Lean Management: OUTILS Le Lean Management et la chasse du gaspillage Qu’est-
Lean Management: OUTILS Le Lean Management et la chasse du gaspillage Qu’est-ce que le Lean Manufacturing? Le Lean repose sur l’élimination des gaspillages dans les processus (par exemple : trop de stock de produits finis, trop de déchets de production) Le Lean n’a pas pour objectif la réduction du nombre d’employés. Le Lean vise à augmenter la capacité de production, en réduisant les coûts et le temps de cycle. Le Lean s‘appuie sur la compréhension des besoins des clients. La Pensée Lean Quantifier la valeur du produit du point de vue du client. Identifier la chaîne de valeur pour mettre en évidence les gaspillages. Créer un flux pour réduire la taille de lots et les encours (WIP). Produire seulement ce que le client a commandé. Rechercher perpétuellement la perfection, en améliorant la qualité et en éliminant les gaspillages Types de Gaspillages (MUDA) Production excessive Stocks excessifs Défauts, déchets Étape sans valeur ajoutée Temps d’attente Mouvements inutiles Déplacements inutiles Sous-utilisation des compétences Système de Production Toyota Lissage Travail Standardisé Kaizen Les bons produits, La bonne quantité, Au bon moment : •Temps TAKT •Flux continu •Production tirée •Changement rapide de d’outils •Logistique intégrée • Arrêt automatique • Séparation homme-machine • Élimination des causes d’erreurs • Contrôle qualité intégré • Analyse de problèmes Motivation Et ResponsabilisationLa meilleure Qualité, les coûts les plus bas, les délais les plus courts,la meilleure Sécurité, la plus haute Éthique. Juste-à-Temps Autonomation Stabilité des 4M : Main