œuvre. Rappelons-nous, tout d’abord, que l'environnement industriel a fortement évolué durant ces 20 dernières années. D’une situation où l'offre était inférieure à la demande, nous sommes passés à une situation où l'offre est supérieure à la demande. Il y a trois causes à ceci : l'exigence de la clientèle s'est accrue. Le client réclame le choix, la qualité, des coûts et des délais raisonnables pour les produits qu'il achète ; la concurrence est beaucoup plus forte, elle est devenue internationale. Dans ce climat, l'entreprise doit rester compétitive ; les industries cherchent à automatiser une partie de leurs équipements afin de gagner en flexibilité et fiabilité. Cette situation a abouti à une complexification de la production. Les entreprises cherchent à améliorer et à mieux gérer leurs productions tout en diminuant les coûts : il s'agit donc de produire mieux. Pour cela, il faudra passer par : la chasse à la non-productivité, c’est à dire lutter contre toutes les causes de non-productivité qui ralentissent la production, une évolution du personnel qui passe par sa requalification et une formation adaptée aux nouvelles technologies, une usine nouvelle, c’est à dire une entreprise cherchant à modifier ou amélio- rer ses méthodes pour tendre vers l'excellence industrielle. Le meilleur moyen d'y parvenir est de se diriger vers la Qualité Totale. 