http://logistiqueconseil.org/ 1 LOGISTIQUE : MANUTENTION, ENTREPÔTS... La logis
http://logistiqueconseil.org/ 1 LOGISTIQUE : MANUTENTION, ENTREPÔTS... La logistique : Ensemble des opérations matérielles visant à assurer des conditions optimales à la circulation des marchandises, interne à l'entreprise, ou lors des opérations de distribution physique entre les fournisseurs et leurs clients. En d'autres termes, la logistique est axée sur la rationalisation des opérations liées au déplacement des marchandises : emballage, conditionnement, étiquetage, stockage, transport, manutention, déclaration en douane...). La gestion des flux logistiques : La gestion des flux consiste à piloter l’ensemble des activités successives qui sont réalisées lors de la fabrication d’un produit ou sa distribution. C’est ce mouvement des matières/composants/sous- ensembles/encours/produit finis lelong de la chaine de fabrication et de distribution qui forme le flux. Dans une usine, lorsque l’ensemble des produits fabriqués parcoure les mêmes étapes de production, il y a une seule chaîne de fabrication et donc un flux. Si par contre on se retrouve avec des produits À, B et C qui parcourent en un moment donné de leur fabrication une série d’activités différentes pour chacun des trois produits, on a un total de trois flux de production. Un flux est aussi appelé une chaîne d’activité ou chaîne de valeur (en anglais : value stream). Les notions de « activité », « valeur » et « chaîne de valeur » La valeur : correspond à l’ensemble des rémunérations des facteurs de production (frais divers, salaires, amortissement…). C’est toute charge réellement supportée pour satisfaire les besoins de la clientèle (ce qu’un client est disposé à payer si on lui