1 Lean manufacturing 1 Plan I. Histoire du Lean II. Composantes du système de p
1 Lean manufacturing 1 Plan I. Histoire du Lean II. Composantes du système de production Toyota (TPS) III. Outils de base du Lean 2 Histoire industrielle : de la production classique vers le Lean Trois phases 3 2 I. Histoire du Lean 1) Production de masse 4 I. Histoire du Lean 5 2) Toyotisme … 2) Toyotisme … 1938 : le concept de Juste-à-Temps naît au sein de Toyota 1940 : le TWI (Training within Industry) est introduit au sein de Toyota, s’appuyant sur la formation des collaborateurs et le partage de connaissances sur le terrain. 1940 : Kaoru Ishikawa invente le diagramme en arrête de poisson, célèbre méthode éponyme de résolution de problèmes. 1949 : Taiichi Ohno, Executif Manager chez Toyota, développe le concept d’«élimination des gaspillages». 1951 : Ohno améliore le Système de Production Toyota (TPS), en incluant le contrôle visuel, les suggestions des employés, le TWI, la réduction de taille de lots et le Kanban. 1965 : Toyota reçoit le prix Deming pour la Qualité. 6 3 3) Maturation… 1986 : Motorola met en place le 6 Sigma. 1988 : Taiichi Ohno publie internationalement le « Toyota Production System ». 1988 : Création de l’EFQM (European Foundation for Quality Management), formalise ainsi une référence pour l’Excellence Opérationnelle 1991 : Publication de « The machine that changed the world » de James Womack, fruit de 5 années d’études. 2000 : Création de la norme ISO 9001, référence des systèmes de gestion de la qualité 2007 : Toyota devient le 1er constructeur automobile mondial 2010 : J.Cox, introduit le TLS comme TOC Lean Sigma, associant le Lean & 6 Sigma dans un environnement TOC (Theory of Constraints). 