1.1 – Vers la qualité totale La Qualité est l'ensemble des caractéristiques d'une entité qui lui confèrent l'apti- tude à satisfaire des besoins exprimés et implicites. Gestion de la Maintenance TPM 2 Recherche de la performance Satisfaire les exigences de la clentèle Evolution des hommes QUALITE TOTALE Figure 13.1 – Vers la Qualité Totale La Qualité Totale est le mode de management d'un organisme centré sur la quali- té, basé sur la participation de tous ses membres et visant au succès à long terme par la satisfaction du client, et à des avantages pour tous les membres de l'organisme et pour la société (Extrait de la Norme ISO 8402). En trois points, les finalités de la Qualité totale sont : rechercher la performance, satisfaire le client, répondre aux aspirations du personnel. En d’autres termes, la qualité totale est une démarche pour aller vers « l’excellence ». La T.P.M. s'inscrit logiquement dans cette démarche. 1.2 – Petit historique Les Japonais ont toujours apprécié les prix pour récompenser une initiative ou un effort. Dans cette optique, la JMA (Japan Management Association), important cabinet de consultant au Japon, offrit à partir de 1964 un prix « Productive Maintenance » pour les entreprises ayant appliqué, avec les meilleurs résultats, une démarche de maintenance intégrée à la production. En 1969, la JMA fonda le JIPM (Japan Institute of Plant Maintenance = Institut japonais de la Maintenance Industrielle) ; celui-ci continua d'attribuer le prix PM aux entreprises. Le JIPM décida alors de transformer ses méthodes « américaines » de main- tenance productive en une méthode « japonaise ». En 1971, NIPPON DENSO fût lauréat pour avoir appliqué brillamment la PM en ayant, en particulier, utilisé des techniques de participation