laissait la possibilité de choisir) Une activité : est une séquence organisée de tâches. Ces dernières se distinguent en deux catégories : les tâches ordinaires du processus qui génère de la valeur pour le client, et les autres tâches tels que les retouches, les manutentions inutiles, le stockage superflu …qui augmentent le coût sans ajouter de la valeur au produit. Elles sont qualifiées de Muda (gaspillages). Si le client était informé de la présence des coûts générés par cette seconde catégorie de tâches dans sa facture, il refuserait de la payer. Chaîne de valeur : Ensemble des activités successives inclues dans un flux. Lorsqu’elle est analysée dans une cartographie, il devient possible de repérer les handicaps ou les avantages de chaque tâche en termes de coût http://logistiqueconseil.org/ 2 . I- Les buts de la gestion des flux Dans cette chaîne d’activités qui forme le flux, le bénéfice recherché est : L’identification, l’analyse et la diminution de toute forme de gaspillage ou de mauvaise utilisation des ressources dans le processus d’approvisionnement, de fabrication ou de distribution. Une étude est périodiquement menée pour déterminer à chaque fois les causes réelles du gaspillage, de les remonter au niveau de l’équipe de pilotage qui se chargera de lancer des actions correctives. La séparation des activités à valeur ajoutée et des activités sans valeur ajoutée (du point de vue de la clientèle ou du besoin à satisfaire). Les activités sans valeur (source de pertes et de gaspillage dans le processus) sont alors supprimées. Cette réduction du gaspillage à la longue fini par devenir un avantage concurrentiel pour l’entreprise. La notion de « Gaspillage » Le gaspillage dans un processus désigne toute activité ou