7 Rappel définition du Lean : Lean= maigre (pourquoi parle-t-on de maigre?) • Une démarche Lean est une approche systématique d'identification et de suppression systématique des gaspillages • Un processus Lean est un processus débarrassé de toutes les opérations « inutiles » et des stocks en excès qui le rendent « obèse » II. Préparation de l’excellence industrielle Lean 8 Les MUDAS de Taiichi Ohno: II. Préparation de l’excellence industrielle Lean 9 4 Le Temps de Cycle d’un process est sa durée, exprimée en temps de travail •Temps de cycle de production : durée entre la première opération et la livraison •Temps de cycle de conception: de la formulation du besoin à la réalisation et validation des maquettes •Temps de cycle réalisation d’une affaire : durée entre la prise d’une commande et la réception par le client Temps de cycle II. Préparation de l’excellence industrielle Lean 10 Temps de gamme & Temps de cycle II. Préparation de l’excellence industrielle Lean 11 Takt Time & juste à temps (eng: JIT) Juste à Temps JIT: II. Préparation de l’excellence industrielle Lean 12 5 Continuité du flux : Flux pièce-à-pièce II. Préparation de l’excellence industrielle Lean 13 Exemple transformation LEAN : Design de lignes de flux : Assemblage Boeing 737 II. Préparation de l’excellence industrielle Lean 14 II. Composantes du TPS 15 6 Annexe 16 Annexe L'andon, 行灯(japonais), composé des caractères 行, aller, et 灯, lampe électrique, pourrait se traduire tout simplement par "lumière où il faut aller". 