d’œuvre, Matière, Machines, Méthodes Processus Lean et Traditionnel Le temps de développement d’un nouveau produit est divisé par 2. L’investissement dans des machines et des outils est réduit de moitié. Les heures d’effort des employés directs et indirects sont divisées par 2. Le Taux de défauts sur les produits finis est divisé par 2. Utilisation de la moitié de la surface de travail pour la même production. Les encours sont divisés par 10 au moins. La taille de lots est réduite. Source : « The machine that changed the world » de Womack et Jones (2009) www.LeLeanManufacturing.com Processus Lean et Traditionnel La capacité et la cadence augmentent. Plus d’espace disponible. Une meilleur rotation des stocks. Amélioration de l’ergonomie des postes de travail. Amélioration de la qualité : réduction des déchets et des retouches. Réduction des stocks : matières, en-cours, produits finis. Réduction des délais d’exécution. Meilleure Marge Brute. Amélioration de la participation, de l’implication et du moral des employés. Source : « The machine that changed the world » de Womack et Jones (2009) Concepts et Outils Lean 5S et Management Visuel Jidoka Kaizen et PDCA Poka Yoke (Systèmes Anti-Erreurs) Changement Rapide d’Outils (SMED) Production Préparation Processus (3P) Flux Tiré (Juste-à-Temps) Travail Standardisé Maintenance Productive Totale (TPM) Formation Intégrée (Training within Industry TWI) Flux de valeur Théorie des Contraintes (TOC) 6 Sigma 5S et Management Visuel 5S Méthode d’organisation des postes de travail. Réduit les gaspillages causés par le désordre, le temps perdu pour trouver un outil ou un équipement libre, des déplacements inutiles, des étapes redondantes ou inutiles, des machines en double… Éléments des 5S Seiri : Trier Seiton : Ranger Seiso : Nettoyer Seiketsu : Standardiser Shitsuke : Respecter 5S + 1 ou 6S On ajoute un sixième « S », pour la Sécurité et la Santé. 