opération inutile ou de trop. Il s’agit des activités sans valeur ajoutée réelle, dont on peut se passer, ou que l’on peut améliorer pour aboutir à un meilleur résultat. Dans le processus de production, on distingue sept gaspillages très courants : La surproduction (cadence plus rapide que nécessaire). Les délais d’attente (standards de travail non respectés) ; Les activités de manutention et transport (convoyage superflu). Les traitements inadéquats (Usinages inutiles). Les stocks inutiles (stocks excessifs). Les mouvements inutiles. Les défauts de fabrication (correction des erreurs). Les méthodes correctives : Méthodes de Lean managemen t : 5M ou méthode d’hishikawa 5S (Seiri - Seiton - Seiso - Seiketsu - Shitsuke ) Etapes des 5S 3M (Muda, Mura, Muri) Le Kaizen, amélioration continue http://logistiqueconseil.org/ 3 SMED (Single Minute Exchange of Die) II- Les différents types de flux logistiques Dans l’espace, on distingue deux catégories de flux logistiques : les flux logistiques internes et les flux logistiques externes. A- Flux logistiques internes Flux de production : circulation de matières et composants dans le réseau de fabrication. Ces flux sont constitués par la chaîne des opérations de transformation, d’usinage, de manutention et de stockage intermédiaires. B- Flux logistiques externes Flux d’approvisionnement ou flux amont : circulation des matières et consommables depuis le magasin du fournisseur jusqu’au magasin de l’entreprise cliente. Flux de distribution ou flux aval : circulation des produits finis ou semis finis de l’entrepôt de l’entreprise jusqu’à ce lui d’une autre entreprise cliente. Les flux de logistique externe sont tous constitués par une chaîne d’opération d’emballage, de manutention, de