17 18 7 Démarche du Lean Management 19 20 21 Les Objectifs du Lean 8 22 Les Objectifs du Lean 23 Les Objectifs du Lean 24 Les Objectifs du Lean 9 25 La Maison du Lean 26 Les Objectifs du Lean 27 Les Etapes de la Démarche Lean 10 28 Les Etapes de la Démarche Lean Les Gaspillages sont des GAINS potentiels Lorsqu’on a rien ... Tout est précieux ... Définition des Gaspillages 29 Définition des Gaspillages 30 11 Définition des Gaspillages 31 Typologie des Gaspillages MUDA MURI (l'excès) MURA (les irrégularités) 32 Les 7 Muda Les « MUDA » décrivent une classification des pertes de l’organisation industrielle. Une remarque préalable est nécessaire : cette classification ne prétend pas à l’exhaustivité. Les frontières entre les muda sont parfois floues. Il peut exister d’autres pertes que les 7 muda habituellement décrites lorsqu’on parle du système de production Toyota. 33 12 Les 7 MUDA 34 Les 7 Muda 1. LE GASPILLAGE DE LA SURPRODUCTION 35 Les 7 Muda Produire plus que le besoin du client. Produire avant la commande. Réaliser une tâche qui ne répond à aucune demande ni exigence client. Le pire des gaspillage car source d’autres gaspillages. Provoque le ralentissement, voire l’arrêt du flux. Exemple de surproduction : Taille de lots inadaptée, produire trop de pièces qui vont finir au stock. Préparer une formation trop compliquée, trop longue par rapport à la population ciblée. Médicaments vendus en quantité fixe, pas au détail. 