du personnel. La JIPM lui décerna le prix TPM. La TPM était née. Son principal promoteur était M. SEICHI NAKAJIMA. En 1983, celui-ci, devenu entre temps le président du JIPM, formalisa les prin- cipes et méthodes de la T.P.M. dans un livre qui devint une référence1. 1.3 – La TPM dans le monde et en France Partant du Japon, la T.P.M s'est logiquement imposée dans les pays avoisinants et principalement dans les nouveaux pays industrialisés : Corée, Singapour, Taiwan, Hong- 1 S. NAKAJIMA - La maintenance productive totale - Afnor Eyrolles - 1986 Gestion de la Maintenance TPM 3 Kong, etc.., où la recherche d'une meilleure performance de l'équipement était un souci permanent. Confrontés à cette concurrence, les pays occidentaux ont dû rapidement trouver de nouvelles méthodes de gestion et d'organisation pour rester compétitifs sur le marché mondial. Les entreprises se sont peu à peu intéressées à la TPM à la suite de missions d'observations au Japon. RENAULT a été notamment l'une des premières entreprises françaises, sous l'impulsion de M. LEVY, à se déplacer au Japon pour chercher à com- prendre les remarquables performances des entreprises japonaises. En France, les entreprises qui ont été touchées les premières par la démarche TPM, sont essentiellement les grandes entreprises utilisant un mode de fabrication en processus continu : sidérurgie et construction automobile. Les résultats de l'application de la TPM. dans des entreprises de renom comme SOLLAC, CITROËN avec le plan Mercure, USINOR SACILOR et sa Topomaintenance, contribuèrent