transport et de stockage. Selon la méthode d’approvisionnement choisie dans le processus, les flux logistiques peuvent prendre différentes formes. C’est ainsi qu’on distingue : Les flux poussés : une particularité des flux internes, dans ce type d’organisation, chaque étape de fabrication est déclenchée par la disponibilité des matières premières ou des composants au niveau du poste amont. Les produits fabriqués sont stockés en attente d’une demande pour la consommation. Les flux tirés : Le déclenchement de la livraison ou de la fabrication d'un produit se fait uniquement sur la demande d’un poste client. Par principe il y a zéro stock dans la chaîne. Les flux tendus : une combinaison des deux précédents flux, c’est équivalent d’un flux tiré, mais avec un minimum de stocks et d'en-cours repartis lelong de la chaîne logistique. Les flux synchrones : dans ce type d’organisation, la livraison de composants différents est réalisée dans le respect de leur ordre d'entrée dans le processus de fabrication. Ils sont donc livrés juste ou moment de leur utilisation. Ce qui permet de réduire les stocks et les coûts qui y sont liés. III- Méthode de gestion des flux : la cartographie de la chaîne de valeur La Cartographie de la chaîne de valeur est aussi appelée Cartographie des Flux de Valeur (CFV) ; en anglais, Value Stream Mapping (VSM) ou Material and information Flow Analysis (MIFA). C’est une représentation schématique des différents flux logistiques d’une entreprise ou d’une fonction de l’entreprise. http://logistiqueconseil.org/ 4 La cartographie de la chaîne de valeur trace dans un graphe l’ensemble des flux des matières et d’informations. Toutes les activités incluent dans le processus sont représentées à l’aide de