5S et Management Visuel Management Visuel Rendre visibles et évidents sur le terrain, les machines, les matières premières et les outils. Rendre visibles sur le terrain, les informations, les indicateurs, les objectifs, les projets. Quelques Idées Identifier sur une carte les chemins d’accès (entrée, sortie, allées, lignes, stocks intermédiaires…) et les zones de travail (postes, tables, bureaux, ateliers, machines…). Effectuer une réorganisation des allées, des entrées, des sorties, si nécessaire. Attribuer un nom, une adresse à chacune des zones de travail. Marquer au sol, les allées, les entrées et sorties et les zones de travail. Identifier les flux avec des flèches au sol ou sur les murs. Réorganiser les postes de travails si besoin. Marquer au sol les zone de stockage, les équipements et machines. Utiliser des codes couleurs en fonction des types de zones d’actions. LE 5S LES 5 ETAPES DU 5S SEIRI DEBARRASSER SEITON RANGER SEISSO NETTOYER SEIKETSU STANDARDISER SHITSUKE RESPECTER MFQ Picardie / Formation 5S / 2002 LE 5S MFQ Picardie / Formation 5S / 2002 RESULTATS ATTENDUS D'UNE ACTION 5S Amélioration des rendements et de la qualité Mode de management basé sur la responsabilisatio n individuelle Amélioration de l'environnement et du moral des employés par une discipline consentie Application pratique et concrète du PDCA assimilable par tous Réduction des risques en matière de sécurité 5 S LE 5S MFQ Picardie / Formation 5S / 2002 L'IMPLICATION DES EMPLOYES Le 5S agit sur leur travail Ils découvrent la discipline par consentement mutuel Ils s'investissent Ils se sentent concernés LE 5S MFQ Picardie / Formation 5S / 2002 PRINCIPES obtenir un lieu clair et plaisant Mettre en pratique ces principes en groupe Respecter une discipline Instaurer des règles maintenir les moyens propres LE 5S MFQ Picardie / Formation 5S / 2002 COMMENT MENER UNE ACTION 5S ? 1 Avoir la décision de la direction 2 Former l'encadrement 3 Mettre en place le comité de pilotage 4 Réaliser un chantier pilote - formation/action - évaluation 5 Etablir le déploiement - autres zones et secteurs - TPM LE 5S ETAPE 1 : DEBARRASSER 5S – ETAPE 1 : DEBARRASSER MFQ Picardie / Formation 5S / 2002 FINALITE Ressources trop importantes Dépenses inutiles Avances de production Libérer l’espace Faire prendre Conscience des gâchis visuellement Nettoyer l’environnement de travail Identifier les anomalies 5S – ETAPE 1 : DEBARRASSER MFQ Picardie / Formation 5S / 2002 FAIRE LA DIFFERENCE ENTRE L’UTILE ET L’INUTILE PRINCIPE GENERAL MFQ Picardie / Formation 5S / 2002 5S – ETAPE 1 : DEBARRASSER MFQ Picardie / Formation 5S / 2002 DEMARCHE 8 Evaluer l'action menée 2 Constituer le groupe de travail 3 Faire le constat 4 Préparer l'action 5 Faire l'inventaire 1 Définir les limites du chantier 7 Etablir le plan d'actions 6 Nettoyer l'environnement de travail 9 Faire évaluer l'action par la direction LE 5S ETAPE 2 : RANGER 5S – ETAPE 2 : RANGER MFQ Picardie / Formation 5S / 2002 FINALITE Gagner du temps en ne cherchant pas Préserver le matériel et les stocks Assurer la sécurité Optimiser le poste de travail