à diffuser le con- cept au-delà de ces secteurs industriels. Des entreprises comme KODAK ou MATRA s’y mirent aussi. Cet intérêt pour la TPM devint grandissant grâce aux nombreux exemples de réussite existant aujourd'hui. 2 – PRESENTATION DE LA TPM Lorsque sous la pression de la concurrence, d’un marché difficile ou tout simple- ment de la hiérarchie, on se penche sur le rendement des machines, on peut, si on choi- sit mal ses indicateurs, se bercer d’illusions, ou alors, si on les choisit bien, tomber des nues !... Pourquoi ? Tout simplement parce que l'analyse du rendement machine se base souvent sur la production achevée par rapport à sa capacité nominale. Devant la faiblesse du rendement obtenu, le responsable est tout trouvé : c’est l’opérateur. En effet, tout le monde sait que le « lampiste » manque de motivation dans son travail, alors que la ma- chine n’en manque pas !... Tout l’art de botter en touche. Regardons un peu plus loin que le bout de notre nez : on a trop tendance à considérer les caractéristiques d'une machine comme immuables, sauf la dégradation de ses performances dans le temps (elle vieillit la pauvre !..), les caractéristiques des machines annoncées par les constructeurs sont toujours optimistes, ceux-ci se refusant à considérer l’existence de facteurs perturbateurs (environnement), la part d'intervention humaine, etc.. ; au moment de l'achat et plus tard en exploitation, qui s’inquiète de la fiabilité des machines, de leur rendement, de la compressibilité des temps technolo- giques, de savoir si les spécifications