Project Lean Manufacturing Université M’HAMED BOUGARA - BOUMERDES Faculté de te
Project Lean Manufacturing Université M’HAMED BOUGARA - BOUMERDES Faculté de technologie Réalisé Par : TALZAZET Khaoula BOUSSA Zahra Enseignante responsable de la matière : Mme, OURARI Table du Matière Introduction Lean Manufacturing 1) Définition 2) Historique de l’approche 3) Personnages importants dans l’histoire du Lean 4) Types de Gaspillages Outilles associes 1) Poka-Yoke . 2) LE SMED . 3) La méthode de Kaizen . Conclusion 1 Introduction Le Lean a été étudie, théorise, outille a partir de l’étude du TPS (Toyota Production System). C’est donc tout naturellement qu’on a parlé tout d’abord de Lean Manufacturing. Les principes sous-jacents (Respect, Kaizen, Challenge, Gemba, Teamwork) du Toyota Way ont mis un peu plus de temps a être découverts. On a parlé alors de Lean Management, puis de Lean Office ou de Lean Service. Mais si le fait que Toyota a aussi une façon de procéder tout à fait spécifique pour concevoir et d´envelopper ses produits a été assez vite compris, le Lean en Ingénierie a été longtemps vu comme une application des outils de la production. Le plus souvent, il s’agissait plutôt d’une tentative d’optimisation des processus, ce qui est considérer le sujet par un tout petit bout de la lorgnette. 2 Lean Manufacturing Définition Lean Manufacturing est une méthode d’optimisation de la performance industrielle qui permet, grâce a une analyse détaillée des différentes étapes d’un processus de production, d’optimiser chaque étape et chaque fonction de l’entreprise. Elle repose sur le principe de la chasse aux