symboles (pictogrammes) simples, et un accent est porté particulièrement sur : L’analyse des délais (durée des cycles, les temps d'arrêt, temps de changement des outils …) ; L’analyse de la qualité des produits (nature des défauts, nombre de défauts, origine…) ; L’analyse des stocks intermédiaires (tailles des lots, taille des stocks et en-cours, coûts) ; L’analyse des opérations de manutention et transport (nombre de mouvements, coûts), L’analyse de l’emploi des ressources (quantité, rendement, efficacité, productivité …) L’analyse des flux d’information (nature et quantités). Démarche de la cartographie de la chaîne de valeur La méthode de cartographie de la chaîne de valeur se réalise en trois phases : Phase 1 : Cartographier la situation actuelle afin de visualiser et comprendre l'état présent des activités (nature des activités inclues dans chaque flux, ordre et temps d’exécution, ressources affectées…) ; Phase 2 : Faire une analyse critique de chaque flux, repérer toute forme de gaspillage, retracer le processus optimisé en prenant le soin d’éliminer dans chaque flux, les activités à non valeur ajoutée. Cartographier la situation future. Des jeux de couleurs différents sont utilisés sur les symboles afin faciliter l'identification, sur la nouvelle carte, des points à améliorer ; Phase 3 : proposer des actions correctives. Détailler dans un planning leur ordre, délai et coût d’exécution. Concevoir les outils de contrôle en désignant les responsables et la périodicité de mise à jour de chaque rapport. Suivre l’avancée des améliorations jusqu’à l’atteinte des objectifs. Gestion des stocks, entrepôts et magasins Après le transport, le stockage est l’activité la plus génératrice des charges sur la chaîne logistique. On