et les stocks Réduire les efforts (ergonomie) Détecter immédiatement toute anomalie 5S – ETAPE 2 : RANGER MFQ Picardie / Formation 5S / 2002 "une place pour chaque chose, chaque chose à sa place" PRINCIPE GENERAL 5S – ETAPE 2 : RANGER MFQ Picardie / Formation 5S / 2002 DEMARCHE 2 Organiser la zone de travail 3 Définir les types de rangement 4 Repérer les objets 5 Identifier les anomalies systématiquement 1 Etablir la fréquence d’utilisation 6 Faire évaluer l'action par la direction LE 5S ETAPE 3 : NETTOYER 5S – ETAPE 3 : NETTOYER FINALITE Rendre l’environnement de travail agréable Eviter les pannes et l’usure prématurée Assurer la sécurité et la qualité Détecter les défaillances potentielles 5S – ETAPE 3 : NETTOYER PRINCIPE GENERAL L’aspect n’est que la résultante de l’effet recherché Anomalie constatée Flaque d’eau au sol Nettoyage Pomper l’eau Diagnostic Fuite sur tuyau Dépannage Poser une rustine Réparation Cause identifiée Action corrective Remplacer le tuyau Frottement du tuyau sur une pièce mobile Attacher le tuyau 5S – ETAPE 3 : NETTOYER DEMARCHE 6 Faire évaluer l’action par la direction 2 Identifier les sources de salissure et les anomalies 3 Réparer les défaillances apparentes 4 Analyser les causes de défaillance et les éliminer 5 Faciliter le nettoyage 1 Nettoyer 2. Simplifier l’accès et le nettoyage des zones concernées 1. Réduire la production de salissures LE 5S ETAPE 4 : STANDARDISER 5S – ETAPE 4 : STANDARDISER FINALITE Pérenniser les résultats obtenus Standardiser les règles pour tous Rendre le 5S auditable 5S – ETAPE 4 : STANDARDISER • Débarras • Rangement • Nettoyage PRINCIPE GENERAL Etablir les règles de : QQOQC 5S – ETAPE 4 : STANDARDISER MFQ Picardie / Formation 5S / 2002 DEMARCHE 2 Diffuser les règles 3 Etablir les gammes de nettoyage 4 Mettre en œuvre les gammes de nettoyage 1 Etablir les règles de rangement LE 5S ETAPE 5 : RESPECTER 5S – ETAPE 5 : RESPECTER FINALITE Appliquer les règles en permanence Optimiser les règles Développer l’amélioration permanente 5S – ETAPE 5 : RESPECTER règles AUDIT 5S PRINCIPE GENERAL 5S – ETAPE 5 : RESPECTER DEMARCHE 2 Réaliser les audits 3 Stimuler la démarche d’amélioration 1 Etablir un référentiel d’audit Concepts et Outils Lean 5S et Management Visuel Jidoka Kaizen et PDCA Poka Yoke (Systèmes Anti-Erreurs) Changement Rapide d’Outils (SMED) Production Préparation Processus (3P) Flux Tiré (Juste-à-Temps) Travail Standardisé Maintenance Productive Totale (TPM) Formation Intégrée (Training within Industry TWI) Flux de valeur Théorie des Contraintes (TOC) 6 Sigma JIDOKA Quelle est la finalité ? Livrer un produit de qualité au moindre cout. Comment y arriver ? En arrêtant en cas de problème et en le fixant à uploads/Industriel/lean-management-2.pdf
Documents similaires
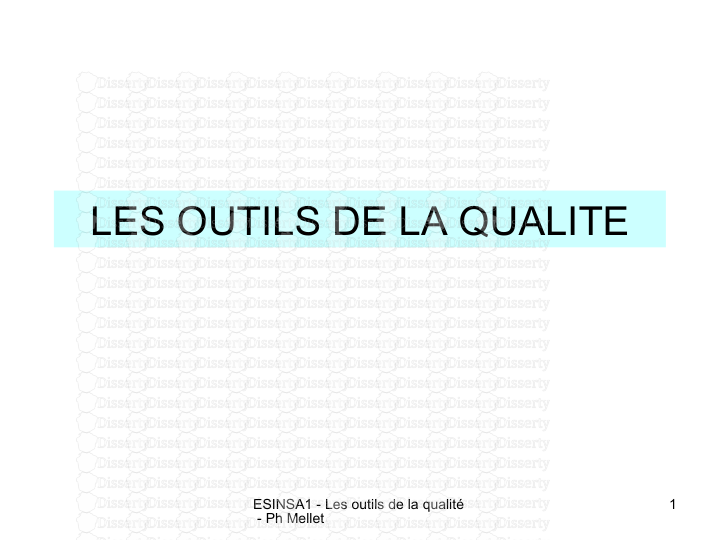
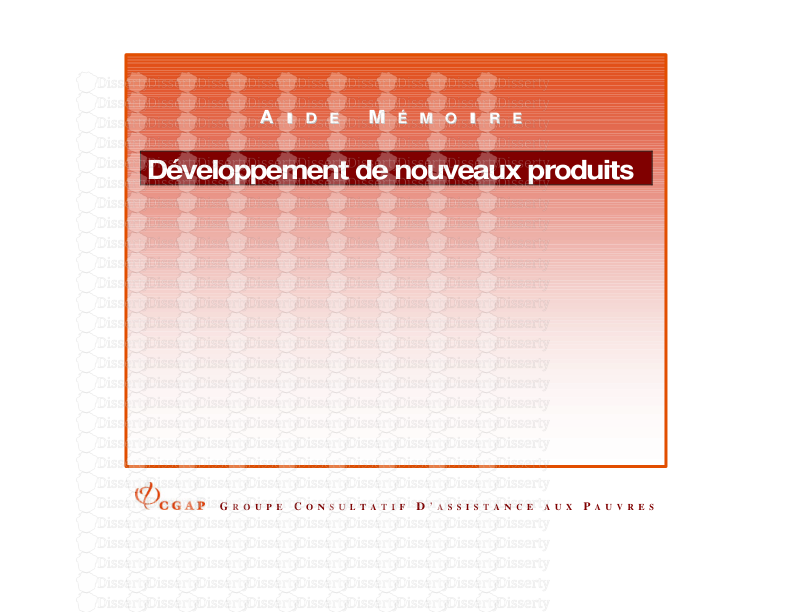
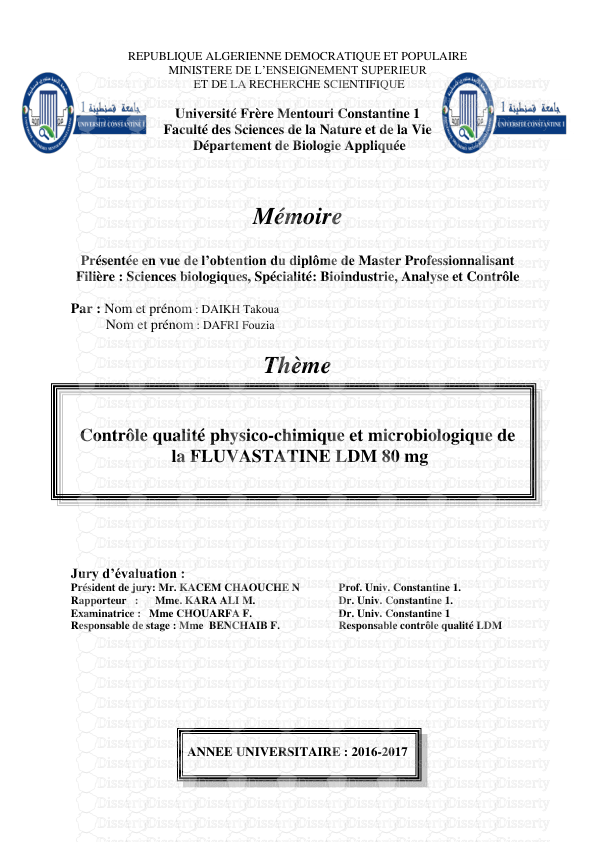
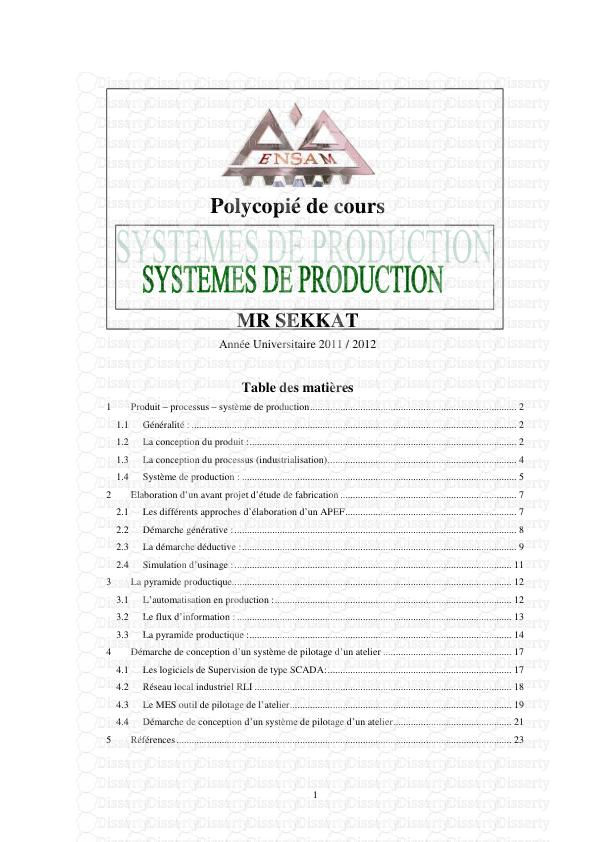
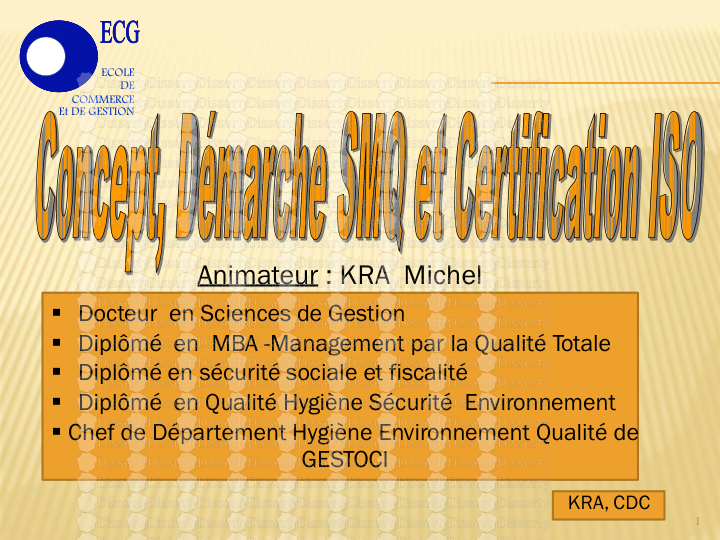
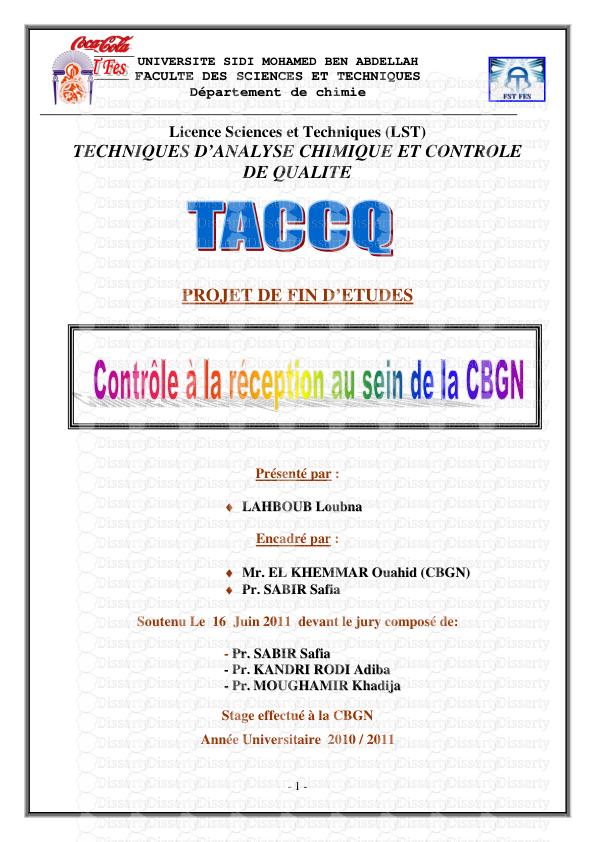
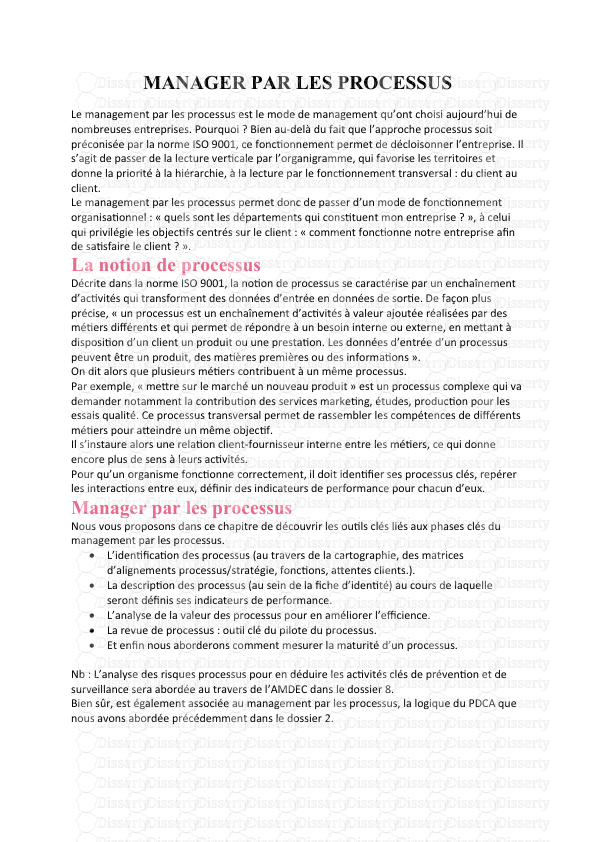
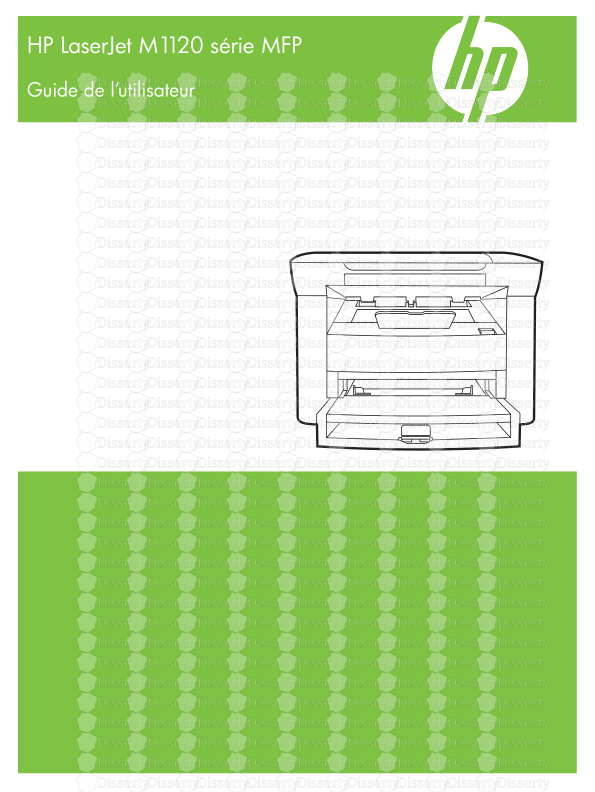
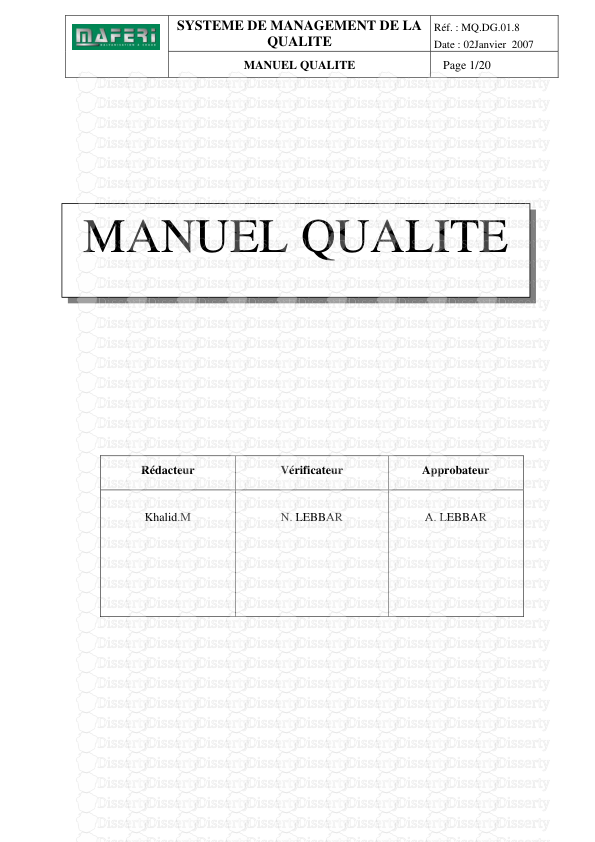

-
59
-
0
-
0
Licence et utilisation
Gratuit pour un usage personnel Attribution requise- Détails
- Publié le Mai 22, 2021
- Catégorie Industry / Industr...
- Langue French
- Taille du fichier 2.3524MB