gaspillages tout au long du processus, et permet donc de réduire les déchets et les couts associes a chaque étape. Historique de l’approche • 1910 : Ford déménage `a Highland Park, lieu de « naissance du lean manufacturing », par la mise en place de chaines de production avec un flux continu de pièces . • 1937 : La production cadencée, introduisant le Takt Time, est utilisée au sein de l’industrie aéronautique Allemande • 1938 : le concept de Juste-à-Temps nait au sein de Toyota • 1940 : le TWI (Training within Industry) est introduit au sein de Toyota, s’appuyant sur la formation des collaborateurs et le partage de connaissances sur le terrain. • 1940 : Kaoru Ishikawa invente le diagramme en arrête de poisson, célèbre méthode éponyme de résolution de problèmes. • 1949 :Taiichi Ohno, manager exécutif chez Toyota, développe le concept d’«élimination des gaspillages ». • 1951 : Ohno améliore le Système de Production Toyota (TPS), en incluant le contrôle visuelle, les suggestions des employés, le TWI, la réduction de taille de lots et le Kanban. •1965 : Toyota reçoit le prix Deming pour la Qualité. • 1975 : Le TPS est mature et inclus le JAT, le kanban, le TQM et le Kaizen. • 1980 : Premier livre d´écrivant le système TPS identifie à du Juste- à Temps : « Kanban : the Coming Revolution » par Norman Bodek 1986 : Motorola met en place le 6 Sigma. • 1988 : Taiichi Ohno publie internationalement le « Toyota Production System ». • 1996 : Publication du livre de Womack et Jones « Système Lean : penser l entreprise au plus juste » • 2000 : Création de la norme ISO 9001, référence des systèmes de gestion de la qualité • 