1. LE GASPILLAGE DE LA SURPRODUCTION 36 13 Les 7 Muda 2. LE GASPILLAGE DE STOCKAGE 37 Les 7 Muda Tout ce qui n’est pas indispensable à la réalisation de la tâche, au bon moment. Causé par la surproduction, mais aussi une mauvaise planification. Causé par des temps d’attente non maîtrisés. Capital immobilisé Empêche la résolution de problèmes. Exemples de sur-stockages : Stock mort suite à de mauvaises prévisions de ventes. Dossiers en attentes, souvent à cause d’une organisation multitâches. Impression de supports de formation supérieure au nombre de participants. Stocks de matériel médical dans les hôpitaux, par peur de manque. 2. LE GASPILLAGE DE STOCKAGE 38 Les 7 Muda 3. LE GASPILLAGE DE NON QUALITE 39 14 Les 7 Muda 4. LE GASPILLAGE DES MOUVEMENTS/DEPLACEMENTS 40 Les 7 Muda 5. LE GASPILLAGE DES RÉPARATIONS ET DES REBUTS 41 Les 7 Muda 6. LE GASPILLAGE DES ATTENTES & DES DELAIS 42 15 Les 7 Muda 7. LE GASPILLAGE DU TRANSPORT 43 8. Talent non utilisé Les 8 Muda ? 44 Les MURI Muri (L'Excès) • Le Muri matériel L’excès de matière première ou de pièces dans les ateliers. • Le Muri personnel la main d'oeuvre excessive, inefficace, en attente d'occupation Exemples de MURI • Matériels et matières achetés en excès, en avance, suite à des prévisions mal évaluées, à une politique d'achat ou des tailles de lots inadaptées, • Equipement acheté mais presque jamais utilisé ; • Main d'oeuvre excessive, mal employée, sous occupée ; • Opérations inutiles découlant de modes opératoires inappropriés. 45 16 Mura (Les irrégularités) L'idée de base est que tout flux de production doit s'écouler harmonieusement. Si des obstacles encombrent son cours, il faut retirer les obstacles et contrôler le flux. Exemple de MURA Vous remarquez augmentation