du constructeur sont bien réelles ? En fait, un suivi attentif révèle vite que les caractéristiques théoriques ne corres- pondent pas à la réalité. Il est même fréquent que, dans les projets d'amélioration de rendement machine, l'attention se focalise plutôt sur le travail de l'homme. Certes, il faut lui donner une certaine priorité, mais lorsque sa part de travail est optimisée ou que l'on a affaire à des machines entièrement automatiques, il devient nécessaire de se pen- cher sur le travail des machines elles-mêmes, sur leur exploitation mais aussi leur amélio- Gestion de la Maintenance TPM 4 ration : accessibilité pour nettoyage et maintenance, ergonomie des commandes, per- formances qui sont autant de pistes d'améliorations potentielles. En poussant la logique jusqu'au bout, pourquoi pas les tailler sur mesure ? En ef- fet, Il est fort probable que certains des concurrents de l’entreprise disposent du même matériel. Comment dès lors se démarquer ? 2.1 - La TPM : une démarche vers l’excellence Dans la mentalité japonaise, surtout celle de l'après guerre qui a façonné l'indus- trie nippone, toute forme de gaspillage est à combattre. La chasse au gaspillage est un gisement de gains qui peut se révéler riche et être exploité facilement. Tendre vers l’excellence, c'est éliminer les pertes et atteindre les cinq zéros : zéro accident, zéro dé- faut, zéro arrêt, zéro délai, zéro papier. 1. Pas d'incident ou d'accident signifie aucun arrêt, pas de perte humaine, donc pas de délai mais aussi pas de frais financier et donc pas de papier. 