2001 : Publication du livre « Le Modelé Toyota » de Jeffrey Liker. • 2007 :Toyota devient le 1er constructeur automobile mondial • 2010 : Publication de « Velocity » de J.Cox, introduisant le TLS, TOC Lean Sigma, associant le Lean 6 Sigma dans un environnement TOC (Theory of Constraints). Personnages importants dans l’histoire du lean • Henry Ford: Créateur de l’entreprise Ford Motor Company et père des lignes d’assemblages modernes utilisées en production de masse. • Taiichi Ohno Manager exécutif chez Toyota, père du Système de Production Toyota, auteur de plusieurs livres sur le TPS. • Shigeo Shingo: Ingénieur industriel Japonais, qui devint un expert renommé en TPS. Plus d’une douzaines de ses livres ont été traduit en anglais et en français, ce qui l’a rendu plus célèbre en occident que au Japon • James Womack: Auteur de « The machine that changed the world » et « Système Lean », qui a initie le mouvement Lean en occident. Types de Gaspillages • Production excessive • Stocks excessifs • défauts, déchets • Etape sans valeur ajoutée • Temps d'attente • Mouvements inutiles • D´emplacements inutiles • Sous-utilisation des compétences 3 Outilles associes Poka-Yoke Essentiellement, Poka-Yoke se traduit en français par la prévention des erreurs, et un dispositif Poka-Yoke est tout ce qui empêche une erreur de se produire dans le processus de fabrication ou est utilise pour rendre les défauts facilement détectables afin qu’ils puissent ˆêtre tries ou corriges. Les différents types de Poka-Yoke • Le détrompeur de contact: Tout-ou-rien Les systèmes anti-erreur de contact sont caractérises par une forme physique