inhabituelle de consommation d’huile par un moteur ; or le nombre d’heures de marche journalier n’a pas changé. Si vous décidez d’augmenter le stock d’huile pour prévenir le risque de rupture, vous créez des Muras. Recherchez plutôt s’il existe des fuites et les réparer. Les MURA 46 Discussion / questions ? 47 Les 5S Lean Manufacturing 48 17 Introduction sur les 5S • Technique de management japonaise, • Élaborée dans le cadre du Système de Production de Toyota (TPS) • Méthode pragmatique de l’amélioration de l’existant nécessitant la participation de l’ensemble du personnel. 5S 49 Introduction sur les 5S 5S Démarche de progrès Fondation de tout projet Lean Management Association et responsabilisation de chacun Amélioration de l’efficacité à chaque poste Première étape à toute démarche qualité Méthode focalisée sur la propreté – l’organisation optimale - la formalisation …. Permet de prévenir des désagréments, accidents 50 Introduction sur les 5S 5S L'absence des "5S" est synonyme de : Inefficacité Muda Discipline librement consentie inexistante Moral bas Qualité faible Coûts élevés Incapacité à respecter les conditions de livraison 51 18 Principe des 5S 5S 52 Les 5S: But 5S 53 Cette démarche a été traduite en français par le mot ORDRE qui signifie : Oter l’inutile, se débarrasser Ranger Dépoussiérer, Découvrir des anomalies Rendre évident, Standardiser Etre rigoureux 5S 54 19 5S Lors de cette étape, il s'agit d'éliminer de l'espace de travail toute chose qui n'a pas sa place. Quelques règles permettent de prendre les bonnes décisions : Tout ce qui ne sert pas (ou plus) depuis