2. Pas de défaut signifie que le temps de fabrication est utilisé à 100%, donc pas de déchet, pas de délai, donc pas de papier. 3. Zéro défaut c’est aussi zéro contrôle, pas de délai, donc pas de papier. Donc, tendre vers l’excellence, c’est : minimiser les arrêts machines, améliorer les machines du parc existant, maximiser l'utilisation de ces machines, réduire les frais financiers, retarder ou rendre inutiles les investissements capacitaires (nouveaux équipe- ments pour assurer la capacité de production), introduire de nouveaux équipements en tenant compte de l'expérience du pas- sé (ne pas refaire les mêmes erreurs). L’esprit TPM, c’est cela, et on voit que cela va revaloriser la fonction Maintenance en affirmant ses liens nécessaires avec les autres fonctions de l’entreprise et en particulier la Production. Mieux, on constate que la TPM correspond à une notion de progrès per- manent. Elle peut être définie comme uploads/Industriel/gestion-de-la-maintenance-tpm.pdf
Documents similaires
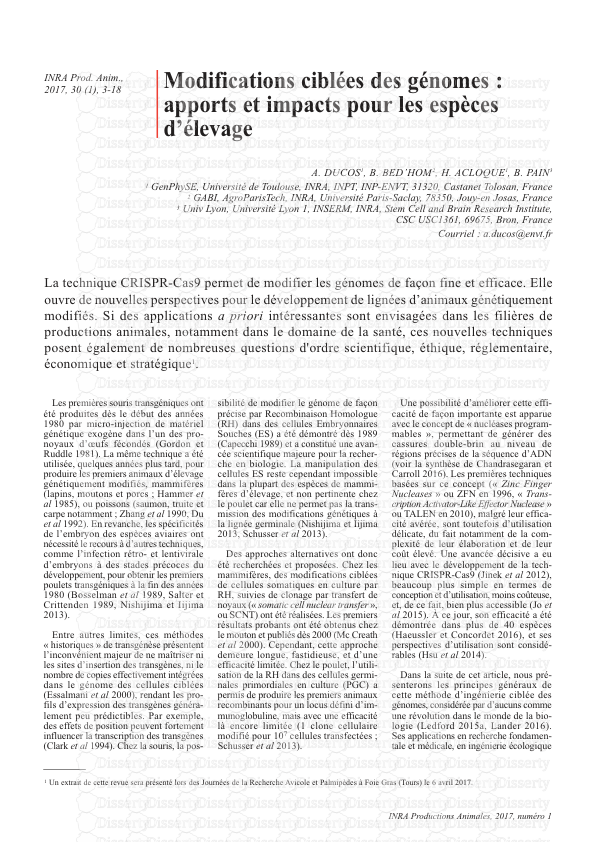
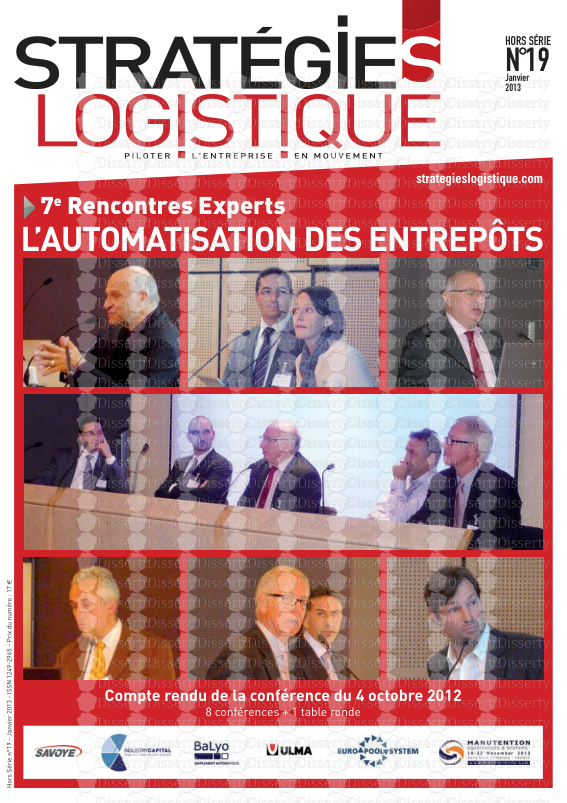
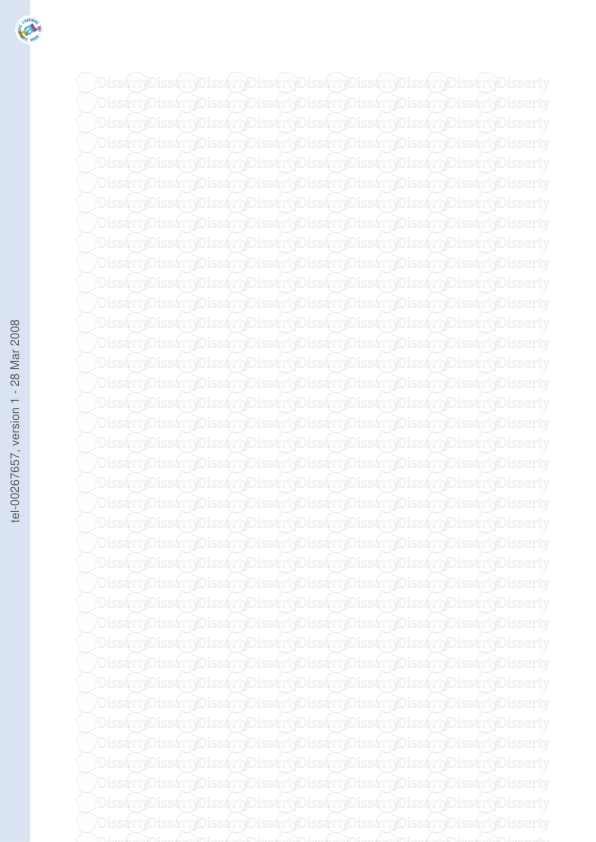
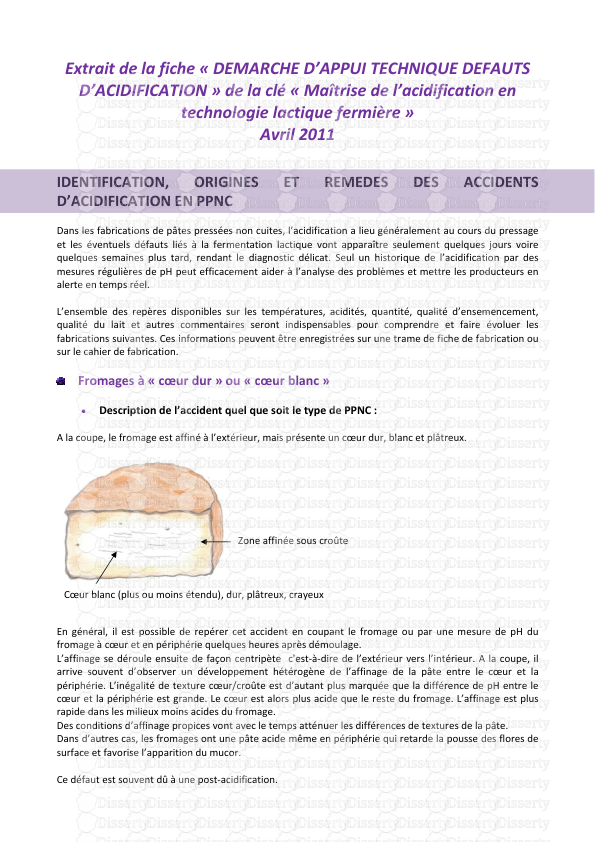
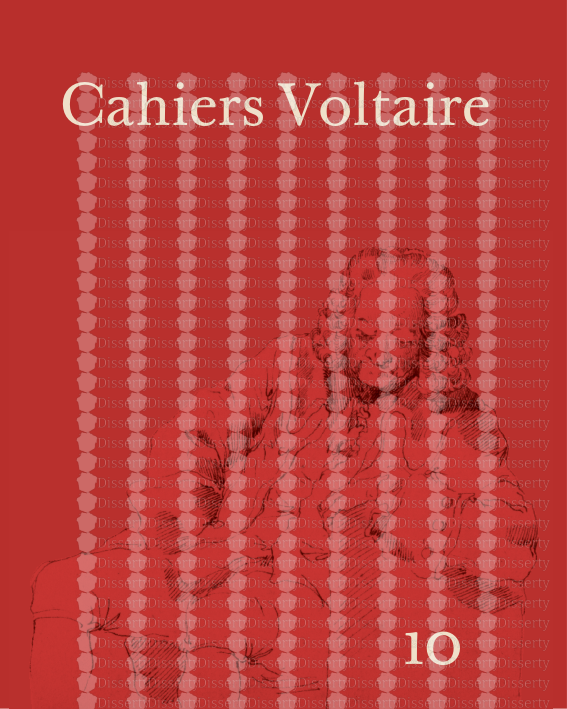
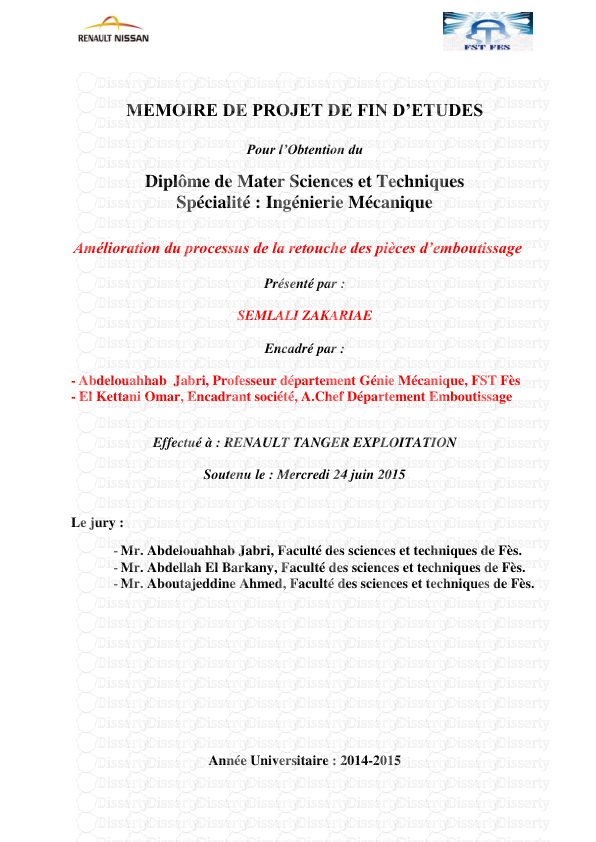
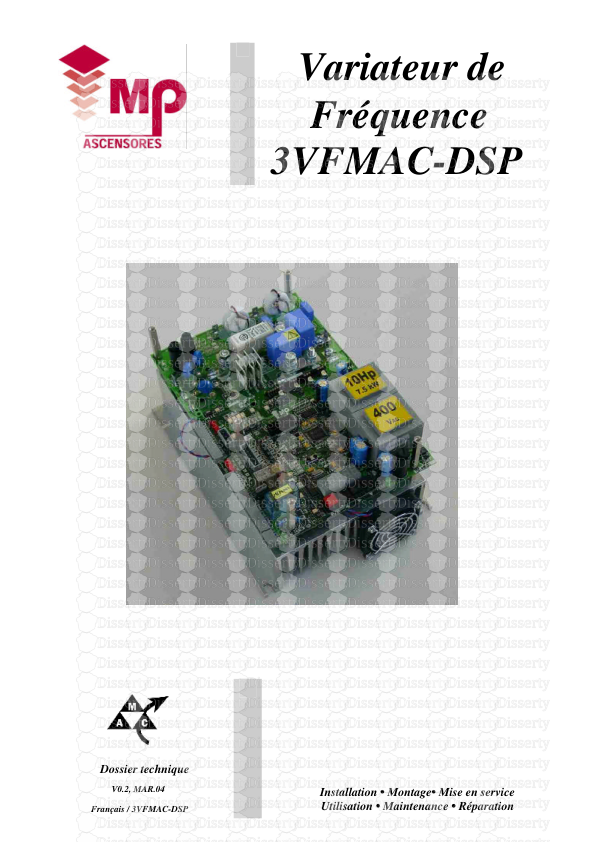

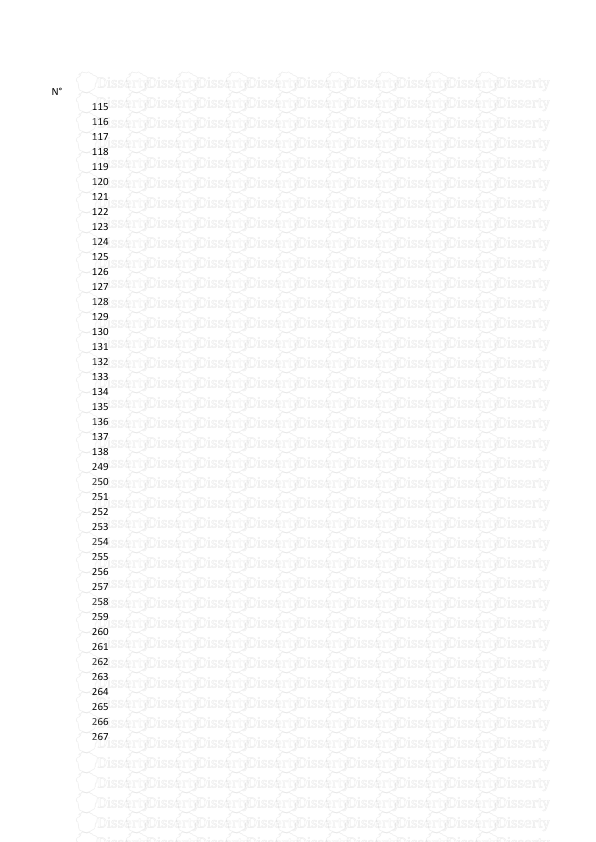
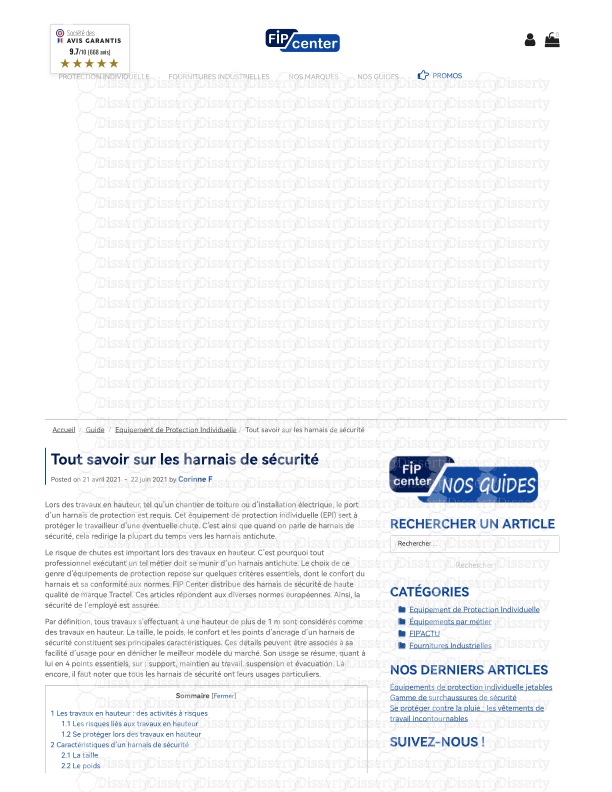
-
58
-
0
-
0
Licence et utilisation
Gratuit pour un usage personnel Attribution requise- Détails
- Publié le Apv 30, 2022
- Catégorie Industry / Industr...
- Langue French
- Taille du fichier 0.2583MB