spécifique qui n’admet qu’une seule position, un seul mode de jonction et/ou la vérification absolue d’une condition. Généralement, ces détrompeurs de contact remplissent la fonction « tout ou rien » ; ils obligent l’operateur a ne pas faire d’erreur. • Le détrompeur de signalement: Les systèmes anti-erreur de signalement utilises seuls ou associes aux autres systèmes anti-erreur remplissent les fonctions de d ´encombrement, signalisation, localisation et de guidage. Ils signalent une erreur, un manquement à une condition • Le détrompeur séquentiel ou chronologique: Il s’agit de systèmes anti-erreur dont le but est spécialement de garantir l’exécution d’une suite d’opération dans un ordre précis. Lorsqu’une seule opération de la gamme est obligée où mal exécutée, elle est aussitôt identifiée. La portée du Poka-Yoke Un dispositif Poka-Yoke peut être mis en place a n’importe quelle étape du processus de production et ce, autant dans l’usine de production que durant la phase de la conception finale d’un produit (ex. concevoir un élément anti- erreur destiné à empêcher une mauvaise utilisation par l’utilisateur final). La prise de courant à trois branches est souvent considérée comme un exemple de ce dispositif. LE SMED Les objectifs de SMED : • Gain de temps : Réduire le temps de changement de série( il faut qu’il ne dépasse pas les 9 min ) • améliorer les conditions pour exécuter des changements d’outils. • Augmenter la capacité à produire (moins de perte du temps plus de production ). • Augmenter les revenus ( plus de production plus de commercialisation ). SMED = Single Minute Exchange of Die Soit : Echange d’outil en moins de 10 minutes. • Norme AFNOR NF X50-310 Le SMED est une méthode d’organisation qui cherche à réduire de façon systématique le temps de changement de série, avec un objectif quantifie. Il faut analyser , mesurer les opérations internes ( machine en arrêt ) et externes ( machine en marche ). [ données de machine , opérations , employeurs ... ] • Il faut déterminer les opérations internes et externes . • Il faut convertir les opérations internes en opérations externes ( les transformer ). • Il faut réduire au minimum le temps des opérations internes et externes. La méthode de Kaizen définition C’est une technique japonaise d’amélioration continue de la qualité ou de perfectionnement du processus de fabrication, reposant sur la somme d’aménagements ou d’améliorations de détail que chacun peut proposer de mettre en œuvre au poste qu’il occupe. Conformément a Masaaki Imai, fondateur du Kaizen, cette philosophie s’appuie sur des solutions simples et ”bon marché”, basées sur le bon sens du personnel, et sur la persistance de toutes les personnes impliquées à avoir à l’esprit l’idée de combattre toutes les pertes (étapes sans valeur ajoutée). Quels sont les objectifs de la méthodes Kaizen ? 1. Diminuer la résistance au changement. 2. Mettre en place un management participatif en impliquant les employés et travailleurs. 3. D´envelopper l’esprit d’ équipe 4. Augmenter la motivation 5. Standardiser le travail 6. Améliorer les conditions de travail. 7. Simplifier les flux : spaghetti chart, carte du processus (process map) 8. Améliorer la qualité : Pareto 9. Améliorer les délais : Temps de cycle (takt time) - Améliorer de la productivité : 5S, SMED. Avantages de KAIZEN 1. Amélioration continue. 