un an est jeté (ou recyclé si possible). De ce qui reste, tout ce qui sert moins d'une fois par mois est remisé à l'écart (par exemple, au département des archives, ou au magasin à l'usine). De ce qui reste, tout ce qui sert moins d'une fois par semaine est remisé à proximité (typiquement dans une armoire au bureau, dans le rangement au poste à l'usine). 1.SEIRI (Se débarrasser ou Supprimer) 55 5S De ce qui reste, tout ce qui sert moins d'une fois par jour est au poste de travail. De ce qui reste, tout ce qui sert moins d'une fois par heure est au poste de travail, directement à portée de main. Et ce qui sert au moins une fois par heure est directement sur l'opérateur. Cette hiérarchisation du matériel de travail conduit logiquement à Seiton 1.SEIRI (Se débarrasser ou Supprimer) 56 5S 1. Classer tout ce qui se trouve dans votre environnement en deux catégories: Ce qui est nécessaire Ce qui n’est pas nécessaire 2. Se débarrasser de ce qui n'est pas nécessaire 1.SEIRI (Se débarrasser ou Supprimer) 57 uploads/Industriel/cours-lm-managem-g2.pdf
Documents similaires
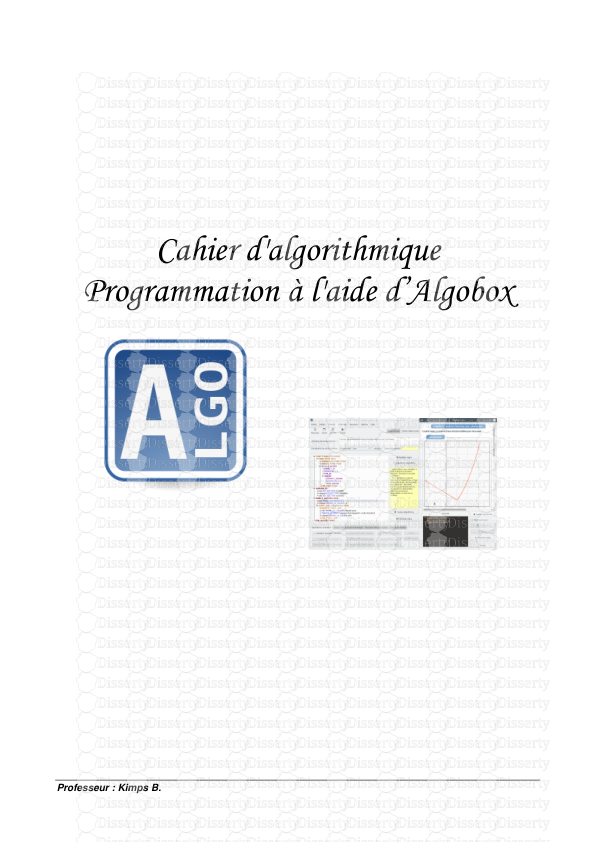

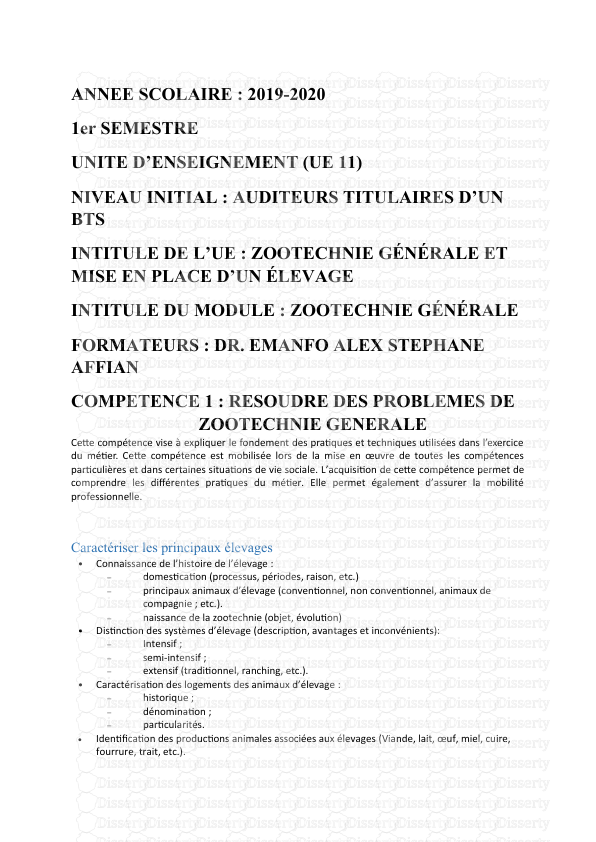
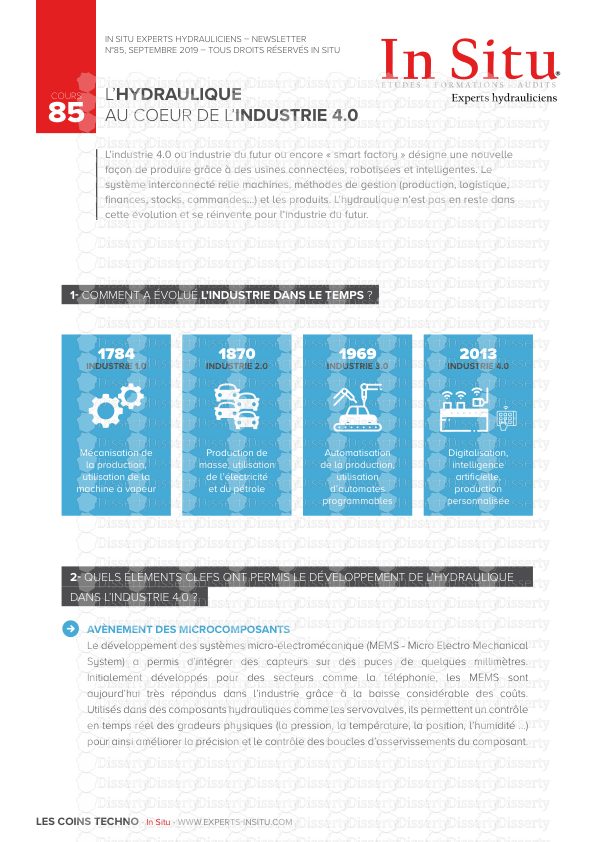
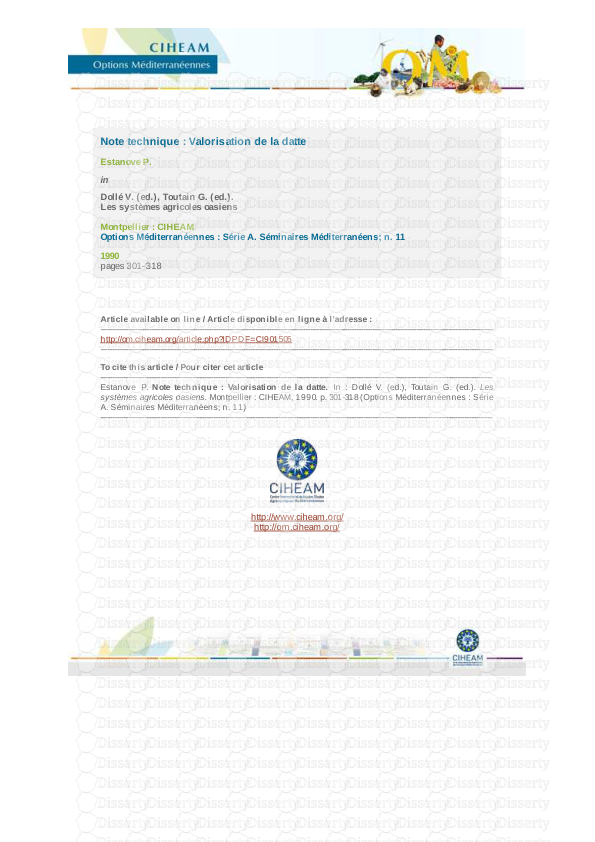
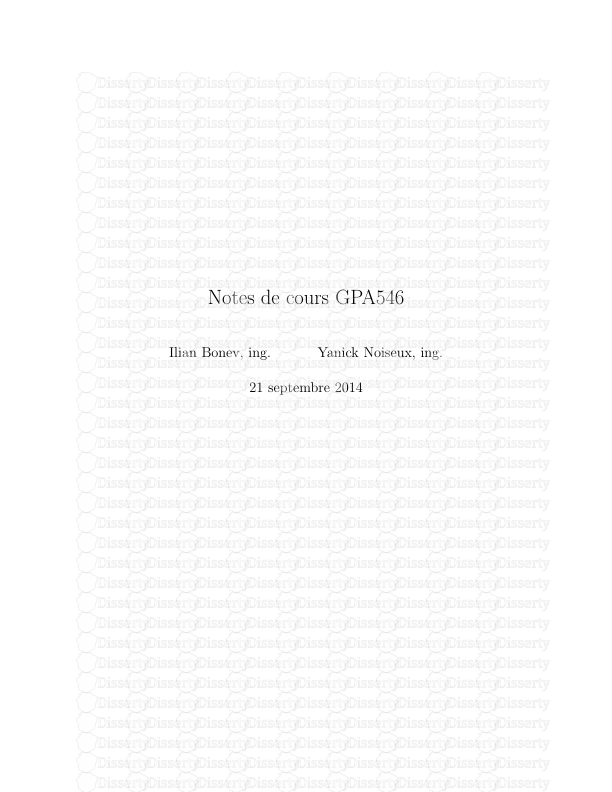

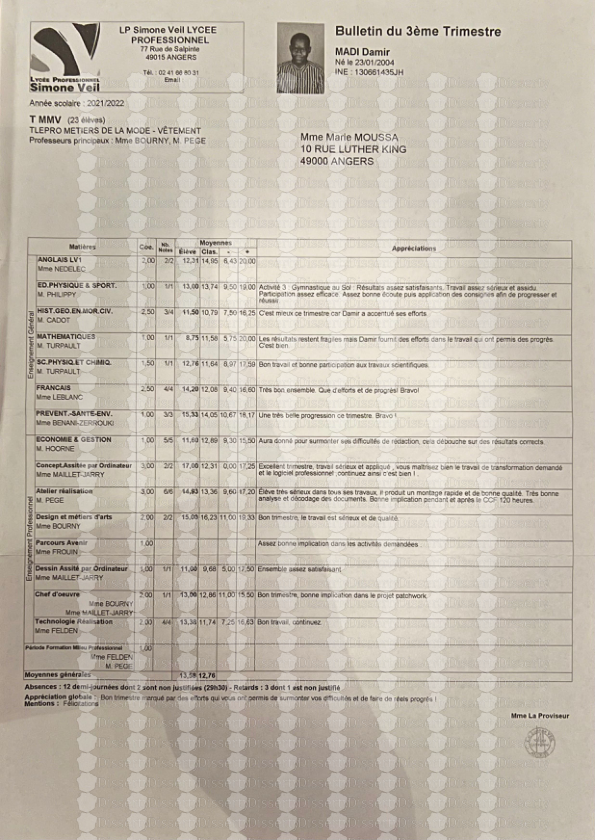
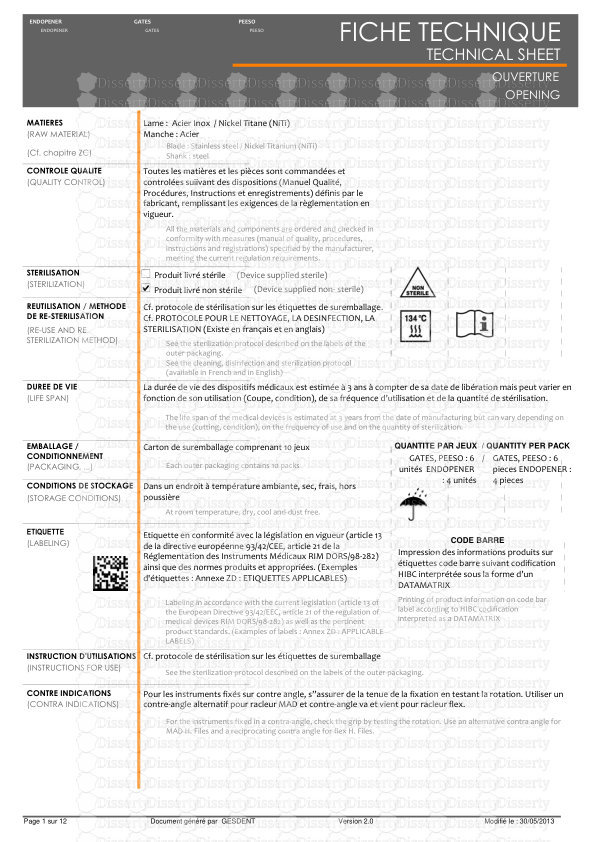
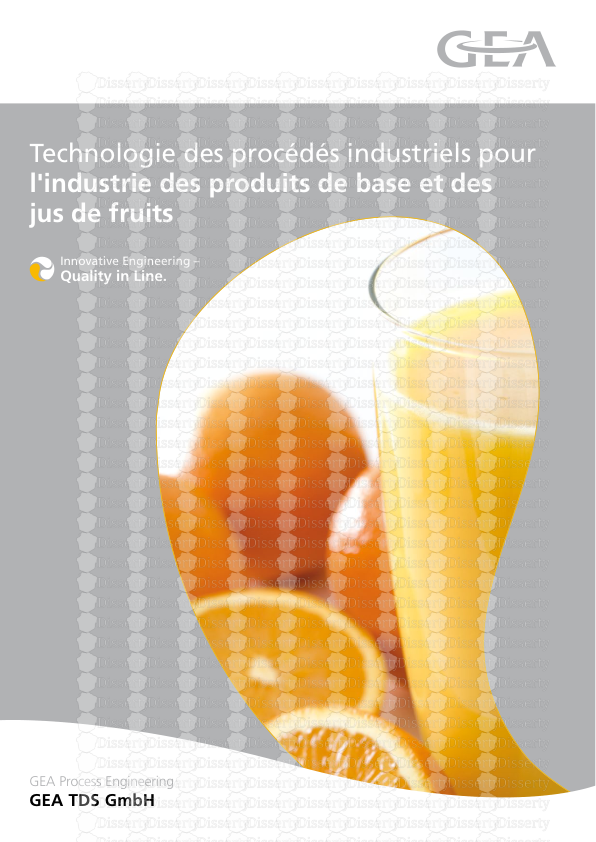
-
50
-
0
-
0
Licence et utilisation
Gratuit pour un usage personnel Attribution requise- Détails
- Publié le Jui 14, 2021
- Catégorie Industry / Industr...
- Langue French
- Taille du fichier 4.7468MB