retrouve dans ce maillon les opérations de manutention manuelle ou mécanique des produits et des colis vers les emplacements de stockage ou vers le lieu d’emballage, de conditionnement, d’éclatement, d’expédition à l’aide d’outils adaptés ; le contrôle qualitatif et quantitatif des marchandises avec saisie informatique ; le traitement physique des supports et contenants (palettes, paniers, conteneurs, bacs en plastiques et caisses) ; la vérification des conditions de stockage (poids, température …) ; les inventaires des stocks (inventaire ponctuel, ou tournant). La gestion des stocks : généralités Techniques et méthodes de réapprovisionnement Catégories, rôle et fonctions des stocks La préparation des commandes Contrôle des marchandises et réception en entrepôt http://logistiqueconseil.org/ 5 Gerer la chaîne d'approvisionnement interne Stock de sécurité et réserves des stocks Méthodes de calcul du stock de sécurité La gestion informatique des fiches articles…. Gestion d'entrepôt : Emballage, Arrimage et manutention La logistique, c'est aussi un ensemble des procédures et techniques mises en œuvre pour manier et uploads/Management/logistique 2 .pdf
Documents similaires
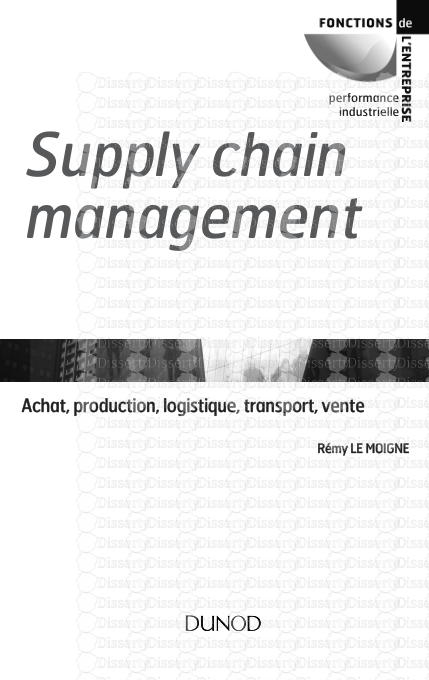
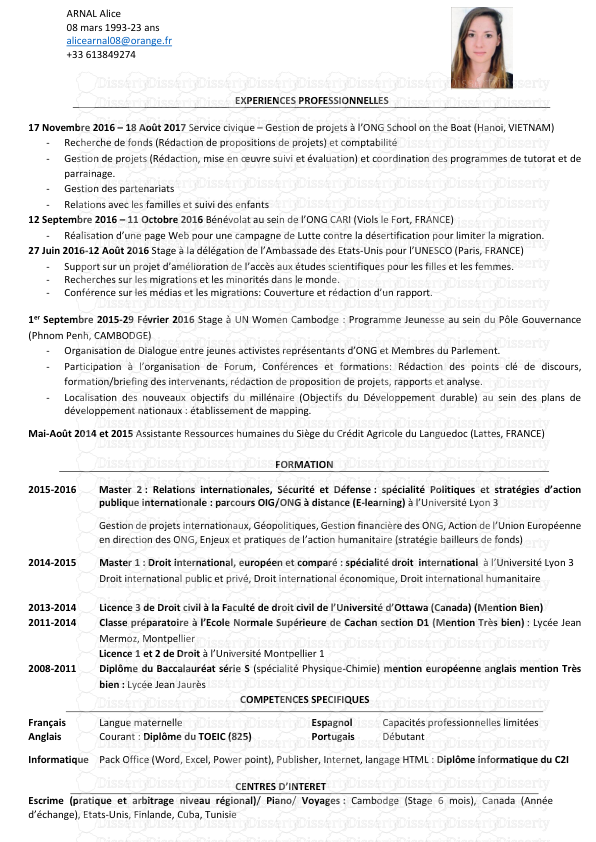
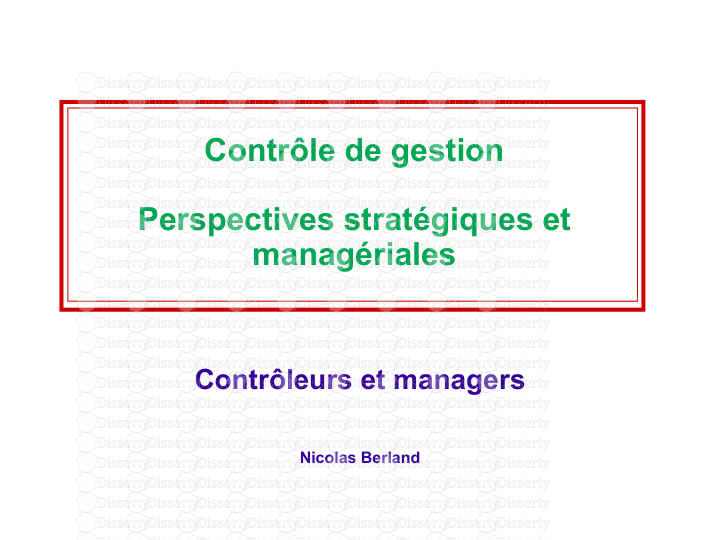
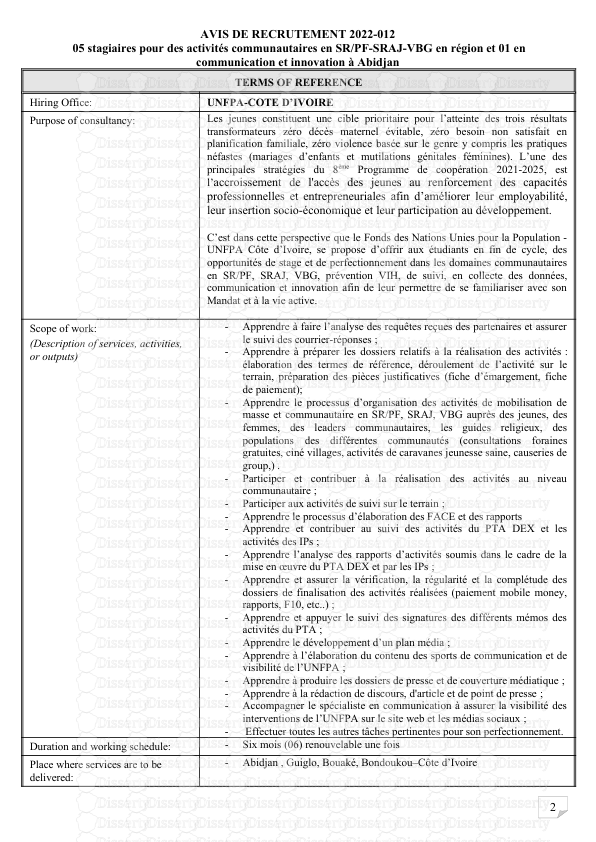

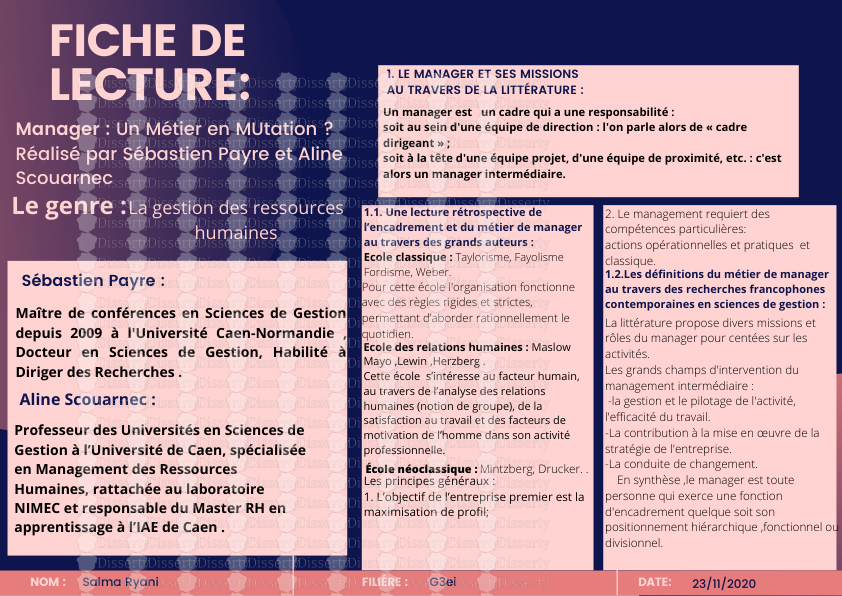
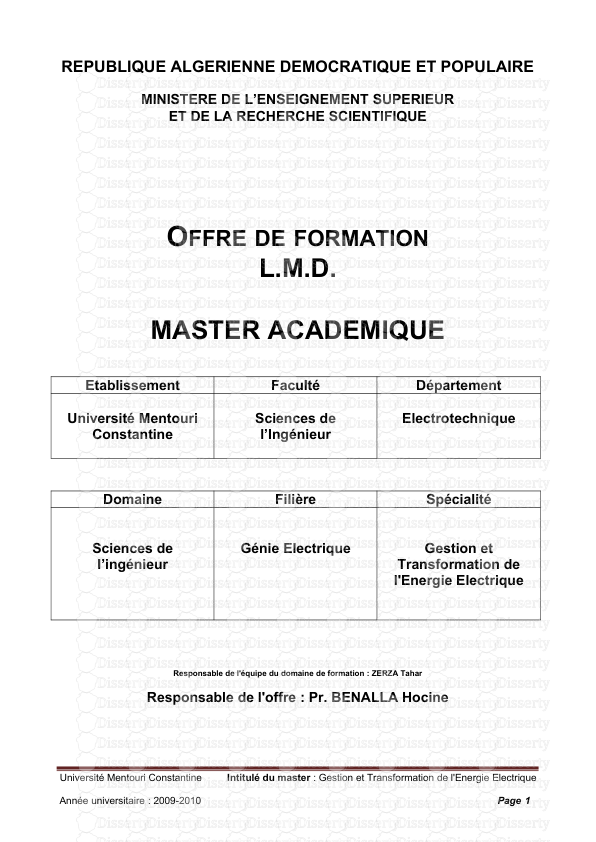
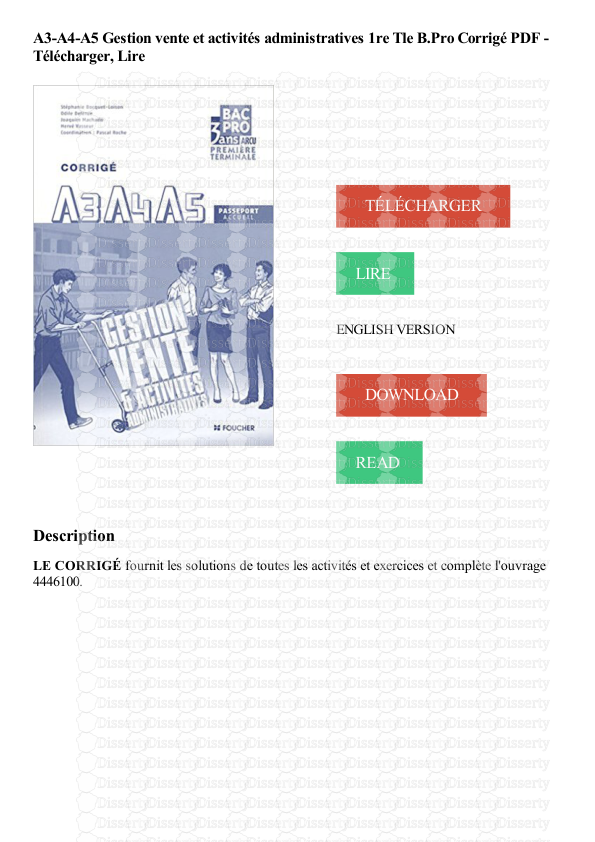
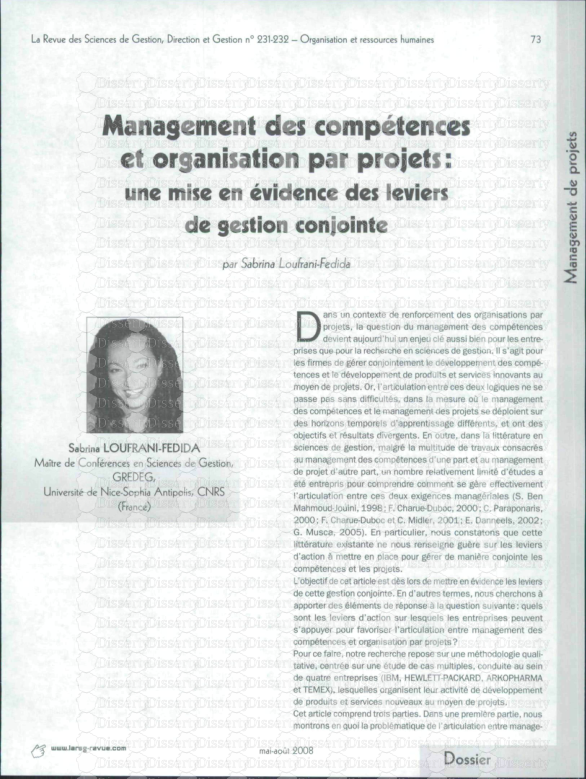
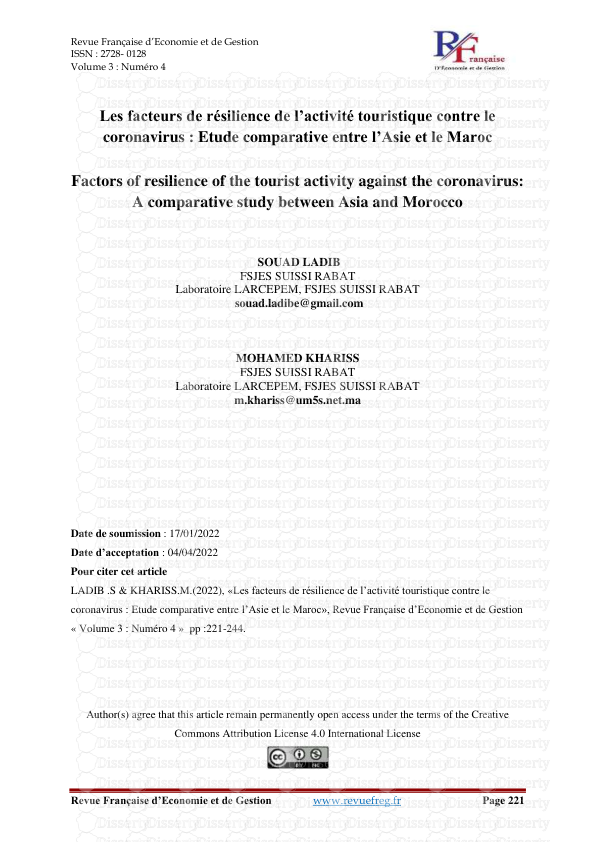
-
53
-
0
-
0
Licence et utilisation
Gratuit pour un usage personnel Attribution requise- Détails
- Publié le Sep 11, 2021
- Catégorie Management
- Langue French
- Taille du fichier 0.6613MB