2. Les gens apprennent de leurs erreurs. 3. Les gens trouvent des moyens d’améliorer les choses. 4. Les biens et services s’améliorent également avec le temps. 5. Mené à un moral améliore, de meilleurs produits et satisfait clients et cout réduit. Exemple Cas de Poka Yoke : • Faire le plein d’essence dans sa voiture 1. Le moteur doit être éteint, sinon la trappe ne s’ouvre pas. 2. Le diamètre du pistolet n’est pas le même en fonction du type de carburant. 3. La distribution s’arrête quand le réservoir est plein, pour éviter tout d ´débordement • Tondeuse a gazon 1. Les nouvelles tondeuses sont équipées de poignée, qu’il faut serrer pour pouvoir démarrer le moteur. 2. Si on lâche la poignée, le moteur s´éteint automatiquement. • Bateau à moteur et Jet ski 1. Sur les petits bateaux à moteurs et les jet-ski, il faut mettre un bracelet qui arrêtera le moteur en cas de chute dans l’eau. Conclusion uploads/Industriel/khao-ula.pdf
Documents similaires
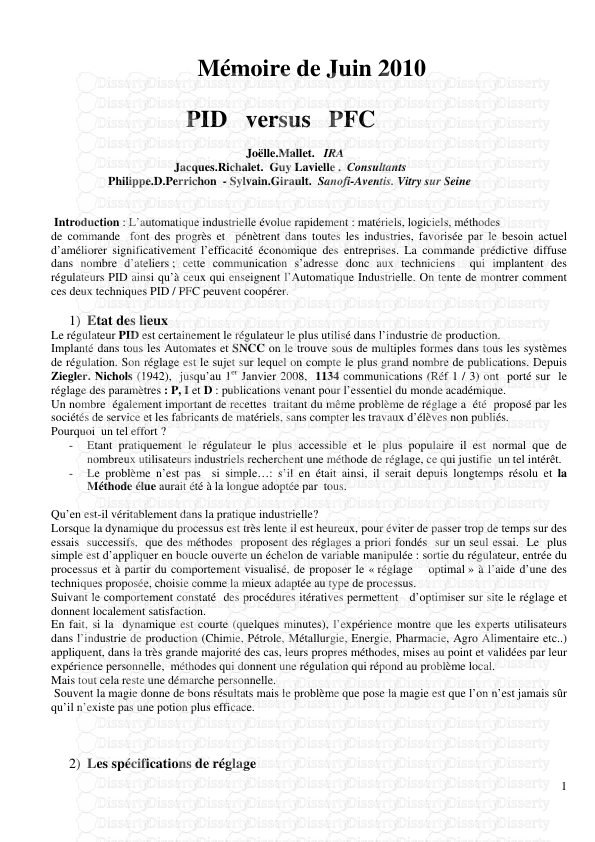
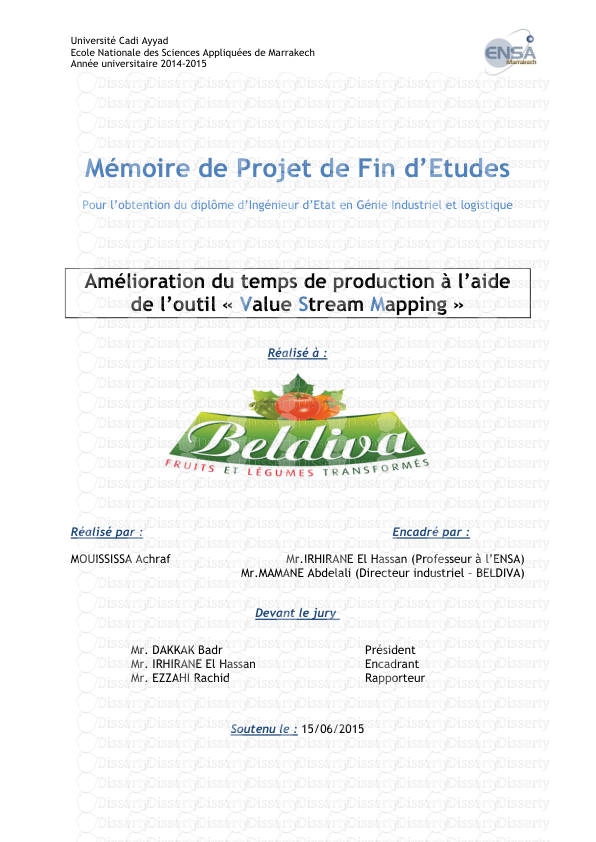

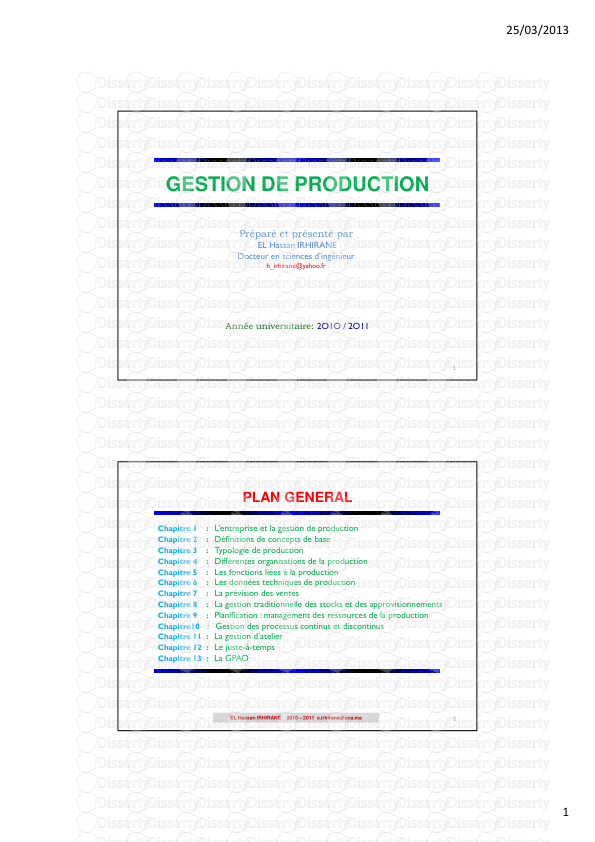
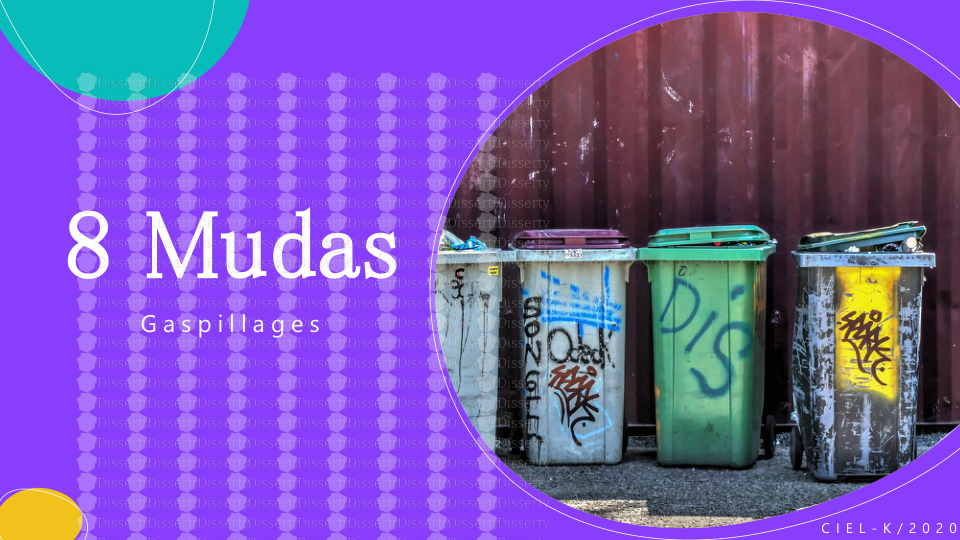
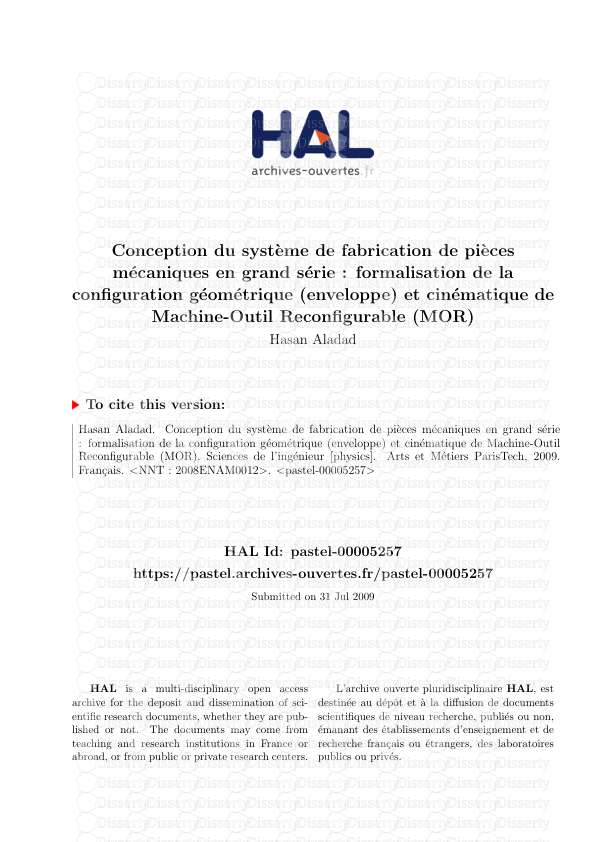
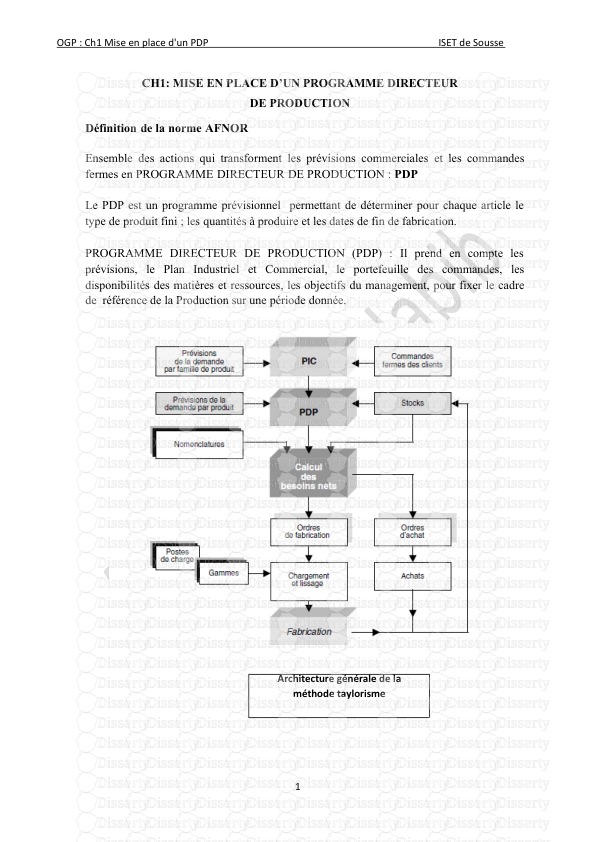
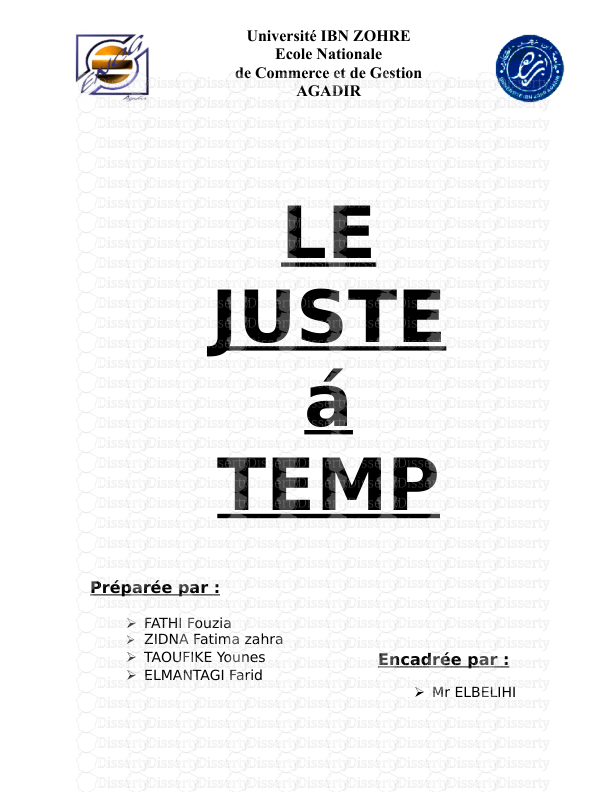
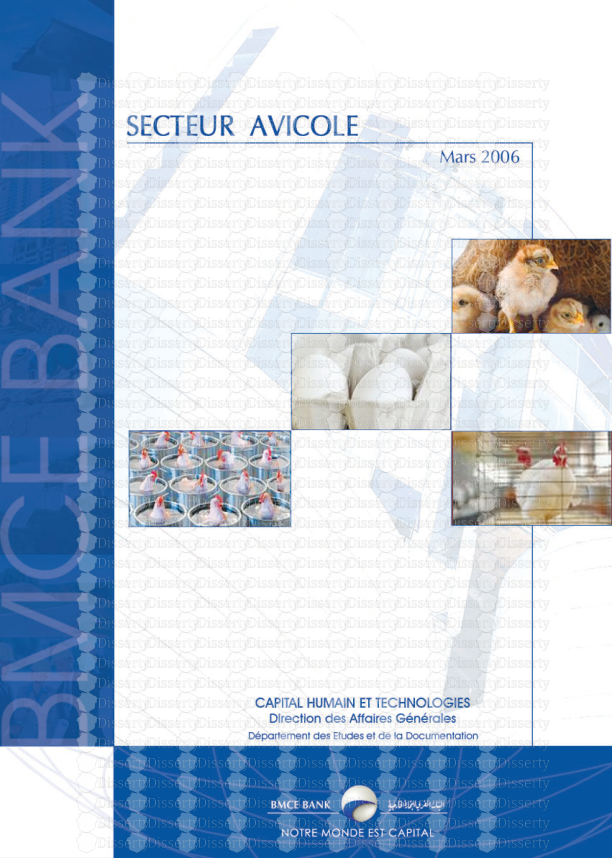
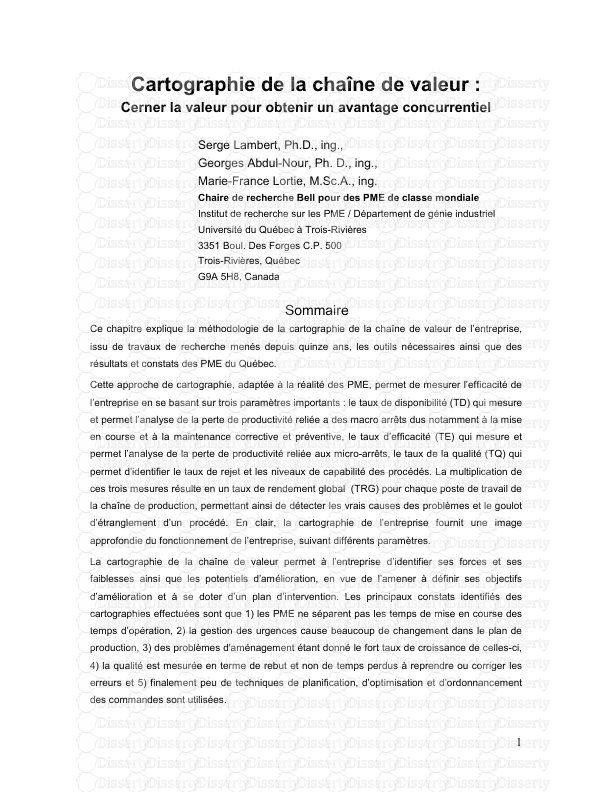
-
48
-
0
-
0
Licence et utilisation
Gratuit pour un usage personnel Attribution requise- Détails
- Publié le Jui 24, 2022
- Catégorie Industry / Industr...